同步旋转控制纤维排列结构的纺纱装置的制作方法



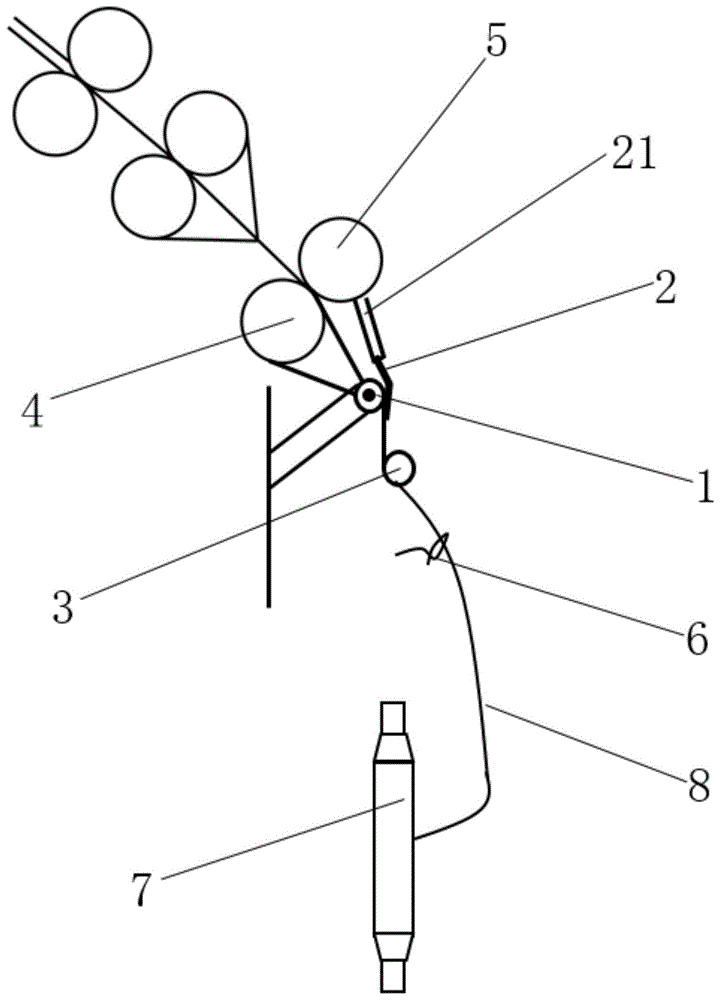
本实用新型涉及纺织加工
技术领域:
,尤其涉及同步旋转控制纤维排列结构的纺纱装置。
背景技术:
:现代纺织行业竞争日益激烈,高产高效是企业实现进一步发展最有效的手段。高产高效必然要求高速,但高速生产会使纺纱张力增大,直接造成细纱断头率增加,细纱品质下降。若要在高速的前提下保证生产正常进行,必须增大细纱捻度,以提高细纱的强力,促使纺纱张力与纱线强力处于相对平衡的状态,降低细纱断头率。捻度不仅影响强力,还是影响成纱残余扭应力的决定性因素之一,细纱捻度与织物紧度共同决定了针织物表面的线圈形态,即针织物表面的线圈歪斜程度。加捻过程中纤维发生弯曲变形,纤维中存在残余扭应力,应力产生应变,使纱线有解捻的趋势,因此细纱中会存在不稳定的捻度。细纱捻度越大,纱体内纤维的回弹性越大,残余扭应力越大,残余扭矩越大,存在的不稳定捻度越多。成纱毛羽的控制对织物性能也有很大影响,有效减少有害毛羽可以减少后续整经的断头率、上浆时的浆纱疵点等,有效提高织物质量和生产效率。环锭纺纱诞生已经有几百年的历史,此项技术之所以延用至今,主要是其技术优点是其它方法无法具有的,但该技术也具有明显的缺点,即对牵伸后的纤维须条的约束和控制不够,导致纤维毛羽增多,成纱纱残余扭应力加大。为了减小甚至消除纱线的有害毛羽和残余扭矩,已发展出种类众多的纺纱方法,根据原理,大体上可以分为两大类:永久性处理法和物理扭矩平衡法。永久性处理法主要是通过将纱线的弹性扭转变形转变为塑性变形,以达到释放残余扭矩的目的,但永久处理法不能有效降低纱线的残余扭矩;物理扭矩平衡法相对于永久性处理而言有一定的优势,它是一种纯机械性的处理技术,该方法是利用纱线的结构使不同纱线产生的残余扭矩相互平衡,而纱线仍保持弹性变形特征,但物理扭矩平衡法存在假捻段存在极大的摩擦、恶化了纱线质量、断头率较高等问题,故不适合用于高支纱线。技术实现要素:有鉴于此,本实用新型的实施例提供了同步旋转控制纤维排列结构的纺纱装置。本实用新型的实施例提供同步旋转控制纤维排列结构的纺纱装置,包括第一转轴、压纱簧片和第二转轴,所述第一转轴两端分别通过轴承固定在前钳口下方,所述第一转轴中部间隔设有带有螺纹的纤维整理段和皮带连接段,所述纤维整理段位于所述前钳口的正下方,所述皮带连接段通过皮带连接前罗拉,所述压纱簧片的一端可活动地压在所述纤维整理段上,所述第二转轴位于所述第一转轴下方,所述第二转轴上设有螺纹,且所述第二转轴上的螺纹方向与所述纤维整理段内的螺纹方向相反,所述皮带用于带动所述第一转轴转动,并控制所述纤维整理段的线速度与所述前罗拉的线速度相同,所述第一转轴与所述第二转轴配合用于整理纱线的纤维结构,以平衡纱线内部扭矩及集聚纤维、减小纱线表面毛羽,所述压纱簧片用于约束纱线在所述纤维整理段的螺纹槽内运动并压迫纱线上的纤维向内转移减少毛羽。进一步地,所述纤维整理段的外径与所述皮带连接段的外径相同,且均小于所述第一转轴的外径。进一步地,所述纤维整理段内部和所述第二转轴内部均设有加热块。进一步地,所述第二转轴固定在固定轴上,所述固定轴连接调节支架,所述调节支架用于调节所述第二转轴的压纱深度及调整纱线在所述纤维整理段上的包围弧。进一步地,所述压纱簧片为钝角“l”形,且所述压纱簧片的另一端连接簧片支架。本实用新型还提供了同步旋转控制纤维排列结构的纺纱装置的纺纱工艺,包括以下步骤:s1、粗纱经牵伸机构牵伸后,纱线从所述前罗拉和前皮辊组成的前钳口输出;s2、所述前罗拉通过所述皮带带动所述第一转轴转动,所述纤维整理段推动纱线在其螺纹槽内翻转并进行整理,在纱线整理过程中,所述压纱簧片持续将纱线约束在所述纤维整理段的螺纹槽内,并压迫纱线表面的纤维向纱线中心转移;s3、从所述压纱簧片穿出的纱线在纱线张力的牵引下进入所述第二转轴的螺纹槽中,并在所述第二转轴的螺纹槽内进行反向翻转,最后从所述第二转轴穿出的纱线经过导纱钩和钢丝圈卷绕在纱锭上。进一步地,步骤s2中,纱线在所述纤维整理段的螺纹槽内翻转过程中,所述纤维整理段内的加热块对所述纤维整理段进行加热,其加热温度为100℃-260℃。进一步地,步骤s3中,纱线在所述第二转轴的螺纹槽内进行反向翻转过程中,所述第二转轴内的加热块对所述第二转轴进行加热,其加热温度为100℃-260℃。本实用新型的实施例提供的技术方案带来的有益效果是:1)本实用新型利用所述前罗拉作为动力,带动所述纤维整理段同步旋转,并推动纱线在所述纤维整理段的螺纹槽内横移,所述压纱簧片协同引纱张力压持纱线翻转以对纱线的纤维进行整理,并迫使纱线表面的纤维向纱线中心转移;2)本实用新型通过所述纤维整理段内的所述加热块降低纤维模量,使纤维在所述纤维整理段内得到充分转移,并使得纱线内部的纤维排列紧密,从而提高纱线的强力利用率和纱线强力;3)本实用新型可通过所述第二转轴对纱线的运行轨迹进行调节,从而增加纱线在所述纤维整理段上形成的包围弧,以提高纱线的整理效率,同时还可通过所述第二转轴上的螺纹槽反向翻转纱线,使纱线扭矩平衡,且可使纱线的外层纤维排列疏松、平直顺滑,另外还可通过所述第二转轴内的加热模块对纱线加热定捻,以使纱线的捻度得到有效控制。附图说明图1是本实用新型同步旋转控制纤维排列结构的纺纱装置的结构示意图。图2是本实用新型同步旋转控制纤维排列结构的纺纱装置的俯视图。图3是图1中纤维整理段11的工作原理图。图中:1-第一转轴,11-纤维整理段,12-皮带连接段,13-皮带,14-轴承,2-压纱簧片,21-簧片支架,3-第二转轴,31-固定轴,32-调节支架,4-前罗拉,5-前皮辊,6-导纱钩,7-纱锭,8-纱线。具体实施方式为使本实用新型的目的、技术方案和优点更加清楚,下面将结合附图对本实用新型实施方式作进一步地描述。请参考图1和图2,本实用新型的实施例提供了同步旋转控制纤维排列结构的纺纱装置,包括第一转轴1、压纱簧片2和第二转轴3。所述第一转轴1两端分别通过轴承14固定在前钳口下方,所述第一转轴1中部间隔设有带有螺纹的纤维整理段11和皮带连接段12,本实例中所述纤维整理段11上的螺纹尺寸可根据实际纱支的型号进行选择,所述纤维整理段11的外径与所述皮带连接段12的外径相同,且均小于所述第一转轴1的外径,所述纤维整理段11位于所述前钳口的正下方,且所述纤维整理段11内部设有加热块,所述加热块可用于提高纤维转移效率同时减少纤维毛羽的产生。所述皮带连接段12通过皮带13连接前罗拉4,所述皮带13用于带动所述第一转轴1转动,并控制所述纤维整理段11的线速度与所述前罗拉4的线速度相同,实现同步旋转,以消除纱线8在所述纤维整理段11上的滑动摩擦带来的条干恶化,本实施例中纱线8嵌入所述纤维整理段11的螺纹槽内且与其保持相同线速度运行,当所纺的纱线8为“z捻”纱线,且所述纤维整理段11的螺纹为左旋螺纹时,纱线8沿所述左旋螺纹旋转区向右移动,并在引纱张力作用下向左翻转,同时向前钳口方向形成“z捻”假捻;同样当所纺纱线8为“s捻”纱线,且所述纤维整理段11的螺纹为右旋螺纹时,纱线8沿所述右旋螺纹向左移动,并在引纱张力作用下向右翻转,同时向前钳口方向形成“s捻”假捻,“z捻”或“s捻”假捻的形成可有效控制纺纱三角区形态,提高纤维转移效率,迫使纤维向纱线8中心集聚,即纱线8内部紧密集聚,提高纱线8强力,且所述纤维整理段11内部的加热快能降低纤维模量,在提高纤维转移效率的同时,还可减少纤维毛羽的产生。所述压纱簧片2为钝角“l”形,所述压纱簧片2的一端可活动地压在所述纤维整理段11上,以限制纱线8在所述纤维整理段11的螺纹槽内运动,所述压纱簧片2的另一端连接簧片支架21,所述压纱簧片2用于约束纱线8在所述纤维整理段11的螺纹槽内运动并压迫纱线8上的纤维向内转移减少毛羽,同时所述压纱簧片2还可用于克服纤维的弹性恢复。本实用新型中当纱线8的横移距离增大移动至其他螺纹槽上时,引纱张力也会不断增大,一旦引纱张力大于所述纤维整理段11的螺纹槽侧面对纱线8的推力,纱线8就会在引纱张力的作用下会翻回至初始的螺纹槽。本实施例中所述压纱簧片2接触于所述纤维整理段11上的螺纹表面形成接触线,通过调节所述簧片支架21的固定角度可改变压所述压纱簧片2对纱线8的作用力,从而可适用于各种不同型号的纱支。所述第二转轴3位于所述第一转轴1下方,具体地,所述第二转轴3固定在固定轴31上,所述固定轴31连接调节支架32,所述调节支架32用于调节所述第二转轴3的压纱深度及调整纱线8在所述纤维整理段11上的包围弧。所述第二转轴3内部同样设有加热块,所述第二转轴3内的加热块可提高纱线8表面纤维平行顺直度,本实施例中所述第二转轴3上设有螺纹,且所述第二转轴3上的螺纹方向与所述纤维整理段11内的螺纹方向相反,所述第一转轴1与所述第二转轴3配合用于整理纱线8的纤维结构,以平衡纱线8内部扭矩及集聚纤维、减小纱线8的表面毛羽。请参考图1-图3,本实用新型还提供同步旋转控制纤维排列结构的纺纱装置的纺纱工艺,包括以下步骤:s1、粗纱经牵伸机构牵伸后,纱线8从所述前罗拉4和前皮辊5组成的前钳口输出;s2、所述前罗拉4通过所述皮带13带动所述第一转轴1转动,从而所述纤维整理段11推动纱线8在其螺纹槽内翻转并进行整理,在纱线8整理过程中,所述压纱簧片2持续将纱线8约束在所述纤维整理段11的螺纹槽内,并压迫纱线8表面的纤维向纱线8中心转移,本实施例中纱线8在所述纤维整理段11的螺纹槽内翻转过程中,所述纤维整理段11内的加热块可对所述纤维整理段33进行加热,其加热温度为100℃-260℃;s3、从所述压纱簧片2穿出的纱线8在纱线张力的牵引下进入所述第二转轴3的螺纹槽中,并在所述第二转轴3的螺纹槽内进行反向翻转,纱线8在所述第二转轴3的螺纹槽内的反向翻转促使纱线8的扭矩平衡,且可使纱线8表面的纤维变疏松,同时经过所述第二转轴3内部的加热块的加热,可使纱线8表面的纤维变得更平行顺直,从而可生产出具有内紧外松结构的纱线8,此外纱线8还具有手感柔软、强力高、毛羽少、条干稳定及残余扭矩少等优点,本实施例中当纱线8在所述第二转轴3的螺纹槽内进行反向翻转过程中,所述第二转轴3内的加热块可对所述第二转轴3进行加热,其加热温度为100℃-260℃,从所述第二转轴3穿出的纱线8最后经过导纱钩6和钢丝圈(附图中未画出)卷绕在纱锭7上,最终形成“外松内紧”的高强超柔纱线。如下是使用传统环锭纺纱机和本实用新型所述的纺纱装置分别进行纺纱的具体实施例:本实施例分别使用传统环锭纺纱机和本实用新型所述的纺纱装置对三种不同型号的纱线进行三种对比实验,在纺纱过程中,传统环锭纺纱机采用传统纺纱工艺,本实用新型所述的纺纱装置采用本实用新型所述的纺纱工艺,且在纺纱过程中传统环锭纺纱机和本实用新型所述的纺纱装置所用原材料与部分纺纱工艺参数相同,见表一:表一传统环锭纺纱机和本实用新型纺纱装置所用纺纱原材料及部分工艺参数项目实验1(z捻)实验2(z捻)实验3(z捻)粗纱定重(g/10m)4.54.54.5纱线号数(tex)101520牵伸倍数45.030.022.5前罗拉线速度(m/min)12.113.315.2锭速(r/min)120001000010000设计捻系数320300300对于每一纱线号数,分别使用传统环锭纺纱机和本实用新型所述的纺纱装置加工成单股纱线样本以作对比,并对各纱线号数的纱线样本的主要性能进行测试,其中残余扭矩利用湿缠绕法进行测试,各纱线样本的主要性能测试结果如表二所示:表二采用传统环锭纺纱机和本实用新型纺纱装置所纺纱线的主要性能从表二可以看出,使用本实用新型的纺纱装置所纺纱线,其毛羽值和残余扭矩(湿扭结数)都显著下降,效果较好;且与使用传统环锭纺纱机所纺纱线相比,使用本实用新型的纺纱装置所纺纱线的断裂强力和断裂伸长率显著提高,而条干性能基本可以保持不变。在本文中,所涉及的前、后、上、下等方位词是以附图中零部件位于图中以及零部件相互之间的位置来定义的,只是为了表达技术方案的清楚及方便。应当理解,所述方位词的使用不应限制本申请请求保护的范围。在不冲突的情况下,本文中上述实施例及实施例中的特征可以相互结合。以上所述仅为本实用新型的较佳实施例,并不用以限制本实用新型,凡在本实用新型的精神和原则之内,所作的任何修改、等同替换、改进等,均应包含在本实用新型的保护范围之内。当前第1页1 2 3 
起点商标作为专业知识产权交易平台,可以帮助大家解决很多问题,如果大家想要了解更多知产交易信息请点击 【在线咨询】或添加微信 【19522093243】与客服一对一沟通,为大家解决相关问题。
此文章来源于网络,如有侵权,请联系删除



tips