一种焦化脱硫废液制硫酸的方法与流程



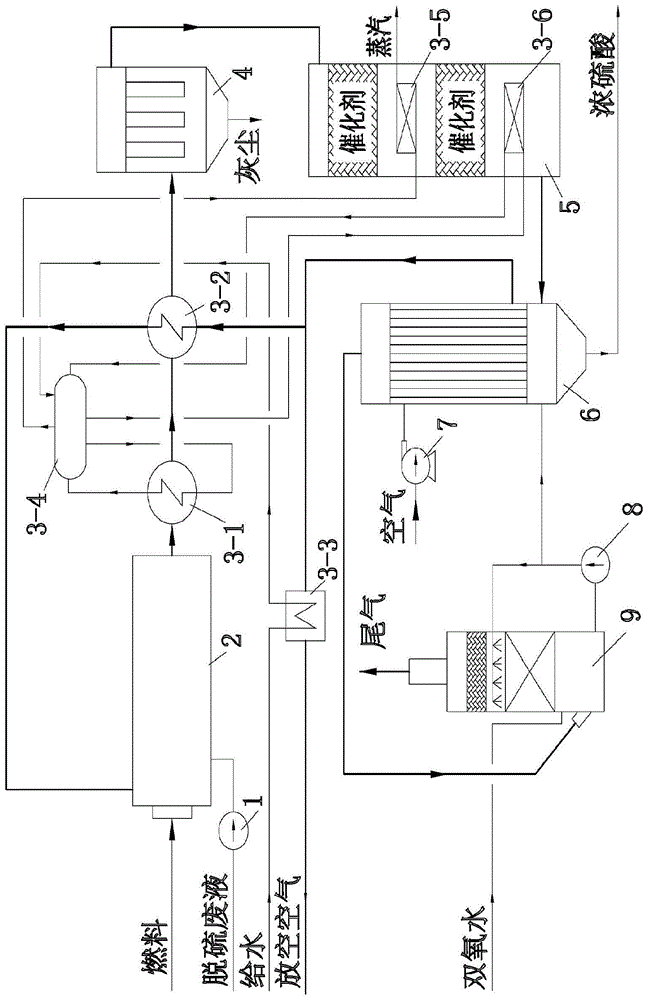
本发明涉及环保领域,具体涉及一种焦化脱硫废液制硫酸的方法。
背景技术:
:目前国内焦化行业生产过程中均设置了脱硫装置,回收工艺过程中的硫元素,这些脱硫装置生产过程中会副产含有硫磺、铵盐等物质的废液,这些废液如直接排放同样会对环境造成污染。现有技术采用焚烧的方法处理脱硫废液,焚烧后含so2气体需经过稀硫酸净化除尘,净化过程中产生的含尘稀硫酸,制酸装置本身无法消化,焦化厂也无法有效利用,且工艺气体采用稀硫酸净化时,采用低温洗涤工艺,工艺气温度显著降低(温降在200℃以上),稀酸温度从50℃左右升高至60℃左右,只能用循环水冷却稀酸,热量很难有效利用。现有技术一般采用2转2吸的生产工艺处理净化出口含so2和水份的工艺气体生成硫酸。具体做法是将净化洗涤后含so2和水份的工艺气体送入干燥设备,用去除水份,干燥设备出口工艺气体温度通常在50℃左右,未达到so2转化为so3所需要的反应温度,需要用转化反应后升温的热工艺气体加热进入转化器的冷工艺气体,将工艺气体加热至380℃以上反应温度,而后在转化器内催化剂的作用下完成一次转化反应,将部分so2氧化为so3,反应后气体温度升高,经换热器与冷工艺气体换热后,再用送入吸收塔,在塔内用大量硫酸循环的方式,吸收工艺气体中so3,吸收so3后循环酸温升高,再用循环水冷却,一次吸收后,工艺气体温度降低至80℃,再经换热器加热至反应温度后,送入转化器进行二次转化,将剩余的so2氧化为so3,换热降温后,再用另一台吸收塔进行二次吸吸收。上述处理工艺流程长,设备多,占地面积大,运行成本高,需要消耗大量电力和循环水,工艺过程热回收率低,且副产物-稀硫酸无法有效利用。技术实现要素:本发明是针对上述现有技术提供一种焦化脱硫废液生产硫酸的方法,有效利用脱硫废液中的硫元素,减少焦化装置副产物对环境的污染。同时,工艺流程短,设备少,占地面积小,工艺过程热回收效率高、运行成本低,且不副产稀硫酸。本发明的目的可以通过以下技术方案实现:一种焦化脱硫废液制硫酸的方法,该方法包括以下步骤:(1)用气体或液体燃料喷入焚烧炉内燃烧产生高温气体,然后将焦化脱硫废液喷入炉内高温气体环境中,脱硫废液中的硫、铵盐和有机物氧化分解,最终在焚烧炉内形成900℃到1200℃的含so2,co2,n2,o2,h2o高温工艺气体;主要反应为:s+o2=so2nh4cns+3o2=2h2o+n2+so2+co2(nh4)2s2o3+2.5o2=4h2o+n2+2so2(nh4)2so4+o2=4h2o+n2+so2(2)出焚烧炉的高温工艺气体经热量回收系统换热器,用工艺气体的热量产生蒸汽或加热其它介质,出换热器后工艺气体温度降至390~450℃;(3)降温至390~450℃的工艺气体再进入除尘器,直接过滤除尘,除尘后工艺气体温度仍维持在催化氧化所需要温度以上;(4)除尘后的工艺气体进入反应器,在催化剂的作用下,工艺气体中的so2进一步氧化为so3,且有部分so3与水蒸汽反应生成硫酸蒸汽,氧化反应和生成硫酸的反应均为放热反应,反应器内布置有热量回收系统换热器,回收反应热产生蒸汽或加热其它介质,出反应器的工艺气体温度为控制在290℃±20℃;so2+1/2o2=so3h2o(汽)+so3=h2so4(汽)(5)离开反应器后的工艺气体进入硫酸蒸汽冷凝器,用空气冷却工艺气,工艺气体中硫酸蒸汽冷凝,剩余的so3继续与水蒸汽反应生成硫酸蒸汽并最终冷凝为液态硫酸;离开硫酸蒸汽冷凝器的工艺气体仍含极少量so2,再进入尾气处理系统,经处理后达标排放。上述方法中:步骤(5)中空气经空气风机升压后先送入硫酸蒸汽冷凝器中冷却工艺气体,换热后空气温度升高,硫酸蒸汽冷凝器出口的热空气分为两部分,其中一部分作为焚烧炉的助燃空气,这一部分空气送入热回收系统换热器的工艺气-空气预热器中,用更高温度的工艺气体加热该部分的助燃空气,再次升温后再送入焚烧炉,减少焚烧炉燃料的消耗;剩余部分空气送入热回收系统的给水加热器,预热送入热回收系统的给水,换热降温后空气直接排放。上述方法中:热量回收系统换热器由布置在焚烧炉出口的蒸发器i、工艺气-空气预热器、布置在反应器内蒸汽过热器和蒸发器ii、给水加热器、汽包以及与这些设备连接的汽水管道组成,回收制酸工艺过程热量,产生蒸汽,热回收系统也可采用导热油或熔盐为导热介质,回收的热量也可产出蒸汽或加热其它工艺物料。在一些具体的技术方案中:外界送入给水经给水加热器用热空气预热至180℃±50℃,送入汽包与炉水混合,汽包中炉水分别流入在焚烧炉出口的蒸发器i和布置在反应器内布置的蒸发器ii,蒸发器i和蒸发器ii中的炉水受热部分蒸发生成汽水混合物,汽水混合物在热虹吸的作用下回流至汽包,在汽包内蒸汽与炉水分离,炉水继续进入蒸发器i和蒸发器ii循环,汽包分离出中压饱和蒸汽;饱和蒸汽再送入反应器内布置蒸汽过热器,经工艺气体加热为中压过热蒸汽外供。上述方法中:脱硫废液含水量为40%以上。上述方法中:实现焦化脱硫废液制硫酸的系统包括焚烧炉、反应器和硫酸蒸汽冷凝器,所述的燃料以及脱硫废液输送至焚烧炉,焚烧炉的输出端依次与热量回收系统以及除尘器相连,所述除尘器的输出端依次通过反应器、硫酸蒸汽冷凝器和尾气处理塔相连。上述方法中:所述的热量回收系统包括布置在焚烧炉出口的蒸发器i,所述的蒸发器i和工艺气-空气预热器相连,给水的输出管道通过给水加热器后与汽包相连,所述的汽包的一个输出端通过蒸发器i与汽包相连,另一个输出端通过蒸发器ii与汽包相连。上述方法中:空气通过空气风机输送至硫酸蒸汽冷凝器,硫酸蒸汽冷凝器的输出端分为两个支路,一个支路输送至给水加热器,另一个支路通过工艺气-空气换热器与焚烧炉相连。反应器内so2氧化为so3,s03与h20反应生成硫酸均为放热反应,本发明技术方案中:反应器中设置可以两个或多个催化剂床层,并在两个催化剂床层出口布置热回收系统换热设备,冷却层间工艺气体,回收反应过程产生的热量,推动催化氧化反应进程。作为优选:反应器中设有2层催化剂层,上层催化剂层的下方设有蒸汽过热器,下层催化剂层的下方设有蒸发器ii。通过热回收系统换热器设备回收反应热量,推动反应进程,最终工艺气体中99%以上so2均氧化为so3,并将反应器出口工艺气体温度控制在290℃±20℃。本发明技术方案中:所述的催化剂包括但不限于五氧化二钒。本发明技术方案中:所述的压力为表压。本发明的有益效果:通过焚烧方式处理焦化脱硫废液生产硫酸,使硫元素得以有效利用,生成产品应用广泛,避免脱硫废液直接排放造成环境污染。本发明采用焚烧后降温至390~450℃工艺气体过滤除尘的方法,不副产含尘稀酸酸,避免出现二次污染物。本发明采用除尘后含so2和水份工艺气体直接进入反应器,将so2氧化生成so3,so3再与水蒸汽反应生成硫酸蒸汽,并最终冷凝生成硫酸,不需要采用现有技术中工艺气体干燥流程,也不需要现有技术中工艺气体先加热再送入转化器反应的换热流程,更不需要用大量循环酸在吸收塔内吸收so3的吸收流程。因此,本发明较现有技术大大缩短工艺流程,工艺设备数量明显减少,生产装置占地面积亦相应减少,不需要使用大量循环水和循环酸,能耗显著降低,运行成本降低,工艺过程热量损失减少,热量回收率大幅提升,副产蒸汽量明显增加。附图说明图1为本发明焦化脱硫废液制硫酸的系统的示意图。其中:1、脱硫废液泵,2、焚烧炉,3、热量回收系统,4、除尘器,5、反应器,6、硫酸蒸汽冷凝器,7、空气风机,8、尾吸循环泵,9、尾气处理塔;热量回收系统设备3-1蒸发器i,3-2工艺气-空气换热器,3-3给水加热器,3-4汽包,3-5蒸汽过热器,3-6蒸发器ii。具体实施方式下面结合实施例对本发明做进一步说明,但本发明的保护范围不限于此:如图1,一种焦化脱硫废液制硫酸的系统,该系统包括焚烧炉2、反应器5和硫酸蒸汽冷凝器6,所述的燃料以及脱硫废液输送至焚烧炉2,焚烧炉2的输出端依次与热量回收系统以及除尘器4相连,所述除尘器4的输出端依次通过反应器5、硫酸蒸汽冷凝器6和尾气处理塔9相连。所述的热量回收系统包括布置在焚烧炉2出口的蒸发器i3-1,所述的蒸发器i3-1和工艺气-空气预热器3-2相连,给水的输出管道通过给水加热器3-3后与汽包3-4相连,所述的汽包3-4的一个输出端通过蒸发器i3-1与汽包3-4相连,另一个输出端通过蒸发器ii3-6与汽包3-4相连。空气通过空气风机7输送至硫酸蒸汽冷凝器6,硫酸蒸汽冷凝器6的输出端分为两个支路,一个支路输送至给水加热器3-3,另一个支路通过工艺气-空气换热器3-2与焚烧炉2相连。反应器5中设有2层催化剂层,上层催化剂层的下方设有蒸汽过热器3-5,下层催化剂层的下方设有蒸发器ii3-6。一种利用上述的系统实现焦化脱硫废液制硫酸的方法,该方法包括以下步骤:脱硫废液成分见下表该处理装置以焦化装置副产的焦炉煤气为燃料,燃料在焚烧炉2中燃烧,产生高温气体,炉膛温度控制在900℃到1200℃左右,焦化脱硫废液喷入炉膛,其中的硫、铵盐和有机物在高温炉膛中氧化分解为含so2,co2,n2,o2,h2o和少量灰尘的高温工艺气体,工艺气体经热回收系统蒸发i3-1和工艺气-空气换热器3-2降温至400℃,而后进入除尘器4,工艺气体去除灰尘后再进入反应器5,反应器5中设2层催化剂,工艺气体中的so2经第一层催化剂部分氧化生成so3,工艺气体温度升高至600℃,经过层间设置的热回收系统蒸汽过热器3-5降温至400℃,而后工艺气体再进入第二层催化剂,工艺气体中剩余的so2继续氧化为so3,经过2层催化剂后99%以上的so2均氧化为so3,工艺气体出催化剂第二层温度升高至520℃,再经热回收系统蒸发器ii3-6降温至300℃;工艺气体出反应器进硫酸蒸汽冷凝器6,在冷凝器内工艺气体经空气冷却降温,硫酸蒸汽逐渐冷凝,工艺气体中剩余so3再继续与水蒸汽反应生成硫酸蒸汽,冷凝器出口,工艺气温度下降至150℃以下,硫酸蒸汽全部冷凝。出硫酸蒸汽冷凝器6后工艺气体再送入尾气处理塔,尾气处理塔9采用双氧水吸收工艺气体中剩余so2,生成浓度20%左右的洁净稀硫酸,出塔尾气中s02含量低于100mg/nm3,可达标排放。尾气处理塔生成20%洁净稀硫酸送冷凝器液态硫酸出口,调节成品酸浓度。空气经空气风机7升压后送入硫酸蒸汽冷凝器6,冷却工艺气体空气温度升高至200℃,硫酸蒸汽冷凝器6出口热空气分为两部分,其中一部分作为焚烧炉2的助燃空气,这一部分空气再送入工艺气-空气预热器3-2中,用更高温度的工艺气体加热至460℃后后再送入焚烧炉2;剩余部分空气送入给水加热器3-3,将104℃的热回收系统的给水加热至160℃,换热降温后空气直接排放。热量回收系统由布置在焚烧炉出口的蒸发器i3-1、工艺气-空气换热器3-2、反应器内布置的过热器3-5和蒸发器ii3-6,汽包3-4、给水加热器3-3及与这些设备连接的汽水管道管道组成。外界送入104℃给水经给水加热器3-3用热空气预热至160℃,送入汽包3-4与炉水混合,汽包3-4中炉水流入蒸发器i3-1和蒸发器ii3-6,炉水受热部分蒸发生成汽水混合物,汽水混合物在热虹吸的作用下回流至汽包3-4,在汽包3-4内蒸汽与炉水分离,炉水继续进入蒸发器i3-1和蒸发器ii3-6循环,汽包3-4分离出6.0mpa的中压饱和蒸汽产量可达9.5t/h;饱和蒸汽再送入反应器内布置过热器3-5,经工艺气体加热为460℃中压过热蒸汽外供。采用现有技术处理脱硫废液需经过焚烧、净化、转化和干吸4个工段,工艺设备多,同等规模处理装置现有技术与本技术连续运行用电设备对比如下:设备名称现有技术用电设备功率(kw)本技术用电设备功率(kw)废液泵1111空气风机37132动力波循环泵30-------填料塔循环泵15-------干燥循环酸泵22-------一吸循环酸泵22-------二吸循环酸泵22-------尾吸循环泵1515so2鼓风机160-------合计334158本技术用电设备功率仅为现有技术的47%,电耗也相应为现有技术的47%。现有技术净化工序动力波循环循环液需要用循环水冷却,干燥塔、一吸塔、二吸塔的循环酸均需循环水冷却,将工艺过程热带出向大气释放,采用现有技术处理5t/h的脱硫废液,循环水用量为600t/h,而采用本技术,硫酸生成热一部分在反应器中被热回收系统回收产生蒸汽,一部分在冷凝器中加热空气,均不需要用循环冷却水,只有反应器出口少量成品硫酸冷却需用循环水,用量为80t/h,仅为现有技术13%。现有技术仅在焚烧炉后设置余热锅炉,锅炉出口300℃的工艺气直接在净化工序用稀酸冷却至40℃,转化器反应热量用于加热转化器进口工艺气温度,干吸工段的吸收反应热也用循环水冷却,同等规模装置采用现有技术的产汽量仅为4.2t/h的5.8mpa(g)饱和蒸汽,采用本技术产汽量可达9.5t/h,蒸汽参数为5.8mpa(g),460℃的过热蒸汽,蒸汽产量为现有技术226%。采用现有技术处理脱硫废液的装置,焚烧工段占地面积200m2,净化工段占地面积230m2,干吸尾吸工段占地310m3,转化工段占地380m2,装置总面积1120m2,且不包含各工段间通道占地面积。采用本技术的处理装置仅需要焚烧工段(占地面积160m2)和工艺气处理工段(350m2)2个部分,装置紧凑,总占地总面积510m2,仅为现有技术45.5%。当前第1页1 2 3 
起点商标作为专业知识产权交易平台,可以帮助大家解决很多问题,如果大家想要了解更多知产交易信息请点击 【在线咨询】或添加微信 【19522093243】与客服一对一沟通,为大家解决相关问题。
此文章来源于网络,如有侵权,请联系删除



tips