一种具有仿真效果的石材干粒、岩板及其制备方法和应用与流程



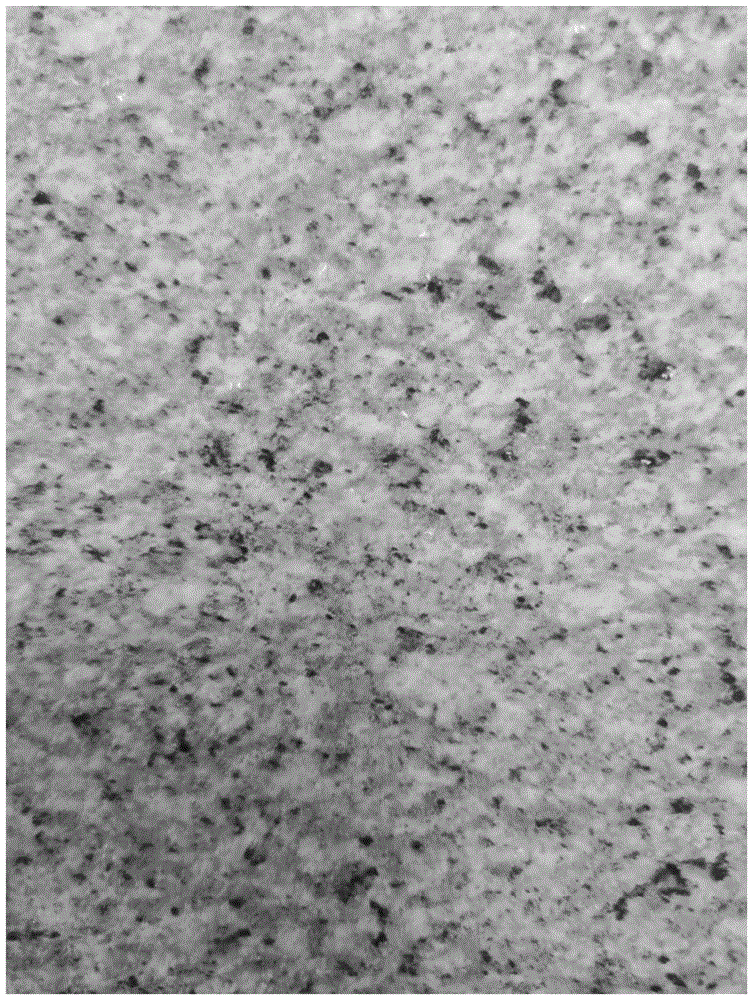
本发明属于砖制品涂料技术领域,具体涉及一种具有仿真效果的石材干粒、岩板及其制备方法和应用。
背景技术:
市场上目前流行的岩板,其图案主要以仿石材干粒类为主。其中石材干粒有个很鲜明的特点,即石材干粒的效果是目前岩板很难仿制的。真实的石材干粒,大部分都包含透料部位,基本以石英成分为主,通透的效果加上略带七彩闪光,凸显石材干粒的层次、立体效果。岩板在仿制这个效果的时候,主要是通过以下两种途径:①调整透料部位喷墨图案灰度,以视觉错觉的方式达到仿真效果,不过这种方式“透料部位”的立体效果不够强;②在岩板釉面添加熔块石材干粒,该方法所得的岩板立体效果尚可,石材干粒要么太透,要么太乳浊,而且没有闪光效果,缺乏层次感。
因此,目前市面上尚无一款既能满足透度适中、层次分明、具有真实石材干粒的仿真效果和立体效果,同时具有较高的始熔点和较适宜的高温粘度的石材干粒,这个问题亟待解决。
技术实现要素:
本发明提出一种具有仿真效果的石材干粒、岩板及其制备方法和应用,以解决现有技术中存在的一个或多个技术问题,至少提供一种有益的选择或创造条件。
为了克服上述技术问题,本发明采用的技术方案如下:
一种具有仿真效果的石材干粒,主要由主熔剂、高温原料、助熔剂、填料和氧化铈制得,其中,所述主熔剂包括钾长石,所述高温原料包括碳酸钡和氧化铝,所述助熔剂包括硼钙石、氧化锌、白云石和方解石,所述填料包括石英。
氧化铈的加入,不仅使得石材干粒具有七彩闪光的效果,同时还具有一定的助熔功能,对于降低石材干粒的高温粘度也有一定帮助。
作为上述方案的进一步改进,按重量份计,所述石材干粒主要由钾长石45-55份、石英8-12份、氧化锌4-10份、方解石3-8份、白云石4-8份、碳酸钡10-15份、硼钙石1-5份、氧化铈3-5份和氧化铝2-4份制得。
进一步优选,按重量份计,所述石材干粒主要由钾长石48-52份、石英9-11份、氧化锌6-8份、方解石5-6份、白云石5-6份、碳酸钡12-14份、硼钙石2-4份、氧化铈3-4份和氧化铝3-4份制得。
作为上述方案的进一步改进,所述石材干粒的化学组分包括二氧化硅和氧化铝,所述二氧化硅与所述氧化铝的摩尔比为(8-9):1。这主要是由于,若二氧化硅的含量过高,则用所得石材干粒制备的岩板的透度会过高;若氧化铝的含量过高,则用所得石材干粒干料制备的岩板很容易出现乳浊。如此,都会影响所得石材干粒以及岩板成品的透度等,而发明人意外发现,当石材干粒中二氧化硅与氧化铝的摩尔比为(8-9):1时,采用所得石材干粒制备的岩板的并未出现上述缺陷,且其透度良好。
一种具有仿真效果的石材干粒的制备方法,包括如下步骤:
1)备料:按所述石材干粒的原料配方称取原料,经混合,得到混合料;
2)熔制:将混合料进行熔制,得到熔块;
3)将熔块粉碎,得到本发明所述的石材干粒。
作为上述方案的进一步改进,所述熔制的温度为1400-1500℃,熔制的时长为5-6h;所述石材干粒的粒径为30-150目;步骤3)中将熔块进行粉碎时,采用的设备为气流磨。
一种具有仿真效果的岩板,其主要由本发明所述的石材干粒制得。
一种具有仿真效果的岩板的制备方法,包括砖坯和石材干粒,所述石材干粒为本发明所述的具有仿真效果的石材干粒,所述制备方法包括如下步骤:将所述的具有仿真效果的石材干粒布施至所述砖坯表面,再经烧制,得所述的岩板。
作为上述方案的进一步改进,所述布施的方式包括用布料机进行布料、采用钟罩进行淋釉或采用喷釉柜进行喷施等。
作为上述方案的进一步改进,所述烧制的温度为1160-1220℃,优选为1180-1200℃,烧制的时长为50-80min,优选为50-60min。
本发明所述的岩板在建筑和装修领域中的应用。
本发明的有益效果是:
(1)本发明提供了一种具有仿真效果的石材干粒,其主要由主熔剂、高温原料、助熔剂、填料和氧化铈制得。其中,钾长石作为主熔剂,石英为填料并起到骨架结构的作用,同时,氧化铈的加入,使得石材干粒具有七彩闪光的效果。此外,硼钙石、氧化锌、白云石和方解石均作为助熔剂,有助于降低石材干粒在高温下的粘度,且流平效果好。碳酸钡和氧化铝作为高温原料,有助于提高石材干粒的始熔点。
(2)本发明还提供了所述具有仿真效果的石材干粒的制备方法,工艺流程简单,原料的成本低廉,适宜于大规模生产。通过本发明所得的石材干粒,透度适中、层次分明、具有真实石材干粒的仿真效果和立体效果,同时具有较高的始熔点和较适宜的高温粘度(1200℃下的粘度为105-106pa·s)。
(3)此外,该具有仿真效果的石材干粒还可以作岩板的制备原料之一,且可经布施至砖坯表面,再经烧制即可得所述岩板。该方法工艺流程简单,原料的成本低廉,适宜于大规模生产,通过本发明所得的产品是一种既满足透度适中、层次分明、具有真实石材干粒的仿真效果和立体效果,同时具有较高的始熔点和较适宜的高温粘度的岩板。
(4)通过本发明所得的岩板能满足建筑和装修领域应用中的透度适中、层次分明、具有真实石材干粒的仿真效果和立体效果,同时具有较高的始熔点和较适宜的高温粘度等性能要求,应用前景广泛。
附图说明
为了更清楚地说明本发明实施例中的技术方案,下面将对实施例描述中所需要使用的附图作简单说明。显然,所描述的附图只是本发明的一部分实施例,而不是全部实施例,本领域的技术人员在不付出创造性劳动的前提下,还可以根据这些附图获得其他设计方案和附图。
图1是实施例1所得岩板成品的照片;
图2是对比例1所得岩板成品的照片。
具体实施方式
下面结合实施例对本发明进行具体描述,以便于所属技术领域的人员对本发明的理解。有必要在此特别指出的是,实施例只适用于对本发明做进一步说明,不能理解为对本发明保护范围的限制,所属领域技术熟练人员,根据上述发明内容对本发明所作出的非本质性的改进和调整,应仍属于本发明的保护范围。同时,下述所提及的原料未详细说明的,均为市售产品;未详细提及的工艺步骤或提取方法为均为本领域技术人员所知晓的工艺步骤或提取方法。
实施例1具有仿真效果的石材干粒和岩板的制备
具有仿真效果的石材干粒的制备步骤为:
取钾长石50kg、石英10kg、氧化锌6kg、方解石5kg、白云石7kg、碳酸钡12kg、硼钙石3kg、氧化铈4kg和氧化铝3kg,混合均匀后,在1450℃下熔制5h,将得到的熔块经气流磨进行粉碎,得到粒径为30-150目的颗粒状的石材干粒,记为具有仿真效果的石材干粒实施例成品1。
制备岩板的步骤为:将具有仿真效果的石材干粒实施例成品1采用钟罩淋釉的方式布施在已经淋好面釉的砖面,再在1200℃下烧制55min,得岩板实施例成品1。
实施例2具有仿真效果的石材干粒和岩板的制备
具有仿真效果的石材干粒的制备步骤为:
取钾长石50kg、石英10kg、氧化锌6kg、方解石4kg、白云石6kg、碳酸钡12kg、硼钙石3kg、氧化铈5kg和氧化铝4kg,混合均匀后,在1450℃下熔制6h,将得到的熔块经气流磨进行粉碎,得到粒径为30-150目的颗粒状的石材干粒,记为具有仿真效果的石材干粒实施例成品2。
制备岩板的步骤为:将具有仿真效果的石材干粒实施例成品2采用钟罩淋釉的方式布施在已经淋好面釉的砖面,再在1200℃下烧制55min,得到岩板实施例成品2。
实施例3具有仿真效果的石材干粒和岩板的制备
具有仿真效果的石材干粒的制备步骤为:
取钾长石50kg、石英11kg、氧化锌6kg、方解石6kg、白云石7kg、碳酸钡12kg、硼钙石3kg、氧化铈3kg和氧化铝2kg,混合均匀后,在1450℃下熔制5.5h,将得到的熔块经气流磨进行粉碎,得到粒径为30-150目的颗粒状的石材干粒,记为具有仿真效果的石材干粒实施例成品3。
制备岩板的步骤为:将具有仿真效果的石材干粒实施例成品3采用钟罩淋釉的方式布施在已经淋好面釉的砖面,再在1200℃下烧制55min,得到岩板实施例成品3。
实施例4具有仿真效果的石材干粒和岩板的制备
具有仿真效果的石材干粒的制备步骤为:
取钾长石50kg、石英10kg、氧化锌4kg、方解石5kg、白云石7kg、碳酸钡14kg、硼钙石3kg、氧化铈4kg和氧化铝3kg,混合均匀后,在1450℃下熔制5.5h,将得到的熔块经气流磨进行粉碎,得到粒径为30-150目的颗粒状的石材干粒,记为具有仿真效果的石材干粒实施例成品4。
制备岩板的步骤为:将具有仿真效果的石材干粒实施例成品1采用钟罩淋釉的方式布施在已经淋好面釉的砖面,再在1200℃下烧制55min,得到岩板实施例成品4。
对比例1(未添加氧化铝)
具有仿真效果的石材干粒的制备步骤为:
取钾长石53kg、石英10kg、氧化锌6kg、方解石5kg、白云石7kg、碳酸钡12kg、硼钙石3kg、氧化铈4kg,混合均匀后,在1450℃下熔制5h,将得到的熔块经气流磨进行粉碎,得到粒径为30-150目的颗粒状的石材干粒,记为具有仿真效果的石材干粒对比例成品1。
制备岩板的步骤为:将具有仿真效果的石材干粒对比例成品1采用钟罩淋釉的方式布施在已经淋好面釉的砖面,再在1200℃下烧制55min,记为岩板对比例成品1。
对比例2(降低氧化锌含量)
具有仿真效果的石材干粒的制备步骤为:
取钾长石54kg、石英10kg、氧化锌2kg、方解石5kg、白云石7kg、碳酸钡12kg、硼钙石3kg、氧化铈4kg和氧化铝3kg,混合均匀后,在1450℃下熔制5h,将得到的熔块经气流磨进行粉碎,得到粒径为30-150目的颗粒状的石材干粒,记为具有仿真效果的石材干粒对比例成品2。
制备岩板的步骤为:将具有仿真效果的石材干粒对比例成品2采用钟罩淋釉的方式布施在已经淋好面釉的砖面,再在1200℃下烧制55min,记为岩板对比例成品2。
对比例3(降低钾长石,增加石英)
具有仿真效果的石材干粒的制备步骤为:
取钾长石40g、石英20kg、氧化锌6kg、方解石5kg、白云石7kg、碳酸钡12kg、硼钙石3kg、氧化铈4kg和氧化铝3kg,混合均匀后,在1450℃下熔制5h,将得到的熔块经气流磨进行粉碎,得到粒径为30-150目的颗粒状的石材干粒,记为具有仿真效果的石材干粒对比例成品3。
制备岩板的步骤为:将具有仿真效果的石材干粒对比例成品3采用钟罩淋釉的方式布施在已经淋好面釉的砖面,再在1200℃下烧制55min,记为岩板对比例成品3。
对比例4(未添加氧化铈)
具有仿真效果的石材干粒的制备步骤为:
取钾长石54g、石英10kg、氧化锌6kg、方解石5kg、白云石7kg、碳酸钡12kg、硼钙石3kg和氧化铝3kg,混合均匀后,在1450℃下熔制5h,将得到的熔块经气流磨进行粉碎,得到粒径为30-150目的颗粒状的石材干粒,记为具有仿真效果的石材干粒对比例成品4。
制备岩板的步骤为:将具有仿真效果的石材干粒对比例成品4采用钟罩淋釉的方式布施在已经淋好面釉的砖面,再在1200℃下烧制55min,记为岩板对比例成品4。
产品性能检测
1.闪光效果(拍照)
将对比例1、实施例1分别所得的岩板对比例成品4和岩板实施例成品1的板材表面分别拍照,得到图1-2,其中,图1为岩板实施例成品1的照片,图2为岩板对比例成品1的照片。
从图1-2可以看出,图1具有闪光效果,而图2没有。
2.透度、观察闪光效果、高温黏度和始熔点
将对比例1-2、实施例1-4分别所得的岩板对比例成品1-2和岩板实施例成品1-4分别进行透度和闪光效果的观察,并分别对岩板进行高温黏度和始熔点的检测。所得结果见表1。
表1岩板实施例成品1-4及岩板对比例成品1-2的检测结果
由表1可见,对比例1中,未添加氧化铝所制备的石材干粒的始融点偏低,主要很可能是因为,氧化铝作为高温材料的部分,能起到提高石材干粒始融点的作用,因此,对比例1的石材干粒的始融点较实施例1-4均是偏低的,只有898℃。而与此同时,发明人还意外发现,在降低氧化铝的同时,即使是添加了氧化铈的岩板,其“闪光能力”也“消失”了,这很可能是因为,氧化铈使得岩板呈现闪光的原因主要是因为氧化铈结晶所带来的。单独的氧化铈本身是不闪的,但其在结晶后形成了一种固定的形态,才会闪光,但去掉氧化铝以后,岩板不闪了,很可能是因为,釉料在1200℃下的高温黏度太低,只有104-105pa·s(1200℃下)。较实施例1-4的高温黏度为105-106pa·s(1200℃下),这样相差了几个数量级,因此,对比例1的体系中,由于釉料的高温黏度太低,体系更多是出现液态的流动,并且难以出现析晶和结晶。由此可见,1200℃下的高温黏度为104-105pa·s,这样黏度太低也是会影响氧化铈的结晶的。
对比例2中,在降低氧化锌含量后所制得石材干粒的始融点偏高,主要是因为,氧化锌在体系中是强助熔剂,氧化锌减少至2kg以后,它的助熔效果就减弱了,体系的温度相当于是更高了,同时,对比例2的体系中,由于釉料的高温黏度太高,而高温高黏度的情况下,体系太粘稠,因此氧化铈析晶结晶的动力不足,虽也能结晶,但结晶不够充分,因此结晶程度不高,石材干粒呈现的是微微闪光。同时助熔剂氧化锌的含量降低了,体系熔的程度变差了,因此透度较差。
对比例3中,钾长石作为主熔剂,其内含70%的石英,对比例3在降低钾长石含量,且增加石英以后,所得釉料在1200℃下的高温黏度增加到108-109pa·s,因此即使此时岩板的透感变好一些了,但是由于黏度太大,与对比例2相似,由于体系太粘稠,因此氧化铈析晶结晶的动力不足,虽也能结晶,但结晶不够充分,因此结晶程度不高,石材干粒呈现的是微微闪光,但透度较为良好。
对比例4中,未添加氧化铈,因此未形成氧化铈结晶,无闪光效果。
而实施例1-4分别所得的石材干粒透度适中、层次分明、具有真实石材干粒的仿真效果和立体效果,同时具有较高的始熔点和较适宜的高温粘度等性能(1200℃下的粘度为105-106pa·s),应用前景广泛。
对于本发明所属技术领域的普通技术人员来说,在不脱离本发明构思的前提下还可以做出若干简单推演或替换,而不必经过创造性的劳动。因此,本领域技术人员根据本发明的揭示,对本发明做出的简单改进都应该在本发明的保护范围之内。上述实施例为本发明的优选实施例,凡与本发明类似的工艺及所作的等效变化,均应属于本发明的保护范畴。
起点商标作为专业知识产权交易平台,可以帮助大家解决很多问题,如果大家想要了解更多知产交易信息请点击 【在线咨询】或添加微信 【19522093243】与客服一对一沟通,为大家解决相关问题。
此文章来源于网络,如有侵权,请联系删除


