一种反重力铸造局部加压用锁模装置及反重力铸造设备的制作方法



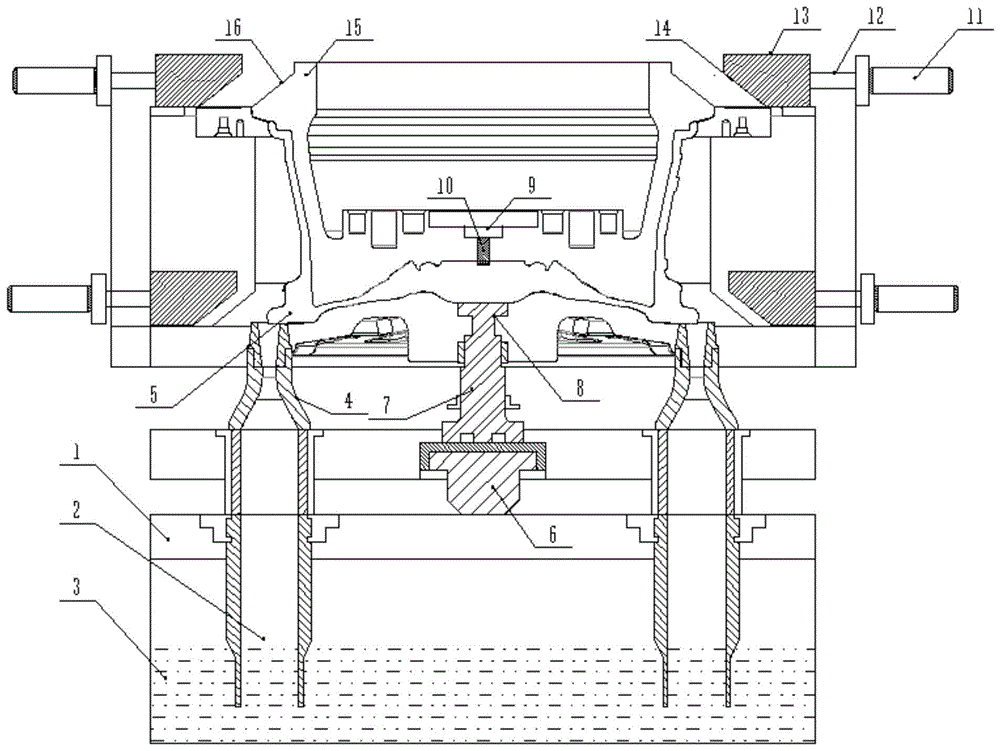
本实用新型涉及铸造技术领域,尤其是涉及一种反重力铸造局部加压用锁模装置及反重力铸造设备。
背景技术:
轻量化是燃油汽车节能减排、新能源汽车降耗增程的最重要途径之一,以铝合金等轻量化材料代替传统的钢铁材料,已成为汽车设计更新换代的必然选择。用于汽车上的铝合金可分为铸造铝合金和变形铝合金,铸造铝合金主要用于制造发动机、离合器壳体、车轮、底盘件等零部件。随着对铸件质量提升的需求和铸造技术的发展,更多的零部件采用低压铸造、差压铸造及调压铸造的方式来生产,均属于反重力铸造方法。该种铸造基本原理是用低压气体驱动坩埚或保温炉内的金属熔体,使其通过升液管上升并进入模具型腔,充型结束后铸型内金属熔体完成在压力作用下的凝固和补缩。
传统的铝合金低压、差压及调压车轮铸造技术通常采用单浇口的单升液管充型技术。以铝合金车轮为例,在车轮的中央位置即车轮的轮心位置设置升液管,使金属熔体进入型腔并完成充型与凝固,该方法设计简单,易于实现,但缺点在于充型距离长,成型困难,为避免产生冷隔,车轮金属型模具温度一般高达400℃以上,导致车轮冷却速度低,组织粗大,并容易在热节部位形成缩孔缩松等铸造缺陷。为了细化组织、消除缩孔缩松等铸造缺陷,现有技术中一般采用水冷、水雾冷等方式加强车轮模具的冷却,然而,加强冷却使车轮凝固时间大为缩短,如加强冷却后的大尺寸车轮的凝固时间可以缩短到100s以内,但同时又引起生产过程中对车轮冷却和凝固过程的温度场难以控制的问题,导致难以实现顺序凝固,产品性能不稳定,合格率低。
车轮现有技术中已有其它充型方式的尝试。专利cn201010107026.8公开了一种铝合金车轮低压铸造双边浇工艺及装置,在车轮两侧设置浇口,使铝液从轮辋处进入,通过对冷却控制使铝液在急冷的模具温度下由轮心向轮辋进行结晶,缩短了铝液流动的距离,配合冷却,减少了r角或轮辋部位的缩松缺陷。专利cn201310557627.2、cn201410825962.0等文献公开了采用中心浇口和两侧浇口结合的方式,以期望能减轻轮毂的重量,提高机械强度。cn201610390494.8采用一机双模轮毂模具,浇口同样设置在轮辋位置上,实现一次浇注两个轮毂。
但上述装置和方法同样存在明显的缺陷,对于铝液仅从轮辋处进入的方式,入口设在轮辋中部,进入后会导致分流,即同时向轮心处和轮缘处充型,造成各处的充型时间不可控,进而造成凝固顺序不可控,容易形成缩孔缩松缺陷。而对于采用中心浇口和两侧浇口结合的方式,由于铝液从两个入口进入,在中间位置会形成汇流,容易因气体排出不顺等原因造成冷隔等。
在本申请人设计了一种基于多升液管的快速顺序凝固车轮成型装置与方法,模具的浇口设置在车轮的轮辋正下方或下轮缘的上方r角外侧。采用该方法可以显著降低充型距离并解决了大尺寸车轮长距离补缩的问题,同时采用局部机械加压的方式以消除中心轮心处的缩孔缩松,但由于局部机械加压的压力很大,远远超过低压或差压铸造的保压压力,因此在局部机械加压时,如何实现有效锁模以保证局部加压效果成为一个亟待解决的问题。
技术实现要素:
为解决上述技术问题,本实用新型提供了一种反重力铸造局部加压用锁模装置及反重力铸造设备。
本实用新型完整的技术方案包括:
一种反重力铸造用锁模装置,所述反重力铸造用锁模装置包括侧模锁紧部、上模锁紧部和下模锁紧部,所述侧模锁紧部通过连接部件固定于反重力铸造设备的侧模模板或机架上,包括锁紧驱动机构、锁紧力传动机构和侧模锁紧块,所述锁紧力驱动机构锁紧力驱动机构上设有锁紧力传动机构,锁紧力传动机构连接侧模锁紧块,所述侧模锁紧块上带有斜面,上模锁紧部和下模锁紧部上设有与侧模锁紧块形状相适应的斜面。
所述锁紧驱动机构可驱动侧模锁紧部左右移动。
锁模状态时,侧模锁紧块的斜面与上模锁紧部和下模锁紧部的斜面匹配贴合,同时侧模驱动机构向该贴合面施加锁模力。
锁模状态时,侧模锁紧块的斜面位于上模锁紧部和下模锁紧部的斜面的上方。
所述锁紧驱动机构为液压油缸,所述锁紧力传动机构为液压杆。
带有所述装置的反重力铸造设备。
所述反重力铸造设备为低压铸造设备或差压铸造设备。
所述反重力铸造设备还包括局部加压和细化装置,所述局部加压和细化装置包括局部加压机构和细化机构;
所述局部加压机构设置于:反重力铸造车轮模具上对应车轮轮心的位置下方,包括压力驱动机构、压力传递机构和压力施加机构,压力施加机构与金属熔体接触,并在充型结束后对金属熔体施加压力;
所述细化机构设于反重力铸造车轮模具上,对应车轮轮心的位置上方,并在金属熔体凝固过程中对其进行细化。
所述压力驱动机构为液压油缸,所述压力传递机构为液压杆、所述压力施加机构为压力块。
所述细化机构为超声细化机构或振动细化机构。
所述反重力铸造设备包括模具,所述模具上的浇口,开设在车轮轮辋正下方的圆环面上。
本实用新型相对于现有技术的优点在于:
本申请人提出的基于多升液管的快速顺序凝固车轮成型装置与方法,模具的浇口设置在车轮的轮辋正下方。通过在多个升液管升液充型,使金属熔体的充型距离相比现有单升液管模式缩短一半以上,金属型模具温度可以由现有的420℃降低到320℃以下,自然地加快了车轮冷却速度与冷却效果,实现了快速顺序凝固。并且进一步改进的,在车轮的中心位置增加局部加压装置,压力施加机构与金属熔体接触,并在充型结束后对金属熔体施加压力。使此处的铝液在极高压下进行凝固,消除了形成缩孔缩松缺陷的可能性。但由于局部机械加压的压力很大,远远超过低压或差压铸造的保压压力,带来了安全性隐患,基于此,本申请人设计了一种反重力铸造局部加压用锁模装置,在施加局部增压时,液压油缸对侧模锁紧块和上模锁紧部的贴合斜面施加锁模力,能够保证金属熔体在受到极高压下条件下,依然保持良好的模具锁紧状态。应用于带有局部加压装置的多升液管反重力车轮铸造成型装置时,在局部加压时可以提供稳定的锁模力,显著提高了安全性。
附图说明
图1为带有本实用新型锁模装置的车轮反重力铸造设备结构,在未锁紧状态下的结构示意图。
图2为带有本实用新型锁模装置的车轮反重力铸造设备结构,在锁紧状态下的结构示意图。
图3为现有技术中的车轮结构示意图。
图4a为图1设备进行充型时的易发生卷气部位。
图4b为图4a的局部放大图。
图4c为图4a处在慢速充型时的充型顺序示意图。
具体实施方式
下面结合附图和具体实施方式对本实用新型做进一步说明。
如图1所示,本实用新型锁模装置包括侧模锁紧部、上模锁紧部和下模锁紧部,其中侧模锁紧部通过连接部件固定于反重力铸造设备的侧模模板或机架上,包括第一侧模锁紧部和第二侧模锁紧部,各侧模锁紧部均包括锁紧驱动机构11、锁紧力传动机构12和侧模锁紧块13,锁紧力驱动机构11可以为液压油缸、电机等任何现有技术中的通用驱动机构,在此处优选采用液压油缸,液压油缸上设有锁紧力传动机构,锁紧力传动机构此处优选使用液压杆,液压杆上前端连接侧模锁紧块13,所述各侧模锁紧块形状类似于半梯形,前端有向前突出的斜面14,该斜面14用以在锁模时分别压紧上模锁紧部15上相对应的上模锁紧部斜面16,以及下模锁紧部上相对应的下模锁紧部斜面。
该锁紧驱动机构11可驱动侧模锁紧部左右移动,以执行开模和锁模操作。
在锁模状态时,侧模锁紧块的斜面与上、下模锁紧部的斜面匹配贴合,同时侧模驱动机构向该贴合面施加一定的锁模力。锁模状态时,侧模锁紧块的斜面位于上、下模锁紧部的斜面的上方。
上、下模和边模进行锁模时,如图1所示,锁紧力驱动机构11带动侧模锁紧部向外侧移动以留出合模空间,上模模板下降合模,随后锁紧力驱动机构11驱动侧模锁紧部向内侧移动,使对应的各自两斜面匹配贴合,侧模锁紧块的斜面位于上、下模锁紧部的斜面的上方,进入锁模状态,如图2所示。随后进行铸造过程。完成后按锁紧方式逆序操作进行解锁。
在本实用新型进行锁紧后,局部加压装置对充型后的铝液进行局部加压时,压力通过铝液传递到上模,此时,侧模驱动机构向上模锁紧部和侧模锁紧部的贴合面施加一定的锁模力。能够保证在极高压下的模具锁紧状态,显著提高了安全性。
下面对与本实用新型相配套使用的车轮成型装置,以及配套工艺进行说明。
图3为一个典型的车轮构造图,其中在现有技术中,通常将车轮的中央位置称为轮心,在车轮外侧,与轮胎装配配合,支撑轮胎的部分称为轮辋,与车轴轮心实施安装连接,并支撑轮辋的车轮部分称为轮辐,多个轮辐中间留有窗口。保持并支撑轮胎方向的轮辋部分称为轮缘。
现有的低压或差压铸造铝合金车轮生产中,几乎全部采用在车轮的中央轮心位置设置升液管,并使熔体通过连接在升液管上的保温杯和浇口套,由轮心处的浇口进入型腔,在分流锥的作用下进行分流,并沿着轮心-轮辐-轮辋-轮缘的顺序依次充型,充满型腔后实现凝固,这是由于在实际生产中,在此处设置浇口和升液管最为容易实现,且浇口的截面形状为规则的圆形,加工简单。同时浇口的面积大,可以使充型速度快。但是上述浇注充型方式带来的一些问题始终无法很好解决,如浇口距离远,充型距离过长,在轮辋与轮辐连接等热节部位非常难以补缩,容易形成缩孔缩松,成为困扰车轮行业生产的一大难题。虽然采用对该处采用水冷、水雾冷等方式加强冷却,以期望实现顺序凝固,但是由于车轮充型和凝固时间短,难以对温度场进行精确控制,仍然不可避免的会产生相当比例的废品。
而现有技术中采用在轮辋侧面中部位置进行双边浇注的方式,同样由于充型分流导致的充型和凝固顺序不可控也非常容易形成缩孔缩松缺陷。
基于此问题,本实用新型提出了一种基于多升液通道的车轮成型装置,如图1所示,包括盛有铝液的保温炉1、保温炉内连接有高压气源,保温炉内设有多个升液管2,该多个升液管的下部浸入铝液3中。在采用高压气源对炉内的铝液进行加压时,铝液可以沿着多个升液管上升。升液管上方通过保温杯和本实用新型公开的异形浇口组件4与模具的浇口连接,并进入模具的型腔5。异性浇口浇注组件包括浇口杯和位于其上方的异形浇口套。
模具的浇口,设置在车轮的轮辋正下方的圆环面上,特别说明的,本实用新型中所述“轮辋正下方的圆环面”是指轮辋上与轮缘相对的一侧,环绕车轮中心轴线所形成的圆环面。构成该圆环的外圆是该面上车轮最外圈轮廓线所构成的圆,内圆是车轮的窗口区外侧轮廓线围绕车轮中心轴线所构成的圆。如图3所示。对应的,浇口套与模具相连通的位置同样设置在该处。
尤其优选的是,该浇口和浇口套可以设置在该圆环面上对应窗口区外侧的位置,也可以设置于该圆环面上对应轮辋与轮辐连接的位置。
在一种优选的实施方式中,该浇口可以设置为两个,可在车轮两侧对称设置,也可以为环绕车轮轴线设置多个浇口。与该浇口相对应的,升液管可以设置为两个,可在车轮两侧对称设置,也可以为环绕车轮轴线设置多个升液管。
采用上述装置可以显著降低充型距离并解决了大尺寸车轮长距离补缩的问题。轮心位置处的充型和凝固时间较晚,以及可能产生对的液流汇聚问题,有可能在此处产生缩孔缩松和夹杂等铸造缺陷。因此在此设计增加局部加压和细化装置,该局部加压和细化装置包括局部加压机构或/和细化机构;所述局部加压机构设置于模具下方,在模具上对应于车轮轮心位置处下方,包括压力驱动机构、压力传递机构和压力施加机构,压力施加机构与金属熔体接触,并在充型结束后对金属熔体施加压力;细化机构设于车轮模具上方,对应车轮轮心的位置上方,并在金属熔体凝固过程中对其进行细化。所述压力驱动机构为液压油缸6,所述压力传递机构为液压杆7、所述压力施加机构为压力块8。具体的加压工艺为在充型结束后施加1000kpa~120mpa的机械压力。使此处的铝液在极高压下进行凝固,防止由于边缘补缩压力不够而在此处形成缩孔缩松缺陷。
所述细化机构为超声细化机构或振动细化机构。在本具体实施方式中包括振动发生器9和振动杆10,振动杆10探入铝液中,在凝固过程中对铝液进行振动,使铝液结晶形成的枝晶被打破,增强形核,以细化晶粒,提高车轮的机械性能。
本实用新型同时公开了一种适应于该充型方式下的低压/差压铸造工艺,由于本实用新型的浇注充型方式相对于现有技术做了巨大的变化,原有的充型方式和凝固工艺无法适用于本实用新型,基于此,本实用新型同时设计了一种适合该充型位置的工艺。
具体包括如下步骤:
(1)锁紧驱动机构带动侧模锁紧部向外侧移动,留出合模空间,随后下模、上模和边模合模,下模、上模和边模合模以后,锁紧驱动机构带动侧模锁紧部向内侧移动,使使两斜面匹配贴合,侧模锁紧块的斜面位于上模锁紧部的斜面的上方,进入锁模状态;
(2)升液:通过高压气源对保温炉内的铝液进行加压,使铝液在压力下沿着升液管上升到浇口位置,该阶段升压速度为2.8~4.0kpa/s,将压力增加到20kpa;
(3)充型:继续升压,使铝液通过浇口进入型腔,该充型阶段为两段式加压,第一阶段升压速度为0.1~0.2kpa/s,时间为2~4s,随后进入第二阶段快速升压,直至将型腔充满,此时压力达到35kpa;
该第二阶段的升压速度p′由如下方式确定:
式中:
p′为升压速度,单位为kpa/s;h为型腔总高度,单位为mm;ρ为金属熔体密度,单位为g/cm3;k为阻力系数,其取值范围为1~1.5;t为预设充型时间,单位为s,优选取10s;102为单位换算系数;n为升液管数量,其取值范围为2~6,可根据不同型号车轮的窗口数量进行选择,优选取2~4;x为其升液指数,取值范围为0.2~0.8,在本实施方式所采用轮型的方案中,取值选0.5。
(4)结晶增压保压:充型结束后,以8~10kpa/的升压速度将压力快速增加到150kpa,并保压60~150s,此时车轮凝固完成。
(5)卸压放气:铝合金车轮凝固完毕,解除保温炉内的气体压力,使升液管和浇道口未凝固的铝液流回到保温炉中。
(6)解锁开模,顶出铸件,进入下一个生产循环。
对于升液阶段和充型阶段的升压速度选择,由于在升液时,升液管的内径固定,基本不会产生紊流,所以采用快速的升压速度,使金属熔体能快速升液达到浇口位置,缩短升液时间。而在充型阶段,则要考虑到型腔和浇口的复杂形状,在传统的充型方式中,由于采用从轮心位置进行浇注的方式,升液管和浇口的截面积相差不大,且轮心处的型腔截面积大,不易产生紊流,因此可以采用经验或者试验得到充型升压速度。而对于本实用新型的充型方式,采用在轮辋圆环面上进行充型,为不规则随形浇口,升液管和浇口的形状面积差距很大,同时轮辋处的空间较小,如充型压力不合理极易产生紊流卷气,造成气孔缺陷。而现有技术中的充型压力设计均采用理想状态下的计算方式,结合阻力系数等进行修正。没有考虑到升液管和浇口的截面积变化造成的流动状态变化。因此无法采用现有技术中的经验式得到理想的充型升压速度。
因此,本实用新型对上述问题进行了研究,结合升液管、浇口、浇口上方型腔形状与截面积,以及金属熔体的流动特性。发现对于车轮轮辋位置,如图4a中箭头所示的圆框处,在充型的最初阶段存在两个面积发生明显变化的部位,如图4b中箭头所示的圆框处,如果产生紊流,该位置处极易形成卷气,经过设计和计算,本实用新型采用两段式加压,第一阶段明显地降低升压速度,使金属熔体在充型最初阶段实现平稳流动,充满上述区域以避免卷气,如图4c所示(此处箭头为熔体充型方向),随后进入第二阶段快速升压以缩短充型时间。在本实用新型第二阶段的充型过程中,研究发现充型稳定性与升液管数量与明显关系,因为传统的从轮心位置进行浇注的方式仅有一个升液管和浇口,因此通过试验即可得到规律并做定量处理。而本实用新型的充型方式,升液管和浇口数量可以为2个或更多。同样升压条件下,在浇口处流速、在浇口上方型腔内的流速均会发生明显变化,从而导致充型流动方式不可控。因此本实用新型通过研究,得到第二阶段的升压方式,从公式(1)中可以看出,在相同的预设充型时间内,随着升液管数量增加,其可采用的升压速度可以逐步增大,并且不会造成紊流卷气等问题。阻力系数取值与金属液粘度、铸型型腔复杂度等有关,阻力小时取下限,阻力大时取上限。
实施例1:
采用2个升液管和浇口,所用金属熔体质量百分比组成如下:si:5~9%,mg:0.3~0.5%,zr:0.01~0.02%,b:0.005~0.007%,re:0.002~0.005%,nd:0.002~0.005%,fe:0.05~0.15%,mn:0.05~0.1%,ti:0.08~0.14%,其余为al和不可避免的杂质。
(1)锁紧驱动机构带动侧模锁紧部向外侧移动,留出合模空间,随后下模、上模和边模合模,下模、上模和边模合模以后,锁紧驱动机构带动侧模锁紧部向内侧移动,使使两斜面匹配贴合,侧模锁紧块的斜面位于上模锁紧部的斜面的上方,进入锁模状态;
(2)升液:通过高压气源对保温炉内的铝液进行加压,使铝液在压力下沿着升液管上升到浇口位置,该阶段升压速度为3.5kpa/s,将压力增加到20kpa;
(3)充型:继续升压,使铝液通过浇口进入型腔,第一阶段升压速度为0.2kpa/s,时间为1.8s,使金属熔体平稳充满图4b箭头所示区域,随后进入第二阶段随后以0.66kpa/s的升压速度快速充型,直至将型腔充满。
(4)结晶增压保压:充型结束后,以8kpa/的升压速度将压力快速增加到150kpa,并保压,液压油缸带动液压杆驱动压力块对轮心位置处施加2000kpa的机械压力,振动发生器带动振动杆对铝液进行振动细化,直到车轮凝固完成。在保压过程中,在浇口处对一直保持轮辋热节的高压力补缩,在高压铝液的补缩下,完全消除了该处的缩孔缩松产生的可能性。同时压力块对轮心处金属液进行局部加压,消除了该处产生缩孔缩松的可能性。
(5)卸压放气:铝合金车轮凝固完毕,解除保温炉内的气体压力,使升液管和浇道口未凝固的铝液流回到保温炉中。
(6)解锁开模,顶出铸件,进入下一个生产循环。
以上所述,仅是本实用新型的较佳实施例,并非对本实用新型作任何限制,凡是根据本实用新型技术实质对以上实施例所作的任何简单修改、变更以及等效结构变化,均仍属于本实用新型技术方案的保护范围内。
起点商标作为专业知识产权交易平台,可以帮助大家解决很多问题,如果大家想要了解更多知产交易信息请点击 【在线咨询】或添加微信 【19522093243】与客服一对一沟通,为大家解决相关问题。
此文章来源于网络,如有侵权,请联系删除


