利用废锂离子电池黑粉与硫化镍钴矿协同制备三元前驱体和碳酸锂的方法及应用与流程



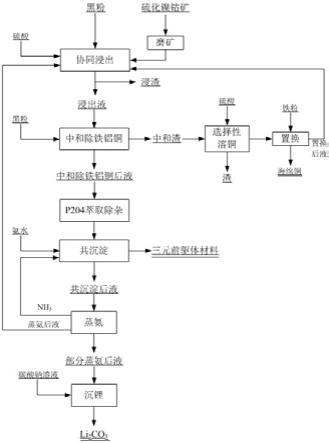
[0001]
本发明涉及冶金技术领域,尤其是涉及一种利用废锂离子电池黑粉与硫化镍钴矿协同制备三元前驱体和碳酸锂的方法及应用。
背景技术:
[0002]
废旧动力电池的再生循环利用主要针对电池容量损耗严重,使得电池无法继续使用而进行的资源化处理。废旧锂离子电池的回收主要分为三大类:火法冶金回收、湿法冶金回收以及生物冶金回收。其中,生物冶金回收处于研发阶段;火法冶金的回收因其消耗大量的能源、对设备耐温要求高以及会产生大量有毒气体,所以正在被逐渐取代;湿法冶金因其温和的条件以及较高的金属浸出率等诸多优点而被广泛采用。
[0003]
湿法冶金回收是采用合适的化学试剂选择性溶解废旧锂离子电池中的电极材料,从而将目标金属元素从浸出液中分离出来的一种方法,具体步骤包括预处理得到活性正极材料,接着采用无机酸(h
2
so
4
、hno
3
、hcl或h
3
po
4
)或有机酸(如柠檬酸、苹果酸、葡萄糖酸或抗坏血酸等)进行有价金属的浸出,有时为了提高有价金属的浸出率,还会引入还原剂(h
2
o
2
、na
2
s
2
o
3
或na
2
so
3
)或增加超声波-微波等的辅助性条件;浸出液经过除铁铝-p204除杂-p507镍钴分离-p204镍锂分离会得到镍钴锰锂的硫酸盐溶液,然后送至前驱体制备车间,金属锂离子则采用蒸发浓缩的方式进行富集,再用饱和碳酸钠溶液沉锂,固液分离得到碳酸锂产品;前驱体的制备:冶炼工序得到的镍、钴、锰/铝溶液进行组分调配,在气氛保护下,加入络合剂和沉淀剂进行前驱体制备,根据溶液中镍、钴、锰/铝的不同比例含量,可得到622、523、811和nca等不同的三元前驱体。
[0004]
传统硫化镍钴矿的处理工艺是浮选得到硫化镍钴精矿后进行火法熔炼,再配合加压浸出等工艺回收镍钴,存在工艺复杂、处理成本高、环境污染重以及金属回收率低等的缺点。锂离子电池的原料镍钴锰锂对废旧电池有价组元的回收、对传统硫化镍钴矿产的高效利用以及对保障锂离子电池材料的循环利用十分重要。因此,如何在温和条件下,加快化学反应过程并且提高目标金属离子的回收率,同时选择性分离有害杂质、采用短程制备材料就具有重要的工业意义。
[0005]
有鉴于此,特提出本发明。
技术实现要素:
[0006]
本发明的目的之一在于提供一种利用废锂离子电池黑粉与硫化镍钴矿协同制备三元前驱体和碳酸锂的方法,通过协同浸出、新型中和剂、p204选择性除杂、镍钴锰锂四元溶液直接沉淀制备前驱体、蒸氨及溶液的循环利用等核心发明点,实现废锂离子电池黑粉和硫化镍钴矿的协同处置,短程制备获得三元前驱体和碳酸锂高值产品。
[0007]
本发明的目的之二在于本方法在制备电池正极中的应用。
[0008]
为了实现本发明的上述目的,特采用以下技术方案:
第一方面,本发明提供了一种利用废锂离子电池黑粉与硫化镍钴矿协同制备三元前驱体和碳酸锂的方法,包括以下步骤:(a)协同浸出:电池黑粉和硫化镍钴矿混合获得矿浆,向所述矿浆中加入助浸剂和浸出剂,并通入含氧气体实现浸出,固液分离后得到浸出渣和浸出液;(b)中和除铁铝铜:中和剂加入到所述浸出液中进行中和,固液分离后得到中和渣和除铁铝铜后液;(c)除杂:对所述除铁铝铜后液进行除杂,制得除杂后液;(d)共沉淀:惰性气体氛围下,向所述除杂后液中加入络合剂和沉淀剂进行共沉淀,固液分离后得到三元前驱体和共沉淀后液;(e)蒸氨:利用蒸汽对所述共沉淀后液进行加热蒸氨,得到蒸氨后液以及氨气;(f)沉锂:向所述蒸氨后液中加入碳酸盐溶液进行沉锂,得到碳酸锂;其中,步骤(a)中所述废锂离子电池为废旧的镍钴锰酸锂电池。
[0009]
优选地,所述矿浆的质量分数为15%~33%;进一步的,所述废锂离子电池黑粉和硫化镍钴矿混合的质量比为1:10~10:1;进一步的,所述硫化镍钴矿的矿粉粒度为-0.074mm占80%以上;优选地,所述助浸剂包含铁离子、铜离子、银离子、锰离子中的一种或多种;进一步优选地,所述助浸剂的浓度为2~10g/l;优选地,所述浸出剂调节矿浆的ph值不大于2.0;优选地,浸出的反应温度为50~95℃,浸出的反应时间为1~10h。
[0010]
优选地,所述中和剂为镍钴锰酸锂电池黑粉、氢氧化镍、氢氧化钴、氢氧化锰、氢氧化锂、碳酸镍、碳酸钴、碳酸锰、碳酸锂、碱式碳酸镍、碱式碳酸钴、碱式碳酸锰、碱式碳酸锂、氧化钴、氧化镍、氧化锰、氧化锂中的一种或者多种;进一步的,所述中和除铁铝铜的ph值为5.4~6.2;进一步的,所述中和除铁铝铜的反应温度25~95℃,反应时间1~10h。
[0011]
优选地,所述方法还包括如下步骤:强酸加入到所述中和渣中,调节ph值为4.8~5.4,在25~95℃下反应1~10h,制得铜离子溶液和铁铝渣;其中,还包括如下步骤:利用铁粉置换所述铜离子溶液制得海绵铜,置换后液作为助浸剂返回步骤(a);优选地,所述铁粉的摩尔用量为置换铜离子所需的理论摩尔量的1.05~1.2倍;优选地,所述置换的反应时间为0.5~3h,置换的反应温度为50~95℃。
[0012]
优选地,步骤(c)中,所述除杂为萃取;其中,所述萃取的有机相采用镍皂、钴皂或锰皂中的一种;进一步地,所述萃取的萃取剂的组成为体积分数10~30%的p204和70~90%的磺化煤油;进一步的,所述萃取的皂化液为10~30g/l me
2+
的硫酸盐溶液,其中,me为镍、钴或锰中的一种。
[0013]
优选地,步骤(d)中,所述络合剂包括氨水,所述沉淀剂包括氢氧化钠溶液;进一步的,所述氨水的浓度为0.1~6.0mol/l;进一步的,所述氢氧化钠溶液浓度为6~8mol/l。
[0014]
优选地,所述共沉淀的ph值保持在10~12;
进一步的,所述共沉淀的反应温度30~70℃,共沉淀的反应时间10~30h。
[0015]
步骤(e)中,所述蒸氨的加热温度为90~98℃;优选地,所述方法还包括如下步骤:步骤(e)得到的氨气返回步骤(d),部分蒸氨后液返回步骤(a)。
[0016]
优选地,步骤(f)中,所述碳酸盐的浓度为200~300g/l;进一步的,所述碳酸盐的摩尔用量为沉锂所需理论摩尔量的1.05~1.2倍;进一步的,所述沉锂的温度为60~90℃,沉锂的时间为1~3h。
[0017]
第二方面,由本发明提供的方法制备得到的三元前驱体在电池正极中的应用。
[0018]
与已有技术相比,本发明具有如下有益效果:本发明利用电池黑粉的氧化性和硫化镍钴矿的还原性高效浸出了ni、co和mn等有价金属,ni浸出率96%以上,co浸出率98%以上,mn浸出率98%以上。
[0019]
本发明提供的方案具有工艺流程短、成本低以及环境绿色友好等的优点。
[0020]
另外,本发明提供的方法进一步还具有如下优选的有益效果:第一,本发明采用的新型中和剂除铁铝铜,可以用原料废锂离子电池黑粉作为中和试剂,这样一来就减少了传统中和剂的使用量,从而避免了向镍钴锰混合的溶液体系引入杂质离子,同时也降低了中和除铁铝铜过程中的镍钴损失。
[0021]
第二,本发明根据三元前驱体材料对溶液镍钴锰摩尔比的要求,可以灵活地选择镍皂、钴皂或锰皂,并且通过萃取控制其他杂质的深度脱除,即本发明提供的方法可以实现镍钴锰锂四元溶液直接用于短程制备三元前驱体材料(一次晶粒)。
[0022]
第三,制备三元前驱体和碳酸锂的过程中,本发明采用蒸氨及溶液的循环再利用等工艺可极大地减少化学试剂的消耗和三废的排放。
附图说明
[0023]
为了更清楚地说明本发明具体实施方式或现有技术中的技术方案,下面将对具体实施方式或现有技术描述中所需要使用的附图作简单地介绍,显而易见地,下面描述中的附图是本发明的一些实施方式,对于本领域普通技术人员来讲,在不付出创造性劳动的前提下,还可以根据这些附图获得其他的附图。
[0024]
图1为本发明实施例1提供的工艺流程图。
具体实施方式
[0025]
下面将结合实施例对本发明的技术方案进行清楚、完整地描述,显然,所描述的实施例是本发明一部分实施例,而不是全部的实施例。基于本发明中的实施例,本领域普通技术人员在没有做出创造性劳动前提下所获得的所有其他实施例,都属于本发明保护的范围。
[0026]
根据本发明的第一个方面,一种利用废锂离子电池黑粉与硫化镍钴矿协同制备三元前驱体和碳酸锂的方法,包括以下步骤:(a)协同浸出:提供废锂离子电池黑粉和硫化镍钴矿混合的矿浆,向矿浆中加入助浸剂和浸出剂,并通入含氧气体进行浸出,固液分离后得到浸出渣和浸出液;优选地,步骤(a)中所述废锂离子电池黑粉包括废旧的镍钴锰酸锂电池黑粉。
[0027]
所述的硫化镍钴矿为破碎细磨后的矿粉。
[0028]
优选地,步骤(a)中所述硫化镍钴矿的矿粉粒度为-0.074mm占80%以上;其中,所述废锂离子电池黑粉和硫化镍钴矿混合的质量比为1:10~10:1,其典型但非限制性的质量比例如为1:10、3:8、5:6、7:4、9:2、10:1;电池黑粉和硫化镍钴矿发生氧化还原反应,协同浸出镍钴锰,无需加入额外的化学试剂。
[0029]
优选地,所述矿浆的质量分数为15%~33%。
[0030]
矿浆的质量分数是固体重量与固体和液体总重量的比值。
[0031]
矿浆典型但非限制性的质量分数例如为15%、21%、27%、33%。
[0032]
助浸剂辅助浸出,强化浸出优选地,所述助浸剂包含铁离子、铜离子、银离子、锰离子中的一种或多种;进一步的,所述助浸剂的浓度为2~10g/l。
[0033]
在电池黑粉与硫化镍钴矿的协同浸出中,黑粉和硫化镍钴矿都是固体,固-固反应速率较慢。加入助浸剂起到传递电子的作用,加快氧化还原反应的速率。
[0034]
助浸剂典型但非限制性的浓度例如为2 g/l、4 g/l、6 g/l、8 g/l、10 g/l。
[0035]
以fe
2+
为例,利用fe
2+
作为电子的传递载体催化氧化还原反应,加速固-固反应动力学过程,该过程发生如下反应:li
z
ni
1-x-y
co
x
mn
y
o
2
+nis+fe
2+
+o
2
+h
2
so
4
→
li
2
so
4
+niso
4
+coso
4
+mnso
4
+h
2
o+fe
3+
+s(b)中和除铁铝铜:中和剂加入到所述浸出液中进行中和,固液分离后得到中和渣和除铁铝铜后液;步骤(b)中,中和除铁铝铜时,加入的中和剂在溶液体系可分解出oh-或者co
32-,与浸出液中的残酸中和生成水,体系oh-变多,oh-与fe
3+
、al
3+
和cu
2+
浓度之积达到金属离子对应氢氧化物的溶度积后,便会沉淀析出,发生如下反应:fe
3+
+3oh-=fe(oh)
3
↓
al
3+
+3oh-=al(oh)
3
↓
cu
2+
+2oh-=cu(oh)
2
↓
从而实现铁铝铜从浸出液中脱除,所采用的中和剂,不引入其他杂质,有利于下一步的提取分离。
[0036]
优选地,所述中和剂为镍钴锰酸锂电池黑粉、氢氧化镍、氢氧化钴、氢氧化锰、氢氧化锂、碳酸镍、碳酸钴、碳酸锰、碳酸锂、碱式碳酸镍、碱式碳酸钴、碱式碳酸锰、碱式碳酸锂、氧化钴、氧化镍、氧化锰、氧化锂中的一种或者多种;进一步的,所述中和除铁铝铜的ph值为5.4~6.2;进一步的,所述中和除铁铝铜的反应温度25~95℃,反应时间1~10h。
[0037]
中和除铁铝铜时典型但非限制性的ph值例如为5.4、5.6、5.8、6.0、6.2。
[0038]
中和除铁铝铜时搅拌的典型但非限制性的温度例如为25℃、35℃、45℃、55℃、65℃、75℃、85℃、95℃。
[0039]
中和除铁铝铜的典型但非限制性的反应时间例如为1h、2h、3h、4h、5h、6h、7h、8h、
9h、10h。
[0040]
优选地,所述方法还包括选择性溶解铜的步骤:强酸加入到所述中和渣中,调节ph值为4.8~5.4,在25~95℃下反应1~10h,制得铜离子溶液和铁铝渣;选择性溶解铜时,利用氢氧化物溶度积的差异,控制浸出体系的ph值在4.8~5.4。在该ph值范围下,氢氧化铁和氢氧化铝处于完全沉淀ph值范围,氢氧化铜可被浸出。发生如下反应:cu(oh)
2
+h
2
so
4
=cuso
4
+2h
2
o选择性溶解铜时典型但非限制性的ph值例如为4.8、5.0、5.2、5.4。
[0041]
选择性溶解铜时搅拌的典型但非限制性的温度例如为25℃、35℃、45℃、55℃、65℃、75℃、85℃、95℃。
[0042]
选择性溶解铜的典型但非限制性的反应时间例如为1h、2h、3h、4h、5h、6h、7h、8h、9h、10h。
[0043]
优选地,所述方法还包括如下步骤:利用铁粉置换铜离子溶液制得海绵铜,置换后液作为助浸剂返回步骤(a);优选地,所述铁粉的摩尔用量为置换铜离子所需的理论摩尔量的1.05~1.2倍;优选地,所述置换的反应时间为0.5~3h,置换的反应温度为50~95℃。稍微过量的铁粉的和特定温度可将硫酸铜溶液快速且充分置换,反应完全而不引入杂质。
[0044]
铁粉和铜离子的典型但非限制性的摩尔量比值例如为1.05、1.10、1.15、1.20。
[0045]
置换典型但非限制性的反应时间例如为0.5h、1.0h、1.5h、2.0h、2.5h、3.0h。
[0046]
置换典型但非限制性的反应温度例如为50℃、65℃、80℃、95℃。
[0047]
(c)除杂:对所述除铁铝铜后液进行除杂,制得除杂后液;优选地,步骤(c)中,所述除杂为萃取;其中,所述萃取的有机相采用镍皂、钴皂或锰皂中的一种;进一步的,所述萃取的萃取剂的组成为体积分数10~30%的p204和70~90%的磺化煤油;进一步的,所述萃取的皂化液为10~30g/l me
2+
的硫酸盐溶液,其中,me为镍、钴或锰中的一种。
[0048]
皂化液典型但非限制性的浓度例如为10 g/l、20 g/l、30g/l。
[0049]
萃取除杂时发生如下反应:me
n+
+nhx =mex
n
+nh
+
萃取过程中,利用萃取剂与溶液中的金属离子(me
n+
)形成萃合物并进入有机溶剂中(负载有机相)。负载有机相和反萃液混合,金属离子回到反萃液中。利用萃取剂对不同金属离子萃取能力的不同,实现杂质离子的去除和镍钴的分离。
[0050]
其中,除杂的后的负载有机相经反萃、反铁、洗涤和洗氯,可再生利用;反萃液为1.5~2.5 mol/l的hcl,反铁液为4.5~6.0 mol/l的hcl,洗涤液为0.5~1.0 mol/l的h
2
so
4
,洗氯液为3~10 g/l的 h
2
so
4
。
[0051]
(d)共沉淀:惰性气体氛围下,向所述除杂后液中加入络合剂和沉淀剂进行共沉淀,固液分离后得到三元前驱体和共沉淀后液;优选地,步骤(d)共沉淀中,所述惰性气体为氮气、氦气等惰性气体中的一种或多种;
共沉淀时,镍钴锰锂四元溶液体系共沉淀制备前驱体材料(一次晶粒)过程中,氨水作为络合剂,氢氧化钠作为沉淀剂,通过控制反应条件形成类球型氢氧化物,反应如下:(1-x-y)ni
2+
+xco
2+
+ymn
2+
+mnh
3
•
h
2
o=[ni
1-x-y
co
x
mn
y
(nh3)
n2+
]+(m-n)nh
3
•
h
2
o[ni
1-x-y
co
x
mn
y
(nh
3
)
n2+
]+2oh-+zh
2
o=ni
1-x-y
co
x
mn
y
(oh)
2
+znh
4
oh+
(n-z)
nh
3
进一步的,所述氨水的浓度为0.1~6.0mol/l;进一步的,所述氢氧化钠溶液浓度为6~8mol/l。
[0052]
优选地,所述共沉淀的ph值保持在10~12;进一步优选地,所述共沉淀的反应温度30~70℃,反应时间10~30h。
[0053]
氨水典型但非限制性的浓度例如为0.1mol/l、1.0mol/l、2.0mol/l、3.0mol/l、4.0mol/l、5.0mol/l、6.0mol/l。
[0054]
共沉淀的典型但非限制性的ph值例如为10、11、12。
[0055]
共沉淀典型但非限制性的反应温度例如为30℃、40℃、50℃、60℃、70℃。
[0056]
共沉淀典型但非限制性的反应时间例如为10h、20h、30h。
[0057]
(e)蒸氨:利用蒸汽对所述共沉淀后液进行加热蒸氨,得到蒸氨后液以及氨气;蒸氨蒸氨是采用一般的载热体水蒸汽作为加热剂,使循环水液面上氨气的平衡蒸汽压大于热载体中氨气的分压,汽液两相逆流接触,进行传质传热,从而使氨气逐渐从循环水中释放出来。
[0058]
优选地,所述蒸氨的加热温度为90~98℃。
[0059]
优选地,所述方法还包括如下步骤:步骤(e)制得的氨气返回步骤(d),部分蒸氨后液返回步骤(a);(f)沉锂:向所述蒸氨后液中加入碳酸盐溶液进行沉锂,得到碳酸锂;优选地,所述碳酸盐的浓度为200~300g/l;优选地,所述碳酸盐的摩尔用量为沉锂所需理论摩尔量的1.05~1.2倍;优选地,所述沉锂的温度为60~90℃,沉锂的时间为1~3h。
[0060]
加入稍微过量的碳酸根离子和适宜的反应时间可实现充分的沉锂。
[0061]
碳酸盐典型但非限制性的浓度例如为200g/l、250 g/l、300 g/l。
[0062]
碳酸盐加入的典型但非限制性的摩尔量比例如为1.05、1.10、1.15、1.20。
[0063]
沉锂典型但非限制性的温度例如为60℃、70℃、80℃、90℃。
[0064]
沉锂典型但非限制性的时间例如为1h、2h、3h。
[0065]
根据本发明的第二个方面,本发明提供的方法在制备电池正极中的应用。
[0066]
下面通过实施例对本发明作进一步说明。如无特别说明,实施例中的材料为根据现有方法制备而得,或直接从市场上购得。
[0067]
实施例1某废锂离子电池黑粉典型主要元素分析见下表:元素镍钴锰锂铝铜钙含量/%20.76.810.85.00.80.40.1某硫化镍钴矿ni 16.07%, co 0.65%, s 35.43%。
[0068]
取上述废锂离子电池黑粉100g,取上述硫化镍钴精矿100g,液固比2:1,单位为ml/
g,控制亚铁离子浓度为5g/l,加入h
2
so
4
控制ph值1.5,在95℃水浴中浸出3h,o
2
的进气流量为15m
3
/h。
[0069]
结果得到,镍的浸出率96.41%,钴的浸出率98.03%,锰的浸出率98.07%。
[0070]
上述溶液加热到70℃,加入镍钴锰酸锂电池黑粉调节溶液ph至6.0,除铁铝铜时间为3h,液固分离得到除铁铝铜渣和除铁铝铜后液,除铁铝铜后液主要成分如下:元素nicomnli含量/(g/l)88.1317.8325.9911.25元素alcufeca含量/(g/l)<0.001<0.001<0.0010.20上述溶液送p204萃取除杂,有机相组成为20%p204+80%磺化煤油,采用32%naoh进行钠皂,钠皂率为60%,钠皂有机再利用20g/l ni
2+
的硫酸镍溶液进行镍皂,负载有机相经反萃、反铁、洗氯等步骤进行再生利用。洗涤液为0.5 mol/l h
2
so
4
,反萃液为2.0 mol/l hcl,反铁液为6.0 mol/l hcl,洗氯液为5 g/l h
2
so
4
。有机与液相流比控制ca、fe、al、cu、zn等杂质完全脱除,mn萃取率控制36%。得到萃余液成分如下:元素nicomnli含量/(g/l)104.0116.9315.8010.02元素alcufeca含量/(g/l)<0.001<0.001<0.001<0.001上述溶液加入电池级硫酸镍结晶,使溶液含镍达134.8g/l。在氮气气氛保护下,络合剂氨水浓度为5mol/l,温度60℃,加入8mol/l氢氧化钠溶液控制ph值11.0,共沉淀时间10h。反应结束后,液固分离、洗涤、干燥,得到粉末状的ni
0.8
co
0.1
mn
0.1
(oh)
2
前驱体。
[0071]
共沉淀后液加热至70℃,加入260g/l碳酸钠溶液,加入量为理论量的1.1倍,反应2h,液固分离、洗涤、干燥,得到粉末状的碳酸锂产品,其整体流程图如图1所示。
[0072]
实施例2与实施例1不同的是,本实施例采用的中和剂为氢氧化镍,其他步骤与实施例1相同,取得与实施例1相同的效果。
[0073]
实施例3与实施例1不同的是,本实施例采用的中和剂为碳酸镍,其他步骤与实施例1相同,取得与实施例1相同的效果。
[0074]
分析常规硫化镍精矿浸出需要在极细的矿石粒度下,长时间浸出才可得到理想的浸出效果,且需加入氯离子作为助浸剂,氯离子在酸性体系中,对设备腐蚀极大。
[0075]
本发明提供的方法巧妙地创造了反应发生的条件,避免了传统处理单种原料需要加入额外化学试剂。本发明采用的新型中和剂除铁铝铜,可以用原料电池黑粉作为中和试剂,减少传统中和剂的使用量,避免向镍钴溶液体系引入杂质离子,同时降低中和除铁铝铜过程的镍钴损失。
[0076]
本发明提供的方法采用蒸氨及溶液的循环利用等工艺可极大地减少试剂消耗和三废排放。该方案是一种绿色、高效的协同处置电池黑粉和硫化镍钴矿直接制备三元前驱体和碳酸锂的方法。
[0077]
最后应说明的是:以上各实施例仅用以说明本发明的技术方案,而非对其限制;尽管参照前述各实施例对本发明进行了详细的说明,本领域的普通技术人员应当理解:其依然可以对前述各实施例所记载的技术方案进行修改,或者对其中部分或者全部技术特征进行等同替换;而这些修改或者替换,并不使相应技术方案的本质脱离本发明各实施例技术方案的范围。
起点商标作为专业知识产权交易平台,可以帮助大家解决很多问题,如果大家想要了解更多知产交易信息请点击 【在线咨询】或添加微信 【19522093243】与客服一对一沟通,为大家解决相关问题。
此文章来源于网络,如有侵权,请联系删除



tips