一种氧化铝复合陶瓷及其制备方法和应用与流程



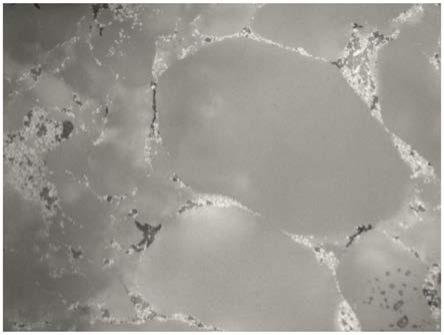
[0001]
本申请属于陶瓷材料的技术领域,尤其涉及一种氧化铝复合陶瓷及其制备方法和应用。
背景技术:
[0002]
随着科技的发展,印刷电路板(pcb)已经成为一种不可或缺的电子部件。自20世纪90年代以来,世界各国已逐渐将印刷电路板改称为电子基板(electronic substrate),标志着传统的印刷电路板已进入了多层基板时代。电子线路日益趋向密集化与微型化,导热问题已成为妨碍印刷电路板进一步发展的瓶颈之一。
[0003]
现有技术中,无机基板多以al2o3陶瓷材料为基材,由于纯氧化铝陶瓷的烧结温度在1800℃以上,烧结成本较高;为了降低烧结成本,通常会加入烧结助剂降低烧结温度,可这些烧结助剂的导热性能较低,同时在烧结后形成较厚的晶界相,这导致al2o3陶瓷基板的热导率大多在20~26w
·
m-1
·
k-1;为提高al2o3陶瓷基板的热导率,在烧结过程中,通常会进一步添加aln微粒作为高热导相,但烧结后的aln晶粒被al2o3晶粒所包裹住,aln微粒的作用有限,往往需要添加大量(>30wt%)的aln微粒才能提高al2o3陶瓷的热导率,可aln微粒的烧结温度也在1800℃以上,这种添加大量aln微粒的氧化铝陶瓷很难在1700℃以下烧结致密,造成氧化铝陶瓷烧结成本依然很高。同时,氧化铝陶瓷的室温弯曲强度在300~450mpa之间,力学性能不高。
技术实现要素:
[0004]
有鉴于此,本申请提供了一种氧化铝复合陶瓷及其制备方法和应用,用于解决氧化铝陶瓷力学性能低、热导率低、烧结温度高导致的烧结成本高的技术问题。
[0005]
本申请第一方面提供了一种氧化铝复合陶瓷,由复合微粒和aln微粒组成;
[0006]
所述复合微粒的粒径为50μm-70μm,所述aln微粒的粒径为0.5μm;
[0007]
所述复合微粒由al2o3、y2o3、m-zro2组成;
[0008]
所述aln微粒分布在所述复合微粒的表面。
[0009]
作为优选,所述aln微粒成三维网状结构分布在所述复合微粒表面。
[0010]
作为优选,以质量份计,所述氧化铝复合陶瓷各部分按以下配比组成;
[0011]
复合微粒
ꢀꢀ
85-95份;
[0012]
aln微粒
ꢀꢀꢀ
5-15份。
[0013]
作为优选,以质量份计,所述复合微粒由以下原料组成;
[0014]
al2o3ꢀꢀꢀꢀꢀꢀꢀ
80.7-84.5份;
[0015]
m-zro2ꢀꢀꢀꢀꢀꢀ
12.7-14.6份;
[0016]
y2o3ꢀꢀꢀꢀꢀꢀꢀꢀ
0.7-2.7份。
[0017]
本申请第二方面提供了一种氧化铝复合陶瓷的制备方法,包括步骤:
[0018]
步骤1、将al2o3、y2o3和m-zro2加入溶剂进行球磨混合,干燥后获得第一复合粉体;
[0019]
步骤2、将所述第一复合粉体喷雾造粒得到第一复合微粒;
[0020]
步骤3、将所述第一复合微粒与aln微粒干法球磨混合得到第二复合微粒;
[0021]
步骤4、将所述第二复合微粒模压得到氧化铝陶瓷胚体;
[0022]
步骤5、将所述氧化铝陶瓷胚体在保护气氛下进行高温烧结,得到所述氧化铝陶瓷;
[0023]
所述第一复合颗粒的粒径为50μm-70μm,所述aln微粒的粒径为0.5μm。
[0024]
作为优选,所述溶剂为乙醇、丙醇、甲醇或丙酮中的一种或多种。
[0025]
作为优选,步骤1中所述球磨混合为在辊式球磨机上球磨混合1~48h,干燥后获得第一复合粉体;
[0026]
步骤3中所述球磨混合为在行星式球磨机上球磨混合2~12h,得第二复合微粒。
[0027]
作为优选,所述高温烧结的升温速率为5-10℃/min,所述高温烧结的温度为1200-1700℃,所述高温烧结的压力为0.1-1mpa,所述高温烧结的时间为1-4h。
[0028]
作为优选,所述行星式球磨机的球磨转速为250r/min。
[0029]
本申请第三方面提供了氧化铝复合陶瓷作为电子元器件材料的应用。
[0030]
与现有技术相比,本申请具有以下有益效果:
[0031]
1、本申请通过将al2o3和m-zro2、y2o3混合后高温烧结,aln与al2o3在烧结时,会生成少量的al6o3n4、al7o3n5、al8o3n6作为增强相,可显著提高氧化铝陶瓷的力学性能。
[0032]
2、本申请通过将al2o3、y2o3和m-zro2混合后的第一复合粉体喷雾造粒得到第一复合微粒,将第一复合微粒与aln微粒干法球磨混合得到第二复合微粒,第一复合微粒的粒径为50μm-70μm,aln微粒的粒径为0.5μm,复合微粒的粒径远大于aln颗粒的粒径,从而添加少量aln颗粒便可使aln颗粒分布在复合微粒的表面,避免了aln颗粒被复合微粒包裹,进而使aln充分发挥其导热性能;进一步的,本申请还通过将aln微粒附着在第二复合微粒表面,通过模压在氧化铝复合陶瓷中形成aln的三维网状结构分布,降低了热量在陶瓷中的散射,从而进一步提高了氧化铝复合陶瓷的热导性能。
[0033]
3、本申请通过将al2o3、y2o3和m-zro2混合后的第一复合粉体喷雾造粒得到第一复合微粒,将第一复合微粒与aln微粒干法球磨混合得到第二复合微粒;第一复合微粒的粒径为50μm-70μm,aln微粒的粒径为0.5μm,复合微粒的粒径远大于aln颗粒的粒径,避免了添加少量aln时,aln颗粒被复合粉体包裹,降低了氧化铝复合陶瓷中氮化铝的添加量,进而降低了氧化铝复合陶瓷的烧结温度和烧结成本。
附图说明
[0034]
为了更清楚地说明本申请实施例或现有技术中的技术方案,下面将对实施例或现有技术描述中所需要使用的附图作简单地介绍。
[0035]
图1为本申请实施例制备得到的样品晶相显微镜照片;
[0036]
图2为本申请实施例制备得到的样品sem照片及相应的元素分布图。
[0037]
图3为附图2所示sem照片及相应的元素分布图的黑白对照图。
具体实施方式
[0038]
本申请提供了一种氧化铝复合陶瓷及其制备方法和应用,用于解决氧化铝陶瓷力
学性能低、导热性能低、烧结温度高导致的烧结成本高的问题。
[0039]
下面将对本申请实施例中的技术方案进行清楚、完整地描述,显然,所描述的实施例仅仅是本申请一部分实施例,而不是全部的实施例。基于本申请中的实施例,本领域普通技术人员在没有做出创造性劳动前提下所获得的所有其他实施例,都属于本申请保护的范围。
[0040]
以下实施例所使用的原料al2o3的粒径为1μm、m-zro2的粒径为1μm、y2o3的粒径为2μm、aln的粒径为0.5μm,上述原料纯度均为99%以上。
[0041]
实施例1
[0042]
本申请实施例1提供了第一种氧化铝复合陶瓷,其具体制备方法如下:
[0043]
1、以质量份计,将80.7份al2o3、13.6份m-zro2、0.7份y2o3混合,以乙醇为溶剂,以al2o3为球磨介质,在辊式球磨机上混合12h,经混料、干燥后获得第一复合粉体;
[0044]
2、将第一复合粉体放入喷雾造粒机中,喷雾造粒得到粒径为50μm的第一复合微粒;
[0045]
3、以质量份计,将95份的第一复合微粒、5份aln微粒在行星式球磨机上以250r/min的转速,球磨12h,得到第二复合微粒;
[0046]
4、将第二复合微粒模压得到氧化铝复合陶瓷胚体;
[0047]
5、将氧化铝复合陶瓷胚体放入氮化硼坩埚中,再将氮化硼坩埚放入烧结炉中,在烧结炉中充入n2作为保护气体,在0.1mpa的烧结压力下,以5℃/min的速率升温至1200℃保温4h后,得到致密度为98%的氧化铝陶瓷。
[0048]
实施例2
[0049]
本申请实施例2提供了第二种氧化铝复合陶瓷,其具体制备方法如下:
[0050]
1、以质量份计,将80.7份al2o3、14.6份m-zro2、2.7份y2o3混合,以乙醇为溶剂,以al2o3为球磨介质,在辊式球磨机上混合24h,经混料、干燥后获得第一复合粉体;
[0051]
2、将第一复合粉体放入喷雾造粒机中,喷雾造粒得到粒径为50μm的第一复合微粒;
[0052]
3、以质量份计,将92份的第一复合微粒、8份aln微粒在行星式球磨机上以250r/min的转速,球磨8h,得到第二复合粉体;
[0053]
4、将第二复合微粒模压得到氧化铝复合陶瓷胚体;
[0054]
5、将氧化铝复合陶瓷胚体放入氮化硼坩埚中,再将氮化硼坩埚放入烧结炉中,在烧结炉中充入n2作为保护气体,在0.1mpa的烧结压力下,以10℃/min的速率升温至1400℃保温2h后,得到致密度为98.2%的氧化铝陶瓷。
[0055]
实施例3
[0056]
本申请实施例3提供了第三种氧化铝复合陶瓷,其具体制备方法如下:
[0057]
1、以质量份计,将82.5份al2o3、12.3份m-zro2、1.2份y2o3混合,以乙醇为溶剂,以al2o3为球磨介质,在辊式球磨机上混合48h,经混料、干燥后获得第一复合粉体;
[0058]
2、将第一复合粉体放入喷雾造粒机中,喷雾造粒得到粒径为60μm的第一复合微粒;
[0059]
3、以质量份计,将88份的第一复合颗粒、12份aln微粒在行星式球磨机上以250r/min的转速,球磨6h,得到第二复合微粒;
[0060]
4、将第二复合微粒模压得到氧化铝复合陶瓷胚体;
[0061]
5、将氧化铝复合陶瓷胚体放入氮化硼坩埚中,再将氮化硼坩埚放入烧结炉中,在烧结炉中充入n2作为保护气体,在0.1mpa的烧结压力下,以10℃/min的速率升温至1600℃保温2h后,得到致密度为99%的氧化铝陶瓷。
[0062]
实施例4
[0063]
本申请实施例4提供了第四种氧化铝复合陶瓷,其具体制备方法如下:
[0064]
1、以质量份计,将82.5份al2o3、14.4份m-zro2、2.1份y2o3混合,以乙醇为溶剂,以al2o3为球磨介质,在辊式球磨机上混合48h,经混料、干燥后获得第一复合粉体;
[0065]
2、将第一复合粉体放入喷雾造粒机中,喷雾造粒得到粒径为60μm的第一复合微粒;
[0066]
3、以质量份计,将85份的第一复合微粒、15份aln微粒在行星式球磨机上以250r/min的转速,球磨12h,得到第二复合微粒;
[0067]
4、将第二复合微粒模压得到氧化铝复合陶瓷胚体;
[0068]
5、将氧化铝复合陶瓷胚体放入氮化硼坩埚中,再将氮化硼坩埚放入烧结炉中,在烧结炉中充入n2作为保护气体,在0.1mpa的烧结压力下,以10℃/min的速率升温至1700℃保温2h后,得到致密度为97.2%的氧化铝陶瓷。
[0069]
对比例1:
[0070]
本申请对比例1提供了一种氧化铝陶瓷,其具体制备方法如下:
[0071]
1、将al2o3微粒模压得到氧化铝陶瓷胚体;
[0072]
2、将氧化铝陶瓷胚体放入氮化硼坩埚中,再将氮化硼坩埚放入烧结炉中,在烧结炉中充入n2作为保护气体,在0.1mpa的烧结压力下,以10℃/min的速率升温至1800℃保温2h后,得到氧化铝陶瓷。
[0073]
对比例2:
[0074]
本申请对比例2提供了一种氧化铝复合陶瓷,其具体制备方法如下:
[0075]
1、以质量份计,将82.5份al2o3、14.4份m-zro2、3.1份y2o3,以乙醇为溶剂,以al2o3为球磨介质,在辊式球磨机上混合24h,经混料、干燥后获得复合粉体;
[0076]
2、复合粉体模压得到氧化铝复合陶瓷胚体;
[0077]
3、将氧化铝复合陶瓷胚体放入氧化铝坩埚中,再将氧化铝坩埚放入马弗炉中,以10℃/min的速率升温至1800℃保温2h后,得到氧化铝陶瓷。
[0078]
实时例5:
[0079]
本申请实施例5是对实施例1-4、对比例1制备的氧化铝复合陶瓷和氧化铝陶瓷进行室温抗弯强度、断裂韧性、热导率试验。
[0080]
1、室温抗弯强度测试:采用astm c 1684-2008《室温下高级陶瓷抗弯强度的标准试验方法》进行测试;
[0081]
2、断裂韧性测试:采用astm c 1421-2009《室温下高级陶瓷断裂韧性测》进行测试;
[0082]
3、热导率测试:采用astm d 5470-2012《热导性电绝缘材料的热传输特性的标准试验方法》进行测试。
[0083]
试验结果表1所示:
[0084]
表1
[0085][0086][0087]
从本申请实施例1-4和对比例1可以理解的是,通过在氧化铝中添加烧结助剂和氮化铝,可以生成al6o3n4、al7o3n5、al8o3n6作为增强相,进而提高氧化铝陶瓷的室内抗弯强度、断裂韧性等力学性能;通过将al2o3、y2o3和m-zro2混合后的第一复合粉体喷雾造粒得到复合微粒,将复合微粒与aln颗粒干法球磨混合得到第二复合微粒,使添加少量的aln便可使aln颗粒分布在复合微粒的表面,降低了氧化铝陶瓷中aln的添加量,进而降低了氧化铝复合陶瓷的烧结温度和烧结成本。
[0088]
从上述实施例、对比例及附图可以理解的是,本申请通过将al2o3、y2o3和m-zro2球磨混合后喷雾造粒成粒径为50μm-70μm的复合颗粒,再将该复合颗粒与粒径为0.5μm的aln球磨,使小颗粒的aln颗粒分布在大颗粒的复合微粒的表面,如附图1所示的晶相显微镜照片,白色相aln包裹了浅灰色al2o3复合相,进而使aln能够发挥其高导热性能,提高了氧化铝复合陶瓷的导热性能;进一步的,本申请还将aln微粒附着在第二复合微粒表面,通过模压在材料中形成aln的三维网状结构分布,如附图2所示的sem照片及相应的元素分布图,al、o、zr元素分布均匀,而n元素分布近似圆形,证明aln在基体中形成了三维网络状结构,由于热量在aln晶粒与aln晶粒之间发生的散射要远远小于热量在aln晶粒与al2o3晶粒、al2o3晶粒与al2o3晶粒之间的散射,联通的三维网络状aln可以减少热量在al2o3晶粒与al2o3晶粒、al2o3晶粒与aln晶粒之间的散射,从而进一步提高了氧化铝复合陶瓷的导热效果。
[0089]
以上所述仅是本申请的优选实施方式,应当指出,对于本技术领域的普通技术人员来说,在不脱离本申请原理的前提下,还可以做出若干改进和润饰,这些改进和润饰也应视为本申请的保护范围。
起点商标作为专业知识产权交易平台,可以帮助大家解决很多问题,如果大家想要了解更多知产交易信息请点击 【在线咨询】或添加微信 【19522093243】与客服一对一沟通,为大家解决相关问题。
此文章来源于网络,如有侵权,请联系删除



tips