具有表面裂纹修复能力的锂铝硅酸盐玻璃及其制备方法与流程



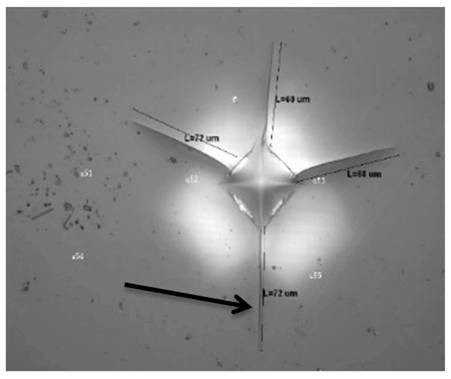
本发明属于玻璃材料技术领域,具体涉及一种具有良好的表面裂纹修复能力的锂铝酸盐玻璃及其制备方法。
背景技术:
玻璃从高温熔体快速冷却至室温的过程以及玻璃加工制程中会在玻璃表面及亚表层产生大量的微裂纹等缺陷。当玻璃使用过程中,常受到不同的外力作用,从而在微裂纹附近产生应力集中,当应力值超过玻璃的极限强度时,微裂纹开始扩展并产生玻璃断裂失效。因此玻璃表面微裂纹的修复对提高玻璃的强度和耐用性是非常重要的。
当玻璃表面存在裂纹后,重新将玻璃再加热至玻璃应变点或以上时,此时高温下玻璃内结构基团(分子或离子)将产生相对移动,离子间发生相互扩散,裂纹处的出现了逐步愈合修复的现象,随着裂纹的修复,玻璃的强度得到改善。但1.5mm以下的薄玻璃在高于应变点以上的热处理导致玻璃出现表面变形和翘曲等问题,限制了该裂纹修复的方法的使用。通过低温离子交换方法对玻璃表面及亚表层的裂纹进行修复,提升玻璃表面强度。
技术实现要素:
本发明目的在于提供一种具有良好的表面裂纹修复能力的锂铝硅酸盐玻璃及其制备方法。为实现上述目的,本发明采用如下技术方案:
所述一种具有表面裂纹修复能力的锂铝硅酸盐玻璃,其特征在于:所述组成以质量百分比计组成,包括:
55-65%的sio2,
15-22%的al2o3,
0.5-4%的b2o3,
3.5-6%的li2o,
8-14%的na2o,
0.2-3%的mgo,
0.1-2.5%的zro2,
上述组成中,(al2o3+ro)/(b2o3+r2o)为1.0~2.0;
(r2o+ro-zro2)/al2o3为0.5~1.0;
所述从钢化锂铝硅酸盐玻璃表面延伸至50μm处压缩应力层至少为30mpa;
所述钢化锂铝硅酸盐玻璃的环压强度至少为1.0gpa。
本发明提供一种具有表面裂纹修复能力的锂铝硅酸盐玻璃,所述组成以质量百分比计组成,包括:
58-63%的sio2,
16.5-22%的al2o3,
0.5-4%的b2o3,
3.5-5%的li2o,
8-14%的na2o,
0.5-3%的mgo,
1-2.5%的zro2,
其中(al2o3+ro)/(b2o3+r2o)为1.25~1.65;
(r2o+ro-zro2)/al2o3为0.6~0.9;
所述从钢化锂铝硅酸盐玻璃表面延伸至50μm处压缩应力层为50mpa;
所述钢化锂铝硅酸盐玻璃的环压强度至少为1.2gpa。
所述的组成中还包括质量分数小于2.0%的p2o5、质量分数小于0.1%的fe2o3、质量分数小于0.5%的澄清剂和质量分数小于2%的zno。
所述的组成中还包括质量分数小于0.1%的k2o、质量分数小于0.1%的cao。
所述玻璃的平均线热膨胀系数最大为95×10-7/k;所述玻璃的未钢化前维氏硬度最大为650mpa。
一种具有表面裂纹修复能力的锂铝硅酸盐玻璃制备方法,其特征在于:所述制备方法包括玻璃的多步钢化:
将玻璃制品的组成以至多20℃/min升温速度预热至300-400℃;
将预热后的组成在盐溶液中以360-420℃进行第一步钢化;
将第一步钢化的组成在盐溶液中以至少400℃进行中间钢化;
将中间钢化的组成在盐溶液中以380-420℃进行最后一步钢化,即可制备得到钢化锂铝硅酸盐玻璃制品;
所述从钢化锂铝硅酸盐玻璃表面延伸至50μm处压缩应力层至少为30mpa;
所述钢化锂铝硅酸盐玻璃内部张应力区距离玻璃表面至少为0.1t;
所述钢化锂铝硅酸盐玻璃的环压强度至少约1gpa。
所述的具有表面裂纹修复能力的锂铝硅酸盐玻璃的制备方法,其特征在于:第一步钢化过程中,所述的盐溶液为nano3盐或nano3和kno3的混合盐,所述混合盐中nano3盐至少为40wt%,剩余为kno3盐。
所述的具有表面裂纹修复能力的锂铝硅酸盐玻璃的制备方法,其特征在于:中间钢化过程中,所述的盐溶液为nano3和kno3的混合盐,其中nano3盐浓度为20-80wt%,剩余为kno3盐;所述的中间钢化过程至少是2步钢化过程。
所述的具有表面裂纹修复能力的锂铝硅酸盐玻璃制品的制备方法,其特征在于:所述的最后一步钢化过程中,所述的盐溶液为nano3和kno3的混合盐或kno3的盐,其中混合盐中kno3盐浓度至少为90wt%,剩余为nano3盐。
所述的具有表面裂纹修复能力的锂铝硅酸盐玻璃的制备方法,其特征在于:第一步钢化时间为30min-240min;中间钢化时间为5min-90min;最后一步钢化时间为90min-300min。
本发明中所述的实施例中玻璃组成都是基于氧化物的质量分数(wt%)。现对实施例中各氧化物组成说明如下:
sio2在玻璃中形成[sio4]四面体,属于玻璃网络形成体,构成玻璃的网络骨架结构。sio2组分能提高玻璃的机械强度,改善耐化学稳定性,在实施例中,sio2组分至少是56%,更优选至少为57%,更优选至少为58%,因为玻璃中过低的sio2浓度会导致耐化性能和表面强度变差,导致玻璃在加工制程中禅文产生更多更深的裂纹,并且裂纹在清晰过程发生扩展,加大了表面裂纹的修复的难度。sio2组分的熔点温度为1713℃,提高了玻璃的粘度,不利于玻璃熔化与澄清,玻璃中sio2组分至多65%,更优选至多为63%。
al2o3属于网络中间体成分,当玻璃中碱金属含量多事,玻璃中al3+倾向于形成铝氧四面体[alo4],成为玻璃网路结构的一部分,提高玻璃的表面强度,减少表面产生裂纹的可能性。由于al-o键长为0.176nm,形成[alo4]的结构单元的体积为41cm3/mol,而si-o键长为0.16nm,形成的[sio4]的结构单元的体积为27.2cm3/mol,[alo4]的体积比[sio4]大约50%,当玻璃中[alo4]参与到玻璃结构中后,使得玻璃的网络结构空隙变大,为离子交换提供通道,起加速离子交换作用,对表面裂纹的修复起到明显的促进作用,因此玻璃中al2o3至少15%,更优选至少16.5%。但al2o3氧化物的熔点温度为2050℃,属于极难熔氧化物,使得玻璃粘度急剧上升,致使玻璃澄清均化难度加大,导致产品良率降低,同时增加玻璃成型和拉薄难度增加,因此玻璃中al2o3含量至多为22wt%。
b2o3属于玻璃形成体氧化物,熔点为450℃,在高温熔化中形成[bo3],降低玻璃的熔点,改善熔化澄清和降低成型拉薄的难度,利于产品的良率提升;在低温阶段形成的[bo4]提高玻璃化学稳定性和热稳定性,提高玻璃的机械强度,减缓裂纹尖端应力的应力集中,有利于表面裂纹的修复,为考虑到氧化硼在高温熔化阶段存在一定的挥发率,b2o3含量至少为0.5%。高b2o3时在玻璃中形成高[bo3]含量,降低玻璃粘度,例如玻璃应变点温度,引起玻璃在离子交换增强过程中应力松弛量过大,导致强化后钢化性能劣化,不利于玻璃表面的裂纹的修复,b2o3至多为4%。
li2o属于网络外体氧化物,对玻璃网络结构起到断网作用,能快速降低玻璃的粘度,降低玻璃熔化温度和成型拉薄难度,有利于产品良率的提升。在高于350℃的nano3熔盐中,玻璃中li+离子和钢化熔盐中na+发生离子交换,离子半径大na+替代离子半径小li+,形成高的压缩应力层深,能有效提升玻璃裂纹的修复能力,尤其是裂纹纵向方向,因此玻璃中应具有足够高的li2o成分,保证足量的li+离子和na+离子进行交换,如果玻璃中li2o含量过低,li+离子和na+离子交换能力不足,li2o含量至少约3.5mol%;li2o中li+具有离子半径小,在玻璃中容易产生积聚作用,因此高含量的li2o促使玻璃倾向于失透,无法生产,li2o含量至多约6%,更优选至多约5%。
na2o属于网络外体氧化物,破坏玻璃的网络结构,改善玻璃熔化和澄清;在高于350℃的硝酸钾熔盐中,玻璃中na+离子与熔盐中k+发生离子交换,离子半径大k+取代离子半径小的na+,在玻璃表面形成高表面压应力值和压应力层,有效修复玻璃表层的裂纹,对裂纹的修复至关重要,因此na2o含量至少8%;过量的na2o会引起玻璃一系列性能变差,例如玻璃的机械性能大幅降低,玻璃耐化性能降低,导致玻璃表面因制程加工产生更多的表面裂纹,不利于表面裂纹的修复,本发明的中na2o含量至多14%。
k2o同属于玻璃网络外体成分,降低玻璃粘度作用,改善玻璃熔化和澄清;并与na2o之间存在“混碱效应”,对改善玻璃的物化性能其一定作用,但k2o含量增加能导致玻璃的膨胀系数急剧增加,玻璃机械性能趋于劣化,不利于玻璃热加工中裂纹的修复,并且玻璃钢化过程中应力松弛量因k2o的存在而明显增加,极大阻碍了玻璃的裂纹的修复与改善,本发明k2o含量优选至多为0.1%,更优选不含k2o。
cao、mgo、zno同属二价阳离子氧化物,且均是网络外体,促进玻璃熔化与熔化,同时改善玻璃的机械性能。但二价阳离子氧化物在玻璃钢化中从玻璃中扩散至熔盐中,并聚集吸附在玻璃表层,阻碍na+、k+和li+之间相互扩散,不利于表面裂纹的修复,因此二价阳离子氧化物不宜过多,其中ca2+因与na+离子半径接近对离子交换的阻碍作用最大,因此玻璃中cao含量至多为0.3%,更有选至多为0.1%。其中mgo还能降低结晶倾向和结晶速度,提高玻璃的化学稳定性,因此优选mgo含量为0.2-3%。其中zno易造成玻璃失透性,对玻璃裂纹的修复作用较小,zno含量0-2%,更优选至多为0.1%。
zro2属于玻璃网络外体氧化物,在玻璃中以[zro8]结构单元存在,夺取玻璃中游离氧,对网络结构起到修补的作用,提高玻璃机械强度和耐化性能,能延缓玻璃在钢化过程中的应力松弛量,有利于玻璃的表面裂纹的修复,zro2含量优选至少0.1%,更优选至少1%。但zro2含量快速提高玻璃的粘度,促进玻璃的失透,zro2含量至多约2.5%。
p2o5属于网络形成体氧化物,以[po4]四面体相互连成网络,属于层状,且层间由范德华力相互连接,降低粘度而利于改善玻璃的熔化和成形拉薄,且促进离子交换,对表面裂纹的修复具有改善作用。过多p2o5导致玻璃表面的化学稳定性趋于劣化,玻璃倾向于失透,本发明中p2o5含量至多为2%。
fe2o3属于网络外体氧化物,其在玻璃中形成fe2+可吸收近红外光谱,有利于改善玻璃的熔化,有利于玻璃在热处理过程中吸收更多的热量减缓玻璃的降温速度,有利于玻璃表面裂纹的修复,但过量fe2o3含量吸收可见光,导致玻璃的透过率低于90%,因此本发明中fe2o3含量至多为0.1%,更优选至多为0.05%,更优选至多为0.03%。
本发明的玻璃中含有澄清剂,澄清剂包括氧化锡、氧化亚锡、氧化铈、硫酸钠等化合物或两种以上的混合物,优选澄清剂为0~0.5%,主要用于玻璃熔制过程中高温澄清,改善玻璃澄清效果,减少玻璃内部缺陷率,防止玻璃的裂纹从内部延伸至玻璃表层,使得该处裂纹无法得到修复。
本发明实施例中,质量比(al2o3+ro):(b2o3+r2o)为1.0~2.0,其中ro为玻璃组成中cao,mgo和zno的含量之和,r2o为玻璃组成中li2o,na2o和k2o的含量之和。(al2o3+ro):(b2o3+r2o)值高于1.0,有利于改善玻璃离子交换,改善玻璃表面裂纹的修复,更优选(al2o3+ro):(b2o3+r2o)值高于1.25。(al2o3+ro):(b2o3+r2o)值不高于2.0,有利于玻璃的熔化、澄清和成形拉薄,更优选(al2o3+ro):(b2o3+r2o)值不高于1.65。
本发明实施例中,质量比(r2o+ro-zro2)/al2o3为0.5~1.0,其中ro为玻璃组成中cao,mgo和zno的含量之和,r2o为玻璃组成中li2o,na2o和k2o的含量之和。(r2o+ro-zro2)/al2o3不低于0.5,有利于改善玻璃的熔化、澄清和拉薄成形,更优选(r2o+ro-zro2)/al2o3不低于0.6,(r2o+ro-zro2)/al2o3不高于1.0,有利于改善玻璃离子交换,改善玻璃表面裂纹的修复,更优选(r2o+ro-zro2)/al2o3不高于0.9。
本发明中实施例的玻璃组成可以通过任意合适的方法进行成形,例如:浮法工艺成形、压延成形、狭缝下拉工艺成形、溢流下拉工艺成形等形成厚度为0.1mm~2mm的玻璃板。
本发明中玻璃表面裂纹的修复与玻璃的钢化制程是密切相关的,本发明通过优化玻璃组成,获得较佳有利于玻璃钢化和裂纹修复的玻璃组成,通过至少二步钢化制程,利用钢化过程中大半径离子替换小半径离子产生挤塞作用,和逐级钢化制程以及玻璃在钢化温度下裂纹的自动修复能力,从而实现玻璃表面的裂纹修复。所述玻璃逐级钢化制程,通过至少两步或两步以上的钢化制程,各钢化制程中nano3浓度差维持在20%或以上,具体说明如下:
玻璃预热:玻璃制品以至多约20℃/min升温速度加热至低于第一步钢化温度至多约50℃。玻璃预热过程中的升温速度对表面裂纹修复产生不利的影响,尤其是在低于200℃范围内升温速度,升温速度越快,玻璃的裂纹趋于扩展,优选升温速度为至多为15℃/min,更优选升温速度为至多为10℃/min,更优选升温速度为至多为5℃/min;预热温度比第一步钢化制程的温度低至多约50℃,更优选低至多40℃,更优选低至多约30℃,更优选低至多约20℃。
第一步钢化制程:熔盐中含至少约40wt%nano3,熔盐中nano3浓度越高,玻璃中li+离子与na+交换后在玻璃中形成的压应力值越高,越有利沿玻璃厚度方向的裂纹的修复,第一步钢化熔盐中优选nano3的浓度至少约50%,更优选nano3的浓度至少约60%,更优选nano3的浓度至少约70%,更优选nano3的浓度至少约80%,更优选nano3的浓度至少约90%,更优选nano3的浓度至少约100%;第一步钢化制程温度至少约360℃,更优选至少为380℃,更优选至少约为400℃。
中间钢化制程优选三种不同nano3浓度的熔盐,更优选两种不同nano3浓度的熔盐,更优选一种不同nano3浓度的熔盐;中间钢化制程的温度优选至少约400℃,更有选至少420℃,更优选至少440℃;中间钢化制程时间总共至多约120min,更优选至多约90min,更优选至多约60min,为了达到中间制程对裂纹的修复能力,中间钢化制程时间总共至少约3min,更优选至少约5min,更优选至少约10min。
最后一步钢化制程:钢化熔盐含至多约10wt%nano3盐,熔盐中kno3浓度越高,玻璃中na+离子与熔盐中k+交换后在玻璃中形成的压应力值越高,越有利玻璃表面的裂纹的修复,钢化熔盐中优选nano3的浓度至多约10%,更优选nano3的浓度至少约5%,更优选nano3的浓度至少约0%;钢化熔盐的温度至高约420℃,更优选至高约410℃,更优选至高约400℃。
附图说明
图1为实施例5钢化前裂纹长度。
图2为实施例5钢化后裂纹长度。
具体实施方式
为进一步公开而不是限制本发明,以下结合实例对本发明作进一步的详细说明。
本发明提供的一种具有表面裂纹修复能力的钢化锂铝硅酸盐玻璃制方法步骤说明如下:
(1)依照各物质的质量比称量各氧化物、氢氧化物和碳酸盐等组成,称重放入混合机内混合均匀,获得均匀的配合料;
(2)然后将配合料转移至为400ml铂坩埚中,将铂坩埚置入硅钼棒高温炉炉内,逐渐升温至1620℃,持温4-8h,通过搅拌加速玻璃气泡排出和使玻璃均化;
(3)熔融后将玻璃液倒入不锈钢模具进行成型,然后取出玻璃块并移入箱式退火炉内进行550-650℃的1小时热处理,随后以1℃/min的速率降至500℃及以下,之后随炉至室温,得到玻璃片。
(4)将采用金刚石线切割机成薄片后进行精密抛光处理,清洗后进行逐级钢化制程处理,即可获得具有表面裂纹修复能力的锂铝硅酸盐玻璃。
本发明的一些实例及玻璃样品的物理性质如表1所示。其定义及解释如下所示:a.膨胀系数,采用膨胀仪器测试,依据gb/t16920-2015标准进行测试。
b.退火点温度,玻璃粘度为1013泊时的温度,采用膨胀仪器依据gb/t16920-2015标准进行测试,获得膨胀曲线后通过切线确定;
c.应变点温度,玻璃粘度为1014.5泊时的温度,采用膨胀仪器依据gb/t16920-2015标准进行测试,获得膨胀曲线后通过切线确定;
d.密度,采用沉浮密度比较仪依据gb/t14901-2008测试25℃时玻璃的密度;
e.维氏硬度,采用显微维氏硬度计测试,依据gb/t4342-1991,加载力为200g,加载时间为10s;
f.cs_k和dol_k,采用fsm-6000leuv表面应力仪测试;
g.cs_50和dol_zero,采用slp-2000表面应力仪测试;
h.表面环压强度:采用抗弯强度试验机测试;
i.裂纹修复率:采用显微维氏硬度计,设置加载力为500g,加载时间为10s,玻璃表面出现裂纹,测量最长裂纹的长度,钢化完成后,再测试该裂纹的长度值,钢化前后两个裂纹长度的比值为裂纹修复比率。
表1实施例组成及性能
以实施例5的钢化前后的玻璃为例,如图1、2所示,图1为实施例5钢化前裂纹长度,裂纹长度为72μm。图2为实施例5钢化后裂纹长度,裂纹长度为0,即没有裂纹的形态,其他实施例也与本案钢化后的裂纹效果效果。
以上所述仅为本发明的较佳实施例,凡依本发明申请专利范围所做的均等变化与修饰,皆应属本发明的涵盖范围。
起点商标作为专业知识产权交易平台,可以帮助大家解决很多问题,如果大家想要了解更多知产交易信息请点击 【在线咨询】或添加微信 【19522093243】与客服一对一沟通,为大家解决相关问题。
此文章来源于网络,如有侵权,请联系删除


