金属组件及其制造方法与流程



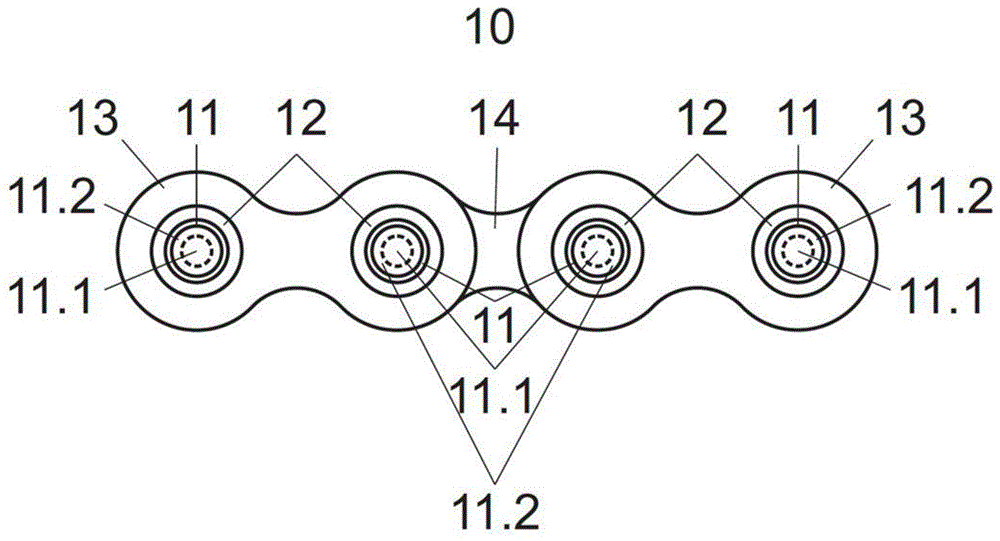
本发明涉及一种用于制造被硬质材料涂层涂覆的金属组件的方法,所述方法包括以下步骤:制备抗结块剂;将所制备的抗结块剂添加到粉末混合物;提供所述粉末混合物;提供由金属制成的基材;在加热装置中加热所述粉末和所述基材;将涂层沉积在所述基材上,所述涂层具有比所述基材高的硬度;以及将所述基材冷却。本发明还涉及具有硬质材料涂层的金属组件。
背景技术:
具有分别通过链节互连的链构件的铰接链以许多形式使用。在用作驱动链或输送链时,具体地,链节的区域的负载如此之重,使得需要抗磨损的支承表面。用经济的涂覆方法和工艺代替昂贵的解决方案也是有用的,特别是在大量零件方面。
de102005047449a1提出了具有改善的磨损性的铰接链,所述铰接链的链螺柱或链套筒设置有硬质材料涂层。这些涂层是使用物理气相沉积(pvd)方法施加的。硬质材料涂层的厚度为1μm到10μm,并且可以另外被润滑涂层(例如,ptfe)包围。
de102006052869a1描述了一种铰接链,其中螺柱和套筒的连接表面设置有pvd硬质材料涂层。在这种情况下,螺柱和套筒由碳含量介于0.4wt.%与1.2wt.%之间的高碳钢组成。
de102011006294a1提出了一种用于制造硬化的经涂覆金属组件的方法。对所述金属组件进行热处理,以便将碳和/或氮浓缩在外层中,并且然后淬火到低于马氏体形成的温度。然后在比随后的涂覆过程发生的温度高的温度下使金属组件回火。涂覆本身是使用化学气相沉积(cvd)或pvd方法执行的。
de102013222244a1描述了一种用于链的链节板,所述链节板设置有减小摩擦的摩擦学涂层。使用pvd或pacvd方法施加所述涂层。
de102016215709a1公开了由钢制成的链组件,如套筒、板、螺柱和滚子,所述链组件设置有减少磨损的crn涂层。crn涂层是使用cvd工艺制造的。在这种情况下,从钢中获得氮,所述钢可以任选地在处理之前被氮化。
wo2014019699a1中提出了一种用于滚子链或套筒型链的链节。使用pvd或cvd方法将氮化物或碳化物硬质材料涂层施加到链节。
用于制造硬化的经涂覆金属组件的上述解决方案具有缺点。pvd工艺需要10-4pa到10pa的工作压力,并且根据涂层类型在几百℃的工作温度下进行。因此,pvd工艺对涂覆室提出了很高的要求。此外,它们不适合于松散材料。基材和要沉积的材料(目标)在涂覆室中在空间上分离。pvd工艺是所谓的视线工艺,即,仅涂覆从目标可见的表面。内表面或孔被涂覆得更薄。此外,当使用抗结块剂时,所有粉末工艺都具有抗结块剂的成分嵌入硬质材料涂层中的风险。这可能导致对硬质材料涂层的损坏并损害所述涂层的性能。
因此,本发明要解决的问题是提供一种用于制造硬化的经涂覆金属组件,优选地钢组件,特别是金属氮化物或金属碳化物涂层的方法,所述金属氮化物或金属碳化物涂层易于使用,每单位时间允许涂覆大量零件并且对于应用是经济的。同时,由于在使用抗结块剂时防止了抗结块剂的成分嵌入硬质材料涂层中,因此确保了硬质材料涂层的足够高的质量。
所述问题通过根据权利要求1的根据本发明的方法和根据权利要求11的金属组件来解决。本发明的其它有利的实施例在从属权利要求中阐述。
根据本发明的用于制造被硬质材料涂层涂覆的金属组件的方法具有至多七个方法步骤。在第一方法步骤中,制备抗结块剂。在第二方法步骤中,将所制备的抗结块剂添加到粉末混合物。在第三方法步骤中,提供所述粉末混合物。
在第四方法步骤中,提供由金属组成的基材。在第五方法步骤中,在加热装置中加热所述粉末混合物和所述基材。在第六方法步骤中,将涂层沉积在所述基材上。沉积的涂层具有比所述基材高的硬度。在第七方法步骤中,将所述基材冷却。随后也可以进行硬化、回火和滚筒抛光的方法步骤。
使用化学气相沉积(cvd),将硬质涂层沉积在由含碳钢制成的基材上,所述涂层具有很高的抗磨损性和耐磨性,硬度高,耐高温,摩擦小,并且具有良好的化学性质和低的粘附趋势。除了提高抗磨损性外,硬质材料涂层还提高了耐腐蚀性。含碳钢优选地用于基材,因为这些钢具有足够的强度和良好的回火性质。金属和非金属硬质材料两者均可以用于硬质材料涂层。硬质材料涂层尤其优选地由过渡元素(例如,钒、铬、钨、锆和钛)的碳化物、氮化物、碳氮化物、硼化物和硅化物制成。金刚石和类金刚石碳(dlc)以及刚玉、碳化硼、立方氮化硼、碳化硅或氮化铝适合作为非金属硬质材料。在本发明的优选实施例中,基材是钢基材,并且硬质材料涂层是碳化物、氮化物和/或碳氮化物涂层。
与现有技术中已知的用于制造硬质材料涂层的pvd方法相比,cvd方法具有优势。与pvd方法相比,cvd方法适合于松散材料,并且在设备工程、操作和工艺技术方面具有经济优势:例如,要涂覆的基材在转筒中与粉末混合。在特定的工艺温度下执行涂覆过程持续若干小时。基材的所有可及表面均被均匀涂覆,包含狭窄的孔。在涂覆过程结束时,将经涂覆基材冷却。在pvd方法中,基材和要沉积的材料不利地在空间上分离;通过在10-4pa到10pa的工作压力下使要沉积的材料蒸发来执行涂覆。
具体地,粉末混合物具有惰性抗结块剂,例如,al2o3。抗结块剂使粉末混合物保持干燥,以便避免结团。此外,在涂覆过程期间防止了金属的部分烧结和熔合。抗结块剂的颗粒在cvd工艺期间掺入硬质材料涂层中,并且因此防止形成均质的硬质材料涂层。基本上存在两种用于使硬质材料涂层中的抗结块剂含量保持尽可能低的选择方案:减少粉末混合物中的抗结块剂的含量;以及制备抗结块剂,使得粉末混合物中的抗结块剂的粒度分布尽可能大,并且仅具有较少的细粒含量。与小颗粒相比,大颗粒一旦其粘附到基材上就可以在涂覆过程期间通过机械摩擦更容易地从硬质材料涂层中去除。
在从属权利要求2到9中阐述了本发明的用于硬质材料涂层的另外的实施例。
在本发明的另一个实施例中,粉末混合物中的抗结块剂的含量小于或等于50wt.%,优选地小于或等于25wt.%,并且特别优选地小于或等于20wt.%。保持粉末混合物中的抗结块剂的含量尽可能低,以便防止抗结块剂掺入硬质材料涂层中。
在本发明的改进方案中,硬质材料涂层中的al的含量低于10at.%,优选地低于5at.%,并且特别优选地低于3at.%。
在本发明的另一个实施例中,制备抗结块剂的方法步骤涉及改变粒度分布。制备抗结块剂,使得粉末混合物中的抗结块剂的粒度分布尽可能大。与小颗粒相比,大颗粒一旦其粘附到基材上就可以在涂覆过程期间通过机械摩擦更容易地从硬质材料涂层中去除。较小的抗结块剂颗粒也更容易被生长中的涂层包围并嵌入硬质材料涂层中。
在本发明的另一个实施例中,通过筛分、沉降、过滤和/或离心、空气分级和/或气动分级来改变粒度分布。
在本发明的另一个实施例中,制备抗结块剂涉及洗涤抗结块剂。洗涤对于将抗结块剂沉降或过滤并干燥以改变粒度分布是必须的。
在本发明的另一方面,抗结块剂的粒度小于20μm的颗粒的含量小于25%,优选地小于15%,并且特别优选地小于10%。大小超过20μm的颗粒的含量应尽可能高,因为与小颗粒相比,大颗粒一旦其粘附到基材上就可以在涂覆过程期间通过机械摩擦更容易地从硬质材料涂层中去除。
在本发明的另一个实施例中,抗结块剂的粒度小于10μm的颗粒的含量小于20%,优选地小于12%,并且特别优选地小于8%。当涂层具有通常达到的涂层厚度1–25μm时,较小的抗结块剂颗粒一旦粘附到基材上就无法脱离,或者仅在付出巨大努力的情况下才能脱离。因此,将这些小于10μm的特别小的颗粒的含量设置得尽可能低。
在本发明的另一个实施例中,抗结块剂含有al2o3。al2o3是具有高熔点和高硬度的惰性固体,并且防止了部分烧结。al2o3也可以低成本获得。其它可能的抗结块剂是高岭土(硅酸铝)、莫来石(氧化铝和氧化硅)、氧化锆、氮化物或硅化物陶瓷和/或任何其它陶瓷惰性物质。
在本发明的另一个实施例中,根据本发明的方法的工艺温度至少部分地高于450℃,优选地高于500℃,并且特别优选地高于550℃。这些高温对于允许用于形成硬质材料涂层的cvd方法中的反应发生是必需的。
通过根据权利要求10的金属组件还解决了根据本发明的问题。
被硬质材料涂层涂覆的根据本发明的金属组件具有由钢制成的基材和由金属碳化物和/或金属氮化物或其混合物制成的硬质材料涂层。硬质材料涂层还具有抗结块剂颗粒。根据本发明,通过硬质材料涂层的显微照片确定的硬质材料涂层中抗结块剂颗粒的表面含量小于15%,优选地小于10%,并且特别优选地少于5%。由于通过例如筛分来制备抗结块剂,与现有技术中已知的解决方案相比,减少了硬质材料涂层中的抗结块剂颗粒的表面含量,并且因此实现了明显更均质的硬质材料涂层。
在从属权利要求11和12中阐述了本发明关于金属组件的另外的实施例。
在本发明的改进方案中,硬质材料涂层中的al的含量小于10at.%,优选地小于5at.%,并且特别优选地小于3at.%。
在本发明的另一个实施例中,基材是链组件,例如,链组件的内板和/或外板、套筒和/或螺柱。链具有通过内板连接的外板,螺柱分别可旋转地安装在套筒中。螺柱和套筒在操作期间经受较高的磨损,并且因此特别适合被硬质材料涂层涂覆。螺柱和/或套筒的连接表面上的硬质材料涂层的涂层厚度为1μm到40μm。尽管涂层厚度较小,但是螺柱和/或套筒的连接表面上的这些硬质材料涂层防止了腐蚀并具有良好的抗磨损性。在这种情况下,在螺柱与套筒之间的接触区域设置有硬质材料涂层是足够的。
在本发明的另一个实施例中,基材是链组件,例如,链组件的内板和/或外板、套筒和/或螺柱。链具有通过内板连接的外板,螺柱分别可旋转地安装在套筒中。螺柱和套筒在操作期间经受较高的磨损,并且因此特别适合被硬质材料涂层涂覆。与常规的保护涂层相比,当将硬质材料涂层用于链时,螺柱和/或套筒的连接表面上的硬质材料涂层具有1μm到40μm的涂层厚度是足够的。尽管涂层厚度较小,但是螺柱和/或套筒的连接表面上的这些硬质材料涂层具有良好的抗腐蚀保护性和良好的抗磨损性。在这种情况下,在螺柱与套筒之间的接触区域设置有硬质材料涂层是足够的。
在本发明的另一个实施例中,基材是链组件,例如,链组件的内板和/或外板、套筒和/或螺柱。链具有通过内板连接的外板,螺柱分别可旋转地安装在套筒中。螺柱和套筒在操作期间经受较高的磨损,并且因此特别适合被硬质材料涂层涂覆。与常规的保护涂层相比,当将硬质材料涂层用于链时,螺柱和/或套筒的连接表面上的硬质材料涂层具有1μm到40μm的涂层厚度是足够的。尽管涂层厚度较小,但是螺柱和/或套筒的连接表面上的这些硬质材料涂层具有良好的抗腐蚀保护性和良好的抗磨损性。在这种情况下,在螺柱与套筒之间的接触区域设置有硬质材料涂层是足够的。在本发明的优选实施例中,链组件由含碳钢制成。
根据本发明的传感器装置和方法的实施例在附图中示意性地且以简化的方式示出,并且在下面的描述中更详细地进行解释。
在附图中:
图1示出了用于链驱动装置的链的设计;
图2示出了在未事先制备抗结块剂的情况下使用现有技术的cvd方法形成硬质材料涂层的工艺;
图3示出了在事先制备抗结块剂的情况下使用根据本发明的cvd方法形成硬质材料涂层的工艺;
图4示出了在未预先制备抗结块剂的情况下使用现有技术的cvd方法制造的硬质材料涂层的显微照片;
图5示出了在预先制备抗结块剂的情况下使用根据本发明的cvd方法制造的硬质材料涂层的显微照片。
根据本发明的用于制造被硬质材料涂层涂覆的金属组件的方法的实施例以及根据本发明的被硬质材料涂层涂覆的金属组件的实施例在附图中示意性地且以简化的方式示出,并且在下面的描述中更详细地进行解释。
图1示出了可以在例如链驱动装置中使用的链10的两个链构件。链10被设计为套筒型链,所述套筒型链包括分别通过链节连接的内链构件和外链构件。内链节由平行延伸的两个内板13和将内凸出件13彼此连接的两个套筒12组成,套筒12垂直于内板13。
外链构件14由平行延伸的两个外板14组成,并且通过两个螺柱11互连,螺柱11可旋转地安装在内链构件13的套筒12中。外链构件14通过螺柱11可旋转地紧固到邻近的内链构件13,并且通过外板14将内链构件13连接到第二内链构件13,外板14与内板13平行地延伸。外链构件14的螺柱11可旋转地安装在内链构件13的套筒12中,由此分别形成链10的链节的连接。链10的螺柱11完全由钢(例如,100cr6)组成,螺柱11的连接表面设置有使用cvd方法施加的硬质材料涂层。可替代地或另外,套筒12也可以由钢制成并且在其连接表面或支承表面上设置有cvd硬质材料涂层。
下面通过实例描述根据本发明的链构件的螺柱11的涂覆方法,所述螺柱由100cr6钢组成。在涂覆过程开始之前,将抗结块剂1洗涤、沉降和干燥,以便将细粒内含物分离。
为了进行比较,使用现有技术中已知的尚未制备的抗结块剂1对同一基材执行涂覆方法。在两种情况下,抗结块剂均为al2o3。未制备的抗结块剂1在筛分分析中显示出以下粒度分布:0-5%>0.2mm,5-15%0.125-0.2mm,65-80%0.063-0.125mm,0-15%0.04-0.063mm,0-10%<0.04mm。因此,粒度为63-125μm的颗粒在抗结块剂1中的比例最高。还以0.4%的比例添加氯化铵作为活化剂2。
对于两个实施例,通过硬化对螺柱11进行预处理。将80kg的螺柱11与37kg的粉末和37kg的抗结块剂混合,并且在旋转鼓中以7rpm和950℃在无氧氮气气氛中在常压下涂覆6小时。粉末具有20%到30%的fe和70%到80%的v。在涂覆之后,将螺柱11在空气冷却室中冷却。涂覆过程的目标是尽可能均质并且抗结块剂1的含量尽可能低的vc硬质材料涂层。
图2示意性地示出了在现有技术中已知的cvd工艺期间形成硬质材料涂层的工艺。粉末具有成分:抗结块剂1、活化剂2、fe3和v4。在涂覆过程之前硬化的松散材料5在cvd工艺期间设置有硬质材料涂层6。硬质材料涂层6由源自粉末的金属和源自松散材料5的碳形成。此外,剥离材料1的颗粒嵌入硬质材料涂层6中。抗结块剂1的颗粒的粒度变化很大,这通过颗粒的不同直径来指示。硬质材料涂层6中的抗结块剂1的含量也较高,这通过抗结块剂1的颗粒的数量来指示。显微照片(图4)证实了这种示意性表示。
图3示出了在根据本发明的方法期间形成硬质材料涂层的工艺。粉末具有成分:抗结块剂1、活化剂2、fe3和v4。松散材料5在cvd工艺期间设置有硬质材料涂层6。硬质材料涂层6由源自粉末的金属和源自松散材料5的碳形成。抗结块剂1的颗粒也嵌入在硬质材料涂层6中。然而,抗结块剂1的颗粒的粒度分布小于前述实施例中的粒度分布,这是通过洗涤、沉降和干燥对抗结块剂1进行预处理的结果。抗结块剂1的较小颗粒大小通过制备工艺分离。制备的抗结块剂1在筛分分析中显示出以下粒度分布:0-5%>0.2mm,5-15%0.125-0.2mm,65-80%0.063-0.125mm,0-10%0.04-0.063mm,0-5%<0.04mm。硬质材料涂层6中的抗结块剂1的含量也明显降低。显微照片(图5)证实了这种示意性表示。
图4示出了螺柱11上的使用现有技术中已知的方法,即,在未制备抗结块剂1的情况下制造的硬质材料涂层6的显微照片。硬质材料涂层6的涂层厚度在此小于10μm。硬质材料涂层6中还包含可通过暗色识别的抗结块剂1。硬质材料涂层中的抗结块剂1的表面含量为大约18%,直径范围为0.1μm到2μm。
图5示出了螺柱11上的通过根据本发明的方法,即,在通过洗涤、沉降和干燥制备抗结块剂1的情况下制造的硬质材料涂层6的显微照片。此实施例中的硬质材料涂层6的涂层厚度小于10μm。硬质材料涂层6中还包含可通过暗色识别的抗结块剂1。硬质材料涂层6中的抗结块剂1的表面含量为大约2.5%,直径范围为0.1μm到2μm。硬质材料涂层6中的抗结块剂1的含量明显低于在未事先制备抗结块剂1的情况下的含量。因此,与来自现有技术的迄今已知的解决方案相比,根据本发明的方法使用制备的抗结块剂(此处具体地是其超细成分与所使用的粉末分离的抗结块剂)制造了明显更均质的硬质材料涂层6。
在另一个实施例中,通过硬化来对螺柱11进行预处理。将80kg的螺柱11与40kg的fecr粉末和30kg的抗结块剂(此处为al2o3)混合,并且在旋转鼓中以7rpm和950℃在无氧氮气气氛中在常压下涂覆6小时。粉末具有20%到30%的fe和70%到80%的cr。在涂覆之后,将螺柱11在空气冷却室中冷却。涂覆过程的目标是尽可能均质并且抗结块剂1的含量尽可能低的crn硬质材料涂层。
在此实施例中,粉末具有成分:抗结块剂1、活化剂2、fe3和cr4。基材材料5是含碳钢,并且在cvd工艺期间设置有硬质材料涂层6。硬质材料涂层6由源自粉末的金属和源自所述气氛的氮形成。抗结块剂1的颗粒也嵌入在硬质材料涂层6中。通过洗涤、沉降和干燥来制备抗结块剂1,并且将具有小粒度的抗结块剂的级分的内含物分离。剩余的抗结块剂粉末用于cvd工艺的粉末混合物中。制备的抗结块剂1在筛分分析中显示出以下粒度分布:0-5%>0.2mm,5-15%0.125-0.2mm,65-80%0.063-0.125mm,0-10%0.04-0.063mm,0-5%<0.04mm。硬质材料涂层6中的抗结块剂1的含量非常低。edx分析表明硬质材料涂层中的al含量为4.5at.%。
附图标记列表
1抗结块剂
2活化剂
3金属1
4金属2
5松散材料基材材料
6硬质材料涂层
10链
11螺柱
12套筒
13内板
14外板
m金属
n碳
起点商标作为专业知识产权交易平台,可以帮助大家解决很多问题,如果大家想要了解更多知产交易信息请点击 【在线咨询】或添加微信 【19522093243】与客服一对一沟通,为大家解决相关问题。
此文章来源于网络,如有侵权,请联系删除


