一种打磨机头壳压铸模具的制作方法



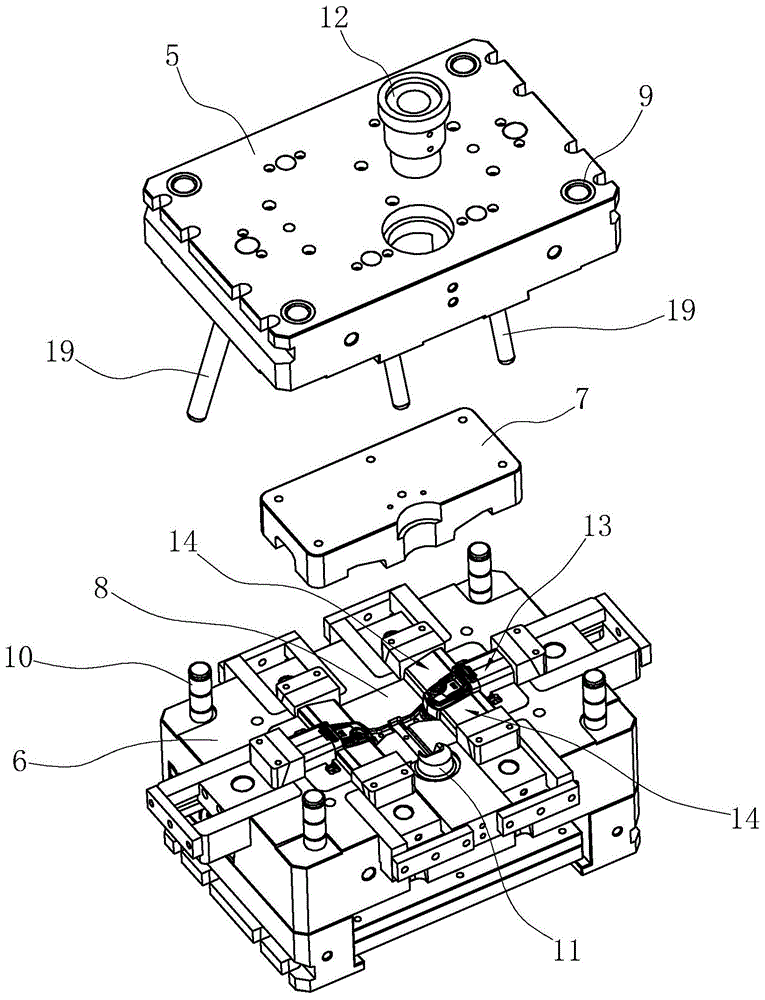
本实用新型涉及压铸模具技术领域,尤其是涉及一种打磨机头壳压铸模具。
背景技术:
目前,压铸模具主要由静模框、静模仁、动模框、动模仁、进料机构、导向机构等组成,动模框和静模框相对运动使得静模仁和动模仁对贴形成模腔,通过将熔化的金属液注入模腔中,冷却后得到具有模腔形状的产品。
如图5为一种打磨机的头壳产品,包括头壳本体1,头壳本体1相对称的两侧壁均设有第一安装孔2,头壳本体1的开口侧设有主轴安装孔3以及位于周边的四个第二安装孔4,由于结构复杂,模具的抽芯难度较大。
技术实现要素:
针对现有技术存在的不足,本实用新型的目的是提供一种用于铸造上述产品的打磨机头壳压铸模具,可在压铸完成后实现抽芯。
本实用新型的上述实用新型目的是通过以下技术方案得以实现的:一种打磨机头壳压铸模具,包括静模框、静模仁、动模框、动模仁、导向机构,动模仁和静模仁对贴至少形成一个产品型腔,每个产品型腔对应设置有一对对称设置的侧型芯以及一个主型芯,侧型芯和主型芯均滑动连接于静模仁和动模仁之间;侧型芯前端设有与头壳本体两对称侧壁的内凹部分相适配的结构;主型芯设有与头壳本体开口侧内壁相适配的结构;所述主型芯和侧型芯均连接有滑动连接于动模框上的联动件,所述静模框与联动件之间设有驱动联动件滑动的驱动结构。
通过采用上述技术方案,主型芯和侧型芯均可以随着联动件滑动从而在动模仁和静模仁之间滑动,静模框与联动件之间设有驱动联动件滑动的驱动结构,通过该驱动结构可实现,当动模框向静模框一侧运动时,驱动结构驱动联动件向动模仁和静模仁所在侧滑动,从而带动主型芯和侧型芯滑动至动模仁及静模仁的指定位置,通过主型芯、侧型芯前端的结构与动模仁和静模仁内壁结构共同构成与头壳本体形状相同的模腔,在铸造完成后,动模框向远离静模框的一侧移动,驱动结构驱动联动件向远离动模仁的一侧滑动,从而将主型芯及侧型芯抽离铸造好的头壳本体,完成抽芯,便于产品从动模仁上取下。
本实用新型在一较佳示例中可以进一步配置为:所述动模框上固定连接有滑轨,所述联动件为滑块,所述滑块滑动连接于滑轨。
通过采用上述技术方案,通过滑轨限定滑块的滑动轨迹,使得滑块滑动方向更加准确。
本实用新型在一较佳示例中可以进一步配置为:所述驱动结构包括设置于滑块上倾斜设置的导孔以及固定于静模框上与导孔配合的斜杆。
通过采用上述技术方案,在动模框向静模框所在一侧运动直至斜杆插入斜孔时,由于动模框运动轨迹固定,因此通过斜杆与导孔的导向作用,可利用斜杆推动滑块在滑轨上滑动,当动模框远离静模框时,也可通过斜杆推动滑块向远离动模仁的方向滑动直至斜杆离开导孔。
本实用新型在一较佳示例中可以进一步配置为:所述滑轨的外端设置有限位板。
通过采用上述技术方案,限位板可用于限定滑块向外滑动的极限位置。
本实用新型在一较佳示例中可以进一步配置为:所述主型芯和侧型芯均包括有芯体和芯杆,芯体上设有穿设孔,所述芯杆穿设连接于芯体上,所述穿设孔朝向滑块的一端边沿设有沉槽,所述芯杆的外端设有大小与沉槽适配的端头,所述端头抵接于滑块,所述芯体和滑块通过螺栓连接。
通过采用上述技术方案,芯杆的长度通常较长,通常用于在产品上成型出各类安装孔,通常较为深入动模仁内,受到金属熔液压力较大,发生开裂失效的几率较高,因此将芯体和芯杆分体并组合的方式,可对失效芯杆进行更换,节约维护成本。芯杆穿设连接于穿设孔且通过端头与沉槽进行限位,使芯杆的安装更为便利,芯体和滑块通过螺栓连接,取下螺栓之后,即可将芯体和芯杆分离,操作方便。
本实用新型在一较佳示例中可以进一步配置为:所述滑块上设有定位槽,所述芯体上设有定位块。
通过采用上述技术方案,通过定位块与定位槽方便将芯体和滑块准确组合安装。
本实用新型在一较佳示例中可以进一步配置为:所述动模仁和静模仁对贴形成两个产品型腔,两个产品型腔关于动模仁的垂直中心线中心对称。
通过采用上述技术方案,可同时对两个产品进行铸造,提高生产效率。
本实用新型在一较佳示例中可以进一步配置为:所述导向机构包括设置于静模框边角处的导套以及设置于动模框边角处的导柱。
通过采用上述技术方案,导柱和导套形成滑动限位,使得动模框与静模框配合更准确。
综上所述,本实用新型包括以下至少一种有益技术效果:
1.可实现本打磨机头壳铸造产品的抽芯操作;
2.芯体和芯杆为组合形式,方便损坏部件的局部更换,降低维护成本。
附图说明
图1是本实施例的爆炸示意图;
图2是本实施例动模框相关部分的结构示意图;
图3是本实施例合模过程的状态示意图;
图4是本实施例凸显芯体和芯杆连接结构的爆炸示意图;
图5是本实施例所铸造产品的结构示意图。
附图标记:1、头壳本体;2、第一安装孔;3、主轴安装孔;4、第二安装孔;5、静模框;6、动模框;7、静模仁;8、动模仁;9、导套;10、导柱;11、分流锥;12、进料筒;13、主型芯;14、侧型芯;15、滑轨;16、滑块;17、限位板;18、导孔;19、斜杆;20、让位槽;21、芯体;22、芯杆;23、沉槽;24、端头;25、定位块;26、定位槽;27、螺纹孔;28、沉孔;29、穿设孔。
具体实施方式
以下结合附图对本实用新型作进一步详细说明。
参照图1,为本实用新型公开的一种打磨机头壳压铸模具,用于铸造图5所示的打磨机头壳产品,其包括头壳本体1,头壳本体1相对称的两侧壁均设有第一安装孔2,头壳本体1的开口侧设有主轴安装孔3以及位于周边的四个第二安装孔4。
如图1所示,本实施例所述打磨机头壳压铸模具包括静模框5、静模仁7、动模框6、动模仁8,静模仁7安装于静模框5上,动模仁8安装于动模框6上。静模框5的四个边角处安装有导套9,动模框6的四个边角处安装有导柱10,导柱10可与导套9配合滑动。动模仁8和静模仁7对贴形成有两个产品型腔,动模框6靠近动模仁8的位置设置有分流锥11,静模框5上安装有进料筒12,动模仁8和静模仁7对贴时,进料筒12封闭于分流锥11周侧,分流锥11与产品型腔连通,通过进料筒12可将金属熔液分流注入两个产品型腔,两个产品型腔关于动模仁8的垂直中心线中心对称。
如图2所示,每个产品型腔对应设置有一对对称设置的侧型芯14以及一个主型芯13,侧型芯14和主型芯13均滑动连接于静模仁7和动模仁8之间;侧型芯14前端设有与头壳本体1两对称侧壁的内凹部分相适配的结构;主型芯13设有与头壳本体1开口侧内壁相适配的结构。通过主型芯13前端、侧型芯14前端的结构与动模仁8和静模仁7内壁结构共同构成与头壳本体1形状相同的模腔。主型芯13和侧型芯14均连接有滑动连接于动模框6上的联动件,静模框5与联动件之间设有驱动联动件滑动的驱动结构。动模框6上固定连接有滑轨15,联动件为滑块16,滑块16滑动连接于滑轨15,滑轨15的外端设置有限位板17。
如图2、3所示,驱动结构包括设置于滑块16上呈倾斜设置的导孔18以及固定于静模框5上与导孔18配合的斜杆19。滑轨15限定滑块16的滑动方向仅为朝向动模仁8或远离动模仁8,在动模仁8上设置让位槽20,在动模仁8和静模仁7对贴时供斜杆19放置。
合模过程参照图2、3所示,当动模框6向静模框5方向运动时,斜杆19将插入对应的滑块16的导孔18内,导孔18与斜杆19是适配的,动模框6与静模框5通过导套9和导柱10定位仅限相对或背离运动,当动模块继续向静模框5所在侧移动时,斜杆19将推动滑块16向动模仁8所在侧滑动,从而同步推动主型芯13和侧型芯14运动,当动模仁8和静模仁7对贴时,主型芯13和侧型芯14也刚好移动到既定位置,从而与动模仁8和静模仁7内壁结构共同构成与头壳本体1形状相同的模腔。当动模框6远离静模框5运动时,斜杆19则推动滑块16向远离动模仁8的方向运动直至斜杆19离开导孔18,使得滑块16带动主型芯13和侧型芯14向远离动模仁8的方向滑动,达到抽芯目的。
如图4、5所示,优选的,主型芯13和侧型芯14均包括有芯体21和芯杆22,芯体21上设有穿设孔29,芯杆22穿设连接于芯体21上,穿设孔29朝向滑块16的一端边沿设有沉槽23,芯杆22的外端设有大小与沉槽23适配的端头24,端头24抵接于滑块16,芯体21和滑块16通过螺栓连接,芯体21上设有螺纹孔27,滑块16上设有供螺栓穿设的沉孔28。本实施例中,主型芯13的芯杆22用于成型出头壳本体1上的主轴安装孔3和第二安装孔4;侧型芯14上的芯杆22用于成型出头壳本体1上的第一安装孔2。滑块16上设有定位槽26,芯体21上设有定位块25。将芯体21和滑块16进行拆卸后,可对芯杆22进行更换。
本具体实施方式的实施例均为本实用新型的较佳实施例,并非依此限制本实用新型的保护范围,故:凡依本实用新型的结构、形状、原理所做的等效变化,均应涵盖于本实用新型的保护范围之内。
起点商标作为专业知识产权交易平台,可以帮助大家解决很多问题,如果大家想要了解更多知产交易信息请点击 【在线咨询】或添加微信 【19522093243】与客服一对一沟通,为大家解决相关问题。
此文章来源于网络,如有侵权,请联系删除


