一种粉体提纯装置的制作方法



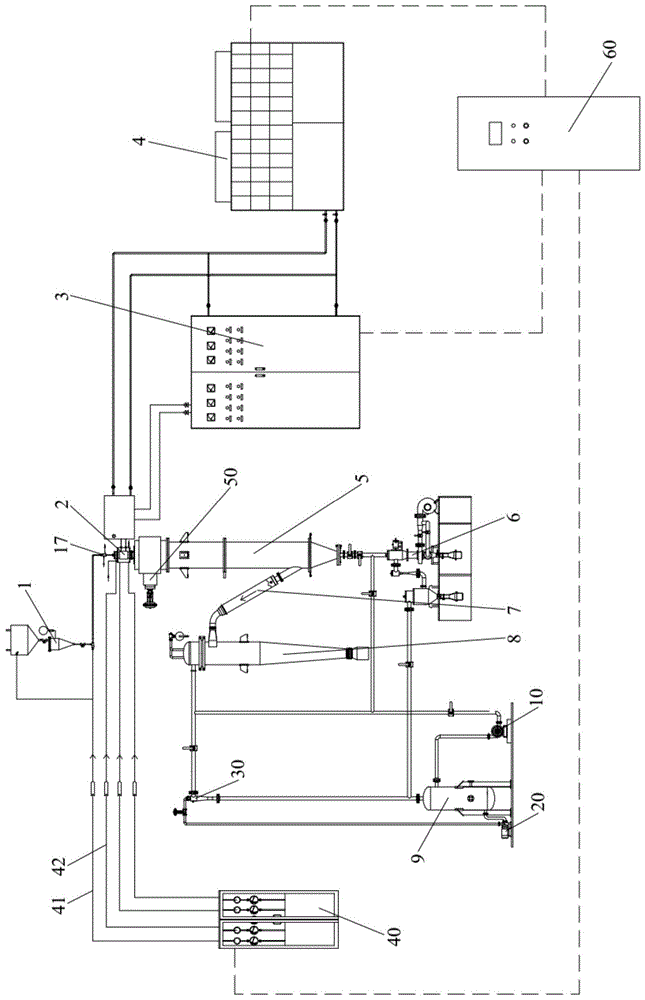
本实用新型涉及难熔金属提纯技术领域,尤其涉及一种粉体提纯装置。
背景技术:
难熔金属一般是指熔点高于1650℃且有一定储量的金属,如铂、钨、镆、钽、铌等。与铝、镁等低熔点金属相比,这些难熔金属的高温力学性能优异。特别地,对于高纯难熔金属,与一般普通工业材料相比,其具有诸多优点,如有高塑性,放气率低,耐冲蚀,抗疲劳性能好,耐碱金属蒸气和熔体腐蚀,高温蠕变性能好等。这些优异的性能使其成为化工、电子、航空航天、原子能、武器装备等领域理想的高温结构和功能元件候选材料。然而,若难熔金属内含有较多的杂质元素,如气体杂质元素、其它金属和非金属杂质元素等,则会对难熔金属的物理和化学性能产生较大的不利影响,甚至直接导致元器件的失效。因此,难熔金属纯度的提高非常重要。
在诸多的难熔金属提纯技术中,由于高频感应等离子体技术具有无电极污染、弧区大、温度均匀、能提供纯净热源及工质不受限制等优点,所以该种技术得到了越来越多的应用。通过该种技术提纯难熔金属的基本原理如下:通过等离子炬产生高温等离子体作为热源,进而加热含有难熔金属的粉体原料,利用粉体原料中各杂质元素与难熔金属的蒸汽压的不同,通过蒸发或升华去除掉粉体原料中的杂质元素,获得高纯度的难熔金属。
然而,对于目前采用高频感应等离子体技术的粉体提纯装置而言,其通常存在以下问题:1、为减少粉体所受污染,装置启动时的真空度可能过高,但此时易出现粉体烧蚀现象,影响得粉率;2、在等离子炬中,由于石英管通常仅依靠其内壁附近的一层工作气进行冷却,所以其冷却效果依赖于工作气的气量,效果不稳定,可能导致石英管被高温等离子体焰流烧损,不利于等离子炬在大功率下稳定运行,同样影响最终粉体产物的获得。受以上问题的影响,通过高温等离子体技术提纯难熔金属的规模化应用受到了限制。
基于此,亟需一种粉体提纯装置,用以解决上述问题。
技术实现要素:
本实用新型的目的在于提供一种粉体提纯装置,在减少粉体所受污染时,可有效避免粉体烧蚀,保证得粉率,同时可使等离子炬在大功率下保持稳定运行,利于高温等离子体技术提纯难熔金属的规模化应用。
为达此目的,本实用新型采用以下技术方案:
一种粉体提纯装置,包括:
等离子炬和高频电源,所述等离子炬包括主石英管、固定仓和电磁感应线圈,所述主石英管的两端分别为原料进口端和等离子体出口端,所述固定仓间隔套设在所述主石英管的外部以形成冷却水通道,且在所述冷却水通道上设置有冷却水进口和冷却水出口,所述电磁感应线圈包括线圈部和连接于所述线圈部端部的连接部,所述线圈部缠绕在所述主石英管的外部且位于所述固定仓内,所述连接部伸出所述固定仓设置并与所述高频电源连接;
反应器,所述反应器的入口端与所述等离子出口端连通;
抽真空机构,同时与所述主石英管的管腔和所述反应器的内腔连通;
供气管路,包括工作气供应管路,所述工作气供应管路与所述主石英管的所述原料进口端连通以提供工作气,且所述工作气为惰性气体。
可选地,所述等离子炬还包括内石英管,所述内石英管间隔嵌套在所述主石英管的内部以形成冷却气通道,且所述内石英管设置在所述等离子炬的所述原料进口端。
可选地,沿所述线圈部的周向,在所述线圈部外部的所述固定仓内设置有热辐射屏蔽板,且所述热辐射屏蔽板设置为中空结构,在所述热辐射屏蔽板上设置有屏蔽板冷却水进口和屏蔽板冷却水出口,所述屏蔽板冷却水进口和所述屏蔽板冷却水出口均与所述热辐射屏蔽板的中空腔相连通。
可选地,所述粉体提纯装置还包括送粉机构,所述送粉机构包括气力输送管道,所述气力输送管道的两端分别形成载气入口和气粉混合物出口,所述气粉混合物出口与所述主石英管的所述原料进口端连通,且所述气力输送管道中所述气粉混合物出口处的管段为文丘里管段,在所述载气入口和所述气粉混合物出口之间的所述气力输送管道上设置有粉体入口;
所述供气管路还包括载气供应管路,所述载气供应管路与所述载气入口连通以提供载气,且所述载气为惰性气体。
可选地,所述送粉机构还包括:
下料斗,用于粉体原料的下料;
送粉管道,所述送粉管道的进口端与所述下料斗的出口端连通,所述送粉管道的出口端与所述粉体入口连通;
螺旋杆,设置在所述送粉管道内以输送所述粉体原料。
可选地,所述送粉机构还包括储料斗,所述储料斗内储存有所述粉体原料,所述储料斗的上部设置有吹扫气入口、保护气入口和排气口,所述吹扫气入口与所述载气供应管路连通,所述储料斗底部的出口通过密封管路与所述下料斗的进口端连通。
可选地,所述抽真空机构包括第一真空泵和第二真空泵,所述第一真空泵的抽气端同时与所述主石英管的管腔和所述反应器的内腔连通,以在所述等离子炬点火前将所述主石英管的管腔和所述反应器的内腔中的真空度均降至第一预设真空度以下;
所述第二真空泵的抽气端与所述反应器的内腔连通,以在所述等离子炬点火后将所述反应器的内腔中的真空度降至第二预设真空度以下,且所述第二预设真空度高于所述第一预设真空度。
可选地,所述粉体提纯装置还包括粉体收集机构,所述粉体收集机构设置在所述反应器的底部,且与所述反应器的出口端连通,以收集提纯后的粉体。
可选地,所述粉体提纯装置还包括:
冷凝器,所述冷凝器通过所述反应器的侧壁与所述反应器的内腔连通,以对所述反应器内流出的气体降温;
气固分离机构,沿所述气体的流出方向,所述气固分离机构设置在所述冷凝器的下游,以去除所述气体中的固体颗粒;
气液分离机构,沿所述气体的流出方向,所述气液分离机构设置在所述气固分离机构的下游,以去除所述气体中的液体组分。
可选地,所述粉体提纯装置还包括测温机构,所述测温机构包括驱动件和测温探头,所述驱动件的输出端与所述测温探头传动连接,以驱动所述测温探头伸入所述反应器的内腔中检测等离子焰的温度。
本实用新型的有益效果:
本实用新型提供了一种粉体提纯装置,当利用抽真空机构对等离子炬中的主石英管及反应器抽到一定真空度之后,可通过供气管路向等离子炬及反应器内通入工作气。由于工作气为惰性气体,所以无需使装置保持过高的真空度,即可有效避免等离子炬或反应器内的粉体被污染,并可有效避免粉体烧蚀,保证得粉率。同时,在等离子炬运行时,通过冷却水进口向冷却水通道中通入冷却水,并使冷却后的冷却水由冷却水出口流出,即可利用循环冷却水对主石英管进行持续冷却,使等离子炬可以在大功率下保持稳定的运行,保证最终粉体产物的获得,利于高温等离子体技术提纯难熔金属的规模化应用。
附图说明
图1是本实用新型实施例提供的粉体提纯装置的整体结构示意图;
图2是本实用新型实施例提供的粉体提纯装置中送粉机构的整体结构示意图;
图3是本实用新型实施例提供的粉体提纯装置中送粉机构的局部放大图;
图4是本实用新型实施例提供的粉体提纯装置中等离子炬的正视结构示意图;
图5是本实用新型实施例提供的粉体提纯装置中等离子炬的俯视结构示意图。
图中:
1、送粉机构;11、储料斗;111、吹扫气入口;112、保护气入口;113、排气口;12、下料斗;13、送粉管道;14、螺旋杆;15、气力输送管道;151、载气入口;152、粉体入口;153、气粉混合物出口;154、收缩管段;155、扩张管段;16、驱动电机;17、送粉枪;171、送粉枪冷却水进口;172、送粉枪冷却水出口;
2、等离子炬;21、主石英管;22、内石英管;23、固定仓;24、电磁感应线圈;241、线圈部;242、连接部;243、线圈冷却水进口;244、线圈冷却水出口;25、热辐射屏蔽板;251、第一弧形板;2511、屏蔽板冷却水进口;252、第二弧形板;2521、屏蔽板冷却水出口;253、连接管;26、冷却气通道;27、冷却水通道;271、冷却水进口;272、冷却水出口;
3、高频电源;4、冷却水循环机构;5、反应器;6、粉体收集机构;7、冷凝器;8、气固分离机构;9、气液分离机构;
10、第一真空泵;20、水泵;30、第二真空泵;40、配气机构;41、载气供应管路;42、工作气供应管路;50、测温机构;60、plc控制器。
具体实施方式
为使本实用新型解决的技术问题、采用的技术方案和达到的技术效果更加清楚,下面结合附图并通过具体实施方式来进一步说明本实用新型的技术方案。
在本实用新型的描述中,除非另有明确的规定和限定,术语“相连”、“连接”、“固定”应做广义理解,例如,可以是固定连接,也可以是可拆卸连接,或成一体;可以是机械连接,也可以是电连接;可以是直接相连,也可以通过中间媒介间接相连,可以是两个元件内部的连通或两个元件的相互作用关系。对于本领域的普通技术人员而言,可以具体情况理解上述术语在本实用新型中的具体含义。
在本实用新型中,除非另有明确的规定和限定,第一特征在第二特征之“上”或之“下”可以包括第一和第二特征直接接触,也可以包括第一和第二特征不是直接接触而是通过它们之间的另外的特征接触。而且,第一特征在第二特征“之上”、“上方”和“上面”包括第一特征在第二特征正上方和斜上方,或仅仅表示第一特征水平高度高于第二特征。第一特征在第二特征“之下”、“下方”和“下面”包括第一特征在第二特征正下方和斜下方,或仅仅表示第一特征水平高度小于第二特征。
在本实施例的描述中,术语“上”、“下”、“左”、“右”等方位或位置关系为基于附图所示的方位或位置关系,仅是为了便于描述和简化操作,而不是指示或暗示所指的装置或元件必须具有特定的方位、以特定的方位构造和操作,因此不能理解为对本实用新型的限制。此外,术语“第一”、“第二”仅仅用于在描述上加以区分,并没有特殊的含义。
本实施例提供了一种粉体提纯装置。如图1所示,该粉体提纯装置包括等离子炬2、高频电源3、反应器5、抽真空机构和供气管路。等离子炬2包括主石英管21、固定仓23和电磁感应线圈24,主石英管21的两端分别为原料进口端和等离子体出口端,固定仓23间隔套设在主石英管21的外部以形成冷却水通道27,且在冷却水通道27上设置有冷却水进口271和冷却水出口272,电磁感应线圈24包括线圈部241和连接于线圈部241端部的连接部242,线圈部241缠绕在主石英管21的外部且位于固定仓23内,连接部242伸出固定仓23设置并与高频电源3连接。反应器5的入口端与等离子出口端连通。抽真空机构同时与主石英管21的管腔和反应器5的内腔连通,以对主石英管21的管腔或反应器5的内腔抽真空。供气管路包括工作气供应管路42,工作气供应管路42与主石英管21的原料进口端连通以提供工作气,且工作气为惰性气体。
一方面,当利用抽真空机构对主石英管21及反应器5抽到一定真空度之后,可通过供气管路向主石英管21及反应器5内通入工作气。由于工作气为惰性气体,所以无需使装置保持过高的真空度,即可有效避免进入等离子炬2或反应器5的粉体被污染。同时,由于无需保持过高的真空度,所以可有效避免粉体烧蚀,保证得粉率。
另一方面,在等离子炬2工作时,通过冷却水进口271向冷却水通道27中通入冷却水,并使冷却后的冷却水由冷却水出口272流出,即可利用循环冷却水对主石英管21进行持续冷却,更有效地避免主石英管21被高温等离子体焰流烧损,使等离子炬2在大功率下保持稳定的运行。
本实施例中,固定仓23与主石英管21之间的间隔不小于10mm,以使冷却水通道27中能够通入足够数量的循环冷却水,保证冷却效果。进一步地,如图1所示,在该粉体提纯装置中设置有冷却水循环机构4,以提供循环冷却水,并供受热后的循环冷却水降温。
可选地,为加强冷却效果,如图4所示,等离子炬2还包括内石英管22,内石英管22间隔嵌套在主石英管21的内部以形成冷却气通道26,且内石英管22设置在等离子炬2的原料进口端。此时,部分工作气可通过冷却气通道26进入主石英管21,更好地贴紧主石英管21的内壁以对主石英管21进行冷却。本实施例中,主石英管21的上端为工作气进口端,内石英管22即设置在该处。当冷却气通道26中的工作气流出时,这些工作气还可流入主石英管21的中部,再用于生成等离子体。
可选地,固定仓23为透明石英仓,以便于操作者观察冷却水通道27中冷却水的流动状态,确保水冷过程的正常运行。进一步地,电磁感应线圈24与该透明石英仓一体化设置,以便于使用。本实施例中,通过浇筑石英玻璃的方式形成该透明石英仓,并使其与电磁感应线圈24呈一体化设置。
可选地,如图4所示,电磁感应线圈24设置为中空结构。具体地,在电磁感应线圈24上设置有线圈冷却水进口243和线圈冷却水出口244,线圈冷却水进口243和线圈冷却水出口244均与电磁感应线圈24的中空腔连通。此时,可向电磁感应线圈24的中空腔内通入循环冷却水,从而同时对主石英管21及固定仓23进行一定程度的冷却,延长设备的使用寿命。
可选地,为有效避免等离子炬2内产生的热量向周围环境辐射,如图4和图5所示,沿线圈部241的周向,在线圈部241外部的固定仓23内设置有热辐射屏蔽板25。本实施例中,热辐射屏蔽板25设置为中空结构,在热辐射屏蔽板25上设置有屏蔽板冷却水进口2511和屏蔽板冷却水出口2521,屏蔽板冷却水进口2511和屏蔽板冷却水出口2521均与热辐射屏蔽板25的中空腔相连通。此时,可向热辐射屏蔽板25的中空腔内通入循环冷却水,通过循环冷却水对固定仓23进行持续冷却,有效延长固定仓23的使用寿命。
以具体结构而言,热辐射屏蔽板25包括第一弧形板251和第二弧形板252,第一弧形板251和第二弧形板252相对间隔设置在线圈部241的两侧,以在起到热辐射屏蔽作用的同时,避免对电磁感应线圈24中连接部242的设置产生干涉。进一步地,屏蔽板冷却水进口2511设置在第一弧形板251上,屏蔽板冷却水出口2521设置在第二弧形板252上。且在热辐射屏蔽板25中还设置有连接管253,以连接第一弧形板251的中空腔和第二弧形板252的中空腔,保证冷却水的流通。
可选地,粉体提纯装置还包括送粉机构1,以便于输送难熔金属提纯所需的粉体原料。如图1-图3所示,送粉机构1包括气力输送管道15,气力输送管道15的两端分别形成载气入口151和气粉混合物出口153,气粉混合物出口153与主石英管21的原料进口端连通。且在载气入口151和气粉混合物出口153之间的气力输送管道15上设置有粉体入口152。供气管路还包括载气供应管路41,载气供应管路41与载气入口151连通以提供载气,且载气为惰性气体。本实施例中,工作气及载气均为氩气。
可选地,如图2所示,在气力输送管道15中的载气入口151处,还设置有载气喷嘴以连接载气供应管路41。进一步地,该载气喷嘴中设置有节流结构,以供载气加速流动并形成超音速流体,使载气与粉体原料的混合更加均匀。
此时,可使粉体原料由粉体入口152送入气力输送管道15,并使粉体原料与气力输送管道15中的载气发生混合,进而随载气向气力输送管道15的出口(即气粉混合物出口153)处流动,最终将粉体原料送入等离子炬2内。可以理解的是,由于载气为惰性气体,所以可有效避免粉体原料在输送过程中被污染。
本实施例中,气力输送管道15中气粉混合物出口153处的管段为文丘里管段。在文丘里管段作用下,可在气力输送管道15的出口处形成负压,产生较强的吸附力,从而既能有效避免粉体原料回流,又能加速载气的流动,有效增强载气与粉体原料的混合效果。
具体地,如图2所示,沿载气的流动方向,文丘里管段包括依次设置的收缩管段154和扩张管段155。可选地,收缩管段154和扩张管段155可拆卸连接,以便于设备的清理。
可选地,如图2所示,送粉机构1还包括下料斗12、送粉管道13和螺旋杆14。其中,下料斗12用于粉体原料的下料。送粉管道13的进口端与下料斗12的出口端连通,送粉管道13的出口端与粉体入口152连通。螺旋杆14设置在送粉管道13内以输送粉体原料。通过螺旋杆14与送粉管道13之间的配合,可便于实现粉体原料的封闭运输,且螺旋杆14运行平稳,可有效防止粉体原料堆积。本实施例中,送粉管道13和螺旋杆14均水平设置,以进一步保证送料的均匀性和稳定性。
进一步地,送粉管道13的出口端的出口方向沿重力方向设置,以便于粉体原料可在重力作用下落到气力输送管道15中。
本实施例中,下料斗12的出口端与送粉管道13的进口端之间及送粉管道13的出口端与气力输送管道15上的粉体入口152之间均通过密封管路连接,以防止粉体原料外泄,同时有效减少粉体原料与外界的接触,尽量减小粉体原料所受的污染。
可选地,如图2所示,该送粉机构1还包括驱动电机16,驱动电机16的输出端与螺旋杆14传动连接,以驱动螺旋杆14转动。
可选地,如图2所示,送粉机构1还包括储料斗11,储料斗11内储存有粉体原料。储料斗11的上部设置有吹扫气入口111、保护气入口112和排气口113,吹扫气入口111与载气供应管路41连通,储料斗11底部的出口通过密封管路与下料斗12的进口端连通。
此时,通过载气供应管路41可向储料斗11中通入载气进行吹扫,形成惰性气氛。之后,可通过保护气入口112向储料斗11中通入保护气,进一步避免储料斗11中的粉体原料受污染。
可选地,如图1和图2所示,送粉机构1还包括送粉枪17。送粉枪17的进口端与气力输送管道15上的气粉混合物出口153连通,送粉枪17的出口端与等离子炬2的原料进口端连通,以更加便于向等离子炬2中通入粉体原料。
进一步地,送粉枪17采用耐高温金属制造,且在其上设置有夹套。夹套上设置有送粉枪冷却水进口171和送粉枪冷却水出口172,以供通入循环冷却水进行冷却。具体地,通入夹套中的冷却水需增压至1.7mpa以上,以确保冷却水具有足够快的流速,以进行快速冷却,避免夹套气化。
可选地,如图1所示,抽真空机构包括第一真空泵10和第二真空泵30。第一真空泵10的抽气端与主石英管21的管腔和反应器5的内腔连通,以在等离子炬2点火前将上述两个腔室中的真空度降至第一预设真空度以下,以提高起弧稳定性,保证点火成功。本实施例中,第一预设真空度为-100pa。
第二真空泵30的抽气端与反应器5的内腔连通,以在等离子炬2点火稳定后降至第二预设真空度以下。其中,第二预设真空度高度第一预设真空度,以利于粉体提纯。本实施例中,第二预设真空度处于-21kpa与-61kpa之间(以大气压为101kpa计算,第二预设真空度的绝对压力值为40kpa-80kpa)。
可选地,第一真空泵10为旋片真空泵,其结构紧凑,噪音低且振动低。第二真空泵30为水力喷射泵,与旋片真空泵并联设置。在装置中还设置有与水力喷射泵配套的水泵20。通过水泵20可以将水打入水力喷射泵的喉管内,以形成稳定负压,最终获得所需的真空度。由于旋片真空泵和水力喷射泵的结构均为现有技术,所以在此不再赘述。当然,在其它实施例中,也可将水力喷射泵替换为液环真空泵。
可选地,如图1所示,该粉体提纯装置还包括测温机构50。该测温机构50包括驱动件和测温探头。驱动件的输出端与测温探头传动连接,以驱动测温探头伸入反应器5的内腔中检测等离子焰的温度,为维持系统正常运行提供有利参考。进一步地,当测得等离子焰温度后,通过驱动件还可驱动测温探头快速收回,以有效避免测温探头被烧毁。
本实施例中,驱动件为气动气缸。测温探头为水冷式探头,也可有效避免被烧毁。此外,可以理解的是,测温机构50与反应器5连接处密封设置,以避免影响反应器5的正常使用。
可选地,高频电源3的功率范围为100kw-2mw,频率范围为0.4mhz-13.6mhz,以保证高温等离子体的生成。
此外,高频电源3具有以下特点:
(1)振荡部分设计为三回路振荡器结构,能够实现宽范围的功率调节,并能维持电子管的最佳工作状态,;
(2)采用单只电子管实现功率输出;
(3)栅极反馈环节电感线圈结构设计及其分压电容配置:首先必须保证反馈信号较功率圈上的信号相差90度;其次,必须保证分压电容的比例与电子管的放大倍数保持乘积为定值;最后,必须保证栅极环节的电容电感与接地电容形成谐振,将该环节的对地信号总和为零。
可选地,如图1所示,该粉体提纯装置中还包括配气机构40。配气机构40中设置有工作气气源及载气气源,这些气源均与供气管路相连,可为供气管路提供所需的工作气及载气等气体。
可选地,为便于调节气体供应,如图1所示,该粉体提纯装置还包括plc控制器60,该plc控制器60与配气机构40连接。通过plc控制器60与配气机构40的共同作用可调节工作气等气体的供给量和供给时间,也可调整工作气和载体等多种气体之间的供给顺序,十分方便。具体地,可在配气机构40的出口端设置电动开关阀,以控制供气或断气。此时,可使plc控制器60与电动开关阀通讯连接,从而通过控制电动开关阀的运行来实现对气体供给的控制。
此外可以理解的是,通过调节气体供应调节可控制粉体原料在等离子炬2中的停留时间,也可调节离子炬2和反应器5腔体内的压力,以满足多种粉体原料的提纯需求。
本实施例中,plc控制器60还与高频电源3及冷却水循环机构4连接,以便于调控高频电源3或冷却水循环机构4的运行。
可选地,如图1所示,该粉体提纯装置还包括粉体收集机构6。粉体收集机构6设置在反应器5的底部,且与反应器5的出口端连通,以收集提纯后的粉体。具体地,粉体收集机构6可以为粉体收集罐。
可选地,如图1所示,该粉体提纯装置还包括冷凝器7、气固分离机构8和气液分离机构9。其中,冷凝器7通过反应器5的侧壁与反应器5的内腔连通,以和对反应器5内流出的气体进行换热,对这些气体进行降温。沿气体的流出方向,气固分离机构8和气液分离机构9依次设置在冷凝器7的下游。当气体流过气固分离机构8时,通过气固分离机构8可有效去除气体中的固体颗粒(即未进入粉体收集机构6的颗粒)。最终,当气体流过气液分离机构9时,通过气液分离机构9可有效去除气体中的液体组分。
本实施例中,气固分离机构8的气体出口端与气液分离机构9的进口端连通,以使分离后的气体顺利进入气液分离机构9中;气固分离机构8的固体出口端与外部废物收集机构连通,以便于对分离出的固体颗粒进行处理。气液分离机构9的气体出口端与大气连通,可使分离后的气体排入大气;气液分离机构9的液体出口端与外部废物收集机构连通,以便于对分离出的液体组分进行处理。
具体地,气固分离机构8可以为旋风分离器,气液分离机构9可以为气液分离罐。由于旋风分离器和气液分离罐的结构均为现有技术,所以在此不再赘述。
具体地,当电磁感应线圈24连通高频电源3时,即可在主石英管21内产生变化的磁场,进而使进入主石英管21内的工作气发生电离并产生焦耳热,形成高温等离子体焰流。当粉体原料流经等离子炬2时,其便会被高温等离子体焰流熔融成液滴,并再进入反应器5的腔体内冷却。此过程中,由于粉体原料中的杂质元素会通过蒸发、升华或脱气等方式被气体带走,所以可实现对难熔金属的提纯。最终,含有提纯后的难熔金属的粉体会进入粉体收集机构6中,含有杂质的气体则会依次流经冷凝器7、气固分离机构8和气液分离机构9而排入大气。
此外,以等离子炬2的实际功率为100kw为例,相比现有技术,由于针对等离子炬2的冷却得到了有效改善,所以等离子炬2的中心温度可稳定在8000k-10000k,从而可使进入等离子炬2中的粉体原料迅速达到熔融液滴状态,有效提高所形成的粉体颗粒的球化率,最终提升粉体产品的性能。
综上,本实施例提供了一种粉体提纯装置,通过将工作气及载气设为惰性气体,无需在装置启动时保持过高的真空度,在减少粉体被污染可能性的同时,可有效避免粉体烧蚀,保证得粉率。同时,通过在等离子炬2设置冷却气通道26和冷却水通道27,可对主石英管21进行持续良好的冷却,使等离子炬2可在大功率下保持稳定运行,保证最终粉体产物的获得,十分利于高温等离子体技术提纯难熔金属的规模化应用,实用性及经济性均较高。
以上内容仅为本实用新型的较佳实施例,对于本领域的普通技术人员,依据本实用新型的思想,在具体实施方式及应用范围上均会有改变之处,本说明书内容不应理解为对本实用新型的限制。
起点商标作为专业知识产权交易平台,可以帮助大家解决很多问题,如果大家想要了解更多知产交易信息请点击 【在线咨询】或添加微信 【19522093243】与客服一对一沟通,为大家解决相关问题。
此文章来源于网络,如有侵权,请联系删除


