包装盒料板的自动定位及模切生产线的制作方法



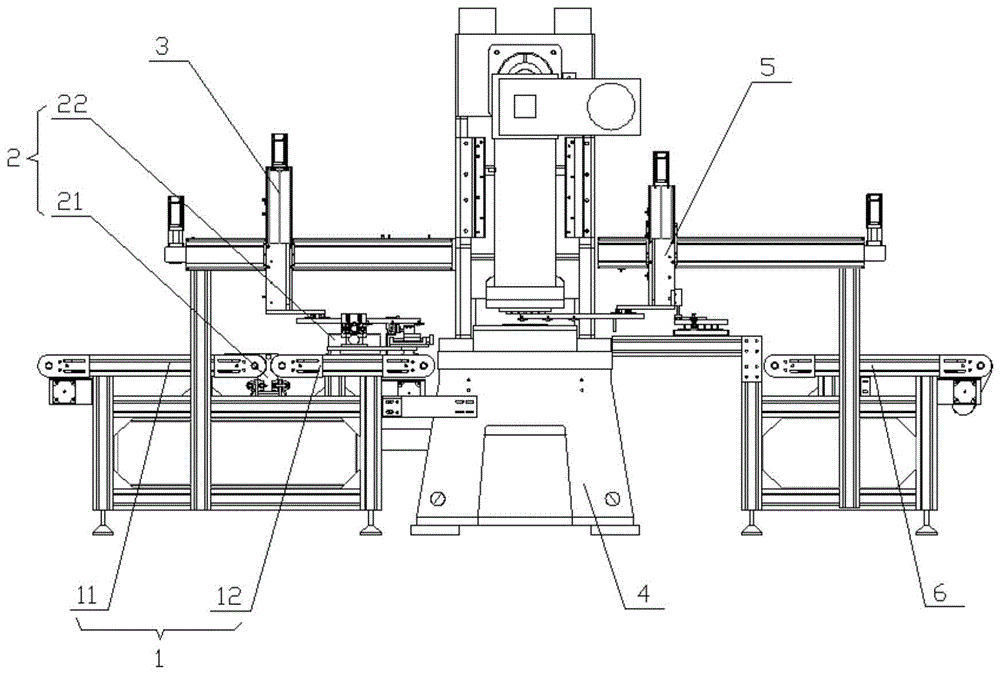
本发明涉及包装设备技术领域,尤其涉及一种包装盒料板的自动定位及模切生产线。
背景技术:
在化妆品包装盒等一类产品中,组成包装盒的料板由纸板和面纸复合而成,其中,纸板厚度在1mm以上,面纸厚度在0.2mm左右,为了加强组成包装盒时的粘贴牢固和美观,面纸的面积一般均大于纸板的面积,即面纸的四边将突出纸板的四周边沿。
在现有技术的包装盒料板生产过程中,需要人手将料板放置定位到模切机上,然后利用模切机进行自动切模后,手工取下完成切模的料板,最后手工对料板进行排废,其存在如下不足:
(1)存在大量的人工作业,安全性能低,生产效率低;
(2)长时间人工操作,容易由于人工误操作或者不恰当操作造成定位不精准的问题,出现较高的废品率,不利于企业降低生产成本。
因此,有必要提供一种能够实现料板全自动流水线作业的生产线。
技术实现要素:
为了克服上述现有技术所述的至少一种缺陷,本发明提供一种包装盒料板的自动定位及模切生产线。
本发明为解决其问题所采用的技术方案是:
一种包装盒料板的自动定位及模切生产线,包括用于料板上料的前端输送装置、自动定位装置、上料模组、冲模装置、下料排废装置以及后端输送装置,其中,所述自动定位装置设置于所述前端输送装置上且用于对所述前端输送装置输送的料板进行定位,所述上料模组用于将完成定位的料板输送至所述冲模装置,所述冲模装置用于对料板进行冲模,所述下料排废装置用于对完成冲模的料板进行废料清除并下料至所述后端输送装置。
本发明所提供的包装盒料板的自动定位及模切生产线,将前端输送、自动定位、上料、冲模、排废下料以及后端输送相结合,通过自动定位装置对料板进行定位,并利用下料排废装置对完成冲模的料板进行废料清除和下料,实现了包装盒料板上料冲模的全自动流水线作业,提高冲模精准度,提高生产效率。
进一步地,所述自动定位装置包括用于将料板进行预定位的预夹正模块以及用于将料板最终定位的定位模块。
进一步地,所述前端输送装置包括前端输送带和后端输送带,所述预夹正模块设置于所述前端输送带与后端输送带之间,所述定位模块设置于所述后端输送带上,所述前端输送带用于将料板输送至所述预夹正模块,所述后端输送带用于将预定位后的料板输送至所述定位模块。
进一步地,所述预夹正模块包括第一电眼、两相对滑动设置的夹板以及驱动两所述夹板相对滑动的驱动装置,所述第一电眼用于检测料板,所述驱动装置驱动两所述夹板相对滑动以将料板夹正到预设位置。
进一步地,所述定位模块包括第二电眼、前限位预压装置以及两侧夹正装置,所述第二电眼用于检测料板,所述前限位预压装置用于抵挡在料板的纸板前侧并对料板的面纸进行预压,两所述侧夹正装置用于夹持在料板的纸板左右两侧以将料板定位。
进一步地,所述前限位预压装置包括前挡板、第一平移驱动机构以及第一竖直驱动机构,所述第一平移驱动机构驱动所述前挡板沿料板的输送方向水平移动,所述第一竖直驱动机构驱动所述前挡板沿竖直方向上下移动。
进一步地,所述侧夹正装置包括侧挡板、第二平移驱动机构以及第二竖直驱动机构,所述第二平移驱动机构驱动所述侧挡板垂直于料板的输送方向水平移动,所述第二竖直驱动机构驱动所述侧挡板沿竖直方向上下移动。
进一步地,所述下料排废装置包括用于吸放料板的下料模组、用于放置料板的排废底模以及排废上模,所述排废上模设置于所述下料模组上,所述排废底模上设置有对应料板废料位置的穿孔,所述排废上模上设置有顶针,当所述下料模组带动所述排废上模相对所述排废底模向下运动时,所述顶针将料板上的废料从所述穿孔处向下顶出清除。
进一步地,所述下料排废装置包括用于吸放料板的下料模组、用于放置料板的排废底模以及用于吹除废料的吹气结构,所述吹气结构位于所述排废底模的侧边,所述排废底模上设置有与料板的废料相对应的凸模,当所述下料模组吸取并带动料板相对所述排废底模向下运动时,所述凸模将料板上的废料向上顶出清除。
进一步地,所述下料排废装置还包括用于扫除所述排废底模上的残存废料的除屑结构,所述除屑结构设置于所述下料模组上。
综上所述,本发明所提供的包装盒料板的自动定位及模切生产线,其有益效果为:
将前端输送、自动定位、上料、冲模、排废下料以及后端输送相结合,通过自动定位装置对料板进行定位,并利用下料排废装置对完成冲模的料板进行废料清除和下料,实现了包装盒料板上料冲模的全自动流水线作业,提高冲模精准度,提高生产效率。本发明的其他有益效果将在具体实施方式中展出。
附图说明
图1为本发明实施例1的结构示意图;
图2为本发明实施例1的自动定位装置的结构示意图;
图3为图2所示的预夹正模块的结构示意图;
图4为图2所示的定位模块的结构示意图;
图5为图4所示的定位模块的定位示意图;
图6为图4所示的前限位预压装置的结构示意图;
图7为图4所示的侧夹正装置的结构示意图;
图8为图1所示的下料排废装置的结构示意图;
图9为图8所示的下料排废装置的排废结构的示意图;
图10为本发明实施例2的下料排废装置的结构示意图;
图11为图10所示的下料排废装置的排废结构的示意图。
其中,附图标记含义如下:
1、前端输送装置;11、前端输送带;12、后端输送带;2、自动定位装置;21、预夹正模块;211、第一电眼;212、夹板;213、驱动装置;2131、预夹基座;2132、滑座;2133、滑杆;2134、水平气缸;2135、限位件;22、定位模块;221、第二电眼;222、前限位预压装置;2221、前挡板;2222、第一平移驱动机构;2223、第一竖直驱动机构;2224、第一预调基座;2225、第一预调螺杆;223、侧夹正装置;2231、侧挡板;2232、第二平移驱动机构;2233、第二竖直驱动机构;2234、第二预调基座;2235、第二预调螺杆;224、定位基座;3、上料模组;4、冲模装置;5、下料排废装置;51、下料模组;511、第一取放组件;512、第二取放组件;513、下压气缸;52、排废底模;521、穿孔;522、凸模;53、排废上模;531、顶针;54、吹气结构;55、除屑结构;6、后端输送装置;7、料板。
具体实施方式
为了更好地理解和实施,下面将结合本发明实施例中的附图,对本发明实施例中的技术方案进行清楚、完整地描述。
在本发明的描述中,需要说明的是,术语“上”、“下”、“前”、“后”、“左”、“右”、“竖直”、“水平”、“顶”、“底”“内”、“外”等指示的方位或位置关系为基于附图所示的方位或位置关系,仅是为了便于描述本发明和简化描述,而不是指示或暗示所指的装置或元件必须具有特定的方位、以特定的方位构造和操作,因此不能理解为对本发明的限制。
除非另有定义,本文所使用的所有的技术和科学术语与属于本发明的技术领域的技术人员通常理解的含义相同。本文中在本发明的说明书中所使用的术语只是为了描述具体的实施例的目的,不是旨在限制本发明。
实施例1
参阅图1至图9,本发明公开了一种包装盒料板的自动定位及模切生产线,包括用于料板7上料的前端输送装置1、自动定位装置2、上料模组3、冲模装置4、下料排废装置5以及后端输送装置6,其中,所述自动定位装置2设置于所述前端输送装置1上且用于对所述前端输送装置1输送的料板7进行定位,所述上料模组3用于将完成定位的料板7输送至所述冲模装置4,所述冲模装置4用于对料板7进行冲模,所述下料排废装置5用于对完成冲模的料板7进行废料清除并下料至所述后端输送装置6。在本发明中,将前端输送、自动定位、上料、冲模、排废下料以及后端输送相结合,通过自动定位装置2对料板7进行定位,并利用下料排废装置5对完成冲模的料板7进行废料清除和下料,实现了包装盒料板上料冲模的全自动流水线作业,提高冲模精准度,提高生产效率。
在本实施例中,所述自动定位装置2包括用于将料板7进行预定位的预夹正模块21以及用于将料板7最终定位的定位模块22。在本发明中,将对料板7的定位工作分为两步,其中,利用所述预夹正模块21将料板7进行预定位,然后再利用所述定位模块22将料板7最终定位,以便于后续的所述定位模块22能够用更短的行程完成对料板7的精准定位,以降低定位难度,防止出现在最终定位时料板7跑偏的问题。
参阅图1和图2,其中,所述前端输送装置1包括前端输送带11和后端输送带12;所述预夹正模块21设置于所述前端输送带11与后端输送带12之间,所述定位模块22设置于所述后端输送带12上,所述前端输送带11用于将料板7输送至所述预夹正模块21,所述后端输送带12用于将预定位后的料板7输送至所述定位模块22。具体的,所述前端输送带11和后端输送带12设置于生产线的机架上,且所述前端输送带11和后端输送带12的输送面位于同一水平面上,以便于料板7从所述前端输送带11移动至所述后端输送带12。
参阅图2和图3,在本实施例中,所述预夹正模块21包括第一电眼211、两相对滑动设置的夹板212以及驱动两所述夹板212相对滑动的驱动装置213,所述第一电眼211用于检测料板7,所述驱动装置213驱动两所述夹板212相对滑动以将料板7夹正到预设位置。其中,两所述夹板212位于所述前端输送带11和后端输送带12之间,所述驱动装置213安装于生产线的机架上,所述第一电眼211的安装位置不具体限定,能够完成是否有料板7位于两所述夹板212之间的检测即可。
由此,利用所述第一电眼211以检测料板7,以便于所述夹板212能够更为精准的将料板7夹正到预设位置,便于精准细化所述料板7的预夹正工作,提高预夹正频率,提高工作效率;同时便于所述夹板212夹持规格的缩小化,便于所述夹板212在生产线上的装配,减少设备成本。
具体的,所述驱动装置213包括预夹基座2131,所述预夹基座2131的两侧分别设置有两滑座2132,同一侧的两所述滑座2132上分别滑动设置有一滑杆2133,两所述夹板212分别固定连接于两所述滑杆2133上,所述预夹基座2131的两侧还设置有两水平气缸2134,两所述水平气缸2134分别驱动两所述滑杆2133反向滑动以带动两所述夹板212相对靠近或远离。较佳的,每一所述滑杆2133上均设置有一限位件2135,所述限位件2135位于两所述夹板212之间且可调节固定于所述滑杆2133的任一位置,利用两所述限位件2135以限定两所述夹板212之间的最小间隔距离。
参阅图2、图4和图5,在本实施例中,所述定位模块22包括第二电眼221、前限位预压装置222以及两侧夹正装置223,所述第二电眼221用于检测料板7,所述前限位预压装置222用于抵挡在料板7的纸板前侧并对料板7的面纸进行预压,两所述侧夹正装置223用于夹持在料板7的纸板左右两侧以将料板7定位。
由此,利用所述第二电眼221以检测料板7,以便于所述前限位预压装置222和侧夹正装置223能够更为精准的将料板7夹持定位,同时便于精准细化所述前限位预压装置222和侧夹正装置223的夹持定位工作,提高夹持定位频率,提高工作效率。
其中,所述定位模块22还包括设置于所述后端输送带12上方的定位基座224,所述前限位预压装置222和侧夹正装置223设置于所述定位基座224。诚然,所述第二电眼221的安装位置不具体限定,能够完成是否有料板7位于所述定位模块22工位的检测即可。
参阅图6,在本实施例中,所述前限位预压装置222包括前挡板2221、第一平移驱动机构2222以及第一竖直驱动机构2223,所述第一平移驱动机构2222驱动所述前挡板2221沿料板7的输送方向水平移动,所述第一竖直驱动机构2223驱动所述前挡板2221沿竖直方向上下移动。其中,所述第一平移驱动机构2222滑动设置于第一预调基座2224上,所述第一预调基座2224上转动设置有第一预调螺杆2225,所述第一预调螺杆2225与所述第一平移驱动机构2222相螺纹配合,当旋转所述第一预调螺杆2225时,所述第一预调螺杆2225螺纹配合带动所述第一平移驱动机构2222在所述第一预调基座2224上滑动,以预调所述第一平移驱动机构2222初始位置;所述前挡板2221设置于所述第一竖直驱动机构2223的输出端,所述第一竖直驱动机构2223设置于所述第一平移驱动机构2222的输出端,所述第一平移驱动机构2222和第一竖直驱动机构2223均采用气缸驱动。
参阅图7,在本实施列中,所述侧夹正装置223包括侧挡板2231、第二平移驱动机构2232以及第二竖直驱动机构2233,所述第二平移驱动机构2232驱动所述侧挡板2231垂直于料板7的输送方向水平移动,所述第二竖直驱动机构2233驱动所述侧挡板2231沿竖直方向上下移动。其中,与所述前限位预压装置222同理,所述第二平移驱动机构2232滑动设置于第二预调基座2234上,所述第二预调基座2234上转动设置有第二预调螺杆2235,所述第二预调螺杆2235与所述第二平移驱动机构2232相螺纹配合,当旋转所述第二预调螺杆2235时,所述第二预调螺杆2235螺纹配合带动所述第二平移驱动机构2232在所述第二预调基座2234上滑动,以预调所述第二平移驱动机构2232初始位置;所述侧挡板2231设置于所述第二竖直驱动机构2233的输出端,所述第二竖直驱动机构2233设置于所述第二平移驱动机构2232的输出端,所述第二平移驱动机构2232和第二竖直驱动机构2233均采用气缸驱动。
在本实施例中,所述自动定位装置2的工作过程如下:
1、当所述第一电眼211检测到料板7进入两所述夹板212之间时,所述前端输送带11停止输送,所述驱动装置213驱动两所述夹板212相对靠近运动,以将偏离预设位置的料板7推动至预设位置,以便于后续的所述定位模块22能够用更短的行程完成对料板7的精准定位;
2、在所述预夹正模块21将料板7完成预定位的同时,两所述侧夹正装置223开始第一步工作,所述第二平移驱动机构2232驱动所述侧挡板2231伸出第一行程,所述侧挡板2231第一行程的距离根据预设位置的参数以及料板7的参数综合计算设定,以防止所述侧挡板2231在后续的水平夹持移动时刮起面纸;同时,所述前限位预压装置222开始第一步工作,所述第一平移驱动机构2222驱动所述前挡板2221伸出第一行程,所述前挡板2221第一行程的距离根据料板7的参数计算设定(具体的,所述前挡板2221第一行程的距离大于面纸突出纸板的长度大小);
3、在所述预夹正模块21将料板7完成预定位后,所述前端输送带11和后端输送带12启动,其中,所述前端输送带11将完成预定位的料板7输送至所述后端输送带12,所述后端输送带12将料板7向前输送,直至所述前限位预压装置222的前挡板2221抵接在料板7的纸板前侧(所述前挡板2221的下端与所述后端输送带12的输送面的距离大于料板7的面纸厚度且小于料板7的整体厚度);
4、此时,所述第二电眼221检测到料板7,所述后端输送带12停止输送,所述第一竖直驱动机构2223驱动所述前挡板2221下压在料板7的面纸上以完成对料板7的预压;
5、所述第二竖直驱动机构2233驱动所述侧挡板2231向下移动,直至所述侧挡板2231的底部与所述后端输送带12的输送面的距离大于料板7的面纸厚度且小于料板7的整体厚度,然后第二平移驱动机构2232驱动所述侧挡板2231水平移动,直至两所述侧挡板2231夹持在料板7的纸板左右两侧,从而完成对料板7的最终定位;
6、所述前挡板2221以及两侧挡板2231上升并退回,所述上料模组3开始工作,吸取完成最终定位的料板7并上料至所述冲模装置4。
在本实施例中,因为所述上料模组3以及冲模装置4均为现有技术,在此不再赘述。
参阅图8和图9,在本实施例中,所述下料排废装置5包括用于吸放料板7的下料模组51以及用于放置料板7的排废底模52。
需要说明的是,在本发明中,所述下料模组51的主体结构与所述上料模组3同样均为现有技术,其差别仅在于,所述上料模组3具有一个取放组件,而所述下料模组51具有两个取放组件,因此,在本实施例中,不再对所述下料模组51的主体结构进行赘述。
在本实施例中,所述下料模组51包括用于将完成冲模的料板7输送至所述排废底模52的第一取放组件511和用于将完成排废的料板7输送至所述下料输送装置6的第二取放组件512;当所述第一取放组件511取料时,所述第二取放组件512与排废底模53相配合以对所述排废底模53上放置的料板7完成排废。由此,所述下料模组51中的第二取放组件512同时具有取放料的功能以及结合排废底模53实现对料板7排废的功能,以实现对料板7的取料、排废、输出下料的一体化作业,提高生产效率。
其中,所述第一取放组件511和第二取放组件512在所述下料模组51的驱动机构作用下,同步平移和升降。当所述第一取放组件511从所述冲模装置4上吸取完成冲模的料板7时,所述第二取放组件512同时从所述排废底模52上吸取完成排废的料板7;当所述第一取放组件511将所吸取的料板7放置至所述排废底模52上时,所述第二取放组件512同时将所吸取的料板7放置至所述下料输送装置6上。以此加快所述冲模下料排废装置5下料的速度,提高生产效率。
在本发明中,所述第一取放组件511和第二取放组件512均为现有技术,所述第一取放组件511和第二取放组件512为现有技术中的负压吸盘结构。
在本实施例中,较佳的,所述第二取放组件512通过一下压气缸513连接至所述下料模组51的主体结构上,其中,所述下压气缸513固定在所述下料模组51的主体结构上,所述第二取放组件512固定连接在所述下压气缸的输出端,当需要下压排废时,可通过系统主动控制所述下压气缸伸缩以带动所述第二取放组件512完成取料和排废。
在本实例中,所述下料排废装置5还包括排废上模53,所述排废上模53设置于所述第二取放组件512上,所述排废上模53与所述第二取放组件512相结合并随所述第二取放组件512移动;所述排废底模52上设置有对应料板7废料位置的穿孔521,所述排废上模53上设置有顶针531,当所述下料模组51带动所述排废上模53相对所述排废底模52向下运动时,所述顶针531将料板7上的废料从所述穿孔521处向下顶出清除。利用所述顶针531与穿孔521的相配合,在所述第二取放组件512对排废底模52上的料板7进行吸取的同时,实现了对横切后料板7的排废,其结构简单,大大的简化了排废结构,节省成本,且动作简洁,在取料的过程中即可完成排废,提高了生产效率。
其中,为了便于废料的顶出下落,所述穿孔521的尺寸大于料板7上的废料的尺寸,所述顶针531的横截面尺寸小于料板7上的废料的尺寸。
当所述第一取放组件511在所述冲模装置4的位置处下压以吸取料板7时,所述第二取放组件512带动所述排废上模53下压,所述顶针531将放置于所述排废底模52的料板7上的废料从所述穿孔521处向下顶出清除,当所述第二取放组件512下压到极限位置后,所述第二取放组件512上的吸盘吸附住完成排废后的料板7。
较佳的,所述顶针531的数量与所述穿孔521以及料板上废料的数量相对应,且每一所述顶针531均对应一所述穿孔521及废料。
在本实施例中,所述排废底模52通过两横杆设置于两排废基座56上,诚然所述排废底模52还可直接安装在生产线上或其他安装架上。其中,两所述排废基座56之间空置,以便于放置收废箱以收集废料。
参阅图8和图9,在本实施例中,所述下料排废装置5还包括用于扫除所述排废底模52上的残存废料的除屑结构55,所述除屑结构55设置于所述下料模组51上。
在本实施例中,较佳的,所述除屑结构55位于所述第一取放组件511和第二取放组件512之间,且所述除屑结构55与第一取放组件511和/第二取放组件512同步平移。
具体的,所述除屑结构55为毛刷,所述毛刷设置于所述第一取放组件511的下方,且位于所述第一取放组件511的负压吸盘与所述第二取放组件512的负压吸盘之间。当所述第一取放组件511和第二取放组件512在所述排废底模52上方往返移动时,所述毛刷能够将所述排废底模52的残存废料扫除干净。
实施例2
参阅图10和图11,本实施例与实施例1的差别仅在于所述料排废装置5中的排废机构的不同。具体如下:
在本实施例中,所述下料排废装置5包括用于吸放料板7的下料模组51、用于放置料板7的排废底模52以及用于吹除废料的吹气结构54,所述排废底模52上设置有与料板7的废料相对应的凸模522,当所述第二取放组件512吸取并带动料板7相对所述排废底模52向下运动时,所述凸模522将料板7上的废料向上顶出清除,所述吹气结构54位于所述排废底模52的侧边以用于吹飞被顶出的废料。由此,利用所述第二取放组件512下压取料时的推力,推动料板7向下运动,并配合排废底模52上的凸模522以将料板7上的废料向上顶出清除,实现了对横切后料板7的排废,其结构更为简洁简单,无需排废上模53,减少了所述第二取放组件512的整体重量;同时,当需要对不同规格的料板7进行生产时,只需要更换所述排废底模52即可,节省人工成本、模具开模成本。
其中,为了便于废料的向上顶出,所述凸模522的尺寸小于料板7上的废料的尺寸。
较佳的,所述凸模522的数量与料板上废料的数量相对应,且每一所述凸模522均对应一废料。
在本实施例中,所述下料模组51的结构与实施1的一致,同样包括第一取放组件511和第二取放组件512,所述第二取放组件512同样通过一下压气缸513连接至所述下料模组51的主体结构上,在此不再赘述。
在本实施例中,当所述第一取放组件511在所述冲模装置4的位置处下压以吸取料板7时,所述第二取放组件512推动料板下压,在下压过程中,所述凸模522将料板7上的废料向上顶出清除,所述吹气结构54开始工作,将顶出的废料吹飞,当所述第二取放组件512下压到极限位置后,所述第二取放组件512上的吸盘吸附住完成排废后的料板7。
综上所述,本发明所提供的包装盒料板的自动定位及模切生产线,将前端输送、自动定位、上料、冲模、排废下料以及后端输送相结合,通过自动定位装置2对料板7进行定位,并利用下料排废装置5对完成冲模的料板7进行废料清除和下料,实现了包装盒料板上料冲模的全自动流水线作业,提高冲模精准度,提高生产效率。
本发明方案所公开的技术手段不仅限于上述实施方式所公开的技术手段,还包括由以上技术特征任意组合所组成的技术方案。应当指出,对于本技术领域的普通技术人员来说,在不脱离本发明原理的前提下,还可以做出若干改进和润饰,这些改进和润饰也视为本发明的保护范围。
起点商标作为专业知识产权交易平台,可以帮助大家解决很多问题,如果大家想要了解更多知产交易信息请点击 【在线咨询】或添加微信 【19522093243】与客服一对一沟通,为大家解决相关问题。
此文章来源于网络,如有侵权,请联系删除


