一种大孔板支撑的双层微穿孔消声器的制作方法



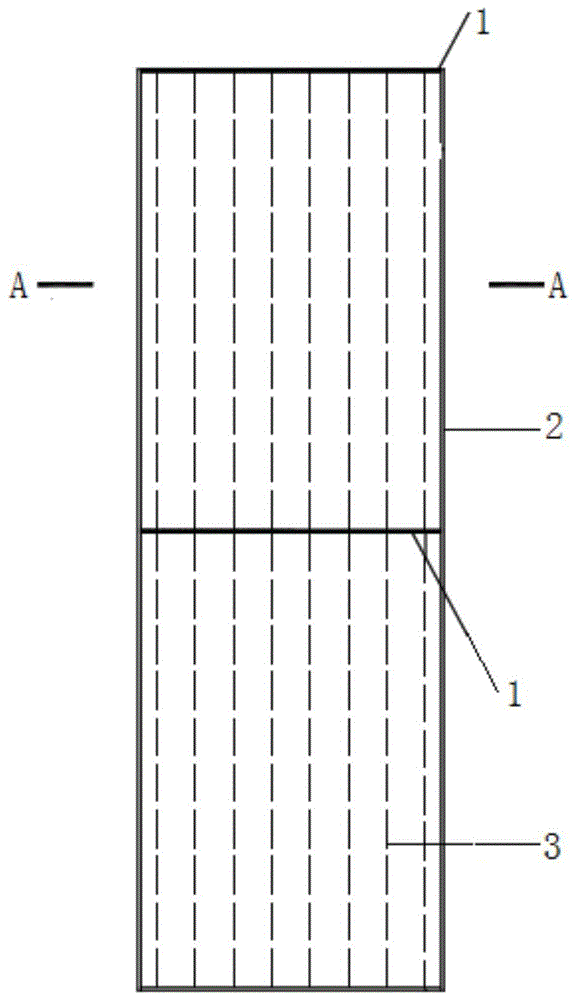
本实用新型涉及一种大孔板支撑的双层微穿孔消声器,属于消声器材技术领域。
背景技术:
微穿孔消声器因其结构特点及性能优势,经常应用于有特殊要求的环境当中,近些年逐步得到国内噪声控制领域的认可并广泛应用。微穿孔消声器声学结构由单层或多层微穿孔板及一定深度的空气层组成,因其吸声原理,微穿孔板厚度通常较小。当微穿板消声器所在气流通道内流速过高、压力过大时,微孔板表面将产生过高的载荷,微孔板自身强度无法承受,需在其承载面背侧进行补强支撑。如图1、图2所示,现有技术通常采用由微孔板1、外壳板2和金属蜂窝管3组成的类似蜂窝支撑结构,但因蜂窝支撑结构密度大、价格高、二次加工难度大,导致消声器的整体制造难度大、生产效率低,制作成本大幅升高。
技术实现要素:
针对上述突出问题,本实用新型提供一种大孔板支撑的双层微穿孔消声器,本实用新型的微孔板具有支撑补强结构,该结构简单可靠,既能保证消声器结构安全稳定具有较大的承载能力,又便于加工制造,提高生产效率,大幅降低消声器整体制作成本。
为实现上述目的,本实用新型采取以下技术方案:
一种大孔板支撑的双层微穿孔消声器,包括:
吸声结构和由外壳板2围成的桶型壳体,所述吸声结构包括设置在所述壳体内的若干微孔板1和与若干所述微孔板1一一对应设置若干衬板4,所述衬板4固定在所述微孔板1的下端面上,相邻两个所述吸声结构之间形成消声空气腔,所述消声空气腔的厚度为50-400mm。
所述的双层微穿孔消声器,优选地,所述微孔板1折叠成下端开口的回字型结构,且开口处的长度小于所述微孔板1上端面的长度,所述衬板4固定在所述微孔板1的内壁面上。
所述的双层微穿孔消声器,优选地,还包括筋板框架5,所述吸声结构焊接固定在所述筋板框架5上,所述筋板框架5是由一竖直筋板和若干水平筋板交叉固定形成的龙骨型结构。
所述的双层微穿孔消声器,优选地,所述龙骨型结构为十字型龙骨结构、x型龙骨结构或所述竖直筋板与所述水平筋板成任意角度的龙骨型结构。所述筋板框架5采用c型钢或矩形钢管制成,c型钢或矩形钢管制成由2mm厚的钢板加工而成。
所述的双层微穿孔消声器,优选地,所述微孔板1与所述衬板4之间设置有胶粘剂涂层,用于将二者固定粘合。更优选地,所胶粘剂涂层为金属胶粘剂涂层。
所述的双层微穿孔消声器,优选地,所述微孔板1与所述衬板4之间设置有电阻焊接点7,用于将二者通过电阻焊接的方式进行固定。更优选地,通过高密度电阻点焊方法将所述微孔板1与所述衬板4焊接到一起。
所述的双层微穿孔消声器,优选地,所述微孔板1的厚度为0.2-2.0mm,其孔径为0.2-2.0mm,穿孔率为0.1-5%。
所述的双层微穿孔消声器,优选地,所述衬板4为大孔径穿孔板,其厚度为2-5mm,孔径为3-20mm,穿孔率为20-40%。
所述的双层微穿孔消声器,优选地,所述消声空气腔的厚度为100-350mm。
所述的双层微穿孔消声器,优选地,所述双层微穿孔消声器的结构可以为长方体、正方体、圆柱体、圆台体或横截面为正多边形的圆柱体。当所述双层微穿孔消声器为正方体或长方体时,长度、宽度和高度均可变化。
所述的双层微穿孔消声器,优选地,所述衬板4和所述微孔板1的材质为镀锌板、钢板、铝合金板或不锈钢板,所述衬板4也可以采用其他材质的材料,只要起到支持作用即可。
所述的双层微穿孔消声器,优选地,所述外壳板2的材质为钢材,所述壳体通过采用所述外壳板2折制而成。
本实用新型所述的双层微穿孔消声器,能够保证消声器在内部高流速(大于20m/s)、大压力(大于5kpa)的工况下,微孔板结构强度及固定方式安全可靠,消声器整体结构稳定,同时大幅降低高流速、大压力工况微孔板消声器的制作成本。
本实用新型由于采取以上技术方案,其具有以下优点:
1、本实用新型未采用现有技术中的由金属蜂窝管所组成的蜂窝状支撑结构,而是在微孔板上固定带有大孔径的衬板来增强微孔板的支撑强度,避免现有技术中金属蜂窝管支撑结构密度大、价格高、二次价格难度大的问题;
2、本实用新型采用带孔的衬板作为微孔板的支撑补强结构,该结构简单可靠,既能保证消声器结构安全稳定具有较大的承载能力,又便于加工制造,提高生产效率,大幅降低消声器整体制作成本;
3、本实用新型通过在外壳板所组成的壳体内设置筋板框架,能够进一步增强微孔板的支撑强度,能够保证消声器在内部高流速(大于20m/s)、大压力(大于5kpa)的工况下,微孔板结构强度及固定方式安全可靠,消声器整体结构稳定。
附图说明
图1为现有技术中的微穿孔消声器的结构示意图;
图2为图1现有技术中的微穿孔消声器的a-a面剖面示意图;
图3为本实用新型中微穿孔消声器的结构示意图;
图4为图3中微穿孔消声器的b-b面剖面示意图;
图5为微孔板与衬板之间利用胶粘剂涂层进行粘合的结构示意图;
图6为微孔板与衬板之间利用电阻焊接进行固定的结构示意图;
图中各标记如下:
1-微孔板;2-外壳板;3-金属蜂窝管;4-衬板;5-筋板框架;6-胶粘剂涂层;7-电阻焊接点。
具体实施方式
为使本实用新型的目的、技术方案和优点更加清楚,下面对本实用新型中的技术方案进行清楚、完整地描述,显然,所描述的实施例是本实用新型一部分实施例,而不是全部的实施例。基于本实用新型中的实施例,本领域普通人员在没有做出创造性劳动前提下所获得的所有其他实施例,都属于本实用新型保护的范围。
实施例1
如图3至5所示,本实施例提供一种大孔板支撑的双层微穿孔消声器,包括:
吸声结构和由外壳板2围成的桶型壳体,所述吸声结构包括设置在所述壳体内的若干微孔板1和与若干所述微孔板1一一对应设置若干衬板4,所述衬板4固定在所述微孔板1的下端面上,相邻两个所述吸声结构之间形成消声空气腔,上下两个相邻所述消声空气腔的厚度分别为100mm、150mm。
本实施例中,还包括筋板框架5,所述吸声结构焊接固定在所述筋板框架5上,所述筋板框架5是由一竖直筋板和若干水平筋板交叉固定形成的龙骨型结构。
本实施例中,所述龙骨型结构为十字型龙骨结构,所述筋板框架5采用c型钢或矩形钢管制成,c型钢或矩形钢管制成由2mm厚的钢板加工而成。
本实施例中,所述微孔板1与所述衬板4之间设置有胶粘剂涂层,用于将二者固定粘合,所胶粘剂涂层为金属胶粘剂涂层。
本实施例中,所述微孔板1的厚度为1mm,其孔径为1mm,穿孔率为1.5%。
本实施例中,所述衬板4为大孔径穿孔板,其厚度为4mm,孔径为5mm,穿孔率为30%。
本实施例中,所述双层微穿孔消声器的结构为长方体。
本实施例中,所述衬板4和所述微孔板1的材质为不锈钢,所述衬板4也可以采用其他材质的材料,只要起到支持作用即可。所述外壳板2的材质为钢材,所述壳体通过采用所述外壳板2折制而成。
实施例2
如图3、图4和图6所示,本实施例提供一种大孔板支撑的双层微穿孔消声器,包括:
吸声结构和由外壳板2围成的桶型壳体,所述吸声结构包括设置在所述壳体内的若干微孔板1和与若干所述微孔板1一一对应设置若干衬板4,所述衬板4固定在所述微孔板1的下端面上,相邻两个所述吸声结构之间形成消声空气腔,上下两个相邻所述消声空气腔的厚度分别为100mm、150mm。
本实施例中,还包括筋板框架5,所述吸声结构焊接固定在所述筋板框架5上,所述筋板框架5是由一竖直筋板和若干水平筋板交叉固定形成的龙骨型结构。
本实施例中,所述龙骨型结构为十字型龙骨结构,所述筋板框架5采用c型钢或矩形钢管制成,c型钢或矩形钢管制成由2mm厚的钢板加工而成。
本实施例中,所述微孔板1与所述衬板4之间设置有电阻焊接点7,用于将二者通过电阻焊接的方式进行固定。更优选地,通过高密度电阻点焊方法将所述微孔板1与所述衬板4焊接到一起。
本实施例中,所述微孔板1的厚度为0.5mm,其孔径为0.5mm,穿孔率为0.8%。
本实施例中,所述衬板4为大孔径穿孔板,其厚度为4mm,孔径为5mm,穿孔率为30%。
本实施例中,所述双层微穿孔消声器的结构为长方体。
本实施例中,所述衬板4和所述微孔板1的材质为不锈钢,所述衬板4也可以采用其他材质的材料,只要起到支持作用即可。所述外壳板2的材质为钢材,所述壳体通过采用所述外壳板2折制而成。
最后应说明的是:以上实施例仅用以说明本实用新型的技术方案,而非对其限制;尽管参照前述实施例对本实用新型进行了详细的说明,本领域的普通技术人员应当理解:其依然可以对前述各实施例所记载的技术方案进行修改,或者对其中部分技术特征进行等同替换;而这些修改或者替换,并不使相应技术方案的本质脱离本实用新型各实施例技术方案的精神和范围。
起点商标作为专业知识产权交易平台,可以帮助大家解决很多问题,如果大家想要了解更多知产交易信息请点击 【在线咨询】或添加微信 【19522093243】与客服一对一沟通,为大家解决相关问题。
此文章来源于网络,如有侵权,请联系删除


