展现出改善的粘结耐久性和/或具有含磷表面的铝合金产品及其制造方法与流程



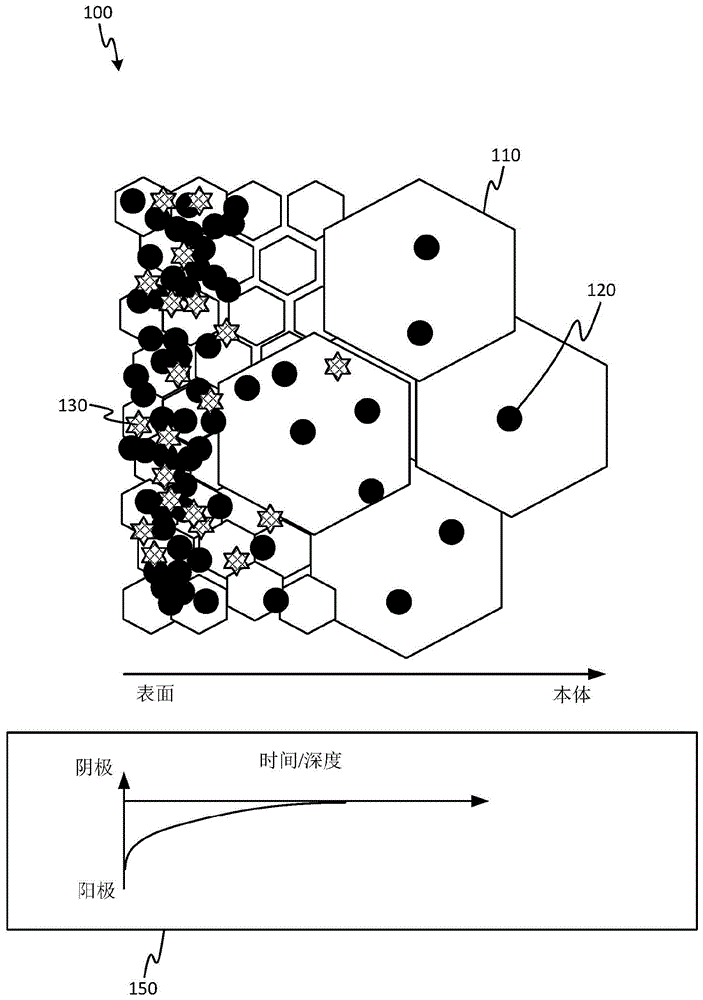
相关申请的交叉引用本申请要求于2017年12月21日提交的美国临时申请第62/608,614号以及于2018年10月5日提交的美国临时申请第62/741,688号的权益,所述美国临时申请通过引用整体并入本文。本公开涉及铝合金产品和所述铝合金产品的表面特征。本公开进一步涉及加工铝合金产品的方法。
背景技术:
:在铝合金和其它金属类产品的制造期间,铝合金产品通常与其它金属或合金(包含其它铝合金)粘结或接合。对铝合金产品的要求包含例如良好的粘结耐久性和高耐腐蚀性。铝合金产品可以以增强粘结耐久性和耐腐蚀性的方式进行加工。另外,铝合金产品应展现出对电阻点焊和其它连接方法的适应性。另外,所述方法应包含安全措施,以使在连接方法中使用的消耗品的更换最少。技术实现要素:本发明的涵盖实施例由权利要求限定,而不是由此
发明内容限定。此
发明内容是本发明的各个方面的高级概述,并且介绍了一些在下文的具体实施方式部分中进一步描述的概念。此
发明内容不旨在标识所要求保护的主题的关键或必要特性,也不旨在单独使用以确定所要求保护的主题的范围。应当通过参考整个说明书的适当部分、任何附图或所有附图以及每个权利要求来理解主题。本文描述了铝合金产品以及用于制造和加工所述铝合金产品的方法。本文所述的铝合金产品包括迁移元素、具有一定浓度的所述迁移元素的亚表面部分以及具有一定浓度的所述迁移元素的本体部分,其中所述铝合金产品包括4.0或更小的富集比,其中所述富集比是所述亚表面部分中的所述迁移元素的所述浓度与所述本体部分中的所述迁移元素的所述浓度之比。任选地,所述迁移元素包括zn、cu、mg和/或si。所述产品的所述亚表面部分可以包括从所述铝合金产品的表面到所述铝合金产品的内部最多约5μm深度(例如,到约2μm的深度)的区域,而所述本体部分可以包括所述铝合金产品的剩余部分。在一些情况下,产品中的富集比可以为2.0或更小、1.5或更小或1.0。所述铝合金产品可以包括7xxx系列铝合金、6xxx系列铝合金、5xxx系列铝合金或2xxx系列铝合金。本文还描述了一种铝合金产品,其包括具有一定浓度的迁移元素的亚表面部分以及具有一定浓度的所述迁移元素的本体部分。在这些产品中,所述亚表面部分中的所述迁移元素的所述浓度可以高于所述本体部分中的所述迁移元素的所述浓度。任选地,所述迁移元素包括cu、mn、cr和/或fe。所述铝合金产品可以任选地包括6xxx系列铝合金或5xxx系列铝合金。本文还描述了生产如本文所述的铝合金产品的方法。所述方法可以包括铸造包括迁移元素的铝合金以产生铸造铝合金制品、轧制所述铸造铝合金制品以提供经过轧制的铝合金制品以及对所述经过轧制的铝合金制品进行热处理以形成铝合金产品,其中所述迁移元素分布在所述铝合金产品的亚表面部分和本体部分内,从而提供4.0或更低的富集比,并且其中所述富集比是所述亚表面部分中的所述迁移元素的所述浓度与所述本体部分中的所述迁移元素的所述浓度之比。所述轧制步骤可以在约200℃到约550℃的温度下进行。所述热处理步骤可以在约400℃到约580℃的温度下进行,并且持续时间约为120秒或更短。所述方法可以进一步包括对所述铸造铝合金产品进行预处理。所述预处理步骤可以包含清洗所述合金产品的表面、蚀刻所述合金产品的所述表面以及对所述合金产品的所述表面施加预处理。任选地,所述预处理在所述热处理步骤之后进行。所述铸造可以包括直接冷激铸造或连续铸造。本文进一步描述了一种铝合金产品,其包括亚表面部分和本体部分,其中所述亚表面部分包括磷(p)。所述p可以以元素p、五氧化二磷、三氧化二磷、一氧化二磷或四氧化二磷中的至少一种形式存在于所述亚表面部分中。任选地,所述亚表面部分包括的p的量为约2原子百分比(at.%)到约10at.%。所述亚表面部分可以包括从所述铝合金产品的表面到约150μm深度(例如,到约83μm的深度)的区域。所述铝合金产品可以包括大于约15(例如,大于约20)的黄度指数(yellowindex)。本文还描述了对铝合金产品的表面进行处理的方法。所述对铝合金产品的表面进行处理的方法可以包括提供具有亚表面部分和本体部分的铝合金产品;以及用包括含p化合物的蚀刻溶液蚀刻所述铝合金产品的表面。任选地,所述提供步骤包括提供包括至少约0.001wt.%的镁(mg)(例如,约0.001wt.%到约10wt.%的mg)的铝合金产品。任选地,所述提供步骤包括提供包括5xxx系列铝合金、6xxx系列铝合金或7xxx系列铝合金的铝合金产品。所述含p化合物可以包括磷酸、膦酸、次膦酸、任何其它含p的酸及其组合。任选地,所述蚀刻溶液进一步包括一种或多种另外的酸(例如,硫酸、氢氟酸、乙酸和/或盐酸)。在一些实例中,所述蚀刻溶液包括磷酸和硫酸。任选地,磷酸与硫酸之比为约3到约5。在某些方面,蚀刻所述铝合金产品的所述表面使所述铝合金产品的所述表面上的mg暴露,并且形成磷酸镁、磷化镁、亚磷酸镁或其任何组合,并且在所述亚表面部分中提供0.001到10的p与mg的原子浓度比。本文还描述了根据本文所述的方法制备的铝合金产品。所述铝合金产品可以包括机动车车身部件等。通过考虑下面的详细描述和附图,另外的方面、目的和优点将变得显而易见。附图说明图1是铝合金产品的亚表面和本体部分内的迁移元素的示意图。图2是通过x射线光电子能谱示出5xxx和6xxx系列铝合金产品中的mg含量的图。图3是通过x射线光电子能谱示出5xxx和6xxx系列铝合金产品中的si含量的图。图4是通过x射线光电子能谱示出示例性铝合金产品表面中的mg含量的图。图5是通过x射线光电子能谱示出示例性铝合金产品表面中的si含量的图。图6是示出根据本文所述的方法制备和加工的示例性合金的粘结耐久性的图。图7是示出根据本文所述的示例性方法提供的示例性铝合金产品表面中的mg含量的图。图8是示出根据本文所述的示例性方法提供的示例性铝合金产品表面中的mg含量的图。图9a是示出通过本文所述的示例性方法产生的铝合金的亚表面和本体部分中的mg的辉光放电光发射能谱的图。图9b是示出通过本文所述的示例性方法产生的铝合金的亚表面和本体部分中的mg的辉光放电光发射能谱的图。图10a是示出通过本文所述的示例性方法产生的铝合金的亚表面和本体部分中的si的辉光放电光发射能谱的图。图10b是示出通过本文所述的示例性方法产生的铝合金的亚表面和本体部分中的si的辉光放电光发射能谱的图。图11a是示出通过本文所述的示例性方法产生的铝合金的亚表面和本体部分中的cu的辉光放电光发射能谱的图。图11b是示出通过本文所述的示例性方法产生的铝合金的亚表面和本体部分中的cu的辉光放电光发射能谱的图。图12a是示出通过本文所述的示例性方法产生的铝合金的亚表面和本体部分中的mn的辉光放电光发射能谱的图。图12b是示出通过本文所述的示例性方法产生的铝合金的亚表面和本体部分中的mn的辉光放电光发射能谱的图。图13a是示出通过本文所述的示例性方法产生的铝合金的亚表面和本体部分中的cr的辉光放电光发射能谱的图。图13b是示出通过本文所述的示例性方法产生的铝合金的亚表面和本体部分中的cr的辉光放电光发射能谱的图。图14a是示出通过本文所述的示例性方法产生的铝合金的亚表面和本体部分中的fe的辉光放电光发射能谱的图。图14b是示出通过本文所述的示例性方法产生的铝合金的亚表面和本体部分中的fe的辉光放电光发射能谱的图。图15是比较根据本公开的某些方面的各个铝合金样品在焊接之后的电阻点焊电极尖端寿命的图。图16是示出在根据本公开的某些方面的在铝合金的蚀刻期间去除的材料的量(被称为“蚀刻重量”)的图。图17是示出根据本公开的某些方面的铝合金中的mg的辉光放电光发射能谱(gdoes)的图。图18是示出根据本公开的某些方面的铝合金中的mg的辉光放电光发射能谱(gdoes)的图。图19是示出根据本公开的某些方面的铝合金中的mg的辉光放电光发射能谱(gdoes)的图。图20是示出根据本公开的某些方面的铝合金中的mg的辉光放电光发射能谱(gdoes)的图。图21a是示出根据本公开的某些方面的铝合金的表面部分的扫描电子显微照片。图21b是示出根据本公开的某些方面的铝合金的表面部分的扫描电子显微照片。图21c是示出根据本公开的某些方面的铝合金的表面部分的扫描电子显微照片。图21d是示出根据本公开的某些方面的铝合金的表面部分的扫描电子显微照片。图22a是示出根据本公开的某些方面的铝合金的表面部分的扫描电子显微照片。图22b是示出根据本公开的某些方面的铝合金的表面部分的扫描电子显微照片。图22c是示出根据本公开的某些方面的铝合金的表面部分的扫描电子显微照片。图22d是示出根据本公开的某些方面的铝合金的表面部分的扫描电子显微照片。图23a是示出根据本公开的某些方面的铝合金的表面部分的扫描电子显微照片。图23b是示出根据本公开的某些方面的铝合金的表面部分的扫描电子显微照片。图23c是示出根据本公开的某些方面的铝合金的表面部分的扫描电子显微照片。图23d是示出根据本公开的某些方面的铝合金的表面部分的扫描电子显微照片。图24a是示出根据本公开的某些方面的铝合金的表面部分的扫描电子显微照片。图24b是示出根据本公开的某些方面的铝合金的表面部分的扫描电子显微照片。图24c是示出根据本公开的某些方面的铝合金的表面部分的扫描电子显微照片。图24d是示出根据本公开的某些方面的铝合金的表面部分的扫描电子显微照片。图25的图片a示出了电阻点焊铜电极尖端的扫描电子显微照片。图25的图片b示出了根据本公开的某些方面的焊接区。图25的图片c示出了图片b的更高放大倍率图像。图26是示出了根据本公开的某些方面的铝合金的黄度指数(yi)的图。图27是示出了根据本公开的某些方面的铝合金的表面粗糙度的图。具体实施方式在本公开的第一实施例中,本文描述了具有期望的表面特性的金属合金产品,包含铝合金产品。本文所述的铝合金产品具有一定浓度的可控制的迁移元素,包含镁和硅。在一些情况下,可以控制贯穿合金产品厚度的迁移元素的浓度,从而产生期望的特性。本文所述的铝合金产品展现出的示例性期望特性包含例如高粘结耐久性和高耐腐蚀性。合金的特性由于加工合金以产生所述板、沙特板(shate)和片材的方法而实现。如本文进一步描述的,可以通过特别设计的轧制、热处理和/或蚀刻和预处理技术来实现期望的特性。在本公开的第二实施例中,本文描述了具有含有磷(p)的表面的铝合金产品。p可以以元素p或氧化磷的形式存在。p可以在表面蚀刻工艺期间沉积,并且可以导致铝合金产品表面展现出期望的特性。本文所述的铝合金产品展现出的此类期望的特性包含例如低接触电阻,从而在电阻点焊设备的电极尖端上提供减小的电子应力,并提供延长的所述电极尖端的使用寿命(例如,直至失效的焊接周期)。定义和描述本文使用的术语“发明(invention)”、“所述发明(theinvention)”、“此发明(thisinvention)”和“本发明(thepresentinvention)”旨在广范地指代此专利申请的所有主题和下文的权利要求。含有这些术语的陈述应理解为不限制本文所描述的主题或不限制下文专利权利要求的含义或范围。在此说明书中,参考由铝行业命名(如“系列”或“6xxx”)标识的合金。为了解最常用于命名和标识铝及其合金的数字命名系统,请参见“锻铝和锻铝合金的国际合金命名和化学组成限制(internationalalloydesignationsandchemicalcompositionlimitsforwroughtaluminumandwroughtaluminumalloys)”或“呈铸件和铸锭形式的铝合金的铝业协会合金命名和化学组成限制的登记记录(registrationrecordofaluminumassociationalloydesignationsandchemicalcompositionslimitsforaluminumalloysintheformofcastingsandingot)”,两者均由铝业协会(thealuminumassociation)出版。如本文所使用的,除非上下文另外明确规定,否则“一个/种(a/an)”或“所述(the)”的意义包含单数和复数参考物。如本文所使用的,板的厚度通常大于约15mm。例如,板可以指厚度大于15mm、大于20mm、大于25mm、大于30mm、大于35mm、大于40mm、大于45mm、大于50mm或大于100mm的铝产品。如本文所使用的,沙特板(也被称为薄板)的厚度通常为约4mm到约15mm。例如,沙特板的厚度可以为4mm、5mm、6mm、7mm、8mm、9mm、10mm、11mm、12mm、13mm、14mm或15mm。如本文所使用的,片材通常是指厚度小于约4mm的铝产品。例如,片材的厚度可以小于4mm、小于3mm、小于2mm、小于1mm、小于0.5mm、小于约0.3mm或小于0.1mm。在本申请中,参考合金的回火或状态。为了解最常用的合金回火描述,请参见“合金和回火命名系统的美国国家标准(ansi)h35(americannationalstandards(ansi)h35onalloyandtemperdesignationsystems)”。f状态或回火是指所制造的铝合金。w状态或回火是指在大于铝合金的溶线温度的温度下进行固溶热处理并淬火的铝合金。o状态或回火是指退火后的铝合金。hxx状态或回火(在本文中也被称为h回火)是指在冷轧之后进行或不进行热处理(例如,退火)的不可热处理的铝合金。合适的h回火包含hx1、hx2、hx3、hx4、hx5、hx6、hx7、hx8或hx9回火。t1状态或回火是指通过热加工和自然时效(例如,在室温下)进行冷却的铝合金。t2状态或回火是指通过热加工、冷加工和自然时效进行冷却的铝合金。t3状态或回火是指经过固溶热处理、冷加工和自然时效的铝合金。t4状态或回火是指经过固溶热处理和自然时效的铝合金。t5状态或回火是指通过热加工和人工时效(在高温下)进行冷却的铝合金。t6状态或回火是指经过固溶热处理和人工时效的铝合金。t7状态或回火是指经过固溶热处理和人工超龄化的铝合金。t8x状态或回火是指经过固溶热处理、冷加工和人工时效的铝合金。t9状态或回火是指经过固溶热处理、人工时效和冷加工的铝合金。w状态或回火是指固溶热处理后的铝合金。如本文所使用的,如“铸造金属制品”、“铸造制品”等术语是可互换的,并且是指通过直接冷激铸造(包含直接冷激共铸造)或半连续铸造、连续铸造(包含例如,通过使用双带式铸造机、双辊式铸造机、块式铸造机或任何其它连续铸造机)、电磁铸造、热顶铸造或任何其它铸造方法产生的产品。如本文所使用的,“粘结耐久性”是指粘结剂在暴露于引发粘结剂失效的环境条件之后将两个产品粘结在一起以承受循环机械应力的能力。粘结耐久性的特征在于施加到结合产品上的机械应力循环的次数,同时所述结合产品暴露于环境条件下,直至粘结失败。如本文所使用的,“室温”可以包含约15℃到约30℃的温度,例如约15℃、约16℃、约17℃、约18℃、约19℃、约20℃、约21℃、约22℃、约23℃、约24℃、约25℃、约26℃、约27℃、约28℃、约29℃或约30℃。本文公开的所有范围应理解为涵盖任何端点以及其中包含的任何和所有子范围。例如,规定的范围“1到10”应被视为包含最小值1与最大值10之间的任何和所有子范围(并且包含所述最小值1和所述最大值10);即,以最小值1或更大值(例如1到6.1)开始,并且以最大值10或更小值(例如5.5到10)结束的所有子范围。展现出改善的粘结耐久性的铝合金产品铝合金产品本文描述了具有期望的表面特性的铝合金产品。除其它特性外,本文所述的铝合金产品贯穿合金产品的厚度(包含在合金产品的亚表面内)含有受控浓度的迁移元素。在一些非限制性实例中,所公开的合金产品具有用于粘结、接合、摩擦、耐腐蚀性和光学特性的改善的表面质量。在某些情况下,合金产品还表现出非常好的阳极氧化质量。在一些方面,具有期望的表面特性(包含改善的粘结和接合特性)的合金具有低的镁(mg)与硅(si)的富集比。合金的亚表面区域与剩余部分(即合金产品的本体)之间的迁移元素的原子浓度差异可以引起电化学活性中的梯度。电化学活性中的梯度可以导致表面更具阳极活性,并且由于合金产品的亚表面与本体部分之间的电偶合而易于被腐蚀。图1是包括铝基质110的铝合金产品100的说明性表示,所述铝基质富含mg120和si130。如图1所示,mg120和si130在热处理期间可能迁移到合金表面,从而提供不期望的表面特性。如图1的开路电势(ocp)曲线150所示,合金亚表面与合金本体(剩余部分)之间的迁移元素的原子浓度差异可以引起电化学活性中的梯度。图2和3分别展示了5xxx系列(合金a和b)和6xxx系列(c、d和e)合金产品中的mg和si的元素分布。与合金产品剩余部分的含量相比,5xxx系列合金(合金a和b)在合金产品表面附近表现出较少的mg和si富集,而6xxx系列合金(合金c、d和e)在合金表面附近表现出更多的mg和si富集。令人惊讶的是,控制亚表面内的迁移元素分布可以逆转图1-3所示的效果并提供期望的表面特性,而无需改变或以其它方式调整用于制备铝合金产品的元素的浓度。下文描述了由于元素在亚表面内的适当分布而含有期望的表面特性的此类铝合金产品。如本文所使用的,术语“亚表面”是指合金产品的从合金产品的外表面延伸到合金产品的内部最多约5μm深度的部分。任选地,亚表面是指延伸到合金产品的内部至以下深度的合金的部分:约0.01μm、约0.05μm、约0.1μm、约0.15μm、约0.2μm、约0.25μm、约0.3μm、约0.35μm、约0.4μm、约0.45μm、约0.5μm、约0.55μm、约0.6μm、约0.65μm、约0.7μm、约0.75μm、约0.8μm、约0.85μm、约0.9μm、约0.95μm、约1.0μm、约1.5μm、约2.0μm、约2.5μm、约3.0μm、约3.5μm、约4.0μm、约4.5μm、或约5.0μm或介于这之间的任何深度。在一些实例中,亚表面从表面延伸到合金产品的内部约2.0μm的深度。铝合金产品的除亚表面部分之外的部分(例如,合金产品的剩余部分)在本文中被称为合金产品的本体。如本文所使用的,术语“迁移元素”是指由于例如合金产品的一个或多个生产和加工步骤(在下文中进一步描述)而可从合金产品中的第一位置扩散到合金产品中的第二位置的元素。示例性迁移元素包含例如镁(mg)、硅(si)、铜(cu)、锰(mn)、锌(zn)、铬(cr)和铁(fe)。任选地,迁移元素呈化合物或相的形式。例如,mg可以以mg2si或mgo的形式存在。mn和fe可以以例如al(femn)或al(fe,mn)si的形式存在。在一些实例中,如本文所述的迁移元素可以扩散到整个合金产品中,使得所述元素的浓度贯穿合金产品的全厚度分布(即,在亚表面和本体部分内)。例如,合金产品可以包含分布在整个合金产品中而不集中在亚表面内的一定浓度的mg和si。此类合金产品显示出卓越的粘结耐久性和耐腐蚀特性。在一些实例中,如本文所述的迁移元素可以朝向合金产品的亚表面部分扩散,使得在合金产品的表面附近提供迁移元素的富集。例如,合金产品可以包含定位在合金产品的亚表面部分内的一定浓度的zn、cu、mn、cr和/或fe。此类合金产品显示出卓越的粘合性能,并且可以作为预处理。另外,在亚表面内包含cr富集的合金产品可以控制fe-si颗粒的分布,从而增强耐腐蚀性。在迁移元素贯穿合金产品的全厚度分布或迁移元素定位在合金产品的亚表面部分内的情况下,迁移元素可以均匀地填充或可变地填充在合金产品的全厚度或亚表面内。如本文所使用的,与迁移元素有关的“均匀地填充”意指特定的迁移元素均匀地分布在合金产品的全厚度或亚表面内。在这些情况下,平均而言,每区域(即,在亚表面的区域内或在合金产品的全厚度的区域内)特定迁移元素的浓度跨区域相对恒定。如本文所使用的,与迁移元素分布有关的“相对恒定”意指铝合金产品的亚表面或全厚度的第一区域中的元素浓度可以与铝合金产品的亚表面或全厚度的第二区域中的元素浓度相差最多约20%(例如,最多约15%、最多约10%、最多约5%或最多约1%)。在其它情况下,区域中特定迁移元素的浓度可变地填充在合金产品的全厚度或亚表面内。如本文所使用的,与迁移元素分布有关的“可变地填充”意指特定的迁移元素不均匀地分布在合金产品的全厚度或亚表面内。例如,与亚表面的第二部分中(或合金产品的全厚度的第二部分中)的迁移元素的浓度相比,可以在亚表面的第一部分中(或合金产品的全厚度的第一部分中)定位相同迁移元素的更高浓度。在一些实例中,可以通过富集比来表征合金产品内的迁移元素分布。富集比是合金产品的亚表面中的迁移元素浓度与本体中的迁移元素浓度的比较。在一些实例中,可以通过测量在亚表面内的深度处以及在合金的厚度内和亚表面外部(即,在合金本体内)的深度处的迁移元素的峰值原子浓度来计算富集比。可以通过以下等式来定量富集比:例如,可以在2nm处和40nm处测量原子浓度,2nm表示可以找到峰值原子浓度的特定合金产品的亚表面内的深度,而40nm表示特定合金产品的本体部分内的深度。可以使用以下等式提供富集比:其中(原子浓度)2nm表示在2nm处的迁移元素的浓度,而(原子浓度)40nm表示在40nm处的迁移元素的浓度。可以使用本领域普通技术人员已知的技术(包含x射线光电子能谱(xps))来测量原子浓度。特定元素的低富集比指示迁移元素的浓度贯穿合金产品分布,而并不主要定位在亚表面内。可被视为低富集比的合适的富集比包含例如约4.0或更低(例如,约1.0到约4.0)。例如,富集比可以大约为4.0或更低、3.9或更低、3.8或更低、3.7或更低、3.6或更低、3.5或更低、3.4或更低、3.3或更低、3.2或更低、3.1或更低、3.0或更低、2.9或更低、2.8或更低、2.7或更低、2.6或更低、2.5或更低、2.4或更低、2.3或更低、2.2或更低、2.1或更低、2.0或更低、1.9或更低、1.8或更低、1.7或更低、1.6或更低、1.5或更低、1.4或更低、1.3或更低、1.2或更低、1.1或更低或1.0。特定元素的高富集比指示迁移元素的高浓度定位在合金产品的亚表面内。可被视为高富集比的合适的富集比包含例如约4.1或更大。例如,富集比可以大约为4.1或更大、4.2或更大、4.3或更大、4.4或更大、4.5或更大、4.6或更大、4.7或更大、4.8或更大、4.9或更大、5.0或更大、5.1或更大、5.2或更大、5.3或更大、5.4或更大、5.5或更大、5.6或更大、5.7或更大、5.8或更大、5.9或更大、6.0或更大、6.1或更大、6.2或更大、6.3或更大、6.4或更大、6.5或更大、6.6或更大、6.7或更大、6.8或更大、6.9或更大、7.0或更大、7.1或更大、7.2或更大、7.3或更大、7.4或更大、7.5或更大、7.6或更大、7.7或更大、7.8或更大、7.9或更大或8.0或更大。在一些情况下,令人期望的是,铝合金产品针对一种或多种迁移元素具有高富集比而针对其它迁移元素具有低富集比(例如,耗尽)。例如,本文所述的铝合金产品可以针对mg、si和/或cu具有低富集比。在一些实例中,本文所述的铝合金产品可以针对cr、mn和/或fe具有高富集比。在一些情况下,铝合金产品的某个区域的元素富集可能伴随另一个区域的元素耗尽。在一些非限制性实例中,mg、si和/或cu的富集可以发生在铝合金产品的亚表面的区域中,fe和mn可以在所述区域中耗尽。在一些其它实例中,铝合金产品可以具有以si、mn和/或fe耗尽以及cu富集为特征的亚表面。在一些方面,迁移元素的粒径和形态可以影响铝合金产品的表面特性。例如,铝合金产品的亚表面内的小型cu分散质和/或颗粒(例如,直径小于约10nm)可以提供良好的粘结耐久性,而对腐蚀敏感性没有显著影响。任选地,cu分散质和/或颗粒的直径约为9nm或更小、直径约为8nm或更小、直径约为7nm或更小、直径约为6nm或更小、直径约为5nm或更小、直径约为4nm或更小、直径约为3nm或更小、直径约为2nm或更小或直径约为1nm或更小。铝合金产品可以具有任何合适的组成。在非限制性实例中,铝合金产品可以包含2xxx系列铝合金、5xxx系列铝合金、6xxx系列铝合金或7xxx系列铝合金。用作铝合金产品的非限制性示例性aa2xxx系列合金可以包含aa2001、a2002、aa2004、aa2005、aa2006、aa2007、aa2007a、aa2007b、aa2008、aa2009、aa2010、aa2011、aa2011a、aa2111、aa2111a、aa2111b、aa2012、aa2013、aa2014、aa2014a、aa2214、aa2015、aa2016、aa2017、aa2017a、aa2117、aa2018、aa2218、aa2618、aa2618a、aa2219、aa2319、aa2419、aa2519、aa2021、aa2022、aa2023、aa2024、aa2024a、aa2124、aa2224、aa2224a、aa2324、aa2424、aa2524、aa2624、aa2724、aa2824、aa2025、aa2026、aa2027、aa2028、aa2028a、aa2028b、aa2028c、aa2029、aa2030、aa2031、aa2032、aa2034、aa2036、aa2037、aa2038、aa2039、aa2139、aa2040、aa2041、aa2044、aa2045、aa2050、aa2055、aa2056、aa2060、aa2065、aa2070、aa2076、aa2090、aa2091、aa2094、aa2095、aa2195、aa2295、aa2196、aa2296、aa2097、aa2197、aa2297、aa2397、aa2098、aa2198、aa2099或aa2199。用作铝合金产品的非限制性示例性aa5xxx系列铝合金可以包含aa5182、aa5183、aa5005、aa5005a、aa5205、aa5305、aa5505、aa5605、aa5006、aa5106、aa5010、aa5110、aa5110a、aa5210、aa5310、aa5016、aa5017、aa5018、aa5018a、aa5019、aa5019a、aa5119、aa5119a、aa5021、aa5022、aa5023、aa5024、aa5026、aa5027、aa5028、aa5040、aa5140、aa5041、aa5042、aa5043、aa5049、aa5149、aa5249、aa5349、aa5449、aa5449a、aa5050、aa5050a、aa5050c、aa5150、aa5051、aa5051a、aa5151、aa5251、aa5251a、aa5351、aa5451、aa5052、aa5252、aa5352、aa5154、aa5154a、aa5154b、aa5154c、aa5254、aa5354、aa5454、aa5554、aa5654、aa5654a、aa5754、aa5854、aa5954、aa5056、aa5356、aa5356a、aa5456、aa5456a、aa5456b、aa5556、aa5556a、aa5556b、aa5556c、aa5257、aa5457、aa5557、aa5657、aa5058、aa5059、aa5070、aa5180、aa5180a、aa5082、aa5182、aa5083、aa5183、aa5183a、aa5283、aa5283a、aa5283b、aa5383、aa5483、aa5086、aa5186、aa5087、aa5187和aa5088。用于铝合金产品的非限制性示例性aa6xxx系列合金可以包含aa6101、aa6101a、aa6101b、aa6201、aa6201a、aa6401、aa6501、aa6002、aa6003、aa6103、aa6005、aa6005a、aa6005b、aa6005c、aa6105、aa6205、aa6305、aa6006、aa6106、aa6206、aa6306、aa6008、aa6009、aa6010、aa6110、aa6110a、aa6011、aa6111、aa6012、aa6012a、aa6013、aa6113、aa6014、aa6015、aa6016、aa6016a、aa6116、aa6018、aa6019、aa6020、aa6021、aa6022、aa6023、aa6024、aa6025、aa6026、aa6027、aa6028、aa6031、aa6032、aa6033、aa6040、aa6041、aa6042、aa6043、aa6151、aa6351、aa6351a、aa6451、aa6951、aa6053、aa6055、aa6056、aa6156、aa6060、aa6160、aa6260、aa6360、aa6460、aa6460b、aa6560、aa6660、aa6061、aa6061a、aa6261、aa6361、aa6162、aa6262、aa6262a、aa6063、aa6063a、aa6463、aa6463a、aa6763、a6963、aa6064、aa6064a、aa6065、aa6066、aa6068、aa6069、aa6070、aa6081、aa6181、aa6181a、aa6082、aa6082a、aa6182、aa6091和aa6092。用于铝合金产品的非限制性示例性aa7xxx系列合金可以包含aa7003、aa7004、aa7204、aa7005、aa7108、aa7108a、aa7009、aa7010、aa7012、aa7014、aa7015、aa7016、aa7116、aa7017、aa7018、aa7019、aa7019a、aa7020、aa7021、aa7022、aa7122、aa7023、aa7024、aa7025、aa7026、aa7028、aa7029、aa7129、aa7229、aa7030、aa7031、aa7032、aa7033、aa7034、aa7035、aa7035a、aa7036、aa7136、aa7037、aa7039、aa7040、aa7140、aa7041、aa7042、aa7046、aa7046a、aa7047、aa7049、aa7049a、aa7149、aa7249、aa7349、aa7449、aa7050、aa7050a、aa7150、aa7055、aa7155、aa7255、aa7056、aa7060、aa7064、aa7065、aa7068、aa7168、aa7072、aa7075、aa7175、aa7475、aa7076、aa7178、aa7278、aa7278a、aa7081、aa7181、aa7085、aa7185、aa7090、aa7093、aa7095、aa7099和aa7199。铝合金产品可以具有任何合适的规格。例如,铝合金产品可以为规格介于约0.5mm与约50mm之间(例如,约0.5mm、约1mm、约2mm、约3mm、约4mm、约5mm、约6mm、约7mm、约8mm、约9mm、约10mm、约15mm、约20mm、约25mm、约30mm、约35mm、约40mm、约45mm、约50mm或介于这之间的任何规格)的铝合金板、铝合金沙特板或铝合金片材。制备合金产品的方法在某些方面,可以使用如本文所述的方法制备所公开的合金产品。在不旨在限制本发明的情况下,铝合金的特性部分地由微结构在合金制备期间的形成来确定。在某些方面,用于合金组合物的制备的方法确定合金是否将具有适于期望的应用的特性。如下文所描述的,某些加工步骤和条件(包含轧制(例如,热轧和/或冷轧)、热处理(例如,均质化、固溶化和/或退火)以及预处理步骤和条件)提供上文描述的具有期望的粘结耐久性和耐腐蚀特性的合金产品。如本文所述的生产铝合金产品的方法可以包含以下步骤:铸造熔融铝合金以形成铸造铝合金制品,以及通过一个或多个步骤(包含例如淬火、轧制、热处理和/或预处理)加工铝合金制品以形成铝合金产品。直接冷激铸造和加工在一些情况下,可以使用直接冷激(dc)铸造工艺来铸造本文所述的铝合金产品,从而形成如铸锭等铸造产品。然后可以将所得铸锭除垢。然后可以对铸造产品进行另外的加工步骤。在一个非限制性实例中,加工方法包含将铝合金铸锭均质化,并对铝合金铸锭进行热轧,从而形成铝合金热带。然后可以对铝合金热带进行冷轧、固溶热处理以及任选的预处理步骤。均质化均质化步骤可以包含加热由本文所述的合金组合物制备的铸造产品以达到约或至少约450℃(例如,至少约460℃、至少约470℃、至少约480℃、至少约490℃、至少约500℃、至少约510℃、至少约520℃、至少约530℃、至少约540℃、至少约550℃、至少约560℃、至少约570℃或至少约580℃)的峰值金属温度(pmt)。例如,可以将铸锭加热至约450℃到约580℃、约460℃到约575℃、约470℃到约570℃、约480℃到约565℃、约490℃到约555℃或约500℃到约550℃的温度。在一些情况下,到达pmt的加热速率可以为约100℃/小时或更低、约75℃/小时或更低、约50℃/小时或更低、约40℃/小时或更低、约30℃/小时或更低、约25℃/小时或更低、约20℃/小时或更低或约15℃/小时或更低。在其它情况下,到达pmt的加热速率可以为约10℃/分钟到约100℃/分钟(例如,约10℃/分钟到约90℃/分钟、约10℃/分钟到约70℃/分钟、约10℃/分钟到约60℃/分钟、约20℃/分钟到约90℃/分钟、约30℃/分钟到约80℃/分钟、约40℃/分钟到约70℃/分钟或约50℃/分钟到约60℃/分钟)。然后使铸锭浸泡(即,保持在指定的温度下)一段时间。根据一个非限制性实例,使铸锭浸泡最多约6小时(例如,约30分钟到约6小时,包含端值)。例如,可以将铸锭在至少约500℃的温度下浸泡约30分钟、约1小时、约2小时、约3小时、约4小时、约5小时、或约6小时或介于这之间的任何时间。热轧在均质化步骤之后,可以进行热轧步骤以形成热带。在某些情况下,将铸锭放下并进行热轧。热轧温度可以在约200℃到约550℃(例如,约250℃到约500℃或约300℃到约400℃)之间。例如,热轧温度可以为约200℃、约205℃、约210℃、约215℃、约220℃、约225℃、约230℃、约235℃、约240℃、约245℃、约250℃、约255℃、约260℃、约265℃、约270℃、约275℃、约280℃、约285℃、约290℃、约295℃、约300℃、约305℃、约310℃、约315℃、约320℃、约325℃、约330℃、约335℃、约340℃、约345℃、约350℃、约355℃、约360℃、约365℃、约370℃、约375℃、约380℃、约385℃、约390℃、约395℃、约400℃、约405℃、约410℃、约415℃、约420℃、约425℃、约430℃、约435℃、约440℃、约445℃、约450℃、约455℃、约460℃、约465℃、约470℃、约475℃、约480℃、约485℃、约490℃、约495℃、约500℃、约505℃、约510℃、约515℃、约520℃、约525℃、约530℃、约535℃、约540℃、约545℃或约550℃。在一些非限制性实例中,热轧出口温度可以为约200℃到约450℃。在一些实例中,热轧出口温度不应超过约360℃。例如,热轧出口温度的范围可以为约250℃到约360℃(例如,约300℃到约350℃)。在这些实例中,热轧出口温度可以为约250℃、约255℃、约260℃、约265℃、约270℃、约275℃、约280℃、约285℃、约290℃、约295℃、约300℃、约305℃、约310℃、约315℃、约320℃、约325℃、约330℃、约335℃、约340℃、约345℃、约350℃、约355℃或约360℃。在某些情况下,可以将铸造制品热轧至约4mm到约15mm厚的规格(例如,约5mm到约12mm厚的规格),其被称为沙特板。例如,可以将铸锭热轧至约4mm厚的规格、约5mm厚的规格、约6mm厚的规格、约7mm厚的规格、约8mm厚的规格、约9mm厚的规格、约10mm厚的规格、约11mm厚的规格、约12mm厚的规格、约13mm厚的规格、约14mm厚的规格或约15mm厚的规格。在某些情况下,可以将铸锭热轧至大于15mm厚的规格(即,板)。在其它情况下,可以将铸锭热轧至小于4mm厚的规格(即,片材)。冷轧可以在热轧步骤之后进行冷轧步骤。在某些方面,可以将来自热轧步骤的热带冷轧成片材。可以将热带的温度降低至约20℃到约200℃(例如,约120℃到约200℃)范围内的温度。冷轧步骤可以进行一段时间,从而得到期望的最终规格厚度。任选地,冷轧步骤可以进行长达约1小时(例如,约10分钟到约30分钟)。例如,冷轧步骤可以进行约10分钟、约20分钟、约30分钟、约40分钟、约50分钟或约1小时。任选地,期望的最终规格厚度小于约4.0mm。在某些方面,将经过轧制的产品冷轧至约0.4mm到约1.0mm、约1.0mm到约3.0mm或约3.0mm到小于约4.0mm的厚度。在某些方面,将合金冷轧至约3.5mm或更小、约3mm或更小、约2.5mm或更小,约2mm或更小、约1.5mm或更小、约1mm或更小、约0.5mm或更小、或约0.4mm或更小、约0.3mm或更小、约0.2mm或更小、或约0.1mm或更小或介于这之间的任何厚度。固溶化然后可以在固溶热处理步骤中将冷轧卷材固溶化。固溶化可以包含将最终规格的铝合金从室温加热至约400℃到约580℃(例如,约450℃到约575℃、约520℃到约580℃、约530℃到约570℃、约545℃到约575℃、约550℃到约570℃、约555℃到约565℃、约540℃到约560℃、约560℃到约580℃或约550℃到约575℃)的温度。例如,可以通过将最终规格的铝合金加热至以下温度来进行固溶化步骤:约400℃、约405℃、约410℃、约415℃、约420℃、约425℃、约430℃、约435℃、约440℃、约445℃、约450℃、约455℃、约460℃、约465℃、约470℃、约475℃、约480℃、约485℃、约490℃、约495℃、约500℃、约505℃、约510℃、约515℃、约520℃、约525℃、约530℃、约535℃、约540℃、约545℃、约550℃、约555℃、约560℃、约565℃、约570℃、约575℃或约580℃。在一些实例中,在560℃或更低(例如,约520℃到约560℃)的温度下进行固溶化。例如,可以在约520℃、约525℃、约530℃、约535℃、约540℃、约545℃、约550℃、约555℃或约560℃的温度下进行固溶化。在560℃或更低温度下的固溶化可以导致合金产品在合金产品亚表面和合金产品本体内具有期望的迁移元素颗粒的粒径和粒径分布,并且针对某些迁移元素(例如,mg和si)具有低富集比。冷轧卷材可以在固溶化温度下浸泡一段时间。在某些方面,使冷轧卷材浸泡最多约2小时(例如,约1秒到约120分钟,包含端值)。例如,可以将冷轧卷材在约525℃到约590℃的固溶化温度下浸泡1秒、5秒、10秒、15秒、20秒、25秒、30秒、35秒、40秒、45秒、50秒、55秒、60秒、65秒、70秒、75秒、80秒、85秒、90秒、95秒、100秒、105秒、110秒、115秒、120秒、125秒、130秒、135秒、140秒、145秒、150秒、5分钟、10分钟、15分钟、20分钟、25分钟、30分钟、35分钟、40分钟、45分钟、50分钟、55分钟、60分钟、65分钟、70分钟、75分钟、80分钟、85分钟、90分钟、95分钟、100分钟、105分钟、110分钟、115分钟、或120分钟或介于这之间的任何时间。在一些实例中,期望较短的浸泡持续时间。例如,可以使冷轧卷材浸泡约120秒或更短(例如,115秒或更短、110秒或更短、105秒或更短、100秒或更短、95秒或更短、90秒或更短、85秒或更短、80秒或更短、75秒或更短、70秒或更短、65秒或更短、60秒或更短、55秒或更短、50秒或更短、45秒或更短、40秒或更短、35秒或更短,30秒或更短、25秒或更短、20秒或更短、15秒或更短、10秒或更短、5秒或更短或1秒)。淬火在某些方面,然后可以在基于所选规格的淬火步骤中以可在约50℃/秒到400℃/秒之间变化的淬火速度将铝合金产品冷却至约35℃的温度。例如,淬火速率可以为约50℃/秒到约375℃/秒、约60℃/秒到约375℃/秒、约70℃/秒到约350℃/秒、约80℃/秒到约325℃/秒、约90℃/秒到约300℃/秒、约100℃/秒到约275℃/秒、约125℃/秒到约250℃/秒、约150℃/秒到约225℃/秒或约175℃/秒到约200℃/秒。在淬火步骤中,用液体(例如,水)和/或气体或另一种所选择的淬火介质将铝合金产品淬火。在某些方面,铝合金产品可以被空气淬火。铝合金产品可以任选地经历预处理工艺,如下文进一步描述的。连续铸造和加工可以使用连续铸造(cc)工艺来铸造本文所述的铝合金产品,从而形成铸造铝合金制品。cc工艺可以包含但不限于使用双带式铸造机、双辊式铸造机或块式铸造机。在一些实例中,通过cc工艺进行铸造工艺以形成铸造产品,如坯料、板坯、沙特板、条带等。本文所述的cc方法可以包含通过水冷却熔融合金、控制熔融合金的进料速率或控制熔融合金的铸造速度来从熔融合金中提取热量,如下文进一步描述的。从熔融合金中提取热量可以控制迁移元素在熔融合金内的扩散。在一些非限制性实例中,连续铸造方法可以包含以受控方式提取热量,从而控制迁移元素在金属制品内的扩散。在一些方面,在不受控的热量提取的情况下固化熔融合金可能导致迁移元素在熔融合金内的不期望的扩散。在一些情况下,迁移元素可以在固化期间扩散到熔融合金的表面,从而提供具有不期望的表面特性的铸造金属制品。在一些非限制性实例中,控制固化速率(例如,以受控方式提取热量)可以控制迁移元素的扩散,从而为铸造金属制品提供期望的表面特性。在一些方面,控制迁移元素的扩散可以提供铸造金属制品表面的选择性富集,从而提供具有定制的表面特性的铸造金属制品。可以通过任何合适的方法从熔融合金中提取热量,所述方法包含用水进行冷却、用空气进行冷却、控制熔融合金进入铸腔的进料速率或控制一对移动的相对铸造表面的速度。可以通过采用一个或多个喷嘴将水直接输送到熔融合金上来进行水冷却。同样,可以通过采用一个或多个喷嘴将强迫通风直接输送到熔融合金上来进行空气冷却。在一些实例中,控制熔融合金进入铸腔的进料速率可以控制迁移元素的扩散。较慢的进料速率可以使熔融合金更靠近熔融金属喷射器固化,从而抑制迁移元素的任何不期望的扩散。同样,较快的进料速率可以使熔融合金更远离熔融金属喷射器固化,从而导致迁移元素的不期望的扩散。在一些实例中,控制一对移动的相对铸造表面的速度可以控制迁移元素的扩散。一对移动的相对铸造表面的较慢速度可以使熔融合金更靠近熔融金属喷射器固化,从而抑制迁移元素的任何不期望的扩散。同样,一对移动的相对铸造表面的较快速度可以使熔融合金更远离熔融金属喷射器固化,从而导致迁移元素的不期望的扩散。在一些非限制性实例中,控制迁移元素的扩散速率可以提供迁移元素的选择性扩散。例如,可以以促进第一迁移元素的扩散并同时抑制第二迁移元素的扩散的速率从熔融金属中提取热量。因此,在固化熔融合金以提供金属制品期间,可以通过所选择的迁移元素选择性地富集金属制品表面。然后可以对铸造铝合金制品进行另外的加工步骤以形成铝合金产品。加工步骤可以包含例如淬火、热轧、冷轧和/或退火步骤。淬火在铸造步骤之后,可以将铸造铝合金制品淬火。在淬火步骤中,可以将铸造铝合金制品冷却至约300℃或低于约300℃的温度。例如,可以将铸造铝合金制品冷却至约290℃或低于约290℃、约280℃或低于约280℃、约270℃或低于约270℃、约260℃或低于约260℃、约250℃或低于约250℃、约240℃或低于约240℃、约230℃或低于约230℃、约220℃或低于约220℃、约210℃或低于约210℃、约200℃或低于约200℃、约190℃或低于约190℃、约180℃或低于约180℃、约170℃或低于约170℃、约160℃或低于约160℃、约150℃或低于约150℃、约140℃或低于约140℃、约130℃或低于约130℃、约120℃或低于约120℃、约110℃或低于约110℃、约100℃或低于约100℃、约90℃或低于约90℃、约80℃或低于约80℃、约70℃或低于约70℃、约60℃或低于约60℃、约50℃或低于约50℃或约40℃或低于约40℃(例如,约25℃)的温度。可以使用液体(例如,水)、气体(例如,空气)或另一种所选择的淬火介质进行淬火步骤。热轧和形成热带所述方法还包含对铸造铝合金制品进行热轧以产生经过轧制的铝合金制品(例如,热带)的步骤。对铸造铝合金制品进行热轧的步骤可以包含将铸造铝合金制品的厚度减小至少约30%且最多约80%(例如,减小约30%、减小约35%、减小约40%、减小约45%、减小约50%、减小约55%、减小约60%、减小约65%、减小约70%或减小约75%)。可以在约400℃到约600℃(例如,约425℃到约575℃或约450℃到约550℃)的温度下进行热轧。例如,可以在约400℃、约410℃、约420℃、约430℃、约440℃、约450℃、约460℃、约470℃、约480℃、约490℃、约500℃、约510℃、约520℃、约530℃、约540℃、约550℃、约560℃、约570℃、约580℃、约590℃、约600℃或介于这之间的任何温度下进行热轧步骤。冷轧和退火然后可以使用例如单机架轧机或多机架轧机进行冷轧步骤。在一些情况下,冷轧步骤为一步冷轧工艺。在一些情况下,冷轧步骤为两步冷轧工艺。在一步冷轧工艺中,可以将卷材或片材的温度降低至约20℃到约150℃(例如,约120℃到约200℃)范围内的温度。在一些情况下,将卷材或片材冷轧,其中入口温度范围为约20℃到约150℃。入口温度可以为例如约20℃、约30℃、约40℃、约50℃、约60℃、约70℃、约80℃、约90℃、约100℃、约110℃、约120℃、约130℃、约140℃或约150℃。在一些情况下,冷轧出口温度的范围可以为约80℃到约200℃。冷轧出口温度可以为例如约80℃、约90℃、约100℃、约110℃、约120℃、约130℃、约140℃、约150℃、约160℃、约170℃、约180℃、约190℃或约200℃。冷轧步骤可以进行一段时间,从而得到约0.2mm到约6mm的规格。例如,所得规格可以为约0.5mm到约5.5mm或约0.8mm到约5.0mm。任选地,冷轧步骤可以进行长达约1小时(例如,约10分钟到约30分钟)。例如,冷轧步骤可以进行约10分钟、约20分钟、约30分钟、约40分钟、约50分钟或约1小时。如上文所讨论的,冷轧步骤可以为两步冷轧工艺,在所述两步冷轧工艺中,在冷轧期间进行中间退火步骤。在两步冷轧工艺中,可以将卷材或片材的温度降低至约20℃到约150℃(例如,约120℃到约200℃)范围内的温度。在一些情况下,将卷材或片材冷轧,其中入口温度范围为约20℃到约150℃。入口温度可以为例如约20℃、约30℃、约40℃、约50℃、约60℃、约70℃、约80℃、约90℃、约100℃、约110℃、约120℃、约130℃、约140℃或约150℃。在一些情况下,冷轧出口温度的范围可以为约80℃到约200℃。出口温度可以为例如约80℃、约90℃、约100℃、约110℃、约120℃、约130℃、约140℃、约150℃、约160℃、约170℃、约180℃、约190℃或约200℃。冷轧步骤的第一步可以进行一段时间,从而得到约1.2mm到约6mm的规格。例如,所得规格可以为约1.25mm到约5.5mm、约1.3mm到约4mm、约1.4mm到约3.5mm或约1.5mm到约3mm。任选地,冷轧步骤可以进行长达约1小时(例如,约10分钟到约30分钟)。例如,冷轧步骤可以进行约10分钟、约20分钟、约30分钟、约40分钟、约50分钟或约1小时。作为两步冷轧工艺的下一步骤,可以进行在本文中被称为中间退火步骤的退火工艺。在中间退火步骤中,可以将冷轧规格保持在约250℃到约450℃(例如,约275℃到约400℃或约300℃到约375℃)范围内的温度下,其中浸泡时间最多为约4小时。例如,浸泡时间的范围可以为约10分钟到约4小时(例如,约10分钟、约30分钟、约1小时、约2小时、约3小时或约4小时)。任选地,中间退火步骤可以产生具有圆形晶粒的合金。在中间退火步骤之后,可以执行冷轧工艺的第二步。在一些情况下,冷轧工艺的第二步包含使用单机架轧机或多机架轧机进行冷轧,其中入口温度范围为约20℃到约150℃。入口温度可以为例如约20℃、约30℃、约40℃、约50℃、约60℃、约70℃、约80℃、约90℃、约100℃、约110℃、约120℃、约130℃、约140℃或约150℃。在一些情况下,冷轧出口温度的范围可以为约80℃到约200℃。出口温度可以为例如约80℃、约90℃、约100℃、约110℃、约120℃、约130℃、约140℃、约150℃、约160℃、约170℃、约180℃、约190℃或约200℃,从而产生约3mm或更小(例如,约0.2mm到约2mm或约0.2mm到约1.4mm)的规格。例如,所得规格可以为约0.2mm、约0.3mm、约0.4mm、约0.5mm、约0.6mm、约0.7mm、约0.8mm、约0.9mm、约1mm、约1.1mm、约1.2mm、约1.3mm、约1.4mm、约1.5mm、约1.6mm、约1.7mm、约1.8mm、约1.9mm、约2mm、约2.1mm、约2.2mm、约2.3mm、约2.4mm、约2.5mm、约2.6mm、约2.7mm、约2.8mm、约2.9mm或约3mm。固溶化然后可以在固溶热处理步骤中将冷轧卷材固溶化。固溶化可以包含将最终规格的铝合金从室温加热至约520℃到约590℃(例如,约520℃到约580℃、约530℃到约570℃、约545℃到约575℃、约550℃到约570℃、约555℃到约565℃、约540℃到约560℃、约560℃到约580℃,或约550℃到约575℃)的温度。冷轧卷材可以在固溶化温度下浸泡一段时间。在某些方面,使冷轧卷材浸泡最多约2小时(例如,约1秒到约120分钟,包含端值)。例如,可以将冷轧卷材在约525℃到约590℃的固溶化温度下浸泡1秒、5秒、10秒、15秒、20秒、25秒、30秒、35秒、40秒、45秒、50秒、55秒、60秒、65秒、70秒、75秒、80秒、85秒、90秒、95秒、100秒、105秒、110秒、115秒、120秒、125秒、130秒、135秒、140秒、145秒、150秒、5分钟、10分钟、15分钟、20分钟、25分钟、30分钟、35分钟、40分钟、45分钟、50分钟、55分钟、60分钟、65分钟、70分钟、75分钟、80分钟、85分钟、90分钟、95分钟、100分钟、105分钟、110分钟、115分钟、或120分钟或介于这之间的任何时间。淬火在某些方面,然后可以在基于所选规格的淬火步骤中以可在约50℃/秒到400℃/秒之间变化的淬火速度将铝合金产品冷却至约35℃的温度。例如,淬火速率可以为约50℃/秒到约375℃/秒、约60℃/秒到约375℃/秒、约70℃/秒到约350℃/秒、约80℃/秒到约325℃/秒、约90℃/秒到约300℃/秒、约100℃/秒到约275℃/秒、约125℃/秒到约250℃/秒、约150℃/秒到约225℃/秒或约175℃/秒到约200℃/秒。可以使用液体(例如,水)、气体(例如,空气)或另一种所选择的淬火介质进行淬火步骤。预处理任选地,可以对本文所述的以及通过dc铸造或cc铸造并随后进行加工的铝合金产品进行预处理。碱洗本文所述的预处理工艺包含将清洗剂(在本文中也被称为入口清洗剂或预清洗剂)施加到铝合金产品的一个或多个表面的步骤。入口清洗剂从铝合金产品表面去除残余的油或松散粘附的氧化物。任选地,可以使用ph为7.5或更高的碱性溶液进行入口清洗。在一些情况下,碱性溶液的ph可以为约8、约8.5、约9、约9.5、约10、约10.5、约11、约11.5、约12、约12.5或约13。碱性溶液中碱性试剂的浓度可以为约1%到约5%(例如,按碱性溶液的体积计,约1%、约2%、约3%、约4%或约5%)。合适的碱性试剂包含例如硅酸盐和氢氧化物(例如,氢氧化钠)。碱性溶液可以进一步包含一种或多种表面活性剂,包含例如阴离子和非离子表面活性剂。酸蚀刻和冲洗本文所述的预处理工艺还可以包含蚀刻铝合金产品的表面的步骤。可以使用如酸蚀刻(即,包含ph小于7的酸溶液的蚀刻流程)、碱蚀刻(即,包含ph大于7的碱性溶液的蚀刻流程)或中性条件下的蚀刻(即,包括ph为7的中性溶液的蚀刻流程)等化学蚀刻来蚀刻铝合金产品的表面。化学蚀刻使表面准备好接受随后施加的预处理。在此步骤期间,可以充分去除任何松散粘附的氧化物(如al氧化物和富mg氧化物)、夹带的油或碎屑。用于进行酸蚀刻的示例性化学品包含硫酸、氢氟酸、硝酸、磷酸及其组合。用于进行碱蚀刻的示例性化学品包含氢氧化钠和氢氧化钾。在酸蚀刻步骤之后,可以用水性或有机溶剂冲洗铝合金产品的表面。施加预处理、冲洗和干燥然后可以对铝合金产品的表面施加预处理。任选地,预处理可以包含粘合促进剂、腐蚀抑制剂、偶联剂、抗微生物剂或其混合物。在施加预处理之后,可以任选地用溶剂(例如,水性或有机溶剂)冲洗铝合金产品的表面。可以在冲洗步骤后干燥铝合金产品的表面。使用方法本文所述的铝合金产品和方法可以用于汽车、电子和运输应用,如商用车辆、航空器或铁路应用。例如,铝合金产品可以用于底盘、横梁和底盘内组件(涵盖但不限于商用车辆底盘中两个c通道之间的所有组件),以增强强度,从而完全或部分替代高强度钢。在某些实例中,可以以f、t4、t6或t8x回火使用铝合金产品。在某些方面,铝合金产品和方法可以用于制备机动车车身部件产品。例如,所公开的铝合金产品和方法可以用于制备汽车车身部件,如保险杠、侧梁、顶梁、横梁、支柱增强件(例如,a支柱、b支柱和c支柱)、内面板、侧面板、底板、通道、结构板、加强板、内引擎罩或行李箱盖板。所公开的铝合金产品和方法还可以用于航空器或铁路车辆应用中,以制备例如外板和内板。本文所述的铝合金产品和方法还可以用于电子应用中,以制备例如外包装和内包装。例如,本文所述的铝合金产品和方法还可以用于制备电子装置(包含移动电话和平板计算机)的壳体。在一些实例中,铝合金产品可以用于制备移动电话(例如,智能手机)的外壳和平板电脑底部底盘的壳体。在某些方面,铝合金产品和方法可以用于制备航空航天机身部件产品。例如,所公开的铝合金产品和方法可以用于制备飞机机身部件,如蒙皮合金(skinalloy)。具有含磷表面的铝合金产品铝合金产品本文描述了具有期望的表面特性的铝合金产品,所述期望的表面特性包含用于某些粘结和接合应用(包含例如电阻点焊(被称为“rsw”))的最佳接触电阻特性。除其它组成特征外,本文所述的铝合金产品在铝合金产品的亚表面部分内含有一定浓度的残余元素。如本文所使用的,术语“亚表面”是指铝合金产品的从合金产品的外表面延伸到合金产品的内部最多约150μm深度的部分。任选地,亚表面是指合金产品的延伸到合金产品的内部至以下深度的部分:约0.01μm、约0.05μm、约0.1μm、约0.15μm、约0.2μm、约0.25μm、约0.3μm、约0.35μm、约0.4μm、约0.45μm、约0.5μm、约0.55μm、约0.6μm、约0.65μm、约0.7μm、约0.75μm、约0.8μm、约0.85μm、约0.9μm、约0.95μm、约1μm、约1.5μm、约2μm、约2.5μm、约3μm、约3.5μm、约4μm、约4.5μm、约5μm、约5.5μm、约6μm、约6.5μm、约7μm、约7.5μm、约8μm、约8.5μm、约9μm、约9.5μm、约10μm、约10.5μm、约11μm、约11.5μm、约12μm、约12.5μm、约13μm、约13.5μm、约14μm、约14.5μm、约15μm、约15.5μm、约16μm、约16.5μm、约17μm、约17.5μm、约18μm、约18.5μm、约19μm、约19.5μm、约20μm、约20.5μm、约21μm、约21.5μm、约22μm、约22.5μm、约23μm、约23.5μm、约24μm、约24.5μm、约25μm、约25.5μm、约26μm、约26.5μm、约27μm、约27.5μm、约28μm、约28.5μm、约29μm、约29.5μm、约30μm、约30.5μm、约31μm、约31.5μm、约32μm、约32.5μm、约33μm、约33.5μm、约34μm、约34.5μm、约35μm、约35.5μm、约36μm、约36.5μm、约37μm、约37.5μm、约38μm、约38.5μm、约39μm、约39.5μm、约40μm、约40.5μm、约41μm、约41.5μm、约42μm、约42.5μm、约43μm、约43.5μm、约44μm、约44.5μm、约45μm、约45.5μm、约46μm、约46.5μm、约47μm、约47.5μm、约48μm、约48.5μm、约49μm、约49.5μm、约50μm、约50.5μm、约51μm、约51.5μm、约52μm、约52.5μm、约53μm、约53.5μm、约54μm、约54.5μm、约55μm、约55.5μm、约56μm、约56.5μm、约57μm、约57.5μm、约58μm、约58.5μm、约59μm、约59.5μm、约60μm、约60.5μm、约61μm、约61.5μm、约62μm、约62.5μm、约63μm、约63.5μm、约64μm、约64.5μm、约65μm、约65.5μm、约66μm、约66.5μm、约67μm、约67.5μm、约68μm、约68.5μm、约69μm、约69.5μm、约70μm、约70.5μm、约71μm、约71.5μm、约72μm、约72.5μm、约73μm、约73.5μm、约74μm、约74.5μm、约75μm、约75.5μm、约76μm、约76.5μm、约77μm、约77.5μm、约78μm、约78.5μm、约79μm、约79.5μm、约80μm、约80.5μm、约81μm、约81.5μm、约82μm、约82.5μm、约83μm、约83.5μm、约84μm、约84.5μm、约85μm、约85.5μm、约86μm、约86.5μm、约87μm、约87.5μm、约88μm、约88.5μm、约89μm、约89.5μm、约90μm、约90.5μm、约91μm、约91.5μm、约92μm、约92.5μm、约93μm、约93.5μm、约94μm、约94.5μm、约95μm、约95.5μm、约96μm、约96.5μm、约97μm、约97.5μm、约98μm、约98.5μm、约99μm、约99.5μm、约100μm、约100.5μm、约101μm、约101.5μm、约102μm、约102.5μm、约103μm、约103.5μm、约104μm、约104.5μm、约105μm、约105.5μm、约106μm、约106.5μm、约107μm、约107.5μm、约108μm、约108.5μm、约109μm、约109.5μm、约110μm、约110.5μm、约111μm、约111.5μm、约112μm、约112.5μm、约113μm、约113.5μm、约114μm、约114.5μm、约115μm、约115.5μm、约116μm、约116.5μm、约117μm、约117.5μm、约118μm、约118.5μm、约119μm、约119.5μm、约120μm、约120.5μm、约121μm、约121.5μm、约122μm、约122.5μm、约123μm、约123.5μm、约124μm、约124.5μm、约125μm、约125.5μm、约126μm、约126.5μm、约127μm、约127.5μm、约128μm、约128.5μm、约129μm、约129.5μm、约130μm、约130.5μm、约131μm、约131.5μm、约132μm、约132.5μm、约133μm、约133.5μm、约134μm、约134.5μm、约135μm、约135.5μm、约136μm、约136.5μm、约137μm、约137.5μm、约138μm、约138.5μm、约139μm、约139.5μm、约140μm、约140.5μm、约141μm、约141.5μm、约142μm、约142.5μm、约143μm、约143.5μm、约144μm、约144.5μm、约145μm、约145.5μm、约146μm、约146.5μm、约147μm、约147.5μm、约148μm、约148.5μm、约149μm、约149.5μm、约150μm或介于这之间的任何深度。在一些实例中,亚表面从表面延伸到铝合金产品的内部约83μm的深度。在一些实例中,亚表面从表面延伸到铝合金产品的内部约5μm的深度。在一些实例中,亚表面从表面延伸到铝合金产品的内部约2μm的深度。铝合金产品的除亚表面部分之外的部分(例如,合金产品的剩余部分)在本文中被称为合金产品的本体。在一些方面,亚表面可以从合金产品的任何外表面延伸。例如,亚表面可以从铝合金产品的第一侧(例如,合金片材的顶部)、铝合金产品的第二侧(例如,合金片材的底部)、铝合金产品的第三侧(例如,合金片材的第一边缘)或铝合金产品的第四侧(例如,合金片材的第二边缘)延伸。如本文所使用的,术语“残余元素”是指即使在经受如下文进一步描述的某些生产和加工步骤之后仍保留在铝合金产品的亚表面部分内的元素。本文所述的残余元素包含例如p。在一些方面,p可以以元素p或氧化的p(例如,p的任何氧化态,包含-3、-2、-1、+1、+2、+3、+4或+5)的形式存在。氧化的p可以以例如五氧化二磷、三氧化二磷、一氧化二磷或四氧化二磷的形式存在于亚表面部分中。在一些非限制性实例中,元素p可以作为残余元素以约2at.%到约10at.%的量存在于亚表面内。例如,元素p可以以约2at.%、3at.%、4at.%、5at.%、6at.%、7at.%、8at.%、9at.%、10at.%或介于这之间的任何量存在。铝合金产品可以具有任何合适的组成。在一些实例中,铝合金产品可以由包含至少约0.001wt.%的镁(mg)的任何铝合金制备。例如,铝合金产品可以由包含约0.001wt.%到约10wt.%(例如,约0.01wt.%到约9wt.%、约0.05wt.%到约8wt.%或约0.1wt.%到约8wt.%)的mg的铝合金制备。任选地,用于本文所述的铝合金产品中的铝合金所包含的mg的量约为0.001wt.%、0.002wt.%、0.003wt.%、0.004wt.%、0.005wt.%、0.006wt.%、0.007wt.%、0.008wt.%、0.009wt.%、0.01wt.%、0.02wt.%、0.03wt.%、0.04wt.%、0.05wt.%、0.06wt.%、0.07wt.%、0.08wt.%、0.09wt.%、0.1wt.%、0.11wt.%、0.12wt.%、0.13wt.%、0.14wt.%、0.15wt.%、0.16wt.%、0.17wt.%、0.18wt.%、0.19wt.%、0.2wt.%、0.3wt.%、0.4wt.%、0.5wt.%、0.6wt.%、0.7wt.%、0.8wt.%、0.9wt.%、1.0wt.%、1.1wt.%、1.2wt.%、1.3wt.%、1.4wt.%、1.5wt.%、1.6wt.%、1.7wt.%、1.8wt.%、1.9wt.%、2.0wt.%、2.1wt.%、2.2wt.%、2.3wt.%、2.4wt.%、2.5wt.%、2.6wt.%、2.7wt.%、2.8wt.%、2.9wt.%、3.0wt.%、3.1wt.%、3.2wt.%、3.3wt.%、3.4wt.%、3.5wt.%、3.6wt.%、3.7wt.%、3.8wt.%、3.9wt.%、4.0wt.%、4.1wt.%、4.2wt.%、4.3wt.%、4.4wt.%、4.5wt.%、4.6wt.%、4.7wt.%、4.8wt.%、4.9wt.%、5.0wt.%、5.1wt.%、5.2wt.%、5.3wt.%、5.4wt.%、5.5wt.%、5.6wt.%、5.7wt.%、5.8wt.%、5.9wt.%、6.0wt.%、6.1wt.%、6.2wt.%、6.3wt.%、6.4wt.%、6.5wt.%、6.6wt.%、6.7wt.%、6.8wt.%、6.9wt.%、7.0wt.%、7.1wt.%、7.2wt.%、7.3wt.%、7.4wt.%、7.5wt.%、7.6wt.%、7.7wt.%、7.8wt.%、7.9wt.%、8.0wt.%、8.1wt.%、8.2wt.%、8.3wt.%、8.4wt.%、8.5wt.%、8.6wt.%、8.7wt.%、8.8wt.%、8.9wt.%、9.0wt.%、9.1wt.%、9.2wt.%、9.3wt.%、9.4wt.%、9.5wt.%、9.6wt.%、9.7wt.%、9.8wt.%、9.9wt.%或10.0wt.%。在非限制性实例中,铝合金产品可以包含5xxx系列铝合金、6xxx系列铝合金或7xxx系列铝合金。用作铝合金产品的合适的5xxx系列铝合金包含例如aa5005、aa5005a、aa5205、aa5305、aa5505、aa5605、aa5006、aa5106、aa5010、aa5110、aa5110a、aa5210、aa5310、aa5016、aa5017、aa5018、aa5018a、aa5019、aa5019a、aa5119、aa5119a、aa5021、aa5022、aa5023、aa5024、aa5026、aa5027、aa5028、aa5040、aa5140、aa5041、aa5042、aa5043、aa5049、aa5149、aa5249、aa5349、aa5449、aa5449a、aa5050、aa5050a、aa5050c、aa5150、aa5051、aa5051a、aa5151、aa5251、aa5251a、aa5351、aa5451、aa5052、aa5252、aa5352、aa5154、aa5154a、aa5154b、aa5154c、aa5254、aa5354、aa5454、aa5554、aa5654、aa5654a、aa5754、aa5854、aa5954、aa5056、aa5356、aa5356a、aa5456、aa5456a、aa5456b、aa5556、aa5556a、aa5556b、aa5556c、aa5257、aa5457、aa5557、aa5657、aa5058、aa5059、aa5070、aa5180、aa5180a、aa5082、aa5182、aa5083、aa5183、aa5183a、aa5283、aa5283a、aa5283b、aa5383、aa5483、aa5086、aa5186、aa5087、aa5187或aa5088。用作铝合金产品的合适的6xxx系列铝合金包含例如aa6101、aa6101a、aa6101b、aa6201、aa6201a、aa6401、aa6501、aa6002、aa6003、aa6103、aa6005、aa6005a、aa6005b、aa6005c、aa6105、aa6205、aa6305、aa6006、aa6106、aa6206、aa6306、aa6008、aa6009、aa6010、aa6110、aa6110a、aa6011、aa6111、aa6012、aa6012a、aa6013、aa6113、aa6014、aa6015、aa6016、aa6016a、aa6116、aa6018、aa6019、aa6020、aa6021、aa6022、aa6023、aa6024、aa6025、aa6026、aa6027、aa6028、aa6031、aa6032、aa6033、aa6040、aa6041、aa6042、aa6043、aa6151、aa6351、aa6351a、aa6451、aa6951、aa6053、aa6055、aa6056、aa6156、aa6060、aa6160、aa6260、aa6360、aa6460、aa6460b、aa6560、aa6660、aa6061、aa6061a、aa6261、aa6361、aa6162、aa6262、aa6262a、aa6063、aa6063a、aa6463、aa6463a、aa6763、a6963、aa6064、aa6064a、aa6065、aa6066、aa6068、aa6069、aa6070、aa6081、aa6181、aa6181a、aa6082、aa6082a、aa6182、aa6091和aa6092。用作铝合金产品的合适的7xxx系列合金包含例如aa7003、aa7004、aa7204、aa7005、aa7108、aa7108a、aa7009、aa7010、aa7012、aa7014、aa7015、aa7016、aa7116、aa7017、aa7018、aa7019、aa7019a、aa7020、aa7021、aa7022、aa7122、aa7023、aa7024、aa7025、aa7026、aa7028、aa7029、aa7129、aa7229、aa7030、aa7031、aa7032、aa7033、aa7034、aa7035、aa7035a、aa7036、aa7136、aa7037、aa7039、aa7040、aa7140、aa7041、aa7042、aa7046、aa7046a、aa7047、aa7049、aa7049a、aa7149、aa7249、aa7349、aa7449、aa7050、aa7050a、aa7150、aa7055、aa7155、aa7255、aa7056、aa7060、aa7064、aa7065、aa7068、aa7168、aa7072、aa7075、aa7175、aa7475、aa7076、aa7178、aa7278、aa7278a、aa7081、aa7181、aa7085、aa7185、aa7090、aa7093、aa7095、aa7099和aa7199。尽管全文描述了铝合金产品,但是所述方法和产品适用于任何金属。在一些实例中,金属产品为铝、铝合金、镁、镁基材料、钛、钛基材料、铜、铜基材料、钢、钢基材料、青铜、青铜基材料、黄铜、黄铜基材料、复合材料、复合材料中使用的片材或任何其它合适的金属或材料组合。产品可以包含整体材料,以及非整体材料,如辊压粘结材料、包层材料、复合材料(如,但不限于含碳纤维的材料)或各种其它材料。在一些实例中,金属产品是金属卷材、金属带、金属板、金属片材、金属坯料、金属铸锭等。在某些实例中,本文所述的合金元素和/或其氧化物可以扩散到整个合金产品中,使得所述合金元素和/或其氧化物的浓度贯穿铝合金产品的全厚度(例如,铝合金的本体)分布(即,至少在亚表面和本体部分内)。例如,铝合金产品可以包含一定浓度的mg和/或mgo,所述mg和/或mgo分布在整个铝合金产品中并且可以在各个加工步骤(包含均质化、热轧、冷轧和固溶化)期间迁移到亚表面部分。在其它情况下,所述浓度的p和mg和/或mgo可以提供至少一部分适合rsw的亚表面。在一些情况下,可以针对rsw优化亚表面的接触电阻。在一些非限制性实例中,优化的接触电阻可以减小在rsw电极的至少一个尖端和/或整个电极上的电子应力(例如,焦耳加热)。在一些实例中,由于热增强的失效机制(包含腐蚀、疲劳、断裂或其任何组合),增加的接触电阻可以导致电极和/或尖端的焦耳加热增加,并加速电极和/或尖端的失效。因此,提供优化的接触电阻可以减慢电极和/或尖端的失效,并使rsw电极的使用寿命大于工业上的当前需求,例如,至少约80个焊接周期。例如,rsw电极和/或尖端可以经受至少约85个焊接周期、至少约90个焊接周期、至少约95个焊接周期或至少约100个焊接周期。在一些情况下,铝合金产品的亚表面内存在的较高浓度的mgo可以缩短rsw电极的使用寿命。然而,当用含p化合物(例如,磷酸)蚀刻和/或清洗铝合金时,可以增加rsw电极的使用寿命。因此,在一些非限制性实例中,向铝合金产品的亚表面部分提供一定浓度的残余p可以提高rsw电极的使用寿命。另外,存在于铝合金产品的表面处的p可以使表面稳定。在一些情况下,存在于表面处和/或亚表面中的p和mg可以形成磷酸镁(mgpo4)、磷酸二镁(mghpo4)、磷酸三镁(mg3(po4)2)、磷化镁(mg3p2)、亚磷酸镁(mg3(po3)2)、磷酸二氢镁(mg(h2po4)2)、任何合适的mg-p化合物或其任何组合。在表面处和/或在亚表面中形成mg-p化合物可以降低mgo的浓度,使表面稳定,从而延长rsw电极的使用寿命(参见图1,在下文中进行详细描述)。在一些实例中,用含p的蚀刻剂(例如,磷酸和硫酸的混合物(h3po4/h2so4))蚀刻铝合金产品的表面可以通过(i)去除mgo和/或(ii)促进mg-p化合物的形成来降低表面处和/或亚表面中的mgo浓度。因此,与不使用含p蚀刻剂进行蚀刻相比,用含p蚀刻剂进行蚀刻进一步降低了mgo浓度。在一些方面,如本文所述的降低mgo浓度可以如上所述延长rsw电极的使用寿命(例如,经受至少约100个焊接周期)。在一些非限制性实例中,h3po4/h2so4混合物中的硫酸可以溶解表面处和/或亚表面中的mgo、氢氧化镁(mg(oh)2)、氧化铝(al2o3)和/或氢氧化铝(al(oh)3)。另外,h3po4/h2so4混合物中的磷酸可以与mgo和mg(oh)2络合,并根据下式形成各种mg-p化合物:mgo+2h3po4→mg(h2po4)2+h2o;等式(i)mgo+h2po4→mgpo4+h2o;等式(ii)3mg(oh)2+2h3po4→mg3(po4)2+6h2o;等式(iii)3mg+h3po4→mg3(po4)2+h2(g);等式(iv)铝合金产品中p和mg的原子浓度根据铝合金产品中的特定位置(例如,深度)以及制备、加工和处理铝合金产品的方法而变化。另外,铝合金产品中的铝合金材料包括来自如上所述的蚀刻的p。可以使用如本领域普通技术人员已知的技术(包含x射线光电子能谱(xps))来测量p和mg的原子浓度(例如,p/mg)。p和mg例如可以存在于铝合金产品的表面处和/或亚表面中。铝合金产品的表面处和/或亚表面中的p与mg的原子浓度比可以具有任何合适的值,所述值的范围通常为约0.001到约10(例如,约0.005到约9、约0.01到约8、约0.05到约7、约0.1到约6、约0.1到约5、约0.15到约5.5、约0.2到约5、约0.25到约4.5、约0.5到约4、约0.75到约3.5、约1到约3、约1.25到约2.5或约1.5到约2)。例如,铝合金产品的表面处和/或亚表面中的p与mg的原子浓度比可以为约0.001、约0.002、约0.003、约0.004、约0.005、约0.006、约0.007、约0.008、约0.009、约0.01、约0.02、约0.03、约0.04、约0.05、约0.06、约0.07、约0.08、约0.09、约0.1、约0.2、约0.3、约0.4、约0.5、约0.6、约0.7、约0.8、约0.9、约1、约1.1、约1.2、约1.3、约1.4、约1.5、约1.6、约1.7、约1.8、约1.9、约2、约2.1、约2.2、约2.3、约2.4、约2.5、约2.6、约2.7、约2.8、约2.9、约3、约3.1、约3.2、约3.3、约3.4、约3.5、约3.6、约3.7、约3.8、约3.9、约4、约4.1、约4.2、约4.3、约4.4、约4.5、约4.6、约4.7、约4.8、约4.9、约5、约5.1、约5.2、约5.3、约5.4、约5.5、约5.6、约5.7、约5.8、约5.9、约6、约6.1、约6.2、约6.3、约6.4、约6.5、约6.6、约6.7、约6.8、约6.9、约7、约7.1、约7.2、约7.3、约7.4、约7.5、约7.6、约7.7、约7.8、约7.9、约8、约8.1、约8.2、约8.3、约8.4、约8.5、约8.6、约8.7、约8.8、约8.9、约9、约9.1、约9.2、约9.3、约9.4、约9.5、约9.6、约9.7、约9.8、约9.9或约10。可以通过分别取表面处或亚表面中的p与mg的原子浓度(例如,p/mg)的简单比来计算表面处或亚表面中的p与mg的原子浓度比,其中使用例如上述xps来测量浓度。在一些实例中,等式(i)可以提供约为2的p/mg比,等式(ii)可以提供约为1的p/mg比,并且等式(iii)和/或等式(iv)可以提供约为0.75的p/mg比。在一些非限制性实例中,在从表面延伸约83μm的亚表面中,p/mg的原子浓度比为约0.6到约0.7。黄度指数(被称为“yi”)可以指示电阻点焊铝合金的最佳表面化学。yi是存在于铝合金的至少一部分表面上的氧化镁(mgo)的浓度的结果,从而导致铝合金具有黄色外观。任选地,yi为至少15(例如,至少约18、至少约20或至少约22)。根据astm标准e313测量yi。本文所述的铝合金产品可以具有任何合适的规格。例如,铝合金产品可以为规格介于约0.5mm与约50mm之间(例如,约0.5mm、约1mm、约2mm、约3mm、约4mm、约5mm、约6mm、约7mm、约8mm、约9mm、约10mm、约15mm、约20mm、约25mm、约30mm、约35mm、约40mm、约50mm或介于这之间的任何规格)的铝合金板、铝合金沙特板或铝合金片材。本文所述的铝合金产品可以具有适合于根据任何合适的粘结技术(包含例如电阻点焊)成功粘结的表面粗糙度。本文所述的铝合金产品可以具有约25纳米(nm)到约50nm的平均表面粗糙度。例如,本文所述的铝合金产品的表面粗糙度可以为约25nm、约26nm、约27nm、约28nm、约29nm、约30nm、约31nm、约32nm、约33nm、约34nm、约35nm、约36nm、约37nm、约38nm、约39nm、约40nm、约41nm、约42nm、约43nm、约44nm、约45nm、约46nm、约47nm、约48nm、约49nm、约50nm或介于这之间的任何表面粗糙度。制备合金产品的方法在某些方面,可以使用如本文所述的方法制备本文所述的铝合金产品。在不旨在限制范围的情况下,铝合金产品的特性部分地由某些组成特征在产品制备期间的形成来确定。如下文所描述的,某些加工步骤和条件(包含蚀刻步骤和条件)提供上文描述的铝合金产品,所述铝合金产品具有期望的粘结耐久特性,并且具体地说,降低电阻点焊(rsw)设备的电极尖端上电子应力并从而延长rsw电极的使用寿命所需的最佳表面化学和/或接触电阻。可以通过任何合适的方法铸造本文所述的任何合适的铝合金(即,含有至少一定量的cu),从而产生铸造产品。在一些实例中,可以使用直接冷激(dc)铸造工艺来铸造合金,从而形成铝合金铸锭。在一些实例中,可以使用连续铸造(cc)工艺来铸造合金,所述连续铸造工艺可以包含但不限于使用双带式铸造机、双辊式铸造机或块式铸造机,从而形成坯料、板坯、沙特板、条带等形式的铸造产品。然后,可以基于用于制备产品的特定铝合金系列,对铸造产品进行加工步骤,所述加工步骤包含但不限于均质化、热轧、冷轧、固溶热处理、淬火和/或时效。在加工之后,铝合金产品可以经历如下文进一步描述的表面制备步骤。表面制备可以对本文所述的以及通过dc铸造或cc或以其它方式铸造并随后进行加工的铝合金产品进行下文所描述的表面制备工艺。清洗任选地,本文所述的表面制备工艺包含将清洗剂(在本文中也被称为入口清洗剂或预清洗剂)施加到铝合金产品的一个或多个表面的步骤。入口清洗剂从铝合金产品表面去除残余的油或松散粘附的氧化物。任选地,可以使用ph为7.5或更高的碱性溶液进行入口清洗。在一些情况下,碱性溶液的ph可以为约8、约8.5、约9、约9.5、约10、约10.5、约11、约11.5、约12、约12.5或约13。碱性溶液中碱性试剂的浓度可以为约1%到约5%(例如,按碱性溶液的体积计,约1%、约2%、约3%、约4%或约5%)。合适的碱性试剂包含例如硅酸盐和氢氧化物(例如,氢氧化钠)。碱性溶液可以进一步包含一种或多种表面活性剂,包含例如阴离子和非离子表面活性剂。蚀刻所述预处理工艺包含蚀刻铝合金产品的表面的步骤。可以使用酸蚀刻(即,包含酸性溶液的蚀刻流程)来蚀刻铝合金产品的表面。蚀刻步骤将p沉积在铝合金产品的亚表面部分内。另外,蚀刻步骤使表面准备好接受随后施加的预处理。在此步骤期间,应充分去除任何松散粘附的氧化物(如al氧化物和富mg氧化物)、夹带的油或碎屑。使用包含至少一种含p化合物的蚀刻溶液来进行蚀刻步骤。在一些实例中,用于蚀刻溶液的合适的含p化合物包含磷酸、膦酸、次膦酸、任何其它含p的酸及其组合。例如,含p化合物可以包含磷酸(h3po4)。任选地,蚀刻溶液可以包含一种或多种另外的酸,包含硫酸、氢氟酸、乙酸和/或盐酸。在一些实例中,蚀刻溶液包含磷酸和硫酸的混合物。在一些情况下,混合物包含的磷酸与硫酸之比为约3到约5。例如,磷酸与硫酸之比可以为约3、约3.1、约3.2、约3.3、约3.4、约3.5、约3.6、约3.7、约3.8、约3.9、约4、约4.1、约4.2、约4.3、约4.4、约4.5、约4.6、约4.7、约4.8、约4.9或约5。如上文所描述的,蚀刻步骤将残余元素浓度(例如,p)沉积在铝合金产品的亚表面部分内。在一些实例中,蚀刻步骤将至少约2at.%到约10at.%的p沉积在铝合金产品的亚表面部分内。p的这种沉积和随后的氧化可以优化用于rsw的亚表面部分的接触电阻。在一些另外的实例中,优化接触电阻可以减少rsw电极上的电子应力,从而将rsw电极的使用寿命延长到超出当前的工业需求。蚀刻后冲洗在蚀刻步骤之后,可以用溶剂冲洗铝合金产品的表面。任选地,溶剂可以是水溶液,如去离子(di)水或反渗透(ro)水。施加预处理任选地,然后可以对铝合金产品的表面施加预处理。合适的预处理包含例如粘合促进剂和腐蚀抑制剂。可以在本领域已知的任何合适的温度下施加预处理。施加预处理会在铝合金产品的表面上产生预处理的薄层。在施加预处理之后,可以如本领域中已知的那样冲洗和/或干燥铝合金产品的表面。使用方法本文所述的铝合金产品和方法可以用于汽车、电子和运输应用,如商用车辆、航空器或铁路应用或任何其它合适的应用。例如,铝合金产品可以用于底盘、横梁和底盘内组件(涵盖但不限于商用车辆底盘中两个c通道之间的所有组件),以增强强度,从而完全或部分替代高强度钢。在某些实例中,可以以f、o、t4、t6或t8x回火使用铝合金产品。在某些方面,铝合金产品和方法可以用于制备机动车车身部件产品。例如,所公开的铝合金产品和方法可以用于制备汽车车身部件,如保险杠、侧梁、顶梁、横梁、支柱增强件(例如,a支柱、b支柱和c支柱)、内面板、侧面板、底板、通道、结构板、加强板、内引擎罩或行李箱盖板。所公开的铝合金产品和方法还可以用于航空器或铁路车辆应用中,以制备例如外板和内板。本文所述的铝合金产品和方法还可以用于电子应用中,以制备例如外包装和内包装。例如,本文所述的铝合金产品和方法还可以用于制备电子装置(包含移动电话和平板计算机)的壳体。在一些实例中,铝合金产品可以用于制备移动电话(例如,智能手机)的外壳和平板电脑底部底盘的壳体。在某些方面,铝合金产品和方法可以用于制备航空航天机身部件产品。例如,所公开的铝合金产品和方法可以用于制备飞机机身部件,如蒙皮合金(skinalloy)。说明说明1是一种铝合金产品,其包括:迁移元素;亚表面部分,所述亚表面部分具有一定浓度的所述迁移元素;以及本体部分,所述本体部分具有一定浓度的所述迁移元素,其中所述铝合金产品包括4.0或更小的富集比,其中所述富集比是所述亚表面部分中的所述迁移元素的所述浓度与所述本体部分中的所述迁移元素的所述浓度之比。说明2是根据任何前一或后一说明所述的铝合金产品,其中所述迁移元素包括zn、cu、mg或si中的至少一种。说明3是根据任何前一或后一说明所述的铝合金产品,其中所述亚表面部分包括从所述铝合金产品的表面到约5μm深度的区域。说明4是根据任何前一或后一说明所述的铝合金产品,其中所述亚表面部分包括从所述铝合金产品的表面到约2μm深度的区域。说明5是根据任何前一或后一说明所述的铝合金产品,其中所述富集比为2.0或更小。说明6是根据任何前一或后一说明所述的铝合金产品,其中所述富集比为1.5或更小。说明7是根据任何前一或后一说明所述的铝合金产品,其中所述富集比为1.0。说明8是根据任何前一或后一说明所述的铝合金产品,其中所述铝合金产品包括7xxx系列铝合金、6xxx系列铝合金、5xxx系列铝合金或2xxx系列铝合金。说明9是一种生产根据任何前一或后一说明所述的铝合金产品的方法,所述方法包括:铸造包括迁移元素的铝合金以产生铸造铝合金制品;轧制所述铸造铝合金制品以提供经过轧制的铝合金制品;以及对所述经过轧制的铝合金制品进行热处理以形成铝合金产品,其中所述迁移元素分布在所述铝合金产品的亚表面部分和本体部分内,从而提供4.0或更低的富集比,其中所述富集比是所述亚表面部分中的所述迁移元素的所述浓度与所述本体部分中的所述迁移元素的所述浓度之比。说明10是根据任何前一或后一说明所述的方法,其中所述轧制步骤在约200℃到约550℃的温度下进行。说明11是根据任何前以或后一说明所述的方法,其中所述热处理步骤在约400℃到约580℃的温度下进行。说明12是根据任何前一或后一说明所述的方法,其中所述热处理步骤进行约120秒或更短。说明13是根据任何前一或后一说明所述的方法,所述方法进一步包括对所述铸造铝合金产品进行预处理。说明14是根据任何前一或后一说明所述的方法,其中所述预处理包括清洗所述铸造铝合金产品的表面、蚀刻所述铸造铝合金产品的所述表面以及对所述铸造铝合金产品的所述表面施加预处理。说明15是根据任何前一或后一说明所述的方法,其中所述预处理在热处理步骤之后进行。说明16是根据任何前一或后一说明所述的方法,其中所述铸造包括直接冷激铸造。说明17是根据任何前一或后一说明所述的方法,其中所述铸造包括连续铸造。说明18是一种铝合金产品,其包括:亚表面部分,所述亚表面部分具有一定浓度的迁移元素;以及本体部分,所述本体部分具有一定浓度的所述迁移元素,其中所述亚表面部分中的所述迁移元素的所述浓度高于所述本体部分中的所述迁移元素的所述浓度。说明19是根据任何前一或后一说明所述的铝合金产品,其中所述迁移元素包括cu、mn、cr和/或fe。说明20是根据任何前一或后一说明所述的铝合金产品,其中所述铝合金产品包括6xxx系列铝合金或5xxx系列铝合金。说明21是根据任何前一或后一说明所述的铝合金产品,其包括亚表面部分和本体部分,其中所述亚表面部分包括p。说明22是根据任何前一或后一说明所述的铝合金产品,其中所述p以元素p、五氧化二磷、三氧化二磷、一氧化二磷或四氧化二磷中的至少一种形式存在于所述亚表面部分中。说明23是根据任何前一或后一说明所述的铝合金产品,其中所述亚表面部分包括的p的量为约2at.%到约10at.%。说明24是根据任何前一或后一说明所述的铝合金产品,其中所述亚表面部分包括从所述铝合金产品的表面到约150μm深度的区域。说明25是根据任何前一或后一说明所述的铝合金产品,其中所述亚表面部分包括从所述铝合金产品的表面到约83μm深度的区域。说明26是根据任何前一或后一说明所述的铝合金产品,其中所述铝合金产品包括大于约15的黄度指数。说明27是根据任何前一或后一说明所述的铝合金产品,其中所述黄度指数大于约20。说明28是一种对根据任何前一或后一说明所述的铝合金产品的表面进行处理的方法,所述方法包括:提供具有亚表面部分和本体部分的铝合金产品;以及用包括含p化合物的蚀刻溶液蚀刻所述铝合金产品的表面。说明29是根据任何前一或后一说明所述的方法,其中所述提供步骤包括提供包括至少约0.001wt.%的mg的铝合金产品。说明30是根据任何前一或后一说明所述的方法,其中所述提供步骤包括提供包括约0.001wt.%到约10wt.%的mg的铝合金产品。说明31是根据任何前一或后一说明所述的方法,其中所述提供步骤包括提供包括5xxx系列铝合金、6xxx系列铝合金或7xxx系列铝合金的铝合金产品。说明32是根据任何前一或后一说明所述的方法,其中所述含p化合物包括磷酸、膦酸、次膦酸及其组合。说明33是根据任何前一或后一说明所述的方法,其中所述蚀刻溶液进一步包括一种或多种另外的酸。说明34是根据任何前一或后一说明所述的方法,其中所述一种或多种另外的酸包括硫酸、氢氟酸、乙酸和/或盐酸。说明35是根据任何前一或后一说明所述的方法,其中所述蚀刻溶液包括磷酸和硫酸。说明36是根据任何前一或后一说明所述的方法,其中磷酸与硫酸之比为约3到约5。说明37是根据任何前一或后一说明所述的方法,其中蚀刻所述铝合金产品的所述表面使所述铝合金产品的所述表面上的mg暴露。说明38是根据任何前一或后一说明所述的方法,其中使mg暴露包括形成磷酸镁、磷化镁、亚磷酸镁或其任何组合。说明39是根据任何前一或后一说明所述的方法,其中形成磷酸镁、磷化镁、亚磷酸镁或其任何组合包括在所述亚表面部分中提供0.001到10的p与mg的原子浓度比。说明40是根据任何前一或后一说明所述的方法制备的铝合金产品,其中所述铝合金产品包括机动车车身部件、航空航天机身部件、运输车身部件、船用车身部件、机动车面板、航空航天蒙皮面板、船用面板、电子装置外壳、建筑结构性部件或建筑美学面板。以下实例将用来进一步说明本发明,但是同时不对本发明构成任何限制。相反,应清楚地理解,在不脱离本发明的精神的情况下,可以借助本领域技术人员在阅读本文的描述之后可以想到的各个实施例、其修改和等效物。除非另有说明,否则在以下实例中描述的研究期间,遵循常规程序。以下出于说明性目的对一些流程进行了描述。实例实例1:通过溶解控制迁移元素浓度通过直接冷激铸造制备两个6xxx系列铝合金样品,并通过均质化、热轧、冷轧、固溶热处理、空气淬火、使用7%的r243进行蚀刻以及用粘合促进剂进行预处理来加工所述样品。加工方法仅固溶热处理步骤不同。将第一合金样品在540℃下固溶热处理1秒(方法1),并且将第二合金样品在578℃下固溶热处理35秒(方法2)。图4呈现了根据方法1制备的样品中的mg含量(由方形符号表示)、根据方法2制备的样品中的mg含量(由三角形符号表示)以及未经过固溶热处理的对比6xxx系列铝合金中的mg含量(“aa6xxx;”由圆圈符号表示)的x射线光电子能谱(xps)深度分布数据。在图4中显而易见的是控制亚表面中的迁移mg浓度并提供贯穿铝合金产品的均匀的mg浓度的能力。与对比6xxx系列铝合金相比,方法1提供了从铝合金的表面到本体的更均匀的mg浓度,并且mg含量更高。方法2提供了更靠近铝合金表面的较高的mg含量和铝合金本体中的较低的mg含量,并且与根据方法1制备的示例性铝合金和对比6xxx系列铝合金相比,提供了更高的mg含量。对比6xxx系列铝合金展现出从铝合金的表面到本体的高度均匀的mg浓度,以及铝合金的表面附近的较低的总mg含量。图5呈现了根据方法1制备的铝合金产品中的si含量(由方形符号表示)、根据方法2制备的铝合金产品中的si含量(由三角形符号表示)以及未经过固溶热处理的对比6xxx系列铝合金中的si含量(由圆圈符号表示)的xps深度分布数据。在图5中显而易见的是控制本体铝合金中的迁移硅(si)浓度并提供深入铝合金本体中的均匀的硅浓度的能力。方法1提供了更靠近铝合金表面的较高的si含量和铝合金本体中的较低的si含量。方法2提供了铝合金的表面附近的较高的si含量和进一步深入铝合金本体中的更均匀的si浓度。方法2合金产品的si含量高于对比6xxx系列铝合金产品的si含量。对比6xxx系列铝合金展现出从铝合金的表面到本体的高度均匀且非常低的si浓度,以及铝合金的表面附近的较低的总si含量。图6示出了根据本文所述方法制备的铝合金的粘结耐久性测试结果。将根据方法1和方法2制备的示例性铝合金样品粘结在一起并进行应力耐久性测试。在应力耐久性测试中,通过螺栓将一组6个搭接接头/粘结件按顺序连接,并竖直放置在90%相对湿度(rh)的湿度箱中。将温度维持在50℃。对粘结工序施加2.4kn的力负荷。应力耐久性测试是周期性暴露测试,所述测试最多进行45个周期。每个周期持续24小时。在每个周期中,将粘结件在湿度箱中暴露22小时,然后浸入5%的nacl中持续15分钟,并且最后空气干燥105分钟。当三个接头断裂时,针对特定接头组的测试中止,并且指示为首次失效。根据方法2(左侧组直方图)制备的示例性铝合金展现出更低的失效周期数目,这指示与根据方法1(右侧组直方图)制备的示例性铝合金相比,粘结耐久性更低。失效的平均周期由每组中的左直方图(阴影直方图)指示,而第一次观察到的失效由每组中的右直方图(交叉影线)指示。实例2:通过热轧控制迁移元素浓度通过直接冷激铸造制备两个6xxx系列铝合金样品,并通过均质化、热轧、冷轧、固溶热处理、空气淬火、使用7%的r243进行蚀刻以及用粘合促进剂进行预处理来加工所述样品。加工方法仅热轧温度不同。将第一合金样品在390℃的热轧机出口温度下热轧(方法1),并且将第二合金样品在330℃的热轧机出口温度下热轧(方法2)。图7示出了由高温(方法1)轧制的表面制备的铝合金产品中的mg含量与由低温(方法2)轧制的表面制备的铝合金产品中的mg含量的xps深度分布图。根据方法1制备的铝合金样品在铝合金亚表面内展现出2的富集比和10%的mg浓度。根据方法2制备的铝合金在铝合金亚表面内展现出1.6的富集比和5%的mg浓度。实例3:通过清洗工序控制迁移元素浓度通过直接冷激铸造制备两个6xxx系列铝合金样品,并通过均质化、热轧、冷轧、固溶热处理、空气淬火、使用7%的r243进行蚀刻以及用粘合促进剂进行预处理来加工所述样品。加工方法仅在清洗步骤的顺序上不同。在固溶热处理之前对第一合金样品进行预清洗(被称为“预清洗→sht”),并且对第二合金样品进行固溶热处理然后进行预清洗(被称为“sht→预清洗”)。两者之后都进行酸蚀刻和预处理。图8呈现了铝合金样品中mg含量的xps深度分布数据。在固溶化之前进行清洗(被称为“预清洗→sht”)的示例性铝合金显示出6%的mg浓度和2.4的富集比。在固溶化之后进行清洗(被称为“sht→预清洗”)的示例性铝合金显示出1.5%的mg浓度和0.7的富集比。实例4:控制连续铸造铝合金中的迁移元素浓度根据如上所述的连续铸造方法制备铝合金产品。以1450mm的宽度铸造产品,并修整到1300mm。然后将产品热轧,冷轧至5.1mm,在400℃下退火2小时,并冷轧至2mm。然后将产品固溶化并在不同条件下淬火,如表1所示。表1样品id固溶化温度淬火方法连续铸造条件1(c1)553℃空气连续铸造条件2(c2)553℃水连续铸造条件3(c3)544℃水连续铸造条件4(c4)560℃空气直接冷激铸造条件(d1)560℃空气通过辉光放电光发射能谱(gdoes)分析铝合金片材的表面。分析了镁(mg)、硅(si)、铜(cu)、锰(mn)、铬(cr)和铁(fe)的量。从表面到2.0μm的深度进行测量。示例性连续铸造铝合金片材被称为“c1”、“c2”、“c3”和“c4”。用粘合促进剂对所有样品进行预处理(由“pt”指示)。铝合金片材的第一表面(例如,与铸造机的皮带接触的表面)由“标记”指示。第二分析表面(例如,与铸造机的皮带不接触的表面)由“未标记”指示。出于连铸铝合金的比较和有效性目的,分析了对比dc铸造铝合金(被称为“d1”),以实现铝合金片材的表面的受控富集。图9a和9b示出了铝合金片材的表面附近(例如,从表面到2.0μm的深度)的mg含量的gdoes数据。图9a示出了延伸到铝合金片材的本体中的mg含量的数据。图9b示出了被认为在铝合金片材的表面中(例如,从表面到0.5μm的深度)发现的mg含量的数据。图9a和9b示出了mg向通过直接冷激铸造产生的铝合金片材(样品d1和d1-lab)的表面的高扩散。图9a和9b示出了mg向铝合金片材的表面的扩散减少以及mg从铝合金片材的表面到本体中的均匀分布,所述铝合金片材通过上文描述的示例性连续铸造方法产生。对于粘结和接合应用,期望铝合金片材的表面附近的mg浓度较低。图10a和10b示出了铝合金片材的表面附近(例如,从表面到2.0μm的深度)的si含量的gdoes数据。图10a示出了延伸到铝合金片材的本体中的si含量的数据。图10b示出了被认为在铝合金片材的表面中(例如,从表面到0.5μm的深度)发现的si含量的数据。图10a和10b示出了si向通过直接冷激铸造产生的铝合金片材(样品d1和d1-lab)的表面的高扩散。图10a和10b示出了si向铝合金片材的表面的扩散减少以及si从铝合金片材的表面到本体中的均匀分布,所述铝合金片材通过上文描述的示例性连续铸造方法产生。图11a和11b示出了铝合金片材的表面附近(例如,从表面到2.0μm的深度)的cu含量的gdoes数据。图11a示出了延伸到铝合金片材的本体中的cu含量的数据。图11b示出了被认为在铝合金片材的表面中(例如,从表面到0.5μm的深度)发现的cu含量的数据。图11a和11b示出了cu向通过直接冷激铸造产生的铝合金片材(样品d1和d1-lab)的表面的低扩散。图11a和11b示出了cu向通过上文描述的示例性连续铸造方法产生的铝合金片材的表面的扩散增加。对于粘结和接合应用,可以期望cu向铝合金片材的表面受控地扩散。图12a和12b示出了铝合金片材的表面附近(例如,从表面到2.0μm的深度)的mn含量的gdoes数据。图12a示出了延伸到铝合金片材的本体中的mn含量的数据。图12b示出了被认为在铝合金片材的表面中(例如,从表面到0.5μm的深度)发现的mn含量的数据。图12a和12b示出了mn没有扩散到通过直接冷激铸造产生的铝合金片材(样品d1和d1-lab)的表面。图12a和12b示出了mn向通过上文描述的示例性连续铸造方法产生的铝合金片材的表面的扩散增加。图13a和13b示出了铝合金片材的表面附近(例如,从表面到2.0μm的深度)的cr含量的gdoes数据。图13a示出了延伸到铝合金片材的本体中的cr含量的数据。图13b示出了被认为在铝合金片材的表面中(例如,从表面到0.5μm的深度)发现的cr含量的数据。图13a和13b示出了cr没有扩散到通过直接冷激铸造产生的铝合金片材(样品d1和d1-lab)的表面。图13a和13b示出了cr向通过上文描述的示例性连续铸造方法产生的铝合金片材的表面的扩散增加。对于粘结和接合应用,可以期望cr向铝合金片材的表面受控地扩散。对于耐腐蚀性,可以期望cr向铝合金片材的表面受控地扩散。图14a和14b示出了铝合金片材的表面附近(例如,从表面到2.0μm的深度)的fe含量的gdoes数据。图14a示出了延伸到铝合金片材的本体中的fe含量的数据。图14b示出了被认为在铝合金片材的表面中(例如,从表面到0.5μm的深度)发现的fe含量的数据。图14a和14b示出了fe没有扩散到通过直接冷激铸造产生的铝合金片材(样品d1和d1-lab)的表面。图14a和14b示出了fe向通过上文描述的示例性连续铸造方法产生的铝合金片材的表面的扩散增加。根据实例2中所述的流程,进行了针对示例性连续铸造铝合金片材和对比直接冷激铸造铝合金片材的粘结耐久性测试结果。对于此实验,45个周期的完成指示接头组通过了粘结耐久性测试。测试结果在下表2中示出。在表2中,每个接头从1到6编号,其中当竖直朝向时,接头1为顶部接头而接头6为底部接头。单元格中的数字(除“45”外)指示在断裂之前的成功周期的数目。单元格中的数字“45”指示接头在45个周期中保持完整。结果汇总于下表2中:表2对于试验1、2和3,从示例性连续铸造铝合金片材上切下测试试片。对测试试片进行碱蚀刻和酸蚀刻,以清洗并准备用于粘结的表面。通过用粘合促进剂对铝合金片材进行预处理并用粘合剂粘结测试试片来进行粘结。将粘结的测试试片暴露在潮湿的环境中,持续最多45个工作周期。对于试验4,从示例性连续铸造铝合金片材上切下测试试片。对测试试片进行强碱清洗和强酸蚀刻,以清洗并准备用于粘结的表面。通过用粘合促进剂对铝合金片材进行预处理并用粘合剂粘结测试试片来进行粘结。将粘结的测试试片暴露在潮湿的环境中,持续最多45个工作周期。对于试验5,从示例性连续铸造铝合金片材上切下测试试片。对测试试片进行酸蚀刻,以清洗并准备用于粘结的表面。通过用粘合促进剂对铝合金片材进行预处理并用粘合剂粘结测试试片来进行粘结。将粘结的测试试片暴露在潮湿的环境中,持续最多45个工作周期。对于试验6,从示例性连续铸造铝合金片材上切下测试试片。在实验室炉中对测试试片进行固溶热处理,并且然后进行碱蚀刻和酸蚀刻,以清洗并准备用于粘结的表面。通过用粘合促进剂对铝合金片材进行预处理并用粘合剂粘结测试试片来进行粘结。将粘结的测试试片暴露在潮湿的环境中,持续最多45个工作周期。对于试验7,从对比直接冷激铸造铝合金片材上切下测试试片。对测试试片进行酸蚀刻,以准备用于粘结的表面。通过用粘合促进剂对铝合金片材进行预处理并用粘合剂粘结测试试片来进行粘结。将粘结的测试试片暴露在潮湿的环境中,持续最多45个工作周期。mn和cr向铝合金片材的表面受控地扩散的示例性连续铸造铝合金片材表现出优异的粘结耐久性,其经受了45个测试周期而没有失效。mg扩散至表面的对比直接冷激铸造铝合金片材表现出较差的粘结耐久性。实例5:用各种蚀刻剂蚀刻后的电阻点焊(rsw)电极寿命通过直接冷激铸造制备四个aa5xxx系列铝合金样品,并通过均质化、热轧、冷轧至1.5mm的规格、固溶热处理、空气淬火以及使用四种不同蚀刻剂进行蚀刻来加工所述样品。所采用的蚀刻剂是(i)磷酸和硫酸的混合物(在下表3中被称为溶液“a”)、(ii)硫酸和氟化铵的混合物(在下表3中被称为溶液“b”)、(iii)硫酸和水合硫酸铁(iii)的混合物(在下表3中被称为溶液“c”)以及(iv)氢氧化钠(在下表3中被称为溶液“d”)。氢氧化钠(naoh)由于具有从亚表面去除任何氧化物层的能力,因此被用作对比控制蚀刻剂。表3–蚀刻条件和结果*蚀刻后采用了另外的去污处理。图15是示出在上述各种蚀刻剂溶液中蚀刻之后用于焊接铝合金样品的rsw电极的rsw电极使用寿命的图。如本领域中已知的,溶液d(naoh)被用作对比控制蚀刻剂,以完全去除存在于经过轧制的铝合金产品上的变形的氧化物层,特别是在停留时间至少为20秒时(例如,表3中的蚀刻15和蚀刻16)。如在图15的图表中显而易见的,溶液a(磷酸和硫酸的混合物(h3po4/h2so4))提供的rsw电极寿命为100个焊接,这高于当前工业需求的80个焊接。另外,在图15的实例中,h3po4/h2so4的混合物在亚表面(从铝合金的表面延伸至约83μm的深度)中提供了约0.65的p/mg的原子浓度比。溶液b(硫酸和氟化铵的混合物(h2so4/nh4f))在蚀刻2秒时提供的rsw电极寿命为80个焊接,然而更长的蚀刻停留时间会导致电极寿命的损耗。溶液c(硫酸与水合硫酸铁(iii)的混合物(h2so4/fe2(so4)3))展现出的性能较差,从而显著缩短了rsw电极寿命。因此,将p掺入含mg的亚表面会显著增加rsw电极寿命。图16是示出每次进行的蚀刻(表3中的蚀刻1-16)的蚀刻重量(即,蚀刻期间从铝合金表面去除的材料的量)的图。在图16和上文描述的曲线图中显而易见的是,溶液d能够提供最大的蚀刻重量,因此被用作对比溶液。在蚀刻溶液a、b和c中,溶液b提供了最大的蚀刻重量并且溶液a和c提供了类似的蚀刻重量,所述蚀刻重量均小于溶液b所提供的蚀刻重量。参见图15,溶液b提供了最大的蚀刻重量(参见图16),但并未展现出rsw电极寿命的改善。令人惊讶的是,溶液a和c提供了类似的蚀刻重量,但同时也提供了显著不同的rsw电极寿命。具体地说,溶液a(含有p)提供了显著改善的rsw电极寿命而溶液c不利于rsw电极寿命。因此,仅去除变形的氧化物层不足以改善rsw电极寿命。在图15和图16中显而易见的是,去除一部分变形的氧化物层以及存在残余的p浓度可以共同改善rsw电极寿命。图17-20是示出上述铝合金样品的表面附近(例如,从表面到5.0μm深度)的mg含量的辉光放电光发射能谱(gdoes)数据的图。图17示出了延伸到用溶液a蚀刻的铝合金样品的本体中的mg含量的数据。图18示出了延伸到用溶液b蚀刻的铝合金样品的本体中的mg含量的数据。图19示出了延伸到用溶液c蚀刻的铝合金样品的本体中的mg含量的数据。图20示出了延伸到用溶液d蚀刻的铝合金样品的本体中的mg含量的数据。不受理论的束缚,铝合金样品的亚表面部分中发现的mg浓度可能对rsw电极寿命产生负面影响。令人惊讶的是,当用溶液a(含有p)蚀刻铝合金样品时,即使所述样品在铝合金的亚表面内含有一定浓度的mg,rsw电极寿命仍显著改善。用对比溶液d蚀刻的铝合金样品(图20)展现出铝合金的表面附近的mg几乎完全去除,这进一步表明,用含p化合物蚀刻后,mg和/或含mg化合物(例如,mgo)的存在提供了显著改善的rsw电极寿命。进一步地,图19示出了用溶液c蚀刻的铝合金样品的gdoes数据。在图19的曲线图中显而易见的是,铝合金样品的表面附近存在mg和/或含mg化合物;然而,溶液c不含p并且不利于rsw电极寿命(参见图15)。因此,在蚀刻溶液中不存在p的情况下,铝合金的表面附近的mg和/或含mg化合物的存在可能对rsw电极寿命不利。实例6:用各种蚀刻剂蚀刻后的铝合金表面特性在一些方面,合金元素和/或合金元素氧化物的粒径和形态可以影响铝合金产品的表面特性。例如,图21、22、23和24呈现了上述铝合金样品的扫描电子显微镜(sem)显微照片。图21a-d示出了使用溶液a蚀刻的铝合金样品的sem显微照片。图21a和21b示出了来自蚀刻1的sem显微照片(参见表3)。图21c和21d示出了来自蚀刻4的sem显微照片。图21a和21c是来自扫描电子模式的显微照片。图21b和21d是来自背散射电子模式的显微照片。图22a-d示出了使用溶液b蚀刻的铝合金样品的sem显微照片。图22a和22b示出了来自蚀刻5的sem显微照片。图22c和22d示出了来自蚀刻7的sem显微照片。图22a和22c是来自扫描电子模式的显微照片。图22b和22d是来自背散射电子模式的显微照片。图23a-d示出了使用溶液c蚀刻的铝合金样品的sem显微照片。图23a和23b示出了来自蚀刻9的sem显微照片。图23c和23d示出了来自蚀刻12的sem显微照片。图23a和23c是来自扫描电子模式的显微照片。图23b和23d是来自背散射电子模式的显微照片。图24a-d示出了使用溶液d蚀刻的铝合金样品的sem显微照片。图24a和24b示出了来自蚀刻13的sem显微照片。图24c和24d示出了来自蚀刻16的sem显微照片。图24a和24c是来自扫描电子模式的显微照片。图24b和24d是来自背散射电子模式的显微照片。在图21-24中显而易见的是,溶液b(图22)提供了蚀刻溶液a、b和c的最大蚀刻重量,参见图16),从而提供mg颗粒和/或含mg化合物颗粒的量(由图21、23和24中的亮点指示)减少且变形的氧化层(在图21、23和24中示出为较深的灰色区域)减少的表面。在所产生的条件下使用厚度为1.1mm的商业化生产的aa5182铝合金片材(意指未按照本文所描述的方法进行蚀刻铝合金片材)。对铝合金片材进行rsw试验。图25的图片a示出了铜制rsw电极尖端。在图25的图片a的实例中,mgo颗粒1105粘附到rsw电极尖端。图25的图片b示出了焊接的显微照片,并且图25的图片c是图25的图片b的放大图。如图25的图片c所示,深色区域1110指示铝合金片材的表面处或亚表面中存在的mgo。在图25的图片c的实例中,mg含量为6.9%。所产生的aa5182铝合金含有4%到5%的mg(例如,约4.5%的mg)。表面处或亚表面中的6.9%的mg含量指示mg在加工期间从铝合金的本体朝向表面迁移,从而在铝合金的表面处或亚表面中提供了不期望的量的mgo。因此,在rsw试验期间,mgo颗粒粘附到rsw电极尖端。这种mgo颗粒的吸附可以显著缩短rsw电极寿命。因此,根据本文所述的方法对铝合金片材的表面进行蚀刻和/或清洗可以从铝合金的表面或亚表面去除mgo,形成如上文所述的mg-p化合物,通过rsw电极消除mgo的吸附,并增加rsw电极寿命。图26是示出如上所述制备的铝合金样品的黄度指数(yi)的图。如上所述,yi可以指示铝合金的表面上存在mg和/或含mg化合物(例如,mgo)。虚线表示缺乏显著的yi(例如,yi小于约1)。使用对比溶液d(例如,提供最大的蚀刻重量)进行蚀刻的铝合金样品展现出非常低的yi,特别是当蚀刻停留时间大于20秒时(例如,蚀刻14、15和16,参见表3)。非常低的yi表明铝合金的表面上的mg或含mg化合物的浓度可忽略不计。另外,使用溶液b(例如,提供示例性蚀刻溶液(溶液a、b和c)的最大蚀刻重量)进行蚀刻的铝合金样品展现出低yi,这表明从铝合金样品的表面显著去除了mg和/或含mg化合物。使用溶液a和c(例如,提供低蚀刻重量)进行蚀刻的铝合金样品针对每个样品展现出更大的yi,这表明与使用溶液b和d进行蚀刻的铝合金样品相比,mg和/或含mg化合物的浓度更高。令人惊讶的是,即使在铝合金样品的表面处具有显著的mg和/或含mg化合物浓度时,使用溶液a进行蚀刻的铝合金样品仍提供了显著改善的rsw电极寿命。另外,从蚀刻参考编号1到蚀刻参考编号2观察到yi增加(例如,观察到“反向效应”),这表明蚀刻流程使另外的mg暴露于合金表面并因此一旦暴露就会氧化另外的mg。另外的mg可以归因于富含mg的亚表面。令人惊讶的是,当使用溶液c进行蚀刻的铝合金样品展现出与使用溶液a进行蚀刻的铝合金样品类似的yi时,其对rsw电极寿命展现出不利影响。因此,通过用含p化合物(残余p可以保留在其中)进行蚀刻而产生的最佳表面化学(其中较低的蚀刻重量允许一定浓度的mg和/或含mg化合物保留在铝合金的亚表面内)提供了显著改善的rsw电极寿命。所有样品的yi标准偏差均小于平均yi的1.5%。图27是示出如上所述制备的铝合金样品的表面粗糙度的图。使用溶液a和c(例如,提供低蚀刻重量)进行蚀刻的铝合金样品随着每个样品的蚀刻时间的增加而展现出的表面粗糙度的变化可忽略不计,这表明与使用溶液b和d进行蚀刻的铝合金样品相比,无论蚀刻时间如何,蚀刻更加均匀(即,更均匀地去除表面材料)。令人惊讶的是,与使用溶液b和d进行蚀刻的铝合金样品(具体地,蚀刻参考编号为8、14、15和16)相比,即使具有较低的表面粗糙度,使用溶液a进行蚀刻的铝合金样品仍提供显著改善的rsw电极寿命。以上引用的所有专利、出版物和摘要均通过引用整体并入本文。为了实现本发明的各个目的,已经描述了本发明的各个实施例。应该认识到,这些实施例仅仅是对本发明的原理的说明。在不脱离以下权利要求所限定的本发明的精神和范围的情况下,所述实施例的许多修改和改变对于本领域技术人员而言将是显而易见的。当前第1页1 2 3 
起点商标作为专业知识产权交易平台,可以帮助大家解决很多问题,如果大家想要了解更多知产交易信息请点击 【在线咨询】或添加微信 【19522093243】与客服一对一沟通,为大家解决相关问题。
此文章来源于网络,如有侵权,请联系删除
相关标签:



tips