一种双工位烫画机转印方法与流程



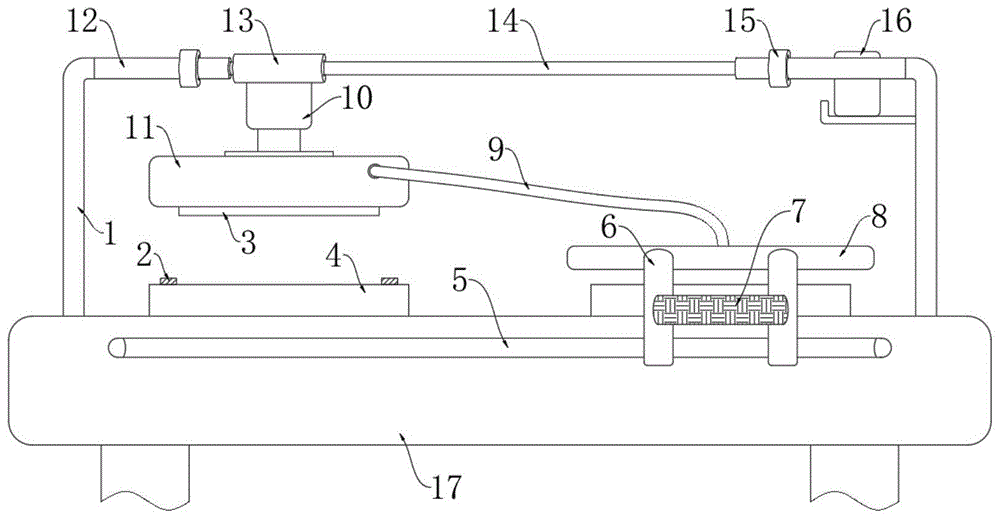
本发明涉及烫画机技术领域,尤其涉及一种双工位烫画机转印方法。
背景技术:
烫画机是利用热转印技术将各种丰富多彩的图案印烫在织物、瓷板、金属等表面,其中平板烫画机使用较为普遍,平板烫画机主要用于各种织物及服装的印烫,在家纺行业具有不可或缺的作用。
常见的烫画机只支持一个工位,在导热板加热承烫物时,加工人员只能耐心等待,从而导致加工效率低下,并且在加工时,导热板的温度一般在110℃以上,远高于环境温度,在热传递的作用下,大量热量逸散在周围环境中,无法得到有效回收利用,为此,我们提出一种双工位烫画机转印方法。
技术实现要素:
本发明的目的是为了解决现有技术中烫画机多为单工位加工,效率低下,并且很难有效回收热量的缺点,而提出的一种双工位烫画机转印方法。
为了实现上述目的,本发明采用了如下技术方案:
s1、开机并查验:打开烫画机开关,观察导热板是否升温,记录升温速度后关闭烫画机,再依次驱动气缸和步进电机,检查设备运转情况;
s2、预热:打开烫画机开关,保持10-20分钟;
s3、校准:调整上板的位置,使其处于一个工位的正上方,同时扁平释放管与另一个工位位置相对;
s4、转印:将两件承烫物分别平铺在两个下板上,控制气缸推动上板向下运动,导热板对承烫物进行加热;
s5、取件:加热到规定时间后,上板向上运动并复位,取出加工后的承烫物并将其冷却,同时步进电机驱动上板运动到另一个工位处,重复烫画;
上述一种双工位烫画机转印方法中还涉及了一种烫画机转印设备,包括工作台,所述工作台上对称设置有两个下板,每个所述下板的上表面均固定设置有多个堵块,所述工作台上通过立架支撑有驱动机构,所述驱动机构通过固定板连接有气缸,所述气缸的活塞杆通过平板固定连接有上板,所述上板的下表面固定安装有导热板,所述上板内开设有空槽,所述空槽通过多个连通口与外界相连通;
所述工作台的侧壁上水平安装有圆杆,所述圆杆上滑动设置有支撑件,所述支撑件的上端通过阻力轴承转动安装有扁平释放管,所述扁平释放管与空槽之间连通有伸缩管,且伸缩管靠近上板的一端安装有压力阀。
其中,所述驱动机构包括固定杆、步进电机和丝杠,所述固定杆的两端均与立架固定相连,所述固定杆的中部设有滑杆,且滑杆上滑动套设有第一滑座,所述丝杠的一端通过轴承与立架转动相连,所述丝杠的另一端通过联轴器与步进电机的输出轴固定相连,所述丝杠上安装有第二滑座,且固定板位于第一滑座、第二滑座之间并与第一滑座、第二滑座固定连接。
其中,每个所述连通口沿中轴线方向上的截面均为凸形,且每个连通口内均粘接有橡胶垫圈。
其中,所述扁平释放管内开设有多个相互连通的排气管道,且多个排气管道均与伸缩管相连通。
其中,所述固定杆上对称套设有两个永磁环,且两个永磁环均靠近滑杆。
本发明的有益效果:
1、通过设置气缸、伺服电机、丝杠、第一滑座、第二滑座等装置组成的驱动机构,可灵活改变上板和导热板的位置,从而实现半自动加工。
2、通过设置双工位,可在其中一个工位转印时,在另一个工位上处理承烫物,节约找平、固定承烫物的时间,从而大大提高加工效率。
3、通过在上板内设置空槽、压力阀、连通口等装置,可回收部分导热板逸散的热量对空槽内的空气进行加热,相对减少了热量的浪费,提高了能量利用效率。
4、当较高温度的气体从扁平释放管处喷出时,因为扁平释放管倾斜朝向下板,所以气流可使平铺在下板上的承烫物更加平整,并且高温还能对织物起到熨烫作用,减轻棉麻类织物的起皱程度,并且随着气流的吹拂,下板、工作台上的线头等杂物也会被清理走。
5、因为滚珠丝杠没有自锁性,因此当第一滑座以及第二滑座运动到工位的正上方时,相对一侧的永磁环可对气缸等部件产生吸引作用,从而与固定杆一起限制第一滑座或第二滑座的运动,保证装置稳定性。
附图说明
图1为本发明的结构示意图;
图2为本发明中驱动机构的俯视图;
图3为本发明中上板的内部结构示意图;
图4为本发明中扁平释放管的正面结构示意图。
图中:1立架、2堵块、3导热板、4下板、5圆杆、6支撑件、7握把、8扁平释放管、9伸缩管、10气缸、11上板、12固定杆、13第一滑座、14滑杆、15永磁环、16步进电机、17工作台、18第二滑座、19丝杠、20空槽、21压力阀、22连通口、23橡胶垫圈、24排气管道。
具体实施方式
下面将结合本发明实施例中的附图,对本发明实施例中的技术方案进行清楚、完整地描述,显然,所描述的实施例仅仅是本发明一部分实施例,而不是全部的实施例。
参照图1-4,一种双工位烫画机转印方法,具体使用方法如下:
s1、开机并查验:打开烫画机开关,观察导热板3是否升温,记录升温速度后关闭烫画机,再依次驱动气缸10和步进电机16,检查设备运转情况;
s2、预热:打开烫画机开关,保持10-20分钟;
s3、校准:调整上板11的位置,使其处于一个工位的正上方,同时扁平释放管8与另一个工位位置相对;
s4、转印:将两件承烫物分别平铺在两个下板4上,控制气缸10推动上板11向下运动,导热板3对承烫物进行加热;
s5、取件:加热到规定时间后,上板11向上运动并复位,取出加工后的承烫物并将其冷却,同时步进电机16驱动上板11运动到另一个工位处,重复烫画。
上述一种精确调节式小型烫画机使用过程中还涉及了一种烫画机转印设备,包括工作台17,工作台17上对称设置有两个下板4,每个下板4的上表面均固定设置有多个堵块2,工作台17上通过立架1支撑有驱动机构,驱动机构通过固定板连接有气缸10,气缸10的活塞杆通过平板固定连接有上板11,上板11的下表面固定安装有导热板3,上板11内开设有空槽20,空槽20通过多个连通口22与外界相连通;
工作台17的侧壁上水平安装有圆杆5,圆杆5上滑动设置有支撑件6,支撑件6上固定有用于手扶的握把7,支撑件6的上端通过阻力轴承转动安装有扁平释放管8,扁平释放管8与空槽20之间连通有伸缩管9,且伸缩管9靠近上板11的一端安装有压力阀21。
其中,驱动机构包括固定杆12、步进电机16和丝杠19,固定杆12的两端均与立架1固定相连,固定杆12的中部设有滑杆14,且滑杆14上滑动套设有第一滑座13,丝杠19的一端通过轴承与立架1转动相连,丝杠19的另一端通过联轴器与步进电机16的输出轴固定相连,丝杠19上安装有第二滑座18,且固定板位于第一滑座13、第二滑座18之间并与第一滑座13、第二滑座18固定连接。
其中,每个连通口22沿中轴线方向上的截面均为凸形,且每个连通口22内均粘接有橡胶垫圈23,堵块2的规格与连通口22的规格相匹配。
其中,扁平释放管8内开设有多个相互连通的排气管道24,且多个排气管道24均与伸缩管9相连通。
其中,固定杆12上对称套设有两个永磁环15,且两个永磁环15均靠近滑杆14。
具体工作时,先预热导热板3一定时间,在此过程中将两件承烫物分别平铺在两个工位上,做转印准备,待导热板3的温度达到要求值后,控制步进电机16开启,电机输出轴转动带动丝杠19同步转动,第二滑座18可沿丝杠19上运动并与第一滑座13共同带动气缸10运动到其中一个工位处,当上板11与一个下板4对齐时,步进电机16的输出轴停止转动,随后气缸10的活塞杆伸长,使导热板3与承烫物贴合,开始转印;
在开始转印前,手扶握把7将扁平释放管8拉至另一个工位处,并调节扁平释放管8与支撑件6的角度,使扁平释放管8倾斜朝向对应的下板4;
当开始转印时,上板11靠近下板4,此时,堵块2进入对应的连通口22,因为连通口22沿中轴线方向上的截面均为凸形,且每个连通口22内均粘接有橡胶垫圈23,因此当堵块2进入连通口22后会阻断空槽20内的气体与外界气体的交换,且导热板3多为铝材外壳,发热管位于铝材外壳内部,如图3所示,因此导热板3处的热量不断向空槽20内传递,使空槽20内的温度快速升高;
当空槽20内的压强超过一定值后,压力阀21打开,较高温度的气体通过伸缩管9进入扁平释放管8内的排气管道24内,然后向外喷出,因为扁平释放管8倾斜朝向对应的下板4,所以气流可使平铺在下板4上的承烫物更加平整,并且高温还能对织物起到熨烫作用,减轻棉麻类织物的起皱程度,并且随着气流的吹拂,下板4、工作台17上的线头等杂物也会被清理走;
需要说明的是,因为堵块2未进入连通口22时,空槽20内的气体可与外界气体循环交换,因此即使导热板3处于预热中,空槽20内的气体温度也还有大量上升空间;
一个工位上的承烫物转印完成后,气缸10回收,步进电机16反向转动,借助驱动机构可使上板11转移到另外一个工位上,对第二个工位上的织物进行烫画,此时在取下烫画完成后的承烫物后,还能再下板4上平铺一件承烫物,做好转印准备,从而提高了工作效率;
值得一提的是,固定杆12上对称套设有两个永磁环15,且两个永磁环15均靠近滑杆14,因为滚珠丝杠没有自锁性,因此当第一滑座13以及第二滑座18运动到工位的正上方时,相对一侧的永磁环15可对气缸10、第一滑座13、第二滑座18等部件产生吸引作用,从而与固定杆12一起限制第一滑座13或第二滑座18的运动。
以上所述,仅为本发明较佳的具体实施方式,但本发明的保护范围并不局限于此,任何熟悉本技术领域的技术人员在本发明揭露的技术范围内,根据本发明的技术方案及其发明构思加以等同替换或改变,都应涵盖在本发明的保护范围之内。
起点商标作为专业知识产权交易平台,可以帮助大家解决很多问题,如果大家想要了解更多知产交易信息请点击 【在线咨询】或添加微信 【19522093243】与客服一对一沟通,为大家解决相关问题。
此文章来源于网络,如有侵权,请联系删除


