带有铍铜块的浇铸模具的制作方法



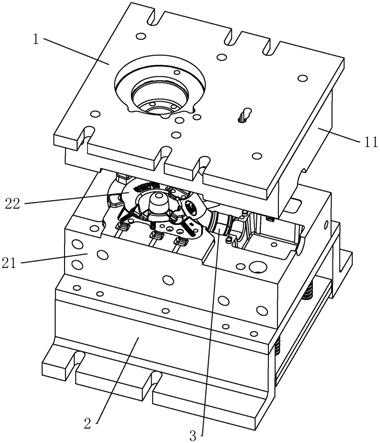
[0001]
本实用新型涉及浇铸模具的技术领域,尤其是涉及一种带有铍铜块的浇铸模具。
背景技术:
[0002]
浇铸成型又称铸塑,是将已准备好的浇铸原料注人模具中,并使其固化,即可获得与模具型腔相似的制品。浇铸成型的原料可以是单体、经初步聚合或缩聚的浆状物或聚合物与单体的溶液等。
[0003]
现有一种用于成型压壳的浇铸模具,其结构如图1和图2所示,包括上模11和下模21,上模11和下模21互相朝向的端面上分别设有用于成型压壳的上型腔12和下型腔22。浇铸时,将熔融的液态金属倒注入浇铸模具,熔融的金属逐渐固化,即可形成压壳。
[0004]
上述技术方案存在以下缺陷:熔融的金属在凝固时,各处的冷却速度不均匀,使得压壳成型后容易发生变形。
技术实现要素:
[0005]
针对现有技术存在的不足,本实用新型的目的是提供一种带有铍铜块的浇铸模具,其具有降低压壳成型后变形的可能性的效果。
[0006]
本实用新型的上述发明目的是通过以下技术方案得以实现的:
[0007]
一种带有铍铜块的浇铸模具,包括下模,所述下模的顶面上设有下型腔,所述下型腔的底面上嵌设有铍铜块。
[0008]
通过采用上述技术方案,在下型腔的底面设置铍铜块,熔融的金属注入上型腔与下型腔之间后,铍铜块的导热性比下模好,可以加速熔融金属中的热量散失,从而加快熔融金属中冷却速度慢的区域冷却,提高熔融金属冷却速度的均匀性,以降低压壳成型后变形的可能性。
[0009]
本实用新型在一较佳示例中可以进一步配置为:所述下型腔的底面上沿竖直方向设有滑移孔,所述铍铜块滑动穿设于滑移孔中,所述铍铜块的侧面底端设有限位块,所述下模的底面上开设有用于容纳限位块的限位槽。
[0010]
通过采用上述技术方案,在铍铜块的侧面底端设置限位块,并将铍铜块与下模滑动配合,可以方便拆卸铍铜块。且限位块与限位槽抵紧时,铍铜块的顶面与下型腔的底面重合,从而保证压壳成型的精度。
[0011]
本实用新型在一较佳示例中可以进一步配置为:所述铍铜块的底面设有锁紧块,所述下模的底面上开设有用于容纳锁紧块的锁紧槽,所述锁紧块的底面上穿设有锁紧螺栓,所述锁紧螺栓与下模螺纹连接,所述铍铜块通过锁紧块与下模栓接。
[0012]
通过采用上述技术方案,设置锁紧块,并在锁紧块上穿设锁紧螺栓,可以方便穿设锁紧螺栓,并将铍铜块与下模栓接。
[0013]
本实用新型在一较佳示例中可以进一步配置为:所述铍铜块的侧面设有密封块,所述滑移孔的侧壁上设有密封槽,所述密封槽的底面与下模的底面连通。
[0014]
通过采用上述技术方案,在铍铜块的侧面设置密封块,可以延长铍铜块与滑移孔之间的渗流路径,进而降低下型腔内的熔融金属从铍铜块与滑移孔之间渗出的可能性。
[0015]
本实用新型在一较佳示例中可以进一步配置为:所述铍铜块上设有进液通道和出液通道,所述进液通道和出液通道的底端均与锁紧块的底面连通,进液通道和出液通道的顶端互相连通。
[0016]
通过采用上述技术方案,在铍铜块上设置进液通道和出液通道,并将进液通道和出液通道连通,当浇铸的熔融金属固化时,向进液通道内供送水冷液,可以加速下型腔内的熔融金属固化。
[0017]
本实用新型在一较佳示例中可以进一步配置为:所述铍铜块包括本体和设置在本体顶面上的顶块,所述进液通道和出液通道的顶端均与本体的顶面连通,所述本体的顶面上设有螺旋形的冷却流道,所述冷却流道的两端分别与进液通道、出液通道连通。
[0018]
通过采用上述技术方案,在本体的顶面上设置螺旋形的冷却流道,可以提高水冷液在与顶块的接触面积,进而提高水冷液对顶块降温的效果,加速下型腔内的熔融金属固化。
[0019]
本实用新型在一较佳示例中可以进一步配置为:所述冷却流道的内壁上设有若干个凸起。
[0020]
通过采用上述技术方案,在冷却流道的内壁上设置凸起,可以增加冷却液在冷却流道中的紊流,进而提高冷却液与顶块之间的热量交换的效率。
[0021]
本实用新型在一较佳示例中可以进一步配置为:所述本体的顶面上设有环形的容纳槽,所述容纳槽环绕冷却流道设置,所述容纳槽内设有密封环,所述密封环的顶面与本体的顶面齐平。
[0022]
通过采用上述技术方案,设置密封环,可以提高本体与顶块之间的密封性,降低冷却流道中的水冷液泄漏的可能性。
[0023]
综上所述,本实用新型包括以下至少一种有益技术效果:
[0024]
1.通过设置铍铜块,可以起到降低压壳成型后变形的可能性的效果;
[0025]
2.通过设置限位块和限位槽,可以起到保证压壳成型精度的效果;
[0026]
3.通过设置进液通道和出液通道,可以起到加速下型腔内的熔融金属固化的效果。
附图说明
[0027]
图1是背景技术中用于成型压壳的浇铸模具的整体结构示意图;
[0028]
图2是背景技术中用于体现上型腔结构的示意图;
[0029]
图3是实施例1的整体结构示意图;
[0030]
图4是实施例1中用于体现上型腔结构的示意图;
[0031]
图5是实施例1中用于体现铍铜块与下模配合方式的示意图;
[0032]
图6是实施例2中用于体现铍铜块结构的示意图;
[0033]
图7是实施例2中用于体现铍铜块与下模配合方式的示意图。
[0034]
图中,1、上模座;11、上模;12、上型腔;2、下模座;21、下模;22、下型腔;23、滑移孔;24、密封槽;25、限位槽;26、锁紧槽;3、铍铜块;31、本体;311、密封块;312、限位块;313、锁紧
块;314、锁紧螺栓;32、顶块;4、冷却流道;41、凸起;42、进液通道;43、出液通道;44、容纳槽;441、密封环。
具体实施方式
[0035]
以下结合附图对本实用新型作进一步详细说明。
[0036]
实施例:
[0037]
参照图3和图4,为本实用新型公开的一种带有铍铜块的浇铸模具,包括下模座2和上模座1,下模座2沿水平方向摆放设置,上模座1位于下模座2的正上方,且上模座1和下模座2互相朝向的端面上分别栓接有上模11和下模21。上模11和下模21互相朝向的端面上分别开设有上型腔12和下型腔22,上模11与下模21互相朝向的端面贴合时,上型腔12与下型腔22拼合形成用于成型压壳的型腔。
[0038]
参照图5,下型腔22的底面沿竖直方向开设有滑移孔23,滑移孔23的截面为矩形。滑移孔23的四个侧棱做倒角处理。滑移孔23内滑动穿设有铍铜块3,铍铜块3的顶面与下型腔22的底面重合。
[0039]
参照图5,铍铜块3的侧面底端一体成型有两个限位块312,两个限位块312分别位于铍铜块3的两侧,下模21的底面上开设有用于容纳限位块312的限位槽25。顶块32的顶面与下型腔22的底面重合时,限位块312的顶面与限位槽25的槽底抵紧,利用限位块312与限位槽25配合,来保证顶块32的顶面与下型腔22的底面重合,保证压壳成型后的精度。
[0040]
参照图5,铍铜块3的底面上还栓接有一个锁紧块313,锁紧块313的长度方向平行于两个限位块312之间的连线,锁紧块313的长度大于两个限位块312之间的最大距离。下模21的底面上开设有用于容纳锁紧块313的锁紧槽26,锁紧块313的底面上穿设有两个锁紧螺栓314,两个锁紧螺栓314分别位于铍铜块3的两侧。两个锁紧螺栓314的螺纹端分别与锁紧槽26的顶面螺纹连接。
[0041]
本实施例的实施原理为:本方案中,将上模11与下模21拼合后,上型腔12与下型腔22拼合为整体的型腔。向型腔内注入熔融的金属,随后型腔内的熔融金属开始固化。铍铜块3可以加快与自身接触的熔融金属固化,进而保证熔融金属各处的固化速度更均匀,以降低压壳成型后变形的可能性。
[0042]
实施例2:
[0043]
参照图6和图7,本实施例与实施例1的不同之处在于:铍铜块3包括本体31和焊接在本体31顶面上的顶块32,顶块32的顶面与下型腔22的底面重合。
[0044]
参照图6和图7,本体31的侧面顶端一体成型有密封块311,密封块311沿本体31的周向设置,密封块311的截面为矩形。滑移孔23的侧壁上开设有用于容纳密封块311的密封槽24,密封槽24与下模21的底面连通,密封块311与密封槽24的顶面抵紧,以延长铍铜块3与滑移孔23之间的渗流距离,从而降低下型腔22内的熔融金属从铍铜块3与滑移孔23之间渗出的可能性。
[0045]
参照图6,本体31的顶面上开设螺旋形的冷却流道4,冷却流道4的底面上胶接有若干个凸起41,若干个凸起41沿冷却流道4的长度方向均匀排列。冷却流道4的两端分别开设有进液通道42和出液通道43,进液通道42和出液通道43均沿竖直方向贯穿本体31和锁紧块313。向进液通道42内供送水冷液,水冷液经过冷却流道4和出液通道43流出,加速顶块32上
的热量散失,进而加速下型腔22内的熔融金属固化。
[0046]
参照图6,本体31的顶面上开设有一个环形的容纳槽44,容纳槽44环绕冷却流道4设置,且容纳槽44的截面为矩形。容纳槽44内铺设有密封环441,密封环441为橡胶环,密封环441的顶面与本体31的顶面齐平。当本体31与顶块32焊接固定时,密封环441的顶面与顶块32的底面抵紧,可以提高本体31与顶块32之间的密封性,从而降低冷却流道4中水冷液泄露的可能性。
[0047]
本具体实施方式的实施例均为本实用新型的较佳实施例,并非依此限制本实用新型的保护范围,故:凡依本实用新型的结构、形状、原理所做的等效变化,均应涵盖于本实用新型的保护范围之内。
起点商标作为专业知识产权交易平台,可以帮助大家解决很多问题,如果大家想要了解更多知产交易信息请点击 【在线咨询】或添加微信 【19522093243】与客服一对一沟通,为大家解决相关问题。
此文章来源于网络,如有侵权,请联系删除



tips