一种用于电厂锅炉受热面的陶瓷涂料及其制备方法与流程



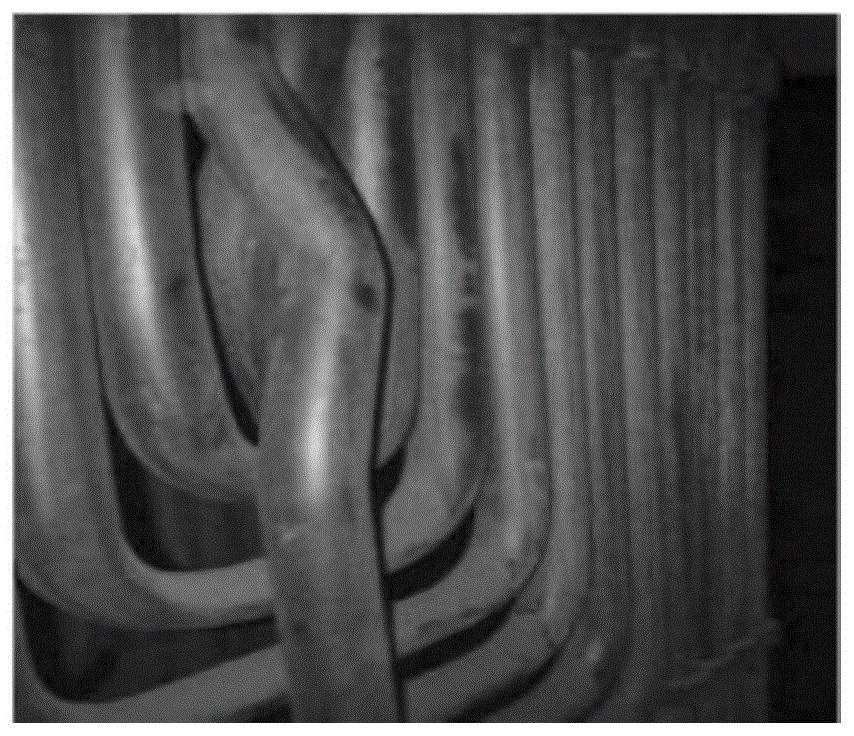
本发明属于涂层技术领域,特别涉及一种用于电厂锅炉受热面的陶瓷涂料及其制备方法。
背景技术:
锅炉是重要的能量转换装置,电厂锅炉,尤其是大型燃煤电厂锅炉,其锅炉管包括炉膛水冷壁、过热器管、省煤器管等部件,由于锅炉管的工作环境恶劣,长期处于硫化腐蚀、氯腐蚀、高温氧化腐蚀的环境中,且由于煤质不同,部分煤高温燃烧后会产生一些胶质物,这些胶质物积累到一定程度形成厚度不等的堆积物附着在水冷壁上面,产生热防护现象,影响锅炉发热效率,造成能源浪费。结焦物也会使得水冷壁导热不均匀,在管道内部局部产生高压蒸汽或者水冷壁管干烧现象,进而造成爆管。
目前主要是通过喷涂涂料,形成致密的保护层,隔绝基质与外部环境的接触;同时通过涂层的性能,来解决燃料消耗大、不耐磨、易结焦等问题。陶瓷涂层因具有抗氧化、耐高温腐蚀等性能,广泛运用于电厂锅炉,但是在使用陶瓷材料制作涂层时,在涂层厚度过大、受热不均匀时,涂层表面易出现裂纹等问题,其保护性能会随之受到破坏。
因此,亟需提供一种电厂锅炉受热面用的陶瓷涂料,具有耐腐蚀、耐磨损的性能,且喷涂后,涂层表面不易出现裂纹。
技术实现要素:
本发明旨在至少解决上述现有技术中存在的技术问题之一。为此,本发明提出一种电厂锅炉受热面用的陶瓷涂料,具有耐腐蚀、耐磨损的性能,且喷涂后,涂层表面不易出现裂纹。
一种陶瓷涂料,主要由钠水玻璃、低熔点玻璃粉、陶瓷晶须、氧化锆、磷酸锆、稀土和促凝剂组成;所述低熔点玻璃粉的熔点为300-420℃。
优选的,所述陶瓷涂料,按重量份计,主要由以下组分组成:
进一步优选的,所述陶瓷涂料,按重量份计,主要由以下组分组成:
优选的,所述钠水玻璃的模数≤3.5。
优选的,所述陶瓷晶须为氧化铝、碳化硅、氮化铝和氮化硅中的至少三种;进一步优选的,所述陶瓷晶须为氧化铝、碳化硅、氮化铝和氮化硅;更优选的,所述氧化铝、碳化硅、氮化铝和氮化硅的质量比为(3-5):(1-2):(1-2):(0.5-1)。当选择氧化铝、碳化硅、氮化铝和氮化硅晶须,且质量比为(3-5):(1-2):(1-2):(0.5-1)时,更易形成分布均匀、稳定的三维结构。
优选的,所述陶瓷晶须的直径为0.05-6μm,长度为50-200μm。具有较大长经比的晶须,在形成陶瓷相时更易形成网状结构,当陶瓷晶须的直径为0.05-6μm,长度为50-200μm,制得的陶瓷相性能更佳。
优选的,所述低熔点玻璃粉的熔点为350-400℃。采用低熔点玻璃粉,促进涂层在低温下自然转化为陶瓷相。
优选的,所述低熔点玻璃粉的粒径为5-10μm。
优选的,所述氧化锆的粒径10-45μm。
优选的,所述稀土选自镧(la)、铈(ce)、钆(gd)、铽(tb)中的至少三种;进一步优选的,所述稀土为镧(la)、铈(ce)、钆(gd)、铽(tb);所述镧(la)、铈(ce)、钆(gd)、铽(tb)的质量比为(1-2):(1-2):(1-2):(1-2)。
优选的,所述促凝剂为氟硅酸钠。
一种陶瓷涂料的制备方法,包括以下步骤:
(1)按配方称取低熔点玻璃粉、陶瓷晶须、氧化锆、磷酸锆和稀土,干燥,混合,得混合粉体。
(2)向步骤(1)制得的混合粉体中加入钠水玻璃,混合,即制得所述陶瓷涂料。
将各粉体在混合前进行干燥,使其混合更充分,同时干燥的粉体可以减少水分的影响。
钠水玻璃作为陶瓷先驱液和粘接剂,使混合粉体相互融合。
具体的,一种陶瓷涂料的制备方法,包括以下步骤:
(1)按配方称取低熔点玻璃粉、陶瓷晶须、氧化锆、磷酸锆、稀土,放入烘干炉中,于200℃下烘2小时,然后混合,得混合粉体。
(2)向步骤(1)制得的混合粉体中加入钠水玻璃,混合均匀,即制得所述陶瓷涂料。
相对于现有技术,本发明的有益效果如下:
(1)采用陶瓷晶须、氧化锆和磷酸锆作为陶瓷涂料的基本骨架,无需高温烧结,在400℃左右即可自然转化为陶瓷相,且陶瓷率达到75%以上;其中陶瓷晶须和氧化锆形成增强性3d网络结构,而磷酸锆通过了稳定的层状结构,分布于3d网络结构中,弥补陶瓷晶须和氧化锆可能因分布不均匀导致的不稳定,使得喷涂后形成的涂层稳定,耐腐蚀、耐磨损,耐磨性为20#钢5倍以上;在涂层厚度过大或受热不均匀时,也不会出现裂纹;且涂层表面致密光滑,熔融的灰粒不易黏附在受热面上,具有良好的抗沾、抗结焦性能。
(2)所述涂料制得的涂层具有较好的热导率,热导率高,可以很好地保持管壁表面的温度平衡,不会产生灰渣熔融粘接现象。
(3)所述陶瓷涂料的其制备方法简单,对设备要求低。
附图说明
图1为实施例1中使用一年后炉管的表面状况图;
图2为不喷涂陶瓷涂料使用一年后炉管的表面状况图。
具体实施方式
为了让本领域技术人员更加清楚明白本发明所述技术方案,现列举以下实施例进行说明。需要指出的是,以下实施例对本发明要求的保护范围不构成限制作用。
以下实施例中所用的原料、试剂或装置如无特殊说明,均可从常规商业途径得到,或者可以通过现有已知方法得到。
实施例1
(1)按配方称取低熔点玻璃粉、陶瓷晶须、氧化锆、磷酸锆和稀土,放入烘干炉中,于200℃下烘2小时,然后混合,得混合粉体。
(2)向混合粉体中加入钠水玻璃,混合均匀,即制得陶瓷涂料。
对锅炉管壁表面进行打磨、清洗处理,然后将制得的陶瓷涂料,采用雾化喷枪均匀喷涂在金属表面,喷涂压力为0.8mpa,涂层厚度为30-120μm。喷涂完成后,涂层自然干燥10h,待启炉后随炉升温固化,涂层不出现裂纹。
然后分别在锅炉连续使用180、270、365天时,对炉管的外观进行观察,如图1可知,在使用一年后仍然光亮如新,而未喷涂陶瓷涂料则表面腐蚀严重,如图2;为了检测其耐腐蚀性能,利用砂轮打磨炉管表面,至露出金属表面后,均匀取20个测点对管壁厚度进行测量,取平均值,结果表明,使用180天后炉管仅减薄0.05nm,使用270天后炉管仅减薄0.1nm,使用365天后炉管仅减薄0.15nm。
实施例2
(1)按配方称取低熔点玻璃粉、陶瓷晶须、氧化锆、磷酸锆和稀土,放入烘干炉中,于200℃下烘2小时,然后混合,得混合粉体。
(2)向步骤(1)制得的混合粉体中加入钠水玻璃,混合均匀,即制得陶瓷涂料。
对锅炉管壁表面进行打磨、清洗处理,然后将制得的陶瓷涂料,采用雾化喷枪均匀喷涂在金属表面,喷涂压力为0.8mpa,涂层厚度为30-120μm。喷涂完成后,涂层自然干燥10h,待启炉后随炉升温固化,涂层不出现裂纹。
然后分别在锅炉连续使用180、270、365天时,对炉管的外观进行观察,在使用一年后仍然光亮如新;为了检测其耐腐蚀性能,利用砂轮打磨炉管表面,至露出金属表面后,均匀取20个测点对管壁厚度进行测量,取平均值,结果表明,使用180天后炉管仅减薄0.08nm,使用270天后炉管仅减薄0.15nm,使用365天后炉管仅减薄0.2nm。
实施例3
(1)按配方称取低熔点玻璃粉、陶瓷晶须、氧化锆、磷酸锆和稀土,放入烘干炉中,于200℃下烘2小时,然后混合,得混合粉体。
(2)向步骤(1)制得的混合粉体中加入钠水玻璃,混合均匀,即制得陶瓷涂料。
对锅炉管壁表面进行打磨、清洗处理,然后将制得的陶瓷涂料,采用雾化喷枪均匀喷涂在金属表面,喷涂压力为0.8mpa,涂层厚度为30-120μm。喷涂完成后,涂层自然干燥10h,待启炉后随炉升温固化,涂层不出现裂纹。
然后分别在锅炉连续使用180、270、365天时,对炉管的外观进行观察,在使用一年后仍然光亮如新;为了检测其耐腐蚀性能,利用砂轮打磨炉管表面,至露出金属表面后,均匀取20个测点对管壁厚度进行测量,取平均值,结果表明,使用180天后炉管仅减薄0.1nm,使用270天后炉管仅减薄0.15nm,使用365天后炉管仅减薄0.2nm。
实施例4
(1)按配方称取低熔点玻璃粉、陶瓷晶须、氧化锆、磷酸锆和稀土,放入烘干炉中,于200℃下烘2小时,然后混合,得混合粉体。
(2)向步骤(1)制得的混合粉体中加入钠水玻璃,混合均匀,即制得所述陶瓷涂料。
对锅炉管壁表面进行打磨、清洗处理,然后将制得的陶瓷涂料,采用雾化喷枪均匀喷涂在金属表面,喷涂压力为0.8mpa,涂层厚度为30-120μm。喷涂完成后,涂层自然干燥10h,待启炉后随炉升温固化,涂层不出现裂纹。
然后分别在锅炉连续使用180、270、365天时,对炉管的外观进行观察,在使用一年后仍然光亮如新;为了检测其耐腐蚀性能,利用砂轮打磨炉管表面,至露出金属表面后,均匀取20个测点对管壁厚度进行测量,取平均值,结果表明,使用180天后炉管仅减薄0.05nm,使用270天后炉管仅减薄0.1nm,使用365天后炉管仅减薄0.15nm。
实施例5
(1)按配方称取低熔点玻璃粉、陶瓷晶须、氧化锆、磷酸锆和稀土,放入烘干炉中,于200℃下烘2小时,然后混合,得混合粉体。
(2)向步骤(1)制得的混合粉体中加入钠水玻璃,混合均匀,即制得所述陶瓷涂料。
对锅炉管壁表面进行打磨、清洗处理,然后将制得的陶瓷涂料,采用雾化喷枪均匀喷涂在金属表面,喷涂压力为0.8mpa,涂层厚度为30-120μm。喷涂完成后,涂层自然干燥10h,待启炉后随炉升温固化,涂层不出现裂纹。
然后分别在锅炉连续使用180、270、365天时,对炉管的外观进行观察,在使用一年后仍然光亮如新;为了检测其耐腐蚀性能,利用砂轮打磨炉管表面,至露出金属表面后,均匀取20个测点对管壁厚度进行测量,取平均值,结果表明,使用180天后炉管仅减薄0.1nm,使用270天后炉管仅减薄0.15nm,使用365天后炉管仅减薄0.25nm。
对比例1
(1)按配方称取低熔点玻璃粉、陶瓷晶须、氧化锆和稀土,放入烘干炉中,于200℃下烘2小时,然后混合,得混合粉体。
(2)向混合粉体中加入钠水玻璃,混合均匀,即制得陶瓷涂料。
对锅炉管壁表面进行打磨、清洗处理,然后将制得的陶瓷涂料,采用雾化喷枪均匀喷涂在金属表面,喷涂压力为0.8mpa,涂层厚度为30-120μm。喷涂完成后,涂层自然干燥10h,待启炉后随炉升温固化,涂层有裂纹。
然后分别在锅炉连续使用180、270、365天时,对炉管的外观进行观察,在使用一年后仍然光亮如新;为了检测其耐腐蚀性能,利用砂轮打磨炉管表面,至露出金属表面后,均匀取20个测点对管壁厚度进行测量,取平均值,结果表明,使用180天后炉管减薄0.55nm,使用270天后炉管减薄0.75nm,使用365天后炉管减薄1.15nm。
对比例2
(1)按配方称取低熔点玻璃粉、陶瓷晶须、氧化锆和磷酸锆,放入烘干炉中,于200℃下烘2小时,然后混合,得混合粉体。
(2)向混合粉体中加入钠水玻璃,混合均匀,即制得陶瓷涂料。
对锅炉管壁表面进行打磨、清洗处理,然后将制得的陶瓷涂料,采用雾化喷枪均匀喷涂在金属表面,喷涂压力为0.8mpa,涂层厚度为30-120μm。喷涂完成后,涂层自然干燥10h,待启炉后随炉升温固化,涂层出现轻微裂纹。
然后分别在锅炉连续使用180、270、365天时,对炉管的外观进行观察,在使用一年后仍然光亮如新;为了检测其耐腐蚀性能,利用砂轮打磨炉管表面,至露出金属表面后,均匀取20个测点对管壁厚度进行测量,取平均值,结果表明,使用180天后炉管减薄0.45nm,使用270天后炉管减薄0.65nm,使用365天后炉管减薄1.25nm。
起点商标作为专业知识产权交易平台,可以帮助大家解决很多问题,如果大家想要了解更多知产交易信息请点击 【在线咨询】或添加微信 【19522093243】与客服一对一沟通,为大家解决相关问题。
此文章来源于网络,如有侵权,请联系删除


