一种化合物的集成式加工装置的制作方法



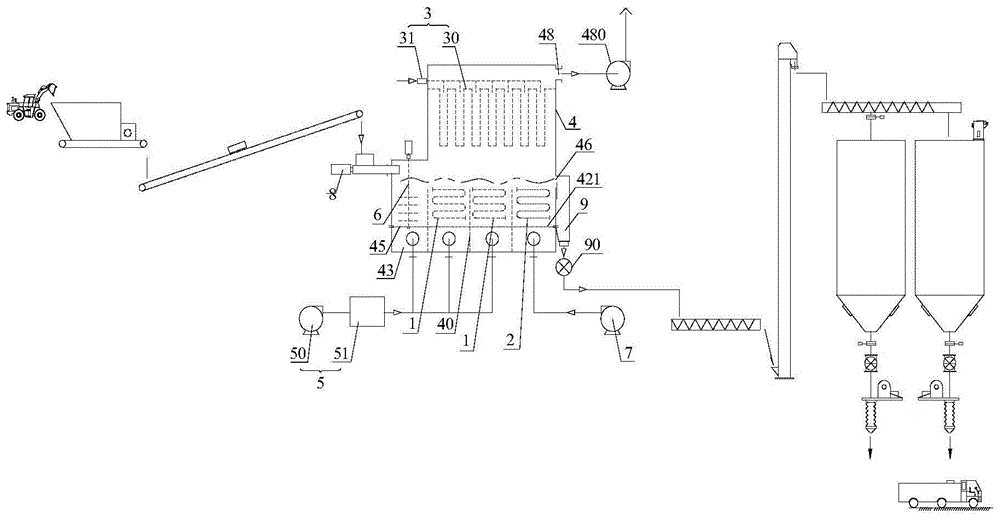
本实用新型涉及化合物加工技术领域,尤其是涉及一种化合物的集成式加工装置。
背景技术:
半水石膏是石膏行业各种石膏制品的主要原料。为了制得半水石膏(分子式为caso4·1/2h2o),通常是将二水石膏(分子式为caso4·2h2o)进行煅烧加工处理,就是通过高温使二水石膏分子式当中的两个结晶水脱去1.5个,从而形成半水石膏。而二水石膏是通过对石膏原料(石膏原料中通常含有5%-30%的游离水)进行干燥脱水得到的。
因此,在利用含有游离水的石膏原料制造半水石膏时,通常需要进行以下几个工序:干燥脱去游离水、煅烧脱去结晶水、冷却、以及附属的除尘和物料输送。
现有的一种用于生产半水石膏等需要脱水的化合物的工艺为气流+流化床两步法工艺,该工艺第一步采用气流干燥工艺,第二步采用埋管流化床煅烧工艺。利用该工艺加工出半水石膏后,还需在熟化料仓中对温度较高的半水石膏进行冷却。在气流干燥过程中、埋管流化床煅烧过程中和冷却过程中,需要分别增设除尘设备以对上述三个过程中产生的粉尘进行除尘。但是在利用气流+流化床两步法工艺加工半水石膏等需要脱水的化合物时,为实现整个生产过程,一条生产线上需要设置大量机器(约50台以上机器),导致操作过程和维修过程均较繁琐。
为了减少设备数量以及节省能源,生产半水石膏等需要脱水的化合物时还可以采用设备成本高于气流+流化床两步法工艺两倍到三倍的蒸汽回转工艺。蒸汽回转工艺利用蒸汽换热装置可以在煅烧窑中将游离水含量低于15%的石膏等化合物原料直接脱水加工成半水石膏等化合物成品。利用冷却机可以对煅烧窑中出来的温度较高的半水石膏等化合物成品进行冷却。其中,部分蒸汽产生的蒸汽冷凝水会进入到蒸汽换热装置中,进而可以节省能源。但是利用蒸汽回转工艺生产半水石膏等需要脱水的化合物时,煅烧窑处和冷却机处也需要分别增设除尘设备以对加工过程中产生的粉尘进行除尘,因此在利用蒸汽回转工艺生产半水石膏等需要脱水的化合物时,为实现整个生产过程,一条生产线上仍旧需要设置多台机器(约40台以上机器)。
因此,在利用气流+流化床两步法工艺或者蒸汽回转工艺生产半水石膏等需要脱水的化合物时,由于脱水工序和冷却工序由不同的设备分别完成,因而脱水工序中和冷却工序中需分别设置除尘设备,导致生产半水石膏等需要脱水的化合物的生产线上需要设置多台机器,使得生产过程中的操作和后期维修保养过程均需要投入很大的人力物力。
技术实现要素:
本实用新型的目的在于提供一种化合物的集成式加工装置,以缓解现有技术中存在的利用气流+流化床两步法工艺或者蒸汽回转工艺生产半水石膏等需要脱水的化合物时,由于脱水工序和冷却工序由不同的设备分别完成,因而脱水工序中和冷却工序中需分别设置除尘设备,导致生产半水石膏等需要脱水的化合物的生产线上需要设置多台机器,使得生产过程中的操作和后期维修保养过程均需要投入很大的人力物力的技术问题。
本实用新型提供的一种化合物的集成式加工装置包括加热模块、制冷模块、除尘组件和壳体;
壳体的内部包括除尘空间和加工空间;壳体的加工空间内设置有至少一个隔板,隔板用于在壳体的加工空间内划分出煅烧室和冷却室;
加热模块设置在煅烧室处,用于对进入煅烧室内的物料加热,以使煅烧室内的物料脱水;制冷模块设置在冷却室内,用于对进入冷却室内的物料降温;
除尘组件安装在壳体的除尘空间内,用于对壳体内的粉尘进行除尘。
进一步的,隔板为多个,多个隔板间隔设置在壳体的加工空间中,以将壳体的加工空间划分出至少三个腔室;
至少三个腔室中包括至少一个干燥室、至少一个煅烧室和至少一个冷却室;煅烧室位于干燥室和冷却室之间;
干燥室处连接有干燥模块,干燥模块用于加快干燥室内的物料中的水分蒸发。
进一步的,干燥模块为热风组件;
干燥室上和煅烧室上均设置有热风口,干燥室上的热风口和煅烧室上的热风口分别与干燥模块连通;
干燥模块用于向干燥室供送热风,以将干燥室内的物料吹送至煅烧室内,以及向煅烧室供送热风,以将煅烧室内的物料吹送至冷却室内。
进一步的,干燥室内和煅烧室内均安装有第一布风板,第一布风板上设置有均匀分布的多个通风孔,第一布风板能够支撑物料;
干燥室上的热风口设置在干燥室的低于第一布风板的位置处;煅烧室上的热风口设置在煅烧室的低于第一布风板的位置处。
进一步的,一种化合物的集成式加工装置还包括打散组件,打散组件设置在干燥室中,用于打散干燥室内的物料。
进一步的,打散组件包括驱动件、打散轴和打散翅片;
打散翅片安装在打散轴上,打散轴和打散翅片均位于干燥室内;
驱动件安装在壳体上并与打散轴连接,驱动件用于驱动打散轴自转,以带动打散翅片以打散轴为转轴转动。
进一步的,干燥室的侧壁远离煅烧室的部分为半圆柱形。
进一步的,隔板可拆卸安装在壳体的底面的内侧壁上,隔板的顶端与壳体的底面之间的间距可调节。
进一步的,冷却室的远离煅烧室的一侧设置有出料口;
一种化合物的集成式加工装置还包括吹风组件,冷却室上低于出料口的位置处设置有冷风口,冷风口与吹风组件连通;
吹风组件用于向冷却室供送气体,以将冷却室内的物料吹送至出料口处。
进一步的,冷却室内靠近底部的位置处安装有第二布风板,第二布风板上设置有均匀分布的多个通风孔,第二布风板能够支撑物料;
冷却室上的冷风口位于冷却室的侧壁上,且位于冷却室的底部和第二布风板之间。
进一步的,出料口处设置有料位调节板,料位调节板用于从出料口的底边至顶边遮挡部分出料口。
进一步的,壳体的除尘空间处的两侧的侧壁上分别设置有进风口和出风口;
除尘组件包括滤袋和空气压缩机;滤袋安装在壳体的除尘空间处的内壁上,并位于煅烧室和冷却室的上方,滤袋用于收集壳体内的粉尘;
空气压缩机安装在壳体上,且空气压缩机上的喷嘴安装在滤袋上方,并与进风口连通。
本实用新型提供的一种化合物的集成式加工装置能产生如下有益效果:
本实用新型提供的化合物的集成式加工装置包括加热模块、制冷模块、除尘组件和壳体。壳体的内部包括除尘空间和加工空间。壳体的加工空间内设置有至少一个隔板,隔板用于在壳体的加工空间内划分出煅烧室和冷却室。加热模块设置在煅烧室处。制冷模块设置在冷却室内。除尘组件安装在壳体的除尘空间内。在利用本实用新型提供的化合物的集成式加工装置生产半水石膏等需要脱水的化合物时,可以先将含有游离水或者结晶水的化合物物料送至煅烧室中,利用加热模块在煅烧室内对物料进行脱水工序。在脱水工序中将上述物料加热脱水至所需状态后,即,在煅烧室中将物料加热脱水得到半水石膏等所需化合物后,再将带有较高温度的半水石膏等所需化合物输送至冷却室中,以对半水石膏等所需化合物进行冷却工序。冷却工序是利用冷却室内的制冷模块将半水石膏等所需化合物降温至一定温度。
与现有技术相比,本实用新型提供的化合物的集成式加工装置中的煅烧室和冷却室均在一个壳体内,即,脱水工序和冷却工序均在一个壳体内进行,因而脱水工序中产生的粉尘和冷却工序中产生的粉尘均可以被壳体内的除尘组件除去,而不需针对脱水工序和冷却工序分别设置一个除尘组件。本实用新型提供的化合物的集成式加工装置将脱水工序、冷却工序和除尘工序整合在一个壳体内进行,能够简化半水石膏等化合物的生产过程,以及可以减少除尘设备的数量,进而可以降低生产过程中的操作和后期维修保养过程中投入的人力和物力。
附图说明
为了更清楚地说明本实用新型具体实施方式或现有技术中的技术方案,下面将对具体实施方式或现有技术描述中所需要使用的附图作简单地介绍,显而易见地,下面描述中的附图是本实用新型的一些实施方式,对于本领域普通技术人员来讲,在不付出创造性劳动的前提下,还可以根据这些附图获得其他的附图。
图1为本实用新型实施例提供的化合物的集成式加工装置的结构示意图;
图2为图1中的干燥室、煅烧室、冷却室、除尘组件和壳体的结构示意图;
图3为图2中的干燥室、煅烧室和冷却室的俯视图;
图4为图2中的加热模块的结构示意图。
图标:1-加热模块;2-制冷模块;3-除尘组件;30-滤袋;31-空气压缩机;4-壳体;40-隔板;41-煅烧室;42-冷却室;420-冷风口;421-第二布风板;422-料位调节板;43-干燥室;44-热风口;45-第一布风板;46-出料口;47-进风口;48-出风口;480-引风机;49-进料口;5-热风组件;50-鼓风机;51-加热器;6-打散组件;60-驱动件;61-打散轴;62-打散翅片;7-吹风组件;8-进料机构;9-出料机构;90-出料阀。
具体实施方式
下面将结合实施例对本实用新型的技术方案进行清楚、完整地描述,显然,所描述的实施例是本实用新型一部分实施例,而不是全部的实施例。基于本实用新型中的实施例,本领域普通技术人员在没有做出创造性劳动前提下所获得的所有其他实施例,都属于本实用新型保护的范围。
实施例:
如图1-图3所示,本实施例提供的化合物的集成式加工装置包括加热模块1、制冷模块2、除尘组件3和壳体4。壳体4的内部包括除尘空间和加工空间。如图2所示,壳体4的加工空间内设置有至少一个隔板40,隔板40用于在壳体4的加工空间内划分出煅烧室41和冷却室42。加热模块1设置在煅烧室41处,用于对进入煅烧室41内的物料加热,以使煅烧室41内的物料脱水。制冷模块2设置在冷却室42内,用于对进入冷却室42内的物料降温。除尘组件3安装在壳体4的除尘空间内,用于对壳体4内的粉尘进行除尘。
在利用本实施例提供的化合物的集成式加工装置生产半水石膏等需要脱水的化合物时,可以先将含有游离水或者结晶水的化合物物料送至煅烧室41中,利用加热模块1在煅烧室41内对物料进行脱水工序。在脱水工序中将上述物料加热脱水至所需状态后,即,在煅烧室41中将物料加热脱水得到半水石膏等所需化合物后,再将带有较高温度的半水石膏等所需化合物输送至冷却室42中,以对半水石膏等所需化合物进行冷却工序。冷却工序是利用冷却室42内的制冷模块2将半水石膏等所需化合物降温至一定温度。
如图4所示,加热模块1可以为换热器,换热器的热源采用蒸汽或者导热油等热媒。
在现有的气流+流化床两步法工艺中,埋管流化床煅烧工艺是将内置热管沸腾床作为埋管流化床,并在内置热管中通入热烟气,利用热烟气与物料换热实现对物料的煅烧。但是热烟气与物料之间的换热系数较低,单位面积热量传递少,不仅能耗高且煅烧效率低。而本实施例提供的加热模块1的热源采用蒸汽或者导热油等热媒,相较于热烟气换热系数更高,煅烧效率更高。
进一步的,换热器可拆卸安装在煅烧室41内。可拆卸安装的安装方式可以降低换热器的维修难度与成本,进而可以延长该化合物的集成式加工装置的使用寿命。
其中,制冷模块2可以为冷却器,冷却器内可以通入冷冻水等冷媒。冷却器内的冷媒可以将带有较高温度的半水石膏冷却到要求的温度。
进一步的,冷却器可拆卸安装在冷却室42内。可拆卸安装的安装方式可以降低冷却器的维修难度与成本,可以进一步的延长该化合物的集成式加工装置的使用寿命。
与现有技术相比,本实施例提供的化合物的集成式加工装置中的煅烧室41和冷却室42均在一个壳体4内,即,脱水工序和冷却工序均在一个壳体4内进行,因而脱水工序中产生的粉尘和冷却工序中产生的粉尘均可以被壳体4内的除尘组件3除去,而不需针对脱水工序和冷却工序分别设置一个除尘组件3。本实施例提供的化合物的集成式加工装置将脱水工序、冷却工序和除尘工序整合在一个壳体4内进行,能够简化半水石膏等化合物的生产过程,以及可以减少除尘设备的数量,进而可以降低生产过程中的操作和后期维修保养过程中投入的人力和物力。
可以看出,本实施例提供的化合物的集成式加工装置缓解了现有技术中存在的利用气流+流化床两步法工艺或者蒸汽回转工艺生产半水石膏等需要脱水的化合物时,由于脱水工序和冷却工序由不同的设备分别完成,因而脱水工序中和冷却工序中需分别设置除尘设备,导致生产半水石膏等需要脱水的化合物的生产线上需要设置多台机器,使得生产过程中的操作和后期维修保养过程均需要投入很大的人力物力的技术问题。
如图2所示,隔板40为多个,多个隔板40间隔设置在壳体4的加工空间中,以将壳体4的加工空间划分出至少三个腔室。至少三个腔室中包括至少一个干燥室43、至少一个煅烧室41和至少一个冷却室42。煅烧室41位于干燥室43和冷却室42之间。干燥室43处连接有干燥模块,干燥模块用于加快干燥室43内的物料中的水分蒸发。
现有的蒸汽回转工艺是将干燥煅烧集中在煅烧窑中进行,若干燥煅烧集中进行过程中,石膏原料等化合物中的游离水含量高于15%,则会使得石膏原料等化合物在煅烧窑内部粘壁,降低半水石膏的产品品质。因而在煅烧石膏原料等化合物之前,对石膏原料等化合物进行干燥降低游离水的含量,可以有效防止石膏原料等化合物在煅烧阶段粘壁。
以生产半水石膏,物料为石膏原料为例,在利用本实施例提供的化合物的集成式加工装置生产半水石膏时,可以先将石膏原料投入干燥室43中,利用干燥模块加快石膏原料中的水分蒸发,脱去石膏原料中的部分游离水。将石膏原料中的游离水含量降低后,再将石膏原料送入煅烧室41中,利用加热模块1将石膏原料中的结晶水脱去,使得石膏原料被煅烧成半水石膏。制成半水石膏后,再将带有较高温度的半水石膏送至冷却室42中,在制冷模块2的作用下,半水石膏的温度降低,继而可以将半水石膏送出至包装处或者储存处。
可以看出,干燥室43和干燥模块用于对石膏原料中的游离水进行脱水,使得石膏原料中的游离水含量降低,进而便于对石膏原料进行下一步的煅烧过程。
此外,由于干燥室43、煅烧室41和冷却室42均位于壳体4内的加工空间中,因而在石膏原料的干燥、煅烧过程中以及在半水石膏的降温过程中,壳体4内的除尘空间中的除尘组件3可以一直处于工作状态,将上述三个过程中产生的粉尘除去。
相较于现有的半水石膏生产过程,本实施例提供的化合物的集成式加工装置将干燥、煅烧、冷却、除尘功能集中于一个壳体内,不仅可以减少石膏生产线上机器的数量,还可以减少石膏生产线中机器的占地面积,有效降低了投资成本,使得操作和维修过程均易于进行,降低了运行费用和维修费用。
如图2所示,煅烧室41可以为多个,多个煅烧室41依次分布,且多个煅烧室41均位于干燥室43和冷却室42之间。其中,每个煅烧室41中均设置有加热模块1,根据产能不同,一个煅烧室41内可以设置有多个加热模块1。在煅烧石膏原料的过程中,可以将石膏原料依次投入多个煅烧室41中,多个煅烧室41可以保证石膏原料的煅烧时间,进而可以提升半水石膏的生产品质。
其中,干燥室43和冷却室42也可以设置为多个,多个干燥室43依次分布,多个冷却室42依次分布。每个冷却室42内可以设置有一个或者多个制冷模块2。
如图2所示,干燥模块为热风组件5。干燥室43上和煅烧室41上均设置有热风口44,干燥室43上的热风口44和煅烧室41上的热风口44分别与干燥模块连通。干燥模块用于向干燥室43供送热风,以将干燥室43内的物料吹送至煅烧室41内,以及向煅烧室41供送热风,以将煅烧室41内的物料吹送至冷却室42内。
热风组件5包括鼓风机50和加热器51,鼓风机50和加热器51连通,鼓风机50可以将气体加压,经过加压的气体经过加热器51后被加热成热风。热风可以流向干燥室43上的热风口44和煅烧室41上的热风口44,并进入到干燥室43中和煅烧室41中。
通过干燥室43上的热风口44进入到干燥室43中的热风可以将干燥室43中的石膏原料吹起流化,干燥室43中的石膏原料在热风作用下被干燥且可以在被干燥后越过隔板40流向与干燥室43相邻的煅烧室41中。
通过煅烧室41上的热风口44进入到煅烧室41中的热风可以将煅烧室41中被加热模块1煅烧过的石膏原料吹起流化,此时煅烧室41中的石膏原料可以在热风作用下越过隔板40,并流向与该煅烧室41相邻的煅烧室41中或者冷却室42中。若上述石膏原料进入到与石膏原料所在的煅烧室41相邻的煅烧室41中,则重复热风组件5的工作过程,直至使得煅烧室41中的石膏原料被吹起流化并越过隔板40进入到冷却室42中。
热风组件5的工作原理类似现有的沸腾床的工作原理,其可以在干燥室43、煅烧室41和冷却室42中依次传输石膏原料。因此,热风组件5不仅可以对石膏原料起到加热作用,进而便于干燥石膏原料以及加快石膏原料的煅烧过程,还可以起到输送石膏原料的作用。
可以看出,本实施例提供的化合物的集成式加工装置中的热风组件5可以进一步的减少石膏生产线上的机器数量,降低设备成本以及减少操作维修过程所需人力物力。
如图2所示,干燥室43内和煅烧室41内均安装有第一布风板45,第一布风板45上设置有均匀分布的多个通风孔,第一布风板45能够支撑物料。干燥室43上的热风口44设置在干燥室43的低于第一布风板45的位置处。煅烧室41上的热风口44设置在煅烧室41的低于第一布风板45的位置处。
热风组件5产生的热风经过干燥室43上的热风口44进入到干燥室43内,或者,热风组件5产生的热风经过煅烧室41上的热风口44进入到煅烧室41内后,会再穿过第一布风板45上的多个通风孔后再将第一布风板45上的石膏原料吹起流化。
其中,第一布风板45起到均布热风的作用,使得石膏原料可以被更均匀的干燥或者煅烧,进而可以提升半水石膏的产品品质。
在实际应用中,第一布风板45可以采用现有的半水石膏生产过程中采用的布风板,其上的通孔设计可以使得热风通过,但会阻碍石膏原料穿过。
如图2和图3所示,本实施例提供的化合物的集成式加工装置还包括打散组件6,打散组件6设置在干燥室43中,用于打散干燥室43内的物料。
当含有一定量游离水的石膏原料进入到干燥室43中后,石膏原料在被干燥模块干燥的同时,还可以被打散组件6破碎打散。打散组件6不仅可以防止石膏原料粘料板结,还可以增加石膏原料的比表面积,增加热风与石膏原料的接触面积,提高干燥效率。
石膏原料在干燥室43内经过打散干燥后,其中的游离水被脱去,游离水含量可以降低至5%以下,此时石膏原料的流动性较高,经过煅烧和冷却后,半水石膏的成品品质较高。
如图2和图3所示,打散组件6包括驱动件60、打散轴61和打散翅片62。打散翅片62安装在打散轴61上,打散轴61和打散翅片62均位于干燥室43内。驱动件60安装在壳体4上并与打散轴61连接,驱动件60用于驱动打散轴61自转,以带动打散翅片62以打散轴61为转轴转动。
其中,打散轴61可以竖直安装在干燥室43中。打散翅片62可以为多组,多组打散翅片62沿打散轴61的轴向间隔安装在打散轴61上。每组打散翅片62均包括多个打散翅片62,每组打散翅片62中的多个打散翅片62均沿打散轴61的周向依次垂直安装在打散轴61的轴身上。
驱动件60可以为电机,电机设置在壳体4外壁上与干燥室43对应的位置处并位于打散轴61上方。打散轴61的其中一端与电机的输出轴固定连接,另一端可以与固定在干燥室43的内侧壁上的支撑件转动连接。
电机用于带动打散轴61转动,石膏原料进入到干燥室43中时,石膏原料会落在高速旋转的打散翅片62上,此时打散翅片62可以将石膏原料破碎打散,破碎后的石膏原料可以在热风的吹动下进行流态化干燥。
其中,打散轴61的其中一端与电机的输出轴固定连接,另一端转动连接在干燥室43中的第一布风板45上,可以使得打散轴61稳定安装在干燥室43中,使得打散组件6运行可靠,进而可以降低打散组件6的维修成本。
进一步的,如图3所示,干燥室43的侧壁远离煅烧室41的部分为半圆柱形。
干燥室43的侧壁远离煅烧室41的部分为半圆柱形,可以使得干燥室43的侧壁形状适应于打散组件6中打散翅片62的运动轨迹,使得打散翅片62能够消除干燥室43内壁上的粘料、集料角落。
在本实施例中,隔板40可拆卸安装在壳体4的底面的内侧壁上,隔板40的顶端与壳体4的底面之间的间距可调节。
其中,隔板40可以为多个,多个隔板40的尺寸不同,当在壳体4的底面上更换不同的隔板40时,可以改变隔板40的顶端与壳体4的底面之间的间距。或者,隔板40可以为可升降隔板40,可升降隔板40也可以改变隔板40的顶端与壳体4的底面之间的间距。
隔板40的顶端与壳体4的底面之间的间距可调节可以改变石膏原料在干燥室43内或者煅烧室41内的停留时间,进而可以控制石膏原料的干燥时长和煅烧时长。而石膏原料的煅烧时长可控,则可以保证产品的煅烧品质。
为了适应不同产能和不同品质的物料,隔板40可以控制物料在煅烧室41内的停留时间在5min-15min之间可调。
可以看出,本实施例提供的化合物的集成式加工装置可以利用隔板40调节物料在煅烧室41内的停留时间,以及可以利用热风组件5实现流态化干燥和煅烧过程,进而可以使得物料的加工过程更加均匀稳定,不会出现一边烧不透,一边过烧等质量问题,有效提升了产品品质。经过实际试验,利用本实施例提供的化合物的集成式加工装置生产出的半水石膏等化合物的成品质量得到了极大的提升,其三相比、抗压强度、抗折强度等都远高于成品标准所规定的数值。
如图2所示,冷却室42的远离煅烧室41的一侧设置有出料口46。本实施例提供的化合物的集成式加工装置还包括吹风组件7,冷却室42上低于出料口46的位置处设置有冷风口420,冷风口420与吹风组件7连通。吹风组件7用于向冷却室42供送气体,以将冷却室42内的物料吹送至出料口46处。
吹风组件7可以为鼓风机50,鼓风机50可以将气体加压,经过加压的气体可以流向冷却室42室上的冷风口420并进入到冷却室42中。经过加压的气体可以为常温下的气体,也可以为经过冷却的气体。
通过冷却室42上的冷风口420进入到冷却室42中的气体可以将冷却室42中的半水石膏吹起流化,冷却室42中的半水石膏在气体作用下不仅可以被加速降温,还可以被吹起流向出料口46处。
因此,吹风组件7不仅可以对半水石膏起到加速降温作用,还可以起到输送半水石膏的作用。
如图2所示,冷却室42内靠近底部的位置处安装有第二布风板421,第二布风板421上设置有均匀分布的多个通风孔,第二布风板421能够支撑物料。冷却室42上的冷风口420位于冷却室42的侧壁上,且位于冷却室42的底部和第二布风板421之间。
吹风组件7产生的气体经过冷却室42上的冷风口420进入到冷却室42内后,会再穿过第二布风板421上的多个通风孔后再将第二布风板421上的半水石膏吹起流化。
第二布风板421起到均布吹风的作用,使得石膏原料可以被更均匀的冷却降温,进而可以提升半水石膏的降温效率。
在实际应用中,第二布风板421可以采用现有的半水石膏生产过程中采用的布风板,其上的通孔设计可以使得气体通过,但会阻碍半水石膏穿过。
其中,第一布风板45和第二布风板421可以为依次连接的整块布风板,整块布风板依次穿过多个隔板40并依次与多个隔板40垂直连接。
如图2所示,出料口46处设置有料位调节板422,料位调节板422用于从出料口46的底边至顶边遮挡部分出料口46。
料位调节板422可以滑动连接在出料口46处,且可以通过螺栓固定在出料口46处。
料位调节板422用于调节冷却室42内的半水石膏的堆积高度,以及可以调节冷却室42内的半水石膏的停留时间,进而可以调节半水石膏的成品品质。
如图2所示,壳体4的除尘空间处的两侧的侧壁上分别设置有进风口47和出风口48。除尘组件3包括滤袋30和空气压缩机31。滤袋30安装在壳体4的除尘空间处的内壁上,并位于煅烧室41和冷却室42的上方,滤袋30用于收集壳体4内的粉尘。空气压缩机31安装在壳体4上,且空气压缩机31上的喷嘴安装在滤袋30上方,并与进风口47连通。
在石膏原料的干燥、煅烧过程中,以及半水石膏的冷却过程中,热风组件5产生的热风对石膏原料完成干燥和煅烧后,以及吹风组件7产生的气体对半水石膏完成冷却后,均会携带蒸发的气态水和大量粉尘上升。气态水和大量粉尘上升后,粉尘可以附着在煅烧室41和冷却室42上方的滤袋30上,气态水可以随着气体通过出风口48排出至壳体4之外。
其中,出风口48处还可以设置有引风机480,引风机480用于将经过除尘后的气体引出至壳体4之外。
而空气压缩机31可以通过喷嘴向滤袋30喷射气体,该气体可以将附着在滤袋30上的粉尘喷吹回落到煅烧室41或者冷却室42中,该部分粉尘被回收利用。空气压缩机31和喷嘴不仅可以减少滤袋30上附着的粉尘,还可以将该部分粉尘回收利用,提升产品的产量。
如图1所示,本实施例提供的化合物的集成式加工装置还包括进料机构8。壳体4上靠近干燥室43的位置处设置有进料口49,进料机构8与进料口49连接。
其中,进料机构8可以为螺旋给料机。
如图1所示,本实施例提供的化合物的集成式加工装置还包括出料机构9,出料机构9与出料口46连接。
其中,出料机构9的出口处还可以设置有出料阀90,出料阀90用于控制出料状态和出料速度。
进一步的,出料机构9之后还可以设置有物料包装机构。
在实际应用中,本实施例提供的化合物的集成式加工装置包括上述加热模块1、制冷模块2、除尘组件3、壳体4、鼓风机50、引风机480、进料机构8、出料机构9和物料包装机构等器件时,总体机器数量为15台左右,相较于现有的石膏生产线上设置的40-50台机器,极大的减少了生产线的上的机器数量,以及简化了生产线的整体流程,同时,还减小了生产线的占地面积,降低了生产线的整体投资成本。
最后应说明的是:以上各实施例仅用以说明本实用新型的技术方案,而非对其限制;尽管参照前述各实施例对本实用新型进行了详细的说明,本领域的普通技术人员应当理解:其依然可以对前述各实施例所记载的技术方案进行修改,或者对其中部分或者全部技术特征进行等同替换;而这些修改或者替换,并不使相应技术方案的本质脱离本实用新型各实施例技术方案的范围。
起点商标作为专业知识产权交易平台,可以帮助大家解决很多问题,如果大家想要了解更多知产交易信息请点击 【在线咨询】或添加微信 【19522093243】与客服一对一沟通,为大家解决相关问题。
此文章来源于网络,如有侵权,请联系删除


