一种用于车轮低压铸造的边模及模具的制作方法



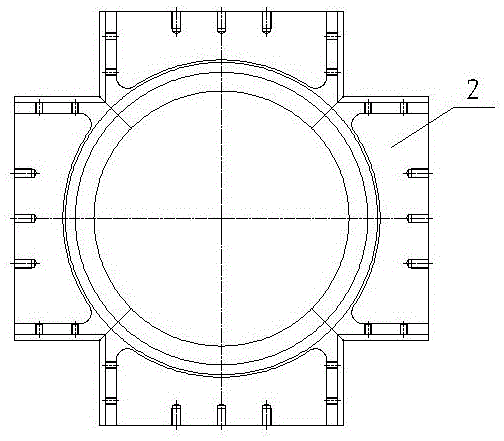
本申请涉及车轮的低压铸造模具技术领域,具体涉及一种用于车轮低压铸造的边模及模具。
背景技术:
低压铸造车轮模具一般采用四个边模,配合上模进行车轮轮辋的成型,在实际应用中效果较好。在铸造过程中,铝液会将大量的热量传递给边模,使其产生严重的热变形,造成车轮轮辋圆周方向的厚度不均,直接会影响到轮辋的成型、轮辋内部组织的均匀性以及质量稳定性,如果是轮辋需要旋压的毛坯,车轮轮辋圆周方向的的厚度不均,会影响轮辋旋压质量,且会使旋压后的轮辋末端产生高低不平的情况,以上问题会给轮辋旋压、后序机加工以及旋压后的车轮毛坯在轨道转运时带来了极大的影响。
技术实现要素:
本申请实施例提供了一种用于车轮低压铸造的边模及模具,可解决背景技术中的问题,在不影响铸造工艺的前提下,遵循模具热变形规律,通过合理设计边模,使整个轮辋在圆周方向上厚度更佳均匀。
为实现上述目的,本实用新型提供如下的技术方案:
第一方面,提供一种用于车轮低压铸造的边模,所述边模沿圆周均分为两块以上,在每块边模中部区域的轮辋型腔上边缘和轮辋型腔下边缘之间设置热变形补偿区域,所述热变形补偿区域为边模轮辋型腔的内凹区域。
在一些实施例中,所述内凹区域的最大内凹径向距离为大约0.5mm~大约1mm。
在一些实施例中,所述热变形补偿区域的范围小于每块边模的轮辋型腔。
在一些实施例中,所述热变形补偿区域的长度为每块边模的圆周长度的大约5/9~大约8/9。
在一些实施例中,所述内凹区域呈圆弧形。
在一些实施例中,在每块边模的中间位置所述热变形补偿区域的内凹径向距离最大,并且所述内凹径向距离从中间位置向两侧沿一圆弧逐渐递减。
在一些实施例中,所述边模沿圆周均分为4块,在每块边模的中间位置所述热变形补偿区域的内凹径向距离最大,并且所述内凹径向距离从中间位置向两侧沿一圆弧逐渐递减;所述热变形补偿区域的圆弧夹角为大约50°~大约80°。
另一方面,本申请实施例中提供了一种用于车轮低压铸造的模具,包括上模、下模和边模,上模、下模和边模围成铝合金车轮的铸造型腔,所述边模为上述任一实施例中所述的一种用于车轮低压铸造的边模。
与现有技术相比,本实用新型的有益效果为:
本申请提供了一种用于车轮低压铸造的边模及模具,在所述边模的轮辋型腔上边缘和轮辋型腔下边缘之间设置热变形补偿区域,所述热变形补偿区域可以补偿边模热态下的热变形量,在不影响铸造工艺的前提下,遵循模具热变形规律,通过合理设置边模型腔的热变形补偿量,补偿了边模热态下的热变形量,实现了车轮轮辋圆周方向上厚度的均匀性,提高了铸造过程中轮辋的内部组织均匀性以及内部铸造质量,同时解决了轮辋旋压后的轮辋末端产生高低不平的情况,进而解决了轮辋旋压、后序机加工以及旋压后的车轮毛坯在轨道转运时的种种问题。
附图说明
为了更清楚地说明本申请实施例中的技术方案,下面将对实施例描述中所需要使用的附图作简单地介绍,显而易见地,下面描述中的附图是本申请的一些实施例,对于本领域普通技术人员来讲,在不付出创造性劳动的前提下,还可以根据这些附图获得其他的附图。
图1是本申请一种用于车轮低压铸造的边模组装结构示意图;
图2是本申请一种用于车轮低压铸造的边模的轮辋型腔范围示意图;
图3是本申请一种用于车轮低压铸造的边模的热变形补偿区域示意图;
图4是本申请一种用于车轮低压铸造的模具的示意图;
其中:1-上模、2-边模、3-下模、4-轮辋型腔范围、5-热变形补偿区域、a-边模轮辋型腔下边缘、b-边模轮辋型腔上边缘、c-边模轮辋型腔上边缘的热变形补偿区域的左端点、d-边模轮辋型腔上边缘的热变形补偿区域的右端点、e-边模轮辋型腔下边缘的热变形补偿区域的左端点、f-边模轮辋型腔下边缘的热变形补偿区域的右端点、g-边模轮辋型腔上边缘中间点、g1-边模轮辋型腔上边缘的热变形补偿区域的中间点、h-边模轮辋型腔下边缘中间点、h1-边模轮辋型腔下边缘的热变形补偿区域的中间点、i-边模轮辋型腔上边缘左端点、j-边模轮辋型腔上边缘右端点、k-边模轮辋型腔下边缘左端点、l-边模轮辋型腔下边缘右端点、0-为圆心。
具体实施方式
本申请的说明书和权利要求书及所述附图中的术语“第一”、“第二”、“第三”和“第四”等是用于区别不同对象,而不是用于描述特定顺序。此外,术语“包括”和“具有”以及它们任何变形,意图在于覆盖不排他的包含。例如包含了一系列步骤或单元的过程、方法、系统、产品或设备没有限定于已列出的步骤或单元,而是可选地还包括没有列出的步骤或单元,或可选地还包括对于这些过程、方法、产品或设备固有的其它步骤或单元。此外,当使用“大约”来描述值时,这意味着包含由所述值的微小变化(至多+/-10%)。
在本文中提及“实施例”意味着,结合实施例描述的特定特征、结构或特性可以包含在本申请的至少一个实施例中。在说明书中的各个位置出现该短语并不一定均是指相同的实施例,也不是与其它实施例互斥的独立的或备选的实施例。本领域技术人员显式地和隐式地理解的是,本文所描述的实施例可以与其它实施例相结合。
本文中已经发现在铸造过程中,铝液会将大量的热量传递给边模,使其产生严重的热变形,使边模产生规律性的扭曲变形,边模中部向中心移动,边模两侧向远离中心方向移动,这就造成边模中部的轮辋偏薄,边模两侧接缝部位轮辋偏厚的情况,造成车轮轮辋圆周方向的厚度不均。为了解决上述问题,本申请实施例中提供了一种用于车轮低压铸造的边模,所述边模沿圆周均分为两块以上,在每块边模中部区域的轮辋型腔上边缘和轮辋型腔下边缘之间设置热变形补偿区域,所述热变形补偿区域为边模轮辋型腔的内凹区域。所述热变形补偿区域可以补偿边模热态下的热变形量,使低压铸造车轮轮辋圆周方向上厚度均匀,通过改善轮辋厚度的均匀性,使轮辋的成型、轮辋内部组织的均匀性、质量稳定性大大提高,并能满足旋压轮辋的种种需要。同时,能够延长模具使用寿命,在机械加工中节约工时和耗材,降低车轮的制造成本,提高企业的盈利能力。
为了使低压铸造车轮轮辋圆周方向上厚度复合工艺标准,不会误差过大,在本申请的一个实施例中,所述内凹区域的最大内凹径向距离优选为大约0.5mm~大约1mm。
在铸造过程中发现边模受热中部向中心移动,边模两侧向远离中心方向移动,因此优先考虑对边模的中部区域进行热变形补偿,在本申请的一个实施例中,优选所述热变形补偿区域的范围小于每块边模的轮辋型腔。因此,从边模的中部区域到两侧边缘区域热变形补偿逐渐减小,甚至边模的边缘区域不进行热变形补偿。
为了获得较优的补偿结果,获得轮辋厚度更均匀的低压铸造车轮,在本申请的一个实施例中,所述热变形补偿区域的长度优选为每块边模的圆周长度的大约5/9~大约8/9。
为了热变形补偿均匀,使铸造成型的车轮轮辋表面平整,降低后续处理难度和成本,在本申请的一个实施例中,优选所述内凹区域呈圆弧形。在本申请的另一个实施例中,优选地,在每块边模的中间位置所述热变形补偿区域的内凹径向距离最大,并且所述内凹径向距离从中间位置向两侧沿一圆弧逐渐递减。
较常用的低压铸造车轮模具一般采用四个边模,配合上模和下模进行车轮轮辋的成型,在实际应用中效果较好,在本申请的一个实施例中,所述边模沿圆周均分为4块,在每块边模的中间位置所述热变形补偿区域的内凹径向距离最大,并且所述内凹径向距离从中间位置向两侧沿一圆弧逐渐递减;所述热变形补偿区域的圆弧夹角为大约50°~大约80°。
另一方面,本申请实施例中提供了一种用于车轮低压铸造的模具,包括上模、下模和边模,上模、下模和边模围成铝合金车轮的铸造型腔,所述边模为上述任一实施例中所述的一种用于车轮低压铸造的边模。所述用于车轮低压铸造的模具,在所述边模的轮辋型腔上边缘和轮辋型腔下边缘之间设置热变形补偿区域,所述热变形补偿区域可以补偿边模热态下的热变形量,在不影响铸造工艺的前提下,遵循模具热变形规律,通过合理设置边模型腔的热变形补偿量,补偿了边模热态下的热变形量,实现了车轮轮辋圆周方向上厚度的均匀性,提高了铸造过程中轮辋的内部组织均匀性以及内部铸造质量,同时解决了轮辋旋压后的轮辋末端产生高低不平的情况,进而解决了轮辋旋压、后序机加工以及旋压后的车轮毛坯在轨道转运时的种种问题。
下面将结合本申请实施例中的附图,对本申请实施例中的技术方案进行清楚、完整地描述,显然,所描述的实施例是本申请一部分实施例,而不是全部的实施例。基于本申请中的实施例,本领域普通技术人员在没有作出创造性劳动前提下所获得的所有其他实施例,都属于本申请保护的范围。
实施例1:
本申请实施例1中提供了一种用于车轮低压铸造的边模,如图1中所示,所述边模2沿圆周均分为4块,在每块边模2中部区域的轮辋型腔上边缘和轮辋型腔下边缘之间设置热变形补偿区域5,所述热变形补偿区域5为边模轮辋型腔的内凹区域。所述内凹区域呈圆弧形,在每块边模2的中间位置所述热变形补偿区域5的内凹径向距离最大,并且所述内凹径向距离从中间位置向两侧沿一圆弧逐渐递减。
为了便于理解,在图2-3中标记了以下的辅助点:a-边模轮辋型腔下边缘、b-边模轮辋型腔上边缘、c-边模轮辋型腔上边缘的热变形补偿区域5的左端点、d-边模轮辋型腔上边缘的热变形补偿区域5的右端点、e-边模轮辋型腔下边缘的热变形补偿区域5的左端点、f-边模轮辋型腔下边缘的热变形补偿区域5的右端点、g-边模轮辋型腔上边缘中间点、g1-边模轮辋型腔上边缘的热变形补偿区域5的中间点、h-边模轮辋型腔下边缘中间点、h1-边模轮辋型腔下边缘的热变形补偿区域5的中间点、i-边模轮辋型腔上边缘左端点、j-边模轮辋型腔上边缘右端点、k-边模轮辋型腔下边缘左端点、l-边模轮辋型腔下边缘右端点、0-圆心。
a~b轴向范围为边模形成轮辋的区域。b为边模轮辋型腔的上边缘,在b所在的原有i-c-g-d-j(该五点共圆)改进前圆弧上,加工出端点为c、d点且通过g1点的热变形补偿圆弧,c、g1、d三点共圆,为热变形补偿圆弧。g、g1两点距离最大,向c、d两点靠近,c-g-d和c-g1-d两圆弧距离逐渐靠近,直至相交,i-c-g1-d-j为改进后圆弧线,并且c、d点位于原始圆弧上,即本实施例中改进后的边模轮辋型腔的上边缘为i-c-g1-d-j圆弧线。
a为边模轮辋型腔的下边缘,在a点所在的原有k-e-h-f-l(该五点共圆)改进前圆弧上,加工出端点为e、f点,且通过h1点的热变形补偿圆弧,e、h1、f三点共圆,为热变形补偿圆弧,h、h1两点距离最大,向e、f两点靠近,e-h-f和e-h1-f两圆弧距离逐渐靠近,直至相交,k-e-h1-f-l为改进后圆弧线,并且e、f点位于原始圆弧上,即本实施例中改进后的边模轮辋型腔的下边缘为k-e-h1-f-l圆弧线。
a~b轴向范围内的c、d、e、f区域为边模轮辋型腔的热补偿区域,四块边模轮辋型腔均按该方案以此类推进行热补偿加工。所述内凹区域的最大内凹径向距离为0.5~1mm,也即边模轮辋型腔最大补偿距离g、g1点的距离和h、h1点的距离为0.5~1mm,g-g1点的距离和h-h1点的距离相等。所述热变形补偿区域5的范围小于每块边模的轮辋型腔,所述热变形补偿区域5的长度为每块边模的圆周长度的5/9~8/9,即所述热变形补偿区域5的圆弧夹角为50°~80°。在图3所示的俯视图中,ce连线及df连线均通过圆心0点,圆心0也即边模2的中心,ce连线及df连线间的夹角为50°~80°;
在本实施例1中热变形补偿区域5的圆弧夹角,也即图3中ce与df的夹角为60°,边模轮辋型腔最大补偿距离g、g1点距离和h、h1点距离均为0.6mm。
使用实施例1中的所述边模,在模具正常工作条件(铝液700℃,模具温度保持正常的温度场)下进行a356铝合金车轮铸造试验。按照以上方法进行普通车轮及需旋压的轮辋车轮各1000件的铸造,结果显示:使用金相显微镜方法,对使用本实用新型的低压铸造边模的车轮轮辋金相结构进行观察,发现铝合金车轮轮辋的切面上晶粒组织较均匀;在轮辋圆周上均与选取10个轮辋样块制作试验棒,用专用的拉伸试验机进行拉伸试验,较改进前,轮辋试验棒伸长率数值差别极小,较均匀;旋压轮辋旋压后的轮辋末端高低不平的现象消失。
实施例2:
实施例2与实施例1的不同之处在于:热变形补偿区域5的圆弧夹角,也即图3中ce与df的夹角为50°,边模轮辋型腔最大补偿距离g、g1点距离和h、h1点距离均为0.5mm。
实施例3:
实施例3与实施例1的不同之处在于:热变形补偿区域5的圆弧夹角,也即图3中ce与df的夹角为70°,边模轮辋型腔最大补偿距离g、g1点距离和h、h1点距离均为0.8mm。
实施例4:
实施例4与实施例1的不同之处在于:热变形补偿区域5的圆弧夹角,也即图3中ce与df的夹角为80°,边模轮辋型腔最大补偿距离g、g1点距离和h、h1点距离均为1mm。
同样使用实施例2-4中的所述边模,在模具正常工作条件(铝液700℃,模具温度保持正常的温度场)下进行a356铝合金车轮铸造试验,同样取得了上述良好效果。以上的各实施例中的所述边模极大的改善了车轮轮辋在圆周方向上厚度不均的问题,同时解决了因轮辋厚度不均而产生的一系列问题,带来了良好的经济和社会效益。
实施例5:
本申请实施例1中提供了一种用于车轮低压铸造的模具,如图4中所示,包括上模1、边模2和下模3,上模1、下模3和四块边模2组合成铝合金车轮的铸造型腔;所述边模2为上述任一实施例中所述的一种用于车轮低压铸造的边模。所述用于车轮低压铸造的模具,在所述边模的轮辋型腔上边缘和轮辋型腔下边缘之间设置热变形补偿区域,所述热变形补偿区域可以补偿边模热态下的热变形量。
本实用新型提供了一种用于车轮低压铸造的模具,带来了以下的有益效果:
(1)通过在四块边模的轮辋型腔区域设置热变形补偿,实现了车轮轮辋圆周方向上厚度的均匀性;
(2)车轮轮辋圆周方向上的厚度均匀,提高了铸造过程中轮辋的内部组织均匀性以及内部铸造质量;
(3)车轮轮辋圆周方向上的厚度均匀,解决了旋压轮辋旋压后的轮辋末端产生高低不平的情况,进而解决了轮辋旋压、后序机加工以及旋压后的车轮毛坯在轨道转运时的种种问题。
以上对本申请实施例进行了详细介绍,本文中应用了具体个例对本申请的原理及实施方式进行了阐述,以上实施例的说明只是用于帮助理解本申请的方法及其核心思想;同时,对于本领域的一般技术人员,依据本申请的思想,在具体实施方式及应用范围上均会有改变之处,综上所述,本说明书内容不应理解为对本申请的限制。
起点商标作为专业知识产权交易平台,可以帮助大家解决很多问题,如果大家想要了解更多知产交易信息请点击 【在线咨询】或添加微信 【19522093243】与客服一对一沟通,为大家解决相关问题。
此文章来源于网络,如有侵权,请联系删除


