锆石基硼硅酸盐玻璃陶瓷制备方法及对放射性核素固化的应用与流程



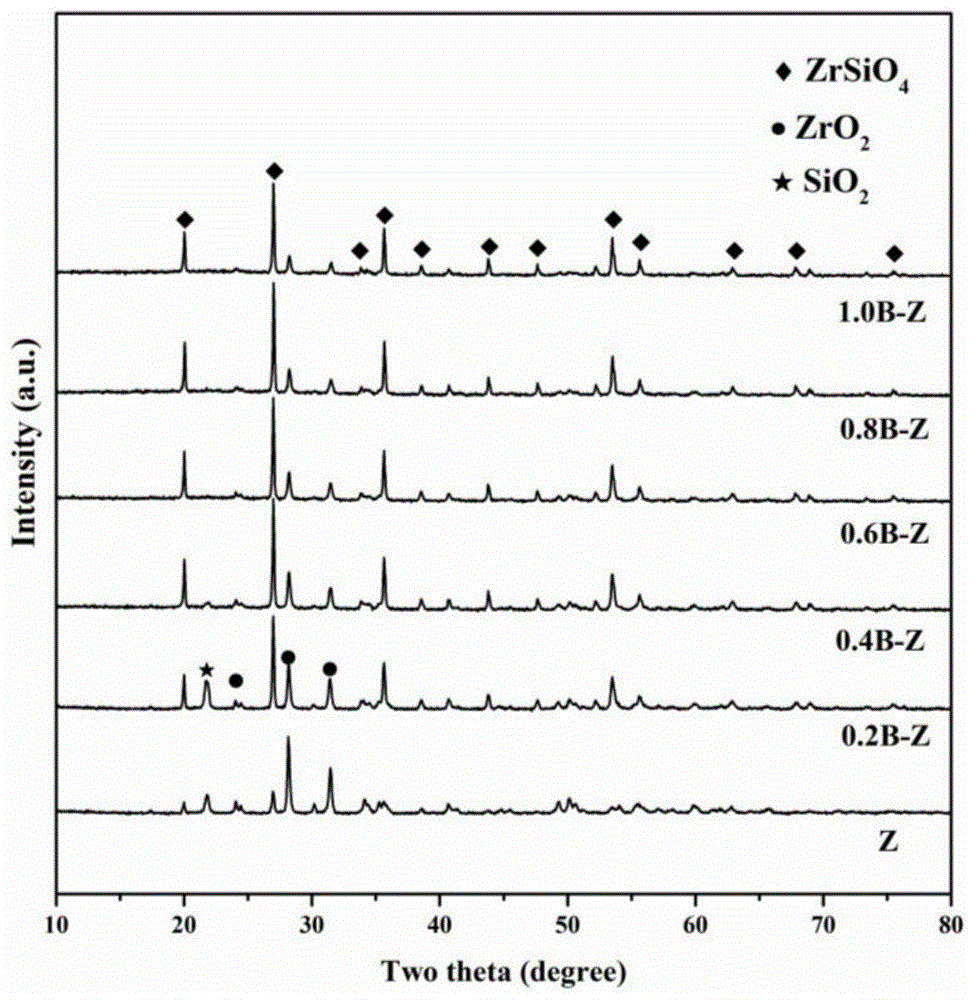
本发明属于放射性核素固化
技术领域:
,具体为一种锆石基硼硅酸盐玻璃陶瓷制备方法及对放射性核素固化的应用。
背景技术:
:高放废物(hlw)因存在放射性水平高、半衰期长、生物毒性大、释热量高、产生高能粒子及成份复杂等特点,其处理处置尤为棘手。此外,高放废物具有核素种类多、组分复杂(常含有大量裂变产物、后处理过程添加的化学成分等)及波动性大等特点。为了达到高放废物的安全有效固化处理,要求固化基材对核素种类、价态等具有良好的适应性,以及良好的致密性等。锆石(zrsio4)被认为是人造岩石(陶瓷)固化锕系核素的候选基材。综合国内外学者和项目组前期研究发现,zrsio4对特定核素(u、pu等)和模拟核素(nd、la、ce及eu等)具有一定的固化能力。然而,单相zrsio4陶瓷对固化处理核素具有较高的针对性,很难实现复杂组分放射性废物的同时固化处理,不具备良好的适应性,且核素固溶量也偏低。同时,单相zrsio4陶瓷固化体的合成相当困难,存在烧结温度高(1550-1700℃)、耗时(>48h)以及致密性差等问题。在实际高放废物固化处理过程中,固化体合成温度过高存在诸多不利。一方面,固化处理温度太高会造成低熔点放射性核素挥发,产生气溶胶,导致二次污染,不利于高放废物的有效固化处理;另一方面,高的固化处理温度对设备要求高,工艺苛刻。这些均严重制约高放废物陶瓷固化的工程化应用。因此,本发明旨在开发高合成率、高致密性锆石基硼硅酸盐玻璃陶瓷及其制备新方法。技术实现要素:本发明的目的是提供一种锆石基硼硅酸盐玻璃陶瓷制备方法。本发明针对单相zrsio4陶瓷核素适应性差、固溶量低、致密性差,以及其合成存在高温、耗时等问题,以硼硅酸盐玻璃为助剂制备高合成率、高致密性锆石基硼硅酸盐玻璃陶瓷,该方法具有低温、快速及高效等优点。本发明的一个目的是解决至少上述问题和/或缺陷,并提供至少后面将说明的优点。为了实现根据本发明的这些目的和其它优点,提供了一种锆石基硼硅酸盐玻璃陶瓷制备方法,包括以下步骤:步骤一、将原料na2co3、sio2、h3bo3和zro2混合后进行研磨;步骤二、将研磨后的原料烘干;步骤三、将烘干的原料置于热压烧结炉中,在压力为25~38mpa,温度为1000~1300℃条件下煅烧1~6h,得到锆石基硼硅酸盐玻璃陶瓷。优选的是,所述步骤一中na2co3、sio2、h3bo3和zro2的质量比为0.2~2.5:5~16:0.2~2.5:9~9.5。优选的是,所述步骤一中的研磨采用湿法球磨,湿法球磨采用的研磨介质为氧化锆球,采用的分散介质为乙醇、丙醇、异丙醇、异丁醇中的任意一种;所述研磨介质、原料、分散介质的质量比为2.5~3:1~1.5:1.2~1.5;研磨的时间为10~12小时;球磨采用的转速为200~500r/min。优选的是,采用的分散介质为醚与水的配制的混合液;所述醚为乙二醇单甲醚、丙二醇单乙醚、丁二醇单甲醚中的任意一种;所述醚与水的质量比为2~5:1。优选的是,所述步骤二中,烘干的温度为85~100℃,烘干时间为5~8小时。优选的是,所述步骤一中的研磨为低温球磨,其方法为:将原料na2co3、sio2、h3bo3和zro2混合后加入到球磨罐中,同时加入氧化锆磨球,向球磨罐中通入液氮,使原料以及氧化锆磨球全部浸没在液氮中,并保持液氮的挥发量与通入量平衡以使液面稳定;恒温15分钟后开始球磨,球磨10~12小时;将球磨后的粉体置于120~160℃的环境中进行氮脱附处理1~2小时,得到研磨后的原料;所述氧化锆磨球与原料的质量比为6~8:1;所述氧化锆磨球的直径为2~5mm;球磨采用的转速为200~500r/min。本发明提供了一种采用如上述的方法对放射性核素固化的应用,包括以下步骤:步骤ⅰ、将原料na2co3、sio2、h3bo3、zro2和ceo2混合后进行研磨;步骤ⅱ、将研磨后的原料烘干;步骤ⅲ、将烘干的原料置于热压烧结炉中,在压力为25~38mpa,温度为1000~1300℃条件下煅烧1~6h,得到0.2b-zr1-xcexsio4固化体,其中,0≤x≤0.15。优选的是,所述步骤ⅰ中na2co3、sio2、h3bo3、zro2和ceo2的质量比为0.45~0.48:6.5~6.8:0.45~0.5:7.5~9.5:0~2。优选的是,所述步骤ⅰ中的研磨采用湿法球磨,湿法球磨采用的研磨介质为氧化锆球,采用的分散介质为醚与水的配制的混合液;所述醚为乙二醇单甲醚、丙二醇单乙醚、丁二醇单甲醚中的任意一种;所述醚与水的质量比为2~5:1;所述研磨介质、原料、分散介质的质量比为2.5~3:1~1.5:1.2~1.5;研磨的时间为10~12小时;球磨采用的转速为200~500r/min;所述步骤ⅱ中,烘干的温度为85~100℃,烘干时间为5~8小时。优选的是,所述步骤ⅰ中的研磨为低温球磨,其方法为:将原料na2co3、sio2、h3bo3、zro2和ceo2混合后加入到球磨罐中,同时加入氧化锆磨球,向球磨罐中通入液氮,使原料以及氧化锆磨球全部浸没在液氮中,并保持液氮的挥发量与通入量平衡以使液面稳定;恒温15分钟后开始球磨,球磨10~12小时;将球磨后的粉体置于120~160℃的环境中进行氮脱附处理1~2小时,得到研磨后的原料;所述氧化锆磨球与两种原料的质量比为6~8:1;所述氧化锆磨球的直径为2~5mm;球磨采用的转速为200~500r/min。本发明至少包括以下有益效果:本发明在较低温度及较短时间下,以硼硅酸盐玻璃为助剂,可制得高合成率、高致密性的锆石基硼硅酸盐玻璃陶瓷固化基材,该方法大大提高锆石合成率、致密性,同时大大降低合成温度及缩短合成时间,节能高效,并且采用该方法对放射性核素进行固化,其放射性核素浸出率低,固化体具有较好的化学稳定性。本发明的其它优点、目标和特征将部分通过下面的说明体现,部分还将通过对本发明的研究和实践而为本领域的技术人员所理解。附图说明:图1为实施例(1)、实施例(3)、实施例(5)、实施例(7)、实施例(9)、实施例(11)制备的不同硼硅酸盐玻璃含量锆石基硼硅酸盐玻璃陶瓷(xb-z)的xrd图谱;图2实施例(1)制备的单相锆石的sem照片(z);图3为本发明实施例(11)制备的锆石基硼硅酸盐玻璃陶瓷(1.0b-z)的sem(b);图4为本发明实施例(11)制备的锆石基硼硅酸盐玻璃陶瓷(1.0b-z)的bse(c)照片图5为对比例(1)、对比例(2)、对比例(3)、对比例(4)、对比例(5)、对比例(6)制备的单相锆石基四价锕系核素固化体(zr1-xcexsio4)的xrd图谱;图6为实施例(14)、实施例(16)、实施例(19)、实施例(24)、实施例(25)、实施例(26)、实施例(27)、实施例(28)、实施例(29)制备的锆石基硼硅酸盐玻璃陶瓷四价锕系核素固化体(0.2b-zr1-xcexsio4)的xrd图谱;图7为对比例(5)单相锆石固化体(zr1-xcexsio4,x=0.04)和本发明实施例(26)锆石基硼硅酸盐玻璃陶瓷固化体(0.2b-zr1-xcexsio4,x=0.12)中ce的归一化浸出率。具体实施方式:下面结合附图对本发明做进一步的详细说明,以令本领域技术人员参照说明书文字能够据以实施。应当理解,本文所使用的诸如“具有”、“包含”以及“包括”术语并不配出一个或多个其它元件或其组合的存在或添加。实施例(1)~(11):一种锆石基硼硅酸盐玻璃陶瓷制备方法,包括以下步骤:步骤一、将原料na2co3、sio2、h3bo3和zro2分别按表1的配方混合后进行研磨;研磨采用湿法球磨,湿法球磨采用的研磨介质为氧化锆球,采用的分散介质为醚与水的配制的混合液;所述醚为丙二醇单乙醚;所述醚与水的质量比为3:1;所述研磨介质、原料、分散介质的质量比为2.8:1.2:1.5;研磨的时间为10小时;球磨采用的转速为300r/min;步骤二、将研磨后的原料烘干;烘干的温度为90℃,烘干时间为8小时;步骤三、将烘干的原料置于热压烧结炉中,在压力为35mpa,温度为1100℃条件下煅烧6h,得到锆石基硼硅酸盐玻璃陶瓷。表1图1为实施例(1)、实施例(3)、实施例(5)、实施例(7)、实施例(9)、实施例(11)制备的不同硼硅酸盐玻璃含量锆石基硼硅酸盐玻璃陶瓷(xb-z)的xrd图谱;如图1所示,硼硅酸盐玻璃含量对锆石基硼硅酸盐玻璃陶瓷的物相具有较大影响,随硼硅酸盐玻璃含量增加,zrsio4相的特征峰增强,原料相zro2和sio2特征峰减弱,表明烧结助剂(硼硅酸盐玻璃)可大大促进锆石相的合成。烧结条件为1100℃,6h时,未添加硼硅酸盐玻璃的纯锆石样品(z)中锆石的合成率较低(20%);当硼硅酸盐玻璃含量为50wt%时(样品1.0b-z),锆石相形成率可达98%;该结果表明,本发明以硼硅酸盐玻璃为烧结助剂,在较低温度(1100℃)、较短时间(6h)下,可制得高合成率、高致密性锆石基硼硅酸盐玻璃陶瓷固化基材。图2实施例(1)制备的单相锆石的sem照片(z),图3为本发明实施例(11)制备的锆石基硼硅酸盐玻璃陶瓷(1.0b-z)的sem(b);图4为本发明实施例(11)制备的锆石基硼硅酸盐玻璃陶瓷(1.0b-z)的bse(c)照片;比较图2和图3可以看出,本发明的锆石基硼硅酸盐玻璃陶瓷具有更致密的结构,玻璃相填充了锆石晶粒间的孔洞(图4),使锆石的致密性得到显著提高。然而,单相锆石陶瓷晶粒与晶粒之间存在大量孔洞,致密性较差。该结果表明,玻璃相对锆石的致密化具有促进作用,可显著提高所制备玻璃陶瓷的致密性。所制备的锆石基硼硅酸盐玻璃陶瓷结构致密,晶粒镶嵌紧密,孔洞较少,这些特征都是高放废物固化基材所追求的优良特性。实施例12:一种锆石基硼硅酸盐玻璃陶瓷制备方法,包括以下步骤:步骤一、将原料na2co3、sio2、h3bo3和zro2分别按表1中实施例(6)的配方混合后进行研磨;研磨采用低温球磨,其方法为:将原料na2co3、sio2、h3bo3和zro2混合后加入到球磨罐中,同时加入氧化锆磨球,向球磨罐中通入液氮,使原料以及氧化锆磨球全部浸没在液氮中,并保持液氮的挥发量与通入量平衡以使液面稳定;恒温15分钟后开始球磨,球磨10小时;将球磨后的粉体置于150℃的环境中进行氮脱附处理1.5小时,得到研磨后的原料;所述氧化锆磨球与原料的质量比为8:1;所述氧化锆磨球的直径为5mm;球磨采用的转速为300r/min;步骤二、将研磨后的原料烘干;烘干的温度为90℃,烘干时间为8小时;步骤三、将烘干的原料置于热压烧结炉中,在压力为35mpa,温度为1100℃条件下煅烧6h,得到锆石基硼硅酸盐玻璃陶瓷。实施例13:一种锆石基硼硅酸盐玻璃陶瓷制备方法,包括以下步骤:步骤一、将原料na2co3、sio2、h3bo3和zro2分别按表1中实施例(8)的配方混合后进行研磨;研磨采用低温球磨,其方法为:将原料na2co3、sio2、h3bo3和zro2混合后加入到球磨罐中,同时加入氧化锆磨球,向球磨罐中通入液氮,使原料以及氧化锆磨球全部浸没在液氮中,并保持液氮的挥发量与通入量平衡以使液面稳定;恒温15分钟后开始球磨,球磨10小时;将球磨后的粉体置于150℃的环境中进行氮脱附处理1.5小时,得到研磨后的原料;所述氧化锆磨球与原料的质量比为8:1;所述氧化锆磨球的直径为5mm;球磨采用的转速为300r/min;步骤二、将研磨后的原料烘干;烘干的温度为90℃,烘干时间为8小时;步骤三、将烘干的原料置于热压烧结炉中,在压力为35mpa,温度为1100℃条件下煅烧6h,得到锆石基硼硅酸盐玻璃陶瓷。表2实施例(1)~(13)制备的不同硼硅酸盐玻璃含量锆石基硼硅酸盐玻璃陶瓷的相对密度,从表2可以看出,随硼硅酸盐玻璃含量增加,锆石基硼硅酸盐玻璃陶瓷的密度增大,表明烧结助剂(硼硅酸盐玻璃)可大大提高产品的致密性。当硼硅酸盐玻璃含量为50wt%时,产品的相对密度可达理论密度的96%。该结果表明,本发明以硼硅酸盐玻璃为烧结助剂,在较低温度(1100℃)、较短时间(6h)下,可制得高致密性锆石基硼硅酸盐玻璃陶瓷固化基材。表2实施例相对密度(%)(1)z82.3(2)0.1b-z86.6(3)0.2b-z89.1(4)0.3b-z90.3(5)0.4b-z91.1(6)0.5b-z91.8(7)0.6b-z92.3(8)0.7b-z93.2(9)0.8b-z94.8(10)0.9b-z96.7(11)1.0b-z98.5(12)0.5b-z94.6(13)0.7b-z96.2实施例(14)~(29):一种采用采用上述的方法对放射性核素固化的应用,包括以下步骤:步骤ⅰ、将原料na2co3、sio2、h3bo3、zro2和ceo2分别按表3中的配方混合后进行研磨;研磨采用湿法球磨,湿法球磨采用的研磨介质为氧化锆球,采用的分散介质为醚与水的配制的混合液;所述醚为丙二醇单乙醚;所述醚与水的质量比为3:1;所述研磨介质、原料、分散介质的质量比为2.8:1.2:1.5;研磨的时间为10小时;球磨采用的转速为300r/min;步骤ⅱ、将研磨后的原料烘干;烘干的温度为90℃,烘干时间为8小时;步骤ⅲ、将烘干的原料置于热压烧结炉中,在压力为35mpa,温度为1100℃条件下煅烧6h,得到0.2b-zr1-xcexsio4固化体;表3实施例30:一种采用采用上述的方法对放射性核素固化的应用,包括以下步骤:步骤ⅰ、将原料na2co3、sio2、h3bo3、zro2和ceo2分别按表3中实施例(26)的配方混合后进行研磨;研磨采用低温球磨,其方法为:将原料na2co3、sio2、h3bo3、zro2和ceo2混合后加入到球磨罐中,同时加入氧化锆磨球,向球磨罐中通入液氮,使原料以及氧化锆磨球全部浸没在液氮中,并保持液氮的挥发量与通入量平衡以使液面稳定;恒温15分钟后开始球磨,球磨10小时;将球磨后的粉体置于150℃的环境中进行氮脱附处理1.5小时,得到研磨后的原料;所述氧化锆磨球与原料的质量比为8:1;所述氧化锆磨球的直径为5mm;球磨采用的转速为300r/min;步骤ⅱ、将研磨后的原料烘干;烘干的温度为90℃,烘干时间为8小时;步骤ⅲ、将烘干的原料置于热压烧结炉中,在压力为35mpa,温度为1100℃条件下煅烧6h,得到0.2b-zr1-xcexsio4固化体;该固化体中ce的浸出率(42天)为1.6×10-7gm-2d-1)。对比例(1)~(16):一种采用采用上述的方法对放射性核素固化的应用,包括以下步骤:步骤ⅰ、将原料sio2、zro2和ceo2分别按表4中的配方混合后进行研磨;研磨采用湿法球磨,湿法球磨采用的研磨介质为氧化锆球,采用的分散介质为醚与水的配制的混合液;所述醚为丙二醇单乙醚;所述醚与水的质量比为3:1;所述研磨介质、原料、分散介质的质量比为2.8:1.2:1.5;研磨的时间为10小时;球磨采用的转速为300r/min;步骤ⅱ、将研磨后的原料烘干;烘干的温度为90℃,烘干时间为8小时;步骤ⅲ、将烘干的原料置于热压烧结炉中,在压力为35mpa,温度为1100℃条件下煅烧6h,得到zr1-xcexsio4固化体;表4图5为对比例(1)、对比例(2)、对比例(3)、对比例(4)、对比例(5)、对比例(6)制备的单相锆石基四价锕系核素固化体(zr1-xcexsio4)的xrd图谱;图6为实施例(14)、实施例(16)、实施例(19)、实施例(24)、实施例(25)、实施例(26)、实施例(27)、实施例(28)、实施例(29)制备的锆石基硼硅酸盐玻璃陶瓷四价锕系核素固化体(0.2b-zr1-xcexsio4)的xrd图谱;从图5中可以看出,当x<0.04时,固化体样品为单一的锆石相结构;然而,当x≥0.04时,样品仍以锆石相为主,但同时出现了第二相ce2si2o7,为锆石相和ce2si2o7相两相共存结构。因此得出,单相锆石固化基材对四价模拟锕系核素ce4+的固溶量约为4at%。从图6可看出,当x<0.12时,固化体样品为单一的锆石相结构;然而,当x≥0.12时,样品仍以锆石相为主,但同时出现了第二相ce2si2o7,为锆石相和ce2si2o7相两相共存结构。因此得出,锆石基硼硅酸盐玻璃陶瓷对四价模拟锕系核素ce4+的固溶量约为12at%。这些结果表明,本发明锆石基硼硅酸盐玻璃陶瓷对四价模拟锕系核素ce4+的固溶量(12at%)远大于单相锆石(4at%)固化基材,锆石基硼硅酸盐玻璃陶瓷具有较好的放射性核素固化能力。图7为对比例(5)单相锆石固化体(zr1-xcexsio4,x=0.04)和本发明实施例(26)锆石基硼硅酸盐玻璃陶瓷固化体(0.2b-zr1-xcexsio4,x=0.12)中ce的归一化浸出率;从图7中可以看出,本发明实施例(26)锆石基硼硅酸盐玻璃陶瓷固化体中ce的浸出率(3.6×10-7gm-2d-1)远低于对比例(5)单相锆石固化体(6.9×10-6gm-2d-1)。该结果表明,本发明锆石基硼硅酸盐玻璃陶瓷固化体具有较好的化学稳定性。总之,本发明的锆石基硼硅酸盐玻璃陶瓷具有合成温度低,时间短,致密性好,核素固溶量高,化学稳定性好,是一种良好的放射性核素固化基材。其中,固化体的浸出实验过程为:采用静态浸出试验(mcc-1)的方法获得固化体的浸出率数据。制备的固化体被悬挂于100毫升装有去离子水的聚四氟乙烯内衬不锈钢反应釜中,反应釜置于烘箱中。根据gb7023-86,使用mcc-1方法,在40℃条件下,不同间隔时间(1,3,7,14,21,28,35和42天)进行固化体浸出试验。ce离子浓度(ci)用感应耦合等离子体质谱仪(icp-ms,安捷伦7700x,安捷伦,美国)进行分析。元素的归一化浸出率(lri,gm-2d-1)由以下等式计算:式中,ci是元素i在溶液中的浓度(g/m3),v是浸出液的体积(m3),s是陶瓷的表面积(m2),fi是元素i的在陶瓷中的质量分数((wt.%))和tn为浸出时间(d)。尽管本发明的实施方案已公开如上,但其并不仅仅限于说明书和实施方式中所列运用,它完全可以被适用于各种适合本发明的领域,对于熟悉本领域的人员而言,可容易地实现另外的修改,因此在不背离权利要求及等同范围所限定的一般概念下,本发明并不限于特定的细节和这里示出与描述的图例。当前第1页1 2 3 
起点商标作为专业知识产权交易平台,可以帮助大家解决很多问题,如果大家想要了解更多知产交易信息请点击 【在线咨询】或添加微信 【19522093243】与客服一对一沟通,为大家解决相关问题。
此文章来源于网络,如有侵权,请联系删除



tips