弯管自动化产线的制作方法



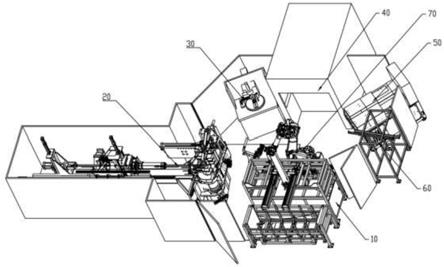
[0001]
本实用新型涉及弯管自动化产线,属于自动化设备的技术领域。
背景技术:
[0002]
弯管是采用成套弯曲设备进行弯曲的,分为冷煨与热推两种工艺。无论是哪一种机器设备及管道,大部分都用到弯管,主要用以输油、输气、输液,工程桥梁建设等。
[0003]
目前冷煨弯管存在多道成型工艺,包括弯管内部涂油、弯管成型、端部切割、弯管整形、端部缩口等,传统弯管制作中,大多采用人工,即通过人工进行工件周转在各成型设备中进行成型作业。作业强度较大,人力成本较高,生产效率较低。
[0004]
当前存在针对弯管成型的自动化产线设计,即通过多轴机械臂进行平直圆管工件在各设备之间的周转,从而满足自动化成型需求,降低了人力成本,提高了作业效率。
[0005]
但是,传统自动化产线存在较多缺陷:其一、需要通过至少两组机械臂进行周转,即其中一个机械臂用于平直圆管供料与弯管成型之间运转,另一个机械臂用于夹持弯折管在切割、整形、缩口、卸料之间运转;其二、平直圆管是堆叠在料舱中的,平直圆管之间堆叠贴靠,机械臂的机械爪很难实现单根平直圆管的抓取,即需要通过人工进行单根平直圆管分离的作业,作业强度依然很大,不利于自动化生产需求。其三、平直圆管上存在轴向线性焊缝,而弯折时对焊缝朝向存在特定需求,因此在机械爪抓取前还需要进行人工焊缝对位,对位精度直接影响到产品合格率。其四、机械臂采用针对平直圆管的双爪设计,在对弯管运转过程中容易产生偏转影响产品精度,而增加抓持力克服旋转扭力又存在夹持形变的情况。
技术实现要素:
[0006]
本实用新型的目的是解决上述现有技术的不足,针对传统自动化产生存在诸多缺陷的问题,提出弯管自动化产线。
[0007]
为了达到上述目的,本实用新型所采用的技术方案为:
[0008]
弯管自动化产线,包括呈环状依次分布的平直圆管供料装置、弯管设备、切割设备、弯管整形设备、管端缩口设备、及卸料架,环状空间内设有用于从所述弯管设备上夹持弯管在切割设备、弯管整形设备、管端缩口设备、及卸料架之间进行弯管周转的运转机构,
[0009]
其中,所述平直圆管供料装置包括单管输送机构、焊缝调节机构、及用于将所述焊缝调节机构上经过焊缝位置调节后平直圆管推送至弯管设备内的推送机构,
[0010]
在所述弯管设备内成型后的弯管具备直角部,所述运转机构包括机械臂和设置在所述机械臂驱动端上的机械夹爪,所述机械夹爪包括夹持通道轴线互呈直角的两个料爪部。
[0011]
优选地,所述单管输送机构包括平直圆管储料架、整列物料架及在所述平直圆管储料架顶部与所述整列物料架顶部之间切换位移取放料的物料运转部,所述整列物料架的出料端设有承料部。
[0012]
优选地,所述整列物料架包括倾斜整列导向底板、设置于所述倾斜整列导向底板顶部的用于释放或阻停平直圆管的放料机构,所述承料部设置于所述倾斜整列导向底板的出料端底部,所述承料部包括若干相间隔设置的承料桩,所述承料桩之间形成间隔空间。
[0013]
优选地,所述物料运转部包括具备在所述平直圆管储料架顶部与所述整列物料架顶部之间切换位移的电磁吸附座,所述电磁吸附座具备升降拾料位移。
[0014]
优选地,所述焊缝调节机构包括基架主体,所述基架主体上设有平直圆管支撑部、旋转驱动部、用于将单管输送机构上平直圆管运转至所述平直圆管支撑部上的运转部、及用于将平直圆管压贴在所述旋转驱动部上的压贴部,所述压贴部上设有用于检测焊缝的视觉传感器,所述视觉传感器与所述旋转驱动部相通讯连接。
[0015]
优选地,所述平直圆管支撑部包括沿平直圆管轴向间隔分布的若干支撑桩,圆管在所述支撑桩上具备自由旋转位移,所述旋转驱动部设置于相邻所述支撑桩之间,
[0016]
所述压贴部设置于所述旋转驱动部的顶部与所述旋转驱动部垂直向相对,所述压贴部包括用于压接在圆管上的随动滚轮组。
[0017]
优选地,所述推送机构包括设置在所述基架主体上的线性轨道、设置于所述线性轨道上的推送滑座,所述推送滑座上设有用于与平直圆管的轴端相抵接的推送部,所述支撑桩的顶部设有输送导向轮。
[0018]
优选地,所述基架主体的出料端设有具备枢轴位移的喷油嘴机构,所述喷油嘴机构具备喷嘴与平直圆管轴向相对的喷油对接位移、及用于送料避让的避让位移。
[0019]
优选地,所述机械夹爪的两个料爪部分别具备开合驱动源,所述机械夹爪上设有同步控制两个所述开合驱动源的联动控制机构,
[0020]
所述联动控制机构包括联动伸缩驱动源,所述联动伸缩驱动源的伸缩端具备两个枢轴配接的水平推杆部,任意所述开合驱动源具备触发开关座,所述水平推杆部与所述触发开关座一一对应配合设置,两个所述水平推杆部相同步运动且水平向位移方向相反。
[0021]
优选地,所述切割设备为伺服双刀切管机。
[0022]
本实用新型的有益效果主要体现在:
[0023]
1.环状分布的自动化产线布局合理,全程自动化作业,各工位之间配合流程高效,且降低了布置空间需求。
[0024]
2.供料及弯管之间为直供设计,满足供料弯管作业与后道切换工位加工作业之间的潮汐交替需求,加工效率得到显著提升。
[0025]
3.平直圆管供料装置集物料运转、物料整列、焊缝调节、端口涂油、及推送料功能于一体,设计非常巧妙,减少了配合作业时间,运行高效流畅。
[0026]
4.特定地机械夹爪设计满足对成型弯管的稳定抓持需求,提高了弯管加工精度,产品合格率得到较大提升。
附图说明
[0027]
图1是本实用新型弯管自动化产线的整体结构示意图。
[0028]
图2是本实用新型中平直圆管供料装置的结构示意图。
[0029]
图3是本实用新型中平直圆管供料装置的主视结构示意图。
[0030]
图4是本实用新型中单管输送机构的结构示意图。
[0031]
图5是本实用新型中焊缝调节机构的结构示意图。
[0032]
图6是本实用新型中机械夹爪的结构示意图。
具体实施方式
[0033]
本实用新型提供弯管自动化产线。以下结合附图对本实用新型技术方案进行详细描述,以使其更易于理解和掌握。
[0034]
弯管自动化产线,如图1所示,包括呈环状依次分布的平直圆管供料装置10、弯管设备20、切割设备30、弯管整形设备40、管端缩口设备50、及卸料架60,环状空间内设有用于从弯管设备20上夹持弯管在切割设备30、弯管整形设备40、管端缩口设备50、及卸料架60之间进行弯管周转的运转机构70。
[0035]
其中,如图2和图3所示,平直圆管供料装置10包括单管输送机构1、焊缝调节机构2、及用于将焊缝调节机构2上经过焊缝位置调节后圆管推送至弯管设备的推送机构3。
[0036]
在弯管设备20内成型后的弯管具备直角部,运转机构70包括机械臂和设置在机械臂驱动端上的机械夹爪4,机械夹爪4包括夹持通道轴线互呈直角的两个料爪部41。
[0037]
具体地实现过程及原理说明:
[0038]
采用围绕运转机构70的环状产线布置,易于实现弯管的物料周转。
[0039]
具体实现过程中,首先将管料装载在平直圆管供料装置10内,单管输送机构1将单管输送至焊缝调节机构2中,焊缝调节机构2对单管的焊缝朝向进行调节后,再由推送机构3推送至弯管设备20中进行弯管作业。
[0040]
弯管加工后,由运转机构70进行直角部的抓取,即通过两个料爪部41分别抓持直角部的两个管端,如此设计,运行可靠稳定。
[0041]
运转机构70抓持固定弯管后,依次经过切割设备30、弯管整形设备40、管端缩口设备50后,最终将成品在卸料架60上进行卸料。
[0042]
切割设备30即用于切割管端,弯管整形设备40用于对弯管的两个外沿端进行压接整形,提高产品形体精度,管端缩口设备50用于对弯管的两个自由端端口进行缩口作业。
[0043]
需要说明的是,本案的切割设备30为伺服双刀切管机,即端口切割后平整,无需修毛边工位。如此布局更合理。
[0044]
而传统弯管成型是通过多个运转机构70进行多轴抓取切换工位,本案中采用了推送机构3与弯管设备20的相对设置,即推送机构3能将焊缝调节后的圆管直接推送至弯管设备20的弯管轨道内,无需采用机械抓进行物料周转,其还具备一个更大地优点:即无需采用针对直管的机械爪手,而可采用本案中机械夹爪4的设计。
[0045]
如图4所示,单管输送机构1包括平直圆管储料架11、整列物料架12及在平直圆管储料架顶部与整列物料架顶部之间切换位移取放料的物料运转部13,整列物料架12的出料端设有承料部14。
[0046]
更细化地,整列物料架12包括倾斜整列导向底板121、设置于倾斜整列导向底板顶部的用于释放或阻停平直圆管的放料机构122,承料部14设置于倾斜整列导向底板的出料端底部,承料部包括若干相间隔设置的承料桩,承料桩之间形成间隔空间141。
[0047]
进一步细化地,该物料运转部13包括具备在平直圆管储料架顶部与整列物料架顶部之间切换位移的电磁吸附座,电磁吸附座具备升降拾料位移。
[0048]
具体地实现过程及原理说明:
[0049]
平直圆管储料架11内进行平直圆管的储料,通过电磁吸附座将其内的物料吸附后在整列导向底板121上进行释放,落料在整列导向底板121上整列后运输至放料机构122,放料机构122进行单根管材的放料,单根管材落至承料部14上,完成单根管材供给。
[0050]
而承料部14上的平直圆管由于间隔空间141的存在,方便焊缝调节机构2上的机构进行平直圆管周转。
[0051]
在一个具体实施例中,如图5所示,焊缝调节机构2包括基架主体21,基架主体21上设有平直圆管支撑部22、旋转驱动部23、用于将单管输送机构1上平直圆管运转至平直圆管支撑部22上的运转部24、及用于将平直圆管压贴在旋转驱动部上的压贴部25,压贴部25上设有用于检测焊缝的视觉传感器,视觉传感器与旋转驱动部相通讯连接。
[0052]
更细化地,平直圆管支撑部22包括沿平直圆管轴向间隔分布的若干支撑桩,圆管在支撑桩上具备自由旋转位移,旋转驱动部设置于相邻支撑桩之间,压贴部设置于旋转驱动部的顶部与旋转驱动部垂直向相对,压贴部包括用于压接在圆管上的随动滚轮组。
[0053]
具体地实现原理及过程说明:
[0054]
运转部24通过间隔空间141将承料部14上的平直圆管导向至平直圆管支撑部22,该运转部24采用翘板枢轴机构实现。
[0055]
平直圆管由平直圆管支撑部22支撑后,压贴部25下压将圆管贴靠在旋转驱动部上,旋转驱动部驱动圆管旋转进行焊缝调节,待视觉传感器检测到焊缝调节到位后即停止旋转,压贴部25上升释放圆管。如此实现焊缝角度调节。
[0056]
在一个具体实施例中,如图5所示,推送机构3包括设置在基架主体21上的线性轨道31、设置于线性轨道31上的推送滑座32,推送滑座32上设有用于与平直圆管的轴端相抵接的推送部33,支撑桩的顶部设有输送导向轮221。
[0057]
具体地说明,通过推送部33与平直圆管的轴端相对后线性位移,使得平直圆管受输送导向轮221导向、推入弯管设备20中。
[0058]
在一个具体实施例中,如图5所示,基架主体21的出料端设有具备枢轴位移的喷油嘴机构5,喷油嘴机构5具备喷嘴与平直圆管轴向相对的喷油对接位移、及用于送料避让的避让位移。并且采用此设计时,推送部33为具备夹持平直圆管端口壁的夹持件。
[0059]
具体地实现过程及原理说明:
[0060]
在平直圆管焊缝调节完成后,推送部33线性位移与平直圆管的端部相贴靠,并且夹持件夹持住圆管,喷油嘴机构5通过枢轴位移使得喷嘴与平直圆管轴向相对,此时夹持件线性位移驱动圆管与喷嘴相轴向对位连接,喷嘴进行喷涂油作业,待喷嘴作业完成后,夹持件线性反向位移将圆管与喷嘴分离,喷油嘴机构5枢轴位移至避让位移,此时夹持件再将圆管推送至弯管设备20中,如此能实现管端的自动对位喷油作业。
[0061]
在一个具体实施例中,如图6所示,机械夹爪4的两个料爪部41分别具备开合驱动源42,机械夹爪4上设有同步控制两个开合驱动源的联动控制机构6。
[0062]
联动控制机构6包括联动伸缩驱动源61,联动伸缩驱动源61的伸缩端具备两个枢轴配接的水平推杆部62,任意开合驱动源具备触发开关座,水平推杆部与触发开关座一一对应配合设置,两个水平推杆部相同步运动且水平向位移方向相反。
[0063]
即通过机械设计的联动控制机构6满足对两个料爪部41的联合驱动,联动控制稳
定可靠,不易产生驱动异步现象。
[0064]
通过以上描述可以发现,本实用新型弯管自动化产线,环状分布的自动化产线布局合理,全程自动化作业,各工位之间配合流程高效,且降低了布置空间需求。供料及弯管之间为直供设计,满足供料弯管作业与后道切换工位加工作业之间的潮汐交替需求,加工效率得到显著提升。平直圆管供料装置集物料运转、物料整列、焊缝调节、端口涂油、及推送料功能于一体,设计非常巧妙,减少了配合作业时间,运行高效流畅。特定地机械夹爪设计满足对成型弯管的稳定抓持需求,提高了弯管加工精度,产品合格率得到较大提升。
[0065]
以上对本实用新型的技术方案进行了充分描述,需要说明的是,本实用新型的具体实施方式并不受上述描述的限制,本领域的普通技术人员依据本实用新型的精神实质在结构、方法或功能等方面采用等同变换或者等效变换而形成的所有技术方案,均落在本实用新型的保护范围之内。
起点商标作为专业知识产权交易平台,可以帮助大家解决很多问题,如果大家想要了解更多知产交易信息请点击 【在线咨询】或添加微信 【19522093243】与客服一对一沟通,为大家解决相关问题。
此文章来源于网络,如有侵权,请联系删除



tips