基于低温共烧陶瓷技术的表面贴装保险丝及其制备方法与流程



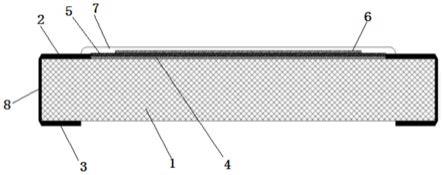
[0001]
本发明涉及表面贴装保险丝技术领域,特别涉及一种基于低温共烧陶瓷技术的表面贴装保险丝及其制备方法。
背景技术:
[0002]
表面贴装熔断器主要应用于印刷电路板和其它电路的过流保护,其原理在于当电路发生故障或异常时,熔断器金属熔体自身熔断切断电流以实现保护电路。金属熔体的周围都被其基体部分的高分子材料或陶瓷材料所紧紧围贴着,即使是已经熔化的金属也无法向两端收缩,只能依靠向周围材料的扩散渗透或被周围材料吸收,如果在这个过程中过电流消失了(例如瞬间脉冲现象)或者产生的热量被基材迅速散掉,而扩散或吸收的过程尚在进行过程中,此时就会造成电阻变大而熔体没有完全熔断的现象。
[0003]
此外,在表面贴装保险丝中,毫安级别的保险丝因电流低,所以发热量小,陶瓷基板的散热较快,对保险丝熔断效果有影响。再有,现有的表面贴装保险丝使用玻璃釉做隔热层会存在玻璃熔化吃银的现象,对熔断器的阻值影响比较大,所以在陶瓷基板上面生产的毫安级别的保险丝存在良率不高,性能不稳定的问题。
技术实现要素:
[0004]
为解决上述技术问题,本发明的目的在于提供一种基于低温共烧陶瓷技术的表面贴装保险丝及其制备方法,该制备方法利用低温共烧陶瓷技术,解决了熔丝电极浆料印刷时扩散和表面不平整的问题,使熔丝的图形更加完整、清晰,可控性较高;制备的表面贴装保险丝熔断过程迅速,而且不会出现拉弧的现象。
[0005]
为实现上述技术目的,达到上述技术效果,本发明通过以下技术方案实现:
[0006]
一种基于低温共烧陶瓷技术的表面贴装保险丝的制备方法,包括如下步骤:
[0007]
步骤一,制备低温共烧陶瓷粉
[0008]
称取氧化钙粉体30-40份、氧化硼粉体25-35份、氧化硅粉体35-45份,置入球磨罐中,进行球磨,再利用筛网对球磨后的物料进行分离,得到混合粉体;
[0009]
将混合粉体于1200℃-1300℃的温度条件下加热0.5-1h,得到熔融料,将该熔融料置于去离子水中进行水淬,得到玻璃渣;
[0010]
将得到的玻璃渣放入球磨罐中,并加入无水乙醇,进行球磨,再利用筛网对球磨后的物料进行分离,所得料液经烘干,得到ca-b-si系微晶玻璃粉;
[0011]
取ca-b-si系微晶玻璃粉80-90份、1-2μm氧化锆粉体10-20份,置于球磨罐中,进行球磨,再利用筛网对球磨后的物料进行分离,得到低温共烧陶瓷粉;具体的,该低温共烧陶瓷粉可以配置为微晶玻璃粉与氧化锆粉体的比例不同的两种;
[0012]
步骤二,配制有机载体
[0013]
该有机载体的制备原料包括丙烯酸树脂、溶剂和成膜剂,其中丙烯酸酯的含量为20-30%,成膜剂的含量为3%-8%;
[0014]
步骤三,制备低温共烧陶瓷浆料
[0015]
取有机载体和低温共烧陶瓷粉,混合后,再经辊轧,得到低温共烧陶瓷浆料;配制的低温共烧陶瓷浆料包括两种,一种为隔热层用低温共烧陶瓷浆料,另一种为灭弧层用低温共烧陶瓷浆料;隔热层用低温共烧陶瓷浆料的固含量为75-80%,灭弧层用低温共烧陶瓷浆料的固含量为65-70%,且灭弧层用低温共烧陶瓷浆料所采用的低温共烧陶瓷粉中的氧化锆的相对用量高于隔热层用低温共烧陶瓷浆料所采用的低温共烧陶瓷粉中的氧化锆的相对用量;
[0016]
步骤四,制备熔丝电极浆料
[0017]
按照重量份数称取:ca-b-si系微晶玻璃粉10-20份,5-10μm片式银粉40-50份,球形亚微米级银粉10-20份,锡铋合金粉5-10份,固体粉体分散剂1-5份,气相二氧化硅粉1-5份,有机载体15-25份,混合均匀后,得到熔丝电极混合料,再对该熔丝电极混合料进行研磨,得到熔丝电极浆料;
[0018]
步骤五,制备端电极浆料和背电极浆料
[0019]
端电极浆料:按照重量份数称取高温玻璃粉1-5份,1-3μm球形银粉60-80份,球形亚微米级银粉10-20份,有机载体10-15份,混合均匀后,得到端电极混合料,再对该端电极混合料进行研磨,得到端电极浆料;
[0020]
背电极浆料:按照重量份数分别称取高温玻璃粉5-10份,1-3μm球形银粉50-60份,有机载体30-40份,混合均匀后,得到背电极混合料,再对该背电极混合料进行研磨,得到背电极浆料;
[0021]
步骤六,制备正电极层和背电极层
[0022]
在陶瓷基板的正面端部印刷步骤五制备的端电极浆料,在陶瓷基板的背面端部印刷步骤五制备的背电极浆料,烧结后,形成正电极层和背电极层;
[0023]
步骤七,印刷共烧浆料
[0024]
在经过步骤六处理后的陶瓷基板的表面印刷固含量为75-80%的隔热层用低温共烧陶瓷浆料;
[0025]
按照设计的保险丝的图形,在隔热层用低温共烧陶瓷浆料层上,印刷熔丝电极浆料;
[0026]
在熔丝电极浆料层上印刷固含量为65-70%的灭弧层用低温共烧陶瓷浆料;
[0027]
步骤八,共烧
[0028]
将经印刷后的陶瓷基板经过排胶处理,再进行烧结,得到表面贴装保险丝半成品;共烧后,陶瓷基板上依次形成有隔热层、熔丝层和灭弧层。
[0029]
进一步的,步骤一的制备混合粉体的过程中,球磨过程的球料比为4:1,球磨时间为4小时,分离时采用的筛网规格为80目;
[0030]
步骤一的制备ca-b-si系微晶玻璃粉的过程中,球磨过程的球料比为5:1,球磨机转速为300rpm,球磨时间为12小时,分离时采用的筛网规格为300目;
[0031]
步骤一中,将ca-b-si系微晶玻璃粉和氧化锆粉体置于球磨罐中进行球磨,球料比为4:1,球磨时间为4小时,分离时采用的筛网规格为80目。
[0032]
优选的,步骤二中,配制有机载体采用的溶剂选自松油醇、丁基卡必醇醋酸酯、dbe、柠檬酸三丁酯、dop中的一种或两种及以上的组合,采用的成膜剂为十二醇酯。
[0033]
进一步的,步骤四中,将熔丝电极浆料研磨至细度10μm以下;.步骤五中,将端电极浆料研磨至细度5μm以下。
[0034]
进一步的,步骤七中,保险丝的图形根据熔丝的阻值要求进行设计。
[0035]
进一步的,步骤八中,排胶温度设定为400-500℃,排胶保温时间为30min,共烧温度设定为800-850℃,共烧保温时间为15min。
[0036]
进一步的,共烧结束后,在表面贴装保险丝半成品的灭弧层上涂布低温玻璃浆料,作为保护层浆料。
[0037]
更进一步的,涂布保护层浆料后,再在表面贴装保险丝半成品的表面印刷标识浆料,再将保护层浆料和标识浆料一起烧结,获得具有玻璃保护层和标识字符的表面贴装保险丝半成品。
[0038]
更进一步的,该制备方法还包括后处理工序,该后处理工序包括依次进行的堆叠、溅射、折粒和电镀,具体为:将表面贴装保险丝半成品堆叠成产品条,然后,在产品条侧面溅射一层可镀性的金属,再利用折粒机折成小颗粒的保险丝器件单元半成品,对保险丝器件单元半成品进行电镀,制得表面贴装保险丝成品。
[0039]
本发明还提供了利用上述制备方法制得的一种表面贴装保险丝。
[0040]
本发明的有益效果是:
[0041]
(1)利用本发明的制备方法制得的表面贴装保险丝熔断性能较好,熔断时间比较集中,熔断过程迅速,无拉弧现象;具体的,表面贴装保险丝的隔热层摒弃常规的玻璃材料,采用低温共烧陶瓷材料,而且其中的灭弧层也采用低温共烧陶瓷材料;低温共烧陶瓷材料采用ca-b-si系微晶玻璃粉和氧化锆粉体制成,其中的氧化锆粉体热导率较低,熔点较高,可以很好的解决熔丝通电过程中散热的问题,使热量更好的集中在保险丝的内部,使熔断过程迅速,而且不会出现拉弧现象;其中的ca-b-si系微晶玻璃粉可以提高低温共烧陶瓷材料的致密度;ca-b-si系微晶玻璃粉与氧化锆粉体的比例调节可以控制低温共烧陶瓷材料的烧后致密程度,满足隔热层和灭弧层的性能要求。隔热层致密度较高,可以防止熔丝电极浆料在丝网印刷时扩散以及金属在烧结过程中熔化后渗透;灭弧层致密度低,为疏松结构,在烧结过程中不会对熔丝电极浆料造成破坏,并有助于熔丝的灭弧。
[0042]
(2)本发明采用隔热层-熔丝层-灭弧层共烧的工艺,从而在印刷熔丝电极浆料的过程中,由于隔热层为未烧结层而且平整性较好,熔丝电极浆料在其表面浸润性较好,浆料印刷后的图形比较清晰、集中,不会出现流淌的现象,而且浆料的流平性较好,烧结后阻值比较集中稳定。此外,本发明采用共烧工艺,且灭弧层为疏松层,不会对熔丝产生影响,避免了灭弧层烧结过程对熔丝破坏所引发的阻值升高。
[0043]
(3)本发明采用隔热层-熔丝层-灭弧层共烧的工艺,区别于传统工艺印刷一次烧结一次的繁琐过程,可以减少烧结次数,减少能耗,避免了因烧结工序过多引发的碎片问题以及熔丝过烧等造成的良率下降问题。
[0044]
(4)本发明采用片式银粉替代金粉作为熔丝电极浆料的主体材料,不仅可以大大降低成本,而且可以满足高温烧结后熔丝较薄阻值较大的ma级保险丝要求。
[0045]
(5)常规印刷厚膜工艺生产的毫安级贴片保险丝阻值相对较大,500毫安级的贴片保险丝阻值在1ω左右,250毫安级的贴片保险丝阻值在4ω左右,125毫安的贴片保险丝,阻值要高达15ω左右,对电路中的电流会产生较大影响。本发明由于采用了独特的熔丝电极
浆料和低温共烧陶瓷材料的低热导率性能,可以将125毫安的贴片保险丝的阻值降低至4ω左右,其他规格的产品的阻值也会相应的降低,从而对线路的影响较小。
附图说明
[0046]
图1是本发明实施例1的表面贴装保险丝的结构示意图。
[0047]
图2是本发明实施例1的表面贴装保险丝中的熔丝图案示意图。
具体实施方式
[0048]
下面将结合具体实施例对本发明中的技术方案进行清楚、完整地描述,显然,所描述的实施例仅仅是本发明一部分实施例,而不是全部的实施例。基于本发明中的实施例,本领域普通技术人员在没有做出创造性劳动前提下所获得的所有其他实施例,都属于本发明保护的范围。
[0049]
实施例1
[0050]
该实施例1的一种基于低温共烧陶瓷技术的表面贴装保险丝的制备方法,包括如下步骤:
[0051]
步骤一,制备低温共烧陶瓷粉
[0052]
称取氧化钙粉体30份、氧化硼粉体25份、氧化硅粉体35份,置入500ml的氧化锆材质的球磨罐中,进行球磨,球料比为4:1,干粉球磨4小时,冷却后超声过80目筛网,分离得到混合粉体;
[0053]
取250ml的铂金坩埚,于高温炉中1250℃预热30min,然后将混合粉体置于铂金坩埚中,在高温炉中于1250℃的温度条件下对混合粉体加热30min,待氧化物粉末未完全熔化时,取出铂金坩埚,得到熔融料,并将该熔融料置于去离子水中进行水淬,得到玻璃渣;
[0054]
将得到的玻璃渣放入氧化锆球磨罐中,球料比为5:1,并加入150ml的无水乙醇,球磨机以300rpm的转速,球磨12小时,球磨后的物料再经过300目筛网分离,所得料液经150℃烘干4小时,得到ca-b-si系微晶玻璃粉;
[0055]
取ca-b-si系微晶玻璃粉80份、1-2μm氧化锆粉体10份,置于500ml的氧化锆球磨罐中,球料比为4:1,干粉球磨4小时,冷却后超声过80目筛网,分离得到低温共烧陶瓷粉一;另外取ca-b-si系微晶玻璃粉80份、1-2μm氧化锆粉体13份,置于500ml的氧化锆球磨罐中,球料比为4:1,干粉球磨4小时,冷却后超声过80目筛网,分离得到低温共烧陶瓷粉二。通过调节微晶玻璃粉和氧化锆粉体的比例,可以在后续的共烧过程中获得致密的隔热层和疏松的灭弧层;
[0056]
步骤二,配制有机载体
[0057]
该有机载体的制备原料包括丙烯酸树脂、松油醇和十二醇酯,其中丙烯酸酯的含量为20%,成膜剂的含量为5%,余量为松油醇。
[0058]
步骤三,制备低温共烧陶瓷浆料
[0059]
取有机载体和低温共烧陶瓷粉,混合后,再经三辊机辊轧,得到低温共烧陶瓷浆料;配制的低温共烧陶瓷浆料包括两种,一种为隔热层用低温共烧陶瓷浆料,利用的是低温陶瓷共烧陶瓷粉一,另一种为灭弧层用低温共烧陶瓷浆料,利用的是低温共烧陶瓷粉二;隔热层用低温共烧陶瓷浆料的固含量为75%,灭弧层用低温共烧陶瓷浆料的固含量为65%;
[0060]
本发明采用丙烯酸树脂作为浆料的粘合剂,由于丙烯酸树脂的分子量相对较小,粘度较低,空气条件下烧结过程中排胶比较干净,不容易发生积碳的现象,使浆料烧结后的表面比较平滑和致密。
[0061]
步骤四,制备熔丝电极浆料
[0062]
按照重量份数称取:ca-b-si系微晶玻璃粉10份,5-10μm片式银粉40份,球形亚微米级银粉10份,锡铋合金粉5份,固体粉体分散剂2份,气相二氧化硅粉2份,有机载体15份,混合均匀后,得到熔丝电极混合料,再对该熔丝电极混合料利用三辊研磨机进行研磨,研磨至细度10μm以下,得到熔丝电极浆料;
[0063]
本发明采用5-10μm片式银粉作为主导电材料,由于其印刷烧结后形成的导电层较薄,有利于熔断,同时添加了部分球形亚微米粉作为辅助导电粉体,防止片式银粉收缩时出现断线的问题。同时浆料中添加一定量的低温共烧陶瓷体系中的微晶玻璃粉体,共烧过程中,微晶玻璃粉体和片式银粉两者的匹配度较高,不会产生因收缩不匹配造成的外观不良。添加的无机填料(固体粉体分散剂和气相二氧化硅粉)可以增加熔丝的电阻,同时在熔断过程中还具有灭弧的功能,瞬间拉开断点的距离,可以快速的切断电流。为了更好的使熔丝熔断,该熔丝电极浆料添加了低熔点的锡铋合金,由于该合金的熔点在300℃以下,从而,熔丝通电产生热量时能迅速熔化并与周围的银熔合形成锡铋银合金,能快速的被周围的灭弧材料吸收,使熔断过程安全迅速。
[0064]
浆料中添加的气相二氧化硅还有利于浆料进行细线印刷,且气相二氧化硅的高触变性,能增加浆料的粘稠度,有利于图形的收缩,添加后熔丝电极浆料印刷的线宽最小可以达到50μm。
[0065]
步骤五,制备端电极浆料和背电极浆料
[0066]
端电极浆料:按照重量份数分别称取高温玻璃粉5份,1-3μm球形银粉60份,球形亚微米级银粉20份,有机载体15份,混合均匀后,得到端电极混合料,再利用三辊研磨机对该端电极混合料进行研磨,研磨至细度为5μm以下,得到端电极浆料;
[0067]
背电极浆料:按照重量份数分别称取高温玻璃粉10份,1-3μm球形银粉50份,有机载体40份,混合均匀后,得到背电极混合料,再利用三辊研磨机对该背电极混合料进行研磨,研磨至细度为5μm以下,得到背电极浆料。
[0068]
为保证端电极优异的导电性能,防止因熔断过程中熔丝与端电极的接触电阻过大造成的接触点熔断不良现象,本发明采用银含80%以上的端电极浆料。
[0069]
步骤六,制备正电极层和背电极层
[0070]
在陶瓷基板的正面端部印刷步骤五制备的端电极浆料,在陶瓷基板的背面端部印刷步骤五制备的背电极浆料,烧结后,形成正电极层和背电极层;为保证后续和熔丝的良好接触,正电极网版的厚度和图形大小是背电极的约1.2-1.5倍。正电极层和背电极层采用850℃烧结后再进行后续的印刷工作。
[0071]
步骤七,印刷共烧浆料
[0072]
在经过步骤六处理后的陶瓷基板的正面印刷固含量为75%的隔热层用低温共烧陶瓷浆料;印刷采用不锈钢丝网2次印刷工艺,第一次印刷完成后烘干,将陶瓷基板旋转180
°
后,再完成第二次印刷,并烘干;旋转的2次印刷工艺,确保了印刷后表面的平整性。
[0073]
根据熔丝的阻值要求设计保险丝的图形,如图2所示,按照图形,在隔热层用低温
共烧陶瓷浆料层上印刷熔丝电极浆料;更具体的,为保证阻值的稳定性,保险丝在制备过程中采取熔丝电极浆料2次印刷的方式;其中的图形设计根据阻值公式:r=ρl/s,同等厚度条件下,线长越长阻值越大。本实施例的图形设计采用弯曲设计,等同于线长增加了一倍,同等阻值条件下,厚度可以加大一倍,因此可以增加印刷次数,从而保证熔丝电极浆料印刷后的厚度均匀性,有利于烧结后熔丝阻值的均匀性提高,也使熔断性能更好。印刷熔丝电极浆料时,由隔热层用低温共烧陶瓷浆料层未进行烧结,熔丝电极浆料印刷后表面不会出现流延的现象,线宽保持的比较好,也提高了阻值的稳定性。
[0074]
然后,在熔丝电极浆料层上印刷固含量为65%的灭弧层用低温共烧陶瓷浆料;灭弧层用低温共烧陶瓷浆料中由于玻璃含量相对少,烧后致密度较低,烧结过程中不会对熔丝浆料造成破坏,还能有助于熔丝的灭弧;当温度急剧升高时,熔丝熔断产生的金属蒸汽会迅速被表面的微孔吸附,快速切断电路。此外,由于ca-b-si系微晶玻璃粉的密度和粒径低于添加的氧化锆的密度和粒径,共烧时玻璃粉颗粒会随着排胶气流逐渐上移,从而在灭弧层表面富集较多,灭弧层底部区域容易形成孔洞;该孔洞的形成可以明显的提高灭弧效果,防止拉弧的发生。
[0075]
步骤八,共烧
[0076]
将经印刷后的陶瓷基板置于链式炉中进行排胶,排胶温度设定为450℃,保温30min,让所有的步骤七中的印刷浆料层充分排胶,防止后续烧结出现排胶不充分引发的积碳孔洞和微裂痕;然后,进行烧结,烧结温度设定为840℃,保温15min,使各印刷浆料层均能充分熔化烧结;烧结后降温,降温时间设定为30min;
[0077]
共烧后,陶瓷基板上依次形成有隔热层、熔丝层和灭弧层,从而得到表面贴装保险丝半成品。
[0078]
步骤十,保护层浆料和标识浆料印刷
[0079]
由于烧结后的灭弧层质地比较脆,容易在后续堆叠折粒工序中被压破,所以需要在灭弧层表面加盖玻璃保护层。具体操作过程为:在步骤八共烧后的贴装保险丝半成品的灭弧层表面,利用丝网印刷涂布低温玻璃浆料,作为保护层浆料,并使其均匀的完全覆盖隔热层、熔丝层和灭弧层区域;
[0080]
由于保险丝器件的阻值不一样,且熔断特性也不一样,为区分不同的产品型号,需要在保险丝器件的最外表面印刷标识字符;本实施例采用白色玻璃浆料作为标识浆料;
[0081]
为保证表面的平整性,将标识浆料和保护层浆料一起烧结,相互熔合后表面平整性较好,不会因表面不平引发抛料的问题。
[0082]
步骤十一,后处理工序
[0083]
该后处理工序包括堆叠、溅射、折粒和电镀,具体为:将经过上述十个步骤处理得到的表面贴装保险丝半成品经折条机沿剥离线堆叠成产品条,然后放置在溅射治具内,通过溅射炉在产品条侧面溅射一层可镀性的金属,并通过调节溅射时间和电流值改变金属层的厚度;溅射好的产品条再经折粒机折成符合尺寸规格的小颗粒的保险丝器件单元半成品;将符合尺寸规格的保险丝器件单元半成品经ph值为中性的电镀液电镀后,得到表面贴装保险丝成品;其中的电镀液为中性,可以防止酸碱电镀液对产品的损坏;且在电镀前,要对正电极层、背电极层和溅射金属层进行清理,电镀时滚动速度要均匀,当产品的电极层符合规矩范围后,结束电镀,防止电镀趴锡,影响器件的外观良率。
[0084]
如图1所示,实施例1得到的表面贴装保险丝,包括陶瓷基板1,陶瓷基板1的正面端部设有正电极层2,陶瓷基板的背面端部设有背电极层3,陶瓷基板1的正面上从下至上依次设有位于两端正电极层之间的隔热层4、熔丝层5、灭弧层6、玻璃保护层7,表面贴装保险丝的最外表面还设有标识字符;表面贴装保险丝的侧端还设有溅射后电镀sn金属层8。
[0085]
实施例2
[0086]
该实施例2的表面贴装保险丝的制备方法同实施例1,其与实施例1的区别在于:
[0087]
实施例2的步骤一的混合粉体包括氧化钙粉体35份、氧化硼粉体30份、氧化硅粉体40份;步骤一中,在制备低温共烧陶瓷粉时,两种低温共烧陶瓷粉分别为,一种是:其含有ca-b-si系微晶玻璃粉85份、氧化锆粉体13份,用于隔热层;另一种是:其含有ca-b-si系微晶玻璃粉85份、氧化锆粉体16份,用于灭弧层;隔热层用低温共烧陶瓷浆料中的固含量为76%,灭弧层用低温共烧陶瓷浆料中的固含量为68%。
[0088]
实施例2中的熔丝电极浆料包括ca-b-si系微晶玻璃粉15份,5-10μm片式银粉45份,球形亚微米级银粉15份,锡铋合金粉7份,固体粉体分散剂3份,气相二氧化硅粉2份,有机载体20份。
[0089]
实施例2中的端电极浆料包括高温玻璃粉2份,1-3μm球形银粉70份,球形亚微米级银粉15份,有机载体13份。
[0090]
实施例2中的背电极浆料包括高温玻璃粉8份,1-3μm球形银粉55份,有机载体37份。
[0091]
实施例3
[0092]
该实施例3的表面贴装保险丝的制备方法同实施例1,其与实施例1的区别在于:
[0093]
实施例3的步骤一的混合粉体包括氧化钙粉体40份、氧化硼粉体35份、氧化硅粉体45份;步骤一中,在制备低温共烧陶瓷粉时,两种低温共烧陶瓷粉分别为,一种是:其含有ca-b-si系微晶玻璃粉90份、氧化锆粉体15份,用于隔热层;另一种是:其含有ca-b-si系微晶玻璃粉90份、氧化锆粉体20份,用于灭弧层;隔热层用低温共烧陶瓷浆料中的固含量为80%,灭弧层用低温共烧陶瓷浆料中的固含量为70%。
[0094]
实施例3中的熔丝电极浆料包括ca-b-si系微晶玻璃粉20份,5-10μm片式银粉50份,球形亚微米级银粉20份,锡铋合金粉10份,固体粉体分散剂5份,气相二氧化硅粉5份,有机载体25份。
[0095]
实施例3中的端电极浆料包括高温玻璃粉1份,1-3μm球形银粉80份,球形亚微米级银粉10份,有机载体10份。
[0096]
实施例3中的背电极浆料包括高温玻璃粉5份,1-3μm球形银粉60份,有机载体35份。
[0097]
实施例2和实施例3得到的表面贴装保险丝的结构同实施例1。
[0098]
以上所述仅为本发明的实施例,并非因此限制本发明的专利范围,凡是利用本发明说明书及附图内容所作的等效结构或等效流程变换,或直接或间接运用在其他相关的技术领域,均同理包括在本发明的专利保护范围内。
起点商标作为专业知识产权交易平台,可以帮助大家解决很多问题,如果大家想要了解更多知产交易信息请点击 【在线咨询】或添加微信 【19522093243】与客服一对一沟通,为大家解决相关问题。
此文章来源于网络,如有侵权,请联系删除



tips