一种航空发动机封严环双向同步加载液压成形设备的制作方法



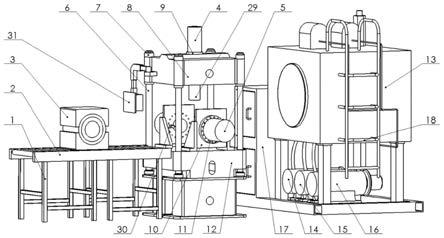
[0001]
本发明属于液压成形领域,涉及一种实现集载荷精确施加、伺服驱动/液压恒载复合控制、载荷/压力实时检测、成形误差智能补偿以及自动装模于一体的航空发动机封严环双向同步加载液压成形设备。
背景技术:
[0002]
金属封严环是一类具有新型密封形式和更好密封效果的轴向自紧式静密封结构,截面一般呈“w”、“m”或更复杂的多波纹形状。金属封严环有回弹性能好、吸振能力强、变形范围大及寿命长等优点,是航空发动机中高温、高压、振动及强腐蚀环境下进行密封泄漏的关键基础零件。
[0003]
液压成形是利用液体作为传力介质使工件贴靠模具的一种塑性加工技术。液压成形是一种先进的柔性成形方法,非常适合金属封严环的整体精确成形制造。目前我国已经基本实现了金属封严环的自主制造,但主要以人工操作设备成形为主,装夹调整、工件对中、型面成形等主要依靠工人技能保障,产品质量一致性和稳定性差。然而,国外在金属封严环生产过程中已普遍采用了全自动化、柔性化、智能化的数控装备,坯料在装载后根据程序设定自动加载完成制造过程,可以用于不同型号规格金属封严环的成形。此外,国外采用自动化成形工艺装备及相应的数字化工艺软件系统,对于0.1mm厚度的金属封严环,可以将整体环的高度方向误差控制在其高度的5%以内,圆度和平面度保持在直径的2%左右。
[0004]
因此,针对目前高温合金金属封严环的生产主要以手工操作数显设备成形为主,导致产品质量一致性与稳定性难保障的问题,研发航空发动机金属封严环专用工艺装备,采用自动化工艺装备保障金属封严环的产品质量一致性和稳定性,解决重点型号航空发动机研制中金属封严领域的“卡脖子”问题,全面提升专业化产品核心技术水平和能力,推动产品快速研制和可持续发展。
技术实现要素:
[0005]
为此,本发明提供了一种航空发动机封严环双向同步加载液压成形专用设备,集载荷精确施加、伺服驱动/液压恒载复合控制、载荷/压力实时检测、成形误差智能补偿以及自动装模等功能于一体,克服目前封严环构件成形设备自动化程度低,过度依赖手工操作影响质量稳定性的问题,保证产品质量一致性和稳定性。
[0006]
本发明提供了一种航空发动机封严环双向同步加载液压成形设备,包括自动装模系统、主机系统、超高压系统以及数控系统,所述数控系统基于上、下位机控制方式和工业以太网通信,采用全数字闭环控制,实时自动控制所述超高压系统;
[0007]
所述自动装模系统包括机架、滚筒输送机和成形模具,所述滚筒输送机固定在所述机架上,所述成形模具通过所述滚筒输送机行进到所述主机系统;
[0008]
所述主机系统包括锁模液压缸和同步进给的两个伺服液压缸,所述锁模液压缸配置成用于为所述成形模具提供锁模力以密封所述成形模具的成形腔,所述两个伺服液压缸
配置成用于双向同步加载所述成形模具,实现双向加载成形封严环;
[0009]
所述超高压系统包括液压附件、第一伺服电机、第二伺服电机和第三伺服电机,所述液压附件包括液压泵和增压缸,所述第一伺服电机驱动所述液压泵和所述增压缸为所述成形腔内提供超高胀形压力,所述第二伺服电机驱动所述锁模液压缸提供锁模力,所述第三伺服电机驱动两个伺服液压缸提供同步进给力。
[0010]
在一些实施例中,所述主机系统可以包括立柱、上安装座、称重传感器、连接座和下安装座;所述上安装座与所述下安装座分别与所述立柱的两端连接;所述锁模液压缸连接固定于所述上安装座上方;所述上安装座沿其高度方向设置有中心通孔;所述锁模液压缸的活塞杆穿过所述中心通孔向下运动,为所述成形模具提供锁模力;各伺服液压缸连接于所述连接座,所述连接座连接固定于所述下安装座上;所述两个伺服液压缸配置成位于行进到所述主机系统的成形模具的对称两侧并且对中所述成形模具。
[0011]
在一些实施例中,所述主机系统可以包括称重传感器,所述称重传感器可以安装于所述锁模液压缸的活塞杆中并随活塞杆运动,以用于实时测量锁模力。
[0012]
在一些实施例中,所述液压附件可以包括比例溢流阀、换向阀、压力传感器、单向阀、液控单向阀和单向顺序阀;所述比例溢流阀用于调节所述成形模具的成形腔内的胀形压力;所述换向阀用于控制液压油路的接通、关断和方向,从而控制所述增压缸的低压、高压和退回等;所述压力传感器用于实时测量所述成形模具的成形腔内的胀形压力;所述单向阀用于控制液压油单向通过;所述液控单向阀用于控制所述增压缸退回时液压油的双向通过;所述单向顺序阀用于所述增压缸退回时的保压回油。
[0013]
在一些实施例中,所述超高压系统可以采用分区控制技术来控制所述成形模具的成形腔内的胀形压力,当成形封严环所需胀形压力低于30mpa,利用所述液压泵直接提供胀形压力;当成形封严环所需胀形压力高于30mpa,通过所述增压缸进行增压,达到所需胀形压力。
[0014]
在一些实施例中,所述增压缸的增压比可以为3.3,所述第一伺服电机驱动所述液压泵和所述增压缸为所述成形腔内提供最大100mpa的超高压胀形压力。
[0015]
在一些实施例中,所述数控系统可以包括触摸屏、工控机和plc系统,通过所述触摸屏将工作参数和成形曲线输入所述工控机,并向所述plc系统输入控制参数;所述plc系统用于采集各传感器的检测数据,并且控制第一伺服电机、第二伺服电机和第三伺服电机的启动和停止。
[0016]
在一些实施例中,所述触摸屏可通过l型臂旋转收放地挂于所述主机系统外侧;第一伺服电机、第二伺服电机和第三伺服电机位于所述超高压系统的下部。
[0017]
在一些实施例中,所述两个伺服液压缸的进给位移可以通过光栅位移传感器测量,并通过所述光栅位移传感器将测量数据传输至所述数控系统。
[0018]
在一些实施例中,所述两个伺服液压缸的双向加载同步控制精度可以达到
±
0.02mm,以保证封严环异型截面的成形精度。
[0019]
本发明的有益效果:
[0020]
1)本发明可实现自动、半自动及手动三种控制方式,保证封严环产品质量一致性与稳定性;
[0021]
2)本发明的主机系统使用两个双向同步加载的伺服进给缸,通过两个光栅位移传
感器监测两伺服缸的位移,利用比例位移同步控制技术,结合pid控制算法与串并联混合反馈信号,分别采用独立的液压控制两伺服缸的进给位移,实现两伺服缸的同步进给,位移同步控制精度达到
±
0.02mm。
[0022]
3)本发明采用伺服驱动/液压恒载混合控制,将液压胀形与双向同步加载相结合,锁模液压缸为成形模具提供锁模力,保证成形时成形模具成形腔密封,两伺服进给缸双向同步加载的同时,超高压系统利用液压泵和增压缸,按一定加载路径向模具成形腔内提供胀形压力,满足不同零件的不同工艺要求,实现双向加载柔性成形;
[0023]
4)本发明的超高压系统利用胀形压力分区控制技术,控制精度高,当所需胀形压力小于30mpa时,直接由液压泵提供,当胀形压力大于30mpa时,通过增压缸(增压比3.3)进行增压,并通过压力传感器实时测量胀形压力,利用比例溢流阀精确调节胀形压力;
[0024]
5)本发明的数控系统采用工业以太网通信,数据传输速度快,抗干扰能力强,可实现远程监控;
[0025]
6)本发明的数控系统采用上、下位机控制方式,采用全数字闭环控制实时显示并调节锁模力、进给位移及胀形压力;可实时采集生产数据并输出各种工作曲线和工作状态,保存数据并建立数据库,再次使用时导入历史设置和过程数据,实现工艺过程的再现与重用。
附图说明
[0026]
图1为本发明航空发动机封严环液压成形设备的结构示意图;
[0027]
图2为本发明的自动装模系统结构示意图;
[0028]
图3为本发明的主机系统结构示意图;
[0029]
图4为本发明的超高压系统结构示意图;
[0030]
图5为本发明的伺服驱动/液压恒载控制原理示意图;
[0031]
图6为本发明的胀形压力分区控制原理示意图;
[0032]
图7为本发明的数控系统闭环控制原理示意图;
[0033]
图8为本发明的两伺服缸比例位移同步控制原理示意图;
[0034]
图9为本发明的工作流程示意图。
[0035]
附图中:
[0036]
1-机架;2-滚筒输送机;3-成形模具;4-锁模液压缸;5-伺服液压缸;6-立柱;7-立柱螺母;8-上安装座;9-锁模缸法兰;10-连接座;11-伺服缸法兰;12-下安装座;13-液压附件;14-第一伺服电机;15-第二伺服电机;16-第三伺服电机;17-控制柜;18-扶梯;19-液压泵;20-增压缸;21-比例溢流阀;22-三位四通换向阀;23-二位四通换向阀;24-二位二通换向阀;25-压力传感器;26-单向阀;27-液控单向阀;28-单向顺序阀;29-称重传感器;30-光栅位移传感器;31-触摸屏;32-零件。
具体实施方式
[0037]
为了能够更清楚地理解本发明的上述目的、特征和优点,下面结合附图和具体实施例对本发明进行进一步的详细描述。需要说明的是,在不冲突的情况下,本发明的实施例及实施例中的特征可以相互组合。
[0038]
在下面的描述中阐述了很多具体细节以便于充分理解本发明,但是,本发明还可以采用其他不同于在此描述的其他方式来实施,因此,本发明的保护范围并不受下面公开的具体实施例的限制。
[0039]
本实施例提供了一种航空发动机封严环双向同步加载液压成形专用设备,包括自动装模系统、主机系统、超高压系统和数控系统四部分,如图1所示,下面将结合附图对各部分做进一步详细说明。
[0040]
本实施例的自动装模系统包括机架1、滚筒输送机2和成形模具3,如图2所示,机架1由切割的特定长度的铝合金型材按桁架结焊接构成,滚筒输送机2固定在机架1上,成形模具3通过滚筒输送机2上进行传送。
[0041]
本发明的主机系统采用两个同步进给的伺服液压缸及一个锁模液压缸,配合模具成形腔内的液压胀形,满足双向同步加载液压成形的工艺需求。如图3所示,本实施例的主机系统包括锁模液压缸4、两个伺服液压缸5、立柱6、立柱螺母7、上安装座8、锁模缸法兰9、连接座10、伺服缸法兰11和下安装座12。其中,上安装座8与下安装座12通过四根立柱6相连并用立柱螺母7固定,立柱6、上安装座8和下安装座12共同组成刚性封闭框架。锁模液压缸4配合锁模缸法兰9通过螺纹连接固定于上安装座8上方,上安装座8沿其高度方向设置有中心通孔,锁模液压缸4的活塞杆能够穿过该中心通孔向下运动,以便为行进到主机系统的成形模具3提供锁模力。特别地,锁模液压缸4最大可提供400kn锁模力,以保证成形过程中高压状态下成形模具3的成形腔密封。两个伺服液压缸5配合伺服缸法兰11通过螺纹连接于各自的连接座10,两个连接座10通过螺纹连接对称固定于下安装座12的两侧,承受来自锁模液压缸4的合模力、伺服液压缸5的轴向进给力等工作载荷。特别地,两个伺服液压缸5位于成形模具3的对称两侧并且对中成形模具3。
[0042]
本实施例的超高压系统包括液压附件13、第一伺服电机14、第二伺服电机15、第三伺服电机16、控制柜17和扶梯18,如图4所示。其中,扶梯18焊接于超高压系统外侧,以便操作人员可手动调节超高压系统。优选地,如在本实施例中,第一伺服电机14、第二伺服电机15和第三伺服电机16三个伺服电机位于超高压系统下部,第一伺服电机14可驱动液压附件13为成形腔内提供最高100mpa的胀形压力,第二伺服电机15驱动锁模液压缸4提供锁模力,第三伺服电机16驱动两个伺服液压缸5提供同步进给力。
[0043]
如图5和图6所示,本实施例中的液压附件13包括液压泵19、增压缸20、比例溢流阀21、三位四通换向阀22、二位四通换向阀23、二位二通换向阀24、压力传感器25、单向阀26、液控单向阀27和单向顺序阀28。其中,液压泵19用于供油;增压缸20的增压比优选为3.3,保证最大胀形压力达100mpa;比例溢流阀21用于实时调节成形腔内的胀形压力;压力传感器25用于实时测量成形腔内的胀形压力;单向阀26用于控制液压油单向通过;液控单向阀27控制增压缸20退回时液压油的双向通过;单向顺序阀28用于增压缸20退回时的保压回油。
[0044]
特别地,本发明在通过比例位移同步控制技术,驱动两伺服液压缸5同步加载的同时,可以利用数控系统控制超高压系统,利用液压泵19、增压缸20和比例溢流阀21,按一定加载路径向模具成形腔内提供不同胀形压力,满足不同类型封严环零件的成形需求,将成形腔内液压胀形与两伺服缸双向加载相结合,实现双向加载柔性成形。
[0045]
具体地,首先如图5所示,超高压系统通过液压泵19调节锁模液压缸4和两伺服液压缸5的压力,分别为成形模具3提供所需锁模力和进给力,同时采用称重传感器29测量锁
模力大小,保证成形过程中成形模具3成形腔的密封。优选地,称重传感器29通过螺栓安装在锁模液压缸4的活塞杆中随活塞杆向下运动(见图9中所示),以便实时测量锁模液压缸4的锁模力。两个伺服液压缸5采用两个独立的液压泵进行控制,驱动成形模具3同步轴向进给,其轴向位移均通过光栅位移传感器30测量(见图3中所示),并通过光栅位移传感器30将数据传输至数控系统用于闭环控制。成形模具3成形腔内的压力通过增压缸20进行调节,采用压力传感器25来实时测量胀形压力并传输给数控系统,换向阀22和23可控制油路的通断,从而控制增压缸20的上行、下行和退回,提供不同成形阶段零件所需不同胀形压力,配合两伺服液压缸5的同步轴向进给实现伺服驱动/液压恒载控制。换向阀24用于收集模具成形腔中的液压油重复利用,或向模具型腔进行补油。其次,特别地,本发明的超高压系统利用胀形压力分区控制技术来控制成形模具3内的胀形压力,以满足不同厚度零件的成形需要。如图6所示,当成形零件需要的胀形压力在30mpa以下时,三位四通换向阀22右位接入油路,二位四通换向阀23不通,二位二通换向阀24接通,液控单向阀27仅能单向流通,由液压泵19直接为液室供油,液压油流经单向阀26、三位四通换向阀22、液控单向阀27、比例溢流阀21和二位二通换向阀24到达成形模具3的成形腔中,流至增压缸20上腔,用压力传感器25实时测量胀形压力,并通过比例溢流阀21调节到所需的压力;当成形零件需要流体压力在30mpa以上时,三位四通换向阀22右位接入油路,二位四通换向阀23接通,二位二通换向阀24接通,液控单向阀27可双向流通,液压泵19供油,液压油流经单向阀26、三位四通换向阀22、液控单向阀27、二位四通换向阀23到达增压缸20下腔,通过增压缸20增压,增压缸20上腔液压油流入成形模具3的成形腔内形成高压,经二位二通换向阀24流出,通过压力传感器25测量胀形压力,并通过比例溢流阀21调节压力,达到所需的成形压力;当成形结束后,增压缸20需退回,三位四通换向阀22左位接入油路,二位四通换向阀23接通,二位二通换向阀24接通,液压油流经单向阀26、三位四通换向阀22、单向顺序阀28进入到增压缸20中腔,增压缸20下腔中液压油通过二位四通换向阀23和液控单向阀27流回。特别地,成形过程中成形模具3的成形腔的胀形压力可随两伺服液压缸5的进给位移连续可调,能够满足高温合金材料的成形要求。
[0046]
本发明的数控系统采用上、下位机控制方式以及闭环控制,如图7所示,上位机系统主要包括触摸屏31和工控机,负责监控成形设备的实时状态,通过触摸屏31将工作参数和成形曲线输入到工控机中,并向下位机系统写入控制参数。下位机系统主要包括plc系统,plc系统能够采集称重传感器29、压力传感器25和光栅位移传感器30的数据,控制3个伺服电机的启动和停止。如图7所示,通信模块将控制参数输入数字量输入模块,实现开关量的设置和控制,高速计数器模块可以读取光栅位移传感器30的数据,压力传感器25和称重传感器29测量所得的实际工作参数可通过模拟量输入模块输入,通过模拟量输出模块输出控制值,调节相应的比例溢流阀,实现闭环控制。特别地,本实施例中的数控系统采用工业以太网通信,其抗干扰能力强,具备数据库和工艺参数分析等智能功能。此外,触摸屏31可以通过l型臂可旋转收放地挂于主机系统外侧(如图1所示),以便能够显示实验数据并输入控制参数,完成对整个成形设备的控制。
[0047]
特别地,本发明的两个伺服液压缸5采用比例位移同步控制技术,结合pid控制算法和串并联混合反馈信号,通过两个电液比例阀进行液压调节控制。如图8所示,首先采用并联控制,两个伺服液压缸5分别采用独立液压动力源,将相同的位移信号分别输入给pid
控制器1和pid控制器2,控制左右两个电液比例阀调节液压缸中液压油的流量和流速来控制位移,光栅位移传感器30将测量的位移信号作为输出与位移给定信号做差值;同时采用串联控制,将两伺服液压缸的位移输出做差值,差值由pid控制器3进行运算后输入到左伺服缸作为输出信号,与pid控制器2的输入信号做差值后给到左电液比例阀,实现串并联混合控制,有利地,同步控制精度可以达到
±
0.02mm。
[0048]
下面通过本发明具体的成形方法和工作流程来进一步说明本发明,结合图9所示,具体过程如下:
[0049]
第一步,在自动装模系统上完成换模与自动送模,利用滚筒输送机2将成形模具3传送到主机系统的平台上,在成形之前主机为未启动状态,安装模具后,两伺服缸5轴向对准成形模具3的两侧,锁模液压缸4位于上部,如图9(a)所示;
[0050]
第二步,通过触摸屏31显示并设置所需的工作参数和成形曲线,数控系统通过工业以太网实时控制主机系统和超高压系统,设置自动运行,自动检查锁模液压缸4的锁模力、两伺服液压缸5的位移、增压缸20的活塞位置以及各工艺参数是否无误。若各设置均正确,系统将执行自动运行命令,通过液压泵控制锁模液压缸4下行接触成形模具3并增大锁模力到设定值,通过称重传感器29实时测量锁模力大小反馈至数控系统,并实时显示在触摸屏31上;通过液压泵控制两伺服液压缸5同步进给贴合成形模具3,并通过液压泵19为成形模具3成形腔充液,控制换向阀22右行和换向阀24上行来控制增压缸下行,此时换向阀23不通,通过压力传感器25实时测量成形模具3成形腔内胀形压力大小,反馈至数控系统后显示在触摸屏31上,按照设定的加载路径,通过比例溢流阀21调节模具成形腔内的胀形压力大小,如图9(b)所示,在不断增大胀形压力到设定值的同时,控制两伺服液压缸5同步进给,通过光栅位移传感器30实时测量两伺服液压缸5的位移,通过数控系统的同步控制算法实现同步精度达
±
0.02mm;当达到设定的位移值后,停止两伺服液压缸5的进给并保持,如图9(c)所示,保持换向阀22右行和换向阀24上行,控制换向阀23右行,从而控制增压缸20增压,成形腔对成形零件进行保压整形;当整形时间到达后,保持换向阀23右行和换向阀24上行,控制换向阀22换向,增压缸20退回泄压后,控制两伺服液压缸5和锁模液压缸4相继卸压,并完成零件32脱模,如图9(d)所示。
[0051]
第三步,在整个成形过程中,通过数控系统的上位机系统和下位机系统,实时监控并自动记录成形过程中锁模液压缸4的锁模力、两伺服液压缸5位移以及成形模具3成形腔内胀形压力(即增压缸20内压力)的变化曲线及各数据点,并通过触摸屏31输出各工作曲线和工作状态,自动生成完整的生产报表,保存数据并建立数据库,再次使用时可导入历史设置和过程数据,实现工艺过程的再现与重用。
[0052]
对于本领域的普通技术人员来说,在不脱离本发明创造构思的前提下,还可以对本发明的实施例作出若干变型和改进,这些都属于本发明的保护范围。
起点商标作为专业知识产权交易平台,可以帮助大家解决很多问题,如果大家想要了解更多知产交易信息请点击 【在线咨询】或添加微信 【19522093243】与客服一对一沟通,为大家解决相关问题。
此文章来源于网络,如有侵权,请联系删除



tips