一种金属陶瓷复合部件及其制备方法与流程



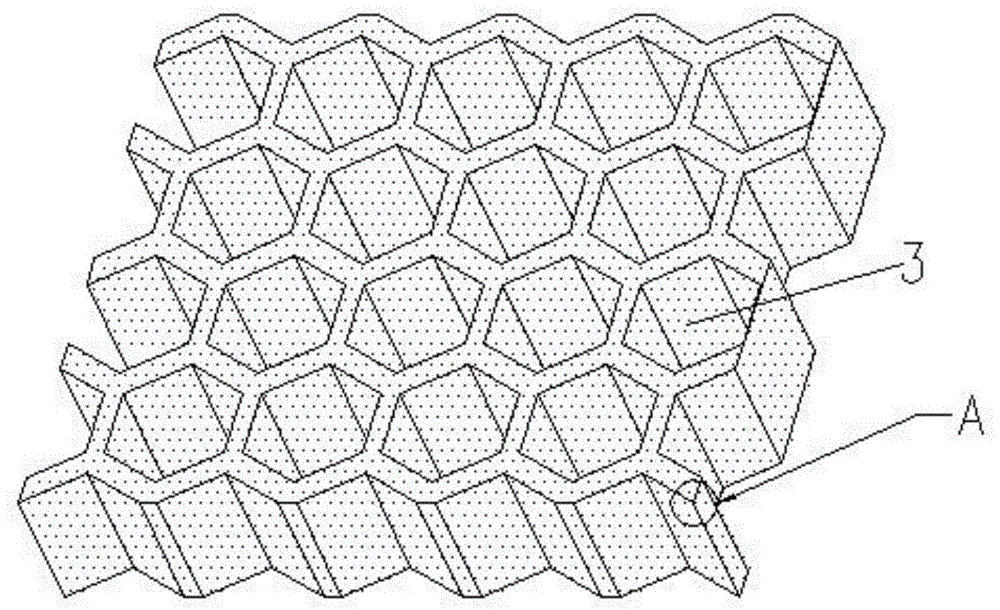
本发明涉及复合材料领域,尤其涉及一种金属陶瓷复合部件及其制备方法。
背景技术:
金属陶瓷复合部件是由金属陶瓷预制体浇注金属熔液制成,金属陶瓷复合部件是将陶瓷的高硬度和高耐磨性与金属的高韧性相结合制备的一类复合材料,在水泥、煤电和矿石等耐磨领域上具有很大的应用前景。
由于陶瓷与金属的物理性能与化学性能差异较大,二者之间很难发生化学反应,从而使得二者之间难以形成有效的连接,传统工艺制备金属陶瓷预制体是通过粉末冶金工艺将陶瓷微粒表面合金化,一般是在陶瓷微粒表面镀镍形成陶瓷与金属的粘接介质,然后再将陶瓷微粒和金属合金粉混合,置于砂型模具中烧结后制得,但是镀镍工艺步骤繁琐,需要进行较多预处理过程,现有技术使用3d打印的方式制备金属陶瓷复合部件,在一定程度上解决了金属与陶瓷二者之间有效连接的问题,但是3d打印料浆的固含量一般不能够大于60%,否则料浆的粘性以及3d打印机的出料流畅度均会受到较大的影响,为了增加陶瓷颗粒与金属粉的粘接性,传统3d打印工艺通常是向打印料浆中加入较多的粘结剂,而这种方法会导致打印料浆中金属粉和陶瓷粉的固含量较低,通过3d打印后的金属陶瓷复合部件中金属粉和陶瓷粉的分布较为分散,烧结排胶后会出现大量孔隙,进而影响金属陶瓷复合部件的耐磨性。
因此如何采用一种简便的方式使金属与陶瓷二者之间形成有效的连接成为了制备金属陶瓷复合材料的关键。
技术实现要素:
为了解决上述技术问题,本发明的目的在于提供一种金属陶瓷复合部件及其制备方法。
根据本发明的一个方面,提供一种金属陶瓷复合部件的制备方法,包括以下步骤:
交替铺设复合层和粘接剂层,制得金属陶瓷素坯并预留渗透孔,所述复合层包括陶瓷微粒、金属合金粉和金属活化剂;
对所述金属陶瓷素坯进行烧结,制得金属陶瓷预制体;
向渗透孔注入金属熔液,待金属熔液凝固以后即得金属陶瓷复合部件。
与现有技术相比,本发明具有以下有益效果:
所述金属陶瓷素坯的复合层均由固体材料组成,相比于用料浆作为制备原料的3d打印制备方法,本发明中采用固体材料为制备原料,陶瓷微粒与金属合金粉的含量较多,在烧结之后的复合层孔隙率较料浆法制备复合材料的孔隙率低,同时相比于用料浆制备的金属陶瓷预制体,本发明中单层复合层的耐磨性更高;高温下粘接剂层逐渐分解消失,在烧结过程中,所述金属活化剂与陶瓷微粒表面发生化学反应,二者形成化学键,同时金属活化剂还会与周围的金属合金粉冶金结合形成金属键,与传统技术相比,本发明中金属活化剂起到了连接桥的作用,代替粘接剂将金属和陶瓷两种物质连接为一个整体,提高了金属陶瓷预制体的耐磨性;金属合金粉在烧结过程中少部分会熔化,熔化后的金属合金液自动填充粘接剂消失导致的空隙,同时,部分金属合金粉的熔化并不会使所述金属陶瓷预制体的固相特征发生改变,从而使金属陶瓷预制体的孔隙率始终保持较低水平,在金属熔液在浇注过程中与金属活化剂冶金结合生成金属键,相比于传统粉末冶金技术制备金属陶瓷复合材料,本发明的金属熔液与金属陶瓷预制体的结合强度更大。
进一步的,所述陶瓷微粒为氧化铝陶瓷微粒,所述氧化铝陶瓷微粒大小为8-15目,所述氧化铝陶瓷微粒占25-45wt%,所述氧化铝陶瓷微粒的致密度大于99%;
其中,所述金属合金粉占55-75wt%,所述金属合金粉为高锰钢、高铬铸铁或镍硬铸铁粉体,所述金属合金粉的纯度大于99%,所述金属合金粉的粒径大小为0.25-0.4mm。
采用上述进一步方案的有益效果在于:将成品的陶瓷微粒作为复合层的成分之一,磨损时优先选择粒径较大的陶瓷作为磨损对象,增加了金属陶瓷复合部件的耐磨性。所述金属合金粉可以与金属熔液发生化学反应,形成强度较高的化学键,使金属熔液可以粘附在金属陶瓷素坯上。
进一步的,所述金属陶瓷素坯由3d打印机打印而成。
采用上述进一步方案的有益效果在于:设置多个呈网格分布的渗透孔,增加了所述金属陶瓷预制体与金属熔液的接触面积,加强了金属熔液对金属陶瓷预制体的浸渗率,采用3d打印工艺可以更快速、容易地实现本技术方案,使所述金属陶瓷复合部件的制造更加快捷。
进一步的,所述复合层还混合有pva粉和硬脂酸钙;
其中,所述pva粉为化学纯级,所述pva粉占所述金属合金粉的1-5wt%,所述硬脂酸钙占金属合金粉的1-4wt%,所述硬脂酸钙的粒径为75-150μm,所述硬脂酸钙的纯度大于99.8%。
采用上述进一步方案的有益效果在于:所述pva粉可以溶于有机溶剂,增加粘接剂的粘性,所述硬脂酸钙用于提高所述复合层的润滑度,增加铺粉的流畅度。
进一步的,所述复合层还混合有金属活化剂,所述金属活化剂为钛粉,所述钛粉的化学纯度大于99%,所述钛粉的粒径在0.01-0.02mm之间,所述钛粉占所述金属合金粉5-15wt%;
其中,所述金属活化剂中掺杂有石墨粉,所述石墨粉的粒径为50-150μm,所述石墨粉占所述金属合金粉的1-6wt%,所述石墨粉的纯度为工业级纯度。
采用上述进一步方案的有益效果在于:钛粉作为金属活化剂,在高温条件下与所述陶瓷微粒表面发生化学反应,形成金属钛的氧化物,同时所述钛粉与金属合金粉冶金结合形成金属键,所述钛粉作为连接桥,增大了陶瓷微粒与金属合金粉的结合强度,提高了所述金属陶瓷预制体的耐磨性,在浇注金属熔液过程中,所述钛粉与金属熔液冶金结合,形成金属键,增加了二者结合的强度,所述石墨的延展性可以降低金属在烧结后降温冷却过程中产生的压应力,提高所述金属陶瓷复合部件整体稳定性。
进一步的,所述粘接剂是乙醇、蒸馏水和聚乙烯吡络烷酮配制而成;
其中,乙醇、蒸馏水、聚乙烯吡络烷酮的用量比为:1:9:0.01。
采用上述进一步方案的有益效果在于:蒸馏水占粘接剂的较大比重,蒸馏水本身易于挥发,不会占用金属陶瓷素坯内部空间,在烧结过程中,不会因为蒸馏水的蒸发,使金属陶瓷素坯层与层之间产生较大空隙,采用乙醇和聚乙烯吡络烷酮作为配置粘接剂的成分,提高了粘接剂的粘稠度,同时有机物在高温下会分解,有利于提高金属陶瓷素坯的强度。
进一步的,所述烧结包括两个阶段,所述第一阶段的烧结温度为400-600度,烧结的时间为2-3小时,第二阶段的烧结温度为1250-1350度,烧结的时间为1-2小时;
其中,在所述烧结过程中持续对所述金属陶瓷素坯加压,施加压力为2-5mpa。
采用上述进一步方案的有益效果在于:所述第一阶段主要是脱脂,利用持续低温使所述金属陶瓷素坯中的有机物分解,所述第二阶段为高温烧结阶段,使内部金属与陶瓷微粒发生化学反应或者冶金结合,提高所述金属陶瓷预制体的强度,在烧结过程中施加压力可以使所述金属陶瓷预制体结构更加紧密,提高其致密性,降低其孔隙率,增加所述金属陶瓷预制体的耐磨性。
根据本发明的另一个方面,提供一种金属陶瓷复合部件,包括:
若干复合层,相邻所述复合层通过金属合金和金属活化剂连接,所述复合层包括陶瓷微粒、金属合金和金属钛,所述复合层上设有渗透孔;
金属连接件,所述金属连接件填充所述渗透孔,所述金属连接件与所述金属合金连接。
与传统技术相比,本发明具有以下有益效果:
本发明由若干复合层相互叠加而成,陶瓷微粒之间的空隙充满了金属合金粉和金属活化剂,烧结后金属合金粉和所述金属活化剂可以部分填充由所述粘接剂层消失而产生的空隙,所述金属活化剂与所述金属合金粉通过金属键连接,所述金属活化剂与所述陶瓷微粒通过化学键连接,其单层复合层的孔隙率要远远低于用料浆制得的同种耐磨材料,同时相邻复合层之间的孔隙率要远远低于传统技术制得的金属陶瓷复合材料,孔隙率越低,其致密性越好,耐磨性就越高,本发明中设有金属连接件,所述金属连接件与所述复合层上的金属合金为金属键连接,所述金属连接件使得本发明更加具有韧性,与传统同种耐磨材料相比,本发明的耐磨性超过普通的金属陶瓷复合材料,韧性更高,本发明由若干复合层相互叠加而成,一层复合层被磨损消耗后,下一层继续承担摩擦任务,与同种耐磨材料相比,本发明比同种耐磨材料的使用寿命要长。
进一步的,所述金属陶瓷复合部件的孔隙率不高于10%。
采用上述进一步方案的有益效果在于:本发明的孔隙率较低,所述复合层的耐磨性越好,使本发明的耐磨性相比于传统同种耐磨材料更高。
进一步的,所述金属陶瓷复合部件应用于水泥立磨。
采用上述进一步方案的有益效果在于:所述金属陶瓷复合部件具有高耐磨,高韧性的特点,可以应用于水泥立磨等耐磨设备。
附图说明
图1为金属陶瓷预制体结构图。
图2为图1中a的局部放大图。
图3为金属陶瓷复合部件实物图。
附图中所示标记:1、金属陶瓷预制体;2、金属连接件;3、渗透孔;4、陶瓷微粒。
具体实施方式
为了更好的了解本发明的技术方案,下面结合具体实施例、说明书附图对本发明作进一步说明。
实施例1:
本实施例提供一种金属陶瓷复合部件的制备方法,具体步骤为:
将25重量份的氧化铝陶瓷微粒4与75重量份的高锰钢粉体混合均匀,然后向其中加入1重量份的pva粉、3重量份的硬脂酸钙粉、5重量份的钛粉和1重量份的石墨粉充分混合均匀,制得复合层的打印原料。
将1重量份的聚乙烯吡络烷酮和100重量份的乙醇在常温下加入到900重量份的蒸馏水中溶解并充分搅拌均匀,用于制备粘接剂层。
使用电脑软件设计多孔网格金属陶瓷预制体1模型,将模型输入到3dp打印机中,使用3d打印机根据模型交替铺设所述复合层和粘接剂层得到金属陶瓷素坯。
将压实后的金属陶瓷素坯取出放入多功能烧结炉中缓慢升温,通入氩气保持压力2mpa,在400℃下保温2h后完成脱脂,快速升温到烧结温度1250℃保温1h完成烧结得到高致密多孔网格金属陶瓷预制体1。
将金属熔液浇注多孔网格金属陶瓷预制体1,所述金属熔液流入渗透孔3并将金属陶瓷预制体1覆盖,待熔液凝固以后即得金属陶瓷复合部件,可用于耐磨领域作为关键工作部件。
实施例2:
本实施例与实施例1相同的特征不再赘述,不同之处在于:
将45重量份的氧化铝陶瓷微粒4与55重量份的高铬铸铁粉体混合均匀,然后向其中加入1重量份的pva粉、3重量份的硬脂酸钙粉、5重量份的钛粉和1重量份的石墨粉充分混合均匀,制得复合层的打印原料。
将1重量份的聚乙烯吡络烷酮和100重量份的乙醇在常温下加入到900重量份的蒸馏水中溶解并充分搅拌均匀,用于制备粘接剂层。
使用电脑软件设计多孔网格金属陶瓷预制体1模型,将模型输入到3dp打印机中,使用3d打印机根据模型交替铺设所述复合层和粘接剂层得到金属陶瓷素坯。
将压实后的金属陶瓷素坯取出放入多功能烧结炉中缓慢升温,通入氩气保持压力5mpa,在500℃保温3h后完成脱脂,快速升温到烧结温度1350℃保温2h完成烧结得到高致密多孔网格金属陶瓷预制体1。
将金属熔液浇注多孔网格金属陶瓷预制体1,所述金属熔液穿过渗透孔3将金属陶瓷预制体1覆盖,待熔液凝固以后即得金属陶瓷复合部件,可用于耐磨领域作为关键工作部件。
实施例3:
本实施例与实施例1相同的特征不再赘述,不同之处在于:
将35重量份的氧化铝陶瓷微粒4与65重量份的高铬铸铁粉体混合均匀,然后向其中加入1重量份的pva粉、3重量份的硬脂酸钙粉、5重量份的钛粉和1重量份的石墨粉充分混合均匀,制得复合层的打印原料。
将1重量份的聚乙烯吡络烷酮和100重量份的乙醇在常温下加入到900重量份的蒸馏水中溶解并充分搅拌均匀,用于制备粘接剂层。
使用电脑软件设计多孔网格金属陶瓷预制体1模型,将模型输入到3dp打印机中,使用3d打印机根据模型交替铺设所述复合层和粘接剂层得到金属陶瓷素坯。
将压实后的金属陶瓷素坯取出放入多功能烧结炉中缓慢升温,通入氩气保持压力4mpa,在600℃保温2.5h后完成脱脂,快速升温到烧结温度1300℃保温1.5h完成烧结得到高致密多孔网格金属陶瓷预制体1。
将金属熔液浇注多孔网格金属陶瓷预制体1,所述金属熔液穿过渗透孔3将金属陶瓷预制体1覆盖,待熔液凝固以后即得金属陶瓷复合部件,可用于耐磨领域作为关键工作部件。
实施例4:
本实施例与实施例1相同的特征不再赘述,不同之处在于:
将陶瓷颗粒和高锰钢粉体混合均匀后,然后向其中加入5重量份的pva粉、5重量份的硬脂酸钙粉、4重量份的钛粉和2重量份的石墨粉充分混合均匀,制得复合层的打印原料。
将1重量份的聚乙烯吡络烷酮和100重量份的乙醇在常温下加入到900重量份的蒸馏水中溶解并充分搅拌均匀,用于制备粘接剂层。
使用电脑软件设计多孔网格金属陶瓷预制体1模型,将模型输入到3dp打印机中,使用3d打印机根据模型交替铺设所述复合层和粘接剂层得到金属陶瓷素坯。
将压实后的金属陶瓷素坯取出放入多功能烧结炉中缓慢升温,通入氩气保持压力3mpa,在500℃保温3h后完成脱脂,快速升温到烧结温度1300℃保温2h完成烧结得到高致密多孔网格金属陶瓷预制体1。
将金属熔液浇注多孔网格金属陶瓷预制体1,所述金属熔液穿过渗透孔3将金属陶瓷预制体1覆盖,待熔液凝固以后即得金属陶瓷复合部件,可用于耐磨领域作为关键工作部件。
上述实施例中,金属陶瓷素坯的打印过程一般需要3-5h,整个制备周期为25h左右。
实施例5:
本实施例提供一种金属陶瓷复合部件,包括:若干复合层,相邻所述复合层3通过金属合金和金属活化剂连接,所述复合层包括陶瓷微粒4、金属合金和金属钛,所述复合层上设有渗透孔3,金属连接件2,所述金属连接件2填充所述渗透孔3,所述金属连接件2与所述金属合金连接,优选的,所述金属活化剂为金属钛,优选的,所述陶瓷微粒4为成品陶瓷颗粒,优选的,相邻所述复合层之间的所述金属合金与金属活化剂的混合物为一个整体,优选的,所述陶瓷微粒4与所述金属活化剂通过化学键连接为一个整体,优选的,所述金属合金与金属活化剂通过金属键连接为一个整体,优选的,所述金属连接件2与所述复合层上的所述混合物通过金属键连接,相邻所述复合层之间的所述混合物与所述复合层内的金属合金和金属活化剂为一个整体,所述陶瓷微粒4与所述金属活化剂连接,使得所述陶瓷微粒4、金属活化剂、金属合金和金属连接件2为一个整体,从而使得本发明既具备陶瓷的耐磨性,又具备了金属的韧性,使得本发明更好的应用于水泥立磨等大型耐磨设备。
以上描述仅为本申请的较佳实施例以及对所运用技术原理的说明。本领域技术人员应当理解,本申请中所涉及的发明范围,并不限于上述技术特征的特定组合而成的技术方案,同时也应涵盖在不脱离所述发明构思的情况下,由上述技术特征或其等同特征进行任意组合而形成的其它技术方案。例如上述特征与本申请中公开的(但不限于)具有类似功能。
起点商标作为专业知识产权交易平台,可以帮助大家解决很多问题,如果大家想要了解更多知产交易信息请点击 【在线咨询】或添加微信 【19522093243】与客服一对一沟通,为大家解决相关问题。
此文章来源于网络,如有侵权,请联系删除


