电沉积法与溶胶凝胶法相结合制备CZTS吸收层的方法与流程



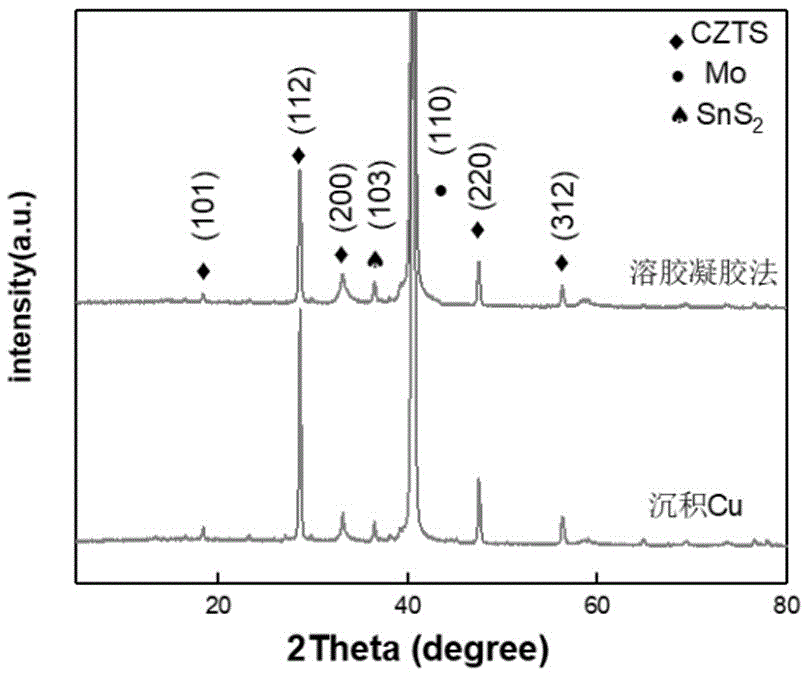
本发明涉及太阳电池领域,具体涉及电沉积法与溶胶凝胶法相结合制备czts吸收层的方法。
背景技术:
化合物半导体薄膜太阳电池以cigs、czts、cdte等直接带隙材料为吸收层,具有很高的光吸收系数(高达104-105cm-1),因此吸收层厚度只需1-2μm即可吸收大部分入射太阳光,吸收层材料的使用量大大减少。同时,cigs、czts和cdte材料的晶界不是活跃的复合中心,因此只需制备多晶材料作为吸收层,制备过程消耗的能量更少,可以降低制造成本,这就使得化合物半导体具有广泛的应用前景。其中,cigs和cdte太阳电池具有较高的光电转换效率,目前最高效率分别达到了22.9%和22.1%。然而,in和ga是稀有元素,在地球上储量较少,使得cigs的大规模商业化发展受到限制。另外,cd是有毒重金属,使得cdte太阳电池在一些国家的推广遇到了阻力。因此,目前迫切需要发展一种新型的太阳电池来满足日益增长的能源需求。cu2znsns4(czts)是一种很有前景的薄膜太阳电池吸收层材料。带隙范围合适,通过调节薄膜中的s元素和se元素的比例可实现薄膜带隙宽度在1.0~1.5ev之间连续调整;吸收系数高,可大于104cm-1,因此czts基太阳电池的吸收层厚度只需1~2μm,可以节省材料,制备柔性薄膜太阳电池。此外,czts不含任何有毒或稀缺元素,成本低、无污染。基于这些潜在的优势,使得czts受到了广泛关注,具有广阔的发展前景。
就生产成本而言,廉价且易于大规模生产的光伏吸收层的研究发展很大程度上依赖于生长技术,通常分为真空和非真空两种。基于真空法的制备过程主要包括在衬底上使用溅射法沉积薄膜和在一定的压力和温度下蒸发/共蒸发靶源。非真空类方法包括肼溶液、溶胶-凝胶、纳米颗粒等溶液涂覆法,及电化学沉积法,喷射热解沉积技术。基于旋涂工艺的溶胶-凝胶法是一种操作简单、成本低廉的制备工艺,对于各种半导体薄膜的制备,是一个值得考虑的选择,包括溶液前驱体、颗粒前驱体和混合粒子-溶液前驱体在内的这种直接液相沉积方法在工业上已经得到了很好的发展,对大面积制造具有重要的意义。
溶胶-凝胶法制备的czts薄膜在制备前驱体溶液这一步时,对铜源的选择要求较高,因为铜盐中的cu是二价的,二价cu2+无法溶解于某些有机溶剂中,这就必须同时考虑有机溶剂和铜源的选择,多次尝试、寻找合适的溶剂和溶质,加大实验成本。此外,由于二价cu2+与二价sn2+氧化还原反应速度较慢,往往需要搅拌五小时以上才能完全反应,延长实验时间。薄膜开裂也是溶胶凝胶法存在的一个显著问题:旋涂制备的湿凝胶中包裹着大量溶剂,烘烤干燥时凝胶体积收缩,产生应力,很容易引起薄膜开裂。涂的薄膜越厚开裂的越厉害,一般通过加入适量的添加剂防止薄膜开裂,但可能会引入更多有机物等杂质残留,也不是最好的解决办法。热力学分析表明,czts/mo界面可能不像cigs/mo界面那样化学稳定。czts电池中mos2层的厚度要明显大于cigs电池体系中mos2层的厚度,而mos2层厚度的增加不但恶化了电池的串联电阻(增加),而且相当于在吸收层和mo之间串联了一个反向的二级管,影响了电池性能。
技术实现要素:
本发明要解决的技术问题是提供一种电沉积法与溶胶凝胶法相结合制备czts吸收层的方法,至少能够克服cu源选择困难和制备前驱体溶液耗时较长的缺陷。
为解决以上技术问题,本发明采用的技术方案是:一种电沉积法与溶胶凝胶法相结合制备czts吸收层的方法,包括:
步骤一,在清洗干净的镀mo钠钙玻璃衬底上采用直流电沉积法电沉积一层cu;
步骤二,配制含有zn、sn和s的前驱体溶液;以氯化锌(zncl2)、氯化亚锡二水合物(sncl2·2h2o)、硫脲(sc(nh2)2)作为溶质,二甲基甲酰胺(n,n-dimethylformamide)作为溶剂,充分搅拌使其充分溶解,得到含有zn,sn和s的金属-硫脲络合物,所述金属-硫脲络合物与dmf发生水解—聚合反应,获得所述前驱体溶液;
步骤三,将步骤二所述的前驱体溶液旋涂在沉积cu的mo背电极上,获得前驱体薄膜;
步骤四,以硫粉和锡粉作为硫源和锡源,将步骤三所得前驱体薄膜在真空环境下进行硫化退火处理,获得czts吸收层薄膜。
进一步地,步骤一中,直流电沉积法电沉积cu的具体步骤如下:将镀mo钠钙玻璃衬底清洗干净后,在cuso4水溶液中沉积cu层,电沉积实验条件包括以下几组参数:沉积时间8s,沉积电流1a,沉积电量8c;沉积时间6s,沉积电流1a,沉积电量6c;沉积时间5s,沉积电流1a,沉积电量5c。
进一步地,步骤二中,前驱体溶液制备过程如下:先将二甲基甲酰胺溶剂放入玻璃瓶中,再放入氯化亚锡二水合物(sncl2·2h2o),放在搅拌台上搅拌至sncl2完全溶解;再放入氯化锌(zncl2),搅拌至完全溶解;最后放入硫脲,完全反应后获得所述前驱体溶液。
进一步地,步骤三中,旋涂前驱体溶液于沉积cu的mo背电极后,置于300℃下预加热烘烤,然后室温冷却,重复旋涂、预加热、室温冷却过程。
进一步地,步骤三中,使用滴管吸取前驱体溶液,滴在沉积cu的mo背电极上,使其完全覆盖表面;启动匀胶机,转速为低速800r/min,时间为5s;再到达高速旋涂模式,高速3500r/min,时间为20s。
进一步地,步骤三中,重复旋涂、预加热、室温冷却过程10次。
进一步地,其特征在于,步骤四中,退火处理的过程如下:将前驱体薄膜样品置于陶瓷舟上,加入硫粉和锡粉,然后将陶瓷舟放入双温区管式炉中,关闭进气阀和出气阀,在真空条件下进行退火。
进一步地,设定双温区管式炉升温曲线为25分钟内从室温线性变化至620℃,保温,然后自然冷却至室温。
进一步地,在620℃下退火之前,先在200℃下加热退火,设定双温区管式炉升温曲线为10分钟内从室温线性变化至200℃,并保温20分钟,然后自然冷却至室温。
进一步地,步骤四中,退火处理的过程如下:将前驱体样品置于陶瓷舟上,加入1g硫粉和1.78g锡粉,然后将陶瓷舟放入双温区管式炉中,实验开始之前,先抽真空20min,然后打开进气阀和出气阀,通20min氩气。
本发明是通过直接在mo背电极上电沉积一层cu,将cu源从溶胶凝胶法中的铜盐溶质变成电沉积后的铜单质,具有以下有益技术效果:(1)避免了铜盐选择上的困难、解决了二价cu2+与二价sn2+氧化还原反应速度较慢,制备前驱体溶液时间较长的问题。(2)本发明提高了薄膜的附着力,使薄膜不易脱落,稳定性强。(3)本发明通过电沉积一层cu,相当于在czts和mo背电极之间加了一层阻挡层,退火过程中,s想穿过吸收层到达mo背电极和mo反应生成mos2,就要先越过cu层,就要先和cu反应生成cu2s,这就减少了到达mo背电极的s量,从而有效地减薄了mos2的厚度。
附图说明
图1为对比例1和实施例1制备的吸收层薄膜x射线衍射谱。
图2为对比例1和实施例1制备的吸收层薄膜拉曼光谱。
图3为对比例1和实施例1制备的吸收层薄膜表面形貌图。
图4为对比例1和实施例1制备的吸收层薄膜横截面形貌图和去除吸收层后的拉曼光谱图。
具体实施方式
本发明一种典型的实施方式提供的电沉积法与溶胶凝胶法相结合制备czts吸收层的方法,包括以下步骤。
步骤一,在清洗干净的镀mo钠钙玻璃衬底上采用直流电沉积法电沉积一层cu;
步骤二,配制含有zn、sn和s的前驱体溶液;以氯化锌(zncl2)、氯化亚锡二水合物(sncl2·2h2o)、硫脲(sc(nh2)2)作为溶质,二甲基甲酰胺(n,n-dimethylformamide)作为溶剂,充分搅拌使其充分溶解,得到含有zn,sn和s的金属-硫脲络合物,所述金属-硫脲络合物与dmf发生水解—聚合反应,获得所述前驱体溶液。
步骤三,将步骤二所述的前驱体溶液旋涂在沉积cu的mo背电极上,获得前驱体薄膜;
步骤四,以硫粉和锡粉作为硫源和锡源,将步骤三所得前驱体薄膜在真空环境下进行硫化退火处理,获得czts吸收层薄膜。
电沉积法可以使用低成本溶液高效大面积沉积薄膜,低投入,高产出,并且高质量,只需合适的电源、电极,而且只要主盐不断补充溶液可循环利用。成本低,浪费少,沉积速率可控,材料利用率高,电沉积材料利用率在90%以上。
本发明的构思是将电沉积法和溶胶凝胶法结合得到制备czts薄膜,本发明是通过直接在mo背电极上电沉积一层cu,将cu源从溶胶凝胶法中的铜盐溶质变成电沉积后的铜单质。结果表明,在电沉积cu的mo上旋涂退火制备的czts吸收层,相比于单纯的溶胶凝胶法,大大缩短了实验时间;得到的薄膜附着力好,结晶性好,晶粒生长均匀,并且显著减薄了mos2的厚度,有益于器件性能的提高。
上述实施方式中,优选地,步骤一中,镀mo钠钙玻璃衬底通过如下步骤清洗:将mo片切成4×6(单位:cm)尺寸,放入玻璃器皿中,先倒入酒精,放入超声波清洗器中超声清洗15min;取出,再放入去离子水,放入超声波清洗器中超声清洗15min。直到去除mo表面残留的灰尘污染和油渍。
作为优选的实施方式,步骤一中,直流电沉积法电沉积cu的具体步骤如下:将镀mo钠钙玻璃衬底清洗干净后,在cuso4水溶液中沉积cu层,电沉积实验条件包括以下几组参数:沉积时间5-8s,沉积电流1a,沉积电量5-8c。根据不同电沉积cu的时间进行选择的,前驱体溶液中,zn,sn和s的摩尔比分别为:当cu沉积时间为8s时,zn/sn=1.75,s/金属元素=2.8;当cu沉积时间为6s时,zn/sn=3.25,s/金属元素=1.8;当cu沉积时间为5s时,zn/sn=1.59,s/金属元素=3。
作为优选的实施方式,步骤二中,前驱体溶液制备过程如下:先将二甲基甲酰胺溶剂放入玻璃瓶中,再放入氯化亚锡二水合物(sncl2·2h2o),放在搅拌台上搅拌至sncl2完全溶解;再放入氯化锌(zncl2),搅拌至完全溶解;最后放入硫脲,完全反应后获得所述前驱体溶液。先放入氯化亚锡二水合物(sncl2·2h2o),使得放入的氯化锌(zncl2)更好更快速的溶解;最后放入硫脲可以使zn源和sn源溶质更容易与之反应生成金属-硫脲络合物,这一放置顺序加快了zn的溶解速度和络合反应的进行。
作为优选的实施方式,步骤三中,旋涂前驱体溶液于沉积cu的mo背电极后,置于300℃下预加热烘烤,其目的是:一方面可以使前驱体溶液较好的附着在mo上;另一方面,可以使有机溶剂分解挥发,避免高温硫化时生成较厚的碳层。然后室温冷却,重复旋涂、预加热、室温冷却过程。
作为优选的实施方式,步骤三中,使用滴管吸取前驱体溶液,滴在沉积cu的mo背电极上,使其完全覆盖表面;启动匀胶机,转速为低速800r/min,时间为5s;再到达高速旋涂模式,高速3500r/min,时间为20s。先高速后低速可以使前驱体溶液更加均匀的涂覆在mo衬底上,从而生成均匀平整的czts预制层。
作为优选的实施方式,步骤三中,重复旋涂、预加热、室温冷却过程10次。
作为优选的实施方式,步骤四中,退火处理的过程如下:将前驱体薄膜样品置于陶瓷舟上,加入硫粉和锡粉,然后将陶瓷舟放入双温区管式炉中,关闭进气阀和出气阀,在真空条件下进行退火。s粉高温退火时生成s蒸汽,提供退火所需s气氛;额外的sn粉补给,可以防止高温退火过程中的sn损失。
作为优选的实施方式,设定双温区管式炉升温曲线为25分钟内从室温线性变化至620℃,保温,然后自然冷却至室温。
作为优选的实施方式,在620℃下退火之前,先在200℃下加热退火,目的是使薄膜中的有机物挥发,避免高温硫化后生成较厚的碳层。设定双温区管式炉升温曲线为10分钟内从室温线性变化至200℃,并保温20分钟,然后自然冷却至室温。
作为优选的实施方式,步骤四中,退火处理的过程如下:将前驱体样品置于陶瓷舟上,加入1g硫粉和1.78g锡粉,然后将陶瓷舟放入双温区管式炉中,实验开始之前,先抽真空20min,然后打开进气阀和出气阀,通20min氩气,目的是冲洗玻璃管,保持干净。
下面通过一些实施例对本发明要求保护的技术方案作进一步说明。但是,实施例和对比例是用于解释本发明实施方案,并不超出本发明主题的范围,本发明保护范围不受所述实施例的限定。除非另作特殊说明,本发明中所用材料、试剂均可从本领域商业化产品中获得。
对比例1
溶胶凝胶法制备czts吸收层薄膜,具体步骤如下:
(1)量取20ml二甲基甲酰胺有机溶剂,放入铜源:乙酸铜一水合物(cu(ch3coo)2·h2o),在加热条件下溶解1小时;再放入锡源:氯化亚锡二水合物(sncl2·2h2o),室温下搅拌五小时,待充分反应,放入锌源:氯化锌(zncl2),半小时后放入硫脲,充分搅拌一整夜,使金属离子与过量的硫脲发生络合作用,生成金属-硫脲络合物,然后金属-硫脲络合物与dmf发生水解—聚合反应,得到所需前驱体溶液。
(2)超声清洗并用n2气吹干镀mo钠钙玻璃衬底:超声清洗顺序依次为酒精和去离子水,分别超声15min,再用n2气吹干表面。
(3)步骤(2)的mo背电极上旋涂步骤(1)的前驱体溶液,并在热台上300℃烘烤2min,放在室温下自然冷却3min。其中旋涂条件为:转速和时间分别为:低速:800r/min,时间:5s;再到达高速旋涂模式,高速:3500r/min,时间:20s。重复旋涂步骤(1)的前驱体溶液10次,并烘烤冷却,得到czts前驱体薄膜。
(4)将步骤(3)所得前驱体薄膜进行退火处理,退火温度和时间:620℃,11min。
实施例1
电沉积法和溶胶凝胶法相结合制备czts吸收层的方法,具体步骤如下:
(1)超声清洗并用n2气吹干镀mo钠钙玻璃衬底:超声清洗顺序依次为酒精和去离子水,分别超声15min,再用n2气吹干表面。
(2)步骤(1)的mo背电极上电沉积一层cu:在cuso4水溶液中沉积cu层。电沉积实验条件为沉积cu的时间、电量、电流,沉积时间8s,沉积电流1a,沉积电量8c。
(3)量取20ml二甲基甲酰胺有机溶剂,再放入氯化亚锡二水合物(sncl2·2h2o),放在搅拌台上搅拌10min左右,sncl2完全溶解;再放入氯化锌(zncl2),搅拌10min,完全溶解;最后放入硫脲,20min中后与sncl2、zncl2完全反应,制得含zn、sn、s的前驱体溶液,该步骤中,zn、sn、s的摩尔比为zn/sn=1.75,s/金属元素=2.8。
(4)将步骤(3)所得前驱体溶液涂在步骤(2)的沉积cu的mo背电极上,并在热台上300℃烘烤2min,放在室温下自然冷却3min。其中旋涂条件为:转速和时间分别为:低速:800r/min,时间:5s;再到达高速旋涂模式,高速:3500r/min,时间:20s。重复旋涂步骤(3)的溶液10次,并烘烤冷却,得到czts前驱体薄膜。
(5)将步骤(4)获得的czts前驱体薄膜样品置于陶瓷舟上,加入1g硫粉和1.78g锡粉,然后将陶瓷舟放入双温区管式炉中。实验开始之前,先抽真空20min,然后打开进气阀和出气阀,通20min氩气,目的是冲洗玻璃管,保持干净。在620℃下退火之前,先在200℃下加热退火,目的是使薄膜中的有机物挥发,避免高温硫化后生成较厚的碳层。设定双温区管式炉升温曲线为10分钟内从室温线性变化至200℃,并保温20分钟,然后自然冷却至室温。
实施例2
与实施例1的区别在于电沉积实验中,沉积时间6s,沉积电流1a,沉积电量6c。zn/sn=3.25,s/金属元素=1.8。
实施例3
与实施例1的区别在于电沉积实验中,沉积时间5s,沉积电流1a,沉积电量5c。zn/sn=1.59,s/金属元素=3。
将对比例1和实施例1作对比,得出电沉积和溶胶凝胶法相结合在制备时间上的优势。通过具体的实验步骤可知,电沉积cu后再旋涂zn,sn,s溶液大大缩短了实验时间,降低了制备成本。电沉积cu所用的cuso4水溶液可以反复利用,电沉积cu的实验过程很快,只需要几秒就能结束。
图1为对比例1和实施例1所制备的czts吸收层薄膜的x射线衍射谱。两个图都与czts的标准衍射峰吻合,衍射峰的强度较高,表明样品结晶性较好。
图2为对比例1和实施例1所制备的czts吸收层薄膜的拉曼图谱。作为xrd的补充测试手段,拉曼散射也是鉴定czts薄膜结构和物相的有力工具。在337cm-1(a1model)处有明显的czts主拉曼散射峰,除此之外,也能分辨出287cm-1处的次峰。所有这些峰值都与文献中所述的czts拉曼峰非常吻合。
将对比例1和实施例1作对比,得出制备的薄膜在形貌上的区别。如图3所示为溶胶凝胶法和电沉积cu(时间:5s和6s)后旋涂zn,sn,s混合溶液制备的czts吸收层薄膜的sem表面图。由图可知,相比于单纯的溶胶凝胶法,结合了电沉积后的溶胶凝胶法,制备的薄膜更加致密,晶粒生长更加均匀。
对比实施例1和对比例1制备出的薄膜附着力的差异。用粘除法测试的两种薄膜的附着力差异。对比例1溶胶凝胶法制备的czts吸收层,很容易就粘下来,但是电沉积cu8s的条件下,制备的薄膜没有丝毫粘落,电沉积cu6s的条件下粘下来一点点,这是因为这个电沉积cu的时间导致cu较少,所以附着力会比电沉积cu8s的要差一些,但是也明显比溶胶凝胶法制备的czts吸收层附着力要好很多。可见,电沉积cu后再旋涂zn,sn,s混合溶液制备czts吸收层可以提高薄膜的附着力。
将对比例1和实施例1制备的薄膜作对比,得出关于减薄mos2层厚度的探究。图4为对比例1和实施例1所制备的吸收层薄膜的sem断面图以及去掉吸收层后的拉曼图谱。拉曼图谱证明断面图中,所示的mo上面的那一层就是mos2。因此通过断面图可明显看出mos2层的减薄,证明电沉积cu后再旋涂zn,sn,s溶液制备的czts吸收层可有效减薄mos2的厚度。
起点商标作为专业知识产权交易平台,可以帮助大家解决很多问题,如果大家想要了解更多知产交易信息请点击 【在线咨询】或添加微信 【19522093243】与客服一对一沟通,为大家解决相关问题。
此文章来源于网络,如有侵权,请联系删除


