一种海砂处理工艺的制作方法



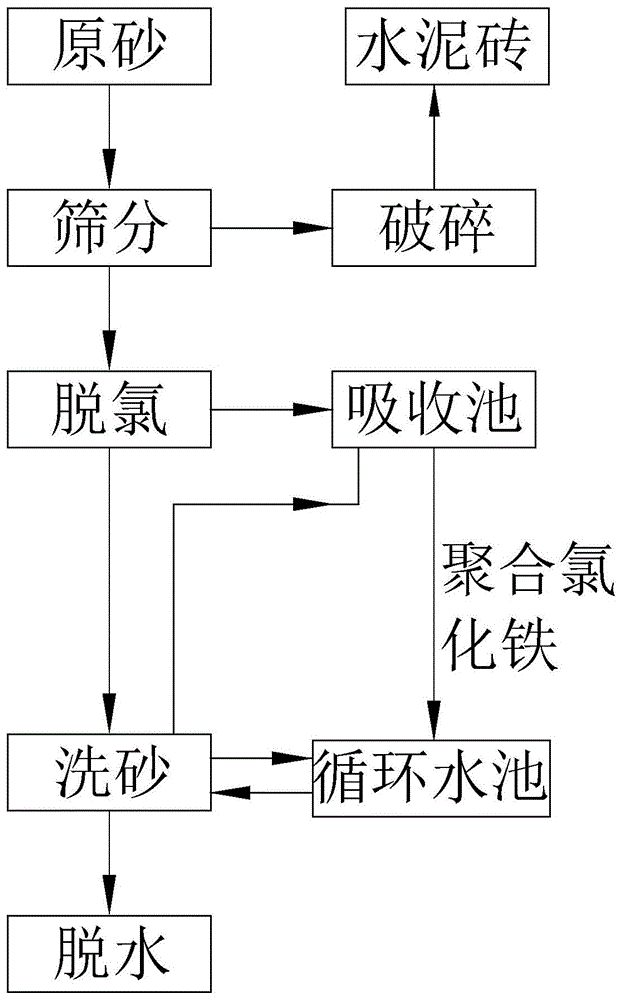
本申请涉及海砂处理
技术领域:
,尤其是涉及一种海砂处理工艺。
背景技术:
:随着我国建筑市场的快速发展,河砂资源日益匮乏,已不能满足建筑用原材料的需求,且河砂的过度开采对自然景观和生态环境带来严重破坏。而我国东部沿海地区海砂资源丰富,合理开发利用当地的海砂资源,对于缓解河砂资源不足的局面及保护生态环境都具有重要的意义。然而,由于海砂含有氯化镁、氯化钠等盐份,使用海砂作为混凝土原料时,海砂中含有的氯盐会导致钢筋蚀锈,使钢筋表面的钝化膜遭受破坏,容易造成建筑物强度、硬度及承受力下降,严重影响建筑物的安全性及使用寿命。因此,对海砂中氯盐的有效去除是海砂淡化的关键。目前,国内外针对海砂中氯盐除去的最新技术措施主要有:海砂淡水冲洗法、钢筋阻锈剂法、钢筋镀膜法、混凝土配比优化法等,其中海砂淡水冲洗法是最为常用的方法。海砂淡水冲洗法是利用淡水对海砂进行反复多次冲洗,以此将氯盐与海砂分离并除去。但这种净化处理工艺的对氯离子的去除效率不高,且用水量大。针对上述中的相关技术,发明人认为存在有氯离子的去除效率不高且用水量大的缺陷。技术实现要素:为了提高氯离子的去除效率并降低用水量,本申请提供一种海砂处理工艺。本申请提供的一种海砂处理工艺采用如下的技术方案:一种海砂处理工艺,包括以下步骤:(1)筛分:对原砂进行振动筛分,将海砂中的贝壳、砾石等杂质筛去;(2)脱氯:将过筛后的海砂输送至脱氯池内,并浸入脱氯剂中进行脱氯,所述脱氯剂采用臭氧水溶液;(3)洗砂:将脱氯后的海砂输送至清洗池内,利用清洗水对海砂进行冲洗;(4)脱水:将清洗后的海砂进行脱水处理,除去海砂内多余的水分,得到成品砂。通过采用上述技术方案,原砂中含有贝壳、砾石等的杂质,通过振动筛分将上述大颗粒物分离出来,以满足建设用砂标准中颗粒粒径小于4.75mm的要求,并降低了后续除氯的负荷;脱氯剂采用臭氧水溶液,臭氧具有强氧化性,海砂浸入脱氯剂的过程中,臭氧分子与海砂中游离的氯离子发生氧化还原反应,氯离子被氧化为氯气,并以气体的形式挥发出去,以此实现氯离子与海砂的分离,达到高效脱氯的效果;利用清洗水对脱氯后的海砂进行冲洗,以此除去海砂内残存的氯离子,进一步降低了海砂中氯离子的含量,并将海砂中的部分泥土冲洗分离,降低了成品砂的含泥量及泥块含量,从而提高了海砂质量;对清洗后的海砂进行脱水处理,将海砂内多余的水分除去,以满足建设用砂标准中对含水率的要求;本申请利用臭氧的强氧化性,有效的将海砂中的氯离子除去,以此提高海砂净化的效率,同时大大降低了用水量。优选的,所述步骤(2)中脱氯剂的质量浓度为30mg/l~100mg/l,海砂的脱氯时间为30~120min。通过采用上述技术方案,当脱氯剂的质量浓度为30mg/l~100mg/l,海砂的脱氯时间为30~120min,随臭氧水的浓度越高、海砂的浸泡时间越长,海砂中氯离子与臭氧发生氧化还原反应就越充分,海砂中氯离子的含量就越低,越有利于提高脱氯效率,且处理后成品砂中的氯离子含量可达建设用砂ⅲ~ⅰ级标准中的氯离子含量的要求,确保了海砂的净化效果。所述步骤(2)中脱氯剂的质量浓度为30mg/l~65mg/l,海砂的脱氯时间为30~75min。通过采用上述技术方案,当臭氧水浓度为30mg/l、脱氯时间为30min时,成品砂的氯离子含量恰好达到建设用砂ⅲ级标准中的氯离子含量的要求;当臭氧水浓度逐渐增加至65mg/l、脱氯时间逐渐延长至75min时,成品砂的氯离子含量恰好达到建设用砂ⅰ级标准中的氯离子含量的要求;工作人员可根据建设用砂所需达到的质量等级,确定相应的臭氧水浓度及脱氯时间,无需继续增大上述工艺参数即可达到所需的净化效果,防止臭氧水浓度过高造成资源浪费,并防止脱氯时间过长增加处理成本,从而确保了生产效益。优选的,所述步骤(3)中清洗水的用水量为海砂重量的30%~60%,洗砂的温度为60℃~90℃。通过采用上述技术方案,当清洗水的用水量为海砂重量的30%~60%时,随清洗水量与海砂的重量比增大,清洗水量中氯离子与海砂上的氯离子的浓度差增大,有利于海砂中的氯离子向清洗水迁移,从而提高了海砂的净化效果,且处理后成品砂中的氯离子含量可达建设用砂ⅲ~ⅰ级标准中的氯离子含量的要求,确保了海砂的净化效果,工作人员可根据建设用砂所需达到的质量等级,确定相应的清洗水量与海砂的重量比,保持良好的净化效果的同时,防止了清洗水用量过大造成水资源浪费,并减少了污水的产生量,具有保护环境的效果;且海砂在清洗的同时进行加热,降低了氯气在水中的溶解度,有利于残留在海砂表面上的氯气的挥发,进一步防止了海砂在使用过程中氯气释放对人体造成危害。优选的,将所述步骤(2)中脱氯的海砂及所述步骤(3)中清洗的海砂均进行搅动。通过采用上述技术方案,对脱氯的海砂进行搅动,使海砂相互之间进行碰撞、摩擦,以此破坏海砂表面的氯离子生物膜,有利于氯离子释放进入臭氧水溶液中,提高了化学反应速率,进而提高了脱氯的效率;对清洗中的海砂进行搅动,使清洗水与海砂充分接触,有利于对残余氯离子进行清洗,以此提高洗砂效率,进一步增强了海砂的净化效果。优选的,所述步骤(2)与所述步骤(3)中设有集气罩与吸收池,产生的氯气由集气罩收集并导入吸收池内进行吸收。通过采用上述技术方案,海砂在脱氯过程中产生有氯气,氯气具有毒性,脱氯过程于密闭空间内进行,且氯气被吸收池收集,有效的防止了氯气进入大气环境造成污染并危害人体健康。优选的,所述吸收池内装有废铁屑与3~10%的氯化氢溶液。通过采用上述技术方案,吸收池内的废铁屑与氯化氢溶液反应生成氯化亚铁溶液,通入氯气后,氯气将氯化亚铁氧化为三氯化铁,以此实现氯气的吸收,此时三氯化铁被吸收池内剩余的废铁屑还原为氯化亚铁,并再次参与吸收反应,使氯气不断被吸收,同时废铁屑得以资源化利用,从而具有良好的经济效益及环境效益。优选的,将所述氯化亚铁溶液进行蒸发浓缩,在温度为50℃~90℃条件下,加入亚硝酸钠并通入氧气,反应3~5h。通过采用上述技术方案,氯化亚铁进行浓缩后,氧气的氧化作用将氯化亚铁充分的氧化为三氯化铁,并在亚硝酸钠的催化作用下发生聚合反应,最终生成聚合氯化铁,聚合氯化铁具有良好的絮凝作用,对水质的净化效果好,防止了氯气吸收带来的二次污染,并实现了废物的资源化利用。优选的,所述步骤(3)中设有循环水池,洗砂完成后将清洗水送至所述循环水池内,并调节ph为3.5~5.0,然后向所述循环水池内投入所述聚合氯化铁溶液,搅拌均匀,静置后将上清液循环至清洗池内。通过采用上述技术方案,清洗水对海砂进行冲洗后,清洗水中含有机物、悬浮颗粒等杂质,将洗砂后的清洗水送至循环水池内,并加入聚合氯化铁溶液,通过聚合氯化铁的絮凝沉淀作用,实现对清洗水的净化,最后将净化后的清洗水循环至清洗池内,以此实现清洗用水的循环利用,从而进一步降低了用水量。优选的,将所述步骤(1)中筛分得到的贝壳、砾石等杂质进行破碎,并回收作为水泥砖的原料。通过采用上述技术方案,将筛分得到的杂质进行破碎,并作为水泥砖的原料,大大降低了水泥砖的制造成本,以此实现固体废物的回收与资源化利用,并有效的防止了杂质于海砂的堆积造成周围环境的破坏。综上所述,本申请包括以下至少一种有益技术效果:1.脱氯剂的强氧化性将海砂中氯离子氧化为氯气并排出,实现氯离子与海砂的分离,且随臭氧水浓度升高及脱氯时间的增加,海砂的脱氯效率提高;利用清洗水对脱氯后的海砂进行冲洗,除去海砂内残存的氯离子及部分泥土,进一步降低海砂中氯离子的同时降低了含泥量及泥块含量,具有提高海砂净化的效率的同时降低用水量的效果;2.吸收池内的废铁屑与氯化氢溶液反应生成氯化亚铁溶液,通入氯气后,氯气将氯化亚铁氧化为三氯化铁,以此实现氯气的吸收,此时三氯化铁被吸收池内剩余的废铁屑还原为氯化亚铁,并再次参与吸收反应,使氯气不断被吸收,同时废铁屑得以资源化利用,从而具有良好的经济效益及环境效益;3.氯化亚铁被氧化为三氯化铁,并在亚硝酸钠的催化作用下发生聚合反应,最终生成聚合氯化铁,清洗水在聚合氯化铁絮凝作用下得以净化,并循环至清洗池内实现循环利用,进一步降低用水量,同时防止了氯气吸收带来的二次污染,并实现了废物的资源化利用。附图说明图1是本申请的海砂处理工艺的流程图。具体实施方式以下结合附图1及实施例,对本申请作进一步详细说明。实施例1一种海砂处理工艺,包括以下步骤:(1)筛分:对原砂进行振动筛分,将海砂中的贝壳、砾石等杂质筛去;并对筛分得到的贝壳、砾石等杂质进行破碎,回收作为水泥砖的原料,实现固体废物的回收与资源化利用;(2)脱氯:将过筛后的海砂输送至脱氯池内,浸入脱氯剂中并搅动海砂进行脱氯,脱氯剂采用质量浓度为30mg/l臭氧水溶液,脱氯时间为30min。脱氯池上设有集气罩及吸收池,吸收池内装有废铁屑与3%的氯化氢溶液,废铁屑与氯化氢溶液反应生成氯化亚铁溶液,产生的氯气由集气罩收集并导入吸收池内被氯化亚铁溶液吸收;(3)洗砂:将脱氯后的海砂输送至清洗池内,清洗池内装有温度为60℃、水量为海砂重量30%的清洗水,此时搅动海砂,利用清洗水对海砂进行冲洗;清洗池上亦设有集气罩,并设有循环水池。洗砂完成后将清洗水送至所述循环水池内,并调节ph为3.5;将步骤(2)中吸收池内吸收完成的氯化亚铁溶液进行蒸发浓缩,然后在温度为50℃条件下,加入亚硝酸钠并通入氧气,反应3h,得到聚合氯化铁溶液;最后向循环水池内投入聚合氯化铁溶液,搅拌均匀,静置后将上清液循环至清洗池内,实现清洗用水的循环利用;(4)脱水:将清洗后的海砂进行脱水处理,除去海砂内多余的水分,得到成品砂。实施例2一种海砂处理工艺,包括以下步骤:(1)筛分:对原砂进行振动筛分,将海砂中的贝壳、砾石等杂质筛去;并对筛分得到的贝壳、砾石等杂质进行破碎,回收作为水泥砖的原料,实现固体废物的回收与资源化利用。(2)脱氯:将过筛后的海砂输送至脱氯池内,浸入脱氯剂中并搅动海砂进行脱氯,脱氯剂采用质量浓度为65mg/l臭氧水溶液,脱氯时间为75min。脱氯池上设有集气罩及吸收池,吸收池内装有废铁屑与7%的氯化氢溶液,废铁屑与氯化氢溶液反应生成氯化亚铁溶液,产生的氯气由集气罩收集并导入吸收池内被氯化亚铁溶液吸收;(3)洗砂:将脱氯后的海砂输送至清洗池内,清洗池内装有温度为75℃、水量为海砂重量45%的清洗水,此时搅动海砂,利用清洗水对海砂进行冲洗;清洗池上亦设有集气罩,并设有循环水池。洗砂完成后将清洗水送至所述循环水池内,并调节ph为4.0;将步骤(2)中吸收池内吸收完成的氯化亚铁溶液进行蒸发浓缩,然后在温度为70℃条件下,加入亚硝酸钠并通入氧气,反应4h,得到聚合氯化铁溶液。最后向循环水池内投入聚合氯化铁溶液,搅拌均匀,静置后将上清液循环至清洗池内,实现清洗用水的循环利用;(4)脱水:将清洗后的海砂进行脱水处理,除去海砂内多余的水分,得到成品砂。实施例3一种海砂处理工艺,包括以下步骤:(1)筛分:对原砂进行振动筛分,将海砂中的贝壳、砾石等杂质筛去;并对筛分得到的贝壳、砾石等杂质进行破碎,回收作为水泥砖的原料,实现固体废物的回收与资源化利用。(2)脱氯:将过筛后的海砂输送至脱氯池内,浸入脱氯剂中并搅动海砂进行脱氯,脱氯剂采用质量浓度为100mg/l臭氧水溶液,脱氯时间为120min。脱氯池上设有集气罩及吸收池,吸收池内装有废铁屑与10%的氯化氢溶液,废铁屑与氯化氢溶液反应生成氯化亚铁溶液,产生的氯气由集气罩收集并导入吸收池内被氯化亚铁溶液吸收。(3)洗砂:将脱氯后的海砂输送至清洗池内,清洗池内装有温度为90℃、水量为海砂重量60%的清洗水,此时搅动海砂,利用清洗水对海砂进行冲洗;清洗池上亦设有集气罩,并设有循环水池。洗砂完成后将清洗水送至所述循环水池内,并调节ph为5.0;将步骤(2)中吸收池内吸收完成的氯化亚铁溶液进行蒸发浓缩,然后在温度为90℃条件下,加入亚硝酸钠并通入氧气,反应5h,得到聚合氯化铁溶液。最后向循环水池内投入聚合氯化铁溶液,搅拌均匀,静置后将上清液循环至清洗池内,实现清洗用水的循环利用;(4)脱水:将清洗后的海砂进行脱水处理,除去海砂内多余的水分,得到成品砂。实施例4本实施例与实施例2的不同之处在于,脱氯剂的质量浓度为20mg/l。实施例5本实施例与实施例2的不同之处在于,脱氯剂的质量浓度为30mg/l。实施例6本实施例与实施例2的不同之处在于,脱氯剂的质量浓度为40mg/l。实施例7本实施例与实施例2的不同之处在于,脱氯剂的质量浓度为50mg/l。实施例8本实施例与实施例2的不同之处在于,脱氯时间为15min。实施例9本实施例与实施例2的不同之处在于,脱氯时间为30min。实施例10本实施例与实施例2的不同之处在于,脱氯时间为45min。实施例11本实施例与实施例2的不同之处在于,脱氯时间为60min。实施例12本实施例与实施例2的不同之处在于,清洗水量与海砂的重量比为30%。实施例13本实施例与实施例2的不同之处在于,清洗水量与海砂的重量比为40%。实施例14本实施例与实施例2的不同之处在于,清洗水量与海砂的重量比为50%。实施例15本实施例与实施例2的不同之处在于,循环水池内未加入聚合氯化铁溶液。对比例1本实施例与实施例2之间的区别仅在于,本实施例未进行脱氯处理。对比例2本实施例与实施例2之间的区别仅在于,本实施例未进行洗砂处理。实验检测及结果根据我国目前执行的《建设用砂》(gb/t14684-2011)中相关的检验方法及检验标准,建设用砂分为ⅰ、ⅱ、ⅲ三个级别,不同类别建设用砂氯离子含量、含泥量以及泥块含量三项指标的性能参数的含量标准见表1。表1建设用砂各性能参数含量标准类别ⅰⅱⅲ氯离子含量(%)≤0.01≤0.02≤0.06含泥量(%)≤1.0≤3.0≤5.0泥块含量(%)0≤1.0≤2.0本申请选取原砂的氯离子含量为0.185%、含泥量为2.7%及泥块含量为0.3%,对由实施例1~14以及对比例1~2处理得到的成品砂进行取样,并对样品进行上述三项性能参数的检测试验,检测结果见表2。表2海砂性能参数的检测结果项目氯离子含量(%)含泥量(%)泥块含量(%)实施例10.0580.80.2实施例20.00880.20实施例30.00230.10实施例40.0730.20实施例50.0530.20实施例60.0190.20实施例70.0120.20实施例80.0960.20实施例90.0550.20实施例100.0310.20实施例110.0140.20实施例120.0570.30.2实施例130.0280.20.1实施例140.00660.10实施例150.0571.70.2对比例10.1360.20对比例20.0772.50.4由表2可知:1、根据实施例1-3的检测数据可知:随脱氯剂质量浓度升高、脱氯时间的增加以及清洗水量与海砂的重量比增大时,成品砂的氯离子含量逐渐降低。且当臭氧水浓度为65mg/l、脱氯时间为75min、清洗水量与海砂的重量比采用45%时,成品砂中的氯离子含量、含泥量以及泥块含量均可达到建设用砂ⅰ级标准的要求,无需继续增大上述工艺参数即可达到良好的净化效果,节约了资源及成本,并确保了生产效益。2、根据实施例2及实施例4-7的检测数据可知:当臭氧水浓度为20mg/l时,成品砂中氯离子含量超过建设用砂ⅲ级标准中的氯离子含量的要求;当臭氧水浓度增加至30mg/l时,成品砂中氯离子含量可达建设用砂ⅲ级标准中的氯离子含量的要求;当臭氧水浓度增加至50mg/l时,成品砂中氯离子含量可达ⅱ级标准中的氯离子含量的要求;当臭氧水浓度增加至65mg/l时,成品砂的氯离子含量即可达ⅰ级标准中的氯离子含量的要求。因此,工作人员可根据建设用砂所需达到的质量等级,确定相应的臭氧水浓度,防止臭氧水浓度过高造成资源浪费。3、根据实施例2及实施例8-11的检测数据可知:当脱氯时间为15min时,成品砂中氯离子含量超过建设用砂ⅲ级标准中的氯离子含量的要求;当脱氯时间延长至30min时,成品砂中氯离子含量可达建设用砂ⅲ级标准中的氯离子含量的要求;当脱氯时间延长至60min时,成品砂的氯离子含量可达ⅱ级标准中的氯离子含量的要求;当脱氯时间延长至75min,成品砂的氯离子含量即可达ⅰ级标准中的氯离子含量的要求。工作人员可根据建设用砂所需达到的质量等级,确定相应的脱氯时间,防止脱氯时间过长增加处理成本,从而确保了生产效益。4、根据实施例2及实施例12-14的检测数据可知:当清洗水量与海砂的重量比为30%时,成品砂的氯离子含量可达建设用砂的ⅲ级标准中的氯离子含量的要求;当清洗水量与海砂的重量比增加至40%时,成品砂的氯离子含量可达ⅱ级标准中的氯离子含量的要求;当清洗水量与海砂的增加至45%时,成品砂的氯离子含量可达ⅰ级标准中的氯离子含量的要求。工作人员可根据建设用砂所需达到的质量等级,确定相应的清洗水量与海砂的重量比,防止清洗水用量过大造成水资源浪费,并减少了污水的产生量,具有保护环境的效果。成品砂的含泥量及泥块含量均随清洗水量与海砂的重量比的升高而降低,在洗砂的过程中,海砂中的部分泥土被清洗水冲洗分离,以此降低了成品砂的含泥量及泥块含量。且当清洗水量与海砂的重量比为30%时,成品砂的含泥量即可达建设用砂的ⅰ级标准的要求,从而确保了海砂的净化效果。5、根据实施例2及实施例15的检测数据可知:当循环水池内未加入聚合氯化铁时,成品砂中含泥量超过建设用砂ⅰ级标准的要求,因为夹带有泥土的清洗水进入循环水池后,泥土吸附于絮状的聚合氯化铁上,以此降低清洗水的含泥量,进一步降低了成品砂的含泥量。6、根据实施例2及对比例1的检测数据可知:未经脱氯处理的成品砂中氯离子含量超过建设用砂ⅲ级标准中氯离子含量的要求。而在相同用水量的情况下,经脱氯处理的成品砂中氯离子含量可达建设用砂ⅰ级标准中氯离子含量的要求,表明脱氯处理有效的提高了海砂中氯离子的去除率,从而确保了海砂的净化效果。7、根据实施例2及对比例2的检测数据可知:未经洗砂处理的成品砂中氯离子含量超过建设用砂ⅲ级标准的要求,因为海砂经脱氯处理后还残存有氯离子,而洗砂处理有利于成品砂中残存氯离子的去除,从而具有提高海砂净化效果的作用。未经洗砂处理的成品砂中含泥量超过建设用砂ⅰ级标准的要求,因为海砂经脱氯处理后还夹带有少量泥土,洗砂处理有利于泥土的去除,起到降低含泥量的效果。综上所述,脱氯剂的强氧化性将海砂中游离的氯离子氧化为氯气,氯气挥发实现氯离子与海砂的分离,达到脱氯的目的,且随臭氧水浓度升高及脱氯时间的增加,海砂的净化效率提高;利用清洗水对脱氯后的海砂进行冲洗,使海砂内残存的氯离子与部分泥土除去,进一步降低海砂中氯离子的同时降低了含泥量及泥块含量;处理时,根据所需达到建设用砂中的标准要求,确定合适的臭氧水浓度、脱氯时间及清洗水量与海砂重量的比例,高效净化海砂的同时防止了过量用水造成浪费。以上均为本申请的较佳实施例,并非依此限制本申请的保护范围,故:凡依本申请的结构、形状、原理所做的等效变化,均应涵盖于本申请的保护范围之内。当前第1页1 2 3 
起点商标作为专业知识产权交易平台,可以帮助大家解决很多问题,如果大家想要了解更多知产交易信息请点击 【在线咨询】或添加微信 【19522093243】与客服一对一沟通,为大家解决相关问题。
此文章来源于网络,如有侵权,请联系删除



tips