一种梯度多孔陶瓷型芯及其制备方法与流程



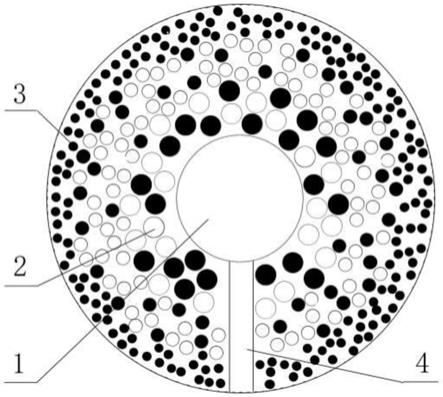
70%;锆英15%-20%;白石蜡10%-15%;邻苯二甲酸二乙酯1%-2%;粉煤灰漂珠3%-30%;泡沫塑料颗粒5%-10%;蜂蜡1%-2%;聚乙烯0.05%-1%;油酸0.05%-1%;合计100%。
[0026]
其中,石英玻璃作为基体材料,锆英作为烧结催化剂,基体材料与烧结催化剂一起称为陶瓷浆料粉末;粉煤灰漂珠和泡沫塑料颗粒一起作为功能性填料;白石蜡、邻苯二甲酸二乙酯、蜂蜡、聚乙烯一起作为塑化剂,共同组成型芯中的蜡芯。油酸作为脱模剂的一种,能够提高了陶瓷型芯的气孔率,加快了陶瓷型芯的脱芯速率。
[0027]
本发明的梯度多孔陶瓷型芯的制备方法,按照以下步骤实施:
[0028]
预备步骤:按照质量百分比称取各个组分,其中,石英玻璃60%-70%;锆英15%-20%;白石蜡10%-15%;邻苯二甲酸二乙酯1%-2%;粉煤灰漂珠3%-30%;泡沫塑料颗粒5%-10%;蜂蜡1%-2%;聚乙烯0.05%-1%;油酸0.05%-1%;合计100%;从石英玻璃总量中分出10%制备方电熔石英、分出10%制备耐火材料,剩余石英玻璃制备石英玻璃粉末;
[0029]
步骤1:制备热塑性陶瓷浆料,
[0030]
1.1)将白石蜡、邻苯二甲酸二乙酯、蜂蜡、聚乙烯一起放入搅拌机中,升温至120-150℃,待其完全融化后得到“蜡芯”,用于放入陶瓷型芯内部作为陶瓷型芯内层中的“蜡芯”;
[0031]
1.2)采用不同粒径的石英玻璃粉末和锆英粉末,将石英玻璃粉末、锆英粉末、方电熔石英三种原料依次放入球磨罐中,加入粒径0.1-0.5mm的功能填料(粉煤灰漂珠和泡沫塑料颗粒),五种原料之和与球磨小球的质量比为5:1;在室温下充分球磨1-2h后,将混合粉体置入烘箱中在150-200℃条件下干燥1-3h;将烘箱中的混合粉体取出,并与制备融化好的蜡芯及油酸混合均匀,控制搅拌转速为400-800r/min,在100-220℃条件下搅拌10-15h,以保证浆料成分均匀,得到多孔致密化浆料;
[0032]
步骤2:热压注,得到成型的陶瓷型芯坯体,
[0033]
将多孔致密化浆料,在表层挤入300~600目的耐火材料(因为涉及梯度,该耐火材料同样从石英玻璃粉末总量中分出10%制备而成。)分梯度预成型,使用陶瓷型芯高压压注机进行压制工序,放入热压注成型机的料桶中,在80-100℃下加热至熔融状态后进行压注,采用油酸作为脱模剂,压注压力为2-4mpa,保压时间20-30s,压注温度为室温;将刚出模的湿态型芯,在湿态情况下放入校正胎具中,用压力机加压,进行尺寸校正,以保证的湿态型芯尺寸良好,无欠注、裂纹现象,得到陶瓷型芯坯体。
[0034]
本步骤采用的陶瓷型芯高压压注机、热压注成型机、校正胎具、压力机均采用公开市场上的现有设备。
[0035]
步骤3:模具加热固化成型,
[0036]
将制备好的陶瓷型芯坯体装入陶瓷槽中,在不同组分对应的熔点进行分梯度升温及保温,保温时间根据组分含量不同有所差异,保持升温速度为120-250℃/h,且每连续升温1h后保温10-20min;当升温至600℃时,保温2h,使陶瓷型芯坯体中的“蜡芯”完全脱除变成空心梯度结构;当升温至1400℃达到最终烧结温度,保温烧结4h;随后按照100℃/h的速度冷却至200-500℃后,再随炉冷却直至室温时取出,得到表面致密化且光滑化的梯度多孔陶瓷型芯,即成。
[0037]
参照图1,本发明方法制备的梯度多孔陶瓷型芯,蜡芯1脱蜡后即形成空心陶瓷型
芯;空心陶瓷型芯中为疏松多孔的漂珠2和石英玻璃粉末3;排蜡孔4用于排除出融化后的蜡芯1。该梯度多孔陶瓷型芯表层为致密结构,用于成型金属铸件内腔,内层为从外至内由密到疏依次排列梯度结构。
[0038]
实施例1
[0039]
预备步骤:按照质量百分比称量以下组分:石英玻璃60%;锆英15%;白石蜡12%;邻苯二甲酸二乙酯1%;粉煤灰漂珠8%;泡沫塑料颗粒2%,蜂蜡1.9%;聚乙烯0.05%;油酸0.05%;合计100%。从石英玻璃总量中分出10%制备方电熔石英、分出10%制备耐火材料,剩余石英玻璃制备石英玻璃粉末;
[0040]
步骤1:制备热塑性陶瓷浆料,
[0041]
1.1)将白石蜡、邻苯二甲酸二乙酯、蜂蜡、聚乙烯一起放入搅拌机中,升温至120℃,待其完全融化后得到“蜡芯”,用于放入陶瓷型芯内部作为陶瓷型芯内层中的“蜡芯”;
[0042]
1.2)采用不同粒径的石英玻璃粉末和锆英粉末,将石英玻璃粉末、锆英粉末、方电熔石英三种原料依次放入球磨罐中,加入粒径0.1mm的功能填料(粉煤灰漂珠和泡沫塑料颗粒),五种原料之和与球磨小球的质量比为5:1;在室温下充分球磨1h后,将混合粉体置入烘箱中在200℃条件下干燥2h;将烘箱中的混合粉体取出,并与制备融化好的蜡芯及油酸混合均匀,控制搅拌转速为400r/min,在100℃条件下搅拌15h,得到多孔致密化浆料;
[0043]
步骤2:热压注,得到成型的陶瓷型芯坯体,
[0044]
将多孔致密化浆料,在表层挤入300目的耐火材料(该耐火材料同样从石英玻璃粉末总量中分出10%制备而成。)分梯度预成型,使用陶瓷型芯高压压注机进行压制工序,放入热压注成型机的料桶中,在80℃下加热至熔融状态后进行压注,采用油酸作为脱模剂,压注压力为3mpa,保压时间30s,压注温度为室温;将刚出模的湿态型芯,在湿态情况下放入校正胎具中,用压力机加压,进行尺寸校正,以保证的湿态型芯尺寸良好,无欠注、裂纹现象,得到陶瓷型芯坯体。
[0045]
步骤3:模具加热固化成型,
[0046]
将制备好的陶瓷型芯坯体装入陶瓷槽中,在不同组分对应的熔点进行分梯度升温及保温,保温时间根据组分含量不同有所差异,保持升温速度为120℃/h,且每连续升温1h后保温20min;当升温至600℃时,保温2h,使陶瓷型芯坯体中的“蜡芯”完全脱除变成空心梯度结构;当升温至1400℃达到最终烧结温度,保温烧结4h;随后按照100℃/h的速度冷却至200℃后,再随炉冷却直至室温时取出,得到表面致密化且光滑化的梯度多孔陶瓷型芯,即成。
[0047]
实施例2
[0048]
预备步骤:按照质量百分比称量以下组分:石英玻璃65%;锆英10%;白石蜡10%;邻苯二甲酸二乙酯1.8%;粉煤灰漂珠7%;泡沫塑料颗粒5%,蜂蜡1%;聚乙烯0.1%;油酸0.1%;合计100%。从石英玻璃总量中分出10%制备方电熔石英、分出10%制备耐火材料,剩余石英玻璃制备石英玻璃粉末;
[0049]
步骤1:制备热塑性陶瓷浆料,
[0050]
1.1)将白石蜡、邻苯二甲酸二乙酯、蜂蜡、聚乙烯一起放入搅拌机中,升温至150℃,待其完全融化后得到“蜡芯”,用于放入陶瓷型芯内部作为陶瓷型芯内层中的“蜡芯”;
[0051]
1.2)采用不同粒径的石英玻璃粉末和锆英粉末,将石英玻璃粉末、锆英粉末、方电
熔石英三种原料依次放入球磨罐中,加入粒径0.5mm的功能填料(粉煤灰漂珠和泡沫塑料颗粒),五种原料之和与球磨小球的质量比为5:1;在室温下充分球磨2h后,将混合粉体置入烘箱中在180℃条件下干燥1h;将烘箱中的混合粉体取出,并与制备融化好的蜡芯及油酸混合均匀,控制搅拌转速为800r/min,在200℃条件下搅拌10h,得到多孔致密化浆料;
[0052]
步骤2:热压注,得到成型的陶瓷型芯坯体,
[0053]
将多孔致密化浆料,在表层挤入600目的耐火材料(该耐火材料同样从石英玻璃粉末总量中分出10%制备而成。)分梯度预成型,使用陶瓷型芯高压压注机进行压制工序,放入热压注成型机的料桶中,在100℃下加热至熔融状态后进行压注,采用油酸作为脱模剂,压注压力为4mpa,保压时间20s,压注温度为室温;将刚出模的湿态型芯,在湿态情况下放入校正胎具中,用压力机加压,进行尺寸校正,以保证的湿态型芯尺寸良好,无欠注、裂纹现象,得到陶瓷型芯坯体。
[0054]
步骤3:模具加热固化成型,
[0055]
将制备好的陶瓷型芯坯体装入陶瓷槽中,在不同组分对应的熔点进行分梯度升温及保温,保温时间根据组分含量不同有所差异,保持升温速度为250℃/h,且每连续升温1h后保温15min;当升温至600℃时,保温2h,使陶瓷型芯坯体中的“蜡芯”完全脱除变成空心梯度结构;当升温至1400℃达到最终烧结温度,保温烧结4h;随后按照100℃/h的速度冷却至500℃后,再随炉冷却直至室温时取出,得到表面致密化且光滑化的梯度多孔陶瓷型芯,即成。
[0056]
实施例3
[0057]
预备步骤:按照质量百分比称量以下组分:石英玻璃70%;锆英14%;白石蜡10%;邻苯二甲酸二乙酯1%;粉煤灰漂珠1%;泡沫塑料颗粒1%,蜂蜡1%;聚乙烯1%;油酸1%;合计100%。
[0058]
从石英玻璃总量中分出10%制备方电熔石英、分出10%制备耐火材料,剩余石英玻璃制备石英玻璃粉末;
[0059]
步骤1:制备热塑性陶瓷浆料,
[0060]
1.1)将白石蜡、邻苯二甲酸二乙酯、蜂蜡、聚乙烯一起放入搅拌机中,升温至140℃,待其完全融化后得到“蜡芯”,用于放入陶瓷型芯内部作为陶瓷型芯内层中的“蜡芯”;
[0061]
1.2)采用不同粒径的石英玻璃粉末和锆英粉末,将石英玻璃粉末、锆英粉末、方电熔石英三种原料依次放入球磨罐中,加入粒径0.4mm的功能填料(粉煤灰漂珠和泡沫塑料颗粒),五种原料之和与球磨小球的质量比为5:1;在室温下充分球磨1.5h后,将混合粉体置入烘箱中在180℃条件下干燥1.5h;将烘箱中的混合粉体取出,并与制备融化好的蜡芯及油酸混合均匀,控制搅拌转速为500r/min,在220℃条件下搅拌10h,得到多孔致密化浆料;
[0062]
步骤2:热压注,得到成型的陶瓷型芯坯体,
[0063]
将多孔致密化浆料,在表层挤入500目的耐火材料(该耐火材料同样从石英玻璃粉末总量中分出10%制备而成。)分梯度预成型,使用陶瓷型芯高压压注机进行压制工序,放入热压注成型机的料桶中,在90℃下加热至熔融状态后进行压注,采用油酸作为脱模剂,压注压力为2.5mpa,保压时间25s,压注温度为室温;将刚出模的湿态型芯,在湿态情况下放入校正胎具中,用压力机加压,进行尺寸校正,以保证的湿态型芯尺寸良好,无欠注、裂纹现象,得到陶瓷型芯坯体。
[0064]
步骤3:模具加热固化成型,
[0065]
将制备好的陶瓷型芯坯体装入陶瓷槽中,在不同组分对应的熔点进行分梯度升温及保温,保温时间根据组分含量不同有所差异,保持升温速度为160℃/h,且每连续升温1h后保温15min;当升温至600℃时,保温2h,使陶瓷型芯坯体中的“蜡芯”完全脱除变成空心梯度结构;当升温至1400℃达到最终烧结温度,保温烧结4h;随后按照100℃/h的速度冷却至350℃后,再随炉冷却直至室温时取出,得到表面致密化且光滑化的梯度多孔陶瓷型芯,即成。
[0066]
实施例4
[0067]
预备步骤:按照质量百分比称量以下组分:石英玻璃60%;锆英15%;白石蜡15%;邻苯二甲酸二乙酯2%;粉煤灰漂珠2%;泡沫塑料颗粒2%,蜂蜡2%;聚乙烯1%;油酸1%;合计100%。
[0068]
从石英玻璃总量中分出10%制备方电熔石英、分出10%制备耐火材料,剩余石英玻璃制备石英玻璃粉末;
[0069]
步骤1:制备热塑性陶瓷浆料,
[0070]
1.1)将白石蜡、邻苯二甲酸二乙酯、蜂蜡、聚乙烯一起放入搅拌机中,升温至140℃,待其完全融化后得到“蜡芯”,用于放入陶瓷型芯内部作为陶瓷型芯内层中的“蜡芯”;
[0071]
1.2)采用不同粒径的石英玻璃粉末和锆英粉末,将石英玻璃粉末、锆英粉末、方电熔石英三种原料依次放入球磨罐中,加入粒径0.4mm的功能填料(粉煤灰漂珠和泡沫塑料颗粒),五种原料之和与球磨小球的质量比为5:1;在室温下充分球磨1.5h后,将混合粉体置入烘箱中在180℃条件下干燥1.5h;将烘箱中的混合粉体取出,并与制备融化好的蜡芯及油酸混合均匀,控制搅拌转速为500r/min,在220℃条件下搅拌10h,得到多孔致密化浆料;
[0072]
步骤2:热压注,得到成型的陶瓷型芯坯体,
[0073]
将多孔致密化浆料,在表层挤入500目的耐火材料(该耐火材料同样从石英玻璃粉末总量中分出10%制备而成。)分梯度预成型,使用陶瓷型芯高压压注机进行压制工序,放入热压注成型机的料桶中,在90℃下加热至熔融状态后进行压注,采用油酸作为脱模剂,压注压力为2.5mpa,保压时间25s,压注温度为室温;将刚出模的湿态型芯,在湿态情况下放入校正胎具中,用压力机加压,进行尺寸校正,以保证的湿态型芯尺寸良好,无欠注、裂纹现象,得到陶瓷型芯坯体。
[0074]
步骤3:模具加热固化成型,
[0075]
将制备好的陶瓷型芯坯体装入陶瓷槽中,在不同组分对应的熔点进行分梯度升温及保温,保温时间根据组分含量不同有所差异,保持升温速度为160℃/h,且每连续升温1h后保温15min;当升温至600℃时,保温2h,使陶瓷型芯坯体中的“蜡芯”完全脱除变成空心梯度结构;当升温至1400℃达到最终烧结温度,保温烧结4h;随后按照100℃/h的速度冷却至350℃后,再随炉冷却直至室温时取出,得到表面致密化且光滑化的梯度多孔陶瓷型芯,即成。
[0076]
综上所述,针对上述四个实施例采用本发明的方法制得的梯度多孔陶瓷型芯型芯结构梯度更紧凑、高温强度好,高温热稳定性好,型芯内部结构多孔致密化、表面光滑化。有效的解决了陶瓷型芯的脱除时间长,脱芯效率低下的问题,大幅提高了陶瓷型芯的脱除效率。
起点商标作为专业知识产权交易平台,可以帮助大家解决很多问题,如果大家想要了解更多知产交易信息请点击 【在线咨询】或添加微信 【19522093243】与客服一对一沟通,为大家解决相关问题。
此文章来源于网络,如有侵权,请联系删除



tips