一种高强高耐磨Al-Si合金及其制备方法和应用与流程



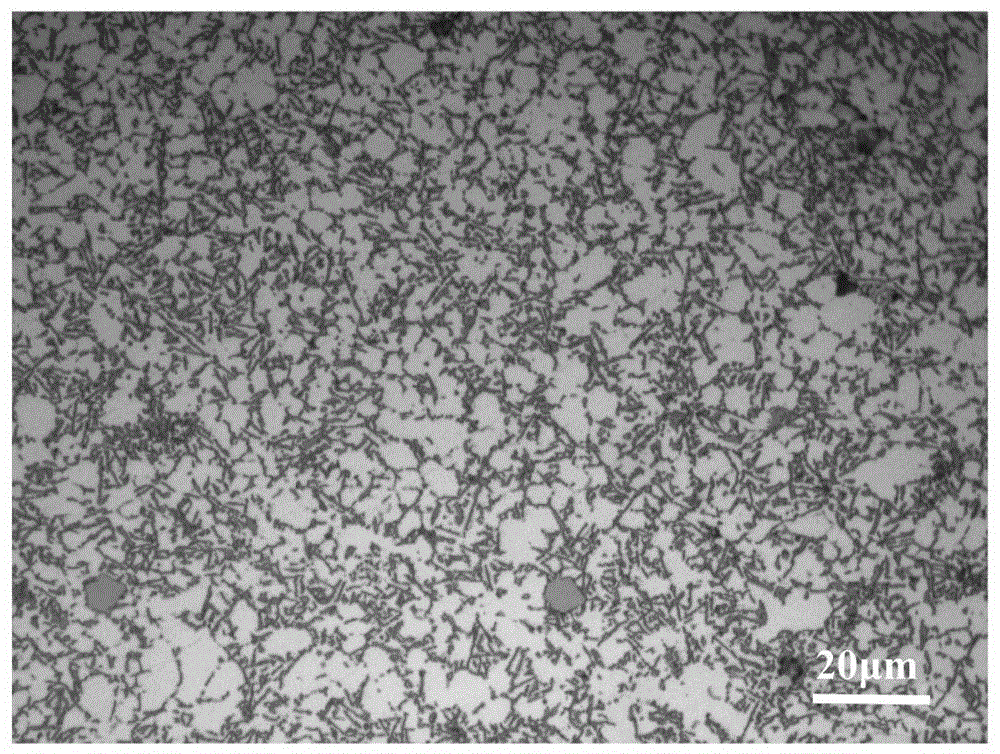
本发明涉及铝合金材料技术领域,具体涉及一种高强高耐磨al-si合金及其制备方法和应用。
背景技术:
铸造al-si合金是铸造铝合金中最重要的一个系列,由于其密度小、比强度高,同时具有优异的铸造性能、耐蚀性能、耐磨损性能、可焊性及热膨胀性,广泛地应用于航空航天、汽车、机械等行业,用来生产形状复杂、薄壁、耐蚀、气密性要求高、承受中高静载荷或冲击载荷、要求在较高温度下工作的大、中、小型铸件。例如现有技术中汽车发动机等部件,通常采用过共晶al-si合金进行压铸成形,但是现有合金成分制备的发动机部件在强度和耐磨性等方面均有一定的局限性。在过共晶al-si合金中加入少量的cu元素和mg元素,在合金中形成al2cu、mg2si以及al-si-cu-mg等强化相,可以在一定程度上提高合金的强度,但是由于合金中si含量较高,成形后会在基体中形成粗大的块状si相和纤维状的共晶si相,对基体有较大的割裂作用,合金的强度和耐磨性有待提高。
技术实现要素:
本发明的目的在于提供一种高强高耐磨al-si合金及其制备方法和应用,本发明提供的合金具有较高的强度和较好的耐磨性。
为了实现上述发明目的,本发明提供以下技术方案:
本发明提供了一种高强高耐磨al-si合金,按质量百分含量计,包括si16~23.5%,cu5~9%,mg3~6.2%,zn2~8%,zr0.1~0.45%,la0.2~0.7%,er0.1~0.3%,mn≤0.2%,fe≤0.15%,余量为al和不可避免的杂质,所述不可避免的杂质中,每种杂质的含量均低于0.01%。
优选地,包括si17.5~22%,cu5~8%,mg3.3~6%,zn3~7%,zr0.15~0.35%,la0.2~0.5%,er0.2~0.3%,mn0.15~0.2%,fe0.1~0.15%,余量为al和不可避免的杂质。
本发明提供了上述技术方案所述高强高耐磨al-si合金的制备方法,包括以下步骤:
按高强高耐磨al-si合金的成分将制备原料进行熔炼,得到合金液;
将所述合金液进行精炼,得到精炼液;
基于超声/电磁复合场对所述精炼液进行熔体处理,得到处理液;
将所述处理液进行挤压铸造,得到高强高耐磨al-si合金。
优选地,所述制备原料包括纯铝锭和中间合金;
所述熔炼包括:将纯铝锭进行第一熔炼,待部分纯铝锭熔化后,加入所述中间合金进行第二熔炼;所述第一熔炼的温度为700~760℃,时间为2~6h,所述第二熔炼的温度为710~770℃,时间为2~5h;所述部分纯铝锭占纯铝锭总质量的45~65%。
优选地,所述精炼为喷粉精炼,所述喷粉精炼的操作参数包括:除气机的旋转速度为110~150rpm,进口压力为0.25~0.65mpa,出粉量为1.5~4.5kg/min,精炼时间为15~45min。
优选地,所述熔体处理的操作参数包括:超声功率为320~420w,超声频率为10~25khz,电磁频率为15~30khz,电磁强度为100~180a。
优选地,所述挤压铸造的操作参数包括:浇铸温度为660~760℃,比压为450~750mpa,保压时间为20~70s,挤压速度为5~15mm/s。
优选地,所述挤压铸造后还包括:
将挤压铸造后所得合金铸锭进行淬火处理,得到淬火合金铸锭;
将所述淬火合金铸锭进行t6热处理,得到高强高耐磨al-si合金。
优选地,所述淬火处理的时间为30~150s;所述淬火处理采用的淬火介质为10wt%的nacl水溶液,所述nacl水溶液的温度为15~25℃;
所述t6热处理包括依次进行的固溶处理和时效处理;所述固溶处理的温度为480~530℃,时间为5~100min;所述时效处理的温度为150~220℃,时间为4~24h。
本发明提供了上述技术方案所述高强高耐磨al-si合金或上述技术方案所述制备方法制备得到的高强高耐磨al-si合金在汽车零部件中的应用。
本发明提供了一种高强高耐磨al-si合金,按质量百分含量计,包括si16~23.5%,cu5~9%,mg3~6.2%,zn2~8%,zr0.1~0.45%,la0.2~0.7%,er0.1~0.3%,mn≤0.2%,fe≤0.15%,余量为al和不可避免的杂质,所述不可避免的杂质中,每种杂质的含量均低于0.01%。本发明通过在合金中加入少量的zr、la、er和较多的zn,同时控制合金中si、cu和mg的含量,可以改善si相形貌,细化晶粒,且合金组织均匀,具有较高的强度和较好的耐磨性。实施例的结果显示,本发明提供的高强高耐磨al-si合金的抗拉强度达到384mpa,屈服强度达到317mpa,延伸率为2.7%,硬度值为217hb,摩擦系数为0.301,能够满足汽车对零部件的性能要求。
本发明提供了所述高强高耐磨al-si合金的制备方法,包括以下步骤:按高强高耐磨al-si合金的成分将制备原料进行熔炼,得到合金液;将所述合金液进行精炼,得到精炼液;基于超声/电磁复合场对所述精炼液进行熔体处理,得到处理液;将所述处理液进行挤压铸造,得到合金铸锭;将所述合金铸锭进行淬火处理,得到淬火合金铸锭;将所述淬火合金铸锭进行t6热处理,得到高强高耐磨al-si合金。本发明提供的方法步骤简单,便于操作;采用本发明提供的方法得到的合金偏析情况得到改善,原料利用率高,且晶粒尺寸细小、组织均匀,表面光洁,具有优异的耐磨性能和力学性能。
附图说明
图1为实施例3制备的高强高耐磨al-si合金的显微组织图;
图2为对比例1制备的al-si合金的显微组织图。
具体实施方式
本发明提供了一种高强高耐磨al-si合金,按质量百分含量计,包括si16~23.5%,cu5~9%,mg3~6.2%,zn2~8%,zr0.1~0.45%,la0.2~0.7%,er0.1~0.3%,mn≤0.2%,fe≤0.15%,余量为al和不可避免的杂质,所述不可避免的杂质中,每种杂质的含量均低于0.01%。
按质量百分含量计,本发明提供的高强高耐磨al-si合金包括si16~23.5%,优选为17.5~22%,进一步优选为17.7~21.5%。
按质量百分含量计,本发明提供的高强高耐磨al-si合金包括cu5~9%,优选为5~8%,进一步优选为5.1~7.2%。
按质量百分含量计,本发明提供的高强高耐磨al-si合金包括mg3~6.2%,优选为3.3~6%,进一步优选为3.5~5.2%。
按质量百分含量计,本发明提供的高强高耐磨al-si合金包括zn2~8%,优选为3~7%,进一步优选为3.2~6.1%。
按质量百分含量计,本发明提供的高强高耐磨al-si合金包括zr0.1~0.45%,优选为0.15~0.35%,进一步优选为0.18~0.3%。
按质量百分含量计,本发明提供的高强高耐磨al-si合金包括la0.2~0.7%,优选为0.2~0.5%,进一步优选为0.22~0.43%。
按质量百分含量计,本发明提供的高强高耐磨al-si合金包括er0.1~0.3%,优选为0.2~0.3%,进一步优选为0.22~0.3%。
按质量百分含量计,本发明提供的高强高耐磨al-si合金包括mn≤0.2%,优选为0.15~0.2%。
按质量百分含量计,本发明提供的高强高耐磨al-si合金包括fe≤0.15%,优选为0.1~0.15%。
本发明提供的高强高耐磨al-si合金包括余量的al和不可避免的杂质,所述不可避免的杂质中,每种杂质的含量均低于0.01%。
在本发明中,si、cu、zn和mg是合金的主要元素,这些合金元素具有固溶强化和时效析出强化的作用,另外mg和si可以析出mg2si强化相,cu和al可以析出al2cu强化相,进一步增强合金的强度,同时al、si、cu和mg四种合金元素也会形成w(alxmg5si4cu)和q(al5mg8si6cu2)强化相。具体的,发明人研究发现,当si含量低于16%、cu含量低于5%、mg含量低于3%以及zn含量低于2%时,合金的强度显著下降,且耐磨性也随之下降;当si含量高于23.5%、cu元素含量高于9%、mg元素含量高于6.2%时,在合金内部会形成粗大的第二相,合金铸件的塑性急剧降低,影响后期的切削加工;zn在合金中的最大固溶度为83.1%,基本完全固溶到基体中,检测不到含有zn的第二相,所以zn主要对合金起到固溶强化作用,当合金中添加zn的含量大于2%时,可以显著提高合金的强度,当zn含量过高(如超过8%),会增加合金的应力开裂倾向。本发明将si、cu、mg和zn的含量控制在上述范围内,可以平衡合金的强度、耐磨性能和抗冲击断裂韧性之间的矛盾关系,将其应用于汽车零部件中,可以满足汽车对零部件强度、耐磨性和韧性的要求。
在本发明中,zr、la和er是合金中添加的微量元素,其中,添加zr可以析出al3zr相,限制了粗大的mg5al8相沿晶界析出,同时al3zr晶体结构和晶格常数均与基体铝极为相似,是α-al优良的异质形核核心;在添加zr的同时添加re(la、er)元素,稀土易在固/液界面前沿富集,富集到一定程度,形成了al3re化合物,并增大了成分过冷而使分枝过程加剧,二次枝晶增多,最终使枝晶间距减小,晶粒细化;此外,稀土元素的表面活性较大,在固/液界面前沿的富集使其起到阻碍α-al晶粒长大的作用,从而使晶粒的长大过程受阻,促进了晶粒的细化;合金中添加少量的fe元素,其可以在合金中形成硬质针状相,使基体强化,提高合金的耐磨性;合金中添加少量的mn元素,可以形成al6mn的弥散质点,阻止再结晶粗大化,提高再结晶温度,同时与合金的不纯净含铁杂质形成al3femn,使fe的化合物形态从针状转变为块状,可以在一定程度提高合金的韧性。
本发明提供了上述技术方案所述高强高耐磨al-si合金的制备方法,包括以下步骤:
按高强高耐磨al-si合金的成分将制备原料进行熔炼,得到合金液;
将所述合金液进行精炼,得到精炼液;
基于超声/电磁复合场对所述精炼液进行熔体处理,得到处理液;
将所述处理液进行挤压铸造,得到高强高耐磨al-si合金。
本发明按高强高耐磨al-si合金的成分将制备原料进行熔炼,得到合金液。在本发明中,所述制备原料优选包括纯铝锭、纯mg、纯zn和中间合金,所述中间合金优选包括al-30%si、al-50%cu、al-10%zr、al-10%la、al-10%er、al-30%mn和al-50%fe。在本发明中,所述熔炼包括:将纯铝锭进行第一熔炼,待部分纯铝锭熔化后,加入所述中间合金进行第二熔炼;所述第一熔炼的温度优选为700~760℃,进一步优选为725~755℃,时间优选为2~6h,进一步优选为2.5~4.5h;所述第二熔炼的温度优选为710~770℃,进一步优选为730~750℃,时间优选为2~5h,进一步优选为2.5~4h;所述部分纯铝锭优选占纯铝锭总质量的45~65%,进一步优选为50%。本发明采用分步熔炼可以有效提高熔炼效率,减少热量散失,并能防止熔炼温度过高而发生过烧的现象。
得到合金液后,本发明将所述合金液进行精炼,得到精炼液。在本发明中,所述精炼优选为喷粉精炼,所述喷粉精炼的操作参数包括:除气机的旋转速度优选为110~150rpm,进一步优选为120~135rpm;进口压力优选为0.25~0.65mpa,进一步优选为0.33~0.6mpa;出粉量优选为1.5~4.5kg/min,进一步优选为2.5~3.8kg/min;精炼时间优选为15~45min,进一步优选为20~35min。在本发明中,所述精炼采用的精炼剂优选包括na3alf6、mg2n3、c2cl6、nacl和kcl,其中,所述na3alf6的添加量优选为合金液总质量的3~5%,所述mg2n3的添加量优选为合金液总质量的4~8%,所述c2cl6的添加量优选为合金液总质量的2~4%,所述nacl和kcl的总添加量优选为合金液总质量的2~4%,所述nacl和kcl的质量比优选为35:65。在本发明中,若除气机转速过高、进口压力过大、精炼时间过长,会造成合金液的喷溅,易产生危险,同时会对精炼的高纯氩气(99.9%)和精炼剂造成浪费;除气机转速过低、进口压力过小、精炼时间过短,合金液内部会有残留的气体和渣质,影响铸锭质量。本发明优选控制喷粉精炼的操作参数在上述范围内,有利于保证具有较好的精炼效果,大幅度地提高合金的洁净度,消除气孔、夹杂等组织缺陷,确保获得的合金铸件组织内部无夹杂物产生,避免夹杂物影响合金性能。
得到精炼液后,本发明基于超声/电磁复合场对所述精炼液进行熔体处理,得到处理液。在本发明中,所述熔体处理的操作参数包括:超声功率优选为320~420w,进一步优选为320~380w;超声频率优选为10~25khz,进一步优选为15~20khz;电磁频率优选为15~30khz,进一步优选为17~25khz;电磁强度优选为100~180a,进一步优选为125~150a。在本发明中,当超声功率较小时,空化和声流效应都较弱,不能达到细化晶粒的效果,但超声功率过大,热量传递到精炼液中使其温度增加,功率越大热量传递效果越明显,导致结晶时间延长,一定程度上降低晶粒的细化效果,同时浪费能源;当电磁频率过高时,搅拌作用相对较弱,随着电磁频率的降低,强迫对流增强。本发明优选控制熔体处理的操作参数在上述范围内,通过超声场的振动以及低频电磁场的搅拌作用,可以有效细化合金内部的组织,改善合金内部的溶质偏析情况。
得到处理液后,本发明将所述处理液进行挤压铸造,得到高强高耐磨al-si合金。在本发明中,进行所述挤压铸造前,优选将所述处理液进行过滤,所述过滤采用的过滤板优选为沫陶瓷过滤板,所述沫陶瓷过滤板的孔隙度优选为80~120ppi。在本发明中,所述挤压铸造的操作参数包括:浇铸温度优选为660~760℃,进一步优选为680~740℃;比压优选为450~750mpa,进一步优选为520~700mpa;保压时间优选为20~70s,进一步优选为30~60s;挤压速度优选为5~15mm/s,进一步优选为6~12mm/s。本发明利用液态挤压成形工艺,对处理液进行挤压铸造,其中,若比压过低,处理液温度过低,则挤压速度慢,挤压过程中易导致处理液过快凝固,不能够完全冲型,铸锭易产生缺陷;若比压过大,处理液温度过高,则挤压速度快,模具内部易卷入气体使处理液溢出。在本发明中,进行所述挤压铸造前,优选对所需模具进行预热;所述预热的温度优选为220~350℃,进一步优选为250~310℃;时间优选为30~100min,进一步优选为50~90min。在本发明中,模具预热温度过高,易在挤压铸造过程中造成晶粒的长大,模具温度过低易使处理液凝固过快。
在本发明中,为了进一步提高高强高耐磨al-si合金性能,所述挤压铸造后优选还包括:
将挤压铸造后所得合金铸锭进行淬火处理,得到淬火合金铸锭;
将所述淬火合金铸锭进行t6热处理,得到高强高耐磨al-si合金。
本发明将挤压铸造后所得合金铸锭进行淬火处理,得到淬火合金铸锭。在本发明中,所述淬火处理具体是将挤压铸造后所得合金铸锭置于淬火介质中进行快速冷却。在本发明中,所述淬火处理的时间优选为30~150s,进一步优选为30~100s,在本发明中,所述淬火处理的时间指合金铸锭处于淬火介质中的时间;所述淬火介质优选为10wt%的nacl水溶液,所述nacl水溶液的温度为15~25℃,进一步优选为16~22℃。淬火处理后,本发明优选将所得淬火合金铸锭放置在通风处自然风干。本发明优选采用上述nacl水溶液进行冷却,可以显著提高冷却速度,使合金铸锭充分、快速冷却,在合金内部快速形成过饱和固溶体,为后续的热处理工艺奠定良好的基础。
得到淬火合金铸锭后,本发明将所述淬火合金铸锭进行t6热处理,得到高强高耐磨al-si合金。在本发明中,所述t6热处理优选包括依次进行的固溶处理和时效处理;所述固溶处理的温度优选为480~530℃,进一步优选为500~520℃;时间优选为5~100min,进一步优选为30~90min;所述时效处理的温度优选为150~220℃,进一步优选为175~190℃,时间优选为4~24h,进一步优选为8~15h。在本发明中,由于基于超声/电磁复合场对精炼液进行熔体处理,在超声振动和电磁搅拌的共同作用下使得合金内部组织均匀,晶粒细小,且挤压铸造成形过程中,处理液有较大的塑性变形,导致合金内部能量较高,位错密度较大。因此,只需要较短时间的固溶处理,消除合金内部的内应力,最后经时效处理得到具有较好力学性能和耐磨性能的al-si合金。
本发明提供了上述技术方案所述高强高耐磨al-si合金或上述技术方案所述制备方法制备得到的高强高耐磨al-si合金在汽车零部件中的应用。本发明提供的合金内应力低、表面光洁、内部组织均匀、晶粒细小且尺寸相差不大,同时性能优良,具有较高的强度和较好的耐磨性能,用于汽车零部件,能够满足后续的机械加工要求,同时可以满足汽车对车身内部零部件性能的要求。
下面将结合本发明中的实施例,对本发明中的技术方案进行清楚、完整地描述。显然,所描述的实施例仅仅是本发明一部分实施例,而不是全部的实施例。基于本发明中的实施例,本领域普通技术人员在没有做出创造性劳动前提下所获得的所有其他实施例,都属于本发明保护的范围。
实施例1
本实施例中高强高耐磨al-si合金,由以下质量百分比的成分组成:si18.0%,cu5.3%,mg4.1%,zn4.2%,zr0.19%,la0.24%,er0.24%,mn0.21%,fe0.11%,余量为al和不可避免的杂质,所述不可避免的杂质中,每种杂质的含量均低于0.01%。
本实施例中高强高耐磨al-si合金的制备方法,包括以下步骤:
按照高强高耐磨al-si合金的配方,将工业纯铝锭加入熔炼炉中,升温至730℃,保温熔炼4h,此时纯铝锭熔化到一半,加入纯mg、纯zn和其它中间合金(具体为al-30%si、al-50%cu、al-10%zr、al-10%er、al-10%la、al-30%mn和al-50%fe),升温至735℃,保温熔炼2.5h,得到合金液;
将除气机的精炼管插入所述合金液中进行喷粉精炼,以实现除气和除渣处理,得到精炼液;其中,所述喷粉精炼的操作参数包括:除气机的旋转速度为125rpm,进口压力为0.35mpa,出粉量为2.0kg/min,精炼时间为25min;所述喷粉精炼采用的精炼剂包括na3alf6、mg2n3、c2cl6、nacl和kcl,其中,na3alf6的添加量为合金液总质量的3.5%,mg2n3的添加量为合金液总质量的4.5%,c2cl6的添加量为合金液总质量的2.5%,nacl和kcl的总添加量为合金液总质量的2.5%,所述nacl和kcl的质量比为35:65;
基于超声/电磁复合场对所述精炼液进行熔体处理,得到处理液;其中,所述熔体处理的操作参数包括:超声功率为330w,超声频率为15khz,电磁频率为18khz,电磁强度为125a;
将模具在250℃条件下预热50min,将所述处理液转入预热后的模具中,进行挤压铸造,得到合金铸锭;其中,所述处理液进行挤压铸造前经泡沫陶瓷过滤板(孔隙度为110ppi)过滤;所述挤压铸造的操作参数包括:浇铸温度为685℃,比压为530mpa,保压时间为35s,挤压速度为6mm/s;
将所述合金铸锭进行淬火处理,其中,淬火处理的时间为35s,淬火介质为10wt%的nacl水溶液,所述nacl水溶液的温度为19℃;淬火处理后自然风干,得到高强高耐磨al-si合金。
实施例2
本实施例中高强高耐磨al-si合金,由以下质量百分比的成分组成:si17.7%,cu5.1%,mg3.5%,zn3.2%,zr0.18%,la0.22%,er0.22%,mn0.2%,fe0.12%,余量为al和不可避免的杂质,所述不可避免的杂质中,每种杂质的含量均低于0.01%。
本实施例中高强高耐磨al-si合金的制备方法,包括以下步骤:
按照高强高耐磨al-si合金的配方,将工业纯铝锭加入熔炼炉中,升温至725℃,保温熔炼4.5h,此时纯铝锭熔化到一半,加入纯mg、纯zn和其它中间合金(具体为al-30%si、al-50%cu、al-10%zr、al-10%er、al-10%la、al-30%mn和al-50%fe),升温至730℃,保温熔炼4h,得到合金液;
将除气机的精炼管插入所述合金液中进行喷粉精炼,以实现除气和除渣处理,得到精炼液;其中,所述喷粉精炼的操作参数包括:除气机的旋转速度为120rpm,进口压力为0.33mpa,出粉量为2.5kg/min,精炼时间为20min;所述喷粉精炼采用的精炼剂包括na3alf6、mg2n3、c2cl6、nacl和kcl,其中,na3alf6的添加量为合金液总质量的3.4%,mg2n3的添加量为合金液总质量的4.3%,c2cl6的添加量为合金液总质量的2.2%,nacl和kcl的总添加量为合金液总质量的2.6%,所述nacl和kcl的质量比为35:65;
基于超声/电磁复合场对所述精炼液进行熔体处理,得到处理液;其中,所述熔体处理的操作参数包括:超声功率为320w,超声频率为15khz,电磁频率为22khz,电磁强度为125a;
将模具在250℃条件下预热50min,将所述处理液转入预热后的模具中,进行挤压铸造,得到合金铸锭;其中,所述处理液进行挤压铸造前经泡沫陶瓷过滤板(孔隙度为100ppi)过滤;所述挤压铸造的操作参数包括:浇铸温度为680℃,比压为520mpa,保压时间为30s,挤压速度为6mm/s;
将所述合金铸锭进行淬火处理,其中,淬火处理的时间为30s,淬火介质为10wt%的nacl水溶液,所述nacl水溶液的温度为17℃;淬火处理后自然风干,得到淬火合金铸锭;
将所述淬火合金铸锭依次进行固溶处理和时效处理,之后随炉冷却得到高强高耐磨al-si合金;其中,所述固溶处理的温度为500℃,时间为90min;所述时效处理的温度为175℃,时间为15h。
实施例3
本实施例中高强高耐磨al-si合金,由以下质量百分比的成分组成:si18.5%,cu6.6%,mg4.5%,zn4.2%,zr0.28%,la0.35%,er0.25%,mn0.15%,fe0.11%,余量为al和不可避免的杂质,所述不可避免的杂质中,每种杂质的含量均低于0.01%。
本实施例中高强高耐磨al-si合金的制备方法,包括以下步骤:
按照高强高耐磨al-si合金的配方,将工业纯铝锭加入熔炼炉中,升温至740℃,保温熔炼3h,此时纯铝锭熔化到一半,加入纯mg、纯zn和其它中间合金(具体为al-30%si、al-50%cu、al-10%zr、al-10%er、al-10%la、al-30%mn和al-50%fe),在740℃条件下继续保温熔炼3h,得到合金液;
将除气机的精炼管插入所述合金液中进行喷粉精炼,以实现除气和除渣处理,得到精炼液;其中,所述喷粉精炼的操作参数包括:除气机的旋转速度为130rpm,进口压力为0.45mpa,出粉量为3.1kg/min,精炼时间为30min;所述喷粉精炼采用的精炼剂包括na3alf6、mg2n3、c2cl6、nacl和kcl,其中,na3alf6的添加量为合金液总质量的4.2%,mg2n3的添加量为合金液总质量的5.1%,c2cl6的添加量为合金液总质量的2.8%,nacl和kcl的总添加量为合金液总质量的3.1%,所述nacl和kcl的质量比为35:65;
基于超声/电磁复合场对所述精炼液进行熔体处理,得到处理液;其中,所述熔体处理的操作参数包括:超声功率为350w,超声频率为18khz,电磁频率为17khz,电磁强度为135a;
将模具在300℃条件下预热75min,将所述处理液转入预热后的模具中,进行挤压铸造,得到合金铸锭;其中,所述处理液进行挤压铸造前经泡沫陶瓷过滤板(孔隙度为120ppi)过滤;所述挤压铸造的操作参数包括:浇铸温度为720℃,比压为600mpa,保压时间为45s,挤压速度为9mm/s;
将所述合金铸锭进行淬火处理,其中,淬火处理的时间为30s,淬火介质为10wt%的nacl水溶液,所述nacl水溶液的温度为20℃;淬火处理后自然风干,得到淬火合金铸锭;
将所述淬火合金铸锭依次进行固溶处理和时效处理,之后随炉冷却得到高强高耐磨al-si合金;其中,所述固溶处理的温度为520℃,时间为60min;所述时效处理的温度为180℃,时间为12h。
实施例4
本实施例中高强高耐磨al-si合金,由以下质量百分比的成分组成:si21.5%,cu7.2%,mg5.2%,zn6.1%,zr0.3%,la0.43%,er0.3%,mn0.2%,fe0.13%,余量为al和不可避免的杂质,所述不可避免的杂质中,每种杂质的含量均低于0.01%。
本实施例中高强高耐磨al-si合金的制备方法,包括以下步骤:
按照高强高耐磨al-si合金的配方,将工业纯铝锭加入熔炼炉中,升温至755℃,保温熔炼2.5h,此时纯铝锭熔化到一半,加入纯mg、纯zn和其它中间合金(具体为al-30%si、al-50%cu、al-10%zr、al-10%er、al-10%la、al-30%mn和al-50%fe),降温至750℃,保温熔炼2.5h,得到合金液;
将除气机的精炼管插入所述合金液中进行喷粉精炼,以实现除气和除渣处理,得到精炼液;其中,所述喷粉精炼的操作参数包括:除气机的旋转速度为135rpm,进口压力为0.6mpa,出粉量为3.8kg/min,精炼时间为35min;所述喷粉精炼采用的精炼剂包括na3alf6、mg2n3、c2cl6、nacl和kcl,其中,na3alf6的添加量为合金液总质量的4,1%,mg2n3的添加量为合金液总质量的5.2%,c2cl6的添加量为合金液总质量的2.9%,nacl和kcl的总添加量为合金液总质量的3.1%,所述nacl和kcl的质量比为35:65;
基于超声/电磁复合场对所述精炼液进行熔体处理,得到处理液;其中,所述熔体处理的操作参数包括:超声功率为380w,超声频率为20khz,电磁频率为25khz,电磁强度为150a;
将模具在310℃条件下预热90min,将所述处理液转入预热后的模具中,进行挤压铸造,得到合金铸锭;其中,所述处理液进行挤压铸造前经泡沫陶瓷过滤板(孔隙度为115ppi)过滤;所述挤压铸造的操作参数包括:浇铸温度为760℃,比压为700mpa,保压时间为60s,挤压速度为12mm/s;
将所述合金铸锭进行淬火处理,其中,淬火处理的时间为30s,淬火介质为10wt%的nacl水溶液,所述nacl水溶液的温度为24℃;淬火处理后自然风干,得到淬火合金铸锭;
将所述淬火合金铸锭依次进行固溶处理和时效处理,之后随炉冷却得到高强高耐磨al-si合金;其中,所述固溶处理的温度为520℃,时间为30min;所述时效处理的温度为190℃,时间为8h。
对比例1
本实施例中高强高耐磨al-si合金,由以下质量百分比的成分组成:si17.7%,cu5.1%,mg3.5%,zr0.18%,la0.22%,er0.22%,mn0.2%,fe0.12%,余量为al和不可避免的杂质,所述不可避免的杂质中,每种杂质的含量均低于0.01%。
本实施例中高强高耐磨al-si合金的制备方法,包括以下步骤:
按照高强高耐磨al-si合金的配方,将工业纯铝锭加入熔炼炉中,升温至725℃,保温熔炼4.5h,此时纯铝锭熔化到一半,加入纯mg和其它中间合金(具体为al-30%si、al-50%cu、、al-10%zr、al-10%er、al-10%la、al-30%mn和al-50%fe),升温至730℃,保温熔炼4h,得到合金液;
将除气机的精炼管插入所述合金液中进行喷粉精炼,以实现除气和除渣处理,得到精炼液;其中,所述喷粉精炼的操作参数包括:除气机的旋转速度为120rpm,进口压力为0.33mpa,出粉量为2.5kg/min,精炼时间为20min;所述喷粉精炼采用的精炼剂包括na3alf6、mg2n3、c2cl6、nacl和kcl,其中,na3alf6的添加量为合金液总质量的3%,mg2n3的添加量为合金液总质量的4.1%,c2cl6的添加量为合金液总质量的3.1%,nacl和kcl的总添加量为合金液总质量的2.1%,所述nacl和kcl的质量比为35:65;
基于超声/电磁复合场对所述精炼液进行熔体处理,得到处理液;其中,所述熔体处理的操作参数包括:超声功率为320w,超声频率为15khz,电磁频率为22khz,电磁强度为125a;
将模具在250℃条件下预热50min,将所述处理液转入预热后的模具中,进行挤压铸造,得到合金铸锭;其中,所述处理液进行挤压铸造前经泡沫陶瓷过滤板(孔隙度为90ppi)过滤;所述挤压铸造的操作参数包括:浇铸温度为680℃,比压为520mpa,保压时间为30s,挤压速度为6mm/s;
将所述合金铸锭进行淬火处理,其中,淬火处理的时间为30s,淬火介质为10wt%的nacl水溶液,所述nacl水溶液的温度为25℃;淬火处理后自然风干,得到淬火合金铸锭;
将所述淬火合金铸锭依次进行固溶处理和时效处理,之后随炉冷却得到高强高耐磨al-si合金;其中,所述固溶处理的温度为500℃,时间为90min;所述时效处理的温度为175℃,时间为15h。
对比例2
本对比例中al-si合金,由以下质量百分比的成分组成:si13.5%,cu0.4%,mg0.32%,余量为al和不可避免的杂质,所述不可避免的杂质中,每种杂质的含量均低于0.01%。
本对比例中al-si合金的制备方法,包括以下步骤:
按照al-si合金的配方,将工业纯铝锭加入熔炼炉中,升温至700℃,保温熔炼5h,此时纯铝锭熔化到一半,加入纯mg和其它中间合金(具体为al-30%si和al-50%cu),升温至710℃,保温熔炼3.5h,得到合金液;
将除气机的精炼管插入所述合金液中进行喷粉精炼,以实现除气和除渣处理,得到精炼液;其中,所述喷粉精炼的操作参数包括:除气机的旋转速度为100rpm,进口压力为0.2mpa,出粉量为1.8kg/min,精炼时间为15min;所述喷粉精炼采用的精炼剂包括na3alf6、mg2n3、c2cl6、nacl和kcl,其中,na3alf6的添加量为合金液总质量的3.1%,mg2n3的添加量为合金液总质量的7.1%,c2cl6的添加量为合金液总质量的3.6%,nacl和kcl的总添加量为合金液总质量的3.8%,所述nacl和kcl的质量比为35:65;
基于超声/电磁复合场对所述精炼液进行熔体处理,得到处理液;其中,所述熔体处理的操作参数包括:超声功率为220w,超声频率为15khz,电磁频率为15khz,电磁强度为100a;
将模具在200℃条件下预热30min,将所述处理液转入预热后的模具中,进行挤压铸造,得到合金铸锭;其中,所述处理液进行挤压铸造前经泡沫陶瓷过滤板(孔隙度为100ppi)过滤;所述挤压铸造的操作参数包括:浇铸温度为680℃,比压为400mpa,保压时间为20s,挤压速度为6mm/s;
将所述合金铸锭进行淬火处理,其中,淬火处理的时间为30s,淬火介质为10wt%的nacl水溶液,所述nacl水溶液的温度为17℃;淬火处理后自然风干,得到淬火合金铸锭;
将所述淬火合金铸锭依次进行固溶处理和时效处理,之后随炉冷却得到al-si合金;其中,所述固溶处理的温度为500℃,时间为180min;所述时效处理的温度为200℃,时间为24h。
对实施例1~4和对比例1~2制备的合金进行性能测试,其中,拉伸试验在wgw-100h型万能材料试验机上完成,硬度测试是在hb3000型布氏硬度仪上完成,耐磨性能测试在mmu-5g材料端面高温摩擦磨损试验机上完成。
具体的,抗拉强度按照gb228-2000标准测试,屈服强度按照gb228-2000标准测试,延伸率按照gb/t17737.308-2018标准测试,硬度按照gb/t231.1-2009标准测试,摩擦系数按照gb3142-82标准测试;结果如表1所示。
由表1可知,本发明通过加入zn、mn、zr以及稀土元素la和er,且将合金成分控制在特定含量范围,保证所得合金具有较高的强度以及耐磨性,综合性能优异。
表1实施例1~4和对比例1~2制备的合金的性能测试结果
图1为实施例3制备的高强高耐磨al-si合金的显微组织图,由图1可知,经挤压成形后al-si合金组织细化效果好,si相尺寸减小,树枝状的α-al转变为等轴状,因此具有较好的力学性能。
图2为对比例1制备的al-si合金的显微组织图,由图2可知,由于al-si合金组织中未加入析出稀土元素,晶粒的细化程度减弱。
以上所述仅是本发明的优选实施方式,应当指出,对于本技术领域的普通技术人员来说,在不脱离本发明原理的前提下,还可以做出若干改进和润饰,这些改进和润饰也应视为本发明的保护范围。
起点商标作为专业知识产权交易平台,可以帮助大家解决很多问题,如果大家想要了解更多知产交易信息请点击 【在线咨询】或添加微信 【19522093243】与客服一对一沟通,为大家解决相关问题。
此文章来源于网络,如有侵权,请联系删除


