面向激光增材制造的柔性夹持装置和动态夹持方法与流程



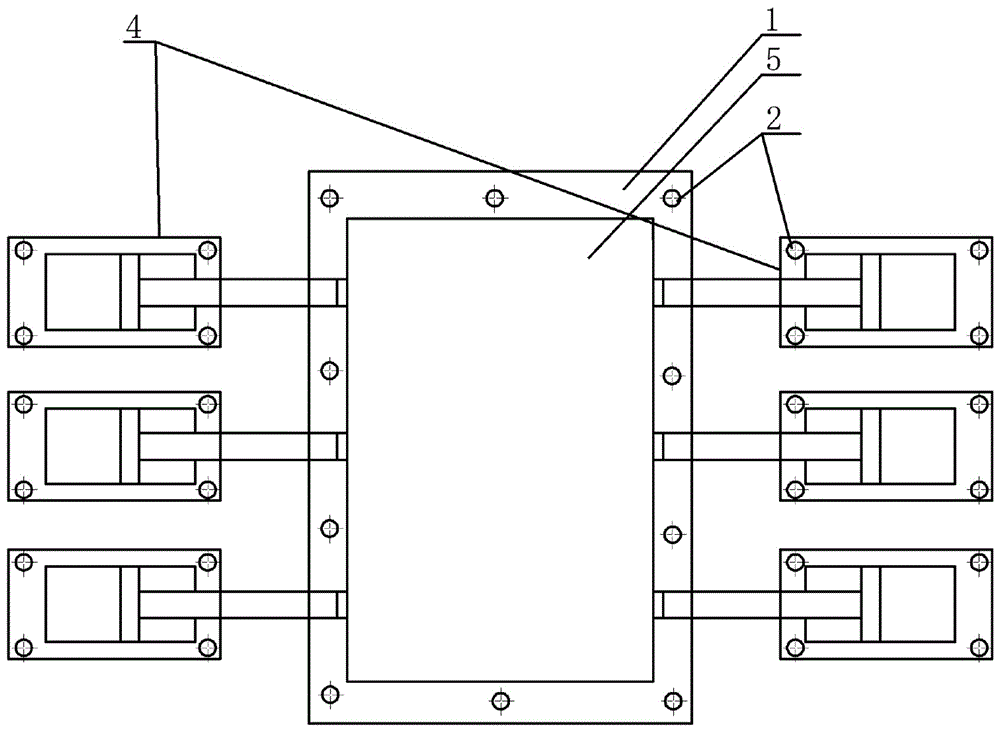
本发明涉及金属激光增材制造领域,具体涉及一种面向同步送粉式激光增材制造的柔性夹持装置和动态夹持方法。
背景技术:
激光增材制造技术是一种基于离散/堆积成形思想的制造技术,利用激光对同轴输送的金属粉末材料按照规划的扫描路径实现逐层熔化堆积,直接沉积制造金属功能零件的技术。无需任何模具,成形制造速度快,降低制造成本;由于高能激光束产生的快速熔化和凝固过程,激光沉积件组织致密、细小且均匀,可消除成分偏析的影响,提高力学性能和耐蚀性能。该技术广泛应用于航空航天、海工等装备领域中的大型复杂构件制造运维,提升飞机、发动机、船舶等装备关键件快速制造运维技术的能力水平、缩短重大装备研制运维周期提供技术支撑,促进航空航天、海工装备、轨道交通等产业的绿色高质量发展。
根据激光增材层层叠加的制造原理,工件尺寸不断地增大的同时,质量也在逐渐增大;尤其是倒梯形或者t字形工件,随着沉积高度的逐渐增大,其重心在逐渐的升高;另外随着热量的不断累积,沉积件的内应力也在逐渐变大。因此,对于质量逐渐变大的成形制件来说,过大的内应力会使工件发生变形,仅仅依靠沉积体与基材在初始结合处的连接来固定成形工件,不足以维持保证工件足够的刚度和稳定性,进而工件发生翘曲变形,甚至会与基板发生开裂脱离,严重影响了增材制造的精度和质量,甚至导致制件报废。
当前通常采用中断成形制造、二次装夹固定工件来保证工件的刚度和稳定性。此种方式中断成形制造,严重影响制造效率,二次充排气净化氛围,也增加制造成本;另外二次装夹容易造成定位误差,引起新的变形超差;接续增材制造容易产生熔合不良等缺陷。
因此,在激光增材制造过程大型复杂结构时,如何设计合理的柔性夹持装置,并根据增材制造工件尺寸变化,对工件进行实时动态夹紧固定,是增材制造顺利完成的保障和关键。
技术实现要素:
本发明提供一种面向同步送粉式激光增材制造的柔性夹持装置和动态夹持方法,其目的在于解决中断成形制造效率低、二次装夹的误差,以及避免接续增材制造的熔合不良等问题。
技术方案:
一种面向激光增材制造的柔性夹持装置,该装置的工作台上设置有多个柔性夹持装置,柔性夹持装置由高度调整机构和气动夹紧机构组成,高度调整机构一端固定在工作台上,高度调整机构的另一端与气动夹紧机构连接,工作台上放置工件;
高度调整机构的连接板固定在工作台上,连接板内设置有驱动装置,驱动装置与支撑板连接,支撑板上固定设置有气动夹紧机构;
气动夹紧机构的气缸固定设置在支撑板上,气缸的活塞杆上设置的柔性驱动组件连接有夹持头;
多个柔性夹持装置对称设置在工件的四周。
柔性驱动组件包括蜗杆、蜗轮和第二伺服电机,蜗轮固定在夹持头上,蜗轮与蜗杆相啮合,蜗杆与第二伺服电机连接,第二伺服电机固定在活塞杆上。
支撑板与连接板上固定设置的轨道立杆滑动连接。
柔性夹持装置还包括金属防尘罩,金属防尘罩固定设置在支撑板上,金属防尘罩伸出活塞杆的开口处设置有激光测距传感器,两激光测距传感器之间的距离大于夹持头的长与工件接触的面设置有多排凹槽。
一种面向激光增材制造的柔性夹持装置的动态夹持方法:
1)根据需要增材制造工件的结构和尺寸设置夹持装置的位置和数量;
2)开启激光增材制造工件,将工件置于工作台的基板上,激光增材制造控制系统通过控制高度动态调整机构,调整夹持头的高度;通过控制气动夹紧机构调整夹持头夹紧力的大小;通过控制气动夹紧机构调整夹持头的角度;
3)随着工件的增高,高度调整机构带动气动夹紧机构随工件也增高,并且根据激光测距传感器的测距来调整活塞杆的位移;根据两激光测距传感器获得的角度调整气动夹紧机构调整夹持头的角度;
4)直至制备完成,设备复位。
步骤2)中角度计算公式为:
其中α为工件侧面倾角,a1为上端传感器所测量距离,a2为下端传感器所测量距离,b为两传感器间距。
夹持头10的高度位于工件5沉积高度值以下10-30mm处。
本发明具有以下优点:
1、夹持装置模块化:夹持装置的高度调整和气动夹紧机构设计制造实现模块化,可根据增材制造工件结构和尺寸来设置夹持装置具体尺寸、安装位置和数量。
2、夹持装置柔性化:通过高度调整机构及气动夹紧机构,可根据增材制造过程中渐长式工件结构尺寸来适时控制改变夹持位置和夹持力,实现夹持动态柔性化;夹持头与活塞杆采用铰链式连接,可根据工件表面形状来自适应调整夹持头夹持角度,从而实现夹紧对表面有倾角的复杂结构的柔性有效夹紧。
3、夹持装置自动化:高度调整机构及气动夹紧机构的控制单元接入激光增材制造控制系统,实现对渐长式工件的自动化夹紧。
4、增材制造工件动态夹紧:采用柔性夹持装置对增材制造的大型复杂结构工件实现动态夹紧固定工件,防止工件在增材制造过程中发生变形,保证制件精度;可实现一次成形制造,避免重复装夹而中断成形制造及带来的二次装夹误差,提高加工效率,降低加工成本;避免中断成形后接续增材制造的熔合不良等缺陷,保证激光增材制造质量。
附图说明:
以下结合附图对本发明做进一步的描述:
图1是柔性夹持装置布置方案示意图;
图2是柔性夹紧装置构成示意图;
图3是气动夹紧机构示意图;
图4是高度调整机构示意图;
图5是柔性夹紧装置与激光增材制造控制系统连接示意图;
图6夹持头角度自动调整示意图;
附图标记:1基板,2螺栓,3工作台,4柔性夹持装置,5工件,6连接板,7第一伺服电机,8丝杠,8-1螺母,9活塞杆,10夹持头,11气缸,12凹槽,13铰链,14激光增材制造控制系统,15气缸电磁阀,16金属防尘罩,17支撑板,18轨道立杆,19蜗杆,20蜗轮,21第二伺服电机连接法兰,22第二伺服电机,23激光测距传感器。
具体实施方式:
本发明目的在于提供一种面向同步送粉式激光增材制造的柔性夹持装置和动态夹持方法,采用多点可调、柔性夹紧的方式,通过设计制造高度调整机构、气动夹紧机构及结构适应性夹持头,对大型复杂结构层层叠加长大的工件进行实时动态夹紧,来固定工件,保证尺寸精度稳定,防止工件在增材制造过程中发生变形,保证制件精度;避免中断成形制造和二次装夹误差,提高加工效率,降低加工成本;避免接续增材制造的熔合不良等缺陷,保证激光增材制造质量。
如图1-2所示,一种面向激光增材制造的柔性夹持装置,该装置的工作台3上放置有工件5,工件5下方设置有基板1,基板1通过螺栓固定在工作台3上,具体为工作台3上的基板1上放置工件5,即增材制造工件5在基板1上叠加制造,工件5四周(即基板1四周)对称设置有多个柔性夹持装置4,柔性夹持装置4由高度调整机构和气动夹紧机构组成,高度调整机构一端固定在工作台3上,高度调整机构的另一端与气动夹紧机构连接,气动夹紧机构与工件5接触。如图4所示,高度调整机构的连接板6固定在工作台3上,连接板6内设置有第一伺服电机7,第一伺服电机7与丝杠8连接,丝杠8上的螺母8-1与支撑板17固定连接,支撑板17与连接板6上固定设置的轨道立杆18滑动连接,轨道立杆18用于限制支撑板17沿着轨道立杆18上下移动。支撑板17上固定设置有气动夹紧机构;高度调整机构用于调整气动夹紧机构的高度,满足不同高度夹紧需求。
气动夹紧机构的气缸11固定设置在支撑板17上,气缸11的活塞杆9端部铰链连接有夹持头10,活塞杆9上设置有柔性驱动组件,柔性驱动组件的一端固定于活塞杆9上,柔性驱动组件的另一端与夹持头10连接,夹持头10与工件5接触。使夹持头10接触夹紧工件5,通过调节气缸11内的气体压力可以改变夹持头10的距离,从而通过相对的两个夹持头10之间的距离,调整对工件5夹紧力的大小。
驱动装置中的第一伺服电机7、气缸11的气缸电磁阀15和柔性驱动组件的第二伺服电机22均与激光增材制造控制系统14连接。
通过高度调整机构及气动夹紧机构,可根据增材制造过程中渐长式工件结构尺寸来适时控制改变夹持位置和夹持力,实现夹持动态柔性化;夹持头10与活塞杆9采用铰链式连接,可根据工件表面形状来自适应调整夹持头夹持角度,从而实现夹紧对表面有倾角的复杂结构的柔性有效夹紧。
第一伺服电机7、气缸11的气缸电磁阀15和第二伺服电机22均与激光增材制造控制系统14连接。即夹持装置的高度调整和气动夹紧机构设计制造实现模块化,高度调整机构及气动夹紧机构的控制单元接入激光增材制造控制系统14,实现对渐长式工件的自动化夹紧。可根据增材制造工件结构和尺寸来设置夹持装置具体尺寸、安装位置和数量。
如图3和6所示,柔性驱动组件包括蜗杆19、蜗轮20和第二伺服电机22,蜗轮20固定在夹持头10上,具体为,夹持头10的一侧通过蜗轮20与蜗杆19连接,夹持头10的另一侧通过轴承与蜗杆19连接,蜗轮20与蜗杆19相啮合,蜗杆19通过伺服电机连接法兰21与第二伺服电机22连接,伺服电机连接法兰21与第二伺服电机22固定在活塞杆9上。
柔性夹持装置4还包括金属防尘罩16,金属防尘罩16固定设置在支撑板17上,金属防尘罩16用于保护高度调整机构和气动夹紧机构,金属防尘罩16伸出活塞杆9的开口的上下两端处设置有激光测距传感器23,两激光测距传感器23之间的距离b大于夹持头10的长l。以避免夹持头10遮挡激光测距传感器23测量距离。
夹持头10角度可根据工件5侧壁角度进行自适应调整,每次调整高度时,上下两激光测距传感器23对工件5的距离进行测量,在系统中设置公式对工件表面倾斜角度进行计算,根据所计算出的倾角α,通过调节第二伺服电机22带动蜗轮20和蜗杆19使夹持头10进行转动。使用蜗轮20和蜗杆19可以提高夹持头10的角度调节精度,并且具有自锁性,防止夹持力过大时导致夹持头10角度发生变化。第二伺服电机22通过第二伺服电机连接法兰21固定在活塞杆上。
随着增材制造渐长式工件5高度和角度的变化,高度调整机构的第一伺服电机7驱动丝杠8转动,由于轨道立杆18的限制,使丝杠8上的螺母8-1带动支撑板17向上或者向下移动,进而带动气动夹紧机构和金属防尘罩16向上或者向下移动,即实现了气动夹紧机构的夹持头10的高度随着工件5高度的变化而变化;金属防尘罩16上的每组激光测距传感器23根据测得至工件5的距离,计算工件5的角度变化,以调整夹持头10的角度随增材制造渐长式工件5形状进行角度的变化,本装置能够适应各种复杂不规则形状零件的柔性夹持。从而对于质量逐渐变大的成形制件来说,本装置能够维持保证工件足够的刚度和稳定性,进而避免工件发生翘曲变形,与基板发生开裂脱离的现象,保证了增材制造的精度和质量。相比于中断成形制造、二次装夹固定工件,有效避免了中断成形制造,提高了制造效率,降低增加制造成本;而且避免了二次装夹容易造成定位误差,引起新的变形超差;接续增材制造容易产生熔合不良等缺陷。
金属防尘罩16防止加工过程飞溅粉末等杂质进入滚珠丝杠8等传动件中,并且保护伺服电机7和气缸11避免高温辐射损坏。
夹持头10与工件5接触的面设置有多排凹槽12。凹槽12的槽为宽1mm、深0.5mm。以增大接触面的摩擦力,使柔性夹持效果更好。
一种面向激光增材制造的柔性夹持装置的动态夹持方法,
1)根据需要增材制造工件的结构和尺寸设置夹持装置的位置和数量;
2)将工件5置于工作台3的基板1上,开启激光增材制造工件5,激光增材制造控制系统14通过控制高度动态调整机构的第一伺服电机7,调整夹持头10至当前工件5沉积高度值以下10-30mm处,优选20mm,当小于10mm时,激光增材制造的热影响大,夹持头10不利于工件5的成形;当大于30mm时,本装置控制工件5变形的支撑力和动态夹持效果差。通过控制气动夹紧机构的气缸电磁阀15调整夹持头10夹紧力的大小;通过控制气动夹紧机构的第二伺服电机22调整夹持头10的角度;以适应工件5的形状,维持工件5足够的刚度和稳定性;夹持头10的表面积,也即夹持头10与工件5的接触面积约为10mm*10mm-30mm*30mm,具体根据工件5尺寸适当选择。
3)随着工件5的增高,高度调整机构带动气动夹紧机构随工件5也增高,并且根据激光测距传感器23的测距来调整活塞杆9的位移;当工件5的角度存在变化时,可以根据两激光测距传感器23获得的角度调整气动夹紧机构调整夹持头10的角度;
高度调整机构通过第一伺服电机7驱动滚珠丝杠8来调节气动夹紧机构的高度,以实现不同高度和渐长式工件5的夹紧;
气动夹紧机构通过气缸电磁阀15,调节气缸11内的气体压力驱动活塞杆9,使夹持头10接触夹紧工件5,以改变夹紧力的大小,保持夹紧力大于150kg,小于300kg,可根据成形壁厚和工件刚度等适当调控夹紧力。
完成对增材制造工件夹持位置、夹持力的适时动态调控,实现渐长式工件的动态化、柔性化、自动化夹持。
4)直至工件5制备完成,设备复位。
步骤2)中角度计算公式为:
其中α为工件侧面倾角,a1为上端传感器所测量距离,a2为下端传感器所测量距离,b为两传感器间距。
夹持头10角度可根据工件5侧壁角度进行自适应调整,每次调整高度时,上下两激光测距仪对工件5的距离进行测量,在系统中设置公式对工件表面倾斜角度进行计算,根据所计算出的倾角α,通过调节第二伺服电机22带动蜗轮20和蜗杆19使夹持头10进行转动。使用蜗轮20和蜗杆19可以提高角度调节精度,并且具有自锁性,防止夹持力过大时导致夹持头10角度发生变化。
本方法采用柔性夹持装置对增材制造的大型复杂结构工件实现动态夹紧固定工件,防止工件在增材制造过程中发生变形,保证制件精度;可实现一次成形制造,避免重复装夹而中断成形制造及带来的二次装夹误差,提高加工效率,降低加工成本;避免中断成形后接续增材制造的熔合不良等缺陷,保证激光增材制造质量。
本装置和方法能够加工各种形状的渐长式工件,尤其是倒梯形或者t字形工件,能够随着沉积高度的逐渐增大,柔性夹持工件,随着工件重心的改变而改变;随着内应力的变大而调整夹持力的大小。从而能够维持保证工件足够的刚度和稳定性,避免工件发生翘曲变形,与基板发生开裂脱离,影响增材制造的精度和质量,甚至导致制件报废等问题。
起点商标作为专业知识产权交易平台,可以帮助大家解决很多问题,如果大家想要了解更多知产交易信息请点击 【在线咨询】或添加微信 【19522093243】与客服一对一沟通,为大家解决相关问题。
此文章来源于网络,如有侵权,请联系删除


