一种提高连铸扇形段轻压下开口度控制精度的控制方法与流程



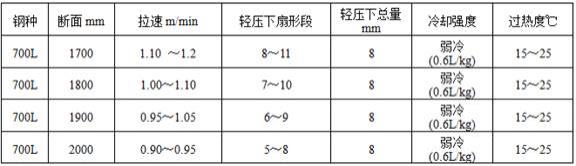
[0001]
本发明涉及一种提高连铸扇形段轻压下开口度控制精度的控制方法,属于炼钢连铸技术领域。
背景技术:
[0002]
达涅利板坯连铸机自2008年投产以来,已运行12年,由于连铸机运行时间久,铸机作业率高,加上设备结构复杂,工况条件差,扇形段运行状况不甚理想,影响了连铸生产节奏,对连铸铸坯质量存在不同程度的影响,给公司造成比较严重经济损失。
[0003]
在实际生产中,铸机扇形段上线运行一段时间以后出现实际辊缝值与目标值偏差的问题,尤其在生产大断面、高强度高硬度钢种时出现凝固末端轻压下扇形段辊缝较设定目标偏差大的问题尤为突出。
[0004]
一段时间以来,实际生产高强管线钢、大梁钢及耐磨钢铸坯经低倍检测在三角区附近内部裂纹时有发生,且出现中心偏析级别在c类1.5以上比例增多,轧材冲击性能不合比例有所增高。亟待提出其解决方法。
[0005]
目前特定钢种及特点尺寸断面,扇形段压不到位现象普遍存在,以弯曲段及铸坯凝固末端最多。铸坯在凝固收缩过程中,主要受扇形段辊面和辊缝的约束,扇形段辊面、辊缝精度直接导致铸坯偏析、内裂等严重的质量问题。
技术实现要素:
[0006]
本发明目的是提供一种提高连铸扇形段轻压下开口度控制精度的控制方法,充分发挥动态轻压下工艺的作用,显著减轻连铸坯中心偏析,消除三角区附近内部裂纹,提高高强钢板坯的内部质量,有效地提高了铸机扇形段压不到位的精度,铸机扇形段位置扇形段压下正常,铸坯凝固末端动态轻压下扇形段开口度偏差在0.1mm以内;实现了扇形段压到位的有效控制,有效的保证了超高强钢产品品质,板坯偏析达到c0.5以上水平,因偏析造成的冲击功不合格率降低到0.1
‰
以下,有效地解决了背景技术中存在的上述问题。
[0007]
本发明的技术方案是:一种提高连铸扇形段轻压下开口度控制精度的控制方法,包含以下步骤:(1)改进扇形段夹紧缸检查更换周期,由原来的7天检查更换改为3天检查更换,避免因液压缸内泄压力不足造成扇形段不到位;(2)将扇形段液压系统压力由目前的155-175bar提高至180-205bar,压力波动范围控制在185bar-195bar之间,从而在动力层面实现扇形段压至目标位;(3)对铸机辊缝进行在线测量和标定,避免扇形段在线投用一段时间后出现偏差,保证辊缝控制精度在
±
0.1mm以内;(4)进行钢种组、浇注断面和对应拉速划分,制定扇形段压到位断面、钢种与拉速匹配表,根据不同钢种、不同断面调整拉速,保证铸坯凝固末端轻压下位置控制正常;(5)制定连拉炉数、直装热送与不同工艺路线匹配表,根据工艺路线和直装直送合同情
况,优化生产节奏,控制合适的温度,确保恒拉速生产,避免拉速变动造成扇形段轻压下位置变化加剧铸坯液芯末端枝晶偏析。
[0008]
所述步骤(3)中,具体步骤如下:
①
将扇形段活动侧调整至机械位置,用手持辊缝仪在辊两侧规定位置测量四个辊缝值;
②ꢀ
将测量的辊缝值输入控制扇形段开口度的四个油缸的位置传感器中,进行机械位置“0位”标定;
③
标定完成后将扇形段辊缝调整至230mm、235mm、240mm或245mm合理的符合实际生产的辊缝值,现场观察夹紧缸动作正常无卡阻,用手持辊缝仪在相同规定位置再次测量,实际测量值与传感器读数误差在
±
0.02mm内,标定完成;
④
实际测量值与液压缸位置传感器读数误差超过
±
0.02mm时,修改补偿值,再重复
①
~
③
步骤,直到辊缝调整到误差范围内。
[0009]
板坯厚度在230~250mm,凝固末端动态轻压下四个扇形段,总压下量在6~8mm,单个扇形段压下量1.5~2.0mm。
[0010]
本发明的有益效果是:充分发挥动态轻压下工艺的作用,显著减轻连铸坯中心偏析,消除三角区附近内部裂纹,提高高强钢板坯的内部质量,有效地提高了铸机扇形段压不到位的精度,铸机扇形段位置扇形段压下正常,铸坯凝固末端动态轻压下扇形段开口度偏差在0.1mm以内;实现了扇形段压到位的有效控制,有效的保证了超高强钢产品品质,板坯偏析达到c0.5以上水平,因偏析造成的冲击功不合格率降低到0.1
‰
以下。
具体实施方式
[0011]
为了使发明实施案例的目的、技术方案和优点更加清楚,下面将对本发明实施案例中的技术方案进行清晰的、完整的描述,显然,所表述的实施案例是本发明一小部分实施案例,而不是全部的实施案例,基于本发明中的实施案例,本领域普通技术人员在没有做出创造性劳动前提下所获得的所有其他实施案例,都属于本发明保护范围。
[0012]
一种提高连铸扇形段轻压下开口度控制精度的控制方法,包含以下步骤:(1)改进扇形段夹紧缸检查更换周期,由原来的7天检查更换改为3天检查更换,避免因液压缸内泄压力不足造成扇形段不到位;(2)将扇形段液压系统压力由目前的155-175bar提高至180-205bar,压力波动范围控制在185bar-195bar之间,从而在动力层面实现扇形段压至目标位;(3)对铸机辊缝进行在线测量和标定,避免扇形段在线投用一段时间后出现偏差,保证辊缝控制精度在
±
0.1mm以内;(4)进行钢种组、浇注断面和对应拉速划分,制定扇形段压到位断面、钢种与拉速匹配表,根据不同钢种、不同断面调整拉速,保证铸坯凝固末端轻压下位置控制正常;(5)制定连拉炉数、直装热送与不同工艺路线匹配表,根据工艺路线和直装直送合同情况,优化生产节奏,控制合适的温度,确保恒拉速生产,避免拉速变动造成扇形段轻压下位置变化加剧铸坯液芯末端枝晶偏析。
[0013]
所述步骤(3)中,具体步骤如下:
①
将扇形段活动侧调整至机械位置,用手持辊缝仪在辊两侧规定位置测量四个辊缝
值;
②ꢀ
将测量的辊缝值输入控制扇形段开口度的四个油缸的位置传感器中,进行机械位置“0位”标定;
③
标定完成后将扇形段辊缝调整至230mm、235mm、240mm或245mm合理的符合实际生产的辊缝值,现场观察夹紧缸动作正常无卡阻,用手持辊缝仪在相同规定位置再次测量,实际测量值与传感器读数误差在
±
0.02mm内,标定完成;
④
实际测量值与液压缸位置传感器读数误差超过
±
0.02mm时,修改补偿值,再重复
①
~
③
步骤,直到辊缝调整到误差范围内。
[0014]
板坯厚度在230~250mm,凝固末端动态轻压下四个扇形段,总压下量在6~8mm,单个扇形段压下量1.5~2.0mm。
[0015]
实施例1:生产高强大梁钢700l,断面在1700~2000mm,在对连铸过程扇形段控制情况进行统计分析,发现铸机扇形段夹紧缸存在内泄现象,液压系统压力偏低,拉速在0.9-1.0m/min,冷却比水量0.72l/kg,此时在连铸浇注过程出现连铸辊缝较目标值偏差大且辊缝值处于0~3mm之间波动状态,铸坯经低倍检测三角区附近存在中间裂纹,对应中心偏析加重。因此,为保证铸机扇形段压下控制精度在
±
0.1mm以内实现减轻中心偏析及消除三角区裂纹,制定连铸设备、工艺改进制度如表1所示,实施方案:
①
产前检查更换扇形段液压缸,系统压力调整为180-195bar;
②
在线测量并标定扇形段保证标定后测量误差在0.02mm以内;
③
制定断面-拉速对应方案,采取二冷弱冷方式;
④
全工序控制保证连铸中间包过热度在10~20℃。跟踪铸坯生产过程动态轻压下扇形段辊缝历史数据,辊缝控制精度在0~0.1mm。消除了上述三角区裂纹,减轻了中心偏析,效果良好。
[0016]
表1 连铸设备、工艺参数实施例2:生产高级管线钢x70,断面在1700~2000mm,为保证轻压下实施正常的设备保障条件,严格按照扇形段在线检查测量标定及调整液压系统压力,保证标定辊缝偏差在0.02mm以内,严控生产节奏,确保恒拉速浇注,避免拉速波动导致的轻压下位置移动引起压不到位问题。在对连铸过程扇形段控制情况进行统计分析,发现铸机扇形段夹紧缸存在内泄现象,液压系统压力偏低,拉速在0.9-1.0m/min,冷却比水量0.80l/kg,此时在连铸浇注过程出现连铸辊缝较目标值偏差大且辊缝值处于0~4mm之间波动状态,铸坯经低倍检测三角区附近存在中间裂纹,对应中心偏析c类1.5比例增大。因此,为减轻中心偏析及消除三角区裂纹,制定连铸设备、工艺改进制度如表2所示,具体为:
①
扇形段系统压力调整为190-205bar;
②
在线测量并标定扇形段保证标定后测量误差在0.02mm以内;
③
严格按照断面-拉速对应方案执行;
④
采取二冷弱冷为0.72 l/kg;
⑤
恒速浇注。跟踪铸坯生产过程动态轻压下扇形段辊缝历史数据,辊缝控制精度在0~0.1mm。消除了上述三角区裂纹,中心偏析c类
≤1.0比例大幅度提高,从60%提高至90%。
[0017]
表2 连铸设备、工艺参数。
起点商标作为专业知识产权交易平台,可以帮助大家解决很多问题,如果大家想要了解更多知产交易信息请点击 【在线咨询】或添加微信 【19522093243】与客服一对一沟通,为大家解决相关问题。
此文章来源于网络,如有侵权,请联系删除
相关标签:



tips