一种耐腐蚀及耐生物附着的EH690钢板及其制造方法与流程



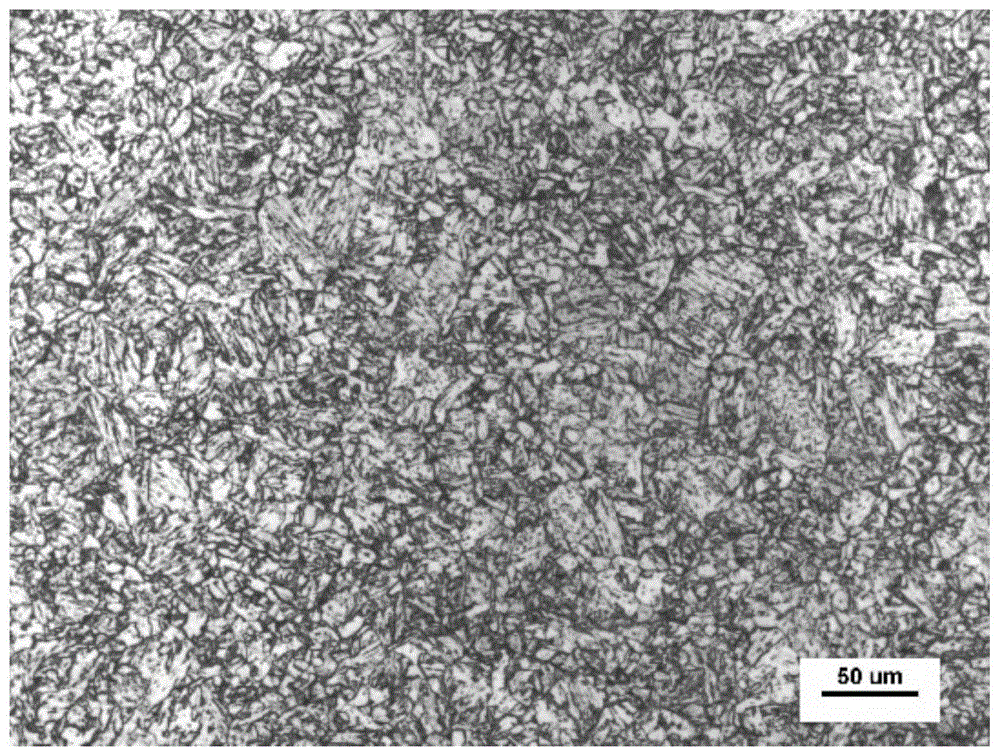
本发明属于钢铁材料制备领域,特别涉及一种耐海洋环境腐蚀及耐生物附着的eh690超高强海工钢板的成分设计及其制造方法。
背景技术:
:21世纪是海洋的世纪,随着科技的发展、人民生活水平的提高,世界各国都将目光聚焦在海洋中蕴藏的巨大资源上。近年来海工装备产业持续快速发展,也促进了海工平台用钢的大量需求和产品的升级换代,市场迫切需要综合性能良好的超高强度特厚海工钢板。海洋工程平台服役环境恶劣,除常规受力外,还要考虑大风、浪涌、潮汐、冰块撞击、地震等多种因素影响,这就决定了海洋平台用钢的特殊性,在平台建造的选材方面必须能适应各种海况条件。同时,钢板长期处于潮湿、高盐度的海洋环境中,受到潮湿空气、海水、海洋生物附着而造成漆膜脱落、钢板表面腐蚀、腐蚀疲劳等问题,降低钢板的力学性能,缩短使用寿命,严重影响海洋工程平台的正常使用。另外,海洋平台远离海岸,不能像船舶那样定期进坞维修、保养。为了能够让海洋工程平台能够在复杂环境下安全使用,急需开发出一种综合性能优良的高品质海洋工程用超高强钢,这种海洋工程用超高强钢板必须具有高强度、高低温韧性、低屈强比、高延展性、抗疲劳、抗氢致裂纹、耐海洋环境腐蚀、耐海洋生物附着、焊接性能优良等优点。目前,海洋工程用钢已能满足海工领域市场的大部分需求,但高强度级别综合性能优良的特殊钢材仍是世界各国的发展的目标,耐海洋环境腐蚀及耐生物附着的eh690钢板其科研问题难度高,生产工艺严格,对设备要求高,开发难度大。公开号为cn106756593a的专利《一种耐海水腐蚀钢及其制造方法》提出了一种耐海水腐蚀钢板及其生产方法,该发明采用较低的合金成分和tmcp工艺生产钢板厚度较薄、屈服强度较低。公开号为cn106756602a的专利《一种耐高湿热海洋大气高强度耐候钢》提出了一种屈服强度700mpa的耐腐蚀钢板,其含c0.01%~0.03%、mn0.3%~0.5%,无法生产高强度大厚度钢板,该专利也没有提出一种适合的生产工艺。公开号为cn103741056a的专利《一种耐南海海洋环境用耐蚀钢板及其生产工艺》提出了一种耐海洋环境腐蚀钢板,其屈服强度和钢板厚度无法满足海洋工程平台关键结构的需求。公开号为cn104419871a的专利《耐海洋环境腐蚀性能优良的焊接结构用钢及其制造方法》中提出了一种屈服强度235~550mpa级tmcp焊接结构用钢板,其合金成分和生产工艺同样无法生产出大厚度、耐海水腐蚀、耐生物附着的超高强度海工钢板。技术实现要素:本发明的目的是克服现有技术不足,制备一种适用于海洋工程领域的耐海洋环境腐蚀、耐生物附着且具备高服役安全性能的超高强度钢板,其耐腐蚀性能和服役安全性能可以达到海洋工程设备服役条件。形成一套特定的耐海水腐蚀、耐生物附超高强度海工钢板成分及相应的生产工艺。本发明利用cu、ni、mo、sb、sn元素相配合的耐海洋环境腐蚀的海工钢板关键生产技术,为实现本发明目的,本发明者通过合金元素筛选与配比、钢质洁净度控制、高效轧制热处理工艺优化与参数选择等几个方面进行了大量系统的试验研究,最终确定了可满足本发明目的合金元素配比及轧制热处理工艺,具体的技术方案是:一种耐海水腐蚀及耐生物附着的eh690钢板,按重量百分比计,钢中含有:c0.09%~0.12%,si0.15%~0.35%,mn1.0%~1.5%,p0.02%~0.03%,s≤0.01%,als0.01%~0.03%,ni1.5%~3.0%,cr0.3%~0.6%,mo0.3%~0.5%,cu0.5%~1.5%,v0.03%~0.06%,ti0.005%~0.02%,b0.0005%~0.001%,sb0.005%~0.3%,sn0.005%~0.3%,其余为fe和不可避免的杂质。钢种化学成分的设计理由如下:(1)c作为钢中基本的强化元素,在本发明方案中是保证强度、硬度的主要元素,c含量过低时晶粒细化效果不明显,钢板强度降低。c含量过高将使钢板耐腐蚀性能降低,焊接裂纹倾向较大,所以本发明精确控制c元素在钢中含量,c的含量控制在0.09%~0.12%。(2)si可提高钢板的强度,同时si作为脱氧剂可减少o含量,si含量大于0.35%时会导致组织粗化,本发明si含量控制为0.15%~0.35%。(3)mn元素与fe原子半径相似,可大量固溶于fe基体中,提高钢板强度,mn含量低于0.6%时对钢板强度贡献较小,同时mn也可以提高钢板淬透性;但是当mn元素质量百分含量过高时,在淬火过程中钢板马氏体转变倾向减弱,不利于调质处理,而且mn元素的偏析又会使得钢板耐腐蚀性能降低、焊接性能下降,所以本发明中mn含量为1.0%~1.5%。(4)p、s元素对钢板的力学性能和焊接性能没有益处,但是钢中适当控制p含量,与cu元素共同作用,可以使内锈层分带明显,有利于提高钢板的耐大气腐蚀性能,所以本发明控制p0.02%~0.03%,s≤0.01%。(5)al是钢中主要的脱氧元素,当al含量过低时脱氧效果不佳,ti等微合金元素因被氧化无法起到细化晶粒和提高焊接性能的目的;相反al元素过高则形成大型夹杂物,als含量为0.01%~0.03%。(6)ni的作用是改善热加工性能,提高韧性。适当加入可以获得较低的韧脆转变温度,同时ni元素可以提高钢板耐海洋环境腐蚀能力。本发明中由于加入大量cu元素,为避免钢板出现高温热裂性,必须加入大量ni元素改善钢板热加工性,所以本发明ni含量为1.5%~3.0%。(7)cr元素在钢中可以有效的提高钢板强度,对于厚度较大的超高强度调质钢来说,可以提高钢板的淬透性;但是cr含量过高会降低钢板冲击韧性,因此,本发明中cr含量为0.3%~0.6%。(8)mo元素可以提高钢板的淬透性,同时mo元素在钢中可以形成细小碳化物,能有效提高钢板强度,mo元素还能配合ni、cu起到一定的耐腐蚀作用,因此,本发明中mo含量为0.3%~0.5%。(9)cu元素可以有效的提高还原气氛下钢材的耐腐蚀能力,也可以有效的抑制微生物的生长附着,特别适用于海洋工程平台用钢,所以成分设计cu含量不低于0.5%。但是cu元素的加入使得钢材的热塑性急剧下降,所以应控制本发明将cu含量为0.5%~1.5%。(10)v是微合金元素,在钢中加入微量的v可以起到晶粒细化作用,在基体中形成v(c,n)粒子,增加钢板的强度和韧性。因此,本发明v含量为0.03%~0.06%。(11)ti元素在基体中能产生强烈的沉淀强化作用,阻止奥氏体再结晶长大,晶粒细化提高钢材的屈服强度。ti与v/n等元素可以在焊接熔池及热影响区附近析出,形成细小弥散的n化物第二相,可以有效促进晶内铁素体形核长大,有效控制原始奥氏体晶粒长大,进而显著提高钢板焊接热影响区性能。合理设计ti、v含量可以降低固溶于基体中的n含量,提高钢板综合性能,因此,本发明将ti含量控制为0.005%~0.02%。(12)b元素可以提高钢板淬透性,微量的b元素即可有明显的提高淬透性效果,b元素过量时钢板脆性增加,焊接裂纹倾向增加,因此,本发明将b元素控制在0.0005%~0.001%。(13)sb元素是本发明中的关键元素,sb元素可以显著改善钢板的耐腐蚀性,加入微量sb就会与cu合金形成致密氧化层,提高还原气氛下钢材的耐腐蚀能力。但是钢中加入sb元素过多时将提高钢的回火脆性,对钢板韧性和焊接性能不利。所以本发明中sb含量为0.005%~0.3%。(14)sn元素与sb元素相近,ni、cu、sb、sn元素共同作用,可以显著提高钢板在海洋大气环境和海水中的耐腐蚀性能,因此,本发明中sb含量为0.005%~0.3%。耐海水腐蚀及耐生物附着的eh690钢板的制造方法采用高洁净度及合金化冶炼、连铸、铸坯低温加热、轧制、淬火+回火处理(即调质处理)、快速冷却,具体包括:(1)高洁净度及合金化冶炼将钢水通过转炉、lf炉、rh或vd炉进行精炼,进一步降低s和非金属夹杂物含量。得到重量百分比组成为:c0.09%~0.12%,si0.15%~0.35%,mn1.0%~1.5%,p0.02%~0.03%,s≤0.01%,als0.01%~0.03%,ni1.5%~3.0%,cr0.3%~0.6%,mo0.3%~0.5%,cu0.5%~1.5%,v0.03%~0.06%,ti0.005%~0.02%,b0.0005%~0.001%,sb0.005%~0.3%,sn0.005%~0.3%,其余为fe和不可避免的杂质。铸坯下线后进缓冷坑堆垛缓冷至室温。(2)轧制工艺钢板在进炉前用薄板包装,避免钢板表面氧化。将铸坯在炉温400~500℃时装入加热炉,保温30~60min,目的是使钢坯在低温阶段保持内外温度一致,为高温段组织均匀做好准备。铸坯在后续升温过程中升温速率控制在3~5℃/min,避免钢坯受热过快导致钢坯内部受热不均。均热温度1100~1150℃,保温100~150min,低温均热保温的目的是在保证c/n化物充分溶解的同时,避免钢中过高的cu元素在铸态组织晶界处液化引起高温热裂。第一阶段开轧温度为1000~1050℃,第二阶段开轧温度为900~1000℃,第二阶段轧制累计压下率为40%~60%,终轧温度为900~950℃。第一阶段热轧目的是改善板坯铸态组织,降低钢坯待温厚度,缩短钢板待温时间;同时避免钢板在1050℃以上轧制,原因是在高温下cu元素在晶界处液化引起高温热脆性,在温度过高时轧钢会导致边角裂纹和钢板表面质量降低。第二阶段轧制工艺设计的目的是在ac3温度以上30~50℃再结晶温度区域增加形变积累,促进奥氏体晶粒扁平化、细小化,达到晶粒细化的效果,900~1000℃低温轧制也可以将形变量渗透到钢板芯部,提升芯部力学性能。(3)调质工艺淬火温度为830~870℃,保温时间为1.0~2.0min/mm,回火温度为600~630℃,保温2~3min/mm,回火后冷却速率5~15℃/s。淬火的目的是使钢板奥氏体化后全部转变为马氏体组织,为后续回火做组织准备。回火处理适当降低回火温度和保温时间、回火后快速冷却的目的是避免钢中的sb、sn、mo等元素造成回火脆性,同时也保证钢板可以进行回火转变,韧塑性得到提高。经过上述方法生产的钢板屈服强度≥690mpa,抗拉强度为770~940mpa,-40℃夏比冲击功单值≥90j,钢板成品厚度为30~100mm。在海水中的腐蚀速率为q345b的50%以下,海洋大气腐蚀速率为q345b的70%以下,同时钢板耐海洋生物附着。有益效果:本发明同现有技术相比,有益效果如下:(1)结合cu、ni、mo、sb、sn元素相配合的耐海洋环境腐蚀的海工钢板关键生产技术,钢板在海水中的腐蚀速率为q345b的50%以下,海洋大气腐蚀速率为q345b的70%以下,同时钢板耐海洋生物附着。(2)本发明创新的合金成分体系可以保证调质处理后钢板的屈服强度≥690mpa,抗拉强度770~940mpa,-40℃夏比冲击功单值≥90j。(3)耐海水腐蚀及耐生物附着的eh690钢板成品厚度为30~100mm。附图说明图1为实施例1钢板厚度1/4处的调质态金相组织,钢板厚度1/4处的组织为回火马氏体;具体实施方式以下实施例用于具体说明本
发明内容,这些实施例仅为本
发明内容的一般描述,并不对本
发明内容进行限制。本发明实施例钢的化学成分见表1,本发明实施例钢铸坯加热及轧制工艺见表2,本发明实施例钢调质处理工艺见表3,本发明实施例钢板力学性能见表4,本发明实施例钢板耐海洋环境腐蚀性能见表5,表6本发明实施例钢耐生物附着性能。表1本发明实施例钢化学成分wt%实施例csimnpsalsnicrmocuvtibsbsn10.1120.211.010.0230.0040.0221.930.360.330.710.0410.0140.00060.0090.0420.0910.261.330.0280.0090.0222.220.590.391.230.0520.0180.00080.010.0930.1190.351.260.0270.0070.0272.830.430.361.420.0600.0190.00090.290.00640.1020.291.490.0260.0090.0182.390.400.411.490.0470.0150.0010.070.2250.1080.321.440.0210.010.0152.960.310.491.110.0310.0130.00050.120.1360.1170.301.290.0240.010.0262.160.330.440.510.0570.0080.000610.220.0670.0960.241.320.020.0080.0231.510.540.460.960.0540.0060.00070.090.2980.1040.281.070.0270.0060.0161.780.560.311.080.0430.0090.000530.050.1790.0980.151.140.030.0110.032.590.510.350.830.0550.0130.00090.260.11100.1120.191.210.0220.0090.0191.580.380.421.330.0340.0160.000840.170.08110.1160.181.390.0290.0090.0191.840.480.370.590.0590.020.000520.040.06120.1170.311.110.0230.0090.0262.670.460.470.870.0310.0050.000920.080.21表2本发明实施例钢铸坯加热及轧制工艺表3本发明实施例钢调质处理工艺表4本发明实施例钢板力学性能表5本发明实施例钢板耐海洋环境腐蚀性能全浸试验参考标准jbt7901,盐雾试验参考标准gbt10125。对比钢成分0.17c-0.35si-1.58mn-0.04nb-0.01ti。表6本发明实施例钢耐生物附着性能备注:表中数值为生物附着面积占钢板总面积百分比%,q345b钢板6个月、12个月海水浸泡生物附着面积占比分别为23%、45%。由表1~6可见,采用本发明技术方案生产的海洋工程用钢,屈服强度≥690mpa,抗拉强度为770~940mpa,-40℃夏比冲击功单值≥90j,钢板成品厚度30~100mm。在海水中的腐蚀速率为q345b的50%以下,海洋大气腐蚀速率为q345b的70%以下,耐海洋环境腐蚀性能优异。当前第1页1 2 3 
起点商标作为专业知识产权交易平台,可以帮助大家解决很多问题,如果大家想要了解更多知产交易信息请点击 【在线咨询】或添加微信 【19522093243】与客服一对一沟通,为大家解决相关问题。
此文章来源于网络,如有侵权,请联系删除



tips