一种高粘性渣土固化用作回填料的方法与流程



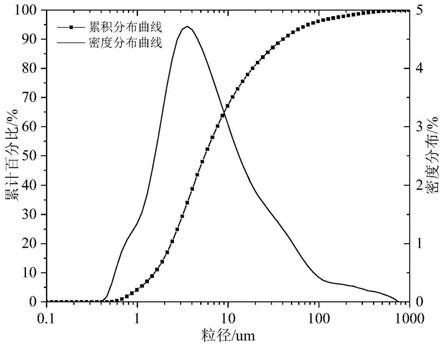
[0001]
本发明涉及一种高粘性渣土处理的技术领域,具体涉及一种高粘性渣土固化用作回填料的方法。
背景技术:
[0002]
目前,我国地铁及其他基础设施建设(如城市综合管廊、管网、地下快速通道、顶管施工等)发展迅速,建设规模大、速度快。其中,盾构法以其安全、高效、地层适应性强等优点被行业公认为较优的区间隧道施工方法,这就必然产生巨量盾构渣土。对于硬岩tbm掘进盾构渣土和泥水平衡盾构渣土,其资源化处置工艺已较为成熟,资源化利用难度相对较小;而对于土石混合渣土或土层类渣土,如土压平衡盾构渣土,呈“膏体”状,其脱水与筛分极为困难,导致资源化利用难度增加、附加值降低,现有的处置方式一般为露天弃置。特别地,对于一些含黏粒较多的软黏质盾构渣土,存在遇水软化、粘性较高等问题,露天堆存危害性更大,高值化利用难度较大或成本较高。
[0003]
综上,有必要探索一种快速、高效的高粘性渣土处置方法。如将其固化用作车站顶板等回填料,就地处置与回填,将处置高粘性渣土的同时提高其附加值。而现有的固化方法对于含黏粒较多的高粘性渣土固化时间较长、固化效果差,通常需要7d才能达到基本的固化回填强度,很难实现同步回填,导致资源化利用效益降低。因此,如若将高粘性渣土快速、高效地固化用作回填料,将节省渣土处置费,同时获得较高的经济效益和环境效益,具有重要意义。
技术实现要素:
[0004]
本发明的目的在于解决高粘性渣土难以处置,现有的固化方式固化效果差、时间长、成本高,难以高值化资源化利用的问题。
[0005]
为解决上述技术问题,本发明提出了一种高粘性渣土固化用作回填料的方法,具体方案如下:
[0006]
一种高粘性渣土固化用作回填料的方法,包括以下步骤:
[0007]
s1、称取所述高粘性渣土,并测试其含水率;
[0008]
s2、根据步骤s1所得含水率,加入高于所述高粘性渣土含水率5-15个百分点的水分,搅拌至均匀状,形成浆料;
[0009]
s3、将6.1wt%以内的固化剂加入步骤s2所制成的均匀状浆料中,搅拌均匀,得固化回填料;
[0010]
其中,所述高粘性渣土中粒径<5μm的黏粒含量>30%,粘度大于5000pa
·
s;所述固化剂按重量份数计,由以下组分组成:
[0011][0012]
在一些实施方式中,所述高粘性渣土中粒径<5μm的黏粒含量≥35%,粒径≤75μm的颗粒含量≥85%。
[0013]
在一些实施方式中,所述高粘性渣土的含水率为18-35%。
[0014]
在一些实施方式中,所述固化剂加入所述均匀状浆料中搅拌均匀,室温自然养护3d后,固化回填料抗压强度达0.8mpa以上,满足回填料要求。
[0015]
在一些实施方式中,所述粒化高炉矿渣的目数为200-400目。
[0016]
在一些实施方式中,所述生石灰含钙量>90%,细度为200目通过率>70%。
[0017]
在一些实施方式中,所述碳酸钠为固体粉末状,目数为150-200目。
[0018]
在一些实施方式中,所述硅酸钠为白色固体粉末,模数为2.3-3.0,细度为100目,溶解时间220s。
[0019]
在一些实施方式中,所述生石膏目数300-400目,白度大于90%。
[0020]
优选的,所述高粘性渣土是地铁盾构区间或车站开挖出的渣土。
[0021]
优选地,在步骤s2中,采用低速搅拌,将高粘性渣土打散并搅拌均匀,搅拌速度为45r/min。
[0022]
优选地,在步骤s3中,采用较高速搅拌,将固化剂与渣土料充分混合搅拌均匀,搅拌速度为120r/min。
[0023]
相较于现有技术,本发明的有益效果为:
[0024]
高粘性渣土具有遇水软化的特点,本发明在高粘性渣土中掺固化剂之前,在先外加相应的水量来克服高粘性渣土难以与固化剂混合均匀的问题,使其浸水后软化松散,与固化剂充分接触并搅拌均匀,提高固化效果,在固化剂掺量较低(<6.1wt%)的情况下,所制成的试件室温自然养护3d后抗压强度可达0.8mpa以上,7d抗压强度可达1.2mpa以上,满足回填土的强度要求。相比现有的固化方法固化时间长、成本高、固化效果差的问题,本发明具有固化强度高,固化速度快,固化效果好的特点,可以实现施工现场同步回填,缩短回填施工工期,且固化成本低,解决了高粘性渣土难以处置以及高值化资源化利用的问题,而且具有很高的经济效益和环境效益。
[0025]
本发明还具有以下优势:
[0026]
(1)无需配合水泥使用,且固化效果优于po42.5水泥,自然养护3d即可达到基本的回填强度要求,有利于缩短施工工期,而且高效环保;
[0027]
(2)充分利用高粘性渣土遇水软化的特点,额外在渣土中添加相应水量来克服其难以与固化剂混合均匀的问题,使其浸水后软化膨胀,形成松散状态,从而与固化剂充分接触并搅拌均匀,提高固化效果;
[0028]
(3)每方渣土固化成本在85元以内,相比施工现场目前的泥岩渣土弃置费用每方
150元及以上,经济效益明显。
附图说明
[0029]
通过参考附图会更加清楚的理解本发明的特征和优点,附图是示意性的而不应理解为对本发明进行任何限制,在附图中:
[0030]
图1是本发明实施例1-3和对比例1-7所用的高粘性渣土(泥岩渣土)粒径分布曲线图。
[0031]
图2是本发明实施例1-3和对比例1-7所用的泥岩渣土xrd谱图。
[0032]
图3是本发明实施例1泥岩渣土制成固化试件并室温自然养护3d和7d后的单轴压缩应力-应变曲线图。
[0033]
图4是本发明实施例2泥岩渣土制成固化试件并室温自然养护3d和7d后的单轴压缩应力-应变曲线图。
具体实施方式
[0034]
为使本发明的上述目的、特征和优点能够更加明显易懂,下面结合附图对本发明的具体实施方式做详细的说明。在下面的描述中阐述了很多具体细节以便于充分理解本发明。但是本发明能够以很多不同于在此描述的其它方式来实施,本领域技术人员可以在不违背本发明内涵的情况下做类似改进,因此本发明不受下面公开的具体实施的限制。
[0035]
本具体实施方式提出一种高粘性渣土固化用作回填料的方法,下述具体实施方式、实施例以及对比例中的泥岩渣土(高粘性渣土)取自南宁地铁5号线二工区某区间的原状渣土料,测得其初始含水率为22%。如图1所示,为该泥岩渣土的粒径分布曲线,可以看出其黏粒(以小于5μm颗粒计算)含量为45%,75μm以下颗粒含量为94%,导致粘性较高。经流变仪测试,在室温条件下,其在60转/分的转速下测得最高粘度值为8205pa
·
s。如图2所示为其xrd谱图,可以看出,其主要矿物成分为石英、云母、高岭石和绿泥石;经测试,主要化学成分及占比分别为sio
2
:62.7%,al
2
o
3
:19.0%,fe
2
o
3
:9.93%。
[0036]
下述具体实施方式、实施例和对比例所使用的固化剂组分,具体参数如下:
[0037]
粒化高炉矿渣的目数为200;生石灰细度为200目通过率80%,含钙量为91%;碳酸钠目数为150;硅酸钠粉,模数为2.85,细度为100目过筛率98.5%;生石膏目数300,白度95%。
[0038]
本发明掺固化剂之前,在渣土中外加相应的水量来克服高粘性渣土难以与固化剂混合均匀的问题,使其浸水后软化松散,从而与固化剂充分接触并搅拌均匀。
[0039]
因此,包括最佳掺水量的研究。同时,为保证固化成本,首先选择粒化高炉矿渣、生石灰、碳酸钠和硅酸钠作为固化剂,如下:
[0040]
取泥岩渣土2000g,分别加入(1):800g水、(2):600g水、(3):400g水、(4):350g水、(5):300g水、(6):250g水、(7):200g水,采用小型搅拌机以45r/min的速度搅拌均匀,再加入116g固化剂并采用120r/min的速度搅拌均匀,得最终的固化料,浇筑入70.7*70.7*70.7mm的三联模具中,室温自然养护7d后测试单轴抗压强度。其中,固化剂由搅拌均匀的80g粒化高炉矿渣、20g生石灰、10g碳酸钠、6g硅酸钠粉组成。
[0041]
经测试第(1)-(7)组的7d抗压强度分别为0.100mpa、0.423mpa、0.445mpa、
0.460mpa、0.587mpa、0.770mpa、0.993mpa。另外,第(6)组和第(7)组的3d抗压强度分别为0.657mpa、0.743mpa。
[0042]
从上述结果可以看出,第(6)组的7d抗压强度接近0.8mpa,第(7)组的7d抗压强度超过0.8mpa,但是其3d抗压强度均低于0.8mpa,不能满足回填料的基本强度要求。
[0043]
为了在确保最大掺水量和搅拌效果,保证固化成本的前提下,进一步提高泥岩渣土固化强度,增加生石膏,优化固化剂组成成分及配合比,以达到最佳的固化效果。
[0044]
为进一步具体说明本发明提出的一种高粘性渣土固化用作回填料的方法,下面列举实施例进行详细说明。
[0045]
实施例1
[0046]
取2000g原状泥岩渣土,测得初始含水率为22%。称取粒化高炉矿渣80g,生石灰20g,碳酸钠10g,硅酸钠6g,生石膏5g,混合搅拌均匀,备用。另外,称取水200g。
[0047]
一种高粘性渣土固化用作回填料的方法,包括以下步骤:
[0048]
s1、称取2000g高粘性渣土,测试其含水率为22%;
[0049]
s2、根据步骤s1所得含水率,外加高于泥岩渣土含水率12.2个百分点的水分(200g),采用45r/min的速度搅拌至均匀状;
[0050]
s3、将6.05%(121g)重量百分比的固化剂加入步骤s2所述的均匀状渣土中,采用120r/min的速度搅拌至均匀状,得固化回填料。
[0051]
将步骤s3所得固化回填料灌入70.7*70.7*70.7mm的立方体三联模具中。经测试,其3d和7d平均抗压强度分别为0.997mpa、1.202mpa。如图3所示,图3为实施例1高粘性渣土固化回填料试件室温自然养护3d和7d后的单轴压缩应力-应变曲线图。
[0052]
实施例2
[0053]
取2000g原状泥岩渣土,测得初始含水率为22%。称取粒化高炉矿渣70g,生石灰20g,碳酸钠10g,硅酸钠6g,生石膏7.5g,混合搅拌均匀,备用。另外,称取水200g。
[0054]
一种高粘性渣土固化用作回填料的方法,包括以下步骤:
[0055]
s1、称取2000g高粘性渣土,测试其含水率为22%;
[0056]
s2、根据步骤s1所得含水率,外加高于泥岩渣土含水率12.2个百分点的水分(200g),采用45r/min的速度搅拌至均匀状;
[0057]
s3、将5.675%(113.5g)重量百分比的固化剂加入步骤s2所述的均匀状渣土中,采用120r/min的速度搅拌至均匀状,得固化回填料。
[0058]
将步骤s3所得固化回填料灌入70.7*70.7*70.7mm的立方体三联模具中。经测试,其3d和7d平均抗压强度分别为0.890mpa、1.280mpa。如图4所示,图4为实施例2高粘性渣土固化回填料试件室温自然养护3d和7d后的单轴压缩应力-应变曲线图。
[0059]
实施例3
[0060]
取2000g原状泥岩渣土,测得初始含水率为22%。称取粒化高炉矿渣70g,生石灰20g,碳酸钠10g,硅酸钠6g,生石膏10g,混合搅拌均匀,备用。另外,称取水200g。
[0061]
一种高粘性渣土固化用作回填料的方法,包括以下步骤:
[0062]
s1、称取2000g高粘性渣土,测试其含水率为22%;
[0063]
s2、根据步骤s1所得含水率,外加高于泥岩渣土含水率12.2个百分点的水分(200g),采用45r/min的速度搅拌至均匀状;
[0064]
s3、将5.80%(116g)重量百分比的固化剂加入步骤s2所述的均匀状渣土中,采用120r/min的速度搅拌至均匀状,得固化回填料。
[0065]
将步骤s3所得固化回填料灌入70.7*70.7*70.7mm的立方体三联模具中,室温自然养护。经测试,其7d平均抗压强度为1.095mpa。
[0066]
对比例1
[0067]
取2000g原状泥岩渣土,测得初始含水率为22%。称取粒化高炉矿渣80g,生石灰20g,碳酸钠10g,硅酸钠6g,生石膏5g,混合搅拌均匀,备用。另外,称取水400g。
[0068]
一种高粘性渣土固化用作回填料的方法,包括以下步骤:
[0069]
s1、称取2000g高粘性渣土,测试其含水率为22%;
[0070]
s2、根据步骤s1所得含水率,外加高于泥岩渣土含水率24.4个百分点的水分(400g),采用45r/min的速度搅拌至均匀状;
[0071]
s3、将6.05%(121g)重量百分比的固化剂加入步骤s2所述的均匀状渣土中,采用120r/min的速度搅拌至均匀状,得固化回填料。
[0072]
将步骤s3所得固化回填料灌入70.7*70.7*70.7mm的立方体三联模具中,室温自然养护。经测试,其7d平均抗压强度为0.643mpa。
[0073]
对比例2
[0074]
取2000g原状泥岩渣土,测得初始含水率为22%。称取粒化高炉矿渣80g,生石灰20g,碳酸钠10g,硅酸钠6g,生石膏5g,混合搅拌均匀,备用。另外,称取水300g。
[0075]
一种高粘性渣土固化用作回填料的方法,包括以下步骤:
[0076]
s1、称取2000g高粘性渣土,测试其含水率为22%;
[0077]
s2、根据步骤s1所得含水率,外加高于泥岩渣土含水率18.3个百分点的水分(300g),采用45r/min的速度搅拌至均匀状;
[0078]
s3、将6.05%(121g)重量百分比的固化剂加入步骤s2所述的均匀状渣土中,采用120r/min的速度搅拌至均匀状,得固化回填料。
[0079]
将步骤s3所得固化回填料灌入70.7*70.7*70.7mm的立方体三联模具中,室温自然养护。经测试,其7d平均抗压强度为0.830mpa。
[0080]
对比例3
[0081]
取2000g原状泥岩渣土,测得初始含水率为22%。称取粒化高炉矿渣80g,生石灰20g,碳酸钠10g,硅酸钠6g,生石膏5g,混合搅拌均匀,备用。另外,称取水250g。
[0082]
一种高粘性渣土固化用作回填料的方法,包括以下步骤:
[0083]
s1、称取2000g高粘性渣土,测试其含水率为22%;
[0084]
s2、根据步骤s1所得含水率,外加高于泥岩渣土含水率15.3个百分点的水分(250g),采用45r/min的速度搅拌至均匀状;
[0085]
s3、将6.05%(121g)重量百分比的固化剂加入步骤s2所述的均匀状渣土中,采用120r/min的速度搅拌至均匀状,得固化回填料。
[0086]
将步骤s3所得固化回填料灌入70.7*70.7*70.7mm的立方体三联模具中,室温自然养护。经测试,其7d平均抗压强度为0.935mpa。
[0087]
对比例4
[0088]
取2000g原状泥岩渣土,测得初始含水率为22%。称取粒化高炉矿渣70g,生石灰
20g,碳酸钠10g,硅酸钠6g,生石膏7.5g,混合搅拌均匀,备用。另外,称取水400g。
[0089]
一种高粘性渣土固化用作回填料的方法,包括以下步骤:
[0090]
s1、称取2000g高粘性渣土,测试其含水率为22%;
[0091]
s2、根据步骤s1所得含水率,外加高于泥岩渣土含水率24.4个百分点的水分(400g),采用45r/min的速度搅拌至均匀状;
[0092]
s3、将5.675%(113.5g)重量百分比的固化剂加入步骤s2所述的均匀状渣土中,采用120r/min的速度搅拌至均匀状,得固化回填料。
[0093]
将步骤s3所得固化回填料灌入70.7*70.7*70.7mm的立方体三联模具中,室温自然养护。经测试,其7d平均抗压强度为0.470mpa。
[0094]
对比例5
[0095]
取2000g原状泥岩渣土,测得初始含水率为22%。称取粒化高炉矿渣70g,生石灰20g,碳酸钠10g,硅酸钠6g,生石膏7.5g,混合搅拌均匀,备用。另外,称取水300g。
[0096]
一种高粘性渣土固化用作回填料的方法,包括以下步骤:
[0097]
s1、称取2000g高粘性渣土,测试其含水率为22%;
[0098]
s2、根据步骤s1所得含水率,外加高于泥岩渣土含水率18.3个百分点的水分(300g),采用45r/min的速度搅拌至均匀状;
[0099]
s3、将5.675%(113.5g)重量百分比的固化剂加入步骤s2所述的均匀状渣土中,采用120r/min的速度搅拌至均匀状,得固化回填料。
[0100]
将步骤s3所得固化回填料灌入70.7*70.7*70.7mm的立方体三联模具中,室温自然养护。经测试,其7d平均抗压强度为0.853mpa。
[0101]
对比例6
[0102]
取2000g原状泥岩渣土,测得初始含水率为22%。称取粒化高炉矿渣70g,生石灰20g,碳酸钠10g,硅酸钠6g,生石膏7.5g,混合搅拌均匀,备用。另外,称取水250g。
[0103]
一种高粘性渣土固化用作回填料的方法,包括以下步骤:
[0104]
s1、称取2000g高粘性渣土,测试其含水率为22%;
[0105]
s2、根据步骤s1所得含水率,外加高于泥岩渣土含水率15.3个百分点的水分(250g),采用45r/min的速度搅拌至均匀状;
[0106]
s3、将5.675%(113.5g)重量百分比的固化剂加入步骤s2所述的均匀状渣土中,采用120r/min的速度搅拌至均匀状,得固化回填料。
[0107]
将步骤s3所得固化回填料灌入70.7*70.7*70.7mm的立方体三联模具中,室温自然养护。经测试,其7d平均抗压强度为0.913mpa。
[0108]
对比例7
[0109]
取2000g原状泥岩渣土,测得初始含水率为22%。称取粒化高炉矿渣70g,生石灰20g,碳酸钠10g,硅酸钠6g,生石膏10g,混合搅拌均匀,备用。另外,称取水250g。
[0110]
一种高粘性渣土固化用作回填料的方法,包括以下步骤:
[0111]
s1、称取2000g高粘性渣土,测试其含水率为22%;
[0112]
s2、根据步骤s1所得含水率,外加高于泥岩渣土含水率15.3个百分点的水分(250g),采用45r/min的速度搅拌至均匀状;
[0113]
s3、将5.80%(116g)重量百分比的固化剂加入步骤s2所述的均匀状渣土中,采用
120r/min的速度搅拌至均匀状,得固化回填料。
[0114]
将步骤s3所得固化回填料灌入70.7*70.7*70.7mm的立方体三联模具中,室温自然养护。经测试,其7d平均抗压强度为0.993mpa。
[0115]
根据上述实施例1-3和对比例1-7的结果可知,最优掺水量为外加高于渣土含水率5-15个百分点的水分,在该掺水量所制成的试件,室温自然养护3d可达0.8mpa以上,满足回填强度要求。水分掺量过多,虽然可以使得搅拌更为充分,但是阻碍了水化反应,导致固化渣土试件强度下降;减少外加水掺量,可以极大的提高试件抗压强度;而当水分掺量过少,则渣土的高粘性副作用凸显,导致固化剂与渣土很难混合搅拌均匀,从而使得固化效果较差,达不到基本的强度要求。同时,对于黏粒含量较高的高粘性渣土,生石膏的双重作用性明显。生石膏掺量在一定范围内,水化反应过程消耗自由水、水化产物填充土体内部孔隙,胶结土颗粒,从而提高固化土强度。当生石膏掺量继续增加,其生成的膨胀性水化产物容易破坏固化土体已有的网状结构,导致固化土体强度不增反降。
[0116]
进一步,对本发明高粘性渣土固化用作回填料的效果以及经济性作详细说明。
[0117]
对比例8
[0118]
取2000g原状泥岩渣土,测得初始含水率为22%。参照实施例1的固化剂重量,称取po42.5水泥121g,备用。另外,称取水200g。
[0119]
一种高粘性渣土固化用作回填料的方法,包括以下步骤:
[0120]
s1、称取2000g高粘性渣土,测试其含水率为22%;
[0121]
s2、根据步骤s1所得含水率,外加高于泥岩渣土含水率12.2个百分点的水分(200g),采用45r/min的速度搅拌至均匀状;
[0122]
s3、将6.05%(121g)重量百分比的po42.5水泥加入步骤s2所述的均匀状渣土中,采用120r/min的速度搅拌至均匀状,得固化回填料。
[0123]
将步骤s3所得固化回填料灌入70.7*70.7*70.7mm的立方体三联模具中。经测试,其室温自然养护3d和7d后的平均抗压强度分别为0.547mpa、0.930mpa。
[0124]
对比例9
[0125]
取2000g原状泥岩渣土,测得初始含水率为22%。参照实施例1的固化剂成本,折算成相同价格的po42.5水泥的重量为166.3g,称取po42.5水泥166.3g,备用。另外,称取水200g。
[0126]
一种高粘性渣土固化用作回填料的方法,包括以下步骤:
[0127]
s1、称取2000g高粘性渣土,测试其含水率为22%;
[0128]
s2、根据步骤s1所得含水率,外加高于泥岩渣土含水率12.2个百分点的水分(200g),采用45r/min的速度搅拌至均匀状;
[0129]
s3、将8.315%(166.3g)重量百分比的加入步骤s2所述的均匀状渣土中,采用120r/min的速度搅拌至均匀状,得固化回填料。
[0130]
将步骤s3所得固化回填料灌入70.7*70.7*70.7mm的立方体三联模具中。经测试,其室温自然养护3d和7d后的平均抗压强度分别为0.710mpa、0.992mpa。
[0131]
可以看出,对比例8和对比例9的3d抗压强度均小于0.8mpa,7d强度虽然可以达到0.8mpa,但是固化效果和经济性都比本发明实施例1、实施例2和实施例3要差。
[0132]
综上,本发明具有以下优势:
[0133]
(1)无需配合水泥使用,且固化效果优于po42.5水泥,自然养护3d即可达到0.8mpa以上,基本的回填料强度要求,固化速度快,有利于缩短施工工期,并且高效环保。
[0134]
(2)充分利用高粘性渣土遇水软化的特点,额外在渣土中加水来克服其难以与固化剂混合均匀的问题,使其浸水后软化膨胀,形成松散状态,从而与固化剂充分接触并搅拌均匀,提高固化效果。
[0135]
(3)每方渣土固化成本在85元以内,相比施工现场目前的泥岩渣土弃置费用每方150元及以上,经济效益明显。
[0136]
除非另有定义,本文所使用的所有的技术和科学术语与属于本发明的技术领域的技术人员通常理解的含义相同。本文中在本发明的说明书中所使用的术语只是为了描述具体的实施例的目的,不是旨在于限制本发明。以上所述实施例的各技术特征可以进行任意的组合,为使描述简洁,未对上述实施例中的各个技术特征所有可能的组合都进行描述,然而,只要这些技术特征的组合不存在矛盾,都应当认为是本说明书记载的范围。
起点商标作为专业知识产权交易平台,可以帮助大家解决很多问题,如果大家想要了解更多知产交易信息请点击 【在线咨询】或添加微信 【19522093243】与客服一对一沟通,为大家解决相关问题。
此文章来源于网络,如有侵权,请联系删除
相关标签: 单轴抗压强度



tips