一种直接还原竖炉装置的制作方法



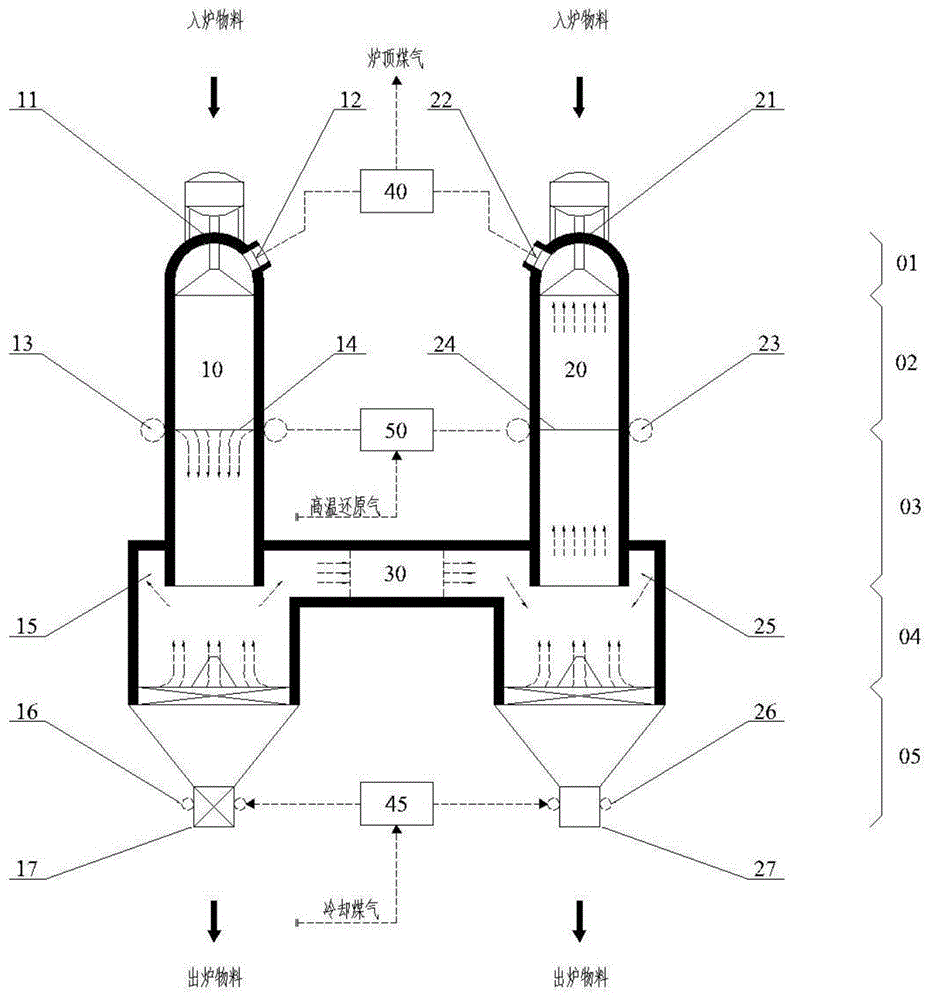
本实用新型属于直接还原技术领域,具体涉及一种直接还原竖炉装置。
背景技术:
为了摆脱焦煤资源短缺对冶金工业发展的羁绊,适应环境保护的要求,进一步地降低炼铁工序能耗,以直接还原为主要发展方向之一的非高炉炼铁技术,日益成为了钢铁行业发展和关注的热点。
直接还原技术作为一种新的炼铁技术,有气基直接还原和煤基直接还原两种。
其中,气基直接还原以h2和co组成的还原气为还原剂,在竖炉或罐式炉内将铁矿中的氧化铁在固态温度下还原成海绵铁;气基直接还原具有单位容积利用高、气体直接传热效率高、生产效率高等优点,而成为现有直接还原工艺的主流技术,典型如midrex法和hyl法。但现有气基直接还原装置依然存在有待进一步完善的工艺环节,如(1)因气流行程较短,炉顶煤气温度一般为400~500℃,比传统高炉工艺的炉顶煤气温度高250~300℃,因此热效率利用上较高炉工艺有一定的差距;(2)因炉顶温度较高,含尘量大,大多采用湿法除尘工艺,通过洗涤对高温还原气同时进行降温和除尘,因此炉顶煤气的显热损耗较大,除尘过程中需要消耗新水并产生污泥,没有传统高炉的干法除尘工艺环保效果好和运行成本低;(3)因煤气温度高,独立循环的炉顶煤气和冷却煤气需要各配置一套冷却设施和加压设施,被冷媒介带走的热量较多,设备的台套数增加,控制环节增多;(4)炉顶煤气一次利用率较低,含有的h2和co的比例较高,总量依然有50~70%;(5)对天然气资源的过渡依赖。
煤基直接还原主要以非焦煤作为还原剂,在回转窑、转底炉或循环流化床内将铁矿石中的氧化铁在固态温度下还原成海绵铁;煤基直接还原不受天然气资源的限制,适用的煤种较多,比较适合天然气资源比较匮乏而煤资源充裕的地区;但煤基直接还原的产能规模有限,难以满足大规模化生产的需要,分析其主要原因,除了受现有煤基直接还原装置的物料运行方式影响,还在于现有煤基直接还原工艺的热效率不高,导致物料所需的还原时间较长。
技术实现要素:
针对现有技术中存在的不足,借鉴于高炉热风炉的并流蓄热和逆流换热的工作原理,本实用新型提出了一种直接还原竖炉装置,以外部高温还原气为热源,通过换向阀的切换,使载热还原气在第一竖炉和第二竖炉来回、同时进行并流加热和逆流蓄热,实现气体直接还原或气固相结合的直接还原;所产生的炉顶煤气作为加热炉的燃料、循环还原气和循环冷却煤气使用;通过采用连通的双竖炉构造,增加煤气行程,解决传统气基竖炉气流行程短的问题,提高了一次还原气的利用率,高温还原气和冷却煤气的显热利用充分,综合热效率大幅提高,炉顶煤气温度更低;并且煤气流的定期在线切换,有利于实现了两个竖炉温度场的同步与统一,也解决了双竖炉同步稳定、高效运行的问题。
本实用新型的技术方案为:
一种直接还原竖炉装置,包括:第一竖炉、第二竖炉,其特征在于,
所述第一竖炉设有第一进料口、第一炉顶煤气溢出口、第一高温还原气环道和与之连通的第一高温还原气喷口、第一煤气环形通道、第一冷却煤气进气口以及第一排料口;
所述第二竖炉设有第二进料口、第二炉顶煤气溢出口、第二高温还原气环道和与之连通的第二高温还原气喷口、第二煤气环形通道、第二冷却煤气进气口以及第二排料口;
所述第一竖炉与第二竖炉镜像对称布置,从上到下依次设有相同的空料段、预热段、还原段、等压段和冷却段;其中还原段腔体直径小于等压段腔体直径,还原段的末端插入等压段腔体内,分别形成第一煤气环形通道和第二煤气环形通道;所述的中间煤气通道与第一煤气环形通道和第二煤气环形通道连通;
所述的第一进料口、第二进料口、第一炉顶煤气溢出口和第二炉顶煤气溢出口分别布置于两个竖炉的空料段顶部,所述的第一高温还原气环道、第二高温还原气环道、第一高温还原气喷口和第二高温还原气喷口分别布置于两个竖炉预热段和还原段的交界处,所述的第一冷却煤气进气口和第二冷却煤气进气口分别布置于两个竖炉的冷却段上,所述的第一排料口、第二排料口分别位于两个竖炉冷却段的下方;
所述第一煤气溢出口与第二煤气溢出口通过管路连通,中间设置有换向阀组;
所述第一高温还原气环道与第二高温还原气环道通过管路连通,中间设置有高温还原气换向阀组;
所述第一冷却煤气进气口与第二冷却煤气进气口通过管路连通,中间设置有冷却煤气阀组;
进一步的,所述的高温还原气通过中间换向阀组切换进入第一竖炉或第二竖炉,按照气流方向,在两个竖炉内同时并流加热和逆流蓄热,过程中发生直接还原反应;
进一步的,所述的炉顶煤气通过中间换向阀组的切换从第一竖炉或第二竖炉排出;炉顶煤气排出方向与高温还原气进气方向相反;
进一步的,所述的炉顶煤气中间的换向阀组与高温还原气换向阀的换向组间隔时间为15~60min;
进一步的,所述的直接还原竖炉装置,可以单独实现气基直接还原或气固结合的直接还原,入炉物料为含铁氧化物的球团或块矿,或者为含铁氧化物的球团或块矿与外配的还原剂;其中球团或块矿的粒度为5~35mm,外配还原剂的粒度为5~50mm;
进一步的,所述的直接还原竖炉装置,排出物料为还原铁或还原铁与残余还原剂的混合物;排料温度为600~700℃或50~120℃;
进一步的,所述的直接还原竖炉装置,高温还原气温度为900~1050℃,为天然气、页岩气、焦炉煤气、半焦炉煤气、发生炉煤气、高炉煤气、转炉煤气中的一种或多种;在还原竖炉能够产生足够数量的煤气的情况下,不需要外部煤气的输入;所述的外配还原剂为生物质炭、碎焦、半焦、褐煤、烟煤、无烟煤中的一种或多种;
进一步的,所述的直接还原竖炉装置,第一竖炉和第二竖炉内存在压力差,高温还原气进气口压力为0.25~0.6mpa,冷却煤气的进气口压力为0.25~0.6mpa,竖炉的煤气环形通道和等压段内的压力为0.2~0.4mpa,炉顶煤气溢出口的压力为0.05~0.4mpa;
进一步的,所述的直接还原竖炉装置,预热段温度为200~600℃,还原段温度为600~1050℃,等压段温度为700~950℃,冷却段温度为50~700℃;
进一步的,所述的直接还原竖炉装置,入炉物料在竖炉内的停留时间为13~24h,其中预热段停留的时间为3~5h,在还原段停留的时间为6~12h,在等压段内停留的时间为1-2h,冷却段停留的时间为3~5h。
与现有技术相比,本实用新型的有益效果为:
(1)没有对还原气质量的严格限制,不受建设地天然气资源的束缚;在还原气条件较好的情况下,可以实施单独的气基直接还原,在还原气条件较差的情况下,可以外配入还原剂,采用气固相结合的直接还原;
(2)采用连通的双竖炉构造,高温还原气在两个竖炉内分别同时进行并流加热和逆流蓄热;煤气行程较长,解决了传统竖炉气流行程短的问题,使得高温还原气和冷却煤气的热量回收充分,炉顶煤气的温度和粉尘浓度较低以及一次还原气的利用效率提高;
(3)采用连通的双竖炉构造,高温还原气和炉顶煤气在换向阀组的切换下,控制着高温还原气在两个竖炉内往复运行,保证了两个竖炉温度场的同步性和统一性,有利于双竖炉同步高效运行,产量和还原质量得到充分保障;
(4)冷却煤气与炉顶煤气之间的闭路循环,省去了现有气基竖炉两路独立循环所需要的设备投入,也减少了中间热量损耗;
(5)由于炉顶温度煤气温度较低,避免了入炉物料急冷到急热时发生爆裂的可能性,对入炉矿石的强度要求降低,原料的适应性提高;
(6)因炉顶煤气温度和粉尘浓度得到了有效的控制,采用高炉工艺常用的干法除尘工艺,能够避免现有的湿法除尘工艺所带来的弊端,不需要消耗新水,不会产生污泥,环保效果好,运行成本低;
(7)炉顶煤气经处理后,作为加热炉的燃料、循环还原煤气和循环冷却煤气,工艺流程简单,投资强度低;煤气资源得到了利用充分,减少了系统co2的排放。
附图说明
图1为本实用新型的结构示意图;
图2为本实用新型实施例1的工艺流程联络图;
图3为本实用新型实施例2的工艺流程联络图;
附图标记:10-第一竖炉;20-第二竖炉;01-空料段;02-预热段;03-还原段;04-等压段;05-冷却段;11-第一进料口;12-第一炉顶煤气溢出口;13-第一高温还原气环道;14-第一高温还原气喷口;15-第一煤气环形通道;16-第一冷却煤气进气口;17-第一排料口;21-第二进料口;22-第二炉顶煤气溢出口;23-第二高温还原气环形通道;24-第二高温还原气喷口;25-第二煤气环形通道;26-第二竖炉冷却煤气进气口;27-第二竖炉排料口;30-中间煤气通道;40-换向阀组;41-除尘装置;42-煤气净化装置;43-煤气脱湿装置;44-煤气加压装置;45-冷却煤气阀组;46-焦油捕集装置;50-高温还原气换向阀组;51-加热炉。
具体实施方式
为了使本实用新型的目的、技术方案和优点更加清楚,下面将结合附图对本实用新型实施方式作进一步地详细描述。本实用新型的作进一步描述的装置均为现有结构。
实施例1:
如图1和图2所示,一种直接还原竖炉装置,包括第一竖炉10和第二竖炉20;第一竖炉10设有第一进料口11、第一炉顶煤气溢出口12、第一高温还原气环道和13与之连通的第一高温还原气喷口14、第一煤气环形通道15、第一冷却煤气进气口16以及第一排料口17;第二竖炉20设有第二进料口21、第二炉顶煤气溢出口22、第二高温还原气环道23和与之连通的第二高温还原气喷口24、第二煤气环形通道25、第二冷却煤气进气口26以及第二排料口27;第一竖炉10与第二竖炉20镜像对称布置,从上到下依次设有相同的空料段01、预热段02、还原段03、等压段04和冷却段05;其中还原段03腔体直径小于等压段04腔体直径,还原段03的末端插入等压段04腔体内,分别形成第一煤气环形通道15和第二煤气环形通道25;所述的中间煤气通道30与第一煤气环形通道15和第二煤气环形通道25连通;
上述的第一进料口11、第二进料口21、第一炉顶煤气溢出口12和第二炉顶煤气溢出口22分别布置于两个竖炉的空料段01顶部,上述的第一高温还原气环道13、第二高温还原气环道23、第一高温还原气喷口14和第二高温还原气喷口24分别布置于两个竖炉预热段02和还原段03的交界处,上述的第一冷却煤气进气口16、第二冷却煤气进气口26分别布置于两个竖炉的冷却段05上,相应的第一排料口17、第二排料口27分别位于两个竖炉冷却段05的下方;
上述的第一煤气溢出口12与第二煤气溢出口22通过管路连通,中间设置有换向阀组40,换向阀组40的出气口通过管道依次与除尘装置41、煤气净化装置42、煤气脱湿装置43连接;
上述的第一高温还原气环道13与第二高温还原气环道23通过管路连通,中间设置有高温还原气换向阀组50,高温还原气换向阀组50的进气口通过管道依次与氧气管道、加热炉51和外部煤气管道连接;
上述的第一冷却煤气进气口16与第二冷却煤气进气口26通过管路连通,中间设置有冷却煤气阀组45,冷却煤气阀组45的进气口通过管道与煤气加压装置44连接;
煤气脱湿装置43出口分别与加热炉51的煤气烧嘴和煤气加压装置44入口连通;煤气加压装置44的出口与外部煤气管道和冷却煤气阀组45连通。
煤气脱湿装置出口与加热炉的煤气烧嘴和煤气加压装置入口连通;炉顶煤气加压装置的出口与外部煤气管道和冷却煤气阀组连通。所述的煤气净化装置具有脱除co2和h2s的功能。
使用该装置及其系统生产直接还原铁的方法为:
(1)高温还原气主要组分为h2和co,混入净化后的部分炉顶煤气后,混合气的h2/co的体积比≥0.5,h2+co的体积和≥0.9;
(2)粒度为5~35mm的球团或块矿自第一竖炉和第二竖炉的空料段同时连续加入,炉料自上而下运行;
(3)外部煤气经加热炉加热至600~750℃;兑入氧气后,温度升高至900~950℃,通过高温还原气换向阀组,自第一高温还原气环道和第一高温还原气喷口进入第一竖炉,与物料在第一竖炉的还原段向下并行,过程中发生铁氧化物的还原反应;
(4)第一竖炉还原段下行的高温还原气经第一煤气环形通道和中间煤气通道进入第二竖炉,并向上逆行,依次经过第二竖炉的等压段、还原段和预热段后,冷却至≤200℃,经炉顶煤气换向阀组进入布袋除尘装置中;
(5)冷却煤气通过冷却煤气阀组同时进入第一竖炉和第二竖炉的冷却段,冷却煤气逆行过程中,带走高温物料的显热;第一竖炉冷却段的冷却煤气经第一煤气环形通道和中间煤气通道进入第二竖炉等压段,第二竖炉冷却段的冷却煤气直接进入第二竖炉等压段;冷却煤气向上逆行,依次经过第二竖炉的等压段、还原段和预热段后,冷却至≤200℃,经炉顶煤气换向阀组进入布袋除尘装置中;
(6)温度≤200℃的炉顶煤气自第二竖炉煤气溢出口排出,依次进入布袋除尘装置、煤气净化装置、煤气脱湿装置中,进行除尘、脱除co2、脱除h2s和除湿;净化的炉顶煤气经加压后循环利用,一部分作为冷却煤气,另一部分与外部煤气混合,重新作为还原气使用;剩余净化后的炉顶煤气直接接至加热炉烧嘴处,作为加热还原气的燃料使用;
(7)每隔15~60min在线切换高温还原气换向阀组和炉顶煤气换向阀组,使高温还原气切换成进入第二竖炉,按照相反的工艺气流方向,在第二竖炉内的还原段发生还原反应后,经第二煤气环形通道和中间煤气通道进入第一竖炉,并向上逆行,依次经过第一竖炉的等压段、还原段和预热段,冷却至≤200℃,经炉顶煤气换向阀组进入布袋除尘装置中;
(8)过程控制中,高温还原气进气口压力为0.25~0.6mpa,冷却煤气的进气口压力为0.25~0.6mpa,竖炉的煤气环形通道和等压段内的压力为0.2~0.4mpa,炉顶煤气溢出口的压力为0.05~0.4mpa;预热段温度为200~600℃,还原段温度为600~950℃,等压段温度为700~950℃,冷却段温度为50~700℃;球团或块矿在竖炉内的停留时间约为13~20h,其中预热段停留的时间约为3~5h,在还原段停留的时间为6~8h,在等压段内停留的时间约为1~2h,冷却段停留的时间约为3~5h;排料口的物料温度为600~700℃或低于50~120℃。
实施例2:
如图1和图3所示,一种直接还原竖炉装置包括第一竖炉10和第二竖炉20;第一竖炉10设有第一进料口11、第一炉顶煤气溢出口12、第一高温还原气环道和13与之连通的第一高温还原气喷口14、第一煤气环形通道15、第一冷却煤气进气口16以及第一排料口17;第二竖炉20设有第二进料口21、第二炉顶煤气溢出口22、第二高温还原气环道23和与之连通的第二高温还原气喷口24、第二煤气环形通道25、第二冷却煤气进气口26以及第二排料口27;第一竖炉10与第二竖炉20镜像对称布置,从上到下依次设有相同的空料段01、预热段02、还原段03、等压段04和冷却段05;其中还原段03腔体直径小于等压段04腔体直径,还原段03的末端插入等压段04腔体内,分别形成第一煤气环形通道15和第二煤气环形通道25;所述的中间煤气通道30与第一煤气环形通道15和第二煤气环形通道25连通;第一进料口11、第二进料口21、第一炉顶煤气溢出口12和第二炉顶煤气溢出口22分别布置于两个竖炉的空料段01顶部,上述的第一高温还原气环道13、第二高温还原气环道23、第一高温还原气喷口14和第二高温还原气喷口喷口24分别布置于两个竖炉预热段02和还原段03的交界处,上述的第一冷却煤气进气口16、第二冷却煤气进气口26分别布置于两个竖炉的冷却段05上,相应的第一排料口17、第二排料口27分别位于两个竖炉冷却段05的下方;第一炉顶煤气溢出口12与第二炉顶煤气溢出口22通过管路连通,中间设置有换向阀组40,换向阀组40的出气口通过管道依次与除尘装置41、焦油捕集装置46、煤气净化装置42和煤气脱湿装置43连通;第一高温还原气环道13与第二高温还原气环道23通过管路连通,中间设置有高温还原气换向阀组50,高温还原气换向阀组50的进气口通过管道依次与氧气管道、加热炉51、外部煤气管道和炉顶煤气加压装置44连通;第一冷却煤气进气口16与第二冷却煤气进气口26通过管路连通,中间设置有冷却煤气阀组45,冷却煤气阀组45的进气口通过管道依次与炉顶煤气加压装置44连通;上述的煤气脱湿装置43出口与加热炉的煤气烧嘴和炉顶煤气加压装置44入口连通;炉顶煤气加压装置44的出口与外部煤气管道和冷却煤气阀组45连通。煤气脱湿装置出口与加热炉的煤气烧嘴和煤气脱co2装置入口连通;所述的炉顶煤气加压装置入口与煤气脱湿装置入口连通;炉顶煤气加压装置的出口与外部煤气管道和冷却煤气阀组连通。所述的煤气净化装置42具有脱除co2和h2s的功能。
使用该装置及其系统生产直接还原铁的方法为:
(1)采用热值为720~4000kcal/nm3的普通煤气为还原气,褐煤作为外配还原剂,按照入炉球团(15~35mm)与褐煤(15~50mm)质量比为1:0.2~0.35混合,自第一竖炉和第二竖炉的空料段同时连续加入;
(2)半焦炉煤气经加热炉加热至600~750℃,兑入部分氧气后,升温至950~1050℃,经高温还原气换向阀组送入第一竖炉内;球团与褐煤的混合料同高温还原气自上向下并行,过程中对球团进行还原反应,产生的h2o和co2与褐煤中的c进一步发生夺氧反应,生成co和h2后重新参与对球团矿的还原反应;
(3)高温还原气下行至等压段,自第一煤气环形通道、中间煤气通道进入第二竖炉,并向上逆行,依次穿过第二竖炉的等压段、还原段、预热段,过程中将热量传递给炉料,并发生还原反应和干馏反应;反应后的煤气温度降至150~200℃,自第二竖炉炉顶煤气溢出口排出,进入后续的除尘装置、焦油捕集装置、煤气净化装置和煤气脱湿装置中;
(4)净化、加压后的炉顶煤气自冷却煤气管路进入第一竖炉和第二竖炉的冷却段,通过对高温物料的冷却,温度从25~50℃升高至600~750℃;一部分自第一竖炉的等压段、第一煤气环形通道和中间煤气通道进入第二竖炉等压段内;另一部分直接穿过第二竖炉的冷却段进入等压段内;载热的冷却煤气在第二竖炉内向上逆行,依次穿过第二竖炉的等压段、还原段、预热段,过程中将热量传递给炉料,并发生还原反应和干馏反应;载热冷却煤气温度降至150~200℃,自第二竖炉炉顶煤气溢出口排出,经炉顶煤气换向阀组进入后续的除尘装置、焦油捕集装置、煤气净化装置和煤气脱湿装置中;
(5)高温还原气换向阀组和炉顶煤气换向阀组每间隔15~60min在线切换气流方向;使得焦炉煤气从第一竖炉切换至进入第二竖炉,并按照与上述相反的气流方向运行,完成对第二竖炉的并流加热和第一竖炉的逆流蓄热;
(6)过程控制中,高温还原气进气口压力为0.2~0.4mpa,冷却煤气的进气口压力为0.2~0.4mpa,竖炉的煤气环形通道和等压段内的压力为0.2~0.3mpa,炉顶煤气溢出口的压力为0.05~0.1mpa;预热段温度200~600℃,还原段温度为600~1050℃,等压段温度为700~950℃,冷却段温度为50~700℃;球团或块矿在竖炉内的停留时间约为14~20h,其中预热段停留的时间为3~5h,在还原段停留的时间为7~8h,在等压段内停留的时间为1-2h,冷却段停留的时间为3~5h;还原后的海绵铁和兰炭自冷却段连续排出,排料温度为600~700℃或50~120℃。
以上结合本实用新型实施例中的附图,对本实用新型实施例中的技术方案进行清楚、完整地描述;应当注意,在此所述的实施例仅为本实用新型中的部分实施例,而非本实用新型的全部实现方式,所述实施例只有示例性,其作用只在于为审查员及公众提供理解本
技术实现要素:
更为直观明了的方式,而不是对本实用新型技术方案的限制。在不脱离本实用新型技术方案构思的前提下,所有本领域普通技术人员没有做出创造性劳动就能想到的其他实施方案,及其他对本实用新型技术方案的简单替换和各种变化,都属于本实用新型的保护范围。
起点商标作为专业知识产权交易平台,可以帮助大家解决很多问题,如果大家想要了解更多知产交易信息请点击 【在线咨询】或添加微信 【19522093243】与客服一对一沟通,为大家解决相关问题。
此文章来源于网络,如有侵权,请联系删除


