一种用于盐岩路基的注浆材料及其制备方法与流程



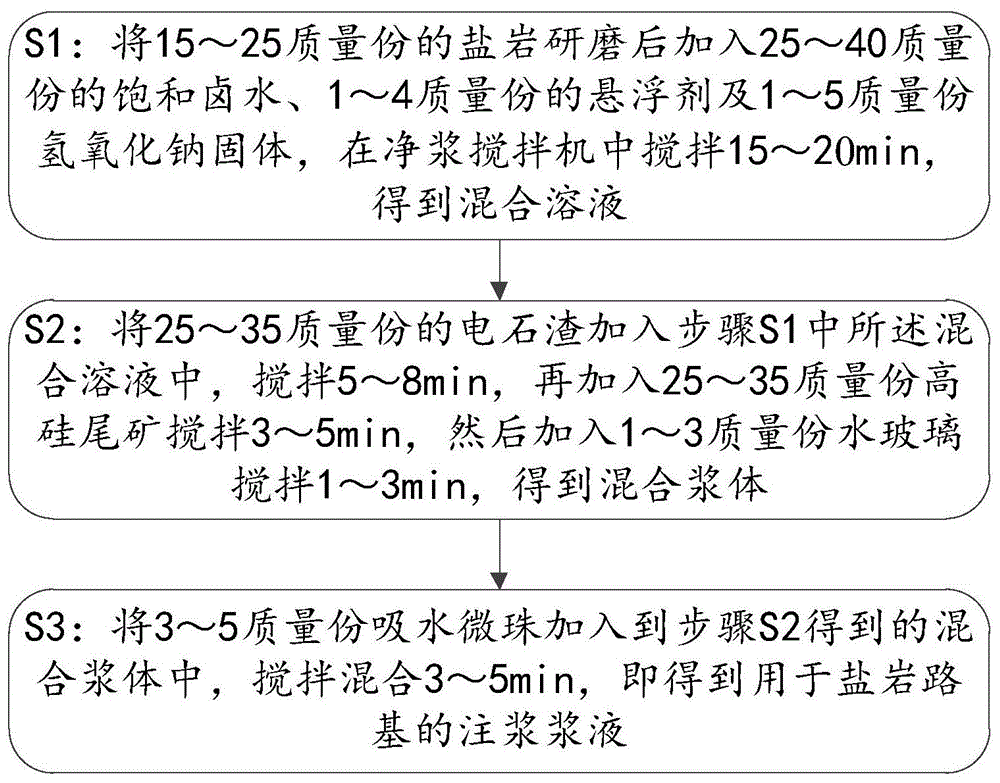
本发明涉及道路工程材料技术领域,尤其涉及一种用于盐岩路基的注浆材料及其制备方法。
背景技术:
注浆加固凭借工艺简单、成本低、开放交通快等优点在道路非开挖维修补强中成为主要的加固补强方法,而注浆材料作为注浆加固中的重要组成部分,其种类和质量将直接影响工程质量及成本。
目前公路领域常见的注浆材料有水泥基注浆材料、高聚物注浆材料、沥青类注浆材料及地聚物注浆材料,而对于部分特殊地区道路出现坑洞及松散等病害时,采取传统注浆材料往往加固补强效果并不理想,尤其是在新疆、青海等干盐湖地区修筑的公路,其部分结构层采用盐岩填筑,若采用水泥基注浆材料容易出现潜在盐胀病害,而其他几类注浆材料又存在处理效果不理想的问题,因此亟需一种与盐岩材料适应性良好且加固补强效果优异的注浆材料,为盐岩道路的养护加固提供技术保障。
技术实现要素:
本发明为了解决上述技术问题提供一种用于盐岩路基的注浆材料及制备方法,以解决盐岩路基盐胀病害及工业废料处置的问题。
本发明为实现上述目的之一提供一种用于盐岩路基的注浆材料。
本发明解决上述技术问题的技术方案如下:一种用于盐岩路基的注浆材料,
所述注浆材料由以下质量份数的组分组成:
盐岩15~25份、高硅尾矿25~35份、电石渣8~15份、饱和卤水25~40份、氢氧化钠1~5份、水玻璃1~3份、吸水微珠3~5份、悬浮剂1~4份。
与现有技术相比,本发明的用于盐岩路基的注浆材料具有以下优势:
1、本发明综合盐岩、饱和卤水、高硅尾矿和电石渣等工业废渣的材料特性,基于盐岩材料及硅铝源物质强度形成机理,不仅能有效保障注浆效果,还能够结合工业废渣的性能优势,在用于盐岩路基加固补强时能够快速形成强度;
2、本发明电石渣中的钙离子与饱和卤水及盐岩中的硫酸根离子进行反应形成硫酸钙沉淀,有效降低溶液中游离的硫酸根离子,消除了注浆后盐岩路基潜在的盐胀病害,同时有利于提升路基整体强度;
3、本发明提供注浆浆液中的电石渣与氢氧化钠能够提供较强的碱性环境,促使高硅尾矿中富含的硅铝源物质与电石渣发生碱激发反应,加入水玻璃后可推进该反应进程,使其能加速促进注浆浆液失水的同时形成强度高、稳定性优良且耐久性优良的碱激发材料,整体激发效果良好,反应充分,有效保障了注浆材料注浆后的前期强度形成,可减少交通封闭时间;
4、本发明结合盐岩强度形成的失水过程及高硅尾矿碱激发反应的水化过程,使得注浆后体系中水分充分参与反应,在保证强度形成的同时避免了失水干缩现象;
5、本发明的吸水微珠的吸水作用可以使浆液能够的自由水含量迅速降低,可加速浆液凝固形成强度。
优选的,上述注浆材料由以下质量份数的组分组成:盐岩18份、高硅尾矿35份、电石渣10份、饱和卤水26份、氢氧化钠3份、水玻璃3份、吸水微珠4份、悬浮剂2份。
采用上述进一步方案的有益效果是:在该组成下,注浆材料具有更好的物化性能。
优选的,上述吸水微珠的直径≤2.0mm,由a组分及包覆于所述a组分外侧的b组分按质量比为1:10~1:20组成;
其中,所述a组分为丙烯酸与2-丙烯酸胺基-2-甲基丙硫磺酸按质量比为4:1~6:1聚合制备而成的丙烯酸聚合物粉末;
所述b组分由以下质量份数的组分组成:环氧树脂e-515~12份、盐岩30~50份、高炉矿渣细粉35~50份和饱和卤水29~37份。
采用上述优选方案的有益效果是:b组分能够对a组分起到防护作用,同时b组分中盐岩能够与饱和卤水离子交换,可以有利于浆液中富余水分侵入吸水微珠的内核,有利于加速浆液的凝固并保证强度。
优选的,上述吸水微珠由以下质量份数的组分组成:
所述吸水微珠由10质量份的a组分和123质量份的b组分组成,其中所述b组分由以下质量份数的组分组成:e-51环氧树脂7份、盐岩40份、高炉矿渣细粉43份和饱和卤水33份。
优选的,上述高硅尾矿为450~600目的细粉,上述盐岩为325~400目的细粉。
优选的,所述电石渣中氢氧化钙含量>85%。
优选的,上述悬浮剂为硅酸镁铝悬浮触变增稠剂。
优选的,上述吸水微珠的直径≤2.0mm。
本发明为实现上述目的之二提供一种用于盐岩路基的注浆材料的制备方法,所述注浆材料通过如下步骤实现:
s1:将15~25质量份的盐岩研磨后加入25~40质量份的饱和卤水、1~4质量份的悬浮剂及1~5质量份氢氧化钠固体,在净浆搅拌机中搅拌15~20min,得到混合溶液;
s2:将25~35质量份的电石渣加入步骤s1中所述混合溶液中,搅拌5~8min,再加入25~35质量份高硅尾矿搅拌3~5min,然后加入1~3质量份水玻璃搅拌1~3min,得到混合浆体;
s3:将3~5质量份吸水微珠加入到步骤s2得到的混合浆体中,搅拌混合3~5min,即得到用于盐岩路基的注浆浆液。
优选的,步骤s3中所述吸水微珠由以下步骤制备得到:
s31:按质量比为4:1~6:1,分别取丙烯酸和2-丙烯酸胺基-2-甲基丙硫磺酸,聚合后,得到丙烯酸聚合物粉末;
取上述丙烯酸聚合物粉末,进行造粒,得到直径0.8~1.0mm的内核a组分;
s32:将35~50质量份的高炉矿渣细粉、30~50质量份的盐岩均研磨至粒径为80~100目,随后加入1~12质量份的环氧树脂e-51、29~37质量份的卤水搅拌混合,得到b组分;
s33:在步骤s31制得的所述a组分的表面喷洒步骤s32制得的所述b组分,固化后,得到直径≤2mm的所述吸水微珠。
优选的,步骤s31中在造粒时进行搅拌,搅拌速率为300~450r/min
本发明采用上述注浆材料制备方法的有益效果是:本发明步骤s1使盐岩失水反应,步骤s2使电石渣以及高硅尾矿水化,步骤s3使富余水保留,有利于保证注浆材料的前期强度,避免失水干缩。
附图说明
图1为本发明用于盐岩路基的注浆材料制备流程图;
图2为本发明吸水微珠制备流程图。
具体实施方式
以下结合附图对本发明的原理和特征进行描述,所举实例只用于解释本发明,并非用于限定本发明的范围。
实施例1
本实施例的用于盐岩路基的注浆材料由以下质量份数制备而成:
盐岩18份、高硅尾矿35份、电石渣10份、饱和卤水26份、氢氧化钠3份、水玻璃3份、吸水微珠3份、悬浮剂2份。
其中吸水微珠由以下质量份数制备而成:a组分丙烯酸聚合物粉末8份;b组分环氧树脂e-517份、盐岩40份、高炉矿渣细粉45份、饱和卤水33份。
上述用于盐岩路基的注浆材料的制备方法,包括如下步骤:
s1:将取上述份数的盐岩研磨至325~400目,加入上述份数的饱和卤水、悬浮剂及氢氧化钠固体,在双转双速净浆搅拌机均匀搅拌15~20min,其搅拌叶公转速度为120±10r/min,自转速度280±10r/min,制备得到混合溶液;
s2:在双转双速净浆搅拌机中将上述份数电石渣加入到上述混合溶液中,继续均匀搅拌5~8min;随后将上述细度为450~600目的高硅尾矿加入混合浆液中均匀搅拌3~5min;最后将上述水玻璃加入混合浆液中搅拌1~3min,制备得到混合浆体;
s3:在双转双速净浆搅拌机中将上述吸水微珠加入到上述混合浆体中均匀搅拌混合3~5min,其搅拌叶公转速度为70±10r/min,自传速度150±10r/min,得到注浆材料。
上述吸水微珠采用以下步骤制备得到:
s31:按质量比5:1,分别取丙烯酸和2-丙烯酸胺基-2-甲基丙硫磺酸,聚合后,得到丙烯酸聚合物粉末;将上述的丙烯酸聚合物粉末加入造粒机中造粒,并在造粒过程中不断搅拌,搅拌速率为300~450r/min,得到直径0.8~1.0mm的a组分;
s32:将上述份数高炉矿渣及盐岩研磨至80~100目,随后加入上述份数环氧树脂e-51和饱和卤水均匀搅拌,得到b组分;
s33:将步骤s31制得的a组分加入制粒包衣机中,将步骤s32制得的b组分喷洒在内核材料的表面形成包衣,待包衣脱水固化后,得到上述要求的吸水微珠,制得直径≤2.0mm的吸水微珠。
性能测试:
1、将上述配方及方法制得的注浆材料倒入尺寸40×40×160mm的模具中,在胶砂振实台上振实,并用刮板刮平,放入标准养护箱分别养护3d(天)和7d(天),测量抗压强度和抗折强度。
2、将上述配方制及方法制得的注浆材料按《混凝土外加剂应用技术规范》(gb50119-2013)中的方法进行胶浆流动度试验,分别测10s、1800s后相互垂直的两个方向的最大直径,试验结果取平均值;
3、将上述配方制及方法制得的注浆材料按《公路桥涵施工技术规范》(jtg_tf50-2011)中附录c4中自由膨胀率试验方法对注浆材料的自由膨胀率进行试验;
4、将上述配方制及方法制得的注浆材料按《公路工程无机结合料稳定材料试验规程》(jtge51-2009)中的方法对注浆材料进行冻融试验,测量五次冻融后膨胀率;
5、将上述配方制及方法制得的注浆材料《水泥标准用水量、凝结时间、安定性检测》(gbt-2011)中的相关规定对注浆材料进行初凝、终凝时间的测定。
测试结果为:3d(天)抗压强度5.6mpa,7d(天)抗压强度14.7mpa,3d(天)抗折强度1.3mpa,7d(天)抗压强度2.7mpa,10s流动性31.7cm,1800s流动性23.9cm,初凝时间215min,终凝时间249min,自由膨胀率0.18%,五次冻融1.3%。
实施例2
本实施例的用于盐岩路基的注浆材料由以下质量份数制备而成:
盐岩20份、高硅尾矿30份、电石渣8份、饱和卤水30份、氢氧化钠3份、水玻璃1份、吸水微珠4份、悬浮剂4份。
其中吸水微珠由以下质量份数制备而成:a组分丙烯酸聚合物粉末5份;b组分环氧树脂e-515份、盐岩50份、高炉矿渣细粉40份、饱和卤水33份。
本实施例注浆材料的制备方法与实施例1相同。
本实施例注浆材料的性能测试方法与实施例1中性能测试方法相同。
测试结果为:3d(天)抗压强度4.7mpa,7d(天)抗压强度12.3mpa,3d(天)抗折强度1.1mpa,7d(天)抗压强度2.1mpa,10s流动性32.9cm,1800s流动性24.8cm,初凝时间242min,终凝时间277min,自由膨胀率0.31%,五次冻融1.7%。
实施例3
本实施例的用于盐岩路基的注浆材料由以下质量份数制备而成:
盐岩17份、高硅尾矿25份、电石渣10份、饱和卤水40份、氢氧化钠3份、水玻璃1份、吸水微珠3份、悬浮剂1份。
其中吸水微珠由以下质量份数制备而成:a组分丙烯酸聚合物粉末10份;b组分环氧树脂e-517份、盐岩40份、高炉矿渣细粉43份、饱和卤水33份。
本实施例注浆材料的制备方法与实施例1相同。
本实施例注浆材料的性能测试方法与实施例1中性能测试方法相同。
测试结果为:3d(天)抗压强度4.1mpa,7d(天)抗压强度10.3mpa,3d(天)抗折强度0.8mpa,7d(天)抗压强度1.7mpa,10s流动性37.5cm,1800s流动性30.1cm,初凝时间309min,终凝时间343min,自由膨胀率0.19%,五次冻融1.3%。
实施例4
本实施例的用于盐岩路基的注浆材料由以下质量份数制备而成:
盐岩25份、高硅尾矿25份、电石渣15份、饱和卤水25份、氢氧化钠1份、水玻璃2份、吸水微珠5份、悬浮剂2份。
其中吸水微珠由以下质量份数制备而成:a组分丙烯酸聚合物粉末8份;b组分环氧树脂e-5112份、盐岩30份、高炉矿渣细粉50份、饱和卤水33份。
本实施例注浆材料的制备方法与实施例1相同。
本实施例注浆材料的性能测试方法与实施例1中性能测试方法相同。
测试结果为:3d(天)抗压强度5.1mpa,7d(天)抗压强度12.5mpa,3d(天)抗折强度1.3mpa,7d(天)抗压强度2.4mpa,10s流动性29.5cm,1800s流动性23.6cm,初凝时间209min,终凝时间241min,自由膨胀率0.2%,五次冻融1.2%。
实施例5
本实施例的用于盐岩路基的注浆材料由以下质量份数制备而成:
盐岩15份、高硅尾矿25份、电石渣14份、饱和卤水35份、氢氧化钠5份、水玻璃1份、吸水微珠3份、悬浮剂2份。
其中吸水微珠由以下质量份数制备而成:a组分丙烯酸聚合物粉末10份;b组分环氧树脂e-515份、盐岩50份、高炉矿渣细粉35份、饱和卤水33份。
本实施例注浆材料的制备方法与实施例1相同。
本实施例注浆材料的性能测试方法与实施例1中性能测试方法相同。
测试结果为:3d(天)抗压强度4.5mpa,7d(天)抗压强度10.9mpa,3d(天)抗折强度1.0mpa,7d(天)抗压强度1.9mpa,10s流动性34.6cm,1800s流动性27.7cm,初凝时间311min,终凝时间349min,自由膨胀率0.21%,五次冻融1.3%。
对比例1
本实施例的用于盐岩路基的注浆材料由以下质量份数制备而成:
盐岩20份、高硅尾矿35份、电石渣8份、饱和卤水30份、吸水微珠4份、悬浮剂3份。
其中吸水微珠由以下质量份数制备而成:a组分丙烯酸聚合物粉末10份;b组分环氧树脂e-517份、盐岩40份、高炉矿渣细粉43份、饱和卤水33份。
上述用于盐岩路基的注浆材料的制备方法,包括如下步骤:
s1:将取上述份数盐岩研磨至325~400目,并加入上述份数的饱和卤水和悬浮剂,在双转双速净浆搅拌机均匀搅拌15~20min,其搅拌叶公转速度为120±10r/min,自转速度280±10r/min,制备得到混合溶液;
s2:在双转双速净浆搅拌机中将上述份数电石渣加入到上述混合溶液中,继续均匀搅拌5~8min;随后将上述细度为450~600目的高硅尾矿加入混合浆液中均匀搅拌3~5min,制备得到混合浆体;
s3:在双转双速净浆搅拌机中将上述吸水微珠加入到上述混合浆体中均匀搅拌混合3~5min,其搅拌叶公转速度为70±10r/min,自传速度150±10r/min,得到注浆材料。
上述吸水微珠采用以下步骤制备得到:
s31:将上述丙烯酸聚合物粉末加入造粒机中造粒,并在造粒过程中不断搅拌,搅拌速率为300~450r/min,得到直径0.8~1.0mm的内核材料;
s32:将上述高炉矿渣及盐岩研磨至80~100目,随后加入环氧树脂e-51和饱和卤水均匀搅拌,得到混合浆体;
s33:将步骤s31制得的内核材料加入制粒包衣机中,将步骤s32制得的混合浆体喷洒在内核材料的表面形成包衣,待包衣脱水固化后,得到上述要求的吸水微珠,制得的吸水微珠的直径≤2.0mm。
本实施例注浆材料的性能测试方法与实施例1中性能测试方法相同。
测试结果为:3d(天)抗压强度3.5mpa,7d(天)抗压强度8.8mpa,3d(天)抗折强度0.5mpa,7d(天)抗压强度1.2mpa,10s流动性30.9cm,1800s流动性25.1cm,初凝时间337min,终凝时间382min,自由膨胀率0.20%,五次冻融1.6%。
对比例2
本实施例的用于盐岩路基的注浆材料由以下质量份数制备而成:
盐岩52份、饱和卤水30份、氢氧化钠5份、吸水微珠5份、悬浮剂5份。
其中吸水微珠由以下质量份数制备而成:a组分丙烯酸聚合物粉末8份;b组分环氧树脂e-517份、盐岩35份、高炉矿渣细粉50份、饱和卤水33份。
上述用于盐岩路基的注浆材料的制备方法,包括如下步骤:
s1:将取上述份数盐岩研磨至325~400目,并加入上述份数的饱和卤水、悬浮剂及氢氧化钠固体,在双转双速净浆搅拌机均匀搅拌15~20min,其搅拌叶公转速度为120±10r/min,自转速度280±10r/min,制备得到混合溶液;
s2:上述水玻璃加入混合浆液中搅拌1~3min,制备得到混合浆体;
s3:在双转双速净浆搅拌机中将上述吸水微珠加入到上述混合浆体中均匀搅拌混合3~5min,其搅拌叶公转速度为70±10r/min,自传速度150±10r/min,得到注浆材料。
上述吸水微珠采用以下步骤制备得到:
s31:将上述丙烯酸聚合物粉末加入造粒机中造粒,并在造粒过程中不断搅拌,搅拌速率为300~450r/min,得到直径0.8~1.0mm的内核材料;
s32:将上述高炉矿渣及盐岩研磨至80~100目,随后加入环氧树脂e-51和饱和卤水均匀搅拌,得到混合浆体;
s33:将步骤s31制得的内核材料加入制粒包衣机中,将步骤s32制得的混合浆体喷洒在内核材料的表面形成包衣,待包衣脱水固化后,得到上述要求的吸水微珠,制得的吸水微珠的直径≤2.0mm。
本实施例注浆材料的性能测试方法与实施例1中性能测试方法相同。
测试结果为:3d(天)抗压强度1.2mpa,7d(天)抗压强度4.3mpa,3d(天)抗折强度0.3mpa,7d(天)抗压强度0.9mpa,10s流动性40.3cm,1800s流动性35.4cm,初凝时间359min,终凝时间391min,自由膨胀率0.93%,五次冻融3.7%。
对比例3
本实施例的用于盐岩路基的注浆材料由以下质量份数制备而成:
盐岩25份、高硅尾矿35份、电石渣15份、饱和卤水25份。
其中吸水微珠由以下质量份数制备而成:a组分丙烯酸聚合物粉末8份;b组分环氧树脂e-517份、盐岩40份、高炉矿渣细粉45份、饱和卤水33份。
上述用于盐岩路基的注浆材料的制备方法,包括如下步骤:
s1:将取上述份数盐岩研磨至325~400目,并加入上述份数的饱和卤水,在双转双速净浆搅拌机均匀搅拌15~20min,其搅拌叶公转速度为120±10r/min,自转速度280±10r/min,制备得到混合溶液;
s2:在双转双速净浆搅拌机中将上述份数电石渣加入到上述混合溶液中,继续均匀搅拌5~8min;随后将上述细度为450~600目的高硅尾矿加入混合浆液中均匀搅拌3~5min,制备得到注浆材料。
本实施例注浆材料的性能测试方法与实施例1中性能测试方法相同。
测试结果为:3d(天)抗压强度3.1mpa,7d(天)抗压强度11.6mpa,3d(天)抗折强度0.4mpa,7d(天)抗压强度1.9mpa,10s流动性26.6cm,1800s流动性19.5cm,初凝时间265min,终凝时间302min,自由膨胀率0.33%,五次冻融1.9%。
实验结果表明,实施例中养护3d和7d的强度指标均优于对比例的强度指标,尤其是实施例1制得的注浆材料优于其他实施例以及对比例,表现出较好的强度特性,表明通过本发明提供的原料配比和制备步骤制得的铸件材料,能够实现盐岩强度形成条件及高硅尾矿活性硅铝活化条件的互补,能够满足盐岩路基注浆加固的要求。
以上所述仅为本发明的较佳实施例,并不用以限制本发明,凡在本发明的精神和原则之内,所作的任何修改、等同替换、改进等,均应包含在本发明的保护范围之内。
起点商标作为专业知识产权交易平台,可以帮助大家解决很多问题,如果大家想要了解更多知产交易信息请点击 【在线咨询】或添加微信 【19522093243】与客服一对一沟通,为大家解决相关问题。
此文章来源于网络,如有侵权,请联系删除


