一种千瓦级燃料电池硼氢化钠水解制氢装置的制作方法



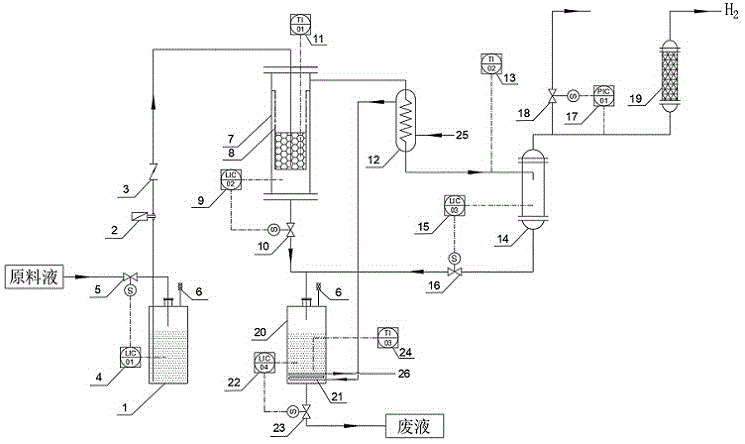
本实用新型属于氢气制备技术领域,尤其提供一种可连续运行的千瓦级燃料电池硼氢化钠水解制氢装置。
背景技术:
质子交换膜燃料电池是通过电化学反应将储存在燃料中的化学能直接转换为电能的发电装置,其具有能量密度高、能量转化效率高、环境友好等诸多优点,是新能源汽车、可移动电子设备、无人机以及通讯基站等优选的动力来源。要实现燃料电池的规模化应用,高密度的储存和快速安全的提供纯净氢气是目前急需解决的一个重要问题。
目前氢燃料的供给主要有物理储氢和化学制氢两种方式。物理储氢方法主要包括高压气态储氢和低温液态储氢两种。其中,高压气态储氢使用方便,应用范围广,但是其体积能量密度低;低温液态储氢能量密度高,但系统复杂,成本较高。化学制氢主要包括烃类水蒸气转化制氢、甲醇重整制氢、电解水制氢和无机氢化物水解制氢。其中,烃类水蒸气转化法和甲醇重整法制氢在工业中应用广泛,但制备的氢气中含有一定量的co杂质,必须经过净化后才能使用,而且这两种方法制氢设备复杂,难于小型化;电解水制氢得到的氢气纯度非常高,但该法制氢成本高、耗电量大,暂时无法大规模推广;无机氢化物水解制氢作为一种小型制氢方法,非常适合应用于便携式小功率燃料电池。
无机氢化物主要包括碱金属和碱土金属氢化物、硼氢化物和铝氢化物,其中,采用硼氢化钠水解制氢是目前比较热门的现场制氢技术,其优点主要有:(1)制氢效率高。硼氢化钠本身含氢量高达10.8wt%,在催化剂的催化作用下放氢完全,可达90%以上。(2)氢气纯度较高。硼氢化钠水解产生的氢气中不含co,无需经过复杂的净化处理。(3)反应条件温和,速率可控。硼氢化钠水解反应在室温即可进行,通过控制硼氢化钠溶液的浓度以及进料流量,就可以方便的控制产氢速率。(4)安全性高。硼氢化钠在干燥空气中性质稳定,储运方便,其碱性溶液非常稳定,不会发生自水解。
截止目前,硼氢化钠制氢反应装置的公开文件中(如cn103253631a、cn106744678b、cn203238030u、cn203402923u、cn203741035u等),部分装置中反应原料液是自上而下或自下而上通过涂覆在床层上的催化剂的,这使得原料液与催化剂接触时间短且不充分,容易造成反应不完全或者产氢速率低。部分制氢装置为间歇式进料,无法连续产氢。此外,硼氢化钠溶液水解反应产生的氢气中会夹带naoh和nabo2等碱性杂质,如果进入燃料电池会对电池的性能和寿命产生较大影响,因此硼氢化钠水解制取的氢气必须经过充分净化后才能供给燃料电池,现有技术中并未解决这一问题。
技术实现要素:
本实用新型的目的在于提供一种千瓦级燃料电池硼氢化钠水解制氢装置,该装置可以实现连续制氢,反应转化率高,制备的氢气经过充分净化,可以直接供给燃料电池使用。
本实用新型是这样实现的:
一种千瓦级燃料电池硼氢化钠水解制氢装置,包括反应单元,所述反应单元包括反应器和催化剂提篮,所述反应器顶端设有进料管、底部设有第一废液管、顶部侧面设有氢气出气管,所述反应器上设有测反应温度的一号温度显示器,所述催化剂提篮设置在反应器内,包括桶形底部,设置在桶形底部上方的网状筒体,及设置在网状筒体上方用于与反应器相接的挂耳;所述进料管向下延伸至催化剂提篮底部。
详细的说,所述反应器上设有二号高/低液位指示表,所述第一废液管上设有与二号高/低液位指示表联锁的二号电磁阀。
进一步的,还包括进料单元,所述进料单元包括原料液储罐,所述原料液储罐顶端设有补液管,所述进料管活动端置于原料液储罐中,进料管上设有进料泵和单向阀。
进一步的,还包括废液排放单元,所述废液排放单元包括废液储罐,所述废液储罐与反应器底部的第一废液管相连,废液储罐底部设有第三废液管。
进一步的,还包括换热单元,所述换热单元包括冷凝器和换热盘管,所述冷凝器设液体的进口和出口、气体的进口和出口;所述换热盘管设置在废液储罐内,并与冷凝器上液体的出口相连;冷凝器上液体的进口连接冷却水源、气体的进口连接氢气出气管,冷凝器的气体出口管道上设有测冷却后气体温度的二号温度显示表(13)。
进一步的,还包括分离净化单元,所述分离净化单元包括气液分离器和干燥除碱罐,所述气液分离器与冷凝器的气体出口管道连接,气液分离器底部设有第二废液管,顶部设有气体出口,气体出口通过管道与干燥除碱罐连接。
详细的说,还包括与气液分离器相连的干燥除碱罐,二者的连接管道上设有压力显示表。
详细的说,所述气液分离器上与干燥除碱罐连接的管道上设有泄压管,泄压管上设有与压力显示表联锁的安全阀。
作为一种优选方案,所述原料液储罐上设有一号高/低液位指示表,原料液储罐的补液管上设有与一号高/低液位指示表联锁的一号电磁阀;所述废液储罐上设有四号高/低液位指示表,废液储罐底部的第三废液管设有与四号高/低液位指示表联锁的四号电磁阀,废液储罐上设有测冷却后废液温度的三号温度显示器。
本实用新型的有益效果是:
(1)本实用新型的制氢装置产氢速率稳定,反应充分。原料液在进入反应器后自催化剂提篮筒形底部逐渐上升,至网状筒体后排出提篮,原料液停留时间充足,可以与催化剂充分接触并反应,反应转化率可达85%以上。
(2)本实用新型的制氢装置自动化程度高。通过高低液位指示表与电磁阀的联锁,可以自动控制原料液的补液和废液的排放,补给和排放过程无需停机,制氢可以连续进行,大大提高了制氢效率。
(3)本实用新型的制氢装置制氢速率可调。制氢速率可以通过改变原料液中硼氢化钠的浓度以及进料泵的进料速率非常方便的进行控制,适用于几十瓦至几千瓦不同功率的燃料电池。
(4)本实用新型的制氢装置制备的氢气纯度高。通过冷凝器和气液分离器可以分离大部分氢气中携带的水蒸汽和naoh、nabo2等碱性杂质,通过干燥除碱罐可以进一步对氢气进行干燥和除碱净化,净化后的氢气可以直接供给燃料电池使用。
(5)本实用新型的制氢装置使用安全。通过温度显示表可以对反应区温度、冷却后氢气温度和冷却后废液温度实时监测,随时掌握反应情况,装置中设置了安全阀,当系统压力达到高限时,安全阀自动打开泄放压力,防止系统超压造成危险。
附图说明
为了更清楚地说明本实用新型实施方式的技术方案,下面将对实施方式中所需要使用的附图作简单地介绍,应当理解,以下附图仅示出了本实用新型的某些实施例,因此不应被看作是对范围的限定,对于本领域普通技术人员来讲,在不付出创造性劳动的前提下,还可以根据这些附图获得其他相关的附图。
图1是本实用新型-千瓦级燃料电池硼氢化钠水解制氢装置的示意图;
图2是本实用新型催化剂提篮的结构示意图。
图标:
1-原料液储罐,2-进料泵,3-单向阀,4-一号高/低液位指示表,5-一号电磁阀,6-放空阀,7-反应器,8-催化剂提篮,9-二号高/低液位指示表,10-二号电磁阀,11-一号温度显示表,12-冷凝器,13-二号温度显示表,14-气液分离器,15-三号高/低液位指示表,16-三号电磁阀,17-压力显示表,18-安全阀,19-干燥除碱罐,20-废液储罐,21-换热盘管,22-四号高/低液位指示表,23-四号电磁阀,24-三号温度显示表,25-冷却水进口,26-冷却水出口,27-实心底面,28-实心侧壁,29-网孔侧壁,30网孔盖子,31-挂耳。
具体实施方式
为使本实用新型实施方式的目的、技术方案和优点更加清楚,下面将结合本实用新型实施方式中的附图,对本实用新型实施方式中的技术方案进行清楚、完整地描述,显然,所描述的实施方式是本实用新型一部分实施方式,而不是全部的实施方式。基于本实用新型中的实施方式,本领域普通技术人员在没有作出创造性劳动前提下所获得的所有其他实施方式,都属于本实用新型保护的范围。
因此,以下对在附图中提供的本实用新型的实施方式的详细描述并非旨在限制要求保护的本实用新型的范围,而是仅仅表示本实用新型的选定实施方式。基于本实用新型中的实施方式,本领域普通技术人员在没有作出创造性劳动前提下所获得的所有其他实施方式,都属于本实用新型保护的范围。
在本实用新型的描述中,需要理解的是,指示方位或位置关系的术语为基于附图所示的方位或位置关系,仅是为了便于描述本实用新型和简化描述,而不是指示或暗示所指的设备或元件必须具有特定的方位、以特定的方位构造和操作,因此不能理解为对本实用新型的限制。
在本实用新型中,除非另有明确的规定和限定,术语“安装”、“相连”、“连接”、“固定”等术语应做广义理解,例如,可以是固定连接,也可以是可拆卸连接,或成一体;可以是机械连接,也可以是电连接;可以是直接相连,也可以通过中间媒介间接相连,可以是两个元件内部的连通或两个元件的相互作用关系。对于本领域的普通技术人员而言,可以根据具体情况理解上述术语在本实用新型中的具体含义。
在本实用新型的描述中,需要说明的是,术语“中心”、“上”、“下”、“左”、“右”、“竖直”、“水平”、“内”、“外”等指示的方位或位置关系为基于附图所示的方位或位置关系,或者是该实用新型产品使用时惯常摆放的方位或位置关系,仅是为了便于描述本实用新型和简化描述,而不是指示或暗示所指的装置或元件必须具有特定的方位、以特定的方位构造和操作,因此不能理解为对本实用新型的限制。此外,术语“第一”、“第二”、“第三”等仅用于区分描述,而不能理解为指示或暗示相对重要性。
此外,术语“水平”、“竖直”、“悬垂”等术语并不表示要求部件绝对水平或悬垂,而是可以稍微倾斜。如“水平”仅仅是指其方向相对“竖直”而言更加水平,并不是表示该结构一定要完全水平,而是可以稍微倾斜。
在本实用新型中,除非另有明确的规定和限定,第一特征在第二特征之上或之下可以包括第一和第二特征直接接触,也可以包括第一和第二特征不是直接接触而是通过它们之间的另外的特征接触。而且,第一特征在第二特征之上、上方和上面包括第一特征在第二特征正上方和斜上方,或仅仅表示第一特征水平高度高于第二特征。第一特征在第二特征之下、下方和下面包括第一特征在第二特征正下方和斜下方,或仅仅表示第一特征水平高度小于第二特征。
本实施例的千瓦级燃料电池硼氢化钠水解制氢装置的结构如图1所示。该装置由进料单元、反应单元、换热单元、分离净化单元和废液排放单元组成。进料单元包括原料液储罐1和进料泵2;反应单元包括反应器7和催化剂提篮8;换热单元包括冷凝器12和换热盘管21;分离净化单元包括气液分离器14和干燥除碱罐19;废液排放单元包括废液储罐20。
详细的说,所述原料液储罐1通过管道与进料泵2连接,进料泵2通过管道接入反应器7,原料液通过进料泵2输送至反应器7中催化剂提篮8的底部;进料泵2和反应器7之间的管路上设置单向阀3,防止流体倒流;原料液储罐内设置有一号高/低液位指示表4,一号高/低液位指示表4与一号电磁阀5联锁,能够自动将原料液输送入原料液储罐;原料液储罐顶部设计放空阀6,防止罐内负压。
所述反应器7顶端用法兰密封;反应器7底部设置二号高/低液位指示表9,二号高/低液位指示表9与二号电磁阀10联锁,能够自动将反应器底部的废液排至废液储罐20;反应器7顶部侧面设计氢气出口,氢气出口通过管道连接冷凝器12;反应器7中接入一号温度显示表11,用于指示反应区温度;催化剂提篮8放置在反应器7内部用于盛装催化剂,催化剂提篮8能够直接从反应器7内取出,方便催化剂的更换。
如图2所示,催化剂提篮8包括实心底面27,实心侧壁28,网孔侧壁29,网孔盖子30和挂耳31,实心底面和实心侧壁形成桶状底部,网孔侧壁和网孔盖子形成网状筒体。所述实心底面27和实心侧壁28使得反应液在催化剂提篮8中有足够停留时间与催化剂充分反应,网孔侧壁使得充分反应后的原料液自网孔溢出并进入反应器7的底部,网孔盖子用于固定催化剂同时使得反应生成的氢气通过,挂耳31用于将催化剂提篮8固定在反应器7中。
冷凝器12通过外部冷却水将氢气中携带的水蒸汽和溶液雾滴冷却为液相状态,冷却后的氢气通过管道进入气液分离器14,冷凝器和气液分离器之间的管路上接入二号温度显示表13,用于指示冷却后的氢气温度;换热盘管设计在废液储罐底部,通过外部冷却水带走废液热量。
气液分离器14底部设置三号高/低液位指示表15,三号高/低液位指示表15与三号电磁阀16联锁,能够自动将气液分离器14底部的液体排至废液储罐20;气液分离器14顶部设计氢气出口,氢气出口通过管道连接干燥除碱罐;氢气出口和干燥除碱罐之间的管路上设置有压力显示表17,压力显示表17与安全阀18联锁,当管路内压力达到高限时,安全阀18自动打开泄放系统压力;干燥除碱罐19上、下端采用法兰密封,干燥除碱罐19内装填干燥剂和除碱剂,用于对氢气进一步进行干燥和除碱净化处理;法兰上设计网孔挡板,用于固定干燥剂和除碱剂;干燥除碱罐19顶部设计纯净氢气出口,供燃料电池使用。
所述废液储罐20内设置有四号高/低液位指示表22,四号高/低液位指示表22与四号电磁阀23联锁,能够自动排放废液;废液储罐20顶部设计放空阀6,防止罐内正压;废液储罐中接入三号温度显示表24,用于指示冷却后的废液温度。
原料液为硼氢化钠和氢氧化钠的混合溶液,溶液呈碱性可以抑制硼氢化钠的自水解反应;催化剂可以是担载型贵金属催化剂、担载型非贵金属催化剂或担载型非金属催化剂中的一种或几种;外部冷却水从冷却水进口25进入,依次经过冷凝器和换热盘管,然后从冷却水出口26流出;干燥除碱罐中的干燥剂可以是分子筛、海绵、无水氯化钙、变色硅胶、棉花、活性炭等的一种或几种的混合物;除碱剂可以是分子筛、杂多酸、硼酸、阳离子交换树脂等的一种或几种的混合物;干燥剂置于除碱剂之前或干燥剂置于除碱剂前后。
本装置各部分均采用耐碱腐蚀的材质,如不锈钢或聚四氟乙烯。
本装置的使用流程如下:
装置在制氢前,首先由外部向原料液储罐1中补充原料液,当原料液液位达到一号高/低液位指示表4的高液位时,一号电磁阀5关闭,停止补液;装填好催化剂提篮8中的催化剂和干燥除碱罐19中的干燥剂和除碱剂,拧紧法兰。
装置在制氢时,打开外部冷却水,冷却水自冷却水进口25进入,通过冷凝器12和换热盘管21,自冷却水出口26流出,设定进料泵2的流速后启动。进料泵将原料液储罐中的原料液输送至反应器7中催化剂提篮8底部,原料液与催化剂接触后发生反应开始制氢,催化剂提篮的实心底面27和实心侧壁28使得反应液在催化剂提篮中有足够停留时间充分反应,原料液液位达到催化剂提篮的网孔侧壁29时,充分反应后的原料液自网孔溢出并进入反应器的底部。反应器中废液液位达到二号高/低液位指示表9的高液位时,二号电磁阀10开启,反应器底部的废液排至废液储罐20;废液液位降至二号高/低液位指示表的低液位时,二号电磁阀关闭,停止排液。一号温度显示表11指示反应区的温度。
反应产生的氢气自催化剂提篮的网孔盖子30进入反应器顶部,通过管道进入冷凝器12,氢气中携带的水蒸汽和溶液雾滴被冷却为液相状态,二号温度显示表13指示冷却后的氢气温度。冷却后的氢气进入气液分离器14,在气液分离器中,经过分离后液体进入气液分离器的底部,当气液分离器中废液液位达到三号高/低液位指示表15的高液位时,三号电磁阀16开启,气液分离器底部的废液排至废液储罐20;废液液位降至三号高低液位指示表的低液位时,三号电磁阀关闭,停止排液。经过分离后的气体进入气液分离器顶部,通过管道进入干燥除碱罐,进一步进行干燥和除碱净化处理,经过净化后的氢气供燃料电池使用。
原料液储罐中原料液液位降至一号高/低液位指示表的低液位时,一号电磁阀开启,进行补液。废液储罐中废液液位达到四号高/低液位指示表22的高液位时,四号电磁阀23开启,废液储罐中的废液向外排放;废液液位降至四号高/低液位指示表的低液位时,四号电磁阀关闭,停止排液。三号温度显示表24指示冷却后的废液温度。气液分离器和干燥除碱罐之间的管路中设置了安全阀,当压力显示表17探测到管路内压力达到高限时,安全阀18自动打开泄放压力,防止系统超压造成危险。
为了更好的检测本装置的效果,特进行了试验,参见以下实例:
实例1
根据图1组装装置,装置整体采用不锈钢材质,原料液采用5wt%硼氢化钠+2wt%氢氧化钠溶液,催化剂采用担载型非贵金属催化剂,干燥剂和除碱剂分别采用变色硅胶和分子筛,变色硅胶置于分子筛之前,设置进料泵的流速为60ml/min。
测试发现,进料2min后产氢速率达到稳定,产氢速率为6.3l/min,可以为功率为500w的燃料电池持续供氢。连续稳定产氢150min后,计算得硼氢化钠产氢转化率为93%,将装置产生的氢气通入一定量的去离子水中,去离子水的ph没有发生变化,说明制备的氢气得到了充分净化。
实例2
根据图1组装装置,装置整体采用不锈钢材质,原料液采用10wt%硼氢化钠+4wt%氢氧化钠溶液,催化剂采用担载型非贵金属催化剂,干燥剂和除碱剂分别采用分子筛和硼酸,分子筛置于硼酸前后,设置进料泵的流速为50ml/min。
测试发现,进料3min后产氢速率达到稳定,产氢速率为11.5l/min,可以为功率为1000w的燃料电池持续供氢。连续稳定产氢150min后,计算得硼氢化钠产氢转化率为89%,将装置产生的氢气通入一定量的去离子水中,去离子水的ph没有发生变化,说明制备的氢气得到了充分净化。
实例3
根据图1组装装置,装置整体采用不锈钢材质,原料液采用15wt%硼氢化钠+4wt%氢氧化钠溶液,催化剂采用担载型非贵金属催化剂,干燥剂和除碱剂分别采用变色硅胶和杂多酸,变色硅胶置于杂多酸前后,设置进料泵的流速为60ml/min。
测试发现,进料6min后产氢速率达到稳定,产氢速率为21.0l/min,可以为功率为2000w的燃料电池持续供氢。连续稳定产氢120min后,计算得硼氢化钠产氢转化率为86%,将装置产生的氢气通入一定量的去离子水中,去离子水的ph没有发生变化,说明制备的氢气得到了充分净化。
可见,本实施例装置解决了目前硼氢化钠水解制氢装置制氢时反应不完全或产氢速率低、产氢不连续以及氢气未经充分净化的技术问题,实现了连续制氢,反应转化率高;制备的氢气经过充分净化,可以直接供给燃料电池使用。
以上所述仅为本实用新型的优选实施方式而已,并不用于限制本实用新型,对于本领域的技术人员来说,本实用新型可以有各种更改和变化。凡在本实用新型的精神和原则之内,所作的任何修改、等同替换、改进等,均应包含在本实用新型的保护范围之内。
起点商标作为专业知识产权交易平台,可以帮助大家解决很多问题,如果大家想要了解更多知产交易信息请点击 【在线咨询】或添加微信 【19522093243】与客服一对一沟通,为大家解决相关问题。
此文章来源于网络,如有侵权,请联系删除


