多型腔铸件的加工装置、加工方法及加工装置的制作方法与流程



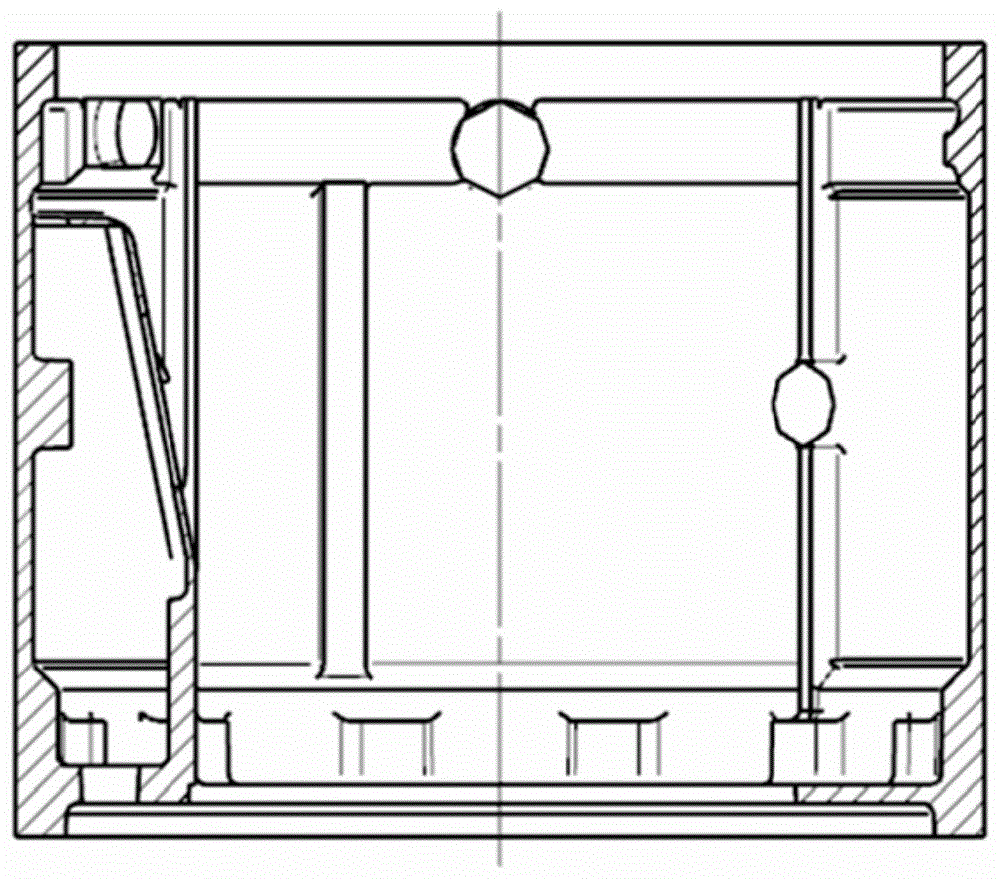
本发明属于铸造技术领域,特别涉及一种多型腔铸件的加工装置、加工方法及加工装置的制作方法。
背景技术:
大型复杂、薄壁铝合金优质铸件的铸造成型一直是国内外铸造领域的研究热点之一。为满足飞航武器在减重、节能、降低制造成本等方面的需求,铝合金铸件正在向结构化、轻量化和薄壁化发展。现有的砂型铸造手段已越来越难以满足大型复杂、精密铝合金铸件的成型与性能要求。同时,航空、航天领域对大型复杂铝合金铸件的整体性、刚性和可靠性提出更高的要求,使得过去通过许多分体零件连接组成的部件转变为整体铸造
铸造生产中发现,薄壁多型腔铸件如后油箱段(如图1所示)分为主腔体和小油池腔,主腔体和小油池腔与后端面连通,具有薄壁区面积大的特点,同时,小油池腔曲面厚度3~4mm,需要一体铸出。铸件尺寸大、壁厚尺寸薄、以及封闭的复杂型腔结构使得该舱段的铸造工艺性大幅度下降。
因此,有必要对该大型复杂、薄壁铸件的铸造装置和工艺进行研究,以满足整体性、薄壁区域的精密成型。
技术实现要素:
为了克服现有技术中的不足,本发明人进行了锐意研究,提供了一种多型腔铸件的加工装置、加工方法及加工装置的制作方法,通过设计能够紧密连接且与铸件型面对应的分体式砂芯,通过砂芯的组合,实现了大尺寸、薄壁厚铸件的整体成型,并通过设计两两相对固定的定位装置,解决了由于芯头间存在微小缝隙,多个砂芯在组合时累计误差过大,导致铸件尺寸精度减小、生产效率降低的问题,有效克服了芯头定位的间隙误差和多个砂芯的组合累计误差,定位精确,一致性好,满足多型腔铸件的尺寸精度要求,从而完成本发明。
本发明提供了的技术方案如下:
第一方面,一种多型腔铸件的加工装置,该加工装置包括底型芯、主腔砂芯、小油池砂芯、第一定位装置和第二定位装置,其中,
所述底型芯的型面与铸件后端面的型面一致;
所述主腔砂芯的型面与铸件的主腔体型面一致;
所述小油池砂芯的型面与铸件的小油池腔型面一致;
所述小油池砂芯和所述主腔砂芯均具有配合形成小油池腔曲面的横向斜面和纵向斜面,两纵向斜面在形成小油池腔曲面端点处相接;
所述主腔砂芯和小油池砂芯组合安装于底型芯上,主腔砂芯与底型芯通过第一定位装置定位安装,小油池砂芯与底型芯通过第二定位装置定位安装,底型芯、主腔砂芯和小油池砂芯组合安装后,整体结构型面与后油箱段内壁型面一致。
第二方面,一种多型腔铸件加工装置的制作方法,包括如下步骤:
底型芯的制作:通过与底型芯具有相同型面的芯盒制作底型芯;
主腔砂芯的制作:通过与主腔砂芯具有相同型面的芯盒制作主腔砂芯,具体地,将芯骨放置在制作主腔砂芯的芯盒中部,芯骨上开设有通孔,芯盒侧壁上加工有盲孔,采用圆锥形定位杆穿过芯骨上的通孔,并进入芯盒侧壁上的盲孔,位于芯骨和芯盒之间的定位杆的结构与主腔砂芯上预留的连接孔结构吻合,向芯骨和芯盒之间装填硅砂、成型拆除芯盒和定位杆,得到主腔砂芯。
小油池砂芯的制作:通过与小油池砂芯具有相同型面的芯盒制作小油池砂芯,具体地,制作小油池砂芯的芯盒侧壁上加工有垂直于小油池砂芯纵向斜面的斜向通孔,斜向通孔位于芯盒内部的开孔端与小油池砂芯上第一螺母所在的位置对应,将螺纹固定杆穿过斜向通孔,其芯盒内部侧的端头固定第一螺母,第一螺母凸出芯盒侧壁,芯盒侧壁外的端头用垫片和螺母紧固,向芯盒内部装填硅砂、成型,拆除芯盒和固定杆,得到小油池砂芯。
第三方面,一种多型腔铸件的加工方法,使用上述第一方面所述的加工装置,通过砂型低压铸造方法实施。
根据本发明提供的一种多型腔铸件的加工装置、加工方法及加工装置的制作方法,具有以下有益效果:
(1)本发明根据多型腔铸件的结构特点,通过设计能够紧密连接且与铸件型面对应的分体式砂芯,通过砂芯的组合,实现了大尺寸、薄壁厚铸件的整体成型;
(2)本发明通过设计两两相对固定的定位装置,解决了由于芯头间存在微小缝隙,多个砂芯在组合时累计误差过大,导致铸件尺寸精度减小、生产效率降低的问题,有效克服了芯头定位的间隙误差和多个砂芯的组合累计误差,定位精确,一致性好,满足多型腔铸件的尺寸精度要求;
(3)本方法中采用的组合定位装置制作简单、通用性强,价格便宜,操作方便,可以反复使用,适用于各种复杂铸件,可提高铸件尺寸精度,降低生产成本。
附图说明
图1示出后油箱段结构示意图;
图2示出本发明一种优选实施方式中后油箱段的加工装置结构示意图;
图3示出第一定位装置的结构示意图;
图4示出第二定位装置的结构示意图;
图5示出第三定位装置的结构示意图;
图6示出制作主腔砂芯的芯盒、芯骨、定位杆的连接结构示意图;
图7示出制作小油池砂芯的芯盒、固定杆与第一螺母的连接结构示意图。
附图标号说明
1-底型芯;2-主腔砂芯;3-小油池砂芯;4-第一定位装置;41-第一定位凹模;42-第一定位凸模;5-第二定位装置;51-第二定位凸模;52-第二定位凹模;6-第三定位装置;61-第一螺母;62-紧固螺杆;63-第二螺母;64-楔形垫片;7-芯骨;8-定位杆;9-固定杆。
具体实施方式
下面通过对本发明进行详细说明,本发明的特点和优点将随着这些说明而变得更为清楚、明确。
基于航空、航天领域对大型复杂铝合金铸件的整体性要求,本发明人进行了大量的摸索研究,确定采用砂型低压铸造方法实施后油箱段的铸造加工,设计了对应的加工装置和加工方法,实现了后油箱段铸件一体化成型,且成型精度高。具体阐述如下:
根据本发明的第一方面,提供了一种多型腔铸件的加工装置,根据后油箱段的结构特点,如图2所示,该加工装置包括底型芯1、主腔砂芯2、小油池砂芯3、第一定位装置4和第二定位装置5,其中,
所述底型芯1的型面与铸件后端面的型面一致,
所述主腔砂芯2的型面与铸件的主腔体型面一致,
所述小油池砂芯3的型面与铸件的小油池腔型面一致,
所述小油池砂芯3和所述主腔砂芯2均具有配合形成小油池腔曲面的横向斜面和纵向斜面,两纵向斜面在形成小油池腔曲面端点处相接;
所述主腔砂芯2和小油池砂芯3组合安装于底型芯1上,主腔砂芯2与底型芯1通过第一定位装置4定位安装,小油池砂芯3与底型芯1通过第二定位装置5定位安装,底型芯1、主腔砂芯2和小油池砂芯3组合安装后,整体结构型面与后油箱段内壁型面一致。
在一种优选的实施方式中,如图3所示,所述第一定位装置4包括第一定位凹模41和第一定位凸模42,所述第一定位凹模41预埋在主腔砂芯2的底部,所述第一定位凸模42对应于第一定位凹模41,预埋在底型芯1上部,装配时,通过将第一定位凸模42插入第一定位凹模41中实现主腔砂芯2和底型芯1间的定位。
进一步地,第一定位凹模41和第一定位凸模42之间为间隙配合,单边间隙为0.05~0.1mm。
进一步地,第一定位凹模41和/或第一定位凸模42伸入砂芯内的一侧加工有固定爪,以提高在砂芯内的牢固度。
在一种优选的实施方式中,如图4所示,所述第二定位装置5包括第二定位凸模51和第二定位凹模52,所述第二定位凸模51预埋在小油池砂芯3的底部,所述第二定位凹模52对应于第二定位凸模51,预埋在底型芯1上部,装配时,通过将第二定位凸模51插入第二定位凹模52中实现小油池砂芯3和底型芯1间的定位。
进一步地,第二定位凸模51和第二定位凹模52之间为间隙配合,单边间隙为0.05~0.1mm。
进一步地,第二定位凸模51和/或第二定位凹模52伸入砂芯内的一侧加工有固定爪,以提高在砂芯内的牢固度。
在一种优选的实施方式中,所述第一定位装置4和第二定位装置5为金属,优选耐磨、耐热模具钢。
在一种优选的实施方式中,所述主腔砂芯2加工为中空结构,中空结构壁面上预埋有芯骨,用于后续主腔砂芯2转运等;结合后油箱段的尺寸,主腔砂芯2上芯骨的内径为170~210mm。
通过上述技术方案,根据铸件的结构和工艺要求,根据多个砂芯,通过砂芯之间的精确定位,可以保证铸件的尺寸精度。
本发明人在后续铸件加工中发现,将主腔砂芯2和小油池砂芯3放置在底型芯1上,然后进行浇注,如果芯头间(砂芯装配位置处)存在微小缝隙,多个砂芯在组合时累计误差过大,可能会导致小油池腔曲面厚度不均、或者存在孔洞,甚至小油池腔曲面难以形成,铸件尺寸精度减小,生产效率降低。
为此,本发明人对砂芯的精确定位进行了更为深入的研究,通过在主腔砂芯2和小油池砂芯3上安装第三定位装置6,进一步对砂芯进行良好的组合定位,有效地克服多个砂芯在组合时的累计误差大、油池腔曲面结构不达标、精度低、生产效率低下等的缺陷。
具体地,如图5所示,所述第三定位装置6包括第一螺母61、紧固螺杆62、第二螺母63,其中,所述第一螺母61预埋在小油池砂芯3朝向主腔砂芯2的纵向斜面内,该预埋点位于小油池砂芯3与主腔砂芯2的紧密贴合部位;主腔砂芯2上预留有连接孔结构,所述紧固螺杆62贯穿连接孔,一端伸入小油池砂芯3与第一螺母61螺纹配合,另一端裸露在芯骨外,与第二螺母63螺纹配合,通过拧紧第二螺母63实现主腔砂芯2和小油池砂芯3间的相对定位。
在一种优选的实施方式中,第一螺母61垂直于螺纹孔的外侧端面与纵向斜面齐平。由于第一螺母61是通过预埋安装在小油池砂芯3内,若第一螺母61深入预埋在小油池砂芯3内部,第一螺母61的深度难以控制,且在小油池砂芯3成型时第一螺母61内易灌填砂粒,难以实现螺纹连接目的。同时,本发明人发现,第一螺母61的安装形态对其在小油池砂芯3中的结合力存在较大影响,当第一螺母61的表面与纵向斜面齐平时,第一螺母61可稳固安装不易脱落,其他安装形态,如垂直固定方式,第一螺母61容易带动附近砂型崩裂,进而脱落。
在一种优选的实施方式中,第一螺母61为碟形螺母,通过螺母翼增加与砂型的结合力。
在一种优选的实施方式中,第二螺母63为碟形螺母。虽然主腔砂芯2内部为中空结构,但由于尺寸限制,难以使用工具紧固螺母,此时采用碟形螺母可便于手动拧紧操作。
在一种优选的实施方式中,主腔砂芯2上预留的连接孔结构为锥孔结构,由第一螺母61端至第二螺母63端,孔径逐渐增大。
在一种优选的实施方式中,第二螺母63内侧安装楔形垫片64,使第一螺母61和第二螺母63平行装配,提高稳定性。所选用的材质为木材或金属。
根据本发明的第二方面,本发明人对多型腔铸件的加工装置的制作方法进行了研究,包括:
底型芯的制作:通过与底型芯1具有相同型面的芯盒制作底型芯1;
主腔砂芯的制作:通过与主腔砂芯2具有相同型面的芯盒制作主腔砂芯2;
小油池砂芯的制作:通过与小油池砂芯3具有相同型面的芯盒制作小油池砂芯3。
在一种优选的实施方式中,在主腔砂芯的制作的步骤中,如图6所示,将芯骨7放置在制作主腔砂芯2的芯盒中部,芯骨7上开设有通孔,芯盒侧壁上加工有盲孔,圆锥形定位杆8穿过芯骨7上的通孔,并进入芯盒侧壁上的盲孔,位于芯骨7和芯盒之间的定位杆8的结构与主腔砂芯2上预留的连接孔结构吻合,向芯骨7和芯盒之间装填硅砂、成型,拆除芯盒和定位杆8,得到主腔砂芯2。
进一步地,芯盒侧壁上加工的盲孔内径不小于第一螺母61的内径。
在一种优选的实施方式中,在小油池砂芯的制作的步骤中,如图7所示,制作小油池砂芯3的芯盒侧壁上加工有垂直于小油池砂芯纵向斜面的斜向通孔,斜向通孔位于芯盒内部的开孔端与小油池砂芯3上第一螺母61所在的位置对应,将螺纹固定杆9穿过斜向通孔,芯盒内部侧的端头固定第一螺母61,第一螺母61凸出芯盒侧壁,芯盒侧壁外的端头用垫片和螺母紧固,向芯盒内部装填硅砂、成型,拆除芯盒和固定杆9,得到小油池砂芯3。
根据本发明的第三方面,本发明提供了一种多型腔铸件的加工方法,使用上述第一方面所述的加工装置,通过砂型低压铸造方法实施。
实施例
实施例1
一种多型腔铸件的加工装置,用于砂型低压铸造后油箱段,如图2所示,该加工装置包括底型芯1、主腔砂芯2、小油池砂芯3、第一定位装置4和第二定位装置5和第三定位装置6,其中,所述底型芯1的型面与铸件后端面的型面一致,所述主腔砂芯2的型面与铸件的主腔体型面一致,所述小油池砂芯3的型面与铸件的小油池腔型面一致,小油池砂芯3和所述主腔砂芯2均具有配合形成小油池腔曲面的横向斜面和纵向斜面,两纵向斜面在形成小油池腔曲面端点处相接;
所述主腔砂芯2和小油池砂芯3组合安装于底型芯1上,主腔砂芯2与底型芯1通过第一定位装置4定位安装,小油池砂芯3与底型芯1通过第二定位装置5定位安装,主腔砂芯2和小油池砂芯3通过第三定位装置6定位;底型芯1、主腔砂芯2和小油池砂芯3组合安装后,整体结构型面与后油箱段内壁型面一致。
第一定位装置4和第二定位装置5的结构如图3和4所示,材质为304不锈钢。第一定位装置4包括第一定位凹模41和第一定位凸模42,单边间隙为0.05mm。第二定位装置5包括第二定位凸模51和第二定位凹模52,单边间隙为0.05mm。
第三定位装置6的结构如图5所示,小油池砂芯3朝向主腔砂芯2的纵向斜面上预埋有与纵向斜面齐平的碟形螺母,螺母翼朝向小油池砂芯3内部;主腔砂芯2内中空,中空结构侧壁安装芯骨,芯骨高400mm,内径180mm,主腔砂芯2上预留有锥孔结构,锥孔结构最小端直径15mm,芯骨上加工有对应的通孔,紧固螺杆62通过芯骨上的通孔、锥孔结构与小油池砂芯3中的碟形螺母配合,裸露在在芯骨外的一端通过楔形垫片64和碟形螺母紧固。所选用的紧固螺杆直径为φ10,长度200mm;碟形螺母的直径为φ10。
采用上述加工装置铸造后油箱段,在不同时间段内生产三批次,第一批加工50个,合格数量49;第二批加工50个,合格数量48;第三批加工50个,合格数量48;铸造的后油箱段,经过3个小批次验证后,合格率稳定在95%以上,远高于行业平均65%的合格率。
以上结合具体实施方式和范例性实例对本发明进行了详细说明,不过这些说明并不能理解为对本发明的限制。本领域技术人员理解,在不偏离本发明精神和范围的情况下,可以对本发明技术方案及其实施方式进行多种等价替换、修饰或改进,这些均落入本发明的范围内。本发明的保护范围以所附权利要求为准。
本发明说明书中未作详细描述的内容属本领域技术人员的公知技术。
起点商标作为专业知识产权交易平台,可以帮助大家解决很多问题,如果大家想要了解更多知产交易信息请点击 【在线咨询】或添加微信 【19522093243】与客服一对一沟通,为大家解决相关问题。
此文章来源于网络,如有侵权,请联系删除


