一种零件涂层制备装置及零件涂层制备方法、终端装置与流程



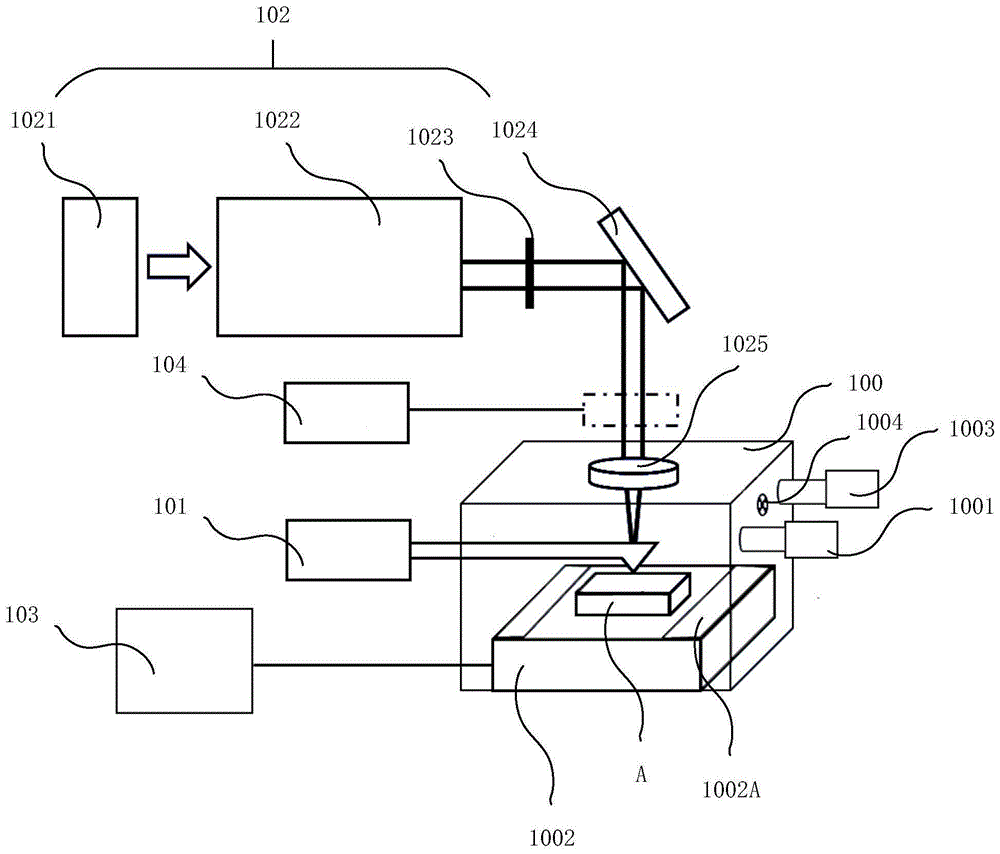
本发明涉及准分子激光器放电腔用涂层制造技术领域,尤其涉及一种零件涂层制备装置及零件涂层制备方法、终端装置。
背景技术:
准分子激光器是紫外波段重要的激光器件,依靠受激混合气体形成的分子向基态跃迁产生激光。但是混合气体中的卤素气体具有强腐蚀性,会与准分子激光器放电腔及其内部零件发生反应,造成准分子激光器放电腔表面污染并释放有害气体。严重影响准分子激光器放电腔的化学稳定性,影响激光器的输出性能。
另一方面,准分子激光器放电过程中会产生激波和声波。部分激波和声波会被阻挡结构反射回放电区,引起放电区气压梯度变化,降低放电区内工作气体的均匀性,进而影响准分子激光器输出能量的稳定性。
技术实现要素:
本发明的目的在于提供一种零件涂层制备装置及零件涂层制备方法、终端装置,用于在零件表面制备零件涂层,防止由于声波和激波的影响,造成工作气体不均匀以及零件在使用过程中被污染,从而影响激光器的输出性能的问题。
第一方面,本发明提供一种零件涂层制备装置,包括:真空样品室,用于为零件提供真空容置环境。与真空样品室连接的送粉装置,用于向真空样品室内的零件表面提供涂层粉末。涂层粉末的材质至少包括高熵合金。激光成形装置,用于对送粉装置提供的涂层粉末进行成形处理,得到零件涂层,零件涂层至少包括致密涂层和形成于致密涂层上的多孔涂层。
与现有技术相比,本发明提供的零件涂层制备装置中,利用高熵合金作为涂层粉末,由于高熵合金中元素组成以及各个元素含量可以调节,因此在不同钝化需求的零件表面制备零件涂层时,选用不同组成成分的高熵合金粉末,得到的对应的高熵合金涂层的耐腐蚀性能更好。并且,由于高熵合金具有抑制扩散的作用,可以抑制腐蚀气体和零件组成元素之间的扩散,从而降低零件和腐蚀气体之间的反应速率,提升零件的化学稳定性,增加激光器的输出性能。
另外,本发明提供的零件涂层制备装置中,零件涂层至少包括致密涂层和形成于致密涂层上的多孔涂层,使得零件表面的声波和激波衰减,提高激光器放电环境的稳定性,从而增加激光器的输出性能。
第二方面,本发明提供一种零件涂层制备方法,应用于具有真空样品室、送粉装置和激光成形装置的零件涂层制备装置。真空样品室内容置有零件。该零件涂层制备方法包括:
控制送粉装置向真空样品室内的零件表面提供涂层粉末。涂层粉末的材质至少包括高熵合金。
控制激光成形装置对送粉装置提供的涂层粉末进行成形处理,得到致密涂层。
控制激光成形装置对送粉装置提供的涂层粉末进行成形处理,得到多孔涂层。
第二方面提供的零件涂层制备方法的有益效果与第一方面或第一方面或任一可能的实现方式描述的零件涂层制备装置的有益效果相同,此处不做赘述。
第三方面,本发明提供一种终端设备。该终端设备包括:处理器以及与处理器耦合的通信接口。处理器用于运行计算机程序,实现第二方面或第二方面任一可能的实现方式描述的零件涂层制备方法。
第三方面提供的终端设备的有益效果与第一方面或第一方面或任一可能的实现方式描述的零件涂层制备装置的有益效果相同,此处不做赘述。
附图说明
此处所说明的附图用来提供对本发明的进一步理解,构成本发明的一部分,本发明的示意性实施例及其说明用于解释本发明,并不构成对本发明的不当限定。在附图中:
图1为本发明实施例中零件涂层制备装置的结构示意图;
图2为本发明实施例中零件涂层制备方法的结构示意图。
具体实施方式
为了使本发明所要解决的技术问题、技术方案及有益效果更加清楚明白,以下结合附图及实施例,对本发明进行进一步详细说明。应当理解,此处所描述的具体实施例仅仅用以解释本发明,并不用于限定本发明。
需要说明的是,当元件被称为“固定于”或“设置于”另一个元件,它可以直接在另一个元件上或者间接在该另一个元件上。当一个元件被称为是“连接于”另一个元件,它可以是直接连接到另一个元件或间接连接至该另一个元件上。
此外,术语“第一”、“第二”仅用于描述目的,而不能理解为指示或暗示相对重要性或者隐含指明所指示的技术特征的数量。由此,限定有“第一”、“第二”的特征可以明示或者隐含地包括一个或者更多个该特征。在本发明的描述中,“多个”的含义是两个或两个以上,除非另有明确具体的限定。“若干”的含义是一个或一个以上,除非另有明确具体的限定。
在本发明的描述中,需要理解的是,术语“上”、“下”、“前”、“后”、“左”、“右”等指示的方位或位置关系为基于附图所示的方位或位置关系,仅是为了便于描述本发明和简化描述,而不是指示或暗示所指的装置或元件必须具有特定的方位、以特定的方位构造和操作,因此不能理解为对本发明的限制。
在本发明的描述中,需要说明的是,除非另有明确的规定和限定,术语“安装”、“相连”、“连接”应做广义理解,例如,可以是固定连接,也可以是可拆卸连接,或一体地连接;可以是机械连接,也可以是电连接;可以是直接相连,也可以通过中间媒介间接相连,可以是两个元件内部的连通或两个元件的相互作用关系。对于本领域的普通技术人员而言,可以根据具体情况理解上述术语在本发明中的具体含义。
准分子激光器是紫外波段重要的激光器件,主要依靠受激混合气体形成的分子向基态跃迁产生激光。这里的混合气体一般是由惰性气体和卤素气体组成,如氩气(ar)和氟气(f2)、氪气(kr)和氟气、氙气(xe)和氯气(cl2)等。研究表明ppm量级的气态腐蚀产物,如hf、sif4、hcl等,将造成arf、krf等准分子激光器输出能量降低10%以上,并影响光束线宽/稳定性等多种参数。因此,需要对准分子激光器放电腔零部件材料的成分进行控制。既需要保证材料表面污染成分含量低,使得污染物能短时间内与卤素介质反应完毕,不会在准分子激光器运行过程中缓慢反应释放危害气体。又要求长时间工作状态下材料内部的危害元素扩散程度低,不会在准分子激光器运行过程逐渐向表面聚集生成大量危害元素。
另一方面,准分子激光器放电过程中将有大量的能量在几十纳秒以内被注入到放电区内很小空间的气体里面,该时间内放电区内工作气体尚未发生膨胀(即定容加热),但会产生温度和压力的跃变,之后气体的等熵膨胀便形成了以超声速向中性气体传播的激波,在该过程中同时伴随着声波的产生。产生的声波和激波向四周传播,到达阻挡结构时会被反射到不同方向。其中,反射回放电区的声波和激波将引起气压梯度变化,降低放电区内工作气体均匀性,进而影响准分子激光器输出能量的稳定性。因此,需要利用放电腔内的结构对声波和激波进行控制,降低其不利影响。
上述两个问题对放电腔零件的设计与制备提出了很高的要求。一方面,零件原材料常含有一定量的间隙元素,如碳、氮、氢、氧,以及部分与卤素介质产物为气态物质的元素如硅、磷等,需要尽量抑制这些元素向表面扩散。零件常规加工过程,表面也很容易引入危害性元素,生成复杂的表面污染层。此外,零件暴露于空气环境中,表面也会缓慢与碳氮氧元素反应,生成污染层。这些危害物质很难通过钝化清洗完全去除,显著影响着放电腔零件的化学稳定性,直接影响着激光器的输出性能。另一方面,放电腔内特殊的流场环境和腐蚀环境造成难以直接使用常规消除声波激波的材料,只能通过增加特殊气路结构或是特殊表面结构的方式,如特殊表面的反射体、腔壁上增加凹槽或层状多孔/堆叠板、采用迂回的气路结构等方法,设计方法复杂。
制备具有良好的耐卤素腐蚀性、极低有害成分含量、抑制危害元素扩散,并能够有效衰减声波与激波的零件涂层,将在很大程度上减少危害气体与声波激波的产生,提高准分子激光器放电环境的稳定性,为获得高性能的准分子激光器件奠定基础。因此,如何同时实现良好耐卤素腐蚀性、极低有害元素含量、抑制危害元素扩散,并能够有效衰减声波与激波的零件涂层成为确保准分子激光器放电环境稳定性的重要问题。
图1示例出本发明实施例提供的零件涂层制备装置的结构示意图。如图1所述,该零件涂层制备装置包括真空样品室100、送粉装置101和激光成形装置102。送粉装置101和真空样品室100连接。
如图1所示,上述零件a可以为激光器电极附近的零件,也可以是激光器其他部位的零件,并不限于此。放入真空样品室内的零件为去除污染层的零件。
如图1所示,上述真空样品室100用于为零件a提供真空容置环境。应理解,这里的真空容置环境可以是通过与真空样品室100连接的真空装置1001实现的。具体的,将零件a放入真空样品室100中,使用真空装置1001对真空样品室100进行抽真空处理,使得零件a置于真空环境中,防止在零件涂层制备的过程中,零件a表面材质与空气中的碳、氮、氧元素发生反应,生成污染层,且难以去除的问题。其中,真空样品室100的真空度为10-5pa~10-4pa。
如图1所述,上述送粉装置101用于向真空样品室内的零件a表面提供涂层粉末。这里的涂层粉末的材质至少包括高熵合金。高熵合金(high-entropyalloys)简称hea,是由五种或五种以上等量或大约等量金属形成的合金。由于高熵合金中元素组成以及各个元素含量可以调节,因此在不同钝化需求的零件表面制备零件涂层时,相应的选用不同组成成分的高熵合金粉末,得到的对应的高熵合金涂层的耐腐蚀性能更好。又由于高熵合金具有抑制扩散的作用,可以抑制腐蚀气体和零件a组成元素之间的扩散,从而降低零件a和腐蚀气体之间的反应速率,提升零件a的化学稳定性,增加激光器的输出性能。
如图1所述,上述激光成形装置102用于对送粉装置101提供的涂层粉末进行成形处理,得到零件涂层。这里的零件涂层至少包括致密涂层和形成于致密涂层上的多孔涂层。一方面,致密涂层用于隔绝零件和腐蚀气体,防止零件被污染,且释放出危害气体。另一方面,多孔涂层可以减弱零件a表面的声波和激波,使得激光器放电环境的稳定性提高,从而增加激光器的输出性能。
由上可知,本发明实施例提供的零件涂层制备装置用于在零件表面至少制备高熵合金涂层,使得零件具有良好的耐卤素腐蚀性,大大减少零件使用过程中有害元素的生成。同时,还可以降低零件和腐蚀气体之间的反应速率,提升零件的化学稳定性,增加激光器的输出性能。通过在零件表面制备多孔涂层,实现对激波和声波的有效衰减,显著提高零件质量与寿命,从而提高激光器放电环境的稳定性。且使用激光成形装置制备零件涂层的设计与制备难度较低,制备过程可控性较高。
作为一种可能的实现方式,如图1所示,上述零件涂层制备装置还包括位于真空样品室100内的移动载台1002和位于移动载台1002上的加热装置1002a。其中,移动载台1002用于承载零件a,加热装置1002a用于对去除表面污染物的零件a进行烘干处理。
在实际应用中,将上述去除表面污染物的零件放入真空样品室的移动载台上,使用加热装置对去除表面污染物的零件进行烘干处理,以去除零件上残留的水分,防止对制作零件涂层产生影响。
在一种可选方式,如图1所示,上述零件涂层制备装置还包括控制终端103。控制终端103和移动载台1002、激光成形装置102通信连接。该通信连接方式可以是无线通信,也可以是有线通信。无线通信可以基于wifi、zigbee等联网技术进行通信。有线通信可以基于数据线或电力线载波实现通信连接。通信接口可以为标准通信接口。该标准通信接口可以为串行接口,也可以为并行接口。例如:控制终端与移动载台可以采用i2c(inter-integratedcircuit)总线通信,也可以采用电力线载波通信技术实现通信连接。此时,控制终端可以用于控制移动载台移动,并将移动载台位置信息上报给控制终端。
上述控制终端可以为工控机或可实现工控机功能的手机、平板电脑等,控制终端可以控制移动载台和激光成形装置运动。例如:当激光成形装置为静止状态时,控制终端用于控制移动载台移动,使得激光成形装置发出的激光束对零件表面的涂层粉末进行成形处理,形成零件涂层。又例如,当激光成形装置为运动状态时,控制终端用于控制激光成形装置和移动载台相对运动,使得激光成形装置发出的激光束对零件表面的涂层粉末进行成形处理,形成零件涂层。
在一种示例中,当移动载台位置不变的情况下,控制终端可以控制激光成形装置移动,使得激光成形装置所发出的激光束对零件表面的涂层粉末进行成形处理,形成零件涂层。
在另一种示例中,当激光成型装置所发出的激光束位置不变的情况下,控制终端可以控制移动载台运动,使得移动载台上的零件表面的涂层粉末被激光成形装置所发出的激光束进行成形处理,形成零件涂层。
在一种可选方式,如图1所示,上述激光成形装置102包括激光控制器1021、激光器1022、光栅1023、反射镜1024以及聚焦透镜1025。该聚焦透镜1025的材质可以为caf2光学材料等透光性较好的材料。
如图1所示,上述激光器1022用于在激光控制器1021的控制下生成激光光束。光栅1023用于将激光光束进行分束,得到分束光束。反射镜1024用于反射分束光束,改变分束光束路径。聚焦透镜1025用于将分束光束聚焦到零件表面的涂层粉末上,使得零件表面的图层粉末熔覆后,形成零件涂层。
在一种可选方式,如图1所示,上述零件涂层制备装置还包括和控制终端103连接的能量检测装置104。该能量检测装置104在控制终端103的控制下检测激光成形装置102发出的激光能量,以防止激光能量过高容易造成涂层粉末的烧蚀和蒸发,或者激光能量过低不能保证涂层粉末完全熔融成均匀零件涂层的情况发生。由于激光光束的能量范围于制备的材料特性有关,因此,针对不同的材料,选用的激光光束的能量范围不同。
在实际应用中,激光器在激光控制器的控制下发出激光光束,激光光束通过光栅分束,反射镜改变光路后,由控制终端控制能量检测装置检测激光光束的能量,能量检测装置将激光光束的能量检测结果发送给控制终端。经过检测的激光光束通过聚焦透镜聚焦后,照射在零件表面的涂层粉末上,对零件表面的涂层粉末进行成形处理,形成零件涂层。这里的激光光束可以为连续激光,也可以为脉冲激光等,并不限于此。激光波长为150nm~10.6μm。激光光斑直径范围约30μm~1000μm。
在一种可选方式,如图1所示,上述零件涂层制备装置还包括与真空样品室100连接的控制阀,用于向真空样品室内充入气体。
如图1所示,上述控制阀包括与真空样品室连接的卤素气体阀1003,该卤素气体阀1003用于像真空样品室100中通入卤素气体。零件涂层的制备环境可以根据对零件材料钝化程度要求进行选择。例如,应用于电极附近的零件将承受较高的温度及少量的卤素离子轰击,因此需要更高的钝化程度和更严格的危害元素控制。对于该零件涂层制备环境应选择含卤素介质体积含量为0.1%~0.5%的常压氩气环境作为制备环境,在制备的同时加速实现零件涂层的卤素化,此时需要使用卤素气体阀1003向真空样品室100中通入卤素气体。又例如,应用于其它部位的零件,不需要较高的钝化程度时,采用真空度10-5pa~10-4pa真空环境制备即可,当然,也可以采用含卤素介质体积含量为0.1%~0.5%的常压氩气环境作为制备环境,制备出钝化程度较高的零件。
如图1所示,上述控制阀包括与真空样品室连接的空气阀1004。空气阀1004用于在零件涂层制备完成后,向真空样品室100中通入空气,释放真空样品室100内的压力,使得真空样品室100达到常压状态,便于取出具有零件涂层的零件。
在一种可选方式,如图1所示,上述真空样品室100的材质、送粉装置101的材质、移动载台1002的材质、加热装置1002a的材质、控制阀的材质中的至少一种为经过钝化处理的耐卤素腐蚀金属或经过钝化处理的耐卤素腐蚀橡胶。以防止被卤素介质腐蚀,影响零件涂层制备装置的使用寿命。这里的钝化处理可以是经强氧化剂或电化学方法氧化处理,并不限于此。耐卤素腐蚀金属可以是镍金属,也可以是高熵合金等。耐卤素腐蚀橡胶可以是全氟橡胶等,并不限于此。
本发明实施例还提供了一种终端设备。该终端设备包括:处理器以及与处理器耦合的通信接口。处理器用于运行计算机程序,实现上述零件涂层制备方法。
下面以终端设备为执行主体描述本发明实施例提供的一种零件涂层制备方法。该零件涂层制备方法可以由终端设备执行的步骤,也可以由应用于终端设备中的芯片执行。下面实施例以终端设备为主要执行主体进行描述。图2示例出本发明实施例提供的一种零件涂层制备方法的结构示意图。如图2所示,该零件涂层制备方法应用于具有真空样品室、送粉装置和激光成形装置的零件涂层制备装置。真空样品室内容置有零件。真空样品室的真空度为10-5pa~10-4pa。
如图2所示,该零件涂层制备方法包括:
步骤s101:终端设备控制送粉装置向真空样品室内的零件表面提供涂层粉末。涂层粉末的材质至少包括高熵合金。
如图2所示,上述零件为去除污染层的零件。去除零件污染层的方式可以为:使用超声波蒸馏水清洗待制备涂层的零件5min~20min,去除零件表面附着的污渍。然后使用浓度为2mol/l~5mol/l的hcl溶液或是hf溶液清洗零件表面2min~5min,以去除零件表面氧化物,最后使用蒸馏水将零件表面残留的酸液冲洗干净并快速吹干表面水分,放入真空样品室中即可。当然,也可以使用其他方式去除零件表面污染物,并不限于此。
如图2所示,上述高熵合金为fe、co、ni、cu、mn、cr、ti、al八种元素中的至少五种。例如,高熵合金可以为feconicumn、crfeconiti、alcocrfeni、fe、co、ni、cu、mn、cr、ti、al等。高熵合金的状态为粒度为20μm~200μm的球形高纯粉料。
当然,为了更好的抑制腐蚀气体的扩散,提高零件化学稳定性。可以选用高熵合金和含卤素介质的纳米颗粒作为涂层粉末。该含卤素介质的纳米颗粒为caf2、mgf2和cacl2中的一种或多种。含卤素介质的纳米颗粒的粒径为1nm~1000μm。
步骤s102:终端设备控制激光成形装置对送粉装置提供的涂层粉末进行成形处理,得到致密涂层。
步骤s103:终端设备控制激光成形装置对送粉装置提供的涂层粉末进行成形处理,得到多孔涂层。
在上述零件涂层制备方法中,通过使用至少包括高熵合金的涂层粉末制备零件涂层,抑制零件组成元素和腐蚀气体之间扩散,减弱零件和腐蚀气体的反应,防止有害气体的生成,同时,使得零件具有良好的耐卤素腐蚀性。通过形成多孔涂层,减弱声波和激波,提高激光器放电环境的稳定性。
在一种可选方式中,如图2所示,上述零件涂层制备装置还包括加热装置。终端设备控制送粉装置向真空样品室内的零件表面提供涂层粉末前,零件涂层制备方法还包括:
步骤s1011a:终端设备控制加热装置对真空样品室内的零件进行加热。以去除零件表面残留的水分,防止影响零件涂层的成形。其中,零件加热温度为100℃~110℃,零件加热时间为30min。
在一种可选方式中,上述零件涂层制备装置还包括加热装置。终端设备控制送粉装置向真空样品室内的零件表面提供涂层粉末前,零件涂层制备方法还包括:
步骤s1012a:终端设备根据零件应用信息向真空样品室提供卤素介质,得到卤素介质体积含量为0.1%~0.5%的常压氩气环境。使得在涂层充分卤素化,充分卤素化的涂层再使用时几乎不与腐蚀气体反应,使得制得的零件更加稳定。
在一种可选方式中,如图2所示,上述零件涂层制备装置还包括移动载台。终端设备控制激光成形装置对送粉装置提供的涂层粉末进行成形处理,得到致密涂层包括:
步骤s1021a:当激光成形装置为静止状态时,终端设备控制移动载台移动,使得激光成形装置发出的激光束对零件表面的涂层粉末进行成形处理,得到致密度在95%以上的致密涂层。
步骤s1022a:当激光成形装置为运动状态时,终端设备控制激光成形装置和移动载台相对运动,使得激光成形装置发出的激光束对零件表面的涂层粉末进行成形处理,得到致密度在95%以上的致密涂层。激光成形装置和移动载台相对运动方式参考上文描述,在此不再赘述。
需要说明的是,上述致密涂层的层数可以根据零件的应用环境选择,例如,致密涂层的层数可以是1层,可以是2层,也可以是3层等。通过在零件表面形成致密涂层,隔绝零件和腐蚀气体,从而防止零件和卤素气体发生反应,生成污染物,影响激光器的性能。
在一种可选方式中,如图2所示,上述零件涂层制备装置还包括移动载台,终端设备控制激光成形装置对送粉装置提供的涂层粉末进行成形处理,得到多孔涂层包括:
步骤s1031a:终端设备控制送粉装置向致密涂层的表面提供涂层粉末。
步骤s1031b:当激光成形装置为静止状态时,终端设备控制移动载台移动,使得激光成形装置发出的激光束对致密涂层的表面上的涂层粉末进行成形处理,形成孔隙率为20%~40%的多孔涂层。
步骤s1032b:当激光成形装置为运动状态时,终端设备控制激光成形装置和移动载台相对运动,使得激光成形装置发出的激光束对致密涂层的表面上的涂层粉末进行成形处理,形成孔隙率为20%~40%的多孔涂层。激光成形装置和移动载台相对运动方式参考上文描述,在此不再赘述。
需要说明的是,上述多孔涂层的层数可以根据零件的应用环境选择,例如,多孔涂层的层数可以是1层,可以是2层,也可以是3层等。通过调整激光功率密度、样品扫描速度、样品离焦量等参数,在致密涂层上形成多孔涂层,可以减弱声波和激波,提高激光器的性能。
由于零件放置位置的激波与声波的强度、反射方向不同,在声波和激波的强度较强的区域的零件需要形成吸波效果更好的多孔涂层。基于此,如图2所示,上述零件涂层制备装置还包括移动载台,终端设备控制激光成形装置对送粉装置提供的涂层粉末进行成形处理,得到多孔涂层后,零件涂层制备方法还包括:
步骤s1041a:终端设备控制送粉装置向多孔涂层的表面提供涂层粉末。
步骤s1041b:当激光成形装置为静止状态时,终端设备控制移动载台移动,使得激光成形装置发出的激光束对多孔涂层的表面上的涂层粉末进行成形处理,形成多孔结构。
步骤s1042b:当激光成形装置为运动状态时,终端设备控制激光成形装置和移动载台相对运动,使得激光成形装置发出的激光束对多孔涂层的表面上的涂层粉末进行成形处理,形成多孔结构。激光成形装置和移动载台相对运动方式参考上文描述,在此不再赘述。
在一种可选方式中,如图2所示,上述多孔结构包括孔隙率为20%~40%的多孔涂层和间距为10μm~500μm,厚度为100μm~1000μm的周期性凹槽结构中的一种或两种的结合。例如,该多孔结构可以为间距为10μm~500μm,厚度为100μm~1000μm的周期性凹槽结构,以提升多孔涂层的吸波效果,衰减声波和激波,从而提升激光器的性能。
在一种可选方式中,如图2所示,上述终端设备控制激光成形装置对送粉装置提供的涂层粉末进行成形处理,得到多孔涂层后,零件涂层制备方法还包括:
步骤s105a:向真空样品室提供空气,使得真空样品室形成常压环境。需要注意的是,当零件涂层制备环境为真空环境时,终端设别控制空气阀向真空样品室充入空气至常压即可。当零件涂层制备环境为含卤素气体环境时,则需要排出真空样品室内的气体并抽真空至10-5pa,充入空气后再抽真空至10-5pa,再充入空气至常压即可。以防止卤素气体溢出,污染环境并对操作人员产生危害。
下面结合实施例对本发明实施例提供的零件涂层制备方法进行进一步的说明。
实施例1
选用的零件为arf准分子激光器放电腔铜合金垫片。该零件涂层的制备方法包括:
1)使用超声波蒸馏水清洗待制备涂层的铜合金垫片零件约10min,去除表面附着的污染物。
2)使用浓度为2.5mol/l的hcl溶液清洗铜合金垫片零件表面2min,去除表面氧化层。
3)使用蒸馏水将零件表面残留的酸液冲洗干净并快速吹干表面水分,放入真空样品室中。
4)开启真空装置对真空样品室抽真空至10-5pa,开启加热装置加热样品至100℃,烘干30min后,去除残留的水分,关闭加热装置。
5)开启卤素气体阀通入含氟气介质含量为0.1%的常压氩气环境作为制备环境。
6)根据零件基体材质,晶格匹配和耐腐蚀性原则,选择高熵合金种类为feconicumn,选择稳定的caf2颗粒作为卤素扩散的抑制颗粒。在激光制备的送粉装置中加入高熵合金粒度为20μm的球形高纯粉料。
7)开启激光控制器和激光器,激光束通过光栅,反射镜,聚焦镜作用于零件表面,其中激光为1.06微米的连续激光,光斑直径约500μm。通过控制终端控制移动载台实现样品的移动,在零件表面制备具有耐卤素气体腐蚀性的高熵合金涂层。
8)使用激光控制器调整激光功率密度、样品扫描速度、样品离焦量等参数,打印2层致密度不低于95%致密涂层。
9)使用激光控制器和移动载台调整激光功率密度、样品扫描速度、样品离焦量等参数,继续制备3层孔隙率约20%多孔涂层。
10)根据零件放置位置的激波与声波的强度/反射方向等情况,使用激光控制器调整激光功率密度、样品扫描速度、样品离焦量等参数,再多孔涂层上继续制备间距10μm,厚度为100μm的周期性直角凹槽结构;
11)排出真空样品室的含氟气体并抽真空至10-5pa,开启空气阀充入空气至常压后关闭,再开启真空装置抽真空至10-5pa后关闭,开启空气阀充入空气至常压,将铜合金垫片零件取出。
实施例2
选用的零件为arf准分子激光器放电腔铜合金垫片。该零件涂层的制备方法包括:
1)使用超声波蒸馏水清洗待制备涂层的铜合金垫片零件约15min,去除表面附着的污染物。
2)使用浓度为3mol/l的hcl溶液清洗铜合金垫片零件表面3min,去除表面氧化层。
3)使用蒸馏水将零件表面残留的酸液冲洗干净并快速吹干表面水分,放入真空样品室中。
4)开启真空装置对真空样品室抽真空至10-5pa,开启加热装置加热样品至105℃,烘干30min后,去除残留的水分,关闭加热装置。
5)开启卤素气体阀通入含氯气介质含量为0.25%的常压氩气环境作为制备环境。
6)根据零件基体材质,晶格匹配和耐腐蚀性原则,选择高熵合金种类为crfeconiti,选择稳定的mgf2颗粒作为卤素扩散的抑制颗粒。在激光制备的送粉装置中加入高熵合金粒度为40μm的球形高纯粉料。
7)开启激光控制器和激光器,激光束通过光栅,反射镜,聚焦镜作用于零件表面,其中激光为1.06微米的连续激光,光斑直径约500μm。通过控制终端控制移动载台实现样品的移动,在零件表面制备具有耐卤素气体腐蚀性的高熵合金涂层。
8)使用激光控制器调整激光功率密度、样品扫描速度、样品离焦量等参数,打印1层致密度不低于97%致密涂层。
9)使用激光控制器和移动载台调整激光功率密度、样品扫描速度、样品离焦量等参数,继续制备2层孔隙率约30%多孔涂层。
10)根据零件放置位置的激波与声波的强度/反射方向等情况,使用激光控制器调整激光功率密度、样品扫描速度、样品离焦量等参数,再多孔涂层上继续制备间距255μm,厚度为500μm的周期性直角凹槽结构;
11)排出真空样品室的含氟气体并抽真空至10-5pa,开启空气阀充入空气至常压后关闭,再开启真空装置抽真空至10-5pa后关闭,开启空气阀充入空气至常压,将铜合金垫片零件取出。
实施例3
选用的零件为arf准分子激光器放电腔铜合金垫片。该零件涂层的制备方法包括:
1)使用超声波蒸馏水清洗待制备涂层的铜合金垫片零件约20min,去除表面附着的污染物。
2)使用浓度为5mol/l的hcl溶液清洗铜合金垫片零件表面5min,去除表面氧化层。
3)使用蒸馏水将零件表面残留的酸液冲洗干净并快速吹干表面水分,放入真空样品室中。
4)开启真空装置对真空样品室抽真空至10-5pa,开启加热装置加热样品至110℃,烘干30min后,去除残留的水分,关闭加热装置。
5)开启卤素气体阀通入含氯气介质含量为0.5%的常压氩气环境作为制备环境。
6)根据零件基体材质,晶格匹配和耐腐蚀性原则,选择高熵合金种类为alcocrfeni,选择稳定的cacl2颗粒作为卤素扩散的抑制颗粒。在激光制备的送粉装置中加入高熵合金粒度为200μm的球形高纯粉料。
7)开启激光控制器和激光器,激光束通过光栅,反射镜,聚焦镜作用于零件表面,其中激光为1.06微米的连续激光,光斑直径约500μm。通过控制终端控制移动载台实现样品的移动,在零件表面制备具有耐卤素气体腐蚀性的高熵合金涂层。
8)使用激光控制器调整激光功率密度、样品扫描速度、样品离焦量等参数,打印1层致密度不低于98%致密涂层。
9)使用激光控制器和移动载台调整激光功率密度、样品扫描速度、样品离焦量等参数,继续制备2层孔隙率约40%多孔涂层。
10)根据零件放置位置的激波与声波的强度/反射方向等情况,使用激光控制器调整激光功率密度、样品扫描速度、样品离焦量等参数,再多孔涂层上继续制备间距500μm,厚度为1000μm的周期性直角凹槽结构;
11)排出真空样品室的含氟气体并抽真空至10-5pa,开启空气阀充入空气至常压后关闭,再开启真空装置抽真空至10-5pa后关闭,开启空气阀充入空气至常压,将铜合金垫片零件取出。
在上述实施方式的描述中,具体特征、结构、材料或者特点可以在任何的一个或多个实施例或示例中以合适的方式结合。
以上所述,仅为本发明的具体实施方式,但本发明的保护范围并不局限于此,任何熟悉本技术领域的技术人员在本发明揭露的技术范围内,可轻易想到变化或替换,都应涵盖在本发明的保护范围之内。因此,本发明的保护范围应以所述权利要求的保护范围为准。
起点商标作为专业知识产权交易平台,可以帮助大家解决很多问题,如果大家想要了解更多知产交易信息请点击 【在线咨询】或添加微信 【19522093243】与客服一对一沟通,为大家解决相关问题。
此文章来源于网络,如有侵权,请联系删除


