一种用于惰性气体灭火系统的气体稳压释放器的制作方法



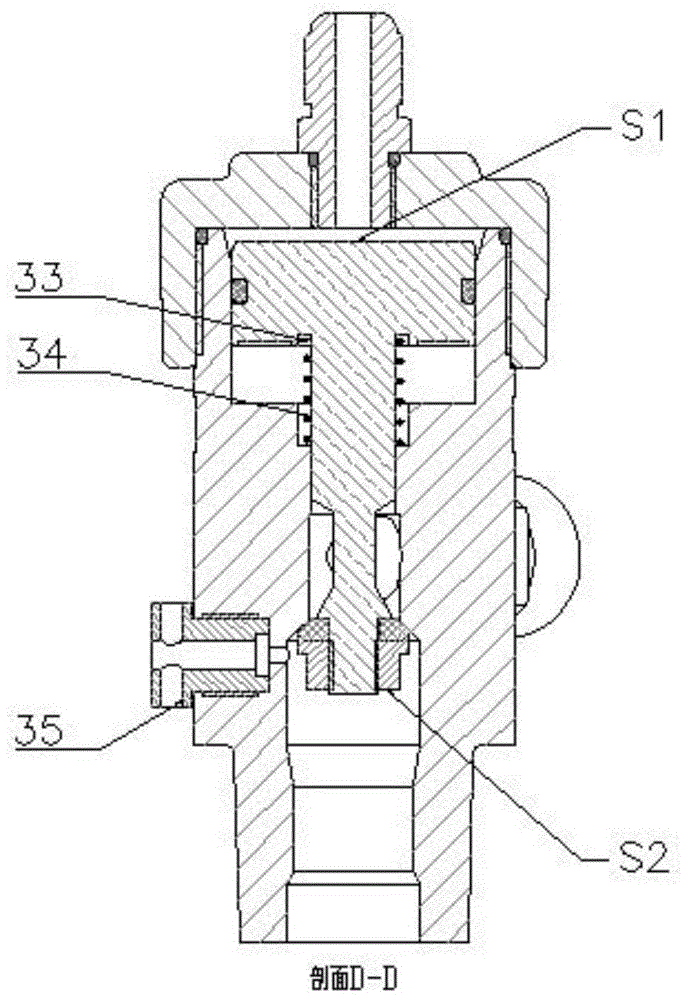
本实用新型属于机械结构技术领域,尤其是涉及一种用于惰性气体灭火系统的气体稳压释放器。
背景技术:
常规惰性气体灭火系统由药剂储气钢瓶、气体释放器、集流管、减压装置、选择阀、管道、喷头及驱动装置等组成。常规惰性气体灭火系统采用一级充压系统,惰性气体灭火剂采用钢瓶存储压力为15mpa@20℃,钢瓶上安装的气体释放器大多为开关式容器阀,结构如图1、图2所示。系统释放过程中,容器阀开启,灭火剂由钢瓶组释放到达集流管,集流管内压力瞬间升高到达释放压力的峰值,然后快速下降。
如图1、图2所示,常规开关式容器阀由阀体1、阀盖2、阀芯3、复位弹簧4、密封锁母5、压力显示器6、阀芯密封圈7、启动器9及置于其内部的撞针8、刺破式启动膜片10等构成,容器阀以钢瓶接口11与药剂储气钢瓶密封连接。当启动器9内的撞针8受气动气压作用向下运动,刺破启动膜片10时,阀芯3中心的气道13导通,储气钢瓶内的气压传导至容器阀上腔14,通过密封圈12,容器阀上、下腔被隔开,而上腔内阀芯3上表面面积大于阀芯3下表面面积及密封锁母5截面积,作用在阀芯3上表面与下表面的压力差大,阀芯3瞬间向下运动,开启容器阀释放通路。待腔体内压力小于复位弹簧的弹簧力4压力时,阀芯3向上运动回到阀门关闭位置。
根据国家实验室研究结果,常规惰性气体灭火系统释放时,管路的压力峰值可达到12mpa以上,随着灭火分区分配的钢瓶数量增加,接近钢瓶的存储工作压力,即15mpa。由于瞬间压力高,流速大,使得后续的灭火药剂释放流量持续性差。高速的释放压力存在诸多问题,例如:集流管的工作压力高,耐压等级高,制造加工工艺要求高;各级管网工作压力高,对管道材料要求高,对施工安装精度要求高;管网计算复杂,对设计计算的要求高等。
为了降低释放管路中的压力,一般在集流管后干管入口处设置孔板减压装置,以减压限流。减压孔板通过节流孔降低灭火剂压力,其功能仅限于将进入干管的灭火剂压力降低,流量减小。国家标准对惰性气体灭火系统喷放时间有严格规定,不能任意减小减压孔板的孔口面积来满足降压需求。以ig541气体灭火系统为例,国家标准要求其喷放至设计用量的95%时,喷放时间不应大于60s且不应小于48s,面对灭火剂释放从开始到峰值再迅速降低,及其剧烈的压力变化,收效不大,虽然经过孔板减压和管道沿程阻力的降压效果,处于保护分区内的管道末端的喷嘴端压力峰值仍高达6mpa。
当系统释放时,保护分区内气压迅速增大并达到高峰值,在此过程中,一旦建筑围挡中门、窗、玻璃等结构损坏,大量的灭火药剂气体泄漏出保护区,而系统释放后期灭火剂气体压力迅速降低,进入保护分区的灭火剂不足,且无法形成足够浓度的灭火药剂对保护区的浸渍条件,而导致灭火失败。
ig541气体灭火系统是一种洁净的惰性混合气体灭火剂,提取自大气,释放后回归大气,理论上是可以用于有人值守保护区域的,但由于常规系统的灭火释放压力的高峰值问题,存在着对人体伤害的安全隐患。在一定程度上限制了ig541气体灭火系统的实际应用。
技术实现要素:
本实用新型要解决的问题是提供一种气体稳压释放器,尤其是结构简单,操作方便,专门适用于惰性气体灭火系统,利用气动自平衡调节原理替代减压装置,从根本上解决了气体灭火系统释放压力峰值高的问题。
为解决上述技术问题,本实用新型采用的技术方案是:一种用于惰性气体灭火系统的气体稳压释放器,包括释放器本体,所述释放器本体纵轴线上设有空腔,所述释放器本体顶部密封设有释放器上盖,所述释放器上盖上设有驱动管路接口,用以与驱动管路密封连接形成密闭通道,使驱动气压进入所述空腔,所述释放器本体底部设有钢瓶接口,用以连接储气钢瓶,所述空腔包括上腔室、中腔室和下腔室,所述空腔内活动设有活塞芯体,所述活塞芯体包括上芯体、中芯体和下芯体,所述上芯体在所述上腔室内滑动,所述上芯体将所述上腔室分为第一上腔室和第二上腔室,所述第一上腔室连通所述驱动管路接口,所述中芯体外表面套装有复位装置置于所述中腔室内,所述下芯体设有锁母密封环,所述下芯体在所述下腔室内运动,实现释放口开合。
进一步的,所述释放口置于所述释放器本体侧面,所述释放口与所述空腔联通。
进一步的,所述空腔呈台阶环状,所述上腔室直径均大于所述中腔室直径和所述下腔室直径,所述中腔室直径小于所述下腔室直径。
进一步的,所述下腔室与所述中腔室连接处为圆锥槽。
进一步的,所述下芯体与所述锁母密封环连接处呈圆锥台,所述圆锥台与所述圆锥槽密封配合。
进一步的,所述复位装置为复位弹簧。
进一步的,所述上芯体底部设有上弹簧凹槽,所述中腔室顶部设有下弹簧凹槽,所述复位弹簧上端置于所述上弹簧凹槽内,所述复位弹簧下端置于所述下弹簧凹槽内。
进一步的,所述释放器本体上设有防爆口,所述防爆口连接防爆装置。
进一步的,所述上芯体上设有o形密封圈,在所述活塞芯体运动过程中,用以密封第一上腔室和第二上腔室。
进一步的,所述释放器本体上设有测压孔,所述测压孔处连接压力显示器。
本实用新型具有的优点和积极效果是:
1、本实用新型通过采用了一种利用气动自平衡调节原理工作的气体稳压释放器,替换传统系统中的开关式容器阀,使整个惰性气体灭火系统中不再需要任何减压装置,在国家标准规定的释放时间内,集流管以及主管道内的压力峰值不高于5mpa,谷值不低于2.5mpa,从根本上解决了常规系统释放压力峰值高的问题,提高了工作效率和安全效率。
2、本实用新型利用工作于其内部第一上腔室的驱动气体压力开启,并与其第二上腔室压力平衡,相互传导并且产生压力差带动活塞芯体做往复运动的原理,具有自调节性能,使储气钢瓶组药剂的释放具有低压稳流特性,可广泛应用于惰性气体灭火系统,应用范围广,实用性强。
3、本实用新型结构简单,操作方便,通过活塞与上腔室、中腔室及下腔室的配合,使释放口的释放压力显著降低,在有效灭火时间内,药剂释放流量持续稳定,灭火效果好,实用性强。
4、本实用新型通过测压孔连接压力显示器,可有效监测释放口的释放压力,便于通过调节驱动气体压力,调节释放口压力,使释放压力平稳,便于药剂释放流量持续稳定。
5、本实用新型通过防爆口连接防爆装置,当储气钢瓶内压力过高时,可通过防爆装置泄压,防止储气钢瓶爆炸,提高了安全性。
附图说明
图1是本实用新型实施例的常规开关式容器阀关闭状态结构示意图。
图2是本实用新型实施例的常规开关式容器阀开启状态结构示意图。
图3是本实用新型实施例的整体结构正视图。
图4是本实用新型实施例的整体结构仰视图。
图5是本实用新型实施例半开状态剖视图。
图6是本实用新型实施例全开状态剖视图。
图7是本实用新型实施例关闭状态剖视图。
图8是本实用新型ig541气体灭火系统使用本实施例低压稳流释放的释放压力曲线实验数据采集图。
图中:
具体实施方式
下面将结合附图对本实用新型的技术方案进行清楚、完整地描述,显然,所描述的实施例是本实用新型一部分实施例,而不是全部的实施例。基于本实用新型中的实施例,本领域普通技术人员在没有做出创造性劳动前提下所获得的所有其他实施例,都属于本实用新型保护的范围。
在本实用新型的描述中,需要说明的是,术语“中心”、“上”、“下”、“左”、“右”、“竖直”、“水平”、“内”、“外”等指示的方位或位置关系为基于附图所示的方位或位置关系,仅是为了便于描述本实用新型和简化描述,而不是指示或暗示所指的装置或元件必须具有特定的方位、以特定的方位构造和操作,因此不能理解为对本实用新型的限制。此外,术语“第一”、“第二”、“第三”仅用于描述目的,而不能理解为指示或暗示相对重要性。
在本实用新型的描述中,需要说明的是,除非另有明确的规定和限定,术语“安装”、“相连”、“连接”应做广义理解,例如,可以是固定连接,也可以是可拆卸连接,或一体地连接;可以是机械连接,也可以是电连接;可以是直接相连,也可以通过中间媒介间接相连,可以是两个元件内部的连通。对于本领域的普通技术人员而言,可以具体情况理解上述术语在本实用新型中的具体含义。
下面结合附图对本实用新型实施例做进一步描述:
如图3、图4所示,一种用于惰性气体灭火系统的气体稳压释放器,包括释放器本体17,释放器本体17纵轴线上设有空腔24。释放器本体17顶部密封设有释放器上盖15,释放器上盖15上设有驱动管路接口19,用以与驱动管路密封连接形成密闭通道,使驱动气压进入空腔24。释放器本体17底部设有钢瓶接口11,用以连接储气钢瓶。如图5-7所示,空腔24包括上腔室25、中腔室26和下腔室27,空腔24内活动设有活塞芯体20,活塞芯体20包括上芯体28、中芯体29和下芯体30。上芯体28在上腔室25内滑动,上芯体28将上腔室25分为第一上腔室31和第二上腔室32,第一上腔室31连通驱动管路接口19。中芯体29外表面套装有复位装置置于中腔室26内,下芯体30连接锁母密封环22,下芯体30在下腔室27内运动,实现释放口16开合。
优选的,上芯体28上设有o形密封圈21,在活塞芯体20运动过程中,用以密封第一上腔室31和第二上腔室32。本实用新型利用工作于其内部第一上腔室31的驱动气体压力开启,并与其第二上腔室32压力平衡,相互传导并且产生压力差带动活塞芯体20做往复运动的原理,具有自调节性能,使储气钢瓶组药剂的释放具有低压稳流特性,可广泛应用于惰性气体灭火系统,应用范围广,实用性强。
上述结构可通过多种方式实现,本实施例提供的释放器本体17上的空腔24呈台阶环状,具体的,上腔室25直径均大于中腔室26直径和下腔室27直径,中腔室26直径小于下腔室27直径。如图5所示,下腔室27与中腔室26连接处为圆锥槽。下芯体30与锁母密封环22连接处呈圆锥台,圆锥台与圆锥槽密封配合。
复位装置为待驱动气体压力取消时,实现上芯体28自动复位的装置,复位装置可为多种结构,具体的,本实施例提供的复位装置为复位弹簧4,如图7所示,上芯体28底部设有上弹簧凹槽33,中腔室26顶部设有下弹簧凹槽34,复位弹簧4上端置于上弹簧凹槽33内,复位弹簧4下端置于下弹簧凹槽34内,便于复位弹簧4固定,防止复位弹簧4错位。
优选的,释放口16置于释放器本体17侧面,释放口16与空腔24联通,通过活塞芯体20的上下运动,实现释放口16的开合。
优选的,释放器本体17上设有防爆口18,防爆口18连接防爆装置35,当储气钢瓶内压力过高时,可通过防爆装置35泄压,防止储气钢瓶爆炸,提高了安全性。
优选的,释放器本体17上设有测压孔23,测压孔23处连接压力显示器6,可有效监测释放口16的释放压力,便于通过调节驱动气体压力,调节释放口16压力,使释放压力平稳,便于药剂释放流量持续稳定。
本实用新型通过采用了一种利用气动自平衡调节原理工作的气体稳压释放器,替换如图1、图2所示的传统系统中的开关式容器阀,使整个惰性气体灭火系统中不再需要任何减压装置,在国家标准规定的释放时间内,集流管以及主管道内的压力峰值不高于5mpa,谷值不低于2.5mpa,从根本上解决了常规系统释放压力峰值高的问题,提高了工作效率和安全效率,如图8所示,为ig541气体灭火系统使用本实施例低压稳流释放的释放压力曲线实验数据采集图。
本实用新型的工作原理是:
释放器本体17底部的钢瓶接口11螺接在储气钢瓶瓶口构成惰性气体药剂储气钢瓶组,释放器上盖15螺接在释放器本体17上与驱动管路密封连接形成密闭通道,活塞芯体20在释放器空腔24中做往复动作。
如图7所示,释放器本体17关闭时,活塞芯体20受向上作用在锁母密封环22及活塞芯体20下表面构成的s2面上的钢瓶储气气压,活塞芯体20的锁母密封环22与释放器本体17内锥面构成密封。当释放器本体17需要启动时,如图5所示,驱动气压由驱动管路接口19进入第一上腔室31,推动活塞芯体20向下动作,开启释放器;此时下腔室27与释放口16导通,释放口16以外连接的是开放管道,故释放口16及下腔室27的压力与释放流量正相关,而释放流量与活塞芯体20与释放器本体17之间形成的孔隙的口径正相关,故达到气动平衡时释放压力p=(p1*s1-ft)*s1,其中,p1为下腔室27内启动压力,s1为活塞芯体20上表面面积,ft为复位弹簧4的弹力。在国标规定的释放有效时间内,由于储气钢瓶内的气量变化是有大到小的,而气动平衡驱动下的释放器开度是由小变大的,最终下腔室27内的压力大于释放口16压力,释放器工作结束时处于全开状态,如图6所示。
当释放器处于关闭状态,活塞芯体20底面受到的储气钢瓶内压缩药剂气体的压力(p2)为储气钢瓶内压强与锁母密封环22的截面积(s2)的乘积;复位弹簧4压紧弹力为ft;活塞芯体20与释放器本体17之间的o形密封圈21造成的滑动摩擦阻力为fz;活塞芯体20上部面积为s1,根据垂直方向受力平衡分析,是活塞芯体20向下运动的启动气压p1应大于p1min,p1min由公式[p1min=(p2*s2+ft+fz)/s1]计算,其中,p1min为最小启动气压。
本实用新型具有的优点和积极效果是:
1、本实用新型通过采用了一种利用气动自平衡调节原理工作的气体稳压释放器,替换传统系统中的开关式容器阀,使整个惰性气体灭火系统中不再需要任何减压装置,在国家标准规定的释放时间内,集流管以及主管道内的压力峰值不高于5mpa,谷值不低于2.5mpa,从根本上解决了常规系统释放压力峰值高的问题,提高了工作效率和安全效率。
2、本实用新型利用工作于其内部第一上腔室的驱动气体压力开启,并与其第二上腔室压力平衡,相互传导并且产生压力差带动活塞芯体做往复运动的原理,具有自调节性能,使储气钢瓶组药剂的释放具有低压稳流特性,可广泛应用于惰性气体灭火系统,应用范围广,实用性强。
3、本实用新型结构简单,操作方便,通过活塞与上腔室、中腔室及下腔室的配合,使释放口的释放压力显著降低,在有效灭火时间内,药剂释放流量持续稳定,灭火效果好,实用性强。
4、本实用新型通过测压孔连接压力显示器,可有效监测释放口的释放压力,便于通过调节驱动气体压力,调节释放口压力,使释放压力平稳,便于药剂释放流量持续稳定。
5、本实用新型通过防爆口连接防爆装置,当储气钢瓶内压力过高时,可通过防爆装置泄压,防止储气钢瓶爆炸,提高了安全性。
以上对本实用新型的一个实施例进行了详细说明,但所述内容仅为本实用新型的较佳实施例,不能被认为用于限定本实用新型的实施范围。凡依本实用新型申请范围所作的均等变化与改进等,均应仍归属于本实用新型的专利涵盖范围之内。
起点商标作为专业知识产权交易平台,可以帮助大家解决很多问题,如果大家想要了解更多知产交易信息请点击 【在线咨询】或添加微信 【19522093243】与客服一对一沟通,为大家解决相关问题。
此文章来源于网络,如有侵权,请联系删除


