高产量高效能的活性炭活化装置及活化工艺的制作方法



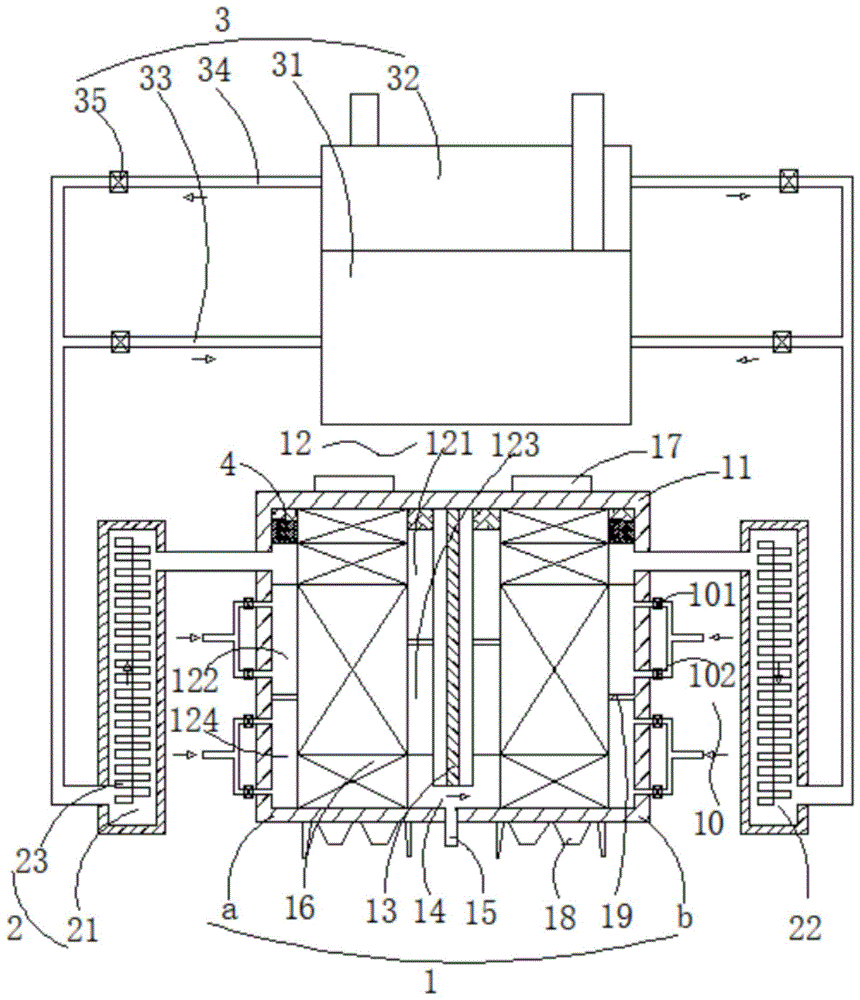
本发明涉及煤基活性炭生产技术领域,具体地涉及一种高产量高效能的活性炭活化装置及活化工艺。
背景技术:
斯列普活化炉是从前苏联引进的砖结构鞍式活化炉,采用水蒸气与烟道气交流活化方法,适用于各种粒状活性炭的生产。活化工艺条件稳定,产品质量均匀,吸附性能好,尤其在高品质活性炭生产方面具有十分独特的优势。
传统的活性炭生产所需的蒸汽动力,是利用燃煤蒸汽锅炉或燃气蒸汽锅炉生产来实现。随着动力能源的使用受限和价格持续走高,尤其是环境保护要求的不断提升和产品能耗的严格限制,传统设施条件下耗能高、效能低、污染大的缺陷日益凸显。因此,活化尾气余热和炭化尾气余热的循环利用成为活性炭生产企业的首选途径,即将活化(炭化)尾气通过焚烧炉净化燃烧并带动活化(炭化)余热锅炉产生蒸汽回用于活性炭生产。
但是在实际生产中,由于传统活化工艺产量低,产生的活化尾气带动余热锅炉生产蒸汽量,无法满足活化炉耗用的蒸汽量,不足蒸汽量只能通过炭化余热锅炉或外接蒸汽源来补充,导致活性炭生产成本居高不下,整体运营效益差。之所以造成活化余热锅炉产气量低、运行效果不佳的一个主要原因,是活化炉在传统工艺条件下,活化速率受活化温度的影响。温度低导致活化速率低,也就导致产量低,活化料投放量也因此降低,投放量又限定了活化尾气的产出量和尾气的热焓值,最终影响蒸汽的生成量,形成一个无法自给自足的循环。所以,想要提升活化余热锅炉的运行效能,实现活化炉生产耗费蒸汽与尾气余热生产蒸汽的平衡,就必须打破原有传统工艺,突破活化炉传统活化温度的极限。
但是,通过提升温度提高活化炉效能的同时,高温会加重活化炉的负担,炉芯砖局部高温容易导致产品道堵死、烧蹋炉芯砖等炉体恶性事故的发生。并且易造成炭烧失率增加问题的产生。因此,活化炉的原结构及工艺控制是制约活化工艺温度提升的主要原因。
技术实现要素:
本发明要解决的技术问题在于,提供一种高产量高效能的活性炭活化装置及活化工艺,通过对活性炭活化装置进行结构重新设计,使得活化工艺突破温度极限,增加活性炭活化速率,提升活化余热锅炉的运行效能,实现活化炉生产耗费蒸汽与尾气余热生产蒸汽的平衡。
一种高产量高效能的活性炭活化装置,包括炉体、蓄热室和蒸汽锅炉,其中:
所述炉体包括炉墙,在炉墙内形成炉膛,炉墙内侧设有侧烟道,所述炉膛正中间由隔离墙将炉体分为左半炉a和右半炉b,左半炉a和右半炉b的下部通过下连烟道连通并设有第一配风口,左半炉a和右半炉b内分别设有炉芯;所述炉芯内设有若干个互相不相通的活化槽,每个活化槽顶部有一个加料槽,活化槽底部设有出料仓;所述侧烟道被盖板砖分为上近烟道、上远烟道、下近烟道及下远烟道,上近烟道、上远烟道、下近烟道及下远烟道上分别设有第二配风口,所述第二配风口包括上配风口和下配风口,在上配风口和下配风口上分别设有阀门;
所述蓄热室包括左蓄热室和右蓄热室,左蓄热室通过上连烟道与左半炉a连通,右蓄热室通过上连烟道与右半炉b连通;
所述蒸汽锅炉包括燃烧室和蒸汽室,左蓄热室和右蓄热室分别通过烟气管道与燃烧室连通,左蓄热室和右蓄热室分别通过蒸汽管道与蒸汽室连通。
优选的,左半炉a和右半炉b自上而下均分成四个区段,分别为加料预热段、补充炭化段、活化段和出料冷却段。并适当增加活化段的砖层数。
优选的,所述炉墙包括外墙和内墙,外墙由红砖砌筑,内墙用耐火粘土砖砌筑,内墙与外墙之间充填硅酸铝纤维毡隔热保温;所述隔离墙用耐火粘土砖砌筑;所述炉芯由异型耐火粘土砖砌筑。
优选的,所述蓄热室通过耐火砖砌成,在蓄热室腔内有耐火砖叠成的蓄热格子,并设有活化剂通道。
优选的,所述左半炉与右半炉内分别设有尾气回注装置,所述尾气回注装置设于活化剂通入一侧,且尾气回注装置与下连烟道连通。
一种高产量高效能的活性炭活化工艺,将炭化料加入加料槽,炭化料在活化槽内自上而下依次经过加料预热段、补充炭化段、活化段和出料冷却段进行活化,最终冷却后的活化料经出料仓输出,所述活化处理的步骤为:
(1)首先以左半炉为活化半炉,以右半炉为加热半炉,打开左蓄热室蒸汽管道、右蓄热室烟气管道、右半炉的配风口阀门及左半炉尾气回注装置入口阀门,关闭左蓄热室烟气管道、右蓄热室蒸汽管道、左半炉的配风口阀门及右半炉尾气回注装置入口阀门,蒸汽室或分汽缸内的预热水蒸气从蒸汽管道进入左蓄热室,待进入炉内的蒸汽压力稳定后,可根据炉压情况开启左侧尾气回注装置阀门;预热水蒸气伴部分活化尾气在左蓄热室内经加热形成过热混合蒸汽,然后该过热混合蒸气通过上连烟道进入左半炉,过热混合蒸气在左半炉内与炉内炭料进行活化反应,活化后的气体经过左半炉底部进入下连烟道,然后再从底部进入右半炉,右半炉的烟道配风口通入氧气助燃,部分烟气燃烧为右半炉升温,剩余活化气体介质从上连烟道进入右蓄热室,然后进入燃烧室经过燃烧,最终从烟囱排出;
(2)30分钟后,进行活化炉的换相操作,以右半炉为活化半炉,以左半炉为加热半炉,打开右蓄热室蒸汽管道、左蓄热室烟气管道、左半炉的配风口阀门及右半炉尾气回注装置入口阀门,关闭右蓄热室烟气管道、左蓄热室蒸汽管道、右半炉的配风口阀门及右半炉尾气回注装置入口阀门,蒸汽室或分汽缸内的预热水蒸气从蒸汽管道进入右蓄热室,待进入炉内的蒸汽压力稳定后,可根据炉压情况开启右侧尾气回注装置阀门;预热水蒸气伴部分活化尾气在右蓄热室内经加热形成过热混合蒸汽,然后该过热混合蒸气通过上连烟道进入右半炉,过热混合蒸气在右半炉内与炭化料进行活化反应,活化后的气体经过右半炉底部进入下连烟道,然后再从底部进入左半炉,此时左半炉的配风口通入氧气助燃,部分烟气燃烧为左半炉升温,剩余活化气体介质从上连烟道进入左蓄热室,然后进入燃烧室经过燃烧,最终从烟囱排出;
燃烧室燃烧产生的热能通过蒸汽余热锅炉热交换生产蒸汽再回用于生产;
(3)30分钟后,进行活化炉的换相操作,重复步骤(1)和步骤(2)的操作。
优选的,所述过热蒸气温度为950~1100℃,入炉蒸汽压力为3.0~3.5kg/cm2;活化半炉的炉压为100~120pa,加热半炉的炉压为70~100pa;烟道抽力为-150pa。在执行上述工艺参数时,为避免发生炉体事故,加热半炉的烟道上配风口阀门要予关闭。
活化装置各部分的作用。预热段:活化预热段是起到将投炉的炭化料缓慢升温,防止温度骤然提升造成炭化料内的挥发成分和预应力快速释放造成炭化料表面爆裂的作用。预热段要装入足够的炭化料,防止炉内烟气向上运动;补充炭化段:是起到将炭化料中的多余挥发成分析出的作用。此时,炭化料与活化剂不直接接触,靠高温气流加热异型砖而将热量辐射给炭化料,达到补充炭化的目的;活化段:补充炭化后的炭化料随产品道下落至活化段,与活化剂直接接触,活化剂通过气道扩散渗入炭层中,与炭发生一系列氧化还原化学反应,将炭的原始空隙打通。使炭形成发达的孔隙结构和巨大的比表面积;冷却段:经活化的炭料不再与炉气接触,进入炭料逐渐降温冷却阶段。避免卸出炉外的炭料在高温下与空气中的氧气发生继续发生反应或引起燃烧,影响炭的质量和活化得率;蓄热室:蓄热室是通过较强蓄热能力,将进入炉内的水蒸气进一步加热提温。蓄热室可充分利用活化炉的热能,进行正常蓄热和加热。无需外部补充热能。它的作用有两个,一是储存热能。由于加热半炉中可燃气体与空气中的氧气燃烧放出大量的热,载热气体在通过蓄热室时与其中的耐火砖进行热交换时,耐火砖获得热能而起到储存热能的作用;二是利用储存的热能加热活化剂,饱和蒸汽从蓄热室底部加入,由下而上通过格子砖进行热交换达到顶部时,温度可达950~1100℃,这个过程是蒸汽(活化剂)进一步获得热量的过程,然后将高温活化剂供给给活化半炉中参与反应。
本发明的原理:
1、本发明的高产量高效能的活性炭活化装置,是在传统斯列普活化炉原结构上进行两项特殊改造。一是适当增加活化带的炉芯砖层数,延长活化段。这种改造是为了增加炉中料与活化媒介的接触时间,从而起到提升活化速率的目的。二是在活化剂通道入活化炉侧内置尾气回注装置。该装置通过高压蒸汽将部分外排活化废气回注活化炉,既可起到降低活化炉蒸汽用量,还改变了炉内活化剂的组分,增加了炉内二氧化碳等氧化剂的浓度。对活化速率的提升起助力作用。另外,活化炉的工艺操作也是一个不可忽略的要点。活化炉的上近烟道、上远烟道、下近烟道及下远烟道上分别设有第二配风口,所述第二配风口包括上配风口和下配风口,在上配风口和下配风口上分别设有阀门。在正常工艺条件下,可以选择使用上配风口和下配风口进行送风,当需要提升温度的时候,必须关闭上配风口的配风阀门,仅使用下配风口送风。因为,上配风口进入的空气,容易悬浮在侧烟道的上方,不易与烟道烟气混合燃烧,增加了进入炉芯水平气道的氧含量,导致炭烧失率的增加,同时,过量氧与炭的直接接触燃烧,会产生炉芯砖的局部高温,增加产品道堵塞、炉芯烧蹋等恶性事故的发生几率,危及活化炉的运行安全,而下配风口配进的空气,能较好的与烟道的烟气融合并燃烧,降低了烟气中的氧含量,减缓了炭烧失率的增加,并抑制了产品道堵塞及炉芯烧蹋等恶性事故的发生。
2、本发明的高产量高效能的活性炭活化工艺,将活化温度由传统工艺的900~950℃提升至950~1100℃,将入炉蒸汽压力从传统工艺的2kg/cm2提高到3~3.5kg/cm2,将传统活化半炉的炉压为80~100pa,加热半炉的炉压为40~60pa,增加为活化半炉的炉压为100~120pa,加热半炉的炉压为70~100pa;烟道抽力由传统工艺的-130pa提升为-150pa。基于对活化装置结构的设置,实现活化温度提升至950~1100℃,在活化带温度提升后,炭与水蒸气反应速度加快,促使炭的活化速率提升。但提温状态下入炉蒸汽量要增加,蒸汽压力控制在3~3.5kg/cm2,产量增幅效果最佳。开启活化尾气回注装置,将部分活化尾气与蒸汽混合,可增加活化剂的组分,有利于活化剂与炭的反应。提升炉内炭的活化速率。同时还能缓解入炉蒸汽压力低导致炉压低的问题。还起到节省活化使用的蒸汽量。炉压需控制在合理的区间,否则会出现大量可燃气体从炉下部卸料口喷出燃烧,加剧出炉活性炭的表面烧蚀。影响活性炭的物料消耗和质量。并且损伤炉子的密闭性,影响其使用寿命。活化炉抽力是使炉内产生的烟气在炉内得以循环运动,并将多余的尾气及时排出,提升炉内气体循环速度,可为活化速率提升创造有利条件。
本发明的有益效果:
1、明显提升活化炉的产量:以336型斯普列活化炉为例,传统运行工艺技术,4.0/60炭的日产量4吨;采用新装置及新工艺技术,4.0/60炭的日产量5.5~6.0吨,产量提升37%以上;
2、明显提升炉内炭的活化深度:以336型斯普列活化炉为例,传统运行工艺技术,ctc>70%以上的活性炭,一般要采用两次活化;采用新装置及新工艺技术,70%<ctc<100%的活性炭,均可一次性活化,且指标控制均匀;
3、活性炭品质优良,活化炉运行稳定:在保证炭化料的挥发分不高于8%,并严格监控活化炉顶部料仓料面是否均匀下降,对各下料器的下料量定期称重(一周不得少于一次),对出现的蓬料、产品道阻塞等问题及时进行处理,则可保活化炉长期稳定运行;
4、提升活化余热锅炉的运行效能,实现活化炉生产耗费蒸汽与尾气余热生产蒸汽的平衡:以336型斯普列活化炉为例,传统运行工艺技术,两台同产品道活化炉的尾气通过焚烧炉产生的热能使余热锅炉生产的蒸汽量最多能够满足两台活化炉活化用汽的三分之二,不足蒸汽要靠炭化尾气余热锅炉补充;采用新活化运行工艺技术,两台同产品道活化炉的尾气通过焚烧炉产生的热能使余热锅炉生产的蒸汽量不仅满足两台活化炉用汽,而且为炭化生产用汽以及生活用汽提供热能。
附图说明
图1为本发明高产量高效能的活性炭活化装置的结构示意图。
图中:炉体1、炉墙11、侧烟道12、上近烟道121、上远烟道122、下近烟道123、下远烟道124、隔离墙13、左半炉a、右半炉b、下连烟道14、第一配风口15、炉芯16、加料槽17、出料仓18、被盖板砖19、第二配风口10、上配风口101、下配风口102、蓄热室2、左蓄热室21、右蓄热室22、蓄热格子23、蒸汽锅炉3、燃烧室31、蒸汽室32、烟气管道33、蒸汽管道34、尾气回注装置4。
具体实施方式
一种高产量高效能的活性炭活化装置,包括炉体1、蓄热室2和蒸汽锅炉3,其中:
所述炉体1包括炉墙11,在炉墙11内形成炉膛,炉墙11内侧设有侧烟道12,所述炉膛正中间由隔离墙13将炉体1分为左半炉a和右半炉b,左半炉a和右半炉b的下部通过下连烟道14连通并设有第一配风口15,左半炉a和右半炉b内分别设有炉芯16;所述炉芯16内设有若干个互相不相通的活化槽,每个活化槽顶部有一个加料槽17,活化槽底部设有出料仓18;所述侧烟道12被盖板砖19分为上近烟道121、上远烟道122、下近烟道123及下远烟道124,上近烟道121、上远烟道122、下近烟道123及下远烟道124上分别设有第二配风口10,所述第二配风口10包括上配风口101和下配风口102,在上配风口101和下配风口102上分别设有阀门;
所述蓄热室2包括左蓄热室21和右蓄热室22,左蓄热室21通过上连烟道与左半炉a连通,右蓄热室22通过上连烟道与右半炉b连通;
所述蒸汽锅炉3包括燃烧室31和蒸汽室32,左蓄热室21和右蓄热室22分别通过烟气管道33与燃烧室31连通,左蓄热室21和右蓄热室22分别通过蒸汽管道34与蒸汽室32连通。
左半炉a和右半炉b自上而下均分成四个区段,分别为加料预热段、补充炭化段、活化段和出料冷却段。
所述炉墙11包括外墙和内墙,外墙由红砖砌筑,内墙用耐火粘土砖砌筑,内墙与外墙之间充填硅酸铝纤维毡隔热保温;所述隔离墙13用耐火粘土砖砌筑;所述炉芯16由异型耐火粘土砖砌筑。
所述蓄热室2通过耐火砖砌成,在蓄热室2腔内有耐火砖叠成的蓄热格子23,并设有活化剂通道。
所述左半炉a与右半炉b内分别设有尾气回注装置4,所述尾气回注装置4设于活化剂通入一侧,且尾气回注装置4与下连烟道14连通。
一种高产量、高效能的活性炭活化工艺,是对原斯列普炉活化炉部分设施改进后所创新的并与之相匹配的活化运行新工艺技术。活化炉的生产过程简述为:将炭化料加入活化炉顶部的加料槽内,炭化料在活化槽内顺产品道自上而下依次经过加料预热段、补充炭化段、活化段和出料冷却段进行活化,最终冷却后的活化料经出料仓输出,所述活化处理的步骤为:
(1)首先以左半炉为活化半炉,以右半炉为加热半炉,打开左蓄热室蒸汽管道、右蓄热室烟气管道、右半炉的配风口阀门及左半炉尾气回注装置入口阀门,关闭左蓄热室烟气管道、右蓄热室蒸汽管道、左半炉的配风口阀门及右半炉尾气回注装置入口阀门,蒸汽室或分汽缸内的预热水蒸气从蒸汽管道进入左蓄热室,待进入炉内的蒸汽压力稳定后,可根据炉压情况开启左侧尾气回注装置阀门;预热水蒸气伴部分活化尾气在左蓄热室内经加热形成过热混合蒸汽,然后该过热混合蒸气通过上连烟道进入左半炉,过热混合蒸气在左半炉内与炉内炭料进行活化反应,活化后的气体经过左半炉底部进入下连烟道,然后再从底部进入右半炉,右半炉的烟道配风口通入氧气助燃,部分烟气燃烧为右半炉升温,剩余活化气体介质从上连烟道进入右蓄热室,然后进入燃烧室经过燃烧,最终从烟囱排出;
(2)30分钟后,进行活化炉的换相操作,以右半炉为活化半炉,以左半炉为加热半炉,打开右蓄热室蒸汽管道、左蓄热室烟气管道、左半炉的配风口阀门及右半炉尾气回注装置入口阀门,关闭右蓄热室烟气管道、左蓄热室蒸汽管道、右半炉的配风口阀门及右半炉尾气回注装置入口阀门,蒸汽室或分汽缸内的预热水蒸气从蒸汽管道进入右蓄热室,待进入炉内的蒸汽压力稳定后,可根据炉压情况开启右侧尾气回注装置阀门;预热水蒸气伴部分活化尾气在右蓄热室内经加热形成过热混合蒸汽,然后该过热混合蒸气通过上连烟道进入右半炉,过热混合蒸气在右半炉内与炭化料进行活化反应,活化后的气体经过右半炉底部进入下连烟道,然后再从底部进入左半炉,此时左半炉的配风口通入氧气助燃,部分烟气燃烧为左半炉升温,剩余活化气体介质从上连烟道进入左蓄热室,然后进入燃烧室经过燃烧,最终从烟囱排出;
燃烧室燃烧产生的热能通过蒸汽余热锅炉热交换生产蒸汽再回用于生产;
(3)30分钟后,进行活化炉的换相操作,重复步骤(1)和步骤(2)的操作。
所述过热蒸气温度为950~1100℃,入炉蒸汽压力为3.0~3.5kg/cm2;活化半炉的炉压为100~120pa,加热半炉的炉压为70~100pa;烟道抽力为-150pa,在执行上述工艺参数时,为避免发生炉体事故,加热半炉的烟道上配风口阀门要予关闭。
应当注意,在此所述的实施例仅为本发明的部分实施例,而非本发明的全部实现方式,所述实施例只有示例性,其作用只在于提供理解本发明内容更为直观明了的方式,而不是对本发明所述技术方案的限制。在不脱离本发明构思的前提下,所有本领域普通技术人员没有做出创造性劳动就能想到的其它实施方式,及其它对本发明技术方案的简单替换和各种变化,都属于本发明的保护范围。
起点商标作为专业知识产权交易平台,可以帮助大家解决很多问题,如果大家想要了解更多知产交易信息请点击 【在线咨询】或添加微信 【19522093243】与客服一对一沟通,为大家解决相关问题。
此文章来源于网络,如有侵权,请联系删除


