烷基黄原酸酯类选矿药剂生产废盐的无害化处理方法与流程



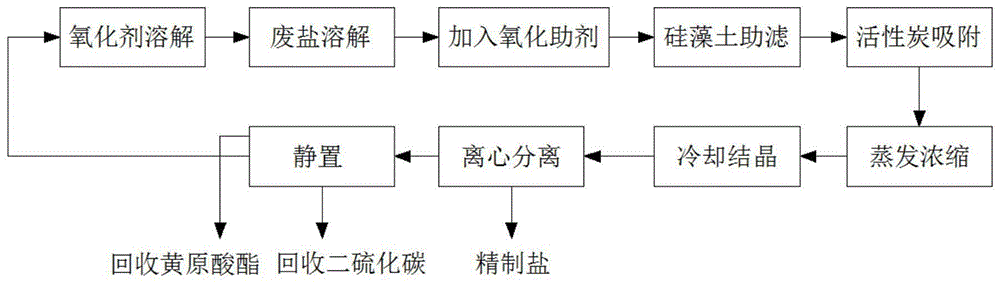
本发明属于工业废盐处理方法技术领域,具体涉及一种烷基黄原酸酯类选矿药剂生产废盐的无害化处理方法。
背景技术:
随着国内环保政策日趋严格,矿山企业对选矿药剂在绿色、低毒、低残留等产品性能方面提出了更高的要求。烷基黄原酸酯是一种新型酯类环保选矿药剂,主要用于有色金属硫化矿的浮选分离,特别是在铜钼硫化矿的浮选应用中选别指标尤为突出,具有选择性高,低毒,低残留,低污染等突出优势。
但该药剂合成中产生的高盐废水却很难进行无害化处理。其中含有微量的刺激性气味副产物及烷基黄药,残存于其废水通过三效蒸发器蒸馏后脱出的固体盐中,致使其盐成为危险废物。为后续环保处理带来很大的问题:一是此盐类中存在较强的刺激性气味;二是此盐类中存在少量的烷基黄药。
技术实现要素:
为了解决上述技术问题,本发明提供一种烷基黄原酸酯类选矿药剂生产废盐的无害化处理方法。
本发明是这样实现的,提供一种烷基黄原酸酯类选矿药剂生产废盐的无害化处理方法,对烷基黄原酸酯类选矿药剂生产废盐进行氧化精制,即:
加热条件下,将烷基黄原酸酯类选矿药剂生产废盐溶解于氧化剂的水溶液,再加入氧化助剂,通过氧化剂及氧化助剂对烷基黄原酸酯类选矿药剂生产废盐进行氧化,然后加入硅藻土成膜过滤,再通过自动过滤机,滤液通过活性炭吸附后进行浓缩、冷却、结晶、离心,得到精制盐。
优选的,上述方法具体包括如下步骤:
1)配制氧化剂水溶液;
2)向步骤1)的氧化剂水溶液中加入烷基黄原酸酯类选矿药剂生产废盐,加热到40-120℃,搅拌至完全溶解,制成饱和盐水;
3)向步骤2)中的饱和盐水中加入氧化助剂,并搅拌30-150分钟;
4)将步骤3)得到的液体泵入保温的混料釜中,并在搅拌状态下将一定质量的硅藻土加入液体中进行混合;
5)将步骤4)混合好的物料导入自动过滤机,进行过滤;
6)将过滤后的滤液通过活性炭吸附,然后泵入三效蒸发器进行浓缩;
7)将浓缩液导入结晶釜中进行冷却结晶;
8)将结晶后的混合液在搅拌状态下引入离心机进行离心分离,得到精制盐;
9)将离心分离后得到的液体静置,回收黄原酸酯和二硫化碳,剩下的液体再次应用于制备步骤1)中的氧化剂水溶液,无须进行水处理。
进一步优选,步骤1)中,氧化剂水溶液的浓度为1-5%。
进一步优选,步骤1)中,所述氧化剂为强氧化剂,为二氧化氯、高锰酸钾、次氯酸钾、次氯酸钠、双氧水中的一种。
进一步优选,步骤3)中,氧化助剂为盐酸、磷酸、硫酸中的一种。
进一步优选,盐酸、磷酸、硫酸的浓度均为10-15%。
进一步优选,所述氧化助剂的添加量为所述氧化剂摩尔质量的1-3%。
进一步优选,步骤4)中,硅藻土的质量为20-100公斤,粒度为100-300目。
进一步优选,步骤8)中,得到的精制盐用做离子膜烧碱和纯碱的生产原料。
与现有技术相比,本发明的优点在于:
对烷基黄原酸酯类选矿药剂生产废盐进行环保处理,工艺流程简单易操作、反应条件温和、处理成本低,而且经处理后的盐可以作为离子膜烧碱和纯碱的生产原料,实现一定的经济效益,生成的废水可以再利用溶解氧化剂,无新的废水产生。
附图说明
图1为本发明工艺流程图。
具体实施方式
为了使本发明的目的、技术方案及优点更加清楚明白,以下结合附图和实施例,对本发明进行进一步详细说明。应当理解,此处所描述的具体实施例仅用以解释本发明,并不用于限定本发明。
参考图1,为了对烷基黄原酸酯类选矿药剂生产废盐进行无害化处理,本发明提供一种处理方法,加热条件下,将烷基黄原酸酯类选矿药剂生产废盐溶解于氧化剂的水溶液,再加入氧化助剂,通过氧化剂及氧化助剂对烷基黄原酸酯类选矿药剂生产废盐进行氧化,然后加入硅藻土成膜过滤,再通过自动过滤机,滤液通过活性炭吸附后进行浓缩、冷却、结晶、离心,得到精制盐,本方法重点在于:
1、本发明的烷基黄原酸酯类选矿药剂生产废盐的无害化处理工艺,要点一在于应用强氧化剂进行氧化;
2、本发明要点二在于应用氧化助剂进行催化反应;
3、本发明要点三在于应用硅藻土进行辅助过滤;
4、得到的精制盐可与离子膜用盐配伍,作为离子膜烧碱的使用原料,因为生产过程中全程无镁及钙引入,所以无须除镁除钙。
实施例1、
1)在反应釜中配制1%的二氧化氯水溶液1800公斤;
2)向步骤1)中加入烷基黄原酸酯废盐700kg,加热到40-90℃,搅拌至完全溶解,制成饱和盐水;
3)在搅拌状态下向步骤2)中缓慢滴入氧化助剂15%盐酸,加入量大约为二氧化氯摩尔质量的1-3%,并搅拌30-150分钟;
4)将步骤3)得到的液体泵入带夹套保温的混料釜中,并在搅拌状态下将20-100公斤100-300目的硅藻土加入液体中进行混合;
5)将混合好的物料导入自动过滤机,进行过滤;
6)将过滤后的滤液通过活性炭吸附后泵入三效蒸发器中进行浓缩;
7)将浓缩液降温到20℃以下进行冷却结晶;
8)将析出结晶后的混合液在搅拌状态下引入离心机进行离心分离;
9)将离心分离后得到的液体静置三天以上,分出上层及下层有机相;
10)将步骤9)得到的上层有机相回收后并入黄原酸酯产品中,下层有机相回收后可用于再生产烷基黄药,中层的水相用于再配制二氧化氯水溶液;
11)离心分离后得到的盐用做离子膜烧碱和纯碱的生产原料;
12)重复步骤1)-9),但步骤2)中加入废盐的量要减至350公斤,循环往复。
实施例2、
1)在反应釜中配制2%的双氧水溶液1800公斤;
2)向步骤1)中加入烷基黄原酸酯废盐700kg,加热到50-90℃,搅拌至完全溶解,制成饱和盐水;
3)在搅拌状态下向步骤2)中缓慢滴入氧化助剂14%盐酸,加入量为双氧水摩尔质量的1-3%,并搅拌30-150分钟;
4)将步骤3)得到的液体泵入带夹套保温的混料釜中,并在搅拌状态下将20-100公斤100-300目的硅藻土加入液体中进行混合;
5)将混合好的物料导入自动过滤机,进行过滤;
6)将过滤后的滤液通过活性炭吸附后泵入三效蒸发器中进行浓缩;
7)将浓缩液降温到20℃以下进行冷却结晶;
8)将析出结晶后的混合液在搅拌状态下引入离心机进行离心分离;
9)将离心分离后得到的液体静置三天以上,分出上层及下层有机相;
10)将步骤9)得到的上层有机相回收后并入黄原酸酯产品中,下层有机相回收后可用于再生产烷基黄药,中层的水相用于再配制双氧水溶液;
11)离心分离后得到的盐用做离子膜烧碱和纯碱的生产原料;
12)重复步骤1)-9),但步骤2)中加入废盐的量要减至350公斤,循环往复。
实施例3、
1)在反应釜中配制3%的次氯酸钠水溶液1800公斤;
2)向步骤1)中加入烷基黄原酸酯废盐700kg,加热到40-90℃,搅拌至完全溶解,制成饱和盐水;
3)在搅拌状态下向步骤2)中缓慢滴入氧化助剂13%盐酸,加入量为次氯酸钠摩尔质量的1-3%,并搅拌30-150分钟;
4)将步骤3)得到的液体泵入带夹套保温的混料釜中,并在搅拌状态下将20-100公斤100-300目的硅藻土加入液体中进行混合;
5)将混合好的物料导入自动过滤机,进行过滤;
6)将过滤后的滤液通过活性炭吸附后泵入三效蒸发器中进行浓缩;
7)将浓缩液降温到20℃以下进行冷却结晶;
8)将析出结晶后的混合液在搅拌状态下引入离心机进行离心分离;
9)将离心分离后得到的液体静置三天以上,分出上层及下层有机相;
10)将步骤9)得到的上层有机相回收后并入黄原酸酯产品中,下层有机相回收后可用于再生产烷基黄药,中层的水相用于再配制次氯酸钠水溶液;
11)离心分离后得到的盐可以用做离子膜烧碱和纯碱的生产原料;
12)重复步骤1)-9),但步骤2)中加入废盐的量要减至350公斤,循环往复。
实施例4、
1)在反应釜中配制4%的次氯酸钾水溶液1800公斤;
2)向步骤1)中加入烷基黄原酸酯废盐700kg,加热到50-90℃,搅拌至完全溶解,制成饱和盐水;
3)在搅拌状态下向步骤2)中缓慢滴入氧化助剂12%盐酸,加入量大约为次氯酸钾摩尔质量的1-3%,并搅拌30-150分钟;
4)将步骤3)得到的液体泵入带夹套保温的混料釜中,并在搅拌状态下将20-100公斤100-300目的硅藻土加入液体中进行混合;
5)将混合好的物料导入自动过滤机,进行过滤;
6)将过滤后的滤液通过活性炭吸附后泵入三效蒸发器中进行浓缩;
7)将浓缩液降温到20℃以下进行冷却结晶;
8)将析出结晶后的混合液在搅拌状态下引入离心机进行离心分离;
9)将离心分离后得到的液体静置三天以上,分出上层及下层有机相;
10)将步骤9)得到的上层有机相回收后并入黄原酸酯产品中,下层有机相回收后可用于再生产烷基黄药。中层的水相用于再配制次氯酸钾水溶液;
11)离心分离后得到的盐可以用做离子膜烧碱和纯碱的生产原料;
12)重复步骤1)-9),但步骤2)中加入废盐的量要减至350公斤,循环往复。
实施例5、
1)在反应釜中配制5%的高锰酸钾水溶液1800公斤;
2)向步骤1)中加入烷基黄原酸酯废盐700kg,加热到50-90℃,搅拌至完全溶解,制成饱和盐水;
3)在搅拌状态下向步骤2)中缓慢滴入氧化助剂11%盐酸,加入量大约为高锰酸钾摩尔质量的1-3%,并搅拌30-150分钟;
4)将步骤3)得到的液体泵入带夹套保温的混料釜中,并在搅拌状态下将20-100公斤100-300目的硅藻土加入液体中进行混合;
5)将混合好的物料导入自动过滤机,进行过滤;
6)将过滤后的滤液通过活性炭吸附后泵入三效蒸发器中进行浓缩;
7)将浓缩液降温到20℃以下进行冷却结晶;
8)将析出结晶后的混合液在搅拌状态下引入离心机进行离心分离;
9)将离心分离后得到的液体静置三天以上,分出上层及下层有机相;
10)将9)得到的上层有机相回收后并入黄原酸酯产品中,下层有机相回收后可用于再生产烷基黄药。中层的水相用于再配制高锰酸钾水溶液;
11)离心分离后得到的盐可以用做离子膜烧碱和纯碱的生产原料;
12)重复步骤1)-9),但步骤2)中加入废盐的量要减至350公斤,循环往复。
实施例6、
1)在反应釜中配制5%的二氧化氯水溶液1800公斤;
2)向步骤1)中加入烷基黄原酸酯废盐700kg,加热到40-90℃,搅拌至完全溶解,制成饱和盐水;
3)在搅拌状态下向步骤2)中缓慢滴入氧化助剂10%磷酸,加入量大约为二氧化氯摩尔质量的1-3%,并搅拌30-150分钟;
4)将步骤3)得到的液体泵入带夹套保温的混料釜中,并在搅拌状态下将20-100公斤100-300目的硅藻土加入液体中进行混合;
5)将混合好的物料导入自动过滤机,进行过滤;
6)将过滤后的滤液通过活性炭吸附后泵入三效蒸发器中进行浓缩;
7)将浓缩液降温到20℃以下进行冷却结晶;
8)将析出结晶后的混合液在搅拌状态下引入离心机进行离心分离;
9)将离心分离后得到的液体静置三天以上,分出上层及下层有机相;
10)将步骤9)得到的上层有机相回收后并入黄原酸酯产品中,下层有机相回收后可用于再生产烷基黄药。中层的水相用于再配制二氧化氯水溶液;
11)离心分离后得到的盐可以用做离子膜烧碱和纯碱的生产原料;
12)重复步骤1)-9),但步骤2)中加入废盐的量要减至350公斤,循环往复。
实施例7、
1)在反应釜中配制1%的双氧水溶液1800公斤;
2)向步骤1)中加入烷基黄原酸酯废盐700kg,加热到50-90℃,搅拌至完全溶解,制成饱和盐水;
3)在搅拌状态下向步骤2)中缓慢滴入氧化助剂15%磷酸,加入量大约为双氧水摩尔质量的1-3%并搅拌30-150分钟;
4)将步骤3)得到的液体泵入带夹套保温的混料釜中,并在搅拌状态下将20-100公斤100-300目的硅藻土加入液体中进行混合;
5)将混合好的物料导入自动过滤机,进行过滤;
6)将过滤后的滤液通过活性炭吸附后泵入三效蒸发器中进行浓缩;
7)将浓缩液降温到20℃以下进行冷却结晶;
8)将析出结晶后的混合液在搅拌状态下引入离心机进行离心分离;
9)将离心分离后得到的液体静置三天以上,分出上层及下层有机相;
10)将步骤9)得到的上层有机相回收后并入黄原酸酯产品中,下层有机相回收后可用于再生产烷基黄药。中层的水相用于再配制双氧水溶液;
11)离心分离后得到的盐可以用做离子膜烧碱和纯碱的生产原料;
12)重复步骤1)-9),但步骤2)中加入废盐的量要减至350公斤,循环往复。
实施例8、
1)在反应釜中配制2%的次氯酸钠水溶液1800公斤;
2)向步骤1)中加入烷基黄原酸酯废盐700kg,加热到40-90℃,搅拌至完全溶解,制成饱和盐水;
3)在搅拌状态下向步骤2)中缓慢滴入氧化助剂14%磷酸,加入量大约为次氯酸钠摩尔质量的1-3%,并搅拌30-150分钟;
4)将步骤3)得到的液体泵入带夹套保温的混料釜中,并在搅拌状态下将20-100公斤100-300目的硅藻土加入液体中进行混合;
5)将混合好的物料导入自动过滤机,进行过滤;
6)将过滤后的滤液通过活性炭吸附后泵入三效蒸发器中进行浓缩;
7)将浓缩液降温到20℃以下进行冷却结晶;
8)将析出结晶后的混合液在搅拌状态下引入离心机进行离心分离;
9)将离心分离后得到的液体静置三天以上,分出上层及下层有机相;
10)将步骤9)得到的上层有机相回收后并入黄原酸酯产品中,下层有机相回收后可用于再生产烷基黄药。中层的水相用于再配制次氯酸钠水溶液;
11)离心分离后得到的盐可以用做离子膜烧碱和纯碱的生产原料;
12)重复步骤1)-9),但步骤2)中加入废盐的量要减至350公斤,循环往复。
实施例9、
1)在反应釜中配制3%的次氯酸钾水溶液1800公斤;
2)向步骤1)中加入烷基黄原酸酯废盐700kg,加热到50-90℃,搅拌至完全溶解,制成饱和盐水;
3)在搅拌状态下向2)中缓慢滴入氧化助剂13%磷酸,加入量大约为次氯酸钾摩尔质量的1-3%,并搅拌30-150分钟;
4)将3)得到的液体泵入带夹套保温的混料釜中,并在搅拌状态下将20-100公斤100-300目的硅藻土加入液体中进行混合;
5)将混合好的物料导入自动过滤机,进行过滤;
6)将过滤后的滤液通过活性炭吸附后泵入三效蒸发器中进行浓缩;
7)将浓缩液降温到20℃以下进行冷却结晶;
8)将析出结晶后的混合液在搅拌状态下引入离心机进行离心分离;
9)将离心分离后得到的液体静置三天以上,分出上层及下层有机相;
10)将9)得到的上层有机相回收后并入黄原酸酯产品中,下层有机相回收后可用于再生产烷基黄药。中层的水相用于再配制次氯酸钾水溶液;
11)离心分离后得到的盐可以用做离子膜烧碱和纯碱的生产原料;
12)重复步骤1)-9),但步骤2)中加入废盐的量要减至350公斤,循环往复。
实施例10、
1)在反应釜中配制4%的高锰酸钾水溶液1800公斤;
2)向步骤1)中加入烷基黄原酸酯废盐700kg,加热到50-90℃,搅拌至完全溶解,制成饱和盐水;
3)在搅拌状态下向步骤2)中缓慢滴入氧化助剂12%磷酸,加入量大约为高锰酸钾摩尔质量的1-3%,并搅拌30-150分钟;
4)将步骤3)得到的液体泵入带夹套保温的混料釜中,并在搅拌状态下将20-100公斤100-300目的硅藻土加入液体中进行混合;
5)将混合好的物料导入自动过滤机,进行过滤;
6)将过滤后的滤液通过活性炭吸附后泵入三效蒸发器中进行浓缩;
7)将浓缩液降温到20℃以下进行冷却结晶;
8)将析出结晶后的混合液在搅拌状态下引入离心机进行离心分离;
9)将离心分离后得到的液体静置三天以上,分出上层及下层有机相;
10)将步骤9)得到的上层有机相回收后并入黄原酸酯产品中,下层有机相回收后可用于再生产烷基黄药。中层的水相用于再配制高锰酸钾水溶液;
11)离心分离后得到的盐可以用做离子膜烧碱和纯碱的生产原料;
12)重复步骤1)-9),但步骤2)中加入废盐的量要减至350公斤,循环往复。
实施例11、
1)在反应釜中配制5%的二氧化氯水溶液1800公斤;
2)向步骤1)中加入烷基黄原酸酯废盐700kg,加热到40-90℃,搅拌至完全溶解,制成饱和盐水;
3)在搅拌状态下向步骤2)中缓慢滴入氧化助剂11%硫酸,加入量大约为二氧化氯摩尔质量的1-3%,并搅拌30-150分钟;
4)将步骤3)得到的液体泵入带夹套保温的混料釜中,并在搅拌状态下将20-100公斤100-300目的硅藻土加入液体中进行混合;
5)将混合好的物料导入自动过滤机,进行过滤;
6)将过滤后的滤液通过活性炭吸附后泵入三效蒸发器中进行浓缩;
7)将浓缩液降温到20℃以下进行冷却结晶;
8)将析出结晶后的混合液在搅拌状态下引入离心机进行离心分离;
9)将离心分离后得到的液体静置三天以上,分出上层及下层有机相;
10)将步骤9)得到的上层有机相回收后并入黄原酸酯产品中,下层有机相回收后可用于再生产烷基黄药。中层的水相用于再配制二氧化氯水溶液;
11)离心分离后得到的盐可以用做离子膜烧碱和纯碱的生产原料;
12)重复步骤1)-9),但步骤2)中加入废盐的量要减至350公斤,循环往复。
实施例12、
1)在反应釜中配制1%的双氧水溶液1800公斤;
2)向步骤1)中加入烷基黄原酸酯废盐700kg,加热到50-90℃,搅拌至完全溶解,制成饱和盐水;
3)在搅拌状态下向步骤2)中缓慢滴入氧化助剂10%硫酸,加入量大约为双氧水摩尔质量的1-3%并搅拌30-150分钟;
4)将步骤3)得到的液体泵入带夹套保温的混料釜中,并在搅拌状态下将20-100公斤100-300目的硅藻土加入液体中进行混合;
5)将混合好的物料导入自动过滤机,进行过滤;
6)将过滤后的滤液通过活性炭吸附后泵入三效蒸发器中进行浓缩;
7)将浓缩液降温到20℃以下进行冷却结晶;
8)将析出结晶后的混合液在搅拌状态下引入离心机进行离心分离;
9)将离心分离后得到的液体静置三天以上,分出上层及下层有机相;
10)将步骤9)得到的上层有机相回收后并入黄原酸酯产品中,下层有机相回收后可用于再生产烷基黄药。中层的水相用于再配制双氧水溶液;
11)离心分离后得到的盐可以用做离子膜烧碱和纯碱的生产原料;
12)重复步骤1)-9),但步骤2)中加入废盐的量要减至350公斤,循环往复。
实施例13、
1)在反应釜中配制1%的次氯酸钠水溶液1800公斤;
2)向步骤1)中加入烷基黄原酸酯废盐700kg,加热到40-90℃,搅拌至完全溶解,制成饱和盐水;
3)在搅拌状态下向步骤2)中缓慢滴入氧化助剂15%硫酸,加入量大约为次氯酸钠摩尔质量的1-3%,并搅拌30-150分钟;
4)将步骤3)得到的液体泵入带夹套保温的混料釜中,并在搅拌状态下将20-100公斤100-300目的硅藻土加入液体中进行混合;
5)将混合好的物料导入自动过滤机,进行过滤;
6)将过滤后的滤液通过活性炭吸附后泵入三效蒸发器中进行浓缩;
7)将浓缩液降温到20℃以下进行冷却结晶;
8)将析出结晶后的混合液在搅拌状态下引入离心机进行离心分离;
9)将离心分离后得到的液体静置三天以上,分出上层及下层有机相;
10)将步骤9)得到的上层有机相回收后并入黄原酸酯产品中,下层有机相回收后可用于再生产烷基黄药。中层的水相用于再配制次氯酸钠水溶液;
11)离心分离后得到的盐可以用做离子膜烧碱和纯碱的生产原料;
12)重复步骤1)-9),但步骤2)中加入废盐的量要减至350公斤,循环往复。
实施例14、
1)在反应釜中配制2%的次氯酸钾水溶液1800公斤;
2)向1)中加入烷基黄原酸酯废盐700kg,加热到50-90℃,搅拌至完全溶解,制成饱和盐水;
3)在搅拌状态下向2)中缓慢滴入氧化助剂14%硫酸,加入量大约为次氯酸钾摩尔质量的1-3%,并搅拌30-150分钟;
4)将步骤3)得到的液体泵入带夹套保温的混料釜中,并在搅拌状态下将20-100公斤100-300目的硅藻土加入液体中进行混合;
5)将混合好的物料导入自动过滤机,进行过滤;
6)将过滤后的滤液通过活性炭吸附后泵入三效蒸发器中进行浓缩;
7)将浓缩液降温到20℃以下进行冷却结晶;
8)将析出结晶后的混合液在搅拌状态下引入离心机进行离心分离;
9)将离心分离后得到的液体静置三天以上,分出上层及下层有机相;
10)将步骤9)得到的上层有机相回收后并入黄原酸酯产品中,下层有机相回收后可用于再生产烷基黄药。中层的水相用于再配制次氯酸钾水溶液;
11)离心分离后得到的盐可以用做离子膜烧碱和纯碱的生产原料;
12)重复步骤1)-9),但步骤2)中加入废盐的量要减至350公斤,循环往复。
实施例15、
1)在反应釜中配制3%的高锰酸钾水溶液1800公斤;
2)向步骤1)中加入烷基黄原酸酯废盐700kg,加热到50-90℃,搅拌至完全溶解,制成饱和盐水;
3)在搅拌状态下向步骤2)中缓慢滴入氧化助剂13%硫酸,加入量大约为高锰酸钾摩尔质量的1-3%,并搅拌30-150分钟;
4)将步骤3)得到的液体泵入带夹套保温的混料釜中,并在搅拌状态下将20-100公斤100-300目的硅藻土加入液体中进行混合;
5)将混合好的物料导入自动过滤机,进行过滤;
6)将过滤后的滤液通过活性炭吸附后泵入三效蒸发器中进行浓缩;
7)将浓缩液降温到20℃以下进行冷却结晶;
8)将析出结晶后的混合液在搅拌状态下引入离心机进行离心分离;
9)将离心分离后得到的液体静置三天以上,分出上层及下层有机相;
10)将步骤9)得到的上层有机相回收后并入黄原酸酯产品中,下层有机相回收后可用于再生产烷基黄药。中层的水相用于再配制高锰酸钾水溶液;
11)离心分离后得到的盐可以用做离子膜烧碱和纯碱的生产原料;
12)重复步骤1)-9),但步骤2)中加入废盐的量要减至350公斤,循环往复。
对实施例1-5处理前、处理后的烷基黄原酸酯废盐进行检测,具体数据如下两表格所示,从结果中看出,通过本发明的方法,处理后的盐已经检测不到黄原酸酯浸出和黄原酸钠浸出,外观从处理前的橘黄色、刺激性气味变成了白色、无味,证明了本发明提供的方法的有效性。
起点商标作为专业知识产权交易平台,可以帮助大家解决很多问题,如果大家想要了解更多知产交易信息请点击 【在线咨询】或添加微信 【19522093243】与客服一对一沟通,为大家解决相关问题。
此文章来源于网络,如有侵权,请联系删除


