石油钻机循环系统用钻井泵空气包外壳胎模锻造方法与流程



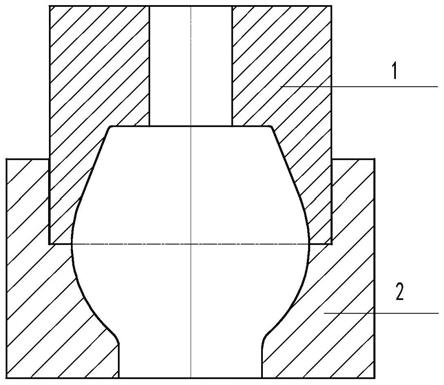
[0001]
本发明属于石油钻机设备制造技术领域,涉及石油钻机循环系统用钻井泵空气包外壳胎模锻造方法。
背景技术:
[0002]
在钻井泵的使用过程中,由于钻井泵缸内流液不连续或液流与活塞运动不同步,引起液体与活塞端面互相撞击而形成水击现象(俗称水锤),造成压力波动,钻井泵出现异常噪声,严重时造成钻井泵管路破裂的后果。空气包是钻井泵的重要组成零件,其外壳是一个中空的球形零件,在钻井泵工作过程中有稳定压力,减小波动,增加水马力,减少井漏等重要作用,因此在钻井生产中,维护空气包的正常工作非常重要。
[0003]
由于空气包外壳为内部中空的球形特殊结构,目前多采用铸造成形或锻造-焊接成形。铸件产品往往在加工过程中发现气孔、夹砂、裂纹等铸造缺陷而报废,使产品成本增高,质量无法保证。锻造-焊接成形材料利用率较高,但设备投入大,深v型焊缝质量有时难以保证。
技术实现要素:
[0004]
本发明的目的是提供一种石油钻机循环系统用钻井泵空气包外壳胎模锻造方法,解决了现有技术中铸造成形的空气包外壳存在气孔、夹砂、裂纹等铸造缺陷的问题。
[0005]
本发明所采用的技术方案是,石油钻井循环系统用钻井泵空气包外壳的胎模锻锻造方法,包括以下步骤:
[0006]
步骤1、根据锻件形状及尺寸设计胎模锻模具的上模和下模;
[0007]
步骤2、加热坯料到始锻温度,经墩粗、冲盲孔、芯轴拔长、锯切工序,制得盲孔长套形坯料;
[0008]
步骤3、将步骤2所得盲孔长套形坯料置于步骤1所得上模和下模内焖形,锻件脱模后空冷,正火处理即得到空气包外壳。
[0009]
步骤1中,上模底部为圆台型内腔,顶部带有圆形通孔与圆台型内腔连通;圆台型内腔和锻件的上半部分尺寸一致;下模底部为球型内腔,顶部带有安装导向套的环形槽;球型内腔和锻件的下半部分尺寸一致;所述胎模锻模具还带有垫圈,垫圈外径尺寸与下模相同,内径尺寸大于上模的外径。
[0010]
步骤2中盲孔长套形坯料4的外径为400mm,内径为190mm,小端台阶直径为330mm,总长度为900mm,内孔深度为750mm,壁厚为105mm。
[0011]
步骤2中的始锻温度为1180-1200℃,保温时长为1.5h。
[0012]
步骤3具体包括以下步骤:
[0013]
步骤3.1、预热步骤1所得到的上模和下模;
[0014]
步骤3.2、将盲孔长套形坯料加热到始锻温度保温后,轻镦去掉表面的氧化皮;
[0015]
步骤3.3、将盲孔长套形坯料放入下模内自由墩粗到高度700mm;
[0016]
步骤3.4、将盲孔长套形坯料加上模继续镦粗,焖型得到锻件;
[0017]
步骤3.5、焖型完成后,操作机夹持下模翻转180
°
置垫圈上,下压后锻件从上模内自动脱模;
[0018]
步骤3.6、锻件出模后空冷,接着装入860℃的炉内保温2小时,出炉空冷到室温;
[0019]
步骤3.1中上模和下模的预热温度为200-300℃。
[0020]
本发明的有益效果是:
[0021]
可以整体锻出空气包外壳,锻造过程中上下胎模限制金属流向,锻件外形接近零件;锻件制坯结构简单,锻件内孔胀型形成自然的圆弧形中空;锻件加工余量少,节约原材料,提高加工效率;锻件脱模容易,操作简单可靠;锻件内部金属流线按零件形状分布,后续机加工不被切断,机械性能更好。
附图说明
[0022]
图1是本发明石油钻机循环系统用钻井泵空气包外壳胎模锻造方法中的模具图;
[0023]
图2是本发明石油钻机循环系统用钻井泵空气包外壳胎模锻造方法中的上模剖视图;
[0024]
图3是本发明石油钻机循环系统用钻井泵空气包外壳胎模锻造方法中的下模剖视图;
[0025]
图4是本发明石油钻机循环系统用钻井泵空气包外壳胎模锻造方法中的垫圈剖视图;
[0026]
图5是本发明石油钻机循环系统用钻井泵空气包外壳胎模锻造方法中的盲孔长套坯料剖视图;
[0027]
图6是本发明石油钻机循环系统用钻井泵空气包外壳胎模锻造方法中所得锻件的剖视图;
[0028]
图7是本发明石油钻机循环系统用钻井泵空气包外壳胎模锻造方法中的拔长芯轴图;
[0029]
图8是本发明石油钻井循环系统用钻井泵空气包外壳的胎模锻锻造方法中的胎模锻锻造流程图;
[0030]
图中,1.上模,2.下模,3.垫圈,4.盲孔长套形坯料,5.锻件,6.拔长芯轴。
具体实施方式
[0031]
下面结合附图和具体实施方式对本发明进行详细说明。
[0032]
如图1-4所示,石油钻井循环系统用钻井泵空气包外壳的胎模锻锻造方法,包括以下步骤:
[0033]
步骤1、根据锻件5形状及尺寸设计胎模锻模具的上模1和下模2;
[0034]
步骤2、加热坯料到始锻温度,经墩粗、冲盲孔、芯轴拔长、锯切工序,制得盲孔长套形坯料4;制坯过程中盲孔长套形坯料4经墩粗,芯轴拔长的大变形过程,可有效锻合原材料中疏松、空洞等冶金缺陷,提高锻件质量。
[0035]
步骤3、将步骤2所得盲孔长套形坯料4置于步骤1所得上模1和下模2内焖形,锻件5脱模后空冷,正火处理即得到空气包外壳。
[0036]
步骤1中,上模1底部为圆台型内腔,顶部带有圆形通孔与圆台型内腔连通;圆台型内腔和锻件5的上半部分尺寸一致;下模2底部为球型内腔,顶部带有安装导向套的环形槽,锻造过程中导向套对上模1起导向作用,使上模1和下模2的中心线重合,防止盲孔长套形坯料4在镦粗过程发生倾斜;球型内腔和锻件5的下半部分尺寸一致;所述胎模锻模具还带有垫圈3,垫圈3外径尺寸与下模2相同,内径尺寸大于上模1的外径,使锻件5顺利从下模2内脱模。
[0037]
如图5,步骤2中盲孔长套形坯料4的外径为400mm,内径为190mm,小端台阶直径为330mm,总长度为900mm,内孔深度为750mm,壁厚为105mm。
[0038]
步骤2中的始锻温度为1180-1200℃,保温时长为1.5h。
[0039]
如图8所示,步骤3具体包括以下步骤:
[0040]
步骤3.1、预热步骤1所得到的上模1和下模2;
[0041]
步骤3.2、将步骤2所得的盲孔长套形坯料4加热到始锻温度保温后,轻镦去掉表面的氧化皮;
[0042]
步骤3.3、将盲孔长套形坯料4放入下模2内由加压机自由墩粗到高度700mm;
[0043]
步骤3.4、将盲孔长套形坯料4加上模1,上模1的下部导入下模2的导向套内,使上模1、下模2和坯料的中心线重合,压机在上模1上加压墩粗,焖型得到锻件5;
[0044]
步骤3.5、焖型完成后,操作机夹持下模2翻转180
°
置垫圈3上,下压后锻件5从上模1内自动脱模;
[0045]
步骤3.6、锻件5出模后空冷,接着装入860℃的炉内保温2小时(正火处理),出炉空冷到室温;
[0046]
步骤3.1中上模1和下模2的预热温度为200-300℃。
[0047]
本方法可以仿型锻造出接近零件的锻件5,有效减少锻件5加工余量,保留完整的金属随形流线,提高锻件5机械性能,延长使用寿命。
[0048]
本发明还具有以下优点:
[0049]
1.胎模结构简单,易于制造,设备工装投入小,锻造过程短,操作简便易行,锻件外形接近零件,加工余量少,减少材料浪费,提高生产效率。
[0050]
2.制坯过程中经过镦粗、冲孔和芯轴拔长等工步,锻造变形量大,能有效消除材料内部冶金缺陷,锻件质量好,使用寿命长。
[0051]
3.盲孔长套形坯料形状简单,胎模内镦粗时,利用盲孔长套形坯料的结构特点,内外自然胀型,外部由模具限制形成锻件外形,内孔形成锻件的中空内腔,所需锻造压力小,节约能源,易于成形。
[0052]
4.锻件在胎模内成形,表面质量好,锻件内部形成的金属流线符合锻件形状,机加工时不切断金属流线,锻件机械性能高。
[0053]
以kbd-45空气包为例,空气包外壳材料为35crmo:
[0054]
1.编制工艺。根据零件图制定锻件图,设计胎模锻模具,计算锻件重量,下料重量,下料规格,确定锻造始锻、终锻温度,锻造火次,锻造变形过程,锻造设备,锻件出模及锻后冷却方式等工艺参数,编制锻造工艺。
[0055]
2.下料。根据锻件形状尺寸,计算锻件重量为698kg,经过制坯和终锻2次完成锻造,考虑盲孔长套形坯料5的切头余料和火耗,计算下料重量为733kg,下料尺寸为φ400
×
739。
[0056]
3.加热。按照加热规范将下料加热到1180-1200℃的始锻温度,保温1.5小时。
[0057]
4.坯料自由镦粗。将坯料沿竖直方向自由镦粗到约550mm高。
[0058]
5.冲盲孔。在坯料中心冲盲孔。
[0059]
6.芯轴拔长。将步骤5所得坯料穿在拔长芯轴6上拔长并压小头台阶。拔长过程中要按芯轴拔长的操作要点进行,不断旋转芯轴,防止芯轴咬死,严格控制小头台阶长度,防止镦粗时产生折叠。
[0060]
7、将步骤6所得坯料在锯床上锯掉两头余料,使端面平齐,得到盲孔长套形坯料4。
[0061]
8.模具内自由墩粗。将盲孔长套形坯料4重新加热后直立轻镦,去掉表面氧化皮,置于下模2内,压机自由镦粗到700mm高。
[0062]
9.模具内焖型。将步骤8所得坯料套上上模1,模具内镦粗焖型。
[0063]
10.脱模。操作机加持下模2翻转置于垫圈3上,加圆钢顶出,锻件5从上模1的圆台型型腔中自动脱模。
[0064]
11.锻后冷却。锻件出模后空冷,正火处理。
起点商标作为专业知识产权交易平台,可以帮助大家解决很多问题,如果大家想要了解更多知产交易信息请点击 【在线咨询】或添加微信 【19522093243】与客服一对一沟通,为大家解决相关问题。
此文章来源于网络,如有侵权,请联系删除



tips