一种熔喷模头的制作方法



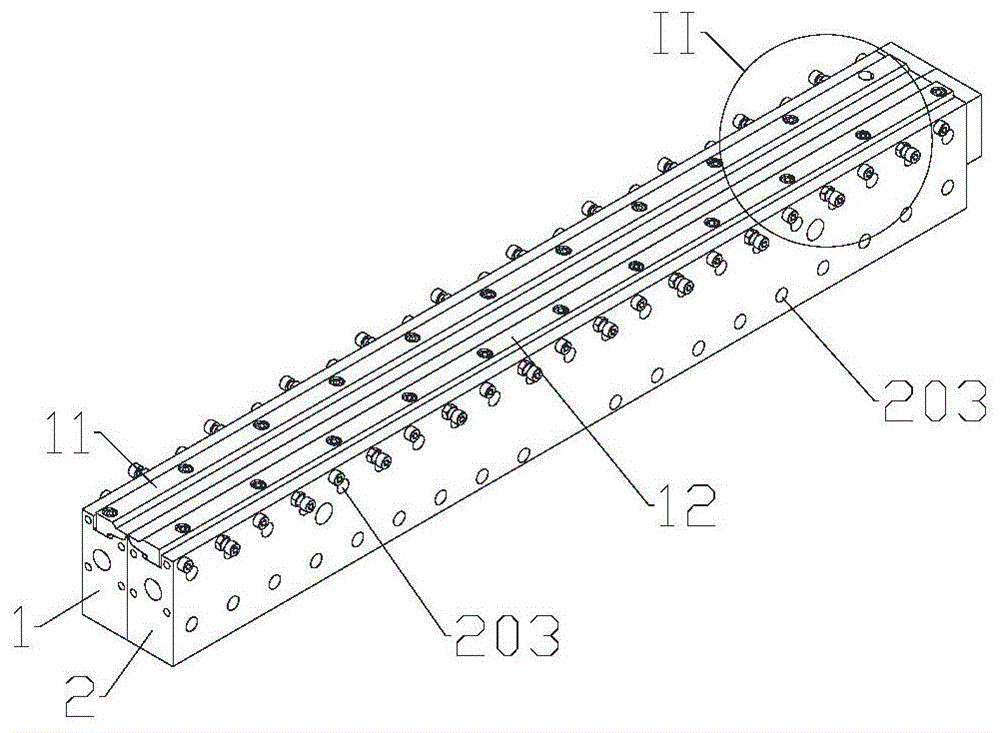
本实用新型涉及塑料加工机械,特别是一种熔喷模头。
背景技术:
现有用于生产熔喷无纺布的熔喷模头上的熔喷孔,直径一般在0.2~0.3mm,多数是采用机械钻孔或激光加工,由于这些加工方式都有可能造成熔喷孔内产生毛刺或表面比较粗糙,熔融聚合物在持续流动过程中,很有可能造成熔喷孔堵塞,或是影响熔融聚合物流动速度,形成结晶,而影响熔喷布质量。因此在用于生产熔喷布之前,一般都需要对这些熔喷孔进行抛光加工,例如采用斯曼克磨粒流抛光。加工一米宽幅的熔喷布,对应会有1250~1400个熔喷孔,不仅熔喷孔的加工工作量大,费时费力,而且对机床和钻头的要求也很高,加工成本较高。另外,个别熔喷孔出现损坏,无法维修,只能更换喷丝板,而喷丝板的价格占到了整个熔喷模头的60%以上,维修成本太高。
技术实现要素:
本实用新型所要达到的目的就是提供一种熔喷模头,更容易加工,降低加工成本及使用成本,同时增加热风的调节方式,方便调试,提高适应性。
为了达到上述目的,本实用新型采用如下技术方案:一种熔喷模头,包括第一部分和第二部分,第一部分和第二部分拼装形成熔融流道,熔融流道的下游端为熔喷孔,第一部分设有第一风道,第二部分设有第二风道,第一部分和第二部分之间夹紧固定有针管,针管的内孔形成熔喷孔,针管的后端外周设有用于轴向定位的第一锥面,第一锥面的直径由后向前缩小,第一部分、第二部分与第一锥面贴合,第一部分的前端设有可移动调节固定位置的第一盖板,第一盖板与第一部分之间形成连接第一风道的第一出风缝隙,第二部分的前端设有可移动调节固定位置的第二盖板,第二盖板与第二部分之间形成连接第二风道的第二出风缝隙,第一出风缝隙的出风口和第二出风缝隙的出风口分别位于熔喷孔的两侧。
进一步的,所述针管的内孔后端内壁设有第二锥面,第二锥面的直径由后向前缩小。
进一步的,所述第一部分的前端设有与第一盖板相对形成第一出风缝隙的第一倾斜面,第二部分的前端设有与第二盖板相对形成第二出风缝隙的第二倾斜面,针管的前端设有与第一倾斜面平齐的第一斜切面、与第二倾斜面平齐的第二斜切面,第一斜切面和第二斜切面通过针管的前端面隔开,第一斜切面、第二斜切面与针管的内孔壁相交形成豁口。
进一步的,所述第一盖板上设有第一调节孔,第一螺栓穿过第一调节孔与第一部分连接将第一盖板固定,第一调节孔的长度大于第一螺栓的螺纹直径。
进一步的,所述第一部分上设有多个用于驱动第一盖板沿第一调节孔的长度方向移动的第一调节件,第一调节件沿第一盖板的长度方向排列。
进一步的,所述第一调节件包括第一调节螺栓,第一部分设有与第一调节螺栓配合的第一螺纹通孔,第一调节螺栓穿过第一螺纹通孔与第一盖板连接。
进一步的,一部分第一调节螺栓上设有锁紧螺母,有锁紧螺母的第一调节螺栓与无锁紧螺母的第一调节螺栓间隔分布。
进一步的,所述第二盖板上设有第二调节孔,第二螺栓穿过第二调节孔与第二部分连接将第二盖板固定,第二调节孔的长度大于第二螺栓的螺纹直径。
进一步的,所述第二部分上设有多个用于驱动第二盖板沿第二调节孔的长度方向移动的第二调节件,第二调节件沿第二盖板的长度方向排列。
进一步的,所述第二调节件包括第二调节螺栓,第二部分设有与第二调节螺栓配合的第二螺纹通孔,第二调节螺栓穿过第二螺纹通孔与第二盖板连接。
采用上述技术方案后,本实用新型具有如下优点:采用针管的内孔形成熔喷孔,由于针管单独加工比较容易,而且针管的内孔表面粗糙度容易控制,可以减少不必要的抛光处理,同时采用第一部分和第二部分拼装夹紧针管的方式,只需要在第一部分和第二部分上设置与针管配合的安装槽即可,不再需要打孔,对加工精度的要求降低至能够满足针管装配的要求即可,由于针管的外径相比现有技术中的熔喷孔直径要大得多,所以安装槽的尺寸也相应比熔喷孔的直径要大,更容易加工,加工精度更容易得到保证,在很大程度上降低了加工成本,由于每根针管可以单独更换,相比现有技术,维修费用大大降低,降低用户的使用成本;由于熔融聚合物在针管的内孔中从针管的后端向前端流动,对针管产生一个向前推动的作用力,而设置第一锥面与第一部分、第二部分贴合,正好可以让针管与第一部分、第二部分贴合更加紧密,并能做到无间隙配合,可以确保熔融聚合物不会进入针管与第一部分、第二部分的装配间隙,由于锥面配合结构的同轴度较高,装卸方便,虽经多次装卸,仍能保证精确的定心作用,更换针管也比较方便,可以在更换后快速地投入使用。第一盖板和第二盖板可移动调节固定位置,通过调节第一盖板和第二盖板的固定位置,可以根据不同原材料或不同型号产品要求来调节第一出风缝隙和第二出风缝隙的宽度,改变热风吹出的风量和风速,增加熔喷模头对不同原材料或不同型号产品的适应性。另外,熔喷模头通过两个部分拼装组成,方便熔融流道抛光、电镀等加工。
附图说明
下面结合附图对本实用新型作进一步说明:
图1为本实用新型一种熔喷模头的结构示意图(拆除左端端盖);
图2为图1中熔喷模头左端面的示意图;
图3为本实用新型一种熔喷模头的剖视图;
图4为图3中i处的放大图;
图5为本实用新型中针管的示意图;
图6为图1中ii处的放大图;
图7为本实用新型中第一部分的示意图;
图8为图7中iii处的放大图。
具体实施方式
本实用新型提供一种熔喷模头,如图1至图5所示,包括第一部分1和第二部分2,第一部分1和第二部分2拼装形成熔融流道100,熔融流道100的下游端为熔喷孔,第一部分1设有第一风道101,第二部分2设有第二风道201,第一部分1和第二部分2之间夹紧固定有针管3,针管3的内孔300形成与熔融流道100连通的熔喷孔,针管3的后端外周设有用于轴向定位的第一锥面301,第一锥面301的直径由后向前缩小,第一部分1、第二部分2与第一锥面301贴合,本实用新型采用针管3的内孔形成熔喷孔,由于针管3单独加工比较容易,而且针管3的内孔表面粗糙度容易控制,可以减少不必要的抛光处理,同时采用第一部分1和第二部分2拼装夹紧针管3的方式,只需要在第一部分1和第二部分2上设置与针管3配合的安装槽即可,不再需要打孔,对加工精度的要求降低至能够满足针管3装配的要求即可,由于针管3的外径相比现有技术中的熔喷孔直径要大得多,所以安装槽的尺寸也相应比熔喷孔的直径要大,更容易加工,加工精度更容易得到保证,在很大程度上降低了加工成本,由于每根针管3可以单独更换,相比现有技术,维修费用大大降低,降低用户的使用成本;由于熔融聚合物在针管3的内孔中从针管3的后端向前端流动,对针管3产生一个向前推动的作用力,而设置第一锥面301与第一部分1、第二部分2贴合,正好可以让针管3与第一部分1、第二部分2贴合更加紧密,并能做到无间隙配合,可以确保熔融聚合物不会进入针管3与第一部分1、第二部分2的装配间隙,由于锥面配合结构的同轴度较高,装卸方便,虽经多次装卸,仍能保证精确的定心作用,更换针管3也比较方便,可以在更换后快速地投入使用。针对不同原材料或不同产品型号的熔喷加工,采用针管的内孔形成的熔喷孔与常规的钻孔加工成型的熔喷孔,对热风的风量、风速等参数要求不同,常规的熔喷孔所适用的经验数据无法完全适用本实用新型,因此为了让操作人员能够方便快速地调试热风吹出的风量及风速,本实用新型在第一部分1的前端设有可移动调节固定位置的第一盖板11,第一盖板11与第一部分1之间形成连接第一风道101的第一出风缝隙102,第二部分2的前端设有可移动调节固定位置的第二盖板21,第二盖板21与第二部分2之间形成连接第二风道201的第二出风缝隙202,第一出风缝隙102的出风口和第二出风缝隙202的出风口分别位于熔喷孔的两侧。第一盖板11和第二盖板21可移动调节固定位置,通过调节第一盖板11和第二盖板21的固定位置,可以根据不同原材料或不同型号产品要求来调节第一出风缝隙102和第二出风缝隙202的宽度,改变热风吹出的风量和风速,增加熔喷模头对不同原材料或不同型号产品的适应性。另外,熔喷模头通过两个部分拼装组成,方便熔融流道抛光、电镀等加工。
热风从第一出风缝隙102的出口和第二出风缝隙202的出口吹出,将熔喷孔喷出的熔融聚合物吹到接收装置上,例如凝网帘或滚筒上,生产出无纺布。
为了熔融聚合物能够更加顺畅地流入熔喷孔,可以在针管3的内孔后端内壁设有第二锥面302,第二锥面302的直径由后向前缩小。在本实施例中,第一锥面301和第二锥面302均是圆锥面,方便针管3加工及安装。可以理解的,虽然可能会增加少量成本,但是采用棱锥面也是可行的。
第一部分1的前端设有与第一盖板11相对形成第一出风缝隙102的第一倾斜面121,第二部分2的前端设有与第二盖板21相对形成第二出风缝隙202的第二倾斜面221,为了减少熔喷无纺布中团块状聚合物的数量,针管3的前端设有与第一倾斜面121平齐的第一斜切面303、与第二倾斜面221平齐的第二斜切面304,第一斜切面303和第二斜切面304通过针管3的前端面隔开,第一斜切面303、第二斜切面304与针管的内孔300壁相交形成豁口306。由于针管3的前端两侧形成豁口306,而熔融聚合物运动至针管3的前端面才会开始与针管3脱离,熔融聚合物在离开针管3之前会通过这两个豁口306与热风接触,受到热风牵伸形成纤维的同时,又因为与针管3接触而受针管3的握持作用不会直接脱离针管3,因此可以让熔融聚合物得到充分拉伸形成超细纤维,减少团块状聚合物的出现。
结合图6看,为实现第一盖板11固定位置的调节,可以在第一盖板11上设有第一调节孔111,第一螺栓112穿过第一调节孔111与第一部分1连接将第一盖板11固定,第一调节孔111的长度大于第一螺栓112的螺纹直径,例如可以将第一调节孔111设置成腰孔,如果第一螺栓112的螺栓头也沉入第一调节孔111,则需要设置第一调节孔111的长度大于第一螺栓112的螺栓头的直径。
由于第一盖板11具有较长的长度,而第一盖板11的固定位置的调节属于比较细小幅度的调节,为实现细小幅度的调节,同时保证第一盖板11调节后的直线度,可以在第一部分1上设有多个用于驱动第一盖板11沿第一调节孔111的长度方向移动的第一调节件13,第一调节件13沿第一盖板11的长度方向排列。在本实施例中,第一调节件13包括第一调节螺栓,第一部分1设有与第一调节螺栓配合的第一螺纹通孔,第一调节螺栓穿过第一螺纹通孔与第一盖板11连接。除了螺纹调节,也可以采用楔块等常见方式来调节。为确保第一盖板11在调节后能够较长时间保持固定位置,可以在一部分第一调节螺栓上设有锁紧螺母131,有锁紧螺母131的第一调节螺栓与无锁紧螺母131的第一调节螺栓间隔分布。
同样的道理,为实现第二盖板21固定位置的调节,可以在第二盖板21上设有第二调节孔211,第二螺栓212穿过第二调节孔211与第二部分2连接将第二盖板21固定,第二调节孔211的长度大于第二螺栓212的螺纹直径。与第一盖板11类似的,第二盖板21也具有较长的长度,为实现细小幅度的调节,同时保证第二盖板21调节后的直线度,可以在第二部分2上设有多个用于驱动第二盖板21沿第二调节孔211的长度方向移动的第二调节件23,第二调节件23沿第二盖板21的长度方向排列。在本实施例中,第二调节件23包括第二调节螺栓,第二部分2设有与第二调节螺栓配合的第二螺纹通孔,第二调节螺栓穿过第二螺纹通孔与第二盖板21连接。与第一调节螺栓类似,也可以在一部分第二调节螺栓上设置锁紧螺母。
由于第一盖板11与第二盖板21属于对称结构,因此可以采用同步调节的结构,例如采用齿轮、齿条等啮合结构来实现。
由于熔喷孔数量较多,为了熔融聚合物能够均匀流入所有熔喷孔,可以在熔融流道100上位于针管3的后端设有一个熔喷缓冲腔1001,熔融聚合物从熔喷缓冲腔1001进入熔喷孔。
而为了让熔融聚合物在熔喷流道内均匀稳定流动,可以设计熔融流道100包括位于上游且呈衣架状的主流道1002和位于主流道1002、熔喷缓冲腔1001之间的平流道1003,平流道1003上设有过渡缓冲腔1004。
下面结合图1、图7和图8看。
为了将第一部分1与第二部分2可靠地固定拼装,可以在第一部分1上位于熔喷缓冲腔1001和过渡缓冲腔1004之间的位置设有连接孔105,第二部分2上位于熔喷缓冲腔1001和过渡缓冲腔1004之间的位置设有连接通孔203,连接通孔203与连接孔105对接,连接螺栓穿过连接通孔与连接孔连接将第一部分1、第二部分2固定。为了第一部分1与第二部分2固定拼装更加可靠,还可以在第一部分1上设置更多的连接孔105,例如本实施例中在主流道1002的外侧设置有整排的连接孔105,第二部分2上设置相应的连接通孔203。
在本实施例中,熔融流道100设于第一部分,第二部分盖住熔融流道100,这样只需要对第一部分1进行装夹加工,加工基准唯一,加工精度容易得到保证,由于形成熔喷缓冲腔1001和过渡缓冲腔1004的空间较大,因此可以在第一部分1和第二部分2上分别加工出一部分,然后拼装形成熔喷缓冲腔1001和过渡缓冲腔1004。可以理解的,也可以将熔融流道100设在第二部分2,第一部分1盖住熔融流道100;或者,在第一部分1设有第一流道槽,第二部分2设有第二流道槽,第二流道槽与第一流道槽组成熔融流道100。
第一部分1上设有用于配合针管3的第一配合槽103,由于针管3的直径较小,加工第一配合槽103具体一定的难度,因此可以在第一部分1上设有用于减少第一配合槽103加工长度的第一节料槽104,第一节料槽104沿第一部分1的长度方向设置并与所有第一配合槽103交叉连通,第一节料槽104的深度大于第一配合槽103的深度,由于加工第一节料槽104时不需要考虑加工精度,而第一配合槽103的加工长度缩短后,加工难度下降,由于针管3的后端设计的第一锥面301结构让针管3的固定不会受第一配合槽103的加工长度缩短的影响。同样的道理,也可以在第二部分2上设有用于配合针管3的第二配合槽,第二部分2上设有用于减少第二配合槽加工长度的第二节料槽,第二节料槽沿第二部分2的长度方向设置并与所有第二配合槽交叉连通,第二节料槽的深度大于第二配合槽的深度。
除上述优选实施例外,本实用新型还有其他的实施方式,本领域技术人员可以根据本实用新型作出各种改变和变形,只要不脱离本实用新型的精神,均应属于本实用新型权利要求书中所定义的范围。
起点商标作为专业知识产权交易平台,可以帮助大家解决很多问题,如果大家想要了解更多知产交易信息请点击 【在线咨询】或添加微信 【19522093243】与客服一对一沟通,为大家解决相关问题。
此文章来源于网络,如有侵权,请联系删除


