一种热镀锌预处理液及其制备方法及其应用与流程



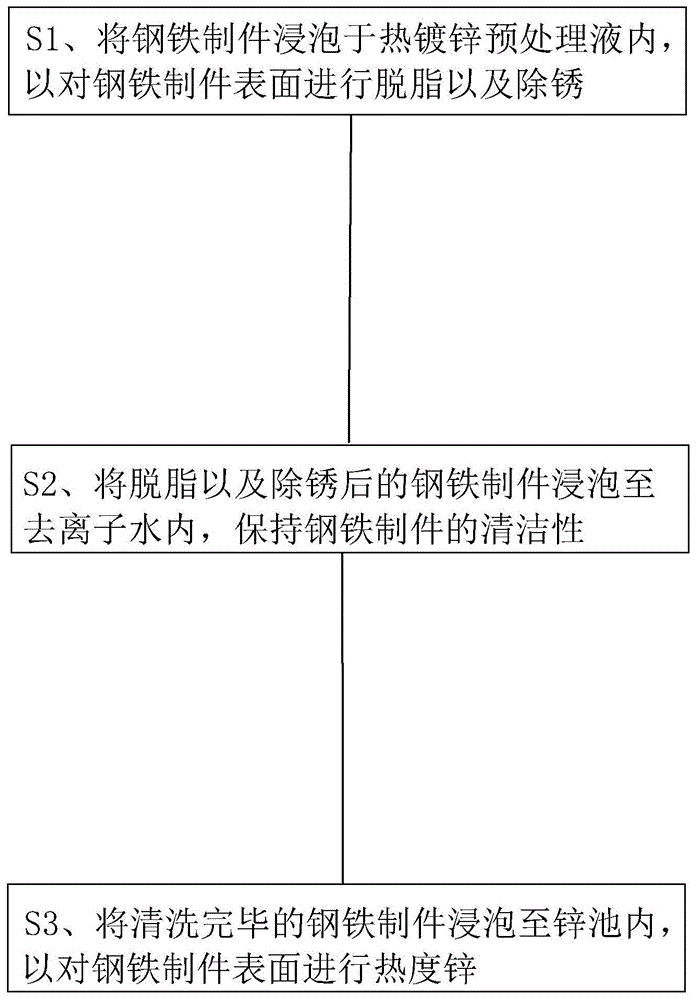
本发明涉及合金镀层制备
技术领域:
,特别涉及一种热镀锌预处理液及其制备方法。
背景技术:
:目前,热镀锌是提高钢铁制件表面抗大气腐蚀的重要手段之一,它先将钢铁制件表面进行预处理,然后浸入熔融的锌液中,在钢铁制件表面形成一层锌金属保护镀层。现有技术中,对钢铁制件表面进行的传统热镀锌工艺具体如下:(1)将钢铁制件浸泡于金属清洗剂中,以对钢铁制件表面进行脱脂;(2)对脱脂完毕的钢铁制件浸泡至去离子水清洗池内,保持钢铁制件表面的清洁性;(3)将清洗完毕的钢铁制件浸泡至金属去锈剂中,以对钢铁制件表面进行除锈;(4)将除锈完毕的钢铁制件浸泡于去离子水清洗池内,保持钢铁制件的清洁性;(5)将清洗完毕的钢铁制件浸泡至锌池内,以对钢铁制件表面进行热度锌。通过上述的传统预处理工艺,能够实现对钢铁制件表面进行去油以及去锈,但是受到传统预处理工艺本身的影响,使上述工艺存在如下缺陷:传统热镀锌预处理工艺中,脱脂工艺与除锈工艺需要分布进行,操作繁琐且浪费时间。技术实现要素:针对现有技术存在的不足,本发明的目的之一在于提供一种热镀锌预处理液,其具有对钢铁制件表面预处理中,脱脂工艺与酸洗工艺同时进行的优点。本发明的第二个目的在于提供一种热镀锌预处理液的制备方法,所述制备方法能够有效促进各组分之间均匀混合,确保热镀锌预处理液具有优良的去油效果以及优良的除锈效果且制备方法简单,便于工业化生产。本发明的第三个目的在于提供一种钢铁制件的热镀锌工艺,其具有减少整体工艺流程,大大减少预处理的时间,提升生产效率的优点。为实现上述第一个目的,本发明提供了如下技术方案:一种热镀锌预处理液,其主要由金属去锈剂和金属去油剂混合搅拌而成;所述金属去锈剂按重量份数计由包括以下物质混合搅拌而成:100-120份质量浓度为36%的盐酸、40-60份去离子水;所述金属去油剂按重量份数计由包括以下物质混合搅拌而成:40-60份去离子水、0.1-2份碳酸锌、0.1-2份苯并三氮唑、1-8份脂肪酸甲酯乙氧基磺酸钠。通过采用上述技术方案,将用于去除钢铁制件表面的铁锈的金属去锈剂与用于去除钢铁制件表面的油污的金属去油剂均匀搅拌混合,其中,金属去锈剂中的质量浓度为36%的盐酸与去离子水进行适配,对钢铁制件表面的铁锈进行氧化还原反应,进而对铁锈进行去除,且金属去油剂中的碳酸锌、苯并三氮唑以及脂肪酸甲酯乙氧基磺酸钠与去离子水进行适配,其中碳酸锌作为碱性盐、苯并三氮唑作为缓蚀剂、脂肪酸甲酯乙氧基磺酸钠作为表面活性剂与去离子水组合形成水基型金属去油剂,将金属除锈剂以及金属去油剂混合,使得热镀锌预处理液可同时脱脂及除锈。进一步地,所述金属去油剂按重量份数计由包括以下物质制备而成:40-60份去离子水、1.2-2份碳酸锌、1.3-2份苯并三氮唑、5-8份脂肪酸甲酯乙氧基磺酸钠。通过采用上述技术方案,金属去油剂原料在此范围内时,能够进一步提高热镀锌预处理液的去油效果,同时由于去离子水含量的变化,促使盐酸的质量浓度保持在20%左右,使得热镀锌预处理液在保证良好的除锈效果的同时,还能避免热镀锌处理液对钢铁制件酸洗过度。进一步地,所述金属去油剂按重量份数计还包括10-50份三氯乙烯。通过采用上述技术方案,在碳酸锌作为碱性盐、苯并三氮唑作为缓蚀剂、脂肪酸甲酯乙氧基磺酸钠作为表面活性剂与去离子水组合形成的水基型金属去油剂中加入有机溶剂三氯乙烯,使得水基型金属去油剂转变为半水基金属去油剂,水基型金属去油剂的主要清洗原理是利用表面活性剂的乳化、渗透、分散与抗再沉积能力对油污脏污进行清洗。其主要清洗特点是:a、不仅对动植油有很好的清洗能力,对矿物油也有很好的清洗作用。适用面很广。b、对金属基体没有任何化学影响,可用黑色金属与有色金属。c、由于活性物的渗透力很强,对一些结构体、盲孔、死角等都能清洗得很彻底。但是水基型金属清洁剂对于重污的油型污垢相对于传统溶剂型金属清洁剂仍有差距,其中传统的溶剂型清洗剂常见的有酒精、汽油、煤油、柴油、白电油、三氯乙烯等有机溶剂,然而传统溶剂型金属清洁剂对水性污垢则无法清洗,如手印。而半水基型金属清洗剂是以水和溶剂为清洗介质,利用表面活性剂的乳化效果,配成水包油型或油包水型的清洗剂,使其清洗能力即结合了水基清洗剂对水性污垢以及大多数油性污垢的清理优势又结合了溶剂型清洗剂对重污的油型污垢的清理优势。进一步地,所述金属去油剂按重量份数计还包括1-2份聚硅氧烷。通过采用上述技术方案,脂肪酸甲酯乙氧基磺酸钠为非离子表面活性剂,由于非离子表面活性剂在溶液中不是以离子状态存在,所以它的稳定性高,不易受强电解质存在的影响,也不易受酸、碱的影响,相容性好,在各种溶剂中均有良好的溶解性,且低泡沫、高浊点、净洗性能优异,所以去污能力极佳。然而,金属去锈剂作为酸性除锈剂对钢铁制件表面进行酸洗时,容易产生氢气,而脂肪酸甲酯乙氧基磺酸钠活化仍会产生气泡,气泡易将酸性物质包裹,进而长时间附着于钢铁制件外表面,进而影响钢铁制件的外观。聚硅氧烷作为热镀锌专用消泡剂,加入至热镀锌预处理液中,对钢铁制件的除锈以及去油进行有效的消泡抑泡,进而保证钢铁制件外观的完整。进一步地,碳酸锌以及苯并三氮唑的粒度为400-900目。通过采用上述技术方案,将碳酸锌以及苯并三氮唑分散至去离子水内,且碳酸锌以及苯并三氮唑的粒度为400-900目,使碳酸锌以及苯并三氮唑充分均匀分散在去离子水内,进而避免热镀锌预处理液出现局部沉淀或分层的现象,影响热镀锌预处理液的去油及除锈效果。为实现上述第二个目的,本发明提供了如下技术方案:一种热镀锌预处理液的制备方法,所述热镀锌预处理液通过如下步骤制备得到:(1)将质量浓度为36%的盐酸与去离子水加入搅拌机中,搅拌得到金属去锈剂;(2)将去离子水、碳酸锌以及苯并三氮唑加入搅拌机中,搅拌得到混合溶液a;(3)将三氯乙烯以及脂肪酸甲酯乙氧基磺酸钠加入至装有混合溶液a的搅拌机内,搅拌得到混合溶液b;(4)最后再将聚硅氧烷加入至装有混合溶液b的搅拌机内,搅拌得到金属去油剂;(5)将金属去锈剂与金属去油剂加入至搅拌机内,搅拌得到热镀锌预处理液。通过采用上述技术方案,先将质量浓度为36%的盐酸加入去离子水中,使质量浓度为36%的盐酸于去离子水充分混合,在搅拌条件下形成金属去锈剂;然后在去离子水内加入碳酸锌以及苯并三氮唑,使其能够在去离子水中通过搅拌均匀分散,得到混合溶液a,之后再将三氯乙烯以及脂肪酸甲酯乙氧基磺酸钠加入至混合溶液a内,通过搅拌,使三氯乙烯以及脂肪酸甲酯乙氧基磺酸钠均匀分散于混合溶液a内并得到混合溶液b,最后再将聚硅氧烷加入至混合溶液b内,通过搅拌,将聚硅氧烷均匀分散于混合溶液b内得到金属去油剂;最后将金属除锈剂与金属去油剂均匀搅拌形成热镀锌预处理液,本申请制备方法不仅操作简单,而且便于控制。进一步地,步骤(1)-(5)中,控制搅拌速度为200-700r/min。通过采用上述技术方案,使质量浓度为36%的盐酸以及去离子水在高速搅拌的条件下,充分均匀分散,形成金属除锈剂,随后将碳酸锌、苯并三氮唑在高速搅拌的条件下充分分散于去离子水内得到混合溶液a,之后再将三氯乙烯以及脂肪酸甲酯乙氧基磺酸钠加入至混合溶液a内,在高速搅拌的条件下充分分散于混合溶液a内得到混合溶液b,最后再将聚硅氧烷加入至混合溶液b内,在高速搅拌的条件下充分分散于混合溶液b得到金属去油剂;最后将金属除锈剂与金属去油剂在高速搅拌的条件下均匀分散,进一步保证热镀锌预处理液各组分的均匀分布。进一步地,步骤(1)中,步骤(1)-(5)中,搅拌时间为10min。通过采用上述技术方案,将质量浓度为36%的盐酸以及去离子水均匀搅拌10min,使其充分均匀分散,形成金属除锈剂,随后将碳酸锌以及苯并三氮唑加入至去离子水内,均匀搅拌10min,使碳酸锌以及苯并三氮唑充分均匀分散于去离子水内,随后将三氯乙烯以及脂肪酸甲酯乙氧基磺酸钠加入至去离子水与碳酸锌以及苯并三氮唑的混合溶液内,均匀搅拌10min,最后将聚硅氧烷加入,继续搅拌10min,通过分布搅拌,将较难分散的粉料提前搅拌间接延长其搅拌时间,进一步保证热镀锌预处理液各组分的均匀分布,最后将金属除锈剂与金属去油剂均匀搅拌10min,进一步保证热镀锌预处理液各组分的均匀分布。进一步地,步骤(1)-(5)中,温度控制为50-90℃。通过采用上述技术方案,金属去油剂的脱脂能力随着温度的上升而逐渐提高,但是由于脂肪酸甲酯乙氧基磺酸钠为非离子型表面活性剂,其在水中的溶解镀随温度升高而降低并产生浊点,在相对较低温度的搅拌条件下,使得脂肪酸甲酯乙氧基磺酸钠更容易的溶解至盐酸溶液内,使金属去油剂的脱脂效果更为优良。为实现上述第三个目的,本发明提供了如下技术方案:一种应用权利要求1-5任一项所述的热镀锌预处理液的热镀锌工艺:s1、将钢铁制件浸泡于热镀锌预处理液内,以对钢铁制件表面进行脱脂以及除锈;s2、将脱脂以及除锈后的钢铁制件浸泡至去离子水内,保持钢铁制件的清洁性;s3、将清洗完毕的钢铁制件浸泡至锌池内,以对钢铁制件表面进行热度锌。通过是上述技术方案,相对于现有技术中对钢铁制键件表面进行的如下传统热镀锌工艺:(1)将钢铁制件浸泡于金属清洗剂中,以对钢铁制件表面进行脱脂;(2)对脱脂完毕的钢铁制件浸泡至去离子水清洗池内,保持钢铁制件表面的清洁性;(3)将清洗完毕的钢铁制件浸泡至金属去锈剂中,以对钢铁制件表面进行除锈;(4)将除锈完毕的钢铁制件浸泡于去离子水清洗池内,保持钢铁制件的清洁性;(5)将清洗完毕的钢铁制件浸泡至锌池内,以对钢铁制件表面进行热度锌;本申请热镀锌预处理液的热镀锌工艺通过配方的改变将脱脂工艺以及除锈工艺合二为一并同时将脱脂工艺以及除锈工艺之间的清洗步骤省去,大大减少预处理的时间,提升生产效率。综上所述,本发明具有以下有益效果:1、将用于去除钢铁制件表面的铁锈的金属去锈剂与用于去除钢铁制件表面的油污的金属去油剂均匀搅拌混合,其中,金属去锈剂中的质量浓度为36%的盐酸与去离子水进行适配,对钢铁制件表面的铁锈进行氧化还原反应,进而对铁锈进行去除,且金属去油剂中的碳酸锌、苯并三氮唑以及脂肪酸甲酯乙氧基磺酸钠与去离子水进行适配,其中碳酸锌作为碱性盐、苯并三氮唑作为缓蚀剂、脂肪酸甲酯乙氧基磺酸钠作为表面活性剂与去离子水组合形成水基型金属去油剂,将金属除锈剂以及金属去油剂混合,使得在对钢铁制件进行预处理工艺时,脱脂工艺与酸洗工艺同时进行;2、在碳酸锌作为碱性盐、苯并三氮唑作为缓蚀剂、脂肪酸甲酯乙氧基磺酸钠作为表面活性剂与去离子水组合形成的水基型金属去油剂中加入有机溶剂三氯乙烯,使得水基型金属去油剂转变为半水基金属去油剂,水基型金属去油剂的主要清洗原理是利用表面活性剂的乳化、渗透、分散与抗再沉积能力对油污脏污进行清洗。其主要清洗特点是:a、不仅对动植油有很好的清洗能力,对矿物油也有很好的清洗作用。适用面很广。b、对金属基体没有任何化学影响,可用黑色金属与有色金属。c、由于活性物的渗透力很强,对一些结构体、盲孔、死角等都能清洗得很彻底。但是水基型金属清洁剂对于重污的油型污垢相对于传统溶剂型金属清洁剂仍有差距,其中传统的溶剂型清洗剂常见的有酒精、汽油、煤油、柴油、白电油、三氯乙烯等有机溶剂,然而传统溶剂型金属清洁剂对水性污垢则无法清洗,如手印;而半水基型金属清洗剂是以水和溶剂为清洗介质,利用表面活性剂的乳化效果,配成水包油型或油包水型的清洗剂,使其清洗能力即结合了水基清洗剂对水性污垢以及大多数油性污垢的清理优势又结合了溶剂型清洗剂对重污的油型污垢的清理优势;3、先将质量浓度为36%的盐酸加入去离子水中,使质量浓度为36%的盐酸于去离子水充分混合,在搅拌条件下形成金属去锈剂;然后在去离子水内加入碳酸锌以及苯并三氮唑,使其能够在去离子水中通过搅拌均匀分散,得到混合溶液a,之后再将三氯乙烯以及脂肪酸甲酯乙氧基磺酸钠加入至混合溶液a内,通过搅拌,使三氯乙烯以及脂肪酸甲酯乙氧基磺酸钠均匀分散于混合溶液a内并得到混合溶液b,最后再将聚硅氧烷加入至混合溶液b内,通过搅拌,将聚硅氧烷均匀分散于混合溶液b内;最后将金属除锈剂与金属去油剂均匀搅拌形成热镀锌预处理液,本申请制备方法不仅操作简单,而且便于控制;4、相对于现有技术中对钢铁制键件表面进行的如下传统热镀锌工艺:(1)将钢铁制件浸泡于金属清洗剂中,以对钢铁制件表面进行脱脂;(2)对脱脂完毕的钢铁制件浸泡至去离子水清洗池内,保持钢铁制件表面的清洁性;(3)将清洗完毕的钢铁制件浸泡至金属去锈剂中,以对钢铁制件表面进行除锈;(4)将除锈完毕的钢铁制件浸泡于去离子水清洗池内,保持钢铁制件的清洁性;(5)将清洗完毕的钢铁制件浸泡至锌池内,以对钢铁制件表面进行热度锌;本申请热镀锌预处理液的热镀锌工艺通过配方的改变将脱脂工艺以及除锈工艺合二为一并同时将脱脂工艺以及除锈工艺之间的清洗步骤省去,大大减少预处理的时间,提升生产效率。附图说明图1是本申请提供的方法的流程图。具体实施方式以下结合具体实施例对本发明作进一步详细说明。本发明中各原料组分如表1:表1各原料组分的来源原料厂家盐酸扬州华富化工碳酸锌阳谷中天锌业苯并三氮唑中北精细化工脂肪酸甲酯乙氧基磺酸钠上海申致化工三氯乙烯上海麦克林聚硅氧烷东菀德丰消泡剂实施例实施例1一种应用热镀锌预处理液的热镀锌工艺:s1、将钢铁制件浸泡于热镀锌预处理液内,以对钢铁制件表面进行脱脂以及除锈;s2、将脱脂以及除锈后的钢铁制件浸泡至去离子水内,保持钢铁制件的清洁性;s3、将清洗完毕的钢铁制件浸泡至锌池内,以对钢铁制件表面进行热度锌。其中s1中涉及的一种热镀锌预处理液,其主要由金属去锈剂和金属去油剂按照7:2的重量比混合搅拌而成。热镀锌预处理液的组成具体见表2所示,其加工操作具体为:(1)将质量浓度为36%的盐酸与去离子水加入搅拌机中,在70℃的温度下,于500r/min的速度匀速搅拌10min,得到金属去锈剂;(2)将去离子水、700目碳酸锌以及700目苯并三氮唑加入搅拌机中,在70℃的温度下,于500r/min的速度匀速搅拌10min,得到混合溶液a;(3)将三氯乙烯以及脂肪酸甲酯乙氧基磺酸钠加入至装有混合溶液a的搅拌机内,在70℃的温度下,于500r/min的速度匀速搅拌10min,得到混合溶液b;(4)最后再将聚硅氧烷加入至装有混合溶液b的搅拌机内,在70℃的温度下,于500r/min的速度匀速搅拌10min,得到金属去油剂;(5)将金属去锈剂与金属去油剂加入至搅拌机内,在70℃的温度下,于500r/min的速度匀速搅拌10min,得到热镀锌预处理液。实施例2-4实施例2-4的热镀锌预处理液与实施例1中的热镀锌预处理液的原料用量有所不同,具体见表2所示。表2实施例1-4中热镀锌预处理液的原料组成及用量重量/g实施例1实施例2实施例3实施例4盐酸110100120110去离子水10012080100碳酸锌1.20.120.8苯并三氮唑1.30.120.9脂肪酸甲酯乙氧基磺酸钠5184三氯乙烯30105020聚硅氧烷1.5121.2实施例5-8实施例5-8的热镀锌预处理液与实施例1中的热镀锌预处理液的原料用量有所不同,具体见表3所示。表3实施例5-7中热镀锌预处理液的原料组成及用量实施例8与实施例1的不同之处在于,步骤(1)-(5)中的搅拌速度为200r/min。实施例9与实施例1的不同之处在于,步骤(1)-(5)中的搅拌速度为700r/min。实施例10与实施例1的不同之处在于,步骤(2)中,碳酸锌以及苯并三氮唑的粒度为400目。实施例11与实施例1的不同之处在于,步骤(2)中,碳酸锌以及苯并三氮唑的粒度为900目。实施例12与实施例1的不同之处在于,步骤(1)-(5)中的混合温度为50℃。实施例13与实施例1的不同之处在于,步骤(1)-(5)中的混合温度为90℃。实施例14与实施例1的不同之处在于,步骤(2)在步骤(5)之前步骤(4)之后搅拌2分钟。对比例对比例1与实施例1的不同之处在于,金属去油剂中不包含苯并三氮唑加入。对比例2与实施例1的不同之处在于,金属去油剂中,用等量的亚硝酸钠替代苯并三氮唑。对比例3与实施例1的不同之处在于,金属去油剂中不包含碳酸锌加入。对比例4与实施例1的不同之处在于,金属去油剂中不包含脂肪酸甲酯乙氧基磺酸钠加入。对比例5与实施例1的不同之处在于,对比例5为
背景技术:
中公开的传统热镀锌工艺。性能检测试验对由实施例1-14以及对比例1-4制备出的热镀锌预处理液进行3次取样,并对样品进行以下性能检测试验,每例中三个检测数据取平均值,具体结果见表4所示。制样:将一片较大铁板表面均匀涂抹过氧化氢,在过氧化氢还湿润的情况下,在铁板表面涂抹氯化钠,随后将铁板放置于通风良好的地方继续风干,通过改变过氧化氢以及氯化钠的含量,控制生锈程度,在铁板生锈后,将锈铁板至于机油池内,待表面吸附有油污后,将铁板均匀分割。去油测试:采用hg/t4738-2014的检测方法对热镀锌预处理液的去油效果进行测试,样品在去污试验机内在30℃下洗涤3h后用测色仪测定样品洗涤前后的白度,由样品洗涤前后的白度差评价热镀锌预处理液的去污效果,以罗马数字ⅰ-ⅳ作为去污值来表征去污效果,去污值越大,表明热镀锌预处理液的去污效果越好。除锈测试:采用国际标准is08501-1中有关除锈等级的内容对热镀锌预处理液的除锈效果进行测试,将样品在热镀锌预处理液池内在30℃下浸泡3h后取出,以字母“sa”表示除锈等级。sa1:即轻度除锈,钢材表面的氧化皮、铁锈和油漆涂层等附着物略微减少。sa2:彻底的除锈。钢材表面的氧化皮、铁锈和油漆涂层等附着物已基本清除,钢材表面附着有不牢的氧化皮、铁锈和油漆涂层等附着物。sa2.5:非常彻底的除锈。钢材表面应无可见的氧化皮、铁锈和油漆涂层等附着物,任何残留的痕迹应仅是点状或条纹状的轻微色斑。sa3:使钢材外观洁净的除锈。钢材表面无氧化皮、铁锈和油漆涂层等附着物,该表面应显示均匀的金属色泽。缓蚀测试:采用gb/t18175-2014中缓蚀性能的测试,通过在去油以及除锈后的样品表面涂抹强酸或者强碱,随后将样品旋转挂片72h,用样品的质量损失计算出缓蚀率,从字母a-d表征缓蚀效果,其中d的质量损失最少且逐步增多。消泡测试:将样品浸泡于热镀锌预处理液内,静止3h后,通过形成泡沫的数量表征消泡效果,从0-3级表征消泡效果,级数越高,消泡效果越好。溶解测试:观察热镀锌预处理液的溶解度。检测结果及分析表4实施例1-14及对比例1-4的热镀锌预处理液的检测数据表以下结合表4提供的实施例1-14及对比例1-4的热镀锌预处理液的检测数据表,详细说明本发明。实施例1-5针对金属去油剂以及金属除锈剂的配比进行了对比。结果发现,实施例2,由于热镀锌预处理液的盐酸的含量减小,使得热镀锌预处理液的除锈效果变差;此外,实施例2以及实施例4中,由于碳酸锌以及脂肪酸甲酯乙氧基磺酸钠的减少,使得热镀锌预处理液的去油效果变差,且由于三氯乙烯的减少,半水基型金属清洗剂的溶剂量减少,热镀锌预处理液的去油效果变差,再加上由于苯并三氮唑的含量也同步减少,使得热镀锌预处理液的缓蚀效果变差,而且,聚硅氧烷的减少,使得热镀锌预处理液的消泡效果显著变差,而实施例3中,热镀锌预处理液的盐酸的含量增大时,实施例3与实施例1的除锈效果一致,实施例3以及实施例5中,碳酸锌、脂肪酸甲酯乙氧基磺酸钠以及三氯乙烯的含量增大时,实施例3以及实施例5的去油效果与实施例1一致,苯并三氮唑的含量增大时,缓蚀效果与实施例1一致,聚硅氧烷的含量增大时,实施例3以及实施例5的消泡效果与实施例1一致,故为成本考虑,实施例1为相对较优。另外,以实施例1为对照,本发明在实施例6中考察了三氯乙烯的影响。结果发现,实施例6中,由于没有三氯乙烯的加入,半水基型金属清洁剂转变为水基型金属清洁剂,使得实施例6对重油污的清洁能力大大降低,且使得实施例6的去油效果以及缓蚀效果显著变差,且由于苯并三氮唑微溶于水而易溶于溶剂,使得实施例6中存在沉淀,进而使苯并三氮唑无法有效对样品进行缓蚀,使得实施例6的缓蚀效果大大降低。本发明在实施例7中考察了聚硅氧烷的影响。结果发现,实施例7中,由于没有聚硅氧烷的加入,三氯乙烯以及脂肪酸甲酯乙氧基磺酸钠由于乳化以及活化而产生的气泡包覆盐酸酸化产生的氢气无法消除而长期存在,进而使实施例7的消泡效果大大降低。本发明在实施例8-9中考察了搅拌速度对热镀锌预处理液的影响,结果发现,在实施例8中,由于搅拌速度显著降低,进而使碳酸锌以及苯并三氮唑由于没有搅拌充分而沉淀,进而使得碳酸锌无法有效对样品进行去油,使得苯并三氮唑无法有效对样品进行缓蚀,导致实施例8的去油效果以及缓蚀效果显著降低,而在实施例9中,搅拌速度显著增加,但是实施例10的所有效果与实施例1一致,为了节约成本,实施例1仍为相对较优。本发明在实施例10-11中考察了碳酸锌以及苯并三氮唑的粒度对热镀锌预处理液的影响,结果发现,在实施例10中,由于碳酸锌以及苯并三氮唑的粒度改为400目而搅拌速度不变,使得碳酸锌以及苯并三氮唑由于无法充分溶解而产生沉淀,进而使得碳酸锌无法有效对样品进行去油,使得苯并三氮唑无法有效对样品进行缓蚀,导致实施例12的去油效果以及缓蚀效果显著降低,而在实施例12中,碳酸锌以及苯并三氮唑的粒度改为900目,但是实施例12的所有效果与实施例1一致,为了节约成本,实施例1仍为相对较优。本发明在实施例12-13中考察了温度对热镀锌预处理液的影响,结果发现,在实施例13中,反应温度改为50℃,由于金属去油剂的脱脂能力随着温度的上升而逐渐提高,使得实施例13由于温度的降低金属去油剂的脱脂能力显著降低;而实施例14中,反应温度改为90℃,由于脂肪酸甲酯乙氧基磺酸钠为非离子型表面活性剂,其在水中的溶解镀随温度升高而降低,在较低温度的搅拌条件下,使得脂肪酸甲酯乙氧基磺酸钠更容易的溶解至盐酸溶液内,而脂肪酸甲酯乙氧基磺酸钠为液体,无沉淀产生,使得实施例14由于表面活性剂的活化效果降低而使得其去油效果降低,故实施例1仍为相对较优。本发明在实施例14中考察了搅拌步骤对热镀锌预处理液的影响,结果发现,在实施例14中,步骤(2)调整至在步骤5)之前步骤(4)之后且仅搅拌2分钟,由于碳酸锌以及苯并三氮唑的搅拌时间显著降低,进而使碳酸锌以及苯并三氮唑由于没有搅拌充分而沉淀,进而使得碳酸锌无法有效对样品进行去油,使得苯并三氮唑无法有效对样品进行缓蚀,导致实施例14的去油效果以及缓蚀效果显著降低,故实施例1仍为相对较优。与实施例1相比,对比例1由于金属去油剂中不包含苯并三氮唑,对比例3缓蚀效果较实施例1显著降低。与实施例1相比,对比例2由于金属去油剂中,用等量的亚硝酸钠替代苯并三氮唑,由于亚硝酸钠为阳极型缓蚀剂,而阳极缓蚀剂在对钢铁制件进行附膜保护时,对浓度有较高的要求,以使全部阳极都被钝化,一旦剂量不足,将在未被钝化的部位造成点蚀,实施例1中,苯并三氮唑为混合型缓蚀剂,相对于阳极型缓蚀剂,混合型缓蚀剂即能在阴极成膜,又可以在阳极成膜,在对浓度要求略微降低的同时,还对成膜的范围进行扩大,进而导致对比例2的缓蚀效果略微降低。与实施例1相比,对比例3由于金属去油剂中不包含碳酸锌,由于碳酸锌作为碱性盐为水基型金属清洁剂的必要组成部分,进而导致对比例3的去油效果略微降低,而对比例4由于金属去油剂中不包含脂肪酸甲酯乙氧基硫磺钠,脂肪酸甲酯乙氧基硫磺钠作为表面活性剂为水基型金属清洁剂的必要组成部分,进而导致实施例4无法活化而造成去油效果显著降低。相对于对比例5的传统热镀锌工艺,采用实施例1中的热镀锌工艺,在对样品表面进行热镀锌中,每条生产线至少能省去2个工艺流程,在达到相同热镀锌效果下,减少来生产时间,增加生产效率。本具体实施例仅仅是对本发明的解释,其并不是对本发明的限制,本领域技术人员在阅读完本说明书后可以根据需要对本实施例做出没有创造性贡献的修改,但只要在本发明的权利要求范围内都受到专利法的保护。当前第1页1 2 3 
起点商标作为专业知识产权交易平台,可以帮助大家解决很多问题,如果大家想要了解更多知产交易信息请点击 【在线咨询】或添加微信 【19522093243】与客服一对一沟通,为大家解决相关问题。
此文章来源于网络,如有侵权,请联系删除



tips