一种通过质心位置调节进行自动翻转的十吨级液相材料装填壳体的制作方法



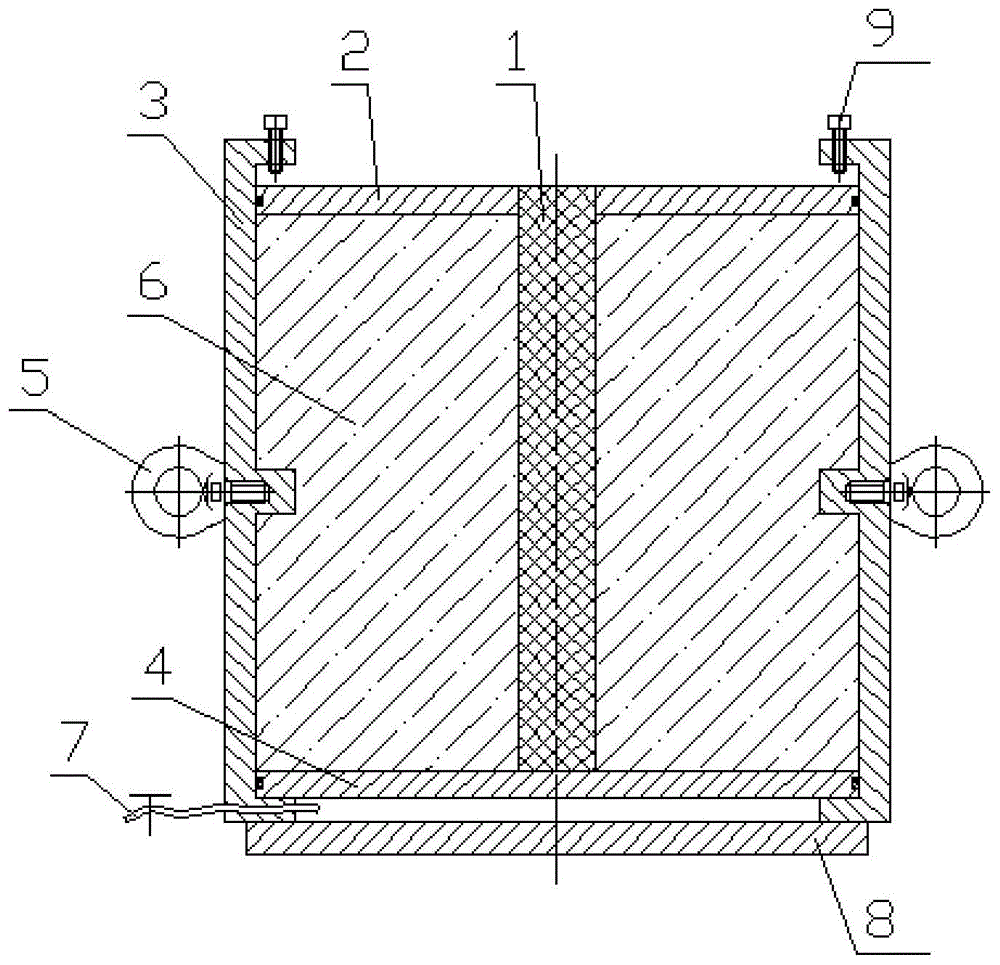
本发明属于液相材料装填壳体
技术领域:
,涉及一种十吨级液相材料装填壳体,特别涉及一种通过质心位置调节进行自动翻转的十吨级液相材料装填壳体。
背景技术:
:爆炸水雾除尘弹及灭火弹内部均装填有液相材料,通过抛撒炸药的爆炸驱动加载作用,液相材料被抛撒到空气中,形成一定空间覆盖范围的云团,爆炸水雾除尘弹及灭火弹的效果,随着抛撒云团直径的增加而增大。为了提高液相材料抛撒形成云团的直径,爆炸水雾除尘弹及灭火弹通常设计为薄壁壳体结构,抛撒炸药爆炸后释放的能量尽可能少的用在壳体破裂上,尽可能多的对液相材料驱动加载做功,进而提高液相材料抛撒速度,提高抛撒云团直径。因此,爆炸水雾除尘弹及灭火弹的宏观结构为装填液相材料的薄壁壳体结构。对于装填液相材料的薄壁壳体,其长径比对抛撒形成云团的形态有较大影响。惠君明等人在文献“fae装置参数对燃料抛撒与爆炸威力影响的实验研究”(高压物理学报,2004年6月,第18卷第2期105页)中报道:对于装填液相材料的圆柱形薄壁壳体,当长径比选择较恰当时,通过炸药抛撒形成的云团形状更理想,云团浓度分布更均匀,通过综合考察,长径比为3~5较好,装填液相材料的薄壁壳体的尺寸设计可在此范围内选择。随着装填液相材料的薄壁壳体相关产品的发展,液相材料的装填体积越来越大,装填液相材料的薄壁壳体的总重量随之增大,目前该类产品的重量已经发展至十吨级。十吨级装填液相材料的薄壁壳体直径约为2米,长度约为8米。运输时,为了运输平稳,壳体采用躺下姿态,轴线与水平面平行。往薄壁壳体内部装填液相材料时,为了装填时壳体稳固及装满,壳体采用起立姿态,轴线与水平面垂直。而该产品使用时,为了提高抛撒云团的覆盖范围,壳体采用起立姿态,轴线与水平面垂直。因此,装填液相材料的薄壁壳体在装填液体、运输和使用时,需要反复进行从躺下到起立的循环翻转工作。十吨级壳体的翻转单纯人力操作无法完成,必须依靠相应辅助装配机械支持设备才能安全、可靠并高效地进行。张玉美等人在文献“多自由度翻转车在卫星装配中的应用”(机械制造,2018年8月,第56卷第648期89页)中报道了一种多自由度翻转车,由推杆、翻转框架和适配器组成,通过推杆的伸缩及摆动带动适配器翻转,可以满足适配器0~90°的翻转。该翻转车对壳体的翻转过程为:将壳体固定在翻转车上,壳体外壁通过若干个点与翻转车连接,通过翻转车对壳体施加翻转力矩,使得壳体发生空间翻转运动,最终完成翻转工作。但是由该翻转车对十吨级装填液相材料的薄壁壳体进行翻转时,出现了以下问题:翻转车在完成壳体的空间翻转工作时,只能保证壳体翻转至需要的角度,对壳体翻转过程的速度无法做到精确控制,壳体的翻转开始和结束阶段速度存在较大突变,由于壳体重量高达十吨级,翻转过程中速度的突变会带来极大的惯性载荷,而翻转车和壳体只是通过若干个点固定连接,极大的惯性载荷作用在这几个点上,每个点承受的力均很大,而壳体为薄壁壳体,外部作用力过大会导致壳体强度不足和破坏,进而导致内部液相材料泄漏,导致装填液相材料的薄壁壳体失效。技术实现要素:为了克服现有技术的不足和缺陷,本发明提供一种通过质心位置调节进行自动翻转的十吨级液相材料装填壳体,本发明通过调节壳体质心位置,使得壳体的空间姿态随着质心的变化进行自适应调整,逐渐完成从躺下姿态到起立姿态,或从起立姿态到躺下姿态的翻转工作。壳体翻转过程速度均匀且缓慢,避免了过大动载荷,保证了壳体强度不受破坏,进而保证了产品的安全性和可靠性。本发明提供的一种通过质心位置调节进行自动翻转的十吨级液相材料装填壳体,包括抛撒管1,上端盖2,下端盖4,液体6,其特征在于还包括壳体3,吊环5,充气管7,临时挡板8,定位螺钉9;抛撒管1为第一圆柱体,抛撒管1的第一圆柱体为回转体,抛撒管1的第一圆柱体的上端面为第一上端圆平面,抛撒管1的第一圆柱体的侧面为第一外圆柱面,抛撒管1的第一圆柱体的下端面为第一下端圆平面;抛撒管1的回转体轴线与水平面垂直,抛撒管1的内部装有炸药,抛撒管1内部的炸药为抛撒液相材料形成云团的能量源;上端盖2为第二圆板,上端盖2的第二圆板为回转体,上端盖2的第二圆板中心带有第二圆孔,上端盖2的第二圆板的上端面为第二上端同心圆平面,上端盖2的第二圆板的外侧面为第二外圆柱面,上端盖2的第二圆板的下端面为第二下端同心圆平面,上端盖2的第二圆孔的内侧面为第二内圆柱面;上端盖2的回转体轴线与抛撒管1的回转体轴线重合,上端盖2位于抛撒管1上端外部,上端盖2的第二内圆柱面与抛撒管1的第一外圆柱面上端接触,上端盖2的第二上端同心圆平面与抛撒管1的第一上端圆平面共面;壳体3为第三圆筒体,壳体3的第三圆筒体为回转体,壳体3的第三圆筒体的外侧面为第三外圆柱面,壳体3的第三圆筒体的内侧面为第三内圆柱面,壳体3的第三圆筒体上端内侧带有第三上端内法兰,壳体3的第三上端内法兰下端面为第三上端向下同心圆环面,壳体3的第三上端内法兰上带有十六个第三螺纹通孔,壳体3的十六个第三螺纹通孔轴线与壳体3的回转体轴线平行,壳体3的十六个第三螺纹通孔绕壳体3的回转体轴线均匀分布,壳体3的第三圆筒体下端内侧带有第三下端内法兰,壳体3的第三下端内法兰上端面为第三下端向上同心圆环面,壳体3的第三下端内法兰下端面为第三下端向下同心圆环面,壳体3的第三下端内法兰的内侧面为第三下端内圆柱面,壳体3的第三下端内法兰上带有一个第三圆形通孔,壳体3的第三圆形通孔轴线与壳体3的回转体轴线垂直,壳体3的第三内圆柱面中部带有第三环形凸台,壳体3的第三外圆柱面中部带有两个第三螺纹盲孔,壳体3的两个第三螺纹盲孔的轴线均垂直于壳体3的回转体轴线;壳体3的回转体轴线与抛撒管1的回转体轴线重合,上端盖2的第二圆板位于壳体3的第三圆筒体内部,上端盖2的第二上端圆平面位于壳体3的第三上端向下同心圆环面下端,壳体3的第三内圆柱面与上端盖2的第二外圆柱面滑动配合接触;下端盖4为第四圆板,下端盖4的第四圆板为回转体,下端盖4的第四圆板的上端面为第四上端圆平面,下端盖4的第四圆板的外侧面为第四外圆柱面,下端盖4的第四圆板的下端面为第四下端圆平面;下端盖4的回转体轴线与抛撒管1的回转体轴线重合,下端盖4的第四上端圆平面与抛撒管1的第一下端圆平面连接,下端盖4的第四圆板位于壳体3的第三圆筒体内部,下端盖4的第四下端圆平面位于壳体3的第三下端向上同心圆环面上端,壳体3的第三内圆柱面与下端盖4的第四外圆柱面滑动配合接触;吊环5由左右两部分组成,吊环5的右部分为第五圆柱体,吊环5的第五圆柱体为回转体,吊环5的第五圆柱体的侧面带有第五外螺纹,吊环5的左部分为第五圆环体,吊环5的第五圆柱体和吊环5的第五圆环体转动配合连接,吊环5共两个;吊环5的第五圆柱体的回转体轴线与抛撒管1的回转体轴线垂直,吊环5的第五外螺纹安装在壳体3的第三螺纹盲孔中;液体6为被炸药抛撒后形成云团的液相材料;液体6位于抛撒管1的第一外圆柱面、上端盖2的第二下端同心圆平面、壳体3的第三内圆柱面和下端盖4的第四上端圆平面组成的封闭空间中;充气管7为第七圆管,充气管7的第七圆管为回转体,充气管7的第七圆管左端带有第七开关;充气管7的回转体轴线与抛撒管1的回转体轴线垂直,充气管7的第七圆管右端与壳体3的第三圆形通孔连接;临时挡板8为第八圆板,临时挡板8的第八圆板为回转体,临时挡板8的第八圆板的上端面为第八上端圆平面;临时挡板8的回转体轴线与抛撒管1的回转体轴线重合,临时挡板8位于壳体3下端,临时挡板8的第八上端圆平面与壳体3的第三下端向下同心圆环面连接;定位螺钉9为第九圆柱体,定位螺钉9的第九圆柱体为回转体,定位螺钉9的第九圆柱体的侧面为第九外圆柱面,定位螺钉9的第九外圆柱面下端带有第九外螺纹,定位螺钉9共十六个;定位螺钉9的回转体轴线与抛撒管1的回转体轴线平行,定位螺钉9的第九外螺纹安装在壳体3的第三螺纹通孔中。上端盖2的第二外圆柱面的轴向长度与上端盖2的第二圆板直径之比为1:9~10;下端盖4的第四外圆柱面的轴向长度与下端盖4的第四圆板直径之比为1:9~10;壳体3的两个第三螺纹盲孔的轴线位于同一水平面,壳体3的两个第三螺纹盲孔的轴线的夹角为176°~178°;壳体3的两个第三螺纹盲孔的轴线所在平面位于本发明系统质心下端120~140mm,上端盖2的第二上端圆平面与壳体3的第三上端向下同心圆环面平行,上端盖2的第二上端圆平面与壳体3的第三上端向下同心圆环面之间的距离为第一距离,壳体3的两个第三螺纹盲孔的轴线所在平面与本发明系统质心距离为第二距离,第一距离和第二距离相同,下端盖4的第四下端圆平面与壳体3的第三下端向上同心圆环面接触;壳体3的第三环形凸台的上端面距离壳体3的第三螺纹盲孔的轴线距离为壳体3的第三螺纹盲孔公称直径的1.4~1.6倍,壳体3的第三环形凸台的下端面距离壳体3的第三螺纹盲孔的轴线距离为壳体3的第三螺纹盲孔公称直径的1.1~1.3;所述一种通过质心位置调节进行自动翻转的十吨级液相材料装填壳体,包括以下步骤:步骤1:将壳体3放在水平台上,使得壳体3的回转体轴线垂直于水平面;步骤2:将下端盖4与壳体3装配;步骤3:将抛撒管1与壳体3装配;步骤4:将上端盖2与壳体3装配;步骤5:将吊环5与壳体3装配;步骤6:将充气管7与壳体3装配;步骤7:将临时挡板8与壳体3装配;步骤8:将定位螺钉9与壳体3装配,定位螺钉9的下端与壳体3的第三上端向下同心圆环面平齐;步骤9:将液体6灌入抛撒管1的第一外圆柱面、上端盖2的第二下端同心圆平面、壳体3的第三内圆柱面和下端盖4的第四上端圆平面组成的封闭空间中;步骤10:将吊绳穿过吊环5的第五圆环体,再将吊绳挂在吊车上,通过吊车将壳体3吊起,使得临时挡板8与地面脱离;步骤11:将本发明的系统由起立姿态转变为躺下姿态:将充气管7的第七圆管的左端与高压空气泵连接,打开充气管7的第七开关,使高压空气进入下端盖4的第四下端圆平面、壳体3的第三下端内圆柱面和临时挡板8的第八上端圆平面组成的封闭空间中,通过高压气体挤压下端盖4,下端盖4再将压力传递给抛撒管1和液体6,液体6再将压力传递给上端盖2,使得抛撒管1、上端盖2、下端盖4和液体6同时向上移动,本发明的系统质心逐渐上移,本发明系统的姿态随着质心的上移逐渐由起立姿态转变为躺下姿态,待抛撒管1的回转体轴线与水平面平行,关闭充气管7的第七开关,断开充气管7的第七圆管的左端与高压空气泵的连接;步骤12:将本发明的系统由躺下姿态转变为起立姿态:打开充气管7的第七开关,放出下端盖4的第四下端圆平面、壳体3的第三下端内圆柱面和临时挡板8的第八上端圆平面组成的封闭空间中的高压气体,将充气管7的第七圆管的左端与真空泵连接,对下端盖4的第四下端圆平面、壳体3的第三下端内圆柱面和临时挡板8的第八上端圆平面组成的封闭空间进行抽真空,使得下端盖4的第四下端圆平面受到负压,下端盖4再将负压传递给抛撒管1和液体6,液体6再将负压传递给上端盖2,使得抛撒管1、上端盖2、下端盖4和液体6同时向靠近临时挡板8的方向移动,本发明的系统质心逐渐靠近临时挡板8,本发明系统的姿态随着质心的靠近临时挡板8逐渐由躺下姿态转变为起立姿态,待抛撒管1的回转体轴线与水平面垂直,关闭充气管7的第七开关,断开充气管7的第七圆管的左端与真空泵的连接;步骤13:将定位螺钉9拧紧,通过定位螺钉9挤压上端盖2的第二上端同心圆平面,固定上端盖2的位置,使得上端盖2与壳体3不能再发生相对运动,卸下临时挡板8,此时,本发明的系统完成实验前准备。本发明的装置左边放置一个检测装置,检测本发明的装置旋转角速度和角加速度的装置,该检测装置同时与充气管7连接,可以控制充气管7内部气体的流速,当检测装置测得本发明的装置旋转角速度为0.02弧度每秒~0.04弧度每秒时,且测得本发明的装置旋转角加速度不超过0.01弧度每平方秒时,充气管7内部气体的流速不变;当测得本发明的装置旋转角加速度超过0.01弧度每平方秒时,减小充气管7内部气体的流速;当检测本发明的装置测得本发明的装置旋转角速度超过0.04弧度每秒时,减小充气管7内部气体的流速;当测得本发明的装置测得本发明的装置旋转角速度低于0.02弧度每秒时,增加充气管7内部气体的流速;上端盖2的第二外圆柱面和壳体3的第三内圆柱面的基本尺寸相同,上端盖2的第二外圆柱面的尺寸公差等级为d10级,壳体3的第三内圆柱面的尺寸公差等级为h10级;下端盖4的第四外圆柱面和壳体3的第三内圆柱面的基本尺寸相同,下端盖4的第四外圆柱面的尺寸公差等级为d10级,壳体3的第三内圆柱面的尺寸公差等级为h10级。在本发明的装置的左边放置一个检测仪器,该检测仪器可以检测本发明的装置各零件内部内应力,当本发明的装置在旋转过程中,任何一个零件内部内应力达到其母材强度极限的百分之60时,即发生报警;上端盖2的第二外圆柱面上安装两道密封圈,上端盖2的第二外圆柱面的上端的密封圈距上端盖2的第二上端同心圆平面为2mm,上端盖2的第二外圆柱面的下端的密封圈距上端盖2的第二下端同心圆平面为2mm。本发明左边放置一个测试装置,测试装置分别与抛撒管1、下端盖4、充气管7的第七开关连接,测试装置可以检测充气管7内气体的流速,测试装置可以检测抛撒管1和下端盖4的运动速度,当测试装置检测到抛撒管1或下端盖4由运动突然停止时,而充气管7内气体仍有流速,则测试装置立即关闭充气管7的第七开关;壳体3的第三外圆柱面的圆柱度不超过0.09mm。吊环5的第五圆柱体和吊环5的第五圆环体的转动配合连接之处安装一个阻尼装置,该阻尼装置可以限制吊环5的第五圆柱体和吊环5的第五圆环体相对运动速度,使得吊环5的第五圆柱体和吊环5的第五圆环体只能以最大0.02弧度每秒的相对速度进行转动;壳体3的毛坯先用普通车床进行车削加工,装夹壳体3下端,用45度偏刀加工壳体3上端和外圆,再用90度偏刀加工壳体3上端内孔,再装夹壳体3上端,用45度偏刀加工壳体3下端和外圆,再用90度偏刀加工壳体3下端内孔;精车后的壳体3用普通铣床进行铣削加工,用分度头加工壳体3下端,用钻头加工壳体3的十六个第三螺纹通孔的底孔,再用圆盘卡主壳体3上端,用顶尖顶住圆盘,用钻头加工壳体3的第三螺纹盲孔的底孔,再用丝锥加工第三螺纹通孔和第三螺纹盲孔。本发明的装置下边放置一个摩擦力检查装置,摩擦力检查装置可以检测吊环5的第五圆柱体和吊环5的第五圆环体转动配合的摩擦力,当第五圆柱体和吊环5的第五圆环体转动配合的摩擦力低于3000n时,检查装置显示绿色,代表安全,当第五圆柱体和吊环5的第五圆环体转动配合的摩擦力高于3000n时,检查装置显示红色,代表危险;壳体3的母材为45钢,粗加工后,进行淬火处理,淬火温度为880~890℃,待热透后,用水进行冷却,获得马氏体组织,再进行回火,加热至600~620℃,保温2小时,在空气中冷却,获得回火马氏体组织。步骤1:壳体3的毛坯为铸铝,由整体铸造方法铸造成型,放底板,放下箱,将壳体3外表形状相同的模型放在底板上,加沙,压实,翻转,放上箱,加沙,压实,扎通气孔,开上箱,取模型,再放入型芯,型芯外表面尺寸形状与壳体3内表面尺寸形状相同,再放上箱,进行铸造成毛坯,再精加工成型,将壳体3放在水平台上,使得壳体3的回转体轴线垂直于水平面;步骤10:将吊绳穿过吊环5的第五圆环体,再将吊绳挂在吊车上,通过吊车将壳体3吊起,使得临时挡板8与地面脱离,同时通过安全吊绳将壳体3的上端左右两点与吊车连接,再通过安全吊绳将壳体3的下端左右两点与吊车连接,安全吊绳与监控器连接,监控器检测本发明装置旋转的角度,将信号传输给阿安全吊绳,安全吊绳根据本发明装置旋转的角度自动进行伸缩,始终保持绷紧又不影响壳体旋转的长度。壳体3的第三内圆柱面上带有两个加强筋,这两个加强筋均为环形,这两个加强筋与壳体3的第三内圆柱面均为移动配合接触,这两个加强筋相对壳体3只能沿着壳体3轴向运动,不能相对壳体3进行转动,这两个加强筋上均带有4个螺纹通孔,上端盖2上连接有4个丝杠,每个丝杠均与上端盖2转动配合接触,每个丝杠外表面均带有外螺纹,4个丝杠与两个加强筋的4个螺纹通孔配合,4个丝杠上端均连接一个定轴齿轮,上端盖2上带有另外4个定轴齿轮,另外这4个定轴齿轮与4个丝杠上端的定轴齿轮组成定轴轮系,每一个齿轮均带动另外七个齿轮转动,由这8个齿轮的转动可以带动壳体3的第三内圆柱面的两个加强筋轴向移动,实现质心的调节。壳体3的第三圆筒体的上端左边带有一个活塞,壳体3的第三圆筒体的上端右边带有一个活塞,壳体3的第三圆筒体的下端左边带有一个活塞,壳体3的第三圆筒体的下端右边带有一个活塞,每个活塞均与壳体3螺纹配合连接,每个活塞内侧连接一个万向铰链,通过连杆将壳体3的第三圆筒体的上端左边的活塞的万向铰链和壳体3的第三圆筒体的下端右边的活塞的万向铰链连接,通过连杆将壳体3的第三圆筒体的下端左边的活塞的万向铰链和壳体3的第三圆筒体的上端右边的活塞的万向铰链连接,壳体3的第三圆筒体的上端左边的活塞的万向铰链和壳体3的第三圆筒体的下端右边的活塞的万向铰链组成双万向铰链机构,壳体3的第三圆筒体的下端左边的活塞的万向铰链和壳体3的第三圆筒体的上端右边的活塞的万向铰链组成双万向铰链机构,旋转下端的活塞可以带动上端的活塞进行旋转,使得下端的流体进入上端的空间,或者使得上端的流体进入下端的空间,使得本发明具有质心微调功能。本发明的一种通过质心位置调节进行自动翻转的十吨级液相材料装填壳体,带来的技术效果体现为:首先将装填液相材料的薄壁壳体在中部加强筋位置吊起来,通过调节壳体质心位置,使得壳体的空间姿态随着质心的变化进行自适应调整,逐渐完成从躺下姿态到起立姿态,或从起立姿态到躺下姿态的翻转工作。整个翻转过程为壳体在重力作用下自动完成,无需外力作用在壳体外壁上。壳体质心的调节可以精确控制,因此,壳体翻转过程中的速度可以精确控制,壳体翻转过程速度均匀且缓慢,避免了速度突变,避免了过大动载荷,保证了壳体强度不受破坏,进而保证了产品的安全性和可靠性。附图说明图1是一种通过质心位置调节进行自动翻转的十吨级液相材料装填壳体的结构示意图。1、抛撒管,2、上端盖,3、壳体,4、下端盖,5、吊环,6、液体,7、充气管,8、临时挡板,9、定位螺钉。具体实施方式下面结合附图和实施例对本发明作进一步的详细说明,需要说明的是本发明不局限于以下具体实施例,凡在本发明技术方案基础上进行的同等变换均在本发明的保护范围内。实施例1:如图1所示,本实施例给出一种通过质心位置调节进行自动翻转的十吨级液相材料装填壳体,包括抛撒管1,上端盖2,下端盖4,液体6,其特征在于还包括壳体3,吊环5,充气管7,临时挡板8,定位螺钉9;抛撒管1为第一圆柱体,抛撒管1的第一圆柱体为回转体,抛撒管1的第一圆柱体的上端面为第一上端圆平面,抛撒管1的第一圆柱体的侧面为第一外圆柱面,抛撒管1的第一圆柱体的下端面为第一下端圆平面;抛撒管1的回转体轴线与水平面垂直,抛撒管1的内部装有炸药,抛撒管1内部的炸药为抛撒液相材料形成云团的能量源;上端盖2为第二圆板,上端盖2的第二圆板为回转体,上端盖2的第二圆板中心带有第二圆孔,上端盖2的第二圆板的上端面为第二上端同心圆平面,上端盖2的第二圆板的外侧面为第二外圆柱面,上端盖2的第二圆板的下端面为第二下端同心圆平面,上端盖2的第二圆孔的内侧面为第二内圆柱面;上端盖2的回转体轴线与抛撒管1的回转体轴线重合,上端盖2位于抛撒管1上端外部,上端盖2的第二内圆柱面与抛撒管1的第一外圆柱面上端接触,上端盖2的第二上端同心圆平面与抛撒管1的第一上端圆平面共面;壳体3为第三圆筒体,壳体3的第三圆筒体为回转体,壳体3的第三圆筒体的外侧面为第三外圆柱面,壳体3的第三圆筒体的内侧面为第三内圆柱面,壳体3的第三圆筒体上端内侧带有第三上端内法兰,壳体3的第三上端内法兰下端面为第三上端向下同心圆环面,壳体3的第三上端内法兰上带有十六个第三螺纹通孔,壳体3的十六个第三螺纹通孔轴线与壳体3的回转体轴线平行,壳体3的十六个第三螺纹通孔绕壳体3的回转体轴线均匀分布,壳体3的第三圆筒体下端内侧带有第三下端内法兰,壳体3的第三下端内法兰上端面为第三下端向上同心圆环面,壳体3的第三下端内法兰下端面为第三下端向下同心圆环面,壳体3的第三下端内法兰的内侧面为第三下端内圆柱面,壳体3的第三下端内法兰上带有一个第三圆形通孔,壳体3的第三圆形通孔轴线与壳体3的回转体轴线垂直,壳体3的第三内圆柱面中部带有第三环形凸台,壳体3的第三外圆柱面中部带有两个第三螺纹盲孔,壳体3的两个第三螺纹盲孔的轴线均垂直于壳体3的回转体轴线;壳体3的回转体轴线与抛撒管1的回转体轴线重合,上端盖2的第二圆板位于壳体3的第三圆筒体内部,上端盖2的第二上端圆平面位于壳体3的第三上端向下同心圆环面下端,壳体3的第三内圆柱面与上端盖2的第二外圆柱面滑动配合接触;下端盖4为第四圆板,下端盖4的第四圆板为回转体,下端盖4的第四圆板的上端面为第四上端圆平面,下端盖4的第四圆板的外侧面为第四外圆柱面,下端盖4的第四圆板的下端面为第四下端圆平面;下端盖4的回转体轴线与抛撒管1的回转体轴线重合,下端盖4的第四上端圆平面与抛撒管1的第一下端圆平面连接,下端盖4的第四圆板位于壳体3的第三圆筒体内部,下端盖4的第四下端圆平面位于壳体3的第三下端向上同心圆环面上端,壳体3的第三内圆柱面与下端盖4的第四外圆柱面滑动配合接触;吊环5由左右两部分组成,吊环5的右部分为第五圆柱体,吊环5的第五圆柱体为回转体,吊环5的第五圆柱体的侧面带有第五外螺纹,吊环5的左部分为第五圆环体,吊环5的第五圆柱体和吊环5的第五圆环体转动配合连接,吊环5共两个;吊环5的第五圆柱体的回转体轴线与抛撒管1的回转体轴线垂直,吊环5的第五外螺纹安装在壳体3的第三螺纹盲孔中;液体6为被炸药抛撒后形成云团的液相材料;液体6位于抛撒管1的第一外圆柱面、上端盖2的第二下端同心圆平面、壳体3的第三内圆柱面和下端盖4的第四上端圆平面组成的封闭空间中;充气管7为第七圆管,充气管7的第七圆管为回转体,充气管7的第七圆管左端带有第七开关;充气管7的回转体轴线与抛撒管1的回转体轴线垂直,充气管7的第七圆管右端与壳体3的第三圆形通孔连接;临时挡板8为第八圆板,临时挡板8的第八圆板为回转体,临时挡板8的第八圆板的上端面为第八上端圆平面;临时挡板8的回转体轴线与抛撒管1的回转体轴线重合,临时挡板8位于壳体3下端,临时挡板8的第八上端圆平面与壳体3的第三下端向下同心圆环面连接;定位螺钉9为第九圆柱体,定位螺钉9的第九圆柱体为回转体,定位螺钉9的第九圆柱体的侧面为第九外圆柱面,定位螺钉9的第九外圆柱面下端带有第九外螺纹,定位螺钉9共十六个;定位螺钉9的回转体轴线与抛撒管1的回转体轴线平行,定位螺钉9的第九外螺纹安装在壳体3的第三螺纹通孔中。关于上端盖2的第二外圆柱面的轴向长度与上端盖2的第二圆板直径之比,主要考虑以下几个因素,既不能太大,以免增加上端盖2不必要的呆重,又不能太小以免上端盖2移动时卡主。通过实验发现,上端盖2在壳体3内部反复移动过程中,当厚度比较小的时候,容易出现卡主现象,一旦卡主,再大的挤压力也无法使其继续运动,而挤压力过大会作用在壳体3上,将壳体3挤破,导致失败。而当上端盖2的第二外圆柱面的轴向长度与上端盖2的第二圆板直径之比不低于1:10时,上端盖2的厚度足够,上端盖2在壳体3内部反复移动过程中,不再出现卡主的问题。上端盖2的重量随着厚度的增加而增大,对于液体材料装填壳体,总重量为10吨级,壳体翻转过程中的难度就在于,总重量太大,翻转惯性大,从而导致壳体承受的压力太大,容易发生破坏,上端盖2的重量过大,只会产生负面效果。因此,上端盖2的厚度越低越好。通过实测实验可知,当上端盖2的第二外圆柱面的轴向长度与上端盖2的第二圆板直径之比不超过1:9时,上端盖2的重量不到总重量的4%,认为不超过4%的上端盖重量在可接受范围以内,因此,上端盖2的第二外圆柱面的轴向长度与上端盖2的第二圆板直径之比不超过1:9。因此,上端盖2的第二外圆柱面的轴向长度与上端盖2的第二圆板直径之比为1:9~10;本实施例中,上端盖2的第二外圆柱面的轴向长度与上端盖2的第二圆板直径之比为1:9。下端盖4的设计同理,下端盖4的第四外圆柱面的轴向长度与下端盖4的第四圆板直径之比为1:9~10;本实施例中,下端盖4的第四外圆柱面的轴向长度与下端盖4的第四圆板直径之比为1:9。上端盖2的第二上端圆平面与壳体3的第三上端向下同心圆环面平行,上端盖2的第二上端圆平面与壳体3的第三上端向下同心圆环面之间的距离为第一距离,壳体3的两个第三螺纹盲孔的轴线所在平面与本发明系统质心距离为第二距离,第一距离和第二距离相同,下端盖4的第四下端圆平面与壳体3的第三下端向上同心圆环面接触。关于壳体3的两个第三螺纹盲孔的轴线所在平面位于本发明系统质心下端距离,主要考虑以下两发方面,既不能太长,导致本发明系统在通过质心调节完成翻转的过程中,由于质心偏移量太大,需要调节的尺寸过多,这部分尺寸未装填液相材料,为无效长度,避免无效长度过多,也不能太短,本发明系统在通过质心调节完成翻转的过程中,由于质心偏移量太小,质心稍微的调节,导致本发明系统在空中旋转角度过大,产生了过大的角速度及角加速度,导致过大的惯性,容易发生危险。通过实验发现,当壳体3的两个第三螺纹盲孔的轴线所在平面位于本发明系统质心下端不低于120mm时,质心偏移量足够,本发明系统在通过质心调节完成翻转的过程中,质心稍微的调节,本发明系统在空中旋转角度不大,产生了的角速度及角加速度不大,在可控制范围以内,满足安全要求。当壳体3的两个第三螺纹盲孔的轴线所在平面位于本发明系统质心下端不超过140mm时,心偏移量不算过大,需要调节的尺寸不算过大,无效长度不超过总长度2%,认为在可接受范围以内。因此,壳体3的两个第三螺纹盲孔的轴线所在平面位于本发明系统质心下端120~140mm;本实施例中,壳体3的两个第三螺纹盲孔的轴线所在平面位于本发明系统质心下端120。关于壳体3的第三环形凸台的上端面距离壳体3的第三螺纹盲孔的轴线距离与壳体3的第三螺纹盲孔公称直径之比,壳体3的第三环形凸台的下端面距离壳体3的第三螺纹盲孔的轴线距离与壳体3的第三螺纹盲孔公称直径之比,主要考虑一下2个方面:既不能太小,导致强度不足,当本发明系统由吊环5吊起时,全部重量,作用在吊环5上,而吊环5将所有重量作用在壳体3的第三环形凸台上,若该尺寸太小,会从壳体3的第三环形凸台处发生断裂,导致系统失效。通过实验发现,当壳体3的第三环形凸台的上端面距离壳体3的第三螺纹盲孔的轴线距离与壳体3的第三螺纹盲孔公称直径之比不低于1.4,壳体3的第三环形凸台的下端面距离壳体3的第三螺纹盲孔的轴线距离与壳体3的第三螺纹盲孔公称直径之比不低于1.1时,壳体3的第三环形凸台强度足够。也不能太大,导致液体材料抛撒后形成的云团由于壳体3的第三环形凸台尺寸过大而发生分层,由于壳体3的第三环形凸台相当于加强筋,当壳体3的第三环形凸台比较小时,对抛撒云团影响不大,云团在后续扩散的时候可以连接到一起。当壳体3的第三环形凸台尺寸比较大时,对抛撒云团影响过大,云团在后续扩散的时候不能连接到一起,形成了断层,影响使用效果。通过实验发现,当壳体3的第三环形凸台的上端面距离壳体3的第三螺纹盲孔的轴线距离与壳体3的第三螺纹盲孔公称直径之比不超过1.6,壳体3的第三环形凸台的下端面距离壳体3的第三螺纹盲孔的轴线距离与壳体3的第三螺纹盲孔公称直径之比不超过1.3时,对抛撒云团影响不大,云团在后续扩散的时候可以连接到一起。因此,壳体3的第三环形凸台的上端面距离壳体3的第三螺纹盲孔的轴线距离为壳体3的第三螺纹盲孔公称直径的1.4~1.6倍,壳体3的第三环形凸台的下端面距离壳体3的第三螺纹盲孔的轴线距离为壳体3的第三螺纹盲孔公称直径的1.1~1.3。本实施例中,壳体3的第三环形凸台的上端面距离壳体3的第三螺纹盲孔的轴线距离为壳体3的第三螺纹盲孔公称直径的1.4倍,壳体3的第三环形凸台的下端面距离壳体3的第三螺纹盲孔的轴线距离为壳体3的第三螺纹盲孔公称直径的1.1。壳体3的两个第三螺纹盲孔的轴线位于同一水平面,关于壳体3的两个第三螺纹盲孔的轴线的夹角,主要考虑一下3个方面:旋转灵敏性,初始起吊安稳性,起吊能力。旋转灵敏性为本发明系统的质心偏移后,本发明系统进行空间旋转的灵敏程度,当旋转灵敏性不好时,本发明系统的质心偏移后,由于本发明系统的质心和两个第三螺纹盲孔连线在竖直方向比较靠近,竖直方向投影几乎重合,导致质心变化后,没有一个偏心的力使得本发明系统进行旋转,这时本发明系统为失稳状态,一旦发生旋转,将是急速大角度旋转,不符合本发明慢速的旋转原则。当旋转灵敏性较好时,本发明系统的质心和两个第三螺纹盲孔连线在竖直方向有一定距离,当本发明系统的质心偏移后,重量乘以本发明系统的质心和两个第三螺纹盲孔连线在竖直方向的距离,为使得本发明系统旋转的力矩,本发明系统随着质心的变化,随即进行空间旋转,避免了失稳的状态。通过实际试验,将旋转灵敏性分为3个标准,以及3个分值。旋转十分灵敏:10分;旋转偶尔灵敏:3分;旋转十分不灵敏:-3分。初始起吊安稳性为本发明系统在通过吊车初始起吊时,安稳程度。主要与吊车初始起吊后,本发明系统的姿态与起吊前相比,旋转的角度。由于吊车将本发明系统起吊的过程中,本发明系统的姿态受重力作用,进行相应的旋转,希望此时旋转的角度越小越好。因为起吊过程不像后续使用过程,旋转的速度可以精确控制,而起吊过程属于简单粗暴过程,希望尽可能小的减小旋转角度,使得壳体只受到向上的力,而进行向上的运动,空间姿态尽可能少的旋转,这样旋转角速度和角加速度都比较小,可以保障壳体安全性。当初始起吊安稳性比较好时,壳体的质心距离2个吊环5连线竖直距离较小,本发明稍微旋转,壳体的质心便可以和2个吊环5连线竖直方向重合,这时,本发明系统已经稳定,稍微旋转的过程中,角速度角加速度均较小,不会发生危险。当初始起吊安稳性不好时,壳体的质心距离2个吊环5连线竖直距离较大,本发明需要旋转很大角度,壳体的质心才能和2个吊环5连线竖直方向重合,这时,本发明系统才能稳定,旋转很大角度的过程中,角速度角加速度均较大,会发生危险。通过实际试验,将初始起吊安稳性分为3个标准,以及3个分值。旋转角度不超过3°:10分;旋转角度3°~10°:5分;旋转角度超过10°:0分。起吊能力为2个吊环5可以起吊的本发明系统的重量多少的能力。由于2个吊环5呈一定角度,起吊时,2个吊环5既承受剪切力,又承受弯转力矩,又承受拉力,应力状态十分复杂,多应力状态下,2个吊环5能承受的本发明系统的重力低于2个吊环实际的抗纯剪切能力。当本发明的结构使得起吊能力较好时,2个吊环5承受的力主要为剪切力,旋转弯矩和拉力均较小,这时,2个吊环5能起吊的本发明的重量接近2个吊环5实际的抗纯剪切能力。当本发明的结构使得起吊能力不好时,2个吊环5承受的力为剪切力、旋转弯矩和拉力均的混合作用,很容易达到2个吊环5母材的极限强度,这时,2个吊环5能起吊的本发明的重量很低,仅为2个吊环5实际的抗纯剪切能力的很小一部分,这时起吊时容易发生危险。通过实际试验,将起吊能力分为3个标准,以及3个分值。起吊重量为实际的抗纯剪切能力的80%以上:10分;起吊重量为实际的抗纯剪切能力的80%~60%:6分;起吊重量为实际的抗纯剪切能力的60%以下:2分。将壳体3的两个第三螺纹盲孔的轴线的夹角分为以下几个区间:179°~180°、178°~179°、177°~178°、176°~177°、175°~176°、174°~175°、173°~174°、172°~173°、171°~172°、170°~171°。分别对以上几个区间的壳体3的两个第三螺纹盲孔的轴线的夹角进行实验,并按照以上三项标准进行评价,获得分值如下:壳体3的两个第三螺纹盲孔的轴线的夹角旋转灵敏性初始起吊安稳性起吊能力总分179°~180°-3101017178°~179°3101023177°~178°10101030176°~177°10101030175°~176°1051025174°~175°105621173°~174°105621172°~173°105621171°~172°100616170°~171°100212通过实验发现,当壳体3的两个第三螺纹盲孔的轴线的夹角为176°~178°时,获得分值最高,获得30分。因此,壳体3的两个第三螺纹盲孔的轴线的夹角为176°~178°。本实施例中,壳体3的两个第三螺纹盲孔的轴线的夹角为176°。本发明的装置左边放置一个检测装置,检测本发明的装置旋转角速度和角加速度的装置,该检测装置同时与充气管7连接,可以控制充气管7内部气体的流速,当检测装置测得本发明的装置旋转角速度为0.02弧度每秒~0.04弧度每秒时,且测得本发明的装置旋转角加速度不超过0.01弧度每平方秒时,充气管7内部气体的流速不变;当测得本发明的装置旋转角加速度超过0.01弧度每平方秒时,减小充气管7内部气体的流速;当检测本发明的装置测得本发明的装置旋转角速度超过0.04弧度每秒时,减小充气管7内部气体的流速;当测得本发明的装置测得本发明的装置旋转角速度低于0.02弧度每秒时,且测得本发明的装置旋转角加速度不超过0.01弧度每平方秒时,,增加充气管7内部气体的流速,通过对充气管7内部气体的流速的控制,使得本发明的装置的角速度和角加速度同时受控,实现缓慢的旋转,避免了过大的惯性,提高了安全性。上端盖2的第二外圆柱面和壳体3的第三内圆柱面的基本尺寸相同,上端盖2的第二外圆柱面的尺寸公差等级为d10级,壳体3的第三内圆柱面的尺寸公差等级为h10级,通过对上端盖2的第二外圆柱面和壳体3的第三内圆柱面配合尺寸的控制,使得上端盖2和壳体3之间即可以自由移动配合,又不会因为间隙过大而泄露内部液相材料;下端盖4的第四外圆柱面和壳体3的第三内圆柱面的基本尺寸相同,下端盖4的第四外圆柱面的尺寸公差等级为d10级,壳体3的第三内圆柱面的尺寸公差等级为h10级,通过对上端盖2的第二外圆柱面和壳体3的第三内圆柱面配合尺寸的控制,使得上端盖2和壳体3之间即可以自由移动配合,又不会因为间隙过大而泄露内部液相材料;所述一种通过质心位置调节进行自动翻转的十吨级液相材料装填壳体,包括以下步骤:步骤1:将壳体3放在水平台上,使得壳体3的回转体轴线垂直于水平面;步骤2:将下端盖4与壳体3装配;步骤3:将抛撒管1与壳体3装配;步骤4:将上端盖2与壳体3装配;步骤5:将吊环5与壳体3装配;步骤6:将充气管7与壳体3装配;步骤7:将临时挡板8与壳体3装配;步骤8:将定位螺钉9与壳体3装配,定位螺钉9的下端与壳体3的第三上端向下同心圆环面平齐;步骤9:将液体6灌入抛撒管1的第一外圆柱面、上端盖2的第二下端同心圆平面、壳体3的第三内圆柱面和下端盖4的第四上端圆平面组成的封闭空间中;步骤10:将吊绳穿过吊环5的第五圆环体,再将吊绳挂在吊车上,通过吊车将壳体3吊起,使得临时挡板8与地面脱离;步骤11:将本发明的系统由起立姿态转变为躺下姿态:将充气管7的第七圆管的左端与高压空气泵连接,打开充气管7的第七开关,使高压空气进入下端盖4的第四下端圆平面、壳体3的第三下端内圆柱面和临时挡板8的第八上端圆平面组成的封闭空间中,通过高压气体挤压下端盖4,下端盖4再将压力传递给抛撒管1和液体6,液体6再将压力传递给上端盖2,使得抛撒管1、上端盖2、下端盖4和液体6同时向上移动,本发明的系统质心逐渐上移,本发明系统的姿态随着质心的上移逐渐由起立姿态转变为躺下姿态,待抛撒管1的回转体轴线与水平面平行,关闭充气管7的第七开关,断开充气管7的第七圆管的左端与高压空气泵的连接;步骤12:将本发明的系统由躺下姿态转变为起立姿态:打开充气管7的第七开关,放出下端盖4的第四下端圆平面、壳体3的第三下端内圆柱面和临时挡板8的第八上端圆平面组成的封闭空间中的高压气体,将充气管7的第七圆管的左端与真空泵连接,对下端盖4的第四下端圆平面、壳体3的第三下端内圆柱面和临时挡板8的第八上端圆平面组成的封闭空间进行抽真空,使得下端盖4的第四下端圆平面受到负压,下端盖4再将负压传递给抛撒管1和液体6,液体6再将负压传递给上端盖2,使得抛撒管1、上端盖2、下端盖4和液体6同时向靠近临时挡板8的方向移动,本发明的系统质心逐渐靠近临时挡板8,本发明系统的姿态随着质心的靠近临时挡板8逐渐由躺下姿态转变为起立姿态,待抛撒管1的回转体轴线与水平面垂直,关闭充气管7的第七开关,断开充气管7的第七圆管的左端与真空泵的连接;步骤13:将定位螺钉9拧紧,通过定位螺钉9挤压上端盖2的第二上端同心圆平面,固定上端盖2的位置,使得上端盖2与壳体3不能再发生相对运动,卸下临时挡板8,此时,本发明的系统完成实验前准备。使用原方案的翻转车进行壳体的从躺下姿态到起立姿态,及从起立姿态到躺下姿态的翻转实验,实验壳体重量为十吨,实验壳体内部状体液相材料,壳体厚度不超过10mm,为薄壁壳体,反复翻转实验结果如下:实验状态实验结果10mm壳体从起立姿态到躺下姿态壳体完好10mm壳体从躺下姿态到起立姿态壳体完好9mm壳体从起立姿态到躺下姿态壳体完好9mm壳体从躺下姿态到起立姿态壳体完好8mm壳体从起立姿态到躺下姿态壳体完好8mm壳体从躺下姿态到起立姿态壳体发生破坏7.5mm壳体从躺下姿态到起立姿态壳体发生破坏7.5mm壳体从躺下姿态到起立姿态无法进行7mm壳体从躺下姿态到起立姿态壳体发生破坏7mm壳体从躺下姿态到起立姿态无法进行6mm壳体从躺下姿态到起立姿态壳体发生破坏6mm壳体从躺下姿态到起立姿态无法进行5mm壳体从躺下姿态到起立姿态壳体发生破坏5mm壳体从躺下姿态到起立姿态无法进行分析可知,当壳体壁厚为8mm时,壳体从起立姿态到躺下姿态,壳体完好,但是壳体从躺下姿态到起立姿态便发生破坏,而壳体壁厚不超过7.5mm时,壳体从起立姿态到躺下姿态,便发生破坏。壳体壁厚至少为9mm时,才能确保从起立姿态到躺下姿态以及从躺下姿态到起立姿态均壳体完好。使用本发明的装置及方法,按照步骤1到步骤13,反复进行从躺下姿态到起立姿态,及从起立姿态到躺下姿态的翻转实验,实验壳体重量为十吨,实验壳体内部状体液相材料,壳体厚度为5mm,为薄壁壳体,反复翻转实验结果如下:实验状态实验结果第1次从起立姿态到躺下姿态壳体完好第1次从躺下姿态到起立姿态壳体完好第2次从起立姿态到躺下姿态壳体完好第2次从躺下姿态到起立姿态壳体完好第3次从起立姿态到躺下姿态壳体完好第3次从躺下姿态到起立姿态壳体完好第4次从起立姿态到躺下姿态壳体完好第4次从躺下姿态到起立姿态壳体完好第5次从起立姿态到躺下姿态壳体完好第5次从躺下姿态到起立姿态壳体完好第6次从起立姿态到躺下姿态壳体完好第6次从躺下姿态到起立姿态壳体完好第7次从起立姿态到躺下姿态壳体完好第7次从躺下姿态到起立姿态壳体完好第8次从起立姿态到躺下姿态壳体完好第8次从躺下姿态到起立姿态壳体完好第9次从起立姿态到躺下姿态壳体完好第9次从躺下姿态到起立姿态壳体完好第10次从起立姿态到躺下姿态壳体完好第10次从躺下姿态到起立姿态壳体完好分析可知,总重量为10吨的液相材料装填薄壁壳体,壳体壁厚5mm,连续进行十次由起立姿态到躺下姿态,再由躺下姿态到起立姿态的翻转实验,壳体完好。对于十吨级装填液相材料的薄壁壳体,使用本发明进行翻转,壳体壁厚可以减少至原翻转方案的55%,大幅度降低了壳体壁厚,减少了壳体壁厚对抛撒范围的影响,增加了产品的使用效果。本发明的一种通过质心位置调节进行自动翻转的十吨级液相材料装填壳体,首先将装填液相材料的薄壁壳体在中部加强筋位置吊起来,通过调节壳体质心位置,使得壳体的空间姿态随着质心的变化进行自适应调整,逐渐完成从躺下姿态到起立姿态,或从起立姿态到躺下姿态的翻转工作。整个翻转过程为壳体在重力作用下自动完成,无需外力作用在壳体外壁上。壳体质心的调节可以精确控制,因此,壳体翻转过程中的速度可以精确控制,壳体翻转过程速度均匀且缓慢,避免了速度突变,避免了过大动载荷,保证了壳体强度不受破坏,进而保证了产品的安全性和可靠性。实施例2:如图1所示,本实施例给出一种通过质心位置调节进行自动翻转的十吨级液相材料装填壳体,包括抛撒管1,上端盖2,下端盖4,液体6,其特征在于还包括壳体3,吊环5,充气管7,临时挡板8,定位螺钉9;抛撒管1为第一圆柱体,抛撒管1的第一圆柱体为回转体,抛撒管1的第一圆柱体的上端面为第一上端圆平面,抛撒管1的第一圆柱体的侧面为第一外圆柱面,抛撒管1的第一圆柱体的下端面为第一下端圆平面;抛撒管1的回转体轴线与水平面垂直,抛撒管1的内部装有炸药,抛撒管1内部的炸药为抛撒液相材料形成云团的能量源;上端盖2为第二圆板,上端盖2的第二圆板为回转体,上端盖2的第二圆板中心带有第二圆孔,上端盖2的第二圆板的上端面为第二上端同心圆平面,上端盖2的第二圆板的外侧面为第二外圆柱面,上端盖2的第二圆板的下端面为第二下端同心圆平面,上端盖2的第二圆孔的内侧面为第二内圆柱面;上端盖2的回转体轴线与抛撒管1的回转体轴线重合,上端盖2位于抛撒管1上端外部,上端盖2的第二内圆柱面与抛撒管1的第一外圆柱面上端接触,上端盖2的第二上端同心圆平面与抛撒管1的第一上端圆平面共面;壳体3为第三圆筒体,壳体3的第三圆筒体为回转体,壳体3的第三圆筒体的外侧面为第三外圆柱面,壳体3的第三圆筒体的内侧面为第三内圆柱面,壳体3的第三圆筒体上端内侧带有第三上端内法兰,壳体3的第三上端内法兰下端面为第三上端向下同心圆环面,壳体3的第三上端内法兰上带有十六个第三螺纹通孔,壳体3的十六个第三螺纹通孔轴线与壳体3的回转体轴线平行,壳体3的十六个第三螺纹通孔绕壳体3的回转体轴线均匀分布,壳体3的第三圆筒体下端内侧带有第三下端内法兰,壳体3的第三下端内法兰上端面为第三下端向上同心圆环面,壳体3的第三下端内法兰下端面为第三下端向下同心圆环面,壳体3的第三下端内法兰的内侧面为第三下端内圆柱面,壳体3的第三下端内法兰上带有一个第三圆形通孔,壳体3的第三圆形通孔轴线与壳体3的回转体轴线垂直,壳体3的第三内圆柱面中部带有第三环形凸台,壳体3的第三外圆柱面中部带有两个第三螺纹盲孔,壳体3的两个第三螺纹盲孔的轴线均垂直于壳体3的回转体轴线;壳体3的回转体轴线与抛撒管1的回转体轴线重合,上端盖2的第二圆板位于壳体3的第三圆筒体内部,上端盖2的第二上端圆平面位于壳体3的第三上端向下同心圆环面下端,壳体3的第三内圆柱面与上端盖2的第二外圆柱面滑动配合接触;下端盖4为第四圆板,下端盖4的第四圆板为回转体,下端盖4的第四圆板的上端面为第四上端圆平面,下端盖4的第四圆板的外侧面为第四外圆柱面,下端盖4的第四圆板的下端面为第四下端圆平面;下端盖4的回转体轴线与抛撒管1的回转体轴线重合,下端盖4的第四上端圆平面与抛撒管1的第一下端圆平面连接,下端盖4的第四圆板位于壳体3的第三圆筒体内部,下端盖4的第四下端圆平面位于壳体3的第三下端向上同心圆环面上端,壳体3的第三内圆柱面与下端盖4的第四外圆柱面滑动配合接触;吊环5由左右两部分组成,吊环5的右部分为第五圆柱体,吊环5的第五圆柱体为回转体,吊环5的第五圆柱体的侧面带有第五外螺纹,吊环5的左部分为第五圆环体,吊环5的第五圆柱体和吊环5的第五圆环体转动配合连接,吊环5共两个;吊环5的第五圆柱体的回转体轴线与抛撒管1的回转体轴线垂直,吊环5的第五外螺纹安装在壳体3的第三螺纹盲孔中;液体6为被炸药抛撒后形成云团的液相材料;液体6位于抛撒管1的第一外圆柱面、上端盖2的第二下端同心圆平面、壳体3的第三内圆柱面和下端盖4的第四上端圆平面组成的封闭空间中;充气管7为第七圆管,充气管7的第七圆管为回转体,充气管7的第七圆管左端带有第七开关;充气管7的回转体轴线与抛撒管1的回转体轴线垂直,充气管7的第七圆管右端与壳体3的第三圆形通孔连接;临时挡板8为第八圆板,临时挡板8的第八圆板为回转体,临时挡板8的第八圆板的上端面为第八上端圆平面;临时挡板8的回转体轴线与抛撒管1的回转体轴线重合,临时挡板8位于壳体3下端,临时挡板8的第八上端圆平面与壳体3的第三下端向下同心圆环面连接;定位螺钉9为第九圆柱体,定位螺钉9的第九圆柱体为回转体,定位螺钉9的第九圆柱体的侧面为第九外圆柱面,定位螺钉9的第九外圆柱面下端带有第九外螺纹,定位螺钉9共十六个;定位螺钉9的回转体轴线与抛撒管1的回转体轴线平行,定位螺钉9的第九外螺纹安装在壳体3的第三螺纹通孔中。关于上端盖2的第二外圆柱面的轴向长度与上端盖2的第二圆板直径之比,主要考虑以下几个因素,既不能太大,以免增加上端盖2不必要的呆重,又不能太小以免上端盖2移动时卡主。通过实验发现,上端盖2在壳体3内部反复移动过程中,当厚度比较小的时候,容易出现卡主现象,一旦卡主,再大的挤压力也无法使其继续运动,而挤压力过大会作用在壳体3上,将壳体3挤破,导致失败。而当上端盖2的第二外圆柱面的轴向长度与上端盖2的第二圆板直径之比不低于1:10时,上端盖2的厚度足够,上端盖2在壳体3内部反复移动过程中,不再出现卡主的问题。上端盖2的重量随着厚度的增加而增大,对于液体材料装填壳体,总重量为10吨级,壳体翻转过程中的难度就在于,总重量太大,翻转惯性大,从而导致壳体承受的压力太大,容易发生破坏,上端盖2的重量过大,只会产生负面效果。因此,上端盖2的厚度越低越好。通过实测实验可知,当上端盖2的第二外圆柱面的轴向长度与上端盖2的第二圆板直径之比不超过1:9时,上端盖2的重量不到总重量的4%,认为不超过4%的上端盖重量在可接受范围以内,因此,上端盖2的第二外圆柱面的轴向长度与上端盖2的第二圆板直径之比不超过1:9。因此,上端盖2的第二外圆柱面的轴向长度与上端盖2的第二圆板直径之比为1:9~10;本实施例中,上端盖2的第二外圆柱面的轴向长度与上端盖2的第二圆板直径之比为1:9。下端盖4的设计同理,下端盖4的第四外圆柱面的轴向长度与下端盖4的第四圆板直径之比为1:9~10;本实施例中,下端盖4的第四外圆柱面的轴向长度与下端盖4的第四圆板直径之比为1:9。上端盖2的第二上端圆平面与壳体3的第三上端向下同心圆环面平行,上端盖2的第二上端圆平面与壳体3的第三上端向下同心圆环面之间的距离为第一距离,壳体3的两个第三螺纹盲孔的轴线所在平面与本发明系统质心距离为第二距离,第一距离和第二距离相同,下端盖4的第四下端圆平面与壳体3的第三下端向上同心圆环面接触。关于壳体3的两个第三螺纹盲孔的轴线所在平面位于本发明系统质心下端距离,主要考虑以下两发方面,既不能太长,导致本发明系统在通过质心调节完成翻转的过程中,由于质心偏移量太大,需要调节的尺寸过多,这部分尺寸未装填液相材料,为无效长度,避免无效长度过多,也不能太短,本发明系统在通过质心调节完成翻转的过程中,由于质心偏移量太小,质心稍微的调节,导致本发明系统在空中旋转角度过大,产生了过大的角速度及角加速度,导致过大的惯性,容易发生危险。通过实验发现,当壳体3的两个第三螺纹盲孔的轴线所在平面位于本发明系统质心下端不低于120mm时,质心偏移量足够,本发明系统在通过质心调节完成翻转的过程中,质心稍微的调节,本发明系统在空中旋转角度不大,产生了的角速度及角加速度不大,在可控制范围以内,满足安全要求。当壳体3的两个第三螺纹盲孔的轴线所在平面位于本发明系统质心下端不超过140mm时,心偏移量不算过大,需要调节的尺寸不算过大,无效长度不超过总长度2%,认为在可接受范围以内。因此,壳体3的两个第三螺纹盲孔的轴线所在平面位于本发明系统质心下端120~140mm;本实施例中,壳体3的两个第三螺纹盲孔的轴线所在平面位于本发明系统质心下端120。关于壳体3的第三环形凸台的上端面距离壳体3的第三螺纹盲孔的轴线距离与壳体3的第三螺纹盲孔公称直径之比,壳体3的第三环形凸台的下端面距离壳体3的第三螺纹盲孔的轴线距离与壳体3的第三螺纹盲孔公称直径之比,主要考虑一下2个方面:既不能太小,导致强度不足,当本发明系统由吊环5吊起时,全部重量,作用在吊环5上,而吊环5将所有重量作用在壳体3的第三环形凸台上,若该尺寸太小,会从壳体3的第三环形凸台处发生断裂,导致系统失效。通过实验发现,当壳体3的第三环形凸台的上端面距离壳体3的第三螺纹盲孔的轴线距离与壳体3的第三螺纹盲孔公称直径之比不低于1.4,壳体3的第三环形凸台的下端面距离壳体3的第三螺纹盲孔的轴线距离与壳体3的第三螺纹盲孔公称直径之比不低于1.1时,壳体3的第三环形凸台强度足够。也不能太大,导致液体材料抛撒后形成的云团由于壳体3的第三环形凸台尺寸过大而发生分层,由于壳体3的第三环形凸台相当于加强筋,当壳体3的第三环形凸台比较小时,对抛撒云团影响不大,云团在后续扩散的时候可以连接到一起。当壳体3的第三环形凸台尺寸比较大时,对抛撒云团影响过大,云团在后续扩散的时候不能连接到一起,形成了断层,影响使用效果。通过实验发现,当壳体3的第三环形凸台的上端面距离壳体3的第三螺纹盲孔的轴线距离与壳体3的第三螺纹盲孔公称直径之比不超过1.6,壳体3的第三环形凸台的下端面距离壳体3的第三螺纹盲孔的轴线距离与壳体3的第三螺纹盲孔公称直径之比不超过1.3时,对抛撒云团影响不大,云团在后续扩散的时候可以连接到一起。因此,壳体3的第三环形凸台的上端面距离壳体3的第三螺纹盲孔的轴线距离为壳体3的第三螺纹盲孔公称直径的1.4~1.6倍,壳体3的第三环形凸台的下端面距离壳体3的第三螺纹盲孔的轴线距离为壳体3的第三螺纹盲孔公称直径的1.1~1.3。本实施例中,壳体3的第三环形凸台的上端面距离壳体3的第三螺纹盲孔的轴线距离为壳体3的第三螺纹盲孔公称直径的1.4倍,壳体3的第三环形凸台的下端面距离壳体3的第三螺纹盲孔的轴线距离为壳体3的第三螺纹盲孔公称直径的1.1。壳体3的两个第三螺纹盲孔的轴线位于同一水平面,关于壳体3的两个第三螺纹盲孔的轴线的夹角,主要考虑一下3个方面:旋转灵敏性,初始起吊安稳性,起吊能力。旋转灵敏性为本发明系统的质心偏移后,本发明系统进行空间旋转的灵敏程度,当旋转灵敏性不好时,本发明系统的质心偏移后,由于本发明系统的质心和两个第三螺纹盲孔连线在竖直方向比较靠近,竖直方向投影几乎重合,导致质心变化后,没有一个偏心的力使得本发明系统进行旋转,这时本发明系统为失稳状态,一旦发生旋转,将是急速大角度旋转,不符合本发明慢速的旋转原则。当旋转灵敏性较好时,本发明系统的质心和两个第三螺纹盲孔连线在竖直方向有一定距离,当本发明系统的质心偏移后,重量乘以本发明系统的质心和两个第三螺纹盲孔连线在竖直方向的距离,为使得本发明系统旋转的力矩,本发明系统随着质心的变化,随即进行空间旋转,避免了失稳的状态。通过实际试验,将旋转灵敏性分为3个标准,以及3个分值。旋转十分灵敏:10分;旋转偶尔灵敏:3分;旋转十分不灵敏:-3分。初始起吊安稳性为本发明系统在通过吊车初始起吊时,安稳程度。主要与吊车初始起吊后,本发明系统的姿态与起吊前相比,旋转的角度。由于吊车将本发明系统起吊的过程中,本发明系统的姿态受重力作用,进行相应的旋转,希望此时旋转的角度越小越好。因为起吊过程不像后续使用过程,旋转的速度可以精确控制,而起吊过程属于简单粗暴过程,希望尽可能小的减小旋转角度,使得壳体只受到向上的力,而进行向上的运动,空间姿态尽可能少的旋转,这样旋转角速度和角加速度都比较小,可以保障壳体安全性。当初始起吊安稳性比较好时,壳体的质心距离2个吊环5连线竖直距离较小,本发明稍微旋转,壳体的质心便可以和2个吊环5连线竖直方向重合,这时,本发明系统已经稳定,稍微旋转的过程中,角速度角加速度均较小,不会发生危险。当初始起吊安稳性不好时,壳体的质心距离2个吊环5连线竖直距离较大,本发明需要旋转很大角度,壳体的质心才能和2个吊环5连线竖直方向重合,这时,本发明系统才能稳定,旋转很大角度的过程中,角速度角加速度均较大,会发生危险。通过实际试验,将初始起吊安稳性分为3个标准,以及3个分值。旋转角度不超过3°:10分;旋转角度3°~10°:5分;旋转角度超过10°:0分。起吊能力为2个吊环5可以起吊的本发明系统的重量多少的能力。由于2个吊环5呈一定角度,起吊时,2个吊环5既承受剪切力,又承受弯转力矩,又承受拉力,应力状态十分复杂,多应力状态下,2个吊环5能承受的本发明系统的重力低于2个吊环实际的抗纯剪切能力。当本发明的结构使得起吊能力较好时,2个吊环5承受的力主要为剪切力,旋转弯矩和拉力均较小,这时,2个吊环5能起吊的本发明的重量接近2个吊环5实际的抗纯剪切能力。当本发明的结构使得起吊能力不好时,2个吊环5承受的力为剪切力、旋转弯矩和拉力均的混合作用,很容易达到2个吊环5母材的极限强度,这时,2个吊环5能起吊的本发明的重量很低,仅为2个吊环5实际的抗纯剪切能力的很小一部分,这时起吊时容易发生危险。通过实际试验,将起吊能力分为3个标准,以及3个分值。起吊重量为实际的抗纯剪切能力的80%以上:10分;起吊重量为实际的抗纯剪切能力的80%~60%:6分;起吊重量为实际的抗纯剪切能力的60%以下:2分。将壳体3的两个第三螺纹盲孔的轴线的夹角分为以下几个区间:179°~180°、178°~179°、177°~178°、176°~177°、175°~176°、174°~175°、173°~174°、172°~173°、171°~172°、170°~171°。分别对以上几个区间的壳体3的两个第三螺纹盲孔的轴线的夹角进行实验,并按照以上三项标准进行评价,获得分值如下:壳体3的两个第三螺纹盲孔的轴线的夹角旋转灵敏性初始起吊安稳性起吊能力总分179°~180°-3101017178°~179°3101023177°~178°10101030176°~177°10101030175°~176°1051025174°~175°105621173°~174°105621172°~173°105621171°~172°100616170°~171°100212通过实验发现,当壳体3的两个第三螺纹盲孔的轴线的夹角为176°~178°时,获得分值最高,获得30分。因此,壳体3的两个第三螺纹盲孔的轴线的夹角为176°~178°。本实施例中,壳体3的两个第三螺纹盲孔的轴线的夹角为176°。在本发明的装置的左边放置一个检测仪器,该检测仪器可以检测本发明的装置各零件内部内应力,当本发明的装置在旋转过程中,任何一个零件内部内应力达到其母材强度极限的百分之60时,即发生报警,这样,只要任何一个零件强度超过60%,便发生报警,避免因为强度不够造成的危险;上端盖2的第二外圆柱面上安装两道密封圈,上端盖2的第二外圆柱面的上端的密封圈距上端盖2的第二上端同心圆平面为2mm,上端盖2的第二外圆柱面的下端的密封圈距上端盖2的第二下端同心圆平面为2mm,这样,上端盖2与壳体3相对运动过程中,由于有2道密封圈,可以避免上端盖2轴线倾斜而导致的卡死,有2道密封圈,可以满足相对运动过程中的密封;所述一种通过质心位置调节进行自动翻转的十吨级液相材料装填壳体,包括以下步骤:步骤1:将壳体3放在水平台上,使得壳体3的回转体轴线垂直于水平面;步骤2:将下端盖4与壳体3装配;步骤3:将抛撒管1与壳体3装配;步骤4:将上端盖2与壳体3装配;步骤5:将吊环5与壳体3装配;步骤6:将充气管7与壳体3装配;步骤7:将临时挡板8与壳体3装配;步骤8:将定位螺钉9与壳体3装配,定位螺钉9的下端与壳体3的第三上端向下同心圆环面平齐;步骤9:将液体6灌入抛撒管1的第一外圆柱面、上端盖2的第二下端同心圆平面、壳体3的第三内圆柱面和下端盖4的第四上端圆平面组成的封闭空间中;步骤10:将吊绳穿过吊环5的第五圆环体,再将吊绳挂在吊车上,通过吊车将壳体3吊起,使得临时挡板8与地面脱离;步骤11:将本发明的系统由起立姿态转变为躺下姿态:将充气管7的第七圆管的左端与高压空气泵连接,打开充气管7的第七开关,使高压空气进入下端盖4的第四下端圆平面、壳体3的第三下端内圆柱面和临时挡板8的第八上端圆平面组成的封闭空间中,通过高压气体挤压下端盖4,下端盖4再将压力传递给抛撒管1和液体6,液体6再将压力传递给上端盖2,使得抛撒管1、上端盖2、下端盖4和液体6同时向上移动,本发明的系统质心逐渐上移,本发明系统的姿态随着质心的上移逐渐由起立姿态转变为躺下姿态,待抛撒管1的回转体轴线与水平面平行,关闭充气管7的第七开关,断开充气管7的第七圆管的左端与高压空气泵的连接;步骤12:将本发明的系统由躺下姿态转变为起立姿态:打开充气管7的第七开关,放出下端盖4的第四下端圆平面、壳体3的第三下端内圆柱面和临时挡板8的第八上端圆平面组成的封闭空间中的高压气体,将充气管7的第七圆管的左端与真空泵连接,对下端盖4的第四下端圆平面、壳体3的第三下端内圆柱面和临时挡板8的第八上端圆平面组成的封闭空间进行抽真空,使得下端盖4的第四下端圆平面受到负压,下端盖4再将负压传递给抛撒管1和液体6,液体6再将负压传递给上端盖2,使得抛撒管1、上端盖2、下端盖4和液体6同时向靠近临时挡板8的方向移动,本发明的系统质心逐渐靠近临时挡板8,本发明系统的姿态随着质心的靠近临时挡板8逐渐由躺下姿态转变为起立姿态,待抛撒管1的回转体轴线与水平面垂直,关闭充气管7的第七开关,断开充气管7的第七圆管的左端与真空泵的连接;步骤13:将定位螺钉9拧紧,通过定位螺钉9挤压上端盖2的第二上端同心圆平面,固定上端盖2的位置,使得上端盖2与壳体3不能再发生相对运动,卸下临时挡板8,此时,本发明的系统完成实验前准备。使用原方案的翻转车进行壳体的从躺下姿态到起立姿态,及从起立姿态到躺下姿态的翻转实验,实验壳体重量为十吨,实验壳体内部状体液相材料,壳体厚度不超过10mm,为薄壁壳体,反复翻转实验结果如下:实验状态实验结果10mm壳体从起立姿态到躺下姿态壳体完好10mm壳体从躺下姿态到起立姿态壳体完好9mm壳体从起立姿态到躺下姿态壳体完好9mm壳体从躺下姿态到起立姿态壳体完好8mm壳体从起立姿态到躺下姿态壳体完好8mm壳体从躺下姿态到起立姿态壳体发生破坏7.5mm壳体从躺下姿态到起立姿态壳体发生破坏7.5mm壳体从躺下姿态到起立姿态无法进行7mm壳体从躺下姿态到起立姿态壳体发生破坏7mm壳体从躺下姿态到起立姿态无法进行6mm壳体从躺下姿态到起立姿态壳体发生破坏6mm壳体从躺下姿态到起立姿态无法进行5mm壳体从躺下姿态到起立姿态壳体发生破坏5mm壳体从躺下姿态到起立姿态无法进行分析可知,当壳体壁厚为8mm时,壳体从起立姿态到躺下姿态,壳体完好,但是壳体从躺下姿态到起立姿态便发生破坏,而壳体壁厚不超过7.5mm时,壳体从起立姿态到躺下姿态,便发生破坏。壳体壁厚至少为9mm时,才能确保从起立姿态到躺下姿态以及从躺下姿态到起立姿态均壳体完好。使用本发明的装置及方法,按照步骤1到步骤13,反复进行从躺下姿态到起立姿态,及从起立姿态到躺下姿态的翻转实验,实验壳体重量为十吨,实验壳体内部状体液相材料,壳体厚度为5mm,为薄壁壳体,反复翻转实验结果如下:实验状态实验结果第1次从起立姿态到躺下姿态壳体完好第1次从躺下姿态到起立姿态壳体完好第2次从起立姿态到躺下姿态壳体完好第2次从躺下姿态到起立姿态壳体完好第3次从起立姿态到躺下姿态壳体完好第3次从躺下姿态到起立姿态壳体完好第4次从起立姿态到躺下姿态壳体完好第4次从躺下姿态到起立姿态壳体完好第5次从起立姿态到躺下姿态壳体完好第5次从躺下姿态到起立姿态壳体完好第6次从起立姿态到躺下姿态壳体完好第6次从躺下姿态到起立姿态壳体完好第7次从起立姿态到躺下姿态壳体完好第7次从躺下姿态到起立姿态壳体完好第8次从起立姿态到躺下姿态壳体完好第8次从躺下姿态到起立姿态壳体完好第9次从起立姿态到躺下姿态壳体完好第9次从躺下姿态到起立姿态壳体完好第10次从起立姿态到躺下姿态壳体完好第10次从躺下姿态到起立姿态壳体完好分析可知,总重量为10吨的液相材料装填薄壁壳体,壳体壁厚5mm,连续进行十次由起立姿态到躺下姿态,再由躺下姿态到起立姿态的翻转实验,壳体完好。对于十吨级装填液相材料的薄壁壳体,使用本发明进行翻转,壳体壁厚可以减少至原翻转方案的55%,大幅度降低了壳体壁厚,减少了壳体壁厚对抛撒范围的影响,增加了产品的使用效果。本发明的一种通过质心位置调节进行自动翻转的十吨级液相材料装填壳体,首先将装填液相材料的薄壁壳体在中部加强筋位置吊起来,通过调节壳体质心位置,使得壳体的空间姿态随着质心的变化进行自适应调整,逐渐完成从躺下姿态到起立姿态,或从起立姿态到躺下姿态的翻转工作。整个翻转过程为壳体在重力作用下自动完成,无需外力作用在壳体外壁上。壳体质心的调节可以精确控制,因此,壳体翻转过程中的速度可以精确控制,壳体翻转过程速度均匀且缓慢,避免了速度突变,避免了过大动载荷,保证了壳体强度不受破坏,进而保证了产品的安全性和可靠性。实施例3:如图1所示,本实施例给出一种通过质心位置调节进行自动翻转的十吨级液相材料装填壳体,包括抛撒管1,上端盖2,下端盖4,液体6,其特征在于还包括壳体3,吊环5,充气管7,临时挡板8,定位螺钉9;抛撒管1为第一圆柱体,抛撒管1的第一圆柱体为回转体,抛撒管1的第一圆柱体的上端面为第一上端圆平面,抛撒管1的第一圆柱体的侧面为第一外圆柱面,抛撒管1的第一圆柱体的下端面为第一下端圆平面;抛撒管1的回转体轴线与水平面垂直,抛撒管1的内部装有炸药,抛撒管1内部的炸药为抛撒液相材料形成云团的能量源;上端盖2为第二圆板,上端盖2的第二圆板为回转体,上端盖2的第二圆板中心带有第二圆孔,上端盖2的第二圆板的上端面为第二上端同心圆平面,上端盖2的第二圆板的外侧面为第二外圆柱面,上端盖2的第二圆板的下端面为第二下端同心圆平面,上端盖2的第二圆孔的内侧面为第二内圆柱面;上端盖2的回转体轴线与抛撒管1的回转体轴线重合,上端盖2位于抛撒管1上端外部,上端盖2的第二内圆柱面与抛撒管1的第一外圆柱面上端接触,上端盖2的第二上端同心圆平面与抛撒管1的第一上端圆平面共面;壳体3为第三圆筒体,壳体3的第三圆筒体为回转体,壳体3的第三圆筒体的外侧面为第三外圆柱面,壳体3的第三圆筒体的内侧面为第三内圆柱面,壳体3的第三圆筒体上端内侧带有第三上端内法兰,壳体3的第三上端内法兰下端面为第三上端向下同心圆环面,壳体3的第三上端内法兰上带有十六个第三螺纹通孔,壳体3的十六个第三螺纹通孔轴线与壳体3的回转体轴线平行,壳体3的十六个第三螺纹通孔绕壳体3的回转体轴线均匀分布,壳体3的第三圆筒体下端内侧带有第三下端内法兰,壳体3的第三下端内法兰上端面为第三下端向上同心圆环面,壳体3的第三下端内法兰下端面为第三下端向下同心圆环面,壳体3的第三下端内法兰的内侧面为第三下端内圆柱面,壳体3的第三下端内法兰上带有一个第三圆形通孔,壳体3的第三圆形通孔轴线与壳体3的回转体轴线垂直,壳体3的第三内圆柱面中部带有第三环形凸台,壳体3的第三外圆柱面中部带有两个第三螺纹盲孔,壳体3的两个第三螺纹盲孔的轴线均垂直于壳体3的回转体轴线;壳体3的回转体轴线与抛撒管1的回转体轴线重合,上端盖2的第二圆板位于壳体3的第三圆筒体内部,上端盖2的第二上端圆平面位于壳体3的第三上端向下同心圆环面下端,壳体3的第三内圆柱面与上端盖2的第二外圆柱面滑动配合接触;下端盖4为第四圆板,下端盖4的第四圆板为回转体,下端盖4的第四圆板的上端面为第四上端圆平面,下端盖4的第四圆板的外侧面为第四外圆柱面,下端盖4的第四圆板的下端面为第四下端圆平面;下端盖4的回转体轴线与抛撒管1的回转体轴线重合,下端盖4的第四上端圆平面与抛撒管1的第一下端圆平面连接,下端盖4的第四圆板位于壳体3的第三圆筒体内部,下端盖4的第四下端圆平面位于壳体3的第三下端向上同心圆环面上端,壳体3的第三内圆柱面与下端盖4的第四外圆柱面滑动配合接触;吊环5由左右两部分组成,吊环5的右部分为第五圆柱体,吊环5的第五圆柱体为回转体,吊环5的第五圆柱体的侧面带有第五外螺纹,吊环5的左部分为第五圆环体,吊环5的第五圆柱体和吊环5的第五圆环体转动配合连接,吊环5共两个;吊环5的第五圆柱体的回转体轴线与抛撒管1的回转体轴线垂直,吊环5的第五外螺纹安装在壳体3的第三螺纹盲孔中;液体6为被炸药抛撒后形成云团的液相材料;液体6位于抛撒管1的第一外圆柱面、上端盖2的第二下端同心圆平面、壳体3的第三内圆柱面和下端盖4的第四上端圆平面组成的封闭空间中;充气管7为第七圆管,充气管7的第七圆管为回转体,充气管7的第七圆管左端带有第七开关;充气管7的回转体轴线与抛撒管1的回转体轴线垂直,充气管7的第七圆管右端与壳体3的第三圆形通孔连接;临时挡板8为第八圆板,临时挡板8的第八圆板为回转体,临时挡板8的第八圆板的上端面为第八上端圆平面;临时挡板8的回转体轴线与抛撒管1的回转体轴线重合,临时挡板8位于壳体3下端,临时挡板8的第八上端圆平面与壳体3的第三下端向下同心圆环面连接;定位螺钉9为第九圆柱体,定位螺钉9的第九圆柱体为回转体,定位螺钉9的第九圆柱体的侧面为第九外圆柱面,定位螺钉9的第九外圆柱面下端带有第九外螺纹,定位螺钉9共十六个;定位螺钉9的回转体轴线与抛撒管1的回转体轴线平行,定位螺钉9的第九外螺纹安装在壳体3的第三螺纹通孔中。关于上端盖2的第二外圆柱面的轴向长度与上端盖2的第二圆板直径之比,主要考虑以下几个因素,既不能太大,以免增加上端盖2不必要的呆重,又不能太小以免上端盖2移动时卡主。通过实验发现,上端盖2在壳体3内部反复移动过程中,当厚度比较小的时候,容易出现卡主现象,一旦卡主,再大的挤压力也无法使其继续运动,而挤压力过大会作用在壳体3上,将壳体3挤破,导致失败。而当上端盖2的第二外圆柱面的轴向长度与上端盖2的第二圆板直径之比不低于1:10时,上端盖2的厚度足够,上端盖2在壳体3内部反复移动过程中,不再出现卡主的问题。上端盖2的重量随着厚度的增加而增大,对于液体材料装填壳体,总重量为10吨级,壳体翻转过程中的难度就在于,总重量太大,翻转惯性大,从而导致壳体承受的压力太大,容易发生破坏,上端盖2的重量过大,只会产生负面效果。因此,上端盖2的厚度越低越好。通过实测实验可知,当上端盖2的第二外圆柱面的轴向长度与上端盖2的第二圆板直径之比不超过1:9时,上端盖2的重量不到总重量的4%,认为不超过4%的上端盖重量在可接受范围以内,因此,上端盖2的第二外圆柱面的轴向长度与上端盖2的第二圆板直径之比不超过1:9。因此,上端盖2的第二外圆柱面的轴向长度与上端盖2的第二圆板直径之比为1:9~10;本实施例中,上端盖2的第二外圆柱面的轴向长度与上端盖2的第二圆板直径之比为1:9。下端盖4的设计同理,下端盖4的第四外圆柱面的轴向长度与下端盖4的第四圆板直径之比为1:9~10;本实施例中,下端盖4的第四外圆柱面的轴向长度与下端盖4的第四圆板直径之比为1:9。上端盖2的第二上端圆平面与壳体3的第三上端向下同心圆环面平行,上端盖2的第二上端圆平面与壳体3的第三上端向下同心圆环面之间的距离为第一距离,壳体3的两个第三螺纹盲孔的轴线所在平面与本发明系统质心距离为第二距离,第一距离和第二距离相同,下端盖4的第四下端圆平面与壳体3的第三下端向上同心圆环面接触。关于壳体3的两个第三螺纹盲孔的轴线所在平面位于本发明系统质心下端距离,主要考虑以下两发方面,既不能太长,导致本发明系统在通过质心调节完成翻转的过程中,由于质心偏移量太大,需要调节的尺寸过多,这部分尺寸未装填液相材料,为无效长度,避免无效长度过多,也不能太短,本发明系统在通过质心调节完成翻转的过程中,由于质心偏移量太小,质心稍微的调节,导致本发明系统在空中旋转角度过大,产生了过大的角速度及角加速度,导致过大的惯性,容易发生危险。通过实验发现,当壳体3的两个第三螺纹盲孔的轴线所在平面位于本发明系统质心下端不低于120mm时,质心偏移量足够,本发明系统在通过质心调节完成翻转的过程中,质心稍微的调节,本发明系统在空中旋转角度不大,产生了的角速度及角加速度不大,在可控制范围以内,满足安全要求。当壳体3的两个第三螺纹盲孔的轴线所在平面位于本发明系统质心下端不超过140mm时,心偏移量不算过大,需要调节的尺寸不算过大,无效长度不超过总长度2%,认为在可接受范围以内。因此,壳体3的两个第三螺纹盲孔的轴线所在平面位于本发明系统质心下端120~140mm;本实施例中,壳体3的两个第三螺纹盲孔的轴线所在平面位于本发明系统质心下端120。关于壳体3的第三环形凸台的上端面距离壳体3的第三螺纹盲孔的轴线距离与壳体3的第三螺纹盲孔公称直径之比,壳体3的第三环形凸台的下端面距离壳体3的第三螺纹盲孔的轴线距离与壳体3的第三螺纹盲孔公称直径之比,主要考虑一下2个方面:既不能太小,导致强度不足,当本发明系统由吊环5吊起时,全部重量,作用在吊环5上,而吊环5将所有重量作用在壳体3的第三环形凸台上,若该尺寸太小,会从壳体3的第三环形凸台处发生断裂,导致系统失效。通过实验发现,当壳体3的第三环形凸台的上端面距离壳体3的第三螺纹盲孔的轴线距离与壳体3的第三螺纹盲孔公称直径之比不低于1.4,壳体3的第三环形凸台的下端面距离壳体3的第三螺纹盲孔的轴线距离与壳体3的第三螺纹盲孔公称直径之比不低于1.1时,壳体3的第三环形凸台强度足够。也不能太大,导致液体材料抛撒后形成的云团由于壳体3的第三环形凸台尺寸过大而发生分层,由于壳体3的第三环形凸台相当于加强筋,当壳体3的第三环形凸台比较小时,对抛撒云团影响不大,云团在后续扩散的时候可以连接到一起。当壳体3的第三环形凸台尺寸比较大时,对抛撒云团影响过大,云团在后续扩散的时候不能连接到一起,形成了断层,影响使用效果。通过实验发现,当壳体3的第三环形凸台的上端面距离壳体3的第三螺纹盲孔的轴线距离与壳体3的第三螺纹盲孔公称直径之比不超过1.6,壳体3的第三环形凸台的下端面距离壳体3的第三螺纹盲孔的轴线距离与壳体3的第三螺纹盲孔公称直径之比不超过1.3时,对抛撒云团影响不大,云团在后续扩散的时候可以连接到一起。因此,壳体3的第三环形凸台的上端面距离壳体3的第三螺纹盲孔的轴线距离为壳体3的第三螺纹盲孔公称直径的1.4~1.6倍,壳体3的第三环形凸台的下端面距离壳体3的第三螺纹盲孔的轴线距离为壳体3的第三螺纹盲孔公称直径的1.1~1.3。本实施例中,壳体3的第三环形凸台的上端面距离壳体3的第三螺纹盲孔的轴线距离为壳体3的第三螺纹盲孔公称直径的1.4倍,壳体3的第三环形凸台的下端面距离壳体3的第三螺纹盲孔的轴线距离为壳体3的第三螺纹盲孔公称直径的1.1。壳体3的两个第三螺纹盲孔的轴线位于同一水平面,关于壳体3的两个第三螺纹盲孔的轴线的夹角,主要考虑一下3个方面:旋转灵敏性,初始起吊安稳性,起吊能力。旋转灵敏性为本发明系统的质心偏移后,本发明系统进行空间旋转的灵敏程度,当旋转灵敏性不好时,本发明系统的质心偏移后,由于本发明系统的质心和两个第三螺纹盲孔连线在竖直方向比较靠近,竖直方向投影几乎重合,导致质心变化后,没有一个偏心的力使得本发明系统进行旋转,这时本发明系统为失稳状态,一旦发生旋转,将是急速大角度旋转,不符合本发明慢速的旋转原则。当旋转灵敏性较好时,本发明系统的质心和两个第三螺纹盲孔连线在竖直方向有一定距离,当本发明系统的质心偏移后,重量乘以本发明系统的质心和两个第三螺纹盲孔连线在竖直方向的距离,为使得本发明系统旋转的力矩,本发明系统随着质心的变化,随即进行空间旋转,避免了失稳的状态。通过实际试验,将旋转灵敏性分为3个标准,以及3个分值。旋转十分灵敏:10分;旋转偶尔灵敏:3分;旋转十分不灵敏:-3分。初始起吊安稳性为本发明系统在通过吊车初始起吊时,安稳程度。主要与吊车初始起吊后,本发明系统的姿态与起吊前相比,旋转的角度。由于吊车将本发明系统起吊的过程中,本发明系统的姿态受重力作用,进行相应的旋转,希望此时旋转的角度越小越好。因为起吊过程不像后续使用过程,旋转的速度可以精确控制,而起吊过程属于简单粗暴过程,希望尽可能小的减小旋转角度,使得壳体只受到向上的力,而进行向上的运动,空间姿态尽可能少的旋转,这样旋转角速度和角加速度都比较小,可以保障壳体安全性。当初始起吊安稳性比较好时,壳体的质心距离2个吊环5连线竖直距离较小,本发明稍微旋转,壳体的质心便可以和2个吊环5连线竖直方向重合,这时,本发明系统已经稳定,稍微旋转的过程中,角速度角加速度均较小,不会发生危险。当初始起吊安稳性不好时,壳体的质心距离2个吊环5连线竖直距离较大,本发明需要旋转很大角度,壳体的质心才能和2个吊环5连线竖直方向重合,这时,本发明系统才能稳定,旋转很大角度的过程中,角速度角加速度均较大,会发生危险。通过实际试验,将初始起吊安稳性分为3个标准,以及3个分值。旋转角度不超过3°:10分;旋转角度3°~10°:5分;旋转角度超过10°:0分。起吊能力为2个吊环5可以起吊的本发明系统的重量多少的能力。由于2个吊环5呈一定角度,起吊时,2个吊环5既承受剪切力,又承受弯转力矩,又承受拉力,应力状态十分复杂,多应力状态下,2个吊环5能承受的本发明系统的重力低于2个吊环实际的抗纯剪切能力。当本发明的结构使得起吊能力较好时,2个吊环5承受的力主要为剪切力,旋转弯矩和拉力均较小,这时,2个吊环5能起吊的本发明的重量接近2个吊环5实际的抗纯剪切能力。当本发明的结构使得起吊能力不好时,2个吊环5承受的力为剪切力、旋转弯矩和拉力均的混合作用,很容易达到2个吊环5母材的极限强度,这时,2个吊环5能起吊的本发明的重量很低,仅为2个吊环5实际的抗纯剪切能力的很小一部分,这时起吊时容易发生危险。通过实际试验,将起吊能力分为3个标准,以及3个分值。起吊重量为实际的抗纯剪切能力的80%以上:10分;起吊重量为实际的抗纯剪切能力的80%~60%:6分;起吊重量为实际的抗纯剪切能力的60%以下:2分。将壳体3的两个第三螺纹盲孔的轴线的夹角分为以下几个区间:179°~180°、178°~179°、177°~178°、176°~177°、175°~176°、174°~175°、173°~174°、172°~173°、171°~172°、170°~171°。分别对以上几个区间的壳体3的两个第三螺纹盲孔的轴线的夹角进行实验,并按照以上三项标准进行评价,获得分值如下:壳体3的两个第三螺纹盲孔的轴线的夹角旋转灵敏性初始起吊安稳性起吊能力总分179°~180°-3101017178°~179°3101023177°~178°10101030176°~177°10101030175°~176°1051025174°~175°105621173°~174°105621172°~173°105621171°~172°100616170°~171°100212通过实验发现,当壳体3的两个第三螺纹盲孔的轴线的夹角为176°~178°时,获得分值最高,获得30分。因此,壳体3的两个第三螺纹盲孔的轴线的夹角为176°~178°。本实施例中,壳体3的两个第三螺纹盲孔的轴线的夹角为176°。本发明左边放置一个测试装置,测试装置分别与抛撒管1、下端盖4、充气管7的第七开关连接,测试装置可以检测充气管7内气体的流速,测试装置可以检测抛撒管1和下端盖4的运动速度,当测试装置检测到抛撒管1或下端盖4由运动突然停止时,而充气管7内气体仍有流速,则测试装置立即关闭充气管7的第七开关,由于当抛撒管1或下端盖4运动过程中突然停止时,极容易发生的现象为运动卡死现象,这时,继续通入高压气体,将会使得本发明的装置破坏,因此,当抛撒管1或下端盖4运动突然停止,需要判断,是否充气管7内气体仍有流速,如有流速,而抛撒管1或下端盖4不再运动,则为危险状态,立即关闭充气管7的第七开关,避免压力过大造成的危险;壳体3的第三外圆柱面的圆柱度不超过0.09mm,壳体3的第三外圆柱面的圆柱度若更大,则上端盖2和下端盖4在壳体3内部运动过程中,会因为配合不紧密,而发生泄漏,或者运动停滞,通过实验发现,当壳体3的第三外圆柱面的圆柱度不超过0.09mm时,可以满足密封和运动要求;所述一种通过质心位置调节进行自动翻转的十吨级液相材料装填壳体,包括以下步骤:步骤1:将壳体3放在水平台上,使得壳体3的回转体轴线垂直于水平面;步骤2:将下端盖4与壳体3装配;步骤3:将抛撒管1与壳体3装配;步骤4:将上端盖2与壳体3装配;步骤5:将吊环5与壳体3装配;步骤6:将充气管7与壳体3装配;步骤7:将临时挡板8与壳体3装配;步骤8:将定位螺钉9与壳体3装配,定位螺钉9的下端与壳体3的第三上端向下同心圆环面平齐;步骤9:将液体6灌入抛撒管1的第一外圆柱面、上端盖2的第二下端同心圆平面、壳体3的第三内圆柱面和下端盖4的第四上端圆平面组成的封闭空间中;步骤10:将吊绳穿过吊环5的第五圆环体,再将吊绳挂在吊车上,通过吊车将壳体3吊起,使得临时挡板8与地面脱离;步骤11:将本发明的系统由起立姿态转变为躺下姿态:将充气管7的第七圆管的左端与高压空气泵连接,打开充气管7的第七开关,使高压空气进入下端盖4的第四下端圆平面、壳体3的第三下端内圆柱面和临时挡板8的第八上端圆平面组成的封闭空间中,通过高压气体挤压下端盖4,下端盖4再将压力传递给抛撒管1和液体6,液体6再将压力传递给上端盖2,使得抛撒管1、上端盖2、下端盖4和液体6同时向上移动,本发明的系统质心逐渐上移,本发明系统的姿态随着质心的上移逐渐由起立姿态转变为躺下姿态,待抛撒管1的回转体轴线与水平面平行,关闭充气管7的第七开关,断开充气管7的第七圆管的左端与高压空气泵的连接;步骤12:将本发明的系统由躺下姿态转变为起立姿态:打开充气管7的第七开关,放出下端盖4的第四下端圆平面、壳体3的第三下端内圆柱面和临时挡板8的第八上端圆平面组成的封闭空间中的高压气体,将充气管7的第七圆管的左端与真空泵连接,对下端盖4的第四下端圆平面、壳体3的第三下端内圆柱面和临时挡板8的第八上端圆平面组成的封闭空间进行抽真空,使得下端盖4的第四下端圆平面受到负压,下端盖4再将负压传递给抛撒管1和液体6,液体6再将负压传递给上端盖2,使得抛撒管1、上端盖2、下端盖4和液体6同时向靠近临时挡板8的方向移动,本发明的系统质心逐渐靠近临时挡板8,本发明系统的姿态随着质心的靠近临时挡板8逐渐由躺下姿态转变为起立姿态,待抛撒管1的回转体轴线与水平面垂直,关闭充气管7的第七开关,断开充气管7的第七圆管的左端与真空泵的连接;步骤13:将定位螺钉9拧紧,通过定位螺钉9挤压上端盖2的第二上端同心圆平面,固定上端盖2的位置,使得上端盖2与壳体3不能再发生相对运动,卸下临时挡板8,此时,本发明的系统完成实验前准备。使用原方案的翻转车进行壳体的从躺下姿态到起立姿态,及从起立姿态到躺下姿态的翻转实验,实验壳体重量为十吨,实验壳体内部状体液相材料,壳体厚度不超过10mm,为薄壁壳体,反复翻转实验结果如下:实验状态实验结果10mm壳体从起立姿态到躺下姿态壳体完好10mm壳体从躺下姿态到起立姿态壳体完好9mm壳体从起立姿态到躺下姿态壳体完好9mm壳体从躺下姿态到起立姿态壳体完好8mm壳体从起立姿态到躺下姿态壳体完好8mm壳体从躺下姿态到起立姿态壳体发生破坏7.5mm壳体从躺下姿态到起立姿态壳体发生破坏7.5mm壳体从躺下姿态到起立姿态无法进行7mm壳体从躺下姿态到起立姿态壳体发生破坏7mm壳体从躺下姿态到起立姿态无法进行6mm壳体从躺下姿态到起立姿态壳体发生破坏6mm壳体从躺下姿态到起立姿态无法进行5mm壳体从躺下姿态到起立姿态壳体发生破坏5mm壳体从躺下姿态到起立姿态无法进行分析可知,当壳体壁厚为8mm时,壳体从起立姿态到躺下姿态,壳体完好,但是壳体从躺下姿态到起立姿态便发生破坏,而壳体壁厚不超过7.5mm时,壳体从起立姿态到躺下姿态,便发生破坏。壳体壁厚至少为9mm时,才能确保从起立姿态到躺下姿态以及从躺下姿态到起立姿态均壳体完好。使用本发明的装置及方法,按照步骤1到步骤13,反复进行从躺下姿态到起立姿态,及从起立姿态到躺下姿态的翻转实验,实验壳体重量为十吨,实验壳体内部状体液相材料,壳体厚度为5mm,为薄壁壳体,反复翻转实验结果如下:分析可知,总重量为10吨的液相材料装填薄壁壳体,壳体壁厚5mm,连续进行十次由起立姿态到躺下姿态,再由躺下姿态到起立姿态的翻转实验,壳体完好。对于十吨级装填液相材料的薄壁壳体,使用本发明进行翻转,壳体壁厚可以减少至原翻转方案的55%,大幅度降低了壳体壁厚,减少了壳体壁厚对抛撒范围的影响,增加了产品的使用效果。本发明的一种通过质心位置调节进行自动翻转的十吨级液相材料装填壳体,首先将装填液相材料的薄壁壳体在中部加强筋位置吊起来,通过调节壳体质心位置,使得壳体的空间姿态随着质心的变化进行自适应调整,逐渐完成从躺下姿态到起立姿态,或从起立姿态到躺下姿态的翻转工作。整个翻转过程为壳体在重力作用下自动完成,无需外力作用在壳体外壁上。壳体质心的调节可以精确控制,因此,壳体翻转过程中的速度可以精确控制,壳体翻转过程速度均匀且缓慢,避免了速度突变,避免了过大动载荷,保证了壳体强度不受破坏,进而保证了产品的安全性和可靠性。实施例4:如图1所示,本实施例给出一种通过质心位置调节进行自动翻转的十吨级液相材料装填壳体,包括抛撒管1,上端盖2,下端盖4,液体6,其特征在于还包括壳体3,吊环5,充气管7,临时挡板8,定位螺钉9;抛撒管1为第一圆柱体,抛撒管1的第一圆柱体为回转体,抛撒管1的第一圆柱体的上端面为第一上端圆平面,抛撒管1的第一圆柱体的侧面为第一外圆柱面,抛撒管1的第一圆柱体的下端面为第一下端圆平面;抛撒管1的回转体轴线与水平面垂直,抛撒管1的内部装有炸药,抛撒管1内部的炸药为抛撒液相材料形成云团的能量源;上端盖2为第二圆板,上端盖2的第二圆板为回转体,上端盖2的第二圆板中心带有第二圆孔,上端盖2的第二圆板的上端面为第二上端同心圆平面,上端盖2的第二圆板的外侧面为第二外圆柱面,上端盖2的第二圆板的下端面为第二下端同心圆平面,上端盖2的第二圆孔的内侧面为第二内圆柱面;上端盖2的回转体轴线与抛撒管1的回转体轴线重合,上端盖2位于抛撒管1上端外部,上端盖2的第二内圆柱面与抛撒管1的第一外圆柱面上端接触,上端盖2的第二上端同心圆平面与抛撒管1的第一上端圆平面共面;壳体3为第三圆筒体,壳体3的第三圆筒体为回转体,壳体3的第三圆筒体的外侧面为第三外圆柱面,壳体3的第三圆筒体的内侧面为第三内圆柱面,壳体3的第三圆筒体上端内侧带有第三上端内法兰,壳体3的第三上端内法兰下端面为第三上端向下同心圆环面,壳体3的第三上端内法兰上带有十六个第三螺纹通孔,壳体3的十六个第三螺纹通孔轴线与壳体3的回转体轴线平行,壳体3的十六个第三螺纹通孔绕壳体3的回转体轴线均匀分布,壳体3的第三圆筒体下端内侧带有第三下端内法兰,壳体3的第三下端内法兰上端面为第三下端向上同心圆环面,壳体3的第三下端内法兰下端面为第三下端向下同心圆环面,壳体3的第三下端内法兰的内侧面为第三下端内圆柱面,壳体3的第三下端内法兰上带有一个第三圆形通孔,壳体3的第三圆形通孔轴线与壳体3的回转体轴线垂直,壳体3的第三内圆柱面中部带有第三环形凸台,壳体3的第三外圆柱面中部带有两个第三螺纹盲孔,壳体3的两个第三螺纹盲孔的轴线均垂直于壳体3的回转体轴线;壳体3的回转体轴线与抛撒管1的回转体轴线重合,上端盖2的第二圆板位于壳体3的第三圆筒体内部,上端盖2的第二上端圆平面位于壳体3的第三上端向下同心圆环面下端,壳体3的第三内圆柱面与上端盖2的第二外圆柱面滑动配合接触;下端盖4为第四圆板,下端盖4的第四圆板为回转体,下端盖4的第四圆板的上端面为第四上端圆平面,下端盖4的第四圆板的外侧面为第四外圆柱面,下端盖4的第四圆板的下端面为第四下端圆平面;下端盖4的回转体轴线与抛撒管1的回转体轴线重合,下端盖4的第四上端圆平面与抛撒管1的第一下端圆平面连接,下端盖4的第四圆板位于壳体3的第三圆筒体内部,下端盖4的第四下端圆平面位于壳体3的第三下端向上同心圆环面上端,壳体3的第三内圆柱面与下端盖4的第四外圆柱面滑动配合接触;吊环5由左右两部分组成,吊环5的右部分为第五圆柱体,吊环5的第五圆柱体为回转体,吊环5的第五圆柱体的侧面带有第五外螺纹,吊环5的左部分为第五圆环体,吊环5的第五圆柱体和吊环5的第五圆环体转动配合连接,吊环5共两个;吊环5的第五圆柱体的回转体轴线与抛撒管1的回转体轴线垂直,吊环5的第五外螺纹安装在壳体3的第三螺纹盲孔中;液体6为被炸药抛撒后形成云团的液相材料;液体6位于抛撒管1的第一外圆柱面、上端盖2的第二下端同心圆平面、壳体3的第三内圆柱面和下端盖4的第四上端圆平面组成的封闭空间中;充气管7为第七圆管,充气管7的第七圆管为回转体,充气管7的第七圆管左端带有第七开关;充气管7的回转体轴线与抛撒管1的回转体轴线垂直,充气管7的第七圆管右端与壳体3的第三圆形通孔连接;临时挡板8为第八圆板,临时挡板8的第八圆板为回转体,临时挡板8的第八圆板的上端面为第八上端圆平面;临时挡板8的回转体轴线与抛撒管1的回转体轴线重合,临时挡板8位于壳体3下端,临时挡板8的第八上端圆平面与壳体3的第三下端向下同心圆环面连接;定位螺钉9为第九圆柱体,定位螺钉9的第九圆柱体为回转体,定位螺钉9的第九圆柱体的侧面为第九外圆柱面,定位螺钉9的第九外圆柱面下端带有第九外螺纹,定位螺钉9共十六个;定位螺钉9的回转体轴线与抛撒管1的回转体轴线平行,定位螺钉9的第九外螺纹安装在壳体3的第三螺纹通孔中。关于上端盖2的第二外圆柱面的轴向长度与上端盖2的第二圆板直径之比,主要考虑以下几个因素,既不能太大,以免增加上端盖2不必要的呆重,又不能太小以免上端盖2移动时卡主。通过实验发现,上端盖2在壳体3内部反复移动过程中,当厚度比较小的时候,容易出现卡主现象,一旦卡主,再大的挤压力也无法使其继续运动,而挤压力过大会作用在壳体3上,将壳体3挤破,导致失败。而当上端盖2的第二外圆柱面的轴向长度与上端盖2的第二圆板直径之比不低于1:10时,上端盖2的厚度足够,上端盖2在壳体3内部反复移动过程中,不再出现卡主的问题。上端盖2的重量随着厚度的增加而增大,对于液体材料装填壳体,总重量为10吨级,壳体翻转过程中的难度就在于,总重量太大,翻转惯性大,从而导致壳体承受的压力太大,容易发生破坏,上端盖2的重量过大,只会产生负面效果。因此,上端盖2的厚度越低越好。通过实测实验可知,当上端盖2的第二外圆柱面的轴向长度与上端盖2的第二圆板直径之比不超过1:9时,上端盖2的重量不到总重量的4%,认为不超过4%的上端盖重量在可接受范围以内,因此,上端盖2的第二外圆柱面的轴向长度与上端盖2的第二圆板直径之比不超过1:9。因此,上端盖2的第二外圆柱面的轴向长度与上端盖2的第二圆板直径之比为1:9~10;本实施例中,上端盖2的第二外圆柱面的轴向长度与上端盖2的第二圆板直径之比为1:9。下端盖4的设计同理,下端盖4的第四外圆柱面的轴向长度与下端盖4的第四圆板直径之比为1:9~10;本实施例中,下端盖4的第四外圆柱面的轴向长度与下端盖4的第四圆板直径之比为1:9。上端盖2的第二上端圆平面与壳体3的第三上端向下同心圆环面平行,上端盖2的第二上端圆平面与壳体3的第三上端向下同心圆环面之间的距离为第一距离,壳体3的两个第三螺纹盲孔的轴线所在平面与本发明系统质心距离为第二距离,第一距离和第二距离相同,下端盖4的第四下端圆平面与壳体3的第三下端向上同心圆环面接触。关于壳体3的两个第三螺纹盲孔的轴线所在平面位于本发明系统质心下端距离,主要考虑以下两发方面,既不能太长,导致本发明系统在通过质心调节完成翻转的过程中,由于质心偏移量太大,需要调节的尺寸过多,这部分尺寸未装填液相材料,为无效长度,避免无效长度过多,也不能太短,本发明系统在通过质心调节完成翻转的过程中,由于质心偏移量太小,质心稍微的调节,导致本发明系统在空中旋转角度过大,产生了过大的角速度及角加速度,导致过大的惯性,容易发生危险。通过实验发现,当壳体3的两个第三螺纹盲孔的轴线所在平面位于本发明系统质心下端不低于120mm时,质心偏移量足够,本发明系统在通过质心调节完成翻转的过程中,质心稍微的调节,本发明系统在空中旋转角度不大,产生了的角速度及角加速度不大,在可控制范围以内,满足安全要求。当壳体3的两个第三螺纹盲孔的轴线所在平面位于本发明系统质心下端不超过140mm时,心偏移量不算过大,需要调节的尺寸不算过大,无效长度不超过总长度2%,认为在可接受范围以内。因此,壳体3的两个第三螺纹盲孔的轴线所在平面位于本发明系统质心下端120~140mm;本实施例中,壳体3的两个第三螺纹盲孔的轴线所在平面位于本发明系统质心下端120。关于壳体3的第三环形凸台的上端面距离壳体3的第三螺纹盲孔的轴线距离与壳体3的第三螺纹盲孔公称直径之比,壳体3的第三环形凸台的下端面距离壳体3的第三螺纹盲孔的轴线距离与壳体3的第三螺纹盲孔公称直径之比,主要考虑一下2个方面:既不能太小,导致强度不足,当本发明系统由吊环5吊起时,全部重量,作用在吊环5上,而吊环5将所有重量作用在壳体3的第三环形凸台上,若该尺寸太小,会从壳体3的第三环形凸台处发生断裂,导致系统失效。通过实验发现,当壳体3的第三环形凸台的上端面距离壳体3的第三螺纹盲孔的轴线距离与壳体3的第三螺纹盲孔公称直径之比不低于1.4,壳体3的第三环形凸台的下端面距离壳体3的第三螺纹盲孔的轴线距离与壳体3的第三螺纹盲孔公称直径之比不低于1.1时,壳体3的第三环形凸台强度足够。也不能太大,导致液体材料抛撒后形成的云团由于壳体3的第三环形凸台尺寸过大而发生分层,由于壳体3的第三环形凸台相当于加强筋,当壳体3的第三环形凸台比较小时,对抛撒云团影响不大,云团在后续扩散的时候可以连接到一起。当壳体3的第三环形凸台尺寸比较大时,对抛撒云团影响过大,云团在后续扩散的时候不能连接到一起,形成了断层,影响使用效果。通过实验发现,当壳体3的第三环形凸台的上端面距离壳体3的第三螺纹盲孔的轴线距离与壳体3的第三螺纹盲孔公称直径之比不超过1.6,壳体3的第三环形凸台的下端面距离壳体3的第三螺纹盲孔的轴线距离与壳体3的第三螺纹盲孔公称直径之比不超过1.3时,对抛撒云团影响不大,云团在后续扩散的时候可以连接到一起。因此,壳体3的第三环形凸台的上端面距离壳体3的第三螺纹盲孔的轴线距离为壳体3的第三螺纹盲孔公称直径的1.4~1.6倍,壳体3的第三环形凸台的下端面距离壳体3的第三螺纹盲孔的轴线距离为壳体3的第三螺纹盲孔公称直径的1.1~1.3。本实施例中,壳体3的第三环形凸台的上端面距离壳体3的第三螺纹盲孔的轴线距离为壳体3的第三螺纹盲孔公称直径的1.4倍,壳体3的第三环形凸台的下端面距离壳体3的第三螺纹盲孔的轴线距离为壳体3的第三螺纹盲孔公称直径的1.1。壳体3的两个第三螺纹盲孔的轴线位于同一水平面,关于壳体3的两个第三螺纹盲孔的轴线的夹角,主要考虑一下3个方面:旋转灵敏性,初始起吊安稳性,起吊能力。旋转灵敏性为本发明系统的质心偏移后,本发明系统进行空间旋转的灵敏程度,当旋转灵敏性不好时,本发明系统的质心偏移后,由于本发明系统的质心和两个第三螺纹盲孔连线在竖直方向比较靠近,竖直方向投影几乎重合,导致质心变化后,没有一个偏心的力使得本发明系统进行旋转,这时本发明系统为失稳状态,一旦发生旋转,将是急速大角度旋转,不符合本发明慢速的旋转原则。当旋转灵敏性较好时,本发明系统的质心和两个第三螺纹盲孔连线在竖直方向有一定距离,当本发明系统的质心偏移后,重量乘以本发明系统的质心和两个第三螺纹盲孔连线在竖直方向的距离,为使得本发明系统旋转的力矩,本发明系统随着质心的变化,随即进行空间旋转,避免了失稳的状态。通过实际试验,将旋转灵敏性分为3个标准,以及3个分值。旋转十分灵敏:10分;旋转偶尔灵敏:3分;旋转十分不灵敏:-3分。初始起吊安稳性为本发明系统在通过吊车初始起吊时,安稳程度。主要与吊车初始起吊后,本发明系统的姿态与起吊前相比,旋转的角度。由于吊车将本发明系统起吊的过程中,本发明系统的姿态受重力作用,进行相应的旋转,希望此时旋转的角度越小越好。因为起吊过程不像后续使用过程,旋转的速度可以精确控制,而起吊过程属于简单粗暴过程,希望尽可能小的减小旋转角度,使得壳体只受到向上的力,而进行向上的运动,空间姿态尽可能少的旋转,这样旋转角速度和角加速度都比较小,可以保障壳体安全性。当初始起吊安稳性比较好时,壳体的质心距离2个吊环5连线竖直距离较小,本发明稍微旋转,壳体的质心便可以和2个吊环5连线竖直方向重合,这时,本发明系统已经稳定,稍微旋转的过程中,角速度角加速度均较小,不会发生危险。当初始起吊安稳性不好时,壳体的质心距离2个吊环5连线竖直距离较大,本发明需要旋转很大角度,壳体的质心才能和2个吊环5连线竖直方向重合,这时,本发明系统才能稳定,旋转很大角度的过程中,角速度角加速度均较大,会发生危险。通过实际试验,将初始起吊安稳性分为3个标准,以及3个分值。旋转角度不超过3°:10分;旋转角度3°~10°:5分;旋转角度超过10°:0分。起吊能力为2个吊环5可以起吊的本发明系统的重量多少的能力。由于2个吊环5呈一定角度,起吊时,2个吊环5既承受剪切力,又承受弯转力矩,又承受拉力,应力状态十分复杂,多应力状态下,2个吊环5能承受的本发明系统的重力低于2个吊环实际的抗纯剪切能力。当本发明的结构使得起吊能力较好时,2个吊环5承受的力主要为剪切力,旋转弯矩和拉力均较小,这时,2个吊环5能起吊的本发明的重量接近2个吊环5实际的抗纯剪切能力。当本发明的结构使得起吊能力不好时,2个吊环5承受的力为剪切力、旋转弯矩和拉力均的混合作用,很容易达到2个吊环5母材的极限强度,这时,2个吊环5能起吊的本发明的重量很低,仅为2个吊环5实际的抗纯剪切能力的很小一部分,这时起吊时容易发生危险。通过实际试验,将起吊能力分为3个标准,以及3个分值。起吊重量为实际的抗纯剪切能力的80%以上:10分;起吊重量为实际的抗纯剪切能力的80%~60%:6分;起吊重量为实际的抗纯剪切能力的60%以下:2分。将壳体3的两个第三螺纹盲孔的轴线的夹角分为以下几个区间:179°~180°、178°~179°、177°~178°、176°~177°、175°~176°、174°~175°、173°~174°、172°~173°、171°~172°、170°~171°。分别对以上几个区间的壳体3的两个第三螺纹盲孔的轴线的夹角进行实验,并按照以上三项标准进行评价,获得分值如下:壳体3的两个第三螺纹盲孔的轴线的夹角旋转灵敏性初始起吊安稳性起吊能力总分179°~180°-3101017178°~179°3101023177°~178°10101030176°~177°10101030175°~176°1051025174°~175°105621173°~174°105621172°~173°105621171°~172°100616170°~171°100212通过实验发现,当壳体3的两个第三螺纹盲孔的轴线的夹角为176°~178°时,获得分值最高,获得30分。因此,壳体3的两个第三螺纹盲孔的轴线的夹角为176°~178°。本实施例中,壳体3的两个第三螺纹盲孔的轴线的夹角为176°。吊环5的第五圆柱体和吊环5的第五圆环体的转动配合连接之处安装一个阻尼装置,该阻尼装置可以限制吊环5的第五圆柱体和吊环5的第五圆环体相对运动速度,使得吊环5的第五圆柱体和吊环5的第五圆环体只能以最大0.02弧度每秒的相对速度进行转动,这样避免了本发明的装置在旋转过程中,因为速度过大造成的惯性过大的风险,使得本发明只能以较低速度进行旋转,提高了安全性;所述一种通过质心位置调节进行自动翻转的十吨级液相材料装填壳体,包括以下步骤:步骤1:壳体3的毛坯先用普通车床进行车削加工,装夹壳体3下端,用45度偏刀加工壳体3上端和外圆,再用90度偏刀加工壳体3上端内孔,再装夹壳体3上端,用45度偏刀加工壳体3下端和外圆,再用90度偏刀加工壳体3下端内孔;精车后的壳体3用普通铣床进行铣削加工,用分度头加工壳体3下端,用钻头加工壳体3的十六个第三螺纹通孔的底孔,再用圆盘卡主壳体3上端,用顶尖顶住圆盘,用钻头加工壳体3的第三螺纹盲孔的底孔,再用丝锥加工第三螺纹通孔和第三螺纹盲孔,通过对加工顺序的控制,提高加工零件的精度;将壳体3放在水平台上,使得壳体3的回转体轴线垂直于水平面;步骤2:将下端盖4与壳体3装配;步骤3:将抛撒管1与壳体3装配;步骤4:将上端盖2与壳体3装配;步骤5:将吊环5与壳体3装配;步骤6:将充气管7与壳体3装配;步骤7:将临时挡板8与壳体3装配;步骤8:将定位螺钉9与壳体3装配,定位螺钉9的下端与壳体3的第三上端向下同心圆环面平齐;步骤9:将液体6灌入抛撒管1的第一外圆柱面、上端盖2的第二下端同心圆平面、壳体3的第三内圆柱面和下端盖4的第四上端圆平面组成的封闭空间中;步骤10:将吊绳穿过吊环5的第五圆环体,再将吊绳挂在吊车上,通过吊车将壳体3吊起,使得临时挡板8与地面脱离;步骤11:将本发明的系统由起立姿态转变为躺下姿态:将充气管7的第七圆管的左端与高压空气泵连接,打开充气管7的第七开关,使高压空气进入下端盖4的第四下端圆平面、壳体3的第三下端内圆柱面和临时挡板8的第八上端圆平面组成的封闭空间中,通过高压气体挤压下端盖4,下端盖4再将压力传递给抛撒管1和液体6,液体6再将压力传递给上端盖2,使得抛撒管1、上端盖2、下端盖4和液体6同时向上移动,本发明的系统质心逐渐上移,本发明系统的姿态随着质心的上移逐渐由起立姿态转变为躺下姿态,待抛撒管1的回转体轴线与水平面平行,关闭充气管7的第七开关,断开充气管7的第七圆管的左端与高压空气泵的连接;步骤12:将本发明的系统由躺下姿态转变为起立姿态:打开充气管7的第七开关,放出下端盖4的第四下端圆平面、壳体3的第三下端内圆柱面和临时挡板8的第八上端圆平面组成的封闭空间中的高压气体,将充气管7的第七圆管的左端与真空泵连接,对下端盖4的第四下端圆平面、壳体3的第三下端内圆柱面和临时挡板8的第八上端圆平面组成的封闭空间进行抽真空,使得下端盖4的第四下端圆平面受到负压,下端盖4再将负压传递给抛撒管1和液体6,液体6再将负压传递给上端盖2,使得抛撒管1、上端盖2、下端盖4和液体6同时向靠近临时挡板8的方向移动,本发明的系统质心逐渐靠近临时挡板8,本发明系统的姿态随着质心的靠近临时挡板8逐渐由躺下姿态转变为起立姿态,待抛撒管1的回转体轴线与水平面垂直,关闭充气管7的第七开关,断开充气管7的第七圆管的左端与真空泵的连接;步骤13:将定位螺钉9拧紧,通过定位螺钉9挤压上端盖2的第二上端同心圆平面,固定上端盖2的位置,使得上端盖2与壳体3不能再发生相对运动,卸下临时挡板8,此时,本发明的系统完成实验前准备。使用原方案的翻转车进行壳体的从躺下姿态到起立姿态,及从起立姿态到躺下姿态的翻转实验,实验壳体重量为十吨,实验壳体内部状体液相材料,壳体厚度不超过10mm,为薄壁壳体,反复翻转实验结果如下:分析可知,当壳体壁厚为8mm时,壳体从起立姿态到躺下姿态,壳体完好,但是壳体从躺下姿态到起立姿态便发生破坏,而壳体壁厚不超过7.5mm时,壳体从起立姿态到躺下姿态,便发生破坏。壳体壁厚至少为9mm时,才能确保从起立姿态到躺下姿态以及从躺下姿态到起立姿态均壳体完好。使用本发明的装置及方法,按照步骤1到步骤13,反复进行从躺下姿态到起立姿态,及从起立姿态到躺下姿态的翻转实验,实验壳体重量为十吨,实验壳体内部状体液相材料,壳体厚度为5mm,为薄壁壳体,反复翻转实验结果如下:实验状态实验结果第1次从起立姿态到躺下姿态壳体完好第1次从躺下姿态到起立姿态壳体完好第2次从起立姿态到躺下姿态壳体完好第2次从躺下姿态到起立姿态壳体完好第3次从起立姿态到躺下姿态壳体完好第3次从躺下姿态到起立姿态壳体完好第4次从起立姿态到躺下姿态壳体完好第4次从躺下姿态到起立姿态壳体完好第5次从起立姿态到躺下姿态壳体完好第5次从躺下姿态到起立姿态壳体完好第6次从起立姿态到躺下姿态壳体完好第6次从躺下姿态到起立姿态壳体完好第7次从起立姿态到躺下姿态壳体完好第7次从躺下姿态到起立姿态壳体完好第8次从起立姿态到躺下姿态壳体完好第8次从躺下姿态到起立姿态壳体完好第9次从起立姿态到躺下姿态壳体完好第9次从躺下姿态到起立姿态壳体完好第10次从起立姿态到躺下姿态壳体完好第10次从躺下姿态到起立姿态壳体完好分析可知,总重量为10吨的液相材料装填薄壁壳体,壳体壁厚5mm,连续进行十次由起立姿态到躺下姿态,再由躺下姿态到起立姿态的翻转实验,壳体完好。对于十吨级装填液相材料的薄壁壳体,使用本发明进行翻转,壳体壁厚可以减少至原翻转方案的55%,大幅度降低了壳体壁厚,减少了壳体壁厚对抛撒范围的影响,增加了产品的使用效果。本发明的一种通过质心位置调节进行自动翻转的十吨级液相材料装填壳体,首先将装填液相材料的薄壁壳体在中部加强筋位置吊起来,通过调节壳体质心位置,使得壳体的空间姿态随着质心的变化进行自适应调整,逐渐完成从躺下姿态到起立姿态,或从起立姿态到躺下姿态的翻转工作。整个翻转过程为壳体在重力作用下自动完成,无需外力作用在壳体外壁上。壳体质心的调节可以精确控制,因此,壳体翻转过程中的速度可以精确控制,壳体翻转过程速度均匀且缓慢,避免了速度突变,避免了过大动载荷,保证了壳体强度不受破坏,进而保证了产品的安全性和可靠性。实施例5:如图1所示,本实施例给出一种通过质心位置调节进行自动翻转的十吨级液相材料装填壳体,包括抛撒管1,上端盖2,下端盖4,液体6,其特征在于还包括壳体3,吊环5,充气管7,临时挡板8,定位螺钉9;抛撒管1为第一圆柱体,抛撒管1的第一圆柱体为回转体,抛撒管1的第一圆柱体的上端面为第一上端圆平面,抛撒管1的第一圆柱体的侧面为第一外圆柱面,抛撒管1的第一圆柱体的下端面为第一下端圆平面;抛撒管1的回转体轴线与水平面垂直,抛撒管1的内部装有炸药,抛撒管1内部的炸药为抛撒液相材料形成云团的能量源;上端盖2为第二圆板,上端盖2的第二圆板为回转体,上端盖2的第二圆板中心带有第二圆孔,上端盖2的第二圆板的上端面为第二上端同心圆平面,上端盖2的第二圆板的外侧面为第二外圆柱面,上端盖2的第二圆板的下端面为第二下端同心圆平面,上端盖2的第二圆孔的内侧面为第二内圆柱面;上端盖2的回转体轴线与抛撒管1的回转体轴线重合,上端盖2位于抛撒管1上端外部,上端盖2的第二内圆柱面与抛撒管1的第一外圆柱面上端接触,上端盖2的第二上端同心圆平面与抛撒管1的第一上端圆平面共面;壳体3为第三圆筒体,壳体3的第三圆筒体为回转体,壳体3的第三圆筒体的外侧面为第三外圆柱面,壳体3的第三圆筒体的内侧面为第三内圆柱面,壳体3的第三圆筒体上端内侧带有第三上端内法兰,壳体3的第三上端内法兰下端面为第三上端向下同心圆环面,壳体3的第三上端内法兰上带有十六个第三螺纹通孔,壳体3的十六个第三螺纹通孔轴线与壳体3的回转体轴线平行,壳体3的十六个第三螺纹通孔绕壳体3的回转体轴线均匀分布,壳体3的第三圆筒体下端内侧带有第三下端内法兰,壳体3的第三下端内法兰上端面为第三下端向上同心圆环面,壳体3的第三下端内法兰下端面为第三下端向下同心圆环面,壳体3的第三下端内法兰的内侧面为第三下端内圆柱面,壳体3的第三下端内法兰上带有一个第三圆形通孔,壳体3的第三圆形通孔轴线与壳体3的回转体轴线垂直,壳体3的第三内圆柱面中部带有第三环形凸台,壳体3的第三外圆柱面中部带有两个第三螺纹盲孔,壳体3的两个第三螺纹盲孔的轴线均垂直于壳体3的回转体轴线;壳体3的回转体轴线与抛撒管1的回转体轴线重合,上端盖2的第二圆板位于壳体3的第三圆筒体内部,上端盖2的第二上端圆平面位于壳体3的第三上端向下同心圆环面下端,壳体3的第三内圆柱面与上端盖2的第二外圆柱面滑动配合接触;下端盖4为第四圆板,下端盖4的第四圆板为回转体,下端盖4的第四圆板的上端面为第四上端圆平面,下端盖4的第四圆板的外侧面为第四外圆柱面,下端盖4的第四圆板的下端面为第四下端圆平面;下端盖4的回转体轴线与抛撒管1的回转体轴线重合,下端盖4的第四上端圆平面与抛撒管1的第一下端圆平面连接,下端盖4的第四圆板位于壳体3的第三圆筒体内部,下端盖4的第四下端圆平面位于壳体3的第三下端向上同心圆环面上端,壳体3的第三内圆柱面与下端盖4的第四外圆柱面滑动配合接触;吊环5由左右两部分组成,吊环5的右部分为第五圆柱体,吊环5的第五圆柱体为回转体,吊环5的第五圆柱体的侧面带有第五外螺纹,吊环5的左部分为第五圆环体,吊环5的第五圆柱体和吊环5的第五圆环体转动配合连接,吊环5共两个;吊环5的第五圆柱体的回转体轴线与抛撒管1的回转体轴线垂直,吊环5的第五外螺纹安装在壳体3的第三螺纹盲孔中;液体6为被炸药抛撒后形成云团的液相材料;液体6位于抛撒管1的第一外圆柱面、上端盖2的第二下端同心圆平面、壳体3的第三内圆柱面和下端盖4的第四上端圆平面组成的封闭空间中;充气管7为第七圆管,充气管7的第七圆管为回转体,充气管7的第七圆管左端带有第七开关;充气管7的回转体轴线与抛撒管1的回转体轴线垂直,充气管7的第七圆管右端与壳体3的第三圆形通孔连接;临时挡板8为第八圆板,临时挡板8的第八圆板为回转体,临时挡板8的第八圆板的上端面为第八上端圆平面;临时挡板8的回转体轴线与抛撒管1的回转体轴线重合,临时挡板8位于壳体3下端,临时挡板8的第八上端圆平面与壳体3的第三下端向下同心圆环面连接;定位螺钉9为第九圆柱体,定位螺钉9的第九圆柱体为回转体,定位螺钉9的第九圆柱体的侧面为第九外圆柱面,定位螺钉9的第九外圆柱面下端带有第九外螺纹,定位螺钉9共十六个;定位螺钉9的回转体轴线与抛撒管1的回转体轴线平行,定位螺钉9的第九外螺纹安装在壳体3的第三螺纹通孔中。关于上端盖2的第二外圆柱面的轴向长度与上端盖2的第二圆板直径之比,主要考虑以下几个因素,既不能太大,以免增加上端盖2不必要的呆重,又不能太小以免上端盖2移动时卡主。通过实验发现,上端盖2在壳体3内部反复移动过程中,当厚度比较小的时候,容易出现卡主现象,一旦卡主,再大的挤压力也无法使其继续运动,而挤压力过大会作用在壳体3上,将壳体3挤破,导致失败。而当上端盖2的第二外圆柱面的轴向长度与上端盖2的第二圆板直径之比不低于1:10时,上端盖2的厚度足够,上端盖2在壳体3内部反复移动过程中,不再出现卡主的问题。上端盖2的重量随着厚度的增加而增大,对于液体材料装填壳体,总重量为10吨级,壳体翻转过程中的难度就在于,总重量太大,翻转惯性大,从而导致壳体承受的压力太大,容易发生破坏,上端盖2的重量过大,只会产生负面效果。因此,上端盖2的厚度越低越好。通过实测实验可知,当上端盖2的第二外圆柱面的轴向长度与上端盖2的第二圆板直径之比不超过1:9时,上端盖2的重量不到总重量的4%,认为不超过4%的上端盖重量在可接受范围以内,因此,上端盖2的第二外圆柱面的轴向长度与上端盖2的第二圆板直径之比不超过1:9。因此,上端盖2的第二外圆柱面的轴向长度与上端盖2的第二圆板直径之比为1:9~10;本实施例中,上端盖2的第二外圆柱面的轴向长度与上端盖2的第二圆板直径之比为1:9。下端盖4的设计同理,下端盖4的第四外圆柱面的轴向长度与下端盖4的第四圆板直径之比为1:9~10;本实施例中,下端盖4的第四外圆柱面的轴向长度与下端盖4的第四圆板直径之比为1:9。上端盖2的第二上端圆平面与壳体3的第三上端向下同心圆环面平行,上端盖2的第二上端圆平面与壳体3的第三上端向下同心圆环面之间的距离为第一距离,壳体3的两个第三螺纹盲孔的轴线所在平面与本发明系统质心距离为第二距离,第一距离和第二距离相同,下端盖4的第四下端圆平面与壳体3的第三下端向上同心圆环面接触。关于壳体3的两个第三螺纹盲孔的轴线所在平面位于本发明系统质心下端距离,主要考虑以下两发方面,既不能太长,导致本发明系统在通过质心调节完成翻转的过程中,由于质心偏移量太大,需要调节的尺寸过多,这部分尺寸未装填液相材料,为无效长度,避免无效长度过多,也不能太短,本发明系统在通过质心调节完成翻转的过程中,由于质心偏移量太小,质心稍微的调节,导致本发明系统在空中旋转角度过大,产生了过大的角速度及角加速度,导致过大的惯性,容易发生危险。通过实验发现,当壳体3的两个第三螺纹盲孔的轴线所在平面位于本发明系统质心下端不低于120mm时,质心偏移量足够,本发明系统在通过质心调节完成翻转的过程中,质心稍微的调节,本发明系统在空中旋转角度不大,产生了的角速度及角加速度不大,在可控制范围以内,满足安全要求。当壳体3的两个第三螺纹盲孔的轴线所在平面位于本发明系统质心下端不超过140mm时,心偏移量不算过大,需要调节的尺寸不算过大,无效长度不超过总长度2%,认为在可接受范围以内。因此,壳体3的两个第三螺纹盲孔的轴线所在平面位于本发明系统质心下端120~140mm;本实施例中,壳体3的两个第三螺纹盲孔的轴线所在平面位于本发明系统质心下端120。关于壳体3的第三环形凸台的上端面距离壳体3的第三螺纹盲孔的轴线距离与壳体3的第三螺纹盲孔公称直径之比,壳体3的第三环形凸台的下端面距离壳体3的第三螺纹盲孔的轴线距离与壳体3的第三螺纹盲孔公称直径之比,主要考虑一下2个方面:既不能太小,导致强度不足,当本发明系统由吊环5吊起时,全部重量,作用在吊环5上,而吊环5将所有重量作用在壳体3的第三环形凸台上,若该尺寸太小,会从壳体3的第三环形凸台处发生断裂,导致系统失效。通过实验发现,当壳体3的第三环形凸台的上端面距离壳体3的第三螺纹盲孔的轴线距离与壳体3的第三螺纹盲孔公称直径之比不低于1.4,壳体3的第三环形凸台的下端面距离壳体3的第三螺纹盲孔的轴线距离与壳体3的第三螺纹盲孔公称直径之比不低于1.1时,壳体3的第三环形凸台强度足够。也不能太大,导致液体材料抛撒后形成的云团由于壳体3的第三环形凸台尺寸过大而发生分层,由于壳体3的第三环形凸台相当于加强筋,当壳体3的第三环形凸台比较小时,对抛撒云团影响不大,云团在后续扩散的时候可以连接到一起。当壳体3的第三环形凸台尺寸比较大时,对抛撒云团影响过大,云团在后续扩散的时候不能连接到一起,形成了断层,影响使用效果。通过实验发现,当壳体3的第三环形凸台的上端面距离壳体3的第三螺纹盲孔的轴线距离与壳体3的第三螺纹盲孔公称直径之比不超过1.6,壳体3的第三环形凸台的下端面距离壳体3的第三螺纹盲孔的轴线距离与壳体3的第三螺纹盲孔公称直径之比不超过1.3时,对抛撒云团影响不大,云团在后续扩散的时候可以连接到一起。因此,壳体3的第三环形凸台的上端面距离壳体3的第三螺纹盲孔的轴线距离为壳体3的第三螺纹盲孔公称直径的1.4~1.6倍,壳体3的第三环形凸台的下端面距离壳体3的第三螺纹盲孔的轴线距离为壳体3的第三螺纹盲孔公称直径的1.1~1.3。本实施例中,壳体3的第三环形凸台的上端面距离壳体3的第三螺纹盲孔的轴线距离为壳体3的第三螺纹盲孔公称直径的1.4倍,壳体3的第三环形凸台的下端面距离壳体3的第三螺纹盲孔的轴线距离为壳体3的第三螺纹盲孔公称直径的1.1。壳体3的两个第三螺纹盲孔的轴线位于同一水平面,关于壳体3的两个第三螺纹盲孔的轴线的夹角,主要考虑一下3个方面:旋转灵敏性,初始起吊安稳性,起吊能力。旋转灵敏性为本发明系统的质心偏移后,本发明系统进行空间旋转的灵敏程度,当旋转灵敏性不好时,本发明系统的质心偏移后,由于本发明系统的质心和两个第三螺纹盲孔连线在竖直方向比较靠近,竖直方向投影几乎重合,导致质心变化后,没有一个偏心的力使得本发明系统进行旋转,这时本发明系统为失稳状态,一旦发生旋转,将是急速大角度旋转,不符合本发明慢速的旋转原则。当旋转灵敏性较好时,本发明系统的质心和两个第三螺纹盲孔连线在竖直方向有一定距离,当本发明系统的质心偏移后,重量乘以本发明系统的质心和两个第三螺纹盲孔连线在竖直方向的距离,为使得本发明系统旋转的力矩,本发明系统随着质心的变化,随即进行空间旋转,避免了失稳的状态。通过实际试验,将旋转灵敏性分为3个标准,以及3个分值。旋转十分灵敏:10分;旋转偶尔灵敏:3分;旋转十分不灵敏:-3分。初始起吊安稳性为本发明系统在通过吊车初始起吊时,安稳程度。主要与吊车初始起吊后,本发明系统的姿态与起吊前相比,旋转的角度。由于吊车将本发明系统起吊的过程中,本发明系统的姿态受重力作用,进行相应的旋转,希望此时旋转的角度越小越好。因为起吊过程不像后续使用过程,旋转的速度可以精确控制,而起吊过程属于简单粗暴过程,希望尽可能小的减小旋转角度,使得壳体只受到向上的力,而进行向上的运动,空间姿态尽可能少的旋转,这样旋转角速度和角加速度都比较小,可以保障壳体安全性。当初始起吊安稳性比较好时,壳体的质心距离2个吊环5连线竖直距离较小,本发明稍微旋转,壳体的质心便可以和2个吊环5连线竖直方向重合,这时,本发明系统已经稳定,稍微旋转的过程中,角速度角加速度均较小,不会发生危险。当初始起吊安稳性不好时,壳体的质心距离2个吊环5连线竖直距离较大,本发明需要旋转很大角度,壳体的质心才能和2个吊环5连线竖直方向重合,这时,本发明系统才能稳定,旋转很大角度的过程中,角速度角加速度均较大,会发生危险。通过实际试验,将初始起吊安稳性分为3个标准,以及3个分值。旋转角度不超过3°:10分;旋转角度3°~10°:5分;旋转角度超过10°:0分。起吊能力为2个吊环5可以起吊的本发明系统的重量多少的能力。由于2个吊环5呈一定角度,起吊时,2个吊环5既承受剪切力,又承受弯转力矩,又承受拉力,应力状态十分复杂,多应力状态下,2个吊环5能承受的本发明系统的重力低于2个吊环实际的抗纯剪切能力。当本发明的结构使得起吊能力较好时,2个吊环5承受的力主要为剪切力,旋转弯矩和拉力均较小,这时,2个吊环5能起吊的本发明的重量接近2个吊环5实际的抗纯剪切能力。当本发明的结构使得起吊能力不好时,2个吊环5承受的力为剪切力、旋转弯矩和拉力均的混合作用,很容易达到2个吊环5母材的极限强度,这时,2个吊环5能起吊的本发明的重量很低,仅为2个吊环5实际的抗纯剪切能力的很小一部分,这时起吊时容易发生危险。通过实际试验,将起吊能力分为3个标准,以及3个分值。起吊重量为实际的抗纯剪切能力的80%以上:10分;起吊重量为实际的抗纯剪切能力的80%~60%:6分;起吊重量为实际的抗纯剪切能力的60%以下:2分。将壳体3的两个第三螺纹盲孔的轴线的夹角分为以下几个区间:179°~180°、178°~179°、177°~178°、176°~177°、175°~176°、174°~175°、173°~174°、172°~173°、171°~172°、170°~171°。分别对以上几个区间的壳体3的两个第三螺纹盲孔的轴线的夹角进行实验,并按照以上三项标准进行评价,获得分值如下:壳体3的两个第三螺纹盲孔的轴线的夹角旋转灵敏性初始起吊安稳性起吊能力总分179°~180°-3101017178°~179°3101023177°~178°10101030176°~177°10101030175°~176°1051025174°~175°105621173°~174°105621172°~173°105621171°~172°100616170°~171°100212通过实验发现,当壳体3的两个第三螺纹盲孔的轴线的夹角为176°~178°时,获得分值最高,获得30分。因此,壳体3的两个第三螺纹盲孔的轴线的夹角为176°~178°。本实施例中,壳体3的两个第三螺纹盲孔的轴线的夹角为176°。本发明的装置下边放置一个摩擦力检查装置,摩擦力检查装置可以检测吊环5的第五圆柱体和吊环5的第五圆环体转动配合的摩擦力,当第五圆柱体和吊环5的第五圆环体转动配合的摩擦力低于3000n时,检查装置显示绿色,代表安全,当第五圆柱体和吊环5的第五圆环体转动配合的摩擦力高于3000n时,检查装置显示红色,代表危险,由于本发明的装置在空中旋转过程中,吊环5的第五圆柱体和吊环5的第五圆环体也相对旋转,若吊环5的第五圆柱体和吊环5的第五圆环体相对摩擦力较低,则本发明的装置不会受到摩擦力的影响,可以安全可靠的完成翻转工作,但若吊环5的第五圆柱体和吊环5的第五圆环体相对摩擦力较大,超过3000n时,意味着壳体继续发生旋转而吊环5的第五圆柱体和吊环5的第五圆环体由于摩擦力过大而卡主,这时,随着壳体继续旋转,吊环5的第五圆柱体和吊环5的第五圆环体相对摩擦力继续增大,这便是不安全状态,当被卡主的吊环5的第五圆柱体和吊环5的第五圆环体随着旋转力的继续增大而超过卡主的力的上限时,吊环5的第五圆柱体和吊环5的第五圆环体会发生较大的旋转冲击力,造成危险,因此,当第五圆柱体和吊环5的第五圆环体转动配合的摩擦力高于3000n时,检查装置显示红色,代表危险,这时认为停止旋转,可以避免危险发生;所述一种通过质心位置调节进行自动翻转的十吨级液相材料装填壳体,包括以下步骤:步骤1:壳体3的母材为45钢,粗加工后,进行淬火处理,淬火温度为880~890℃,待热透后,用水进行冷却,获得马氏体组织,再进行回火,加热至600~620℃,保温2小时,在空气中冷却,获得回火马氏体组织;通过对热处理工艺的控制,获得好的微观组织,获得的回火马氏体具有好的力学性能和塑性,适合本发明的装置的壳体使用。组织将壳体3放在水平台上,使得壳体3的回转体轴线垂直于水平面;步骤2:将下端盖4与壳体3装配;步骤3:将抛撒管1与壳体3装配;步骤4:将上端盖2与壳体3装配;步骤5:将吊环5与壳体3装配;步骤6:将充气管7与壳体3装配;步骤7:将临时挡板8与壳体3装配;步骤8:将定位螺钉9与壳体3装配,定位螺钉9的下端与壳体3的第三上端向下同心圆环面平齐;步骤9:将液体6灌入抛撒管1的第一外圆柱面、上端盖2的第二下端同心圆平面、壳体3的第三内圆柱面和下端盖4的第四上端圆平面组成的封闭空间中;步骤10:将吊绳穿过吊环5的第五圆环体,再将吊绳挂在吊车上,通过吊车将壳体3吊起,使得临时挡板8与地面脱离;步骤11:将本发明的系统由起立姿态转变为躺下姿态:将充气管7的第七圆管的左端与高压空气泵连接,打开充气管7的第七开关,使高压空气进入下端盖4的第四下端圆平面、壳体3的第三下端内圆柱面和临时挡板8的第八上端圆平面组成的封闭空间中,通过高压气体挤压下端盖4,下端盖4再将压力传递给抛撒管1和液体6,液体6再将压力传递给上端盖2,使得抛撒管1、上端盖2、下端盖4和液体6同时向上移动,本发明的系统质心逐渐上移,本发明系统的姿态随着质心的上移逐渐由起立姿态转变为躺下姿态,待抛撒管1的回转体轴线与水平面平行,关闭充气管7的第七开关,断开充气管7的第七圆管的左端与高压空气泵的连接;步骤12:将本发明的系统由躺下姿态转变为起立姿态:打开充气管7的第七开关,放出下端盖4的第四下端圆平面、壳体3的第三下端内圆柱面和临时挡板8的第八上端圆平面组成的封闭空间中的高压气体,将充气管7的第七圆管的左端与真空泵连接,对下端盖4的第四下端圆平面、壳体3的第三下端内圆柱面和临时挡板8的第八上端圆平面组成的封闭空间进行抽真空,使得下端盖4的第四下端圆平面受到负压,下端盖4再将负压传递给抛撒管1和液体6,液体6再将负压传递给上端盖2,使得抛撒管1、上端盖2、下端盖4和液体6同时向靠近临时挡板8的方向移动,本发明的系统质心逐渐靠近临时挡板8,本发明系统的姿态随着质心的靠近临时挡板8逐渐由躺下姿态转变为起立姿态,待抛撒管1的回转体轴线与水平面垂直,关闭充气管7的第七开关,断开充气管7的第七圆管的左端与真空泵的连接;步骤13:将定位螺钉9拧紧,通过定位螺钉9挤压上端盖2的第二上端同心圆平面,固定上端盖2的位置,使得上端盖2与壳体3不能再发生相对运动,卸下临时挡板8,此时,本发明的系统完成实验前准备。使用原方案的翻转车进行壳体的从躺下姿态到起立姿态,及从起立姿态到躺下姿态的翻转实验,实验壳体重量为十吨,实验壳体内部状体液相材料,壳体厚度不超过10mm,为薄壁壳体,反复翻转实验结果如下:实验状态实验结果10mm壳体从起立姿态到躺下姿态壳体完好10mm壳体从躺下姿态到起立姿态壳体完好9mm壳体从起立姿态到躺下姿态壳体完好9mm壳体从躺下姿态到起立姿态壳体完好8mm壳体从起立姿态到躺下姿态壳体完好8mm壳体从躺下姿态到起立姿态壳体发生破坏7.5mm壳体从躺下姿态到起立姿态壳体发生破坏7.5mm壳体从躺下姿态到起立姿态无法进行7mm壳体从躺下姿态到起立姿态壳体发生破坏7mm壳体从躺下姿态到起立姿态无法进行6mm壳体从躺下姿态到起立姿态壳体发生破坏6mm壳体从躺下姿态到起立姿态无法进行5mm壳体从躺下姿态到起立姿态壳体发生破坏5mm壳体从躺下姿态到起立姿态无法进行分析可知,当壳体壁厚为8mm时,壳体从起立姿态到躺下姿态,壳体完好,但是壳体从躺下姿态到起立姿态便发生破坏,而壳体壁厚不超过7.5mm时,壳体从起立姿态到躺下姿态,便发生破坏。壳体壁厚至少为9mm时,才能确保从起立姿态到躺下姿态以及从躺下姿态到起立姿态均壳体完好。使用本发明的装置及方法,按照步骤1到步骤13,反复进行从躺下姿态到起立姿态,及从起立姿态到躺下姿态的翻转实验,实验壳体重量为十吨,实验壳体内部状体液相材料,壳体厚度为5mm,为薄壁壳体,反复翻转实验结果如下:实验状态实验结果第1次从起立姿态到躺下姿态壳体完好第1次从躺下姿态到起立姿态壳体完好第2次从起立姿态到躺下姿态壳体完好第2次从躺下姿态到起立姿态壳体完好第3次从起立姿态到躺下姿态壳体完好第3次从躺下姿态到起立姿态壳体完好第4次从起立姿态到躺下姿态壳体完好第4次从躺下姿态到起立姿态壳体完好第5次从起立姿态到躺下姿态壳体完好第5次从躺下姿态到起立姿态壳体完好第6次从起立姿态到躺下姿态壳体完好第6次从躺下姿态到起立姿态壳体完好第7次从起立姿态到躺下姿态壳体完好第7次从躺下姿态到起立姿态壳体完好第8次从起立姿态到躺下姿态壳体完好第8次从躺下姿态到起立姿态壳体完好第9次从起立姿态到躺下姿态壳体完好第9次从躺下姿态到起立姿态壳体完好第10次从起立姿态到躺下姿态壳体完好第10次从躺下姿态到起立姿态壳体完好分析可知,总重量为10吨的液相材料装填薄壁壳体,壳体壁厚5mm,连续进行十次由起立姿态到躺下姿态,再由躺下姿态到起立姿态的翻转实验,壳体完好。对于十吨级装填液相材料的薄壁壳体,使用本发明进行翻转,壳体壁厚可以减少至原翻转方案的55%,大幅度降低了壳体壁厚,减少了壳体壁厚对抛撒范围的影响,增加了产品的使用效果。本发明的一种通过质心位置调节进行自动翻转的十吨级液相材料装填壳体,首先将装填液相材料的薄壁壳体在中部加强筋位置吊起来,通过调节壳体质心位置,使得壳体的空间姿态随着质心的变化进行自适应调整,逐渐完成从躺下姿态到起立姿态,或从起立姿态到躺下姿态的翻转工作。整个翻转过程为壳体在重力作用下自动完成,无需外力作用在壳体外壁上。壳体质心的调节可以精确控制,因此,壳体翻转过程中的速度可以精确控制,壳体翻转过程速度均匀且缓慢,避免了速度突变,避免了过大动载荷,保证了壳体强度不受破坏,进而保证了产品的安全性和可靠性。实施例6:如图1所示,本实施例给出一种通过质心位置调节进行自动翻转的十吨级液相材料装填壳体,包括抛撒管1,上端盖2,下端盖4,液体6,其特征在于还包括壳体3,吊环5,充气管7,临时挡板8,定位螺钉9;抛撒管1为第一圆柱体,抛撒管1的第一圆柱体为回转体,抛撒管1的第一圆柱体的上端面为第一上端圆平面,抛撒管1的第一圆柱体的侧面为第一外圆柱面,抛撒管1的第一圆柱体的下端面为第一下端圆平面;抛撒管1的回转体轴线与水平面垂直,抛撒管1的内部装有炸药,抛撒管1内部的炸药为抛撒液相材料形成云团的能量源;上端盖2为第二圆板,上端盖2的第二圆板为回转体,上端盖2的第二圆板中心带有第二圆孔,上端盖2的第二圆板的上端面为第二上端同心圆平面,上端盖2的第二圆板的外侧面为第二外圆柱面,上端盖2的第二圆板的下端面为第二下端同心圆平面,上端盖2的第二圆孔的内侧面为第二内圆柱面;上端盖2的回转体轴线与抛撒管1的回转体轴线重合,上端盖2位于抛撒管1上端外部,上端盖2的第二内圆柱面与抛撒管1的第一外圆柱面上端接触,上端盖2的第二上端同心圆平面与抛撒管1的第一上端圆平面共面;壳体3为第三圆筒体,壳体3的第三圆筒体为回转体,壳体3的第三圆筒体的外侧面为第三外圆柱面,壳体3的第三圆筒体的内侧面为第三内圆柱面,壳体3的第三圆筒体上端内侧带有第三上端内法兰,壳体3的第三上端内法兰下端面为第三上端向下同心圆环面,壳体3的第三上端内法兰上带有十六个第三螺纹通孔,壳体3的十六个第三螺纹通孔轴线与壳体3的回转体轴线平行,壳体3的十六个第三螺纹通孔绕壳体3的回转体轴线均匀分布,壳体3的第三圆筒体下端内侧带有第三下端内法兰,壳体3的第三下端内法兰上端面为第三下端向上同心圆环面,壳体3的第三下端内法兰下端面为第三下端向下同心圆环面,壳体3的第三下端内法兰的内侧面为第三下端内圆柱面,壳体3的第三下端内法兰上带有一个第三圆形通孔,壳体3的第三圆形通孔轴线与壳体3的回转体轴线垂直,壳体3的第三内圆柱面中部带有第三环形凸台,壳体3的第三外圆柱面中部带有两个第三螺纹盲孔,壳体3的两个第三螺纹盲孔的轴线均垂直于壳体3的回转体轴线;壳体3的回转体轴线与抛撒管1的回转体轴线重合,上端盖2的第二圆板位于壳体3的第三圆筒体内部,上端盖2的第二上端圆平面位于壳体3的第三上端向下同心圆环面下端,壳体3的第三内圆柱面与上端盖2的第二外圆柱面滑动配合接触;下端盖4为第四圆板,下端盖4的第四圆板为回转体,下端盖4的第四圆板的上端面为第四上端圆平面,下端盖4的第四圆板的外侧面为第四外圆柱面,下端盖4的第四圆板的下端面为第四下端圆平面;下端盖4的回转体轴线与抛撒管1的回转体轴线重合,下端盖4的第四上端圆平面与抛撒管1的第一下端圆平面连接,下端盖4的第四圆板位于壳体3的第三圆筒体内部,下端盖4的第四下端圆平面位于壳体3的第三下端向上同心圆环面上端,壳体3的第三内圆柱面与下端盖4的第四外圆柱面滑动配合接触;吊环5由左右两部分组成,吊环5的右部分为第五圆柱体,吊环5的第五圆柱体为回转体,吊环5的第五圆柱体的侧面带有第五外螺纹,吊环5的左部分为第五圆环体,吊环5的第五圆柱体和吊环5的第五圆环体转动配合连接,吊环5共两个;吊环5的第五圆柱体的回转体轴线与抛撒管1的回转体轴线垂直,吊环5的第五外螺纹安装在壳体3的第三螺纹盲孔中;液体6为被炸药抛撒后形成云团的液相材料;液体6位于抛撒管1的第一外圆柱面、上端盖2的第二下端同心圆平面、壳体3的第三内圆柱面和下端盖4的第四上端圆平面组成的封闭空间中;充气管7为第七圆管,充气管7的第七圆管为回转体,充气管7的第七圆管左端带有第七开关;充气管7的回转体轴线与抛撒管1的回转体轴线垂直,充气管7的第七圆管右端与壳体3的第三圆形通孔连接;临时挡板8为第八圆板,临时挡板8的第八圆板为回转体,临时挡板8的第八圆板的上端面为第八上端圆平面;临时挡板8的回转体轴线与抛撒管1的回转体轴线重合,临时挡板8位于壳体3下端,临时挡板8的第八上端圆平面与壳体3的第三下端向下同心圆环面连接;定位螺钉9为第九圆柱体,定位螺钉9的第九圆柱体为回转体,定位螺钉9的第九圆柱体的侧面为第九外圆柱面,定位螺钉9的第九外圆柱面下端带有第九外螺纹,定位螺钉9共十六个;定位螺钉9的回转体轴线与抛撒管1的回转体轴线平行,定位螺钉9的第九外螺纹安装在壳体3的第三螺纹通孔中。关于上端盖2的第二外圆柱面的轴向长度与上端盖2的第二圆板直径之比,主要考虑以下几个因素,既不能太大,以免增加上端盖2不必要的呆重,又不能太小以免上端盖2移动时卡主。通过实验发现,上端盖2在壳体3内部反复移动过程中,当厚度比较小的时候,容易出现卡主现象,一旦卡主,再大的挤压力也无法使其继续运动,而挤压力过大会作用在壳体3上,将壳体3挤破,导致失败。而当上端盖2的第二外圆柱面的轴向长度与上端盖2的第二圆板直径之比不低于1:10时,上端盖2的厚度足够,上端盖2在壳体3内部反复移动过程中,不再出现卡主的问题。上端盖2的重量随着厚度的增加而增大,对于液体材料装填壳体,总重量为10吨级,壳体翻转过程中的难度就在于,总重量太大,翻转惯性大,从而导致壳体承受的压力太大,容易发生破坏,上端盖2的重量过大,只会产生负面效果。因此,上端盖2的厚度越低越好。通过实测实验可知,当上端盖2的第二外圆柱面的轴向长度与上端盖2的第二圆板直径之比不超过1:9时,上端盖2的重量不到总重量的4%,认为不超过4%的上端盖重量在可接受范围以内,因此,上端盖2的第二外圆柱面的轴向长度与上端盖2的第二圆板直径之比不超过1:9。因此,上端盖2的第二外圆柱面的轴向长度与上端盖2的第二圆板直径之比为1:9~10;本实施例中,上端盖2的第二外圆柱面的轴向长度与上端盖2的第二圆板直径之比为1:9。下端盖4的设计同理,下端盖4的第四外圆柱面的轴向长度与下端盖4的第四圆板直径之比为1:9~10;本实施例中,下端盖4的第四外圆柱面的轴向长度与下端盖4的第四圆板直径之比为1:9。上端盖2的第二上端圆平面与壳体3的第三上端向下同心圆环面平行,上端盖2的第二上端圆平面与壳体3的第三上端向下同心圆环面之间的距离为第一距离,壳体3的两个第三螺纹盲孔的轴线所在平面与本发明系统质心距离为第二距离,第一距离和第二距离相同,下端盖4的第四下端圆平面与壳体3的第三下端向上同心圆环面接触。关于壳体3的两个第三螺纹盲孔的轴线所在平面位于本发明系统质心下端距离,主要考虑以下两发方面,既不能太长,导致本发明系统在通过质心调节完成翻转的过程中,由于质心偏移量太大,需要调节的尺寸过多,这部分尺寸未装填液相材料,为无效长度,避免无效长度过多,也不能太短,本发明系统在通过质心调节完成翻转的过程中,由于质心偏移量太小,质心稍微的调节,导致本发明系统在空中旋转角度过大,产生了过大的角速度及角加速度,导致过大的惯性,容易发生危险。通过实验发现,当壳体3的两个第三螺纹盲孔的轴线所在平面位于本发明系统质心下端不低于120mm时,质心偏移量足够,本发明系统在通过质心调节完成翻转的过程中,质心稍微的调节,本发明系统在空中旋转角度不大,产生了的角速度及角加速度不大,在可控制范围以内,满足安全要求。当壳体3的两个第三螺纹盲孔的轴线所在平面位于本发明系统质心下端不超过140mm时,心偏移量不算过大,需要调节的尺寸不算过大,无效长度不超过总长度2%,认为在可接受范围以内。因此,壳体3的两个第三螺纹盲孔的轴线所在平面位于本发明系统质心下端120~140mm;本实施例中,壳体3的两个第三螺纹盲孔的轴线所在平面位于本发明系统质心下端120。关于壳体3的第三环形凸台的上端面距离壳体3的第三螺纹盲孔的轴线距离与壳体3的第三螺纹盲孔公称直径之比,壳体3的第三环形凸台的下端面距离壳体3的第三螺纹盲孔的轴线距离与壳体3的第三螺纹盲孔公称直径之比,主要考虑一下2个方面:既不能太小,导致强度不足,当本发明系统由吊环5吊起时,全部重量,作用在吊环5上,而吊环5将所有重量作用在壳体3的第三环形凸台上,若该尺寸太小,会从壳体3的第三环形凸台处发生断裂,导致系统失效。通过实验发现,当壳体3的第三环形凸台的上端面距离壳体3的第三螺纹盲孔的轴线距离与壳体3的第三螺纹盲孔公称直径之比不低于1.4,壳体3的第三环形凸台的下端面距离壳体3的第三螺纹盲孔的轴线距离与壳体3的第三螺纹盲孔公称直径之比不低于1.1时,壳体3的第三环形凸台强度足够。也不能太大,导致液体材料抛撒后形成的云团由于壳体3的第三环形凸台尺寸过大而发生分层,由于壳体3的第三环形凸台相当于加强筋,当壳体3的第三环形凸台比较小时,对抛撒云团影响不大,云团在后续扩散的时候可以连接到一起。当壳体3的第三环形凸台尺寸比较大时,对抛撒云团影响过大,云团在后续扩散的时候不能连接到一起,形成了断层,影响使用效果。通过实验发现,当壳体3的第三环形凸台的上端面距离壳体3的第三螺纹盲孔的轴线距离与壳体3的第三螺纹盲孔公称直径之比不超过1.6,壳体3的第三环形凸台的下端面距离壳体3的第三螺纹盲孔的轴线距离与壳体3的第三螺纹盲孔公称直径之比不超过1.3时,对抛撒云团影响不大,云团在后续扩散的时候可以连接到一起。因此,壳体3的第三环形凸台的上端面距离壳体3的第三螺纹盲孔的轴线距离为壳体3的第三螺纹盲孔公称直径的1.4~1.6倍,壳体3的第三环形凸台的下端面距离壳体3的第三螺纹盲孔的轴线距离为壳体3的第三螺纹盲孔公称直径的1.1~1.3。本实施例中,壳体3的第三环形凸台的上端面距离壳体3的第三螺纹盲孔的轴线距离为壳体3的第三螺纹盲孔公称直径的1.4倍,壳体3的第三环形凸台的下端面距离壳体3的第三螺纹盲孔的轴线距离为壳体3的第三螺纹盲孔公称直径的1.1。壳体3的两个第三螺纹盲孔的轴线位于同一水平面,关于壳体3的两个第三螺纹盲孔的轴线的夹角,主要考虑一下3个方面:旋转灵敏性,初始起吊安稳性,起吊能力。旋转灵敏性为本发明系统的质心偏移后,本发明系统进行空间旋转的灵敏程度,当旋转灵敏性不好时,本发明系统的质心偏移后,由于本发明系统的质心和两个第三螺纹盲孔连线在竖直方向比较靠近,竖直方向投影几乎重合,导致质心变化后,没有一个偏心的力使得本发明系统进行旋转,这时本发明系统为失稳状态,一旦发生旋转,将是急速大角度旋转,不符合本发明慢速的旋转原则。当旋转灵敏性较好时,本发明系统的质心和两个第三螺纹盲孔连线在竖直方向有一定距离,当本发明系统的质心偏移后,重量乘以本发明系统的质心和两个第三螺纹盲孔连线在竖直方向的距离,为使得本发明系统旋转的力矩,本发明系统随着质心的变化,随即进行空间旋转,避免了失稳的状态。通过实际试验,将旋转灵敏性分为3个标准,以及3个分值。旋转十分灵敏:10分;旋转偶尔灵敏:3分;旋转十分不灵敏:-3分。初始起吊安稳性为本发明系统在通过吊车初始起吊时,安稳程度。主要与吊车初始起吊后,本发明系统的姿态与起吊前相比,旋转的角度。由于吊车将本发明系统起吊的过程中,本发明系统的姿态受重力作用,进行相应的旋转,希望此时旋转的角度越小越好。因为起吊过程不像后续使用过程,旋转的速度可以精确控制,而起吊过程属于简单粗暴过程,希望尽可能小的减小旋转角度,使得壳体只受到向上的力,而进行向上的运动,空间姿态尽可能少的旋转,这样旋转角速度和角加速度都比较小,可以保障壳体安全性。当初始起吊安稳性比较好时,壳体的质心距离2个吊环5连线竖直距离较小,本发明稍微旋转,壳体的质心便可以和2个吊环5连线竖直方向重合,这时,本发明系统已经稳定,稍微旋转的过程中,角速度角加速度均较小,不会发生危险。当初始起吊安稳性不好时,壳体的质心距离2个吊环5连线竖直距离较大,本发明需要旋转很大角度,壳体的质心才能和2个吊环5连线竖直方向重合,这时,本发明系统才能稳定,旋转很大角度的过程中,角速度角加速度均较大,会发生危险。通过实际试验,将初始起吊安稳性分为3个标准,以及3个分值。旋转角度不超过3°:10分;旋转角度3°~10°:5分;旋转角度超过10°:0分。起吊能力为2个吊环5可以起吊的本发明系统的重量多少的能力。由于2个吊环5呈一定角度,起吊时,2个吊环5既承受剪切力,又承受弯转力矩,又承受拉力,应力状态十分复杂,多应力状态下,2个吊环5能承受的本发明系统的重力低于2个吊环实际的抗纯剪切能力。当本发明的结构使得起吊能力较好时,2个吊环5承受的力主要为剪切力,旋转弯矩和拉力均较小,这时,2个吊环5能起吊的本发明的重量接近2个吊环5实际的抗纯剪切能力。当本发明的结构使得起吊能力不好时,2个吊环5承受的力为剪切力、旋转弯矩和拉力均的混合作用,很容易达到2个吊环5母材的极限强度,这时,2个吊环5能起吊的本发明的重量很低,仅为2个吊环5实际的抗纯剪切能力的很小一部分,这时起吊时容易发生危险。通过实际试验,将起吊能力分为3个标准,以及3个分值。起吊重量为实际的抗纯剪切能力的80%以上:10分;起吊重量为实际的抗纯剪切能力的80%~60%:6分;起吊重量为实际的抗纯剪切能力的60%以下:2分。将壳体3的两个第三螺纹盲孔的轴线的夹角分为以下几个区间:179°~180°、178°~179°、177°~178°、176°~177°、175°~176°、174°~175°、173°~174°、172°~173°、171°~172°、170°~171°。分别对以上几个区间的壳体3的两个第三螺纹盲孔的轴线的夹角进行实验,并按照以上三项标准进行评价,获得分值如下:壳体3的两个第三螺纹盲孔的轴线的夹角旋转灵敏性初始起吊安稳性起吊能力总分179°~180°-3101017178°~179°3101023177°~178°10101030176°~177°10101030175°~176°1051025174°~175°105621173°~174°105621172°~173°105621171°~172°100616170°~171°100212通过实验发现,当壳体3的两个第三螺纹盲孔的轴线的夹角为176°~178°时,获得分值最高,获得30分。因此,壳体3的两个第三螺纹盲孔的轴线的夹角为176°~178°。本实施例中,壳体3的两个第三螺纹盲孔的轴线的夹角为176°。所述一种通过质心位置调节进行自动翻转的十吨级液相材料装填壳体,包括以下步骤:步骤1:壳体3的毛坯为铸铝,由整体铸造方法铸造成型,放底板,放下箱,将壳体3外表形状相同的模型放在底板上,加沙,压实,翻转,放上箱,加沙,压实,扎通气孔,开上箱,取模型,再放入型芯,型芯外表面尺寸形状与壳体3内表面尺寸形状相同,再放上箱,进行铸造成毛坯,再精加工成型,通过对壳体3的毛坯铸造方法的控制,提高毛坯铸造性能,保障本发明的功能。将壳体3放在水平台上,使得壳体3的回转体轴线垂直于水平面;步骤2:将下端盖4与壳体3装配;步骤3:将抛撒管1与壳体3装配;步骤4:将上端盖2与壳体3装配;步骤5:将吊环5与壳体3装配;步骤6:将充气管7与壳体3装配;步骤7:将临时挡板8与壳体3装配;步骤8:将定位螺钉9与壳体3装配,定位螺钉9的下端与壳体3的第三上端向下同心圆环面平齐;步骤9:将液体6灌入抛撒管1的第一外圆柱面、上端盖2的第二下端同心圆平面、壳体3的第三内圆柱面和下端盖4的第四上端圆平面组成的封闭空间中;步骤10:将吊绳穿过吊环5的第五圆环体,再将吊绳挂在吊车上,通过吊车将壳体3吊起,使得临时挡板8与地面脱离,同时通过安全吊绳将壳体3的上端左右两点与吊车连接,再通过安全吊绳将壳体3的下端左右两点与吊车连接,安全吊绳与监控器连接,监控器检测本发明装置旋转的角度,将信号传输给阿安全吊绳,安全吊绳根据本发明装置旋转的角度自动进行伸缩,始终保持绷紧又不影响壳体旋转的长度,这样,由于有了安全吊绳,使得本发明的装置吊在空中后多了一道保障,在本发明使用过程中,若吊绳或吊环5或壳体3发生折断,由于有安全吊绳的存在,本发明不至于吊在地上摔坏,提高了安全性;步骤11:将本发明的系统由起立姿态转变为躺下姿态:将充气管7的第七圆管的左端与高压空气泵连接,打开充气管7的第七开关,使高压空气进入下端盖4的第四下端圆平面、壳体3的第三下端内圆柱面和临时挡板8的第八上端圆平面组成的封闭空间中,通过高压气体挤压下端盖4,下端盖4再将压力传递给抛撒管1和液体6,液体6再将压力传递给上端盖2,使得抛撒管1、上端盖2、下端盖4和液体6同时向上移动,本发明的系统质心逐渐上移,本发明系统的姿态随着质心的上移逐渐由起立姿态转变为躺下姿态,待抛撒管1的回转体轴线与水平面平行,关闭充气管7的第七开关,断开充气管7的第七圆管的左端与高压空气泵的连接;步骤12:将本发明的系统由躺下姿态转变为起立姿态:打开充气管7的第七开关,放出下端盖4的第四下端圆平面、壳体3的第三下端内圆柱面和临时挡板8的第八上端圆平面组成的封闭空间中的高压气体,将充气管7的第七圆管的左端与真空泵连接,对下端盖4的第四下端圆平面、壳体3的第三下端内圆柱面和临时挡板8的第八上端圆平面组成的封闭空间进行抽真空,使得下端盖4的第四下端圆平面受到负压,下端盖4再将负压传递给抛撒管1和液体6,液体6再将负压传递给上端盖2,使得抛撒管1、上端盖2、下端盖4和液体6同时向靠近临时挡板8的方向移动,本发明的系统质心逐渐靠近临时挡板8,本发明系统的姿态随着质心的靠近临时挡板8逐渐由躺下姿态转变为起立姿态,待抛撒管1的回转体轴线与水平面垂直,关闭充气管7的第七开关,断开充气管7的第七圆管的左端与真空泵的连接;步骤13:将定位螺钉9拧紧,通过定位螺钉9挤压上端盖2的第二上端同心圆平面,固定上端盖2的位置,使得上端盖2与壳体3不能再发生相对运动,卸下临时挡板8,此时,本发明的系统完成实验前准备。使用原方案的翻转车进行壳体的从躺下姿态到起立姿态,及从起立姿态到躺下姿态的翻转实验,实验壳体重量为十吨,实验壳体内部状体液相材料,壳体厚度不超过10mm,为薄壁壳体,反复翻转实验结果如下:实验状态实验结果10mm壳体从起立姿态到躺下姿态壳体完好10mm壳体从躺下姿态到起立姿态壳体完好9mm壳体从起立姿态到躺下姿态壳体完好9mm壳体从躺下姿态到起立姿态壳体完好8mm壳体从起立姿态到躺下姿态壳体完好8mm壳体从躺下姿态到起立姿态壳体发生破坏7.5mm壳体从躺下姿态到起立姿态壳体发生破坏7.5mm壳体从躺下姿态到起立姿态无法进行7mm壳体从躺下姿态到起立姿态壳体发生破坏7mm壳体从躺下姿态到起立姿态无法进行6mm壳体从躺下姿态到起立姿态壳体发生破坏6mm壳体从躺下姿态到起立姿态无法进行5mm壳体从躺下姿态到起立姿态壳体发生破坏5mm壳体从躺下姿态到起立姿态无法进行分析可知,当壳体壁厚为8mm时,壳体从起立姿态到躺下姿态,壳体完好,但是壳体从躺下姿态到起立姿态便发生破坏,而壳体壁厚不超过7.5mm时,壳体从起立姿态到躺下姿态,便发生破坏。壳体壁厚至少为9mm时,才能确保从起立姿态到躺下姿态以及从躺下姿态到起立姿态均壳体完好。使用本发明的装置及方法,按照步骤1到步骤13,反复进行从躺下姿态到起立姿态,及从起立姿态到躺下姿态的翻转实验,实验壳体重量为十吨,实验壳体内部状体液相材料,壳体厚度为5mm,为薄壁壳体,反复翻转实验结果如下:分析可知,总重量为10吨的液相材料装填薄壁壳体,壳体壁厚5mm,连续进行十次由起立姿态到躺下姿态,再由躺下姿态到起立姿态的翻转实验,壳体完好。对于十吨级装填液相材料的薄壁壳体,使用本发明进行翻转,壳体壁厚可以减少至原翻转方案的55%,大幅度降低了壳体壁厚,减少了壳体壁厚对抛撒范围的影响,增加了产品的使用效果。本发明的一种通过质心位置调节进行自动翻转的十吨级液相材料装填壳体,首先将装填液相材料的薄壁壳体在中部加强筋位置吊起来,通过调节壳体质心位置,使得壳体的空间姿态随着质心的变化进行自适应调整,逐渐完成从躺下姿态到起立姿态,或从起立姿态到躺下姿态的翻转工作。整个翻转过程为壳体在重力作用下自动完成,无需外力作用在壳体外壁上。壳体质心的调节可以精确控制,因此,壳体翻转过程中的速度可以精确控制,壳体翻转过程速度均匀且缓慢,避免了速度突变,避免了过大动载荷,保证了壳体强度不受破坏,进而保证了产品的安全性和可靠性。实施例7:如图1所示,本实施例给出一种通过质心位置调节进行自动翻转的十吨级液相材料装填壳体,包括抛撒管1,上端盖2,下端盖4,液体6,其特征在于还包括壳体3,吊环5,充气管7,临时挡板8,定位螺钉9;抛撒管1为第一圆柱体,抛撒管1的第一圆柱体为回转体,抛撒管1的第一圆柱体的上端面为第一上端圆平面,抛撒管1的第一圆柱体的侧面为第一外圆柱面,抛撒管1的第一圆柱体的下端面为第一下端圆平面;抛撒管1的回转体轴线与水平面垂直,抛撒管1的内部装有炸药,抛撒管1内部的炸药为抛撒液相材料形成云团的能量源;上端盖2为第二圆板,上端盖2的第二圆板为回转体,上端盖2的第二圆板中心带有第二圆孔,上端盖2的第二圆板的上端面为第二上端同心圆平面,上端盖2的第二圆板的外侧面为第二外圆柱面,上端盖2的第二圆板的下端面为第二下端同心圆平面,上端盖2的第二圆孔的内侧面为第二内圆柱面;上端盖2的回转体轴线与抛撒管1的回转体轴线重合,上端盖2位于抛撒管1上端外部,上端盖2的第二内圆柱面与抛撒管1的第一外圆柱面上端接触,上端盖2的第二上端同心圆平面与抛撒管1的第一上端圆平面共面;壳体3为第三圆筒体,壳体3的第三圆筒体为回转体,壳体3的第三圆筒体的外侧面为第三外圆柱面,壳体3的第三圆筒体的内侧面为第三内圆柱面,壳体3的第三圆筒体上端内侧带有第三上端内法兰,壳体3的第三上端内法兰下端面为第三上端向下同心圆环面,壳体3的第三上端内法兰上带有十六个第三螺纹通孔,壳体3的十六个第三螺纹通孔轴线与壳体3的回转体轴线平行,壳体3的十六个第三螺纹通孔绕壳体3的回转体轴线均匀分布,壳体3的第三圆筒体下端内侧带有第三下端内法兰,壳体3的第三下端内法兰上端面为第三下端向上同心圆环面,壳体3的第三下端内法兰下端面为第三下端向下同心圆环面,壳体3的第三下端内法兰的内侧面为第三下端内圆柱面,壳体3的第三下端内法兰上带有一个第三圆形通孔,壳体3的第三圆形通孔轴线与壳体3的回转体轴线垂直,壳体3的第三内圆柱面中部带有第三环形凸台,壳体3的第三外圆柱面中部带有两个第三螺纹盲孔,壳体3的两个第三螺纹盲孔的轴线均垂直于壳体3的回转体轴线;壳体3的回转体轴线与抛撒管1的回转体轴线重合,上端盖2的第二圆板位于壳体3的第三圆筒体内部,上端盖2的第二上端圆平面位于壳体3的第三上端向下同心圆环面下端,壳体3的第三内圆柱面与上端盖2的第二外圆柱面滑动配合接触;下端盖4为第四圆板,下端盖4的第四圆板为回转体,下端盖4的第四圆板的上端面为第四上端圆平面,下端盖4的第四圆板的外侧面为第四外圆柱面,下端盖4的第四圆板的下端面为第四下端圆平面;下端盖4的回转体轴线与抛撒管1的回转体轴线重合,下端盖4的第四上端圆平面与抛撒管1的第一下端圆平面连接,下端盖4的第四圆板位于壳体3的第三圆筒体内部,下端盖4的第四下端圆平面位于壳体3的第三下端向上同心圆环面上端,壳体3的第三内圆柱面与下端盖4的第四外圆柱面滑动配合接触;吊环5由左右两部分组成,吊环5的右部分为第五圆柱体,吊环5的第五圆柱体为回转体,吊环5的第五圆柱体的侧面带有第五外螺纹,吊环5的左部分为第五圆环体,吊环5的第五圆柱体和吊环5的第五圆环体转动配合连接,吊环5共两个;吊环5的第五圆柱体的回转体轴线与抛撒管1的回转体轴线垂直,吊环5的第五外螺纹安装在壳体3的第三螺纹盲孔中;液体6为被炸药抛撒后形成云团的液相材料;液体6位于抛撒管1的第一外圆柱面、上端盖2的第二下端同心圆平面、壳体3的第三内圆柱面和下端盖4的第四上端圆平面组成的封闭空间中;充气管7为第七圆管,充气管7的第七圆管为回转体,充气管7的第七圆管左端带有第七开关;充气管7的回转体轴线与抛撒管1的回转体轴线垂直,充气管7的第七圆管右端与壳体3的第三圆形通孔连接;临时挡板8为第八圆板,临时挡板8的第八圆板为回转体,临时挡板8的第八圆板的上端面为第八上端圆平面;临时挡板8的回转体轴线与抛撒管1的回转体轴线重合,临时挡板8位于壳体3下端,临时挡板8的第八上端圆平面与壳体3的第三下端向下同心圆环面连接;定位螺钉9为第九圆柱体,定位螺钉9的第九圆柱体为回转体,定位螺钉9的第九圆柱体的侧面为第九外圆柱面,定位螺钉9的第九外圆柱面下端带有第九外螺纹,定位螺钉9共十六个;定位螺钉9的回转体轴线与抛撒管1的回转体轴线平行,定位螺钉9的第九外螺纹安装在壳体3的第三螺纹通孔中。关于上端盖2的第二外圆柱面的轴向长度与上端盖2的第二圆板直径之比,主要考虑以下几个因素,既不能太大,以免增加上端盖2不必要的呆重,又不能太小以免上端盖2移动时卡主。通过实验发现,上端盖2在壳体3内部反复移动过程中,当厚度比较小的时候,容易出现卡主现象,一旦卡主,再大的挤压力也无法使其继续运动,而挤压力过大会作用在壳体3上,将壳体3挤破,导致失败。而当上端盖2的第二外圆柱面的轴向长度与上端盖2的第二圆板直径之比不低于1:10时,上端盖2的厚度足够,上端盖2在壳体3内部反复移动过程中,不再出现卡主的问题。上端盖2的重量随着厚度的增加而增大,对于液体材料装填壳体,总重量为10吨级,壳体翻转过程中的难度就在于,总重量太大,翻转惯性大,从而导致壳体承受的压力太大,容易发生破坏,上端盖2的重量过大,只会产生负面效果。因此,上端盖2的厚度越低越好。通过实测实验可知,当上端盖2的第二外圆柱面的轴向长度与上端盖2的第二圆板直径之比不超过1:9时,上端盖2的重量不到总重量的4%,认为不超过4%的上端盖重量在可接受范围以内,因此,上端盖2的第二外圆柱面的轴向长度与上端盖2的第二圆板直径之比不超过1:9。因此,上端盖2的第二外圆柱面的轴向长度与上端盖2的第二圆板直径之比为1:9~10;本实施例中,上端盖2的第二外圆柱面的轴向长度与上端盖2的第二圆板直径之比为1:9。下端盖4的设计同理,下端盖4的第四外圆柱面的轴向长度与下端盖4的第四圆板直径之比为1:9~10;本实施例中,下端盖4的第四外圆柱面的轴向长度与下端盖4的第四圆板直径之比为1:9。上端盖2的第二上端圆平面与壳体3的第三上端向下同心圆环面平行,上端盖2的第二上端圆平面与壳体3的第三上端向下同心圆环面之间的距离为第一距离,壳体3的两个第三螺纹盲孔的轴线所在平面与本发明系统质心距离为第二距离,第一距离和第二距离相同,下端盖4的第四下端圆平面与壳体3的第三下端向上同心圆环面接触。关于壳体3的两个第三螺纹盲孔的轴线所在平面位于本发明系统质心下端距离,主要考虑以下两发方面,既不能太长,导致本发明系统在通过质心调节完成翻转的过程中,由于质心偏移量太大,需要调节的尺寸过多,这部分尺寸未装填液相材料,为无效长度,避免无效长度过多,也不能太短,本发明系统在通过质心调节完成翻转的过程中,由于质心偏移量太小,质心稍微的调节,导致本发明系统在空中旋转角度过大,产生了过大的角速度及角加速度,导致过大的惯性,容易发生危险。通过实验发现,当壳体3的两个第三螺纹盲孔的轴线所在平面位于本发明系统质心下端不低于120mm时,质心偏移量足够,本发明系统在通过质心调节完成翻转的过程中,质心稍微的调节,本发明系统在空中旋转角度不大,产生了的角速度及角加速度不大,在可控制范围以内,满足安全要求。当壳体3的两个第三螺纹盲孔的轴线所在平面位于本发明系统质心下端不超过140mm时,心偏移量不算过大,需要调节的尺寸不算过大,无效长度不超过总长度2%,认为在可接受范围以内。因此,壳体3的两个第三螺纹盲孔的轴线所在平面位于本发明系统质心下端120~140mm;本实施例中,壳体3的两个第三螺纹盲孔的轴线所在平面位于本发明系统质心下端120。关于壳体3的第三环形凸台的上端面距离壳体3的第三螺纹盲孔的轴线距离与壳体3的第三螺纹盲孔公称直径之比,壳体3的第三环形凸台的下端面距离壳体3的第三螺纹盲孔的轴线距离与壳体3的第三螺纹盲孔公称直径之比,主要考虑一下2个方面:既不能太小,导致强度不足,当本发明系统由吊环5吊起时,全部重量,作用在吊环5上,而吊环5将所有重量作用在壳体3的第三环形凸台上,若该尺寸太小,会从壳体3的第三环形凸台处发生断裂,导致系统失效。通过实验发现,当壳体3的第三环形凸台的上端面距离壳体3的第三螺纹盲孔的轴线距离与壳体3的第三螺纹盲孔公称直径之比不低于1.4,壳体3的第三环形凸台的下端面距离壳体3的第三螺纹盲孔的轴线距离与壳体3的第三螺纹盲孔公称直径之比不低于1.1时,壳体3的第三环形凸台强度足够。也不能太大,导致液体材料抛撒后形成的云团由于壳体3的第三环形凸台尺寸过大而发生分层,由于壳体3的第三环形凸台相当于加强筋,当壳体3的第三环形凸台比较小时,对抛撒云团影响不大,云团在后续扩散的时候可以连接到一起。当壳体3的第三环形凸台尺寸比较大时,对抛撒云团影响过大,云团在后续扩散的时候不能连接到一起,形成了断层,影响使用效果。通过实验发现,当壳体3的第三环形凸台的上端面距离壳体3的第三螺纹盲孔的轴线距离与壳体3的第三螺纹盲孔公称直径之比不超过1.6,壳体3的第三环形凸台的下端面距离壳体3的第三螺纹盲孔的轴线距离与壳体3的第三螺纹盲孔公称直径之比不超过1.3时,对抛撒云团影响不大,云团在后续扩散的时候可以连接到一起。因此,壳体3的第三环形凸台的上端面距离壳体3的第三螺纹盲孔的轴线距离为壳体3的第三螺纹盲孔公称直径的1.4~1.6倍,壳体3的第三环形凸台的下端面距离壳体3的第三螺纹盲孔的轴线距离为壳体3的第三螺纹盲孔公称直径的1.1~1.3。本实施例中,壳体3的第三环形凸台的上端面距离壳体3的第三螺纹盲孔的轴线距离为壳体3的第三螺纹盲孔公称直径的1.4倍,壳体3的第三环形凸台的下端面距离壳体3的第三螺纹盲孔的轴线距离为壳体3的第三螺纹盲孔公称直径的1.1。壳体3的两个第三螺纹盲孔的轴线位于同一水平面,关于壳体3的两个第三螺纹盲孔的轴线的夹角,主要考虑一下3个方面:旋转灵敏性,初始起吊安稳性,起吊能力。旋转灵敏性为本发明系统的质心偏移后,本发明系统进行空间旋转的灵敏程度,当旋转灵敏性不好时,本发明系统的质心偏移后,由于本发明系统的质心和两个第三螺纹盲孔连线在竖直方向比较靠近,竖直方向投影几乎重合,导致质心变化后,没有一个偏心的力使得本发明系统进行旋转,这时本发明系统为失稳状态,一旦发生旋转,将是急速大角度旋转,不符合本发明慢速的旋转原则。当旋转灵敏性较好时,本发明系统的质心和两个第三螺纹盲孔连线在竖直方向有一定距离,当本发明系统的质心偏移后,重量乘以本发明系统的质心和两个第三螺纹盲孔连线在竖直方向的距离,为使得本发明系统旋转的力矩,本发明系统随着质心的变化,随即进行空间旋转,避免了失稳的状态。通过实际试验,将旋转灵敏性分为3个标准,以及3个分值。旋转十分灵敏:10分;旋转偶尔灵敏:3分;旋转十分不灵敏:-3分。初始起吊安稳性为本发明系统在通过吊车初始起吊时,安稳程度。主要与吊车初始起吊后,本发明系统的姿态与起吊前相比,旋转的角度。由于吊车将本发明系统起吊的过程中,本发明系统的姿态受重力作用,进行相应的旋转,希望此时旋转的角度越小越好。因为起吊过程不像后续使用过程,旋转的速度可以精确控制,而起吊过程属于简单粗暴过程,希望尽可能小的减小旋转角度,使得壳体只受到向上的力,而进行向上的运动,空间姿态尽可能少的旋转,这样旋转角速度和角加速度都比较小,可以保障壳体安全性。当初始起吊安稳性比较好时,壳体的质心距离2个吊环5连线竖直距离较小,本发明稍微旋转,壳体的质心便可以和2个吊环5连线竖直方向重合,这时,本发明系统已经稳定,稍微旋转的过程中,角速度角加速度均较小,不会发生危险。当初始起吊安稳性不好时,壳体的质心距离2个吊环5连线竖直距离较大,本发明需要旋转很大角度,壳体的质心才能和2个吊环5连线竖直方向重合,这时,本发明系统才能稳定,旋转很大角度的过程中,角速度角加速度均较大,会发生危险。通过实际试验,将初始起吊安稳性分为3个标准,以及3个分值。旋转角度不超过3°:10分;旋转角度3°~10°:5分;旋转角度超过10°:0分。起吊能力为2个吊环5可以起吊的本发明系统的重量多少的能力。由于2个吊环5呈一定角度,起吊时,2个吊环5既承受剪切力,又承受弯转力矩,又承受拉力,应力状态十分复杂,多应力状态下,2个吊环5能承受的本发明系统的重力低于2个吊环实际的抗纯剪切能力。当本发明的结构使得起吊能力较好时,2个吊环5承受的力主要为剪切力,旋转弯矩和拉力均较小,这时,2个吊环5能起吊的本发明的重量接近2个吊环5实际的抗纯剪切能力。当本发明的结构使得起吊能力不好时,2个吊环5承受的力为剪切力、旋转弯矩和拉力均的混合作用,很容易达到2个吊环5母材的极限强度,这时,2个吊环5能起吊的本发明的重量很低,仅为2个吊环5实际的抗纯剪切能力的很小一部分,这时起吊时容易发生危险。通过实际试验,将起吊能力分为3个标准,以及3个分值。起吊重量为实际的抗纯剪切能力的80%以上:10分;起吊重量为实际的抗纯剪切能力的80%~60%:6分;起吊重量为实际的抗纯剪切能力的60%以下:2分。将壳体3的两个第三螺纹盲孔的轴线的夹角分为以下几个区间:179°~180°、178°~179°、177°~178°、176°~177°、175°~176°、174°~175°、173°~174°、172°~173°、171°~172°、170°~171°。分别对以上几个区间的壳体3的两个第三螺纹盲孔的轴线的夹角进行实验,并按照以上三项标准进行评价,获得分值如下:通过实验发现,当壳体3的两个第三螺纹盲孔的轴线的夹角为176°~178°时,获得分值最高,获得30分。因此,壳体3的两个第三螺纹盲孔的轴线的夹角为176°~178°。本实施例中,壳体3的两个第三螺纹盲孔的轴线的夹角为176°。壳体3的第三内圆柱面上带有两个加强筋,这两个加强筋均为环形,这两个加强筋与壳体3的第三内圆柱面均为移动配合接触,这两个加强筋相对壳体3只能沿着壳体3轴向运动,不能相对壳体3进行转动,这两个加强筋上均带有4个螺纹通孔,上端盖2上连接有4个丝杠,每个丝杠均与上端盖2转动配合接触,每个丝杠外表面均带有外螺纹,4个丝杠与两个加强筋的4个螺纹通孔配合,4个丝杠上端均连接一个定轴齿轮,上端盖2上带有另外4个定轴齿轮,另外这4个定轴齿轮与4个丝杠上端的定轴齿轮组成定轴轮系,定轴轮系每一个齿轮均带动另外七个齿轮转动,由这8个齿轮的转动可以带动壳体3的第三内圆柱面的两个加强筋轴向移动,实现质心的调节;由于壳体的旋转是靠质心变化,进而引起旋转力矩进行的。当需要旋转角度微调的时候,通过压缩空气毕竟每次每次改变的质心比较多,微调效果不好。通过两个移动加强筋,可以在调节壳体角度的时候实现微调,加强筋轴向移动带来的质心变化是细微的,产生的旋转效果也是细微的,这样可以实现旋转角度的微调,提高调节的精度。所述一种通过质心位置调节进行自动翻转的十吨级液相材料装填壳体,包括以下步骤:步骤1:将壳体3放在水平台上,使得壳体3的回转体轴线垂直于水平面;步骤2:将下端盖4与壳体3装配;步骤3:将抛撒管1与壳体3装配;步骤4:将上端盖2与壳体3装配;步骤5:将吊环5与壳体3装配;步骤6:将充气管7与壳体3装配;步骤7:将临时挡板8与壳体3装配;步骤8:将定位螺钉9与壳体3装配,定位螺钉9的下端与壳体3的第三上端向下同心圆环面平齐;步骤9:将液体6灌入抛撒管1的第一外圆柱面、上端盖2的第二下端同心圆平面、壳体3的第三内圆柱面和下端盖4的第四上端圆平面组成的封闭空间中;步骤10:将吊绳穿过吊环5的第五圆环体,再将吊绳挂在吊车上,通过吊车将壳体3吊起,使得临时挡板8与地面脱离;步骤11:将本发明的系统由起立姿态转变为躺下姿态:将充气管7的第七圆管的左端与高压空气泵连接,打开充气管7的第七开关,使高压空气进入下端盖4的第四下端圆平面、壳体3的第三下端内圆柱面和临时挡板8的第八上端圆平面组成的封闭空间中,通过高压气体挤压下端盖4,下端盖4再将压力传递给抛撒管1和液体6,液体6再将压力传递给上端盖2,使得抛撒管1、上端盖2、下端盖4和液体6同时向上移动,本发明的系统质心逐渐上移,本发明系统的姿态随着质心的上移逐渐由起立姿态转变为躺下姿态,待抛撒管1的回转体轴线与水平面平行,关闭充气管7的第七开关,断开充气管7的第七圆管的左端与高压空气泵的连接;步骤12:将本发明的系统由躺下姿态转变为起立姿态:打开充气管7的第七开关,放出下端盖4的第四下端圆平面、壳体3的第三下端内圆柱面和临时挡板8的第八上端圆平面组成的封闭空间中的高压气体,将充气管7的第七圆管的左端与真空泵连接,对下端盖4的第四下端圆平面、壳体3的第三下端内圆柱面和临时挡板8的第八上端圆平面组成的封闭空间进行抽真空,使得下端盖4的第四下端圆平面受到负压,下端盖4再将负压传递给抛撒管1和液体6,液体6再将负压传递给上端盖2,使得抛撒管1、上端盖2、下端盖4和液体6同时向靠近临时挡板8的方向移动,本发明的系统质心逐渐靠近临时挡板8,本发明系统的姿态随着质心的靠近临时挡板8逐渐由躺下姿态转变为起立姿态,待抛撒管1的回转体轴线与水平面垂直,关闭充气管7的第七开关,断开充气管7的第七圆管的左端与真空泵的连接;步骤13:将定位螺钉9拧紧,通过定位螺钉9挤压上端盖2的第二上端同心圆平面,固定上端盖2的位置,使得上端盖2与壳体3不能再发生相对运动,卸下临时挡板8,此时,本发明的系统完成实验前准备。使用原方案的翻转车进行壳体的从躺下姿态到起立姿态,及从起立姿态到躺下姿态的翻转实验,实验壳体重量为十吨,实验壳体内部状体液相材料,壳体厚度不超过10mm,为薄壁壳体,反复翻转实验结果如下:实验状态实验结果10mm壳体从起立姿态到躺下姿态壳体完好10mm壳体从躺下姿态到起立姿态壳体完好9mm壳体从起立姿态到躺下姿态壳体完好9mm壳体从躺下姿态到起立姿态壳体完好8mm壳体从起立姿态到躺下姿态壳体完好8mm壳体从躺下姿态到起立姿态壳体发生破坏7.5mm壳体从躺下姿态到起立姿态壳体发生破坏7.5mm壳体从躺下姿态到起立姿态无法进行7mm壳体从躺下姿态到起立姿态壳体发生破坏7mm壳体从躺下姿态到起立姿态无法进行6mm壳体从躺下姿态到起立姿态壳体发生破坏6mm壳体从躺下姿态到起立姿态无法进行5mm壳体从躺下姿态到起立姿态壳体发生破坏5mm壳体从躺下姿态到起立姿态无法进行分析可知,当壳体壁厚为8mm时,壳体从起立姿态到躺下姿态,壳体完好,但是壳体从躺下姿态到起立姿态便发生破坏,而壳体壁厚不超过7.5mm时,壳体从起立姿态到躺下姿态,便发生破坏。壳体壁厚至少为9mm时,才能确保从起立姿态到躺下姿态以及从躺下姿态到起立姿态均壳体完好。使用本发明的装置及方法,按照步骤1到步骤13,反复进行从躺下姿态到起立姿态,及从起立姿态到躺下姿态的翻转实验,实验壳体重量为十吨,实验壳体内部状体液相材料,壳体厚度为5mm,为薄壁壳体,反复翻转实验结果如下:实验状态实验结果第1次从起立姿态到躺下姿态壳体完好第1次从躺下姿态到起立姿态壳体完好第2次从起立姿态到躺下姿态壳体完好第2次从躺下姿态到起立姿态壳体完好第3次从起立姿态到躺下姿态壳体完好第3次从躺下姿态到起立姿态壳体完好第4次从起立姿态到躺下姿态壳体完好第4次从躺下姿态到起立姿态壳体完好第5次从起立姿态到躺下姿态壳体完好第5次从躺下姿态到起立姿态壳体完好第6次从起立姿态到躺下姿态壳体完好第6次从躺下姿态到起立姿态壳体完好第7次从起立姿态到躺下姿态壳体完好第7次从躺下姿态到起立姿态壳体完好第8次从起立姿态到躺下姿态壳体完好第8次从躺下姿态到起立姿态壳体完好第9次从起立姿态到躺下姿态壳体完好第9次从躺下姿态到起立姿态壳体完好第10次从起立姿态到躺下姿态壳体完好第10次从躺下姿态到起立姿态壳体完好分析可知,总重量为10吨的液相材料装填薄壁壳体,壳体壁厚5mm,连续进行十次由起立姿态到躺下姿态,再由躺下姿态到起立姿态的翻转实验,壳体完好。对于十吨级装填液相材料的薄壁壳体,使用本发明进行翻转,壳体壁厚可以减少至原翻转方案的55%,大幅度降低了壳体壁厚,减少了壳体壁厚对抛撒范围的影响,增加了产品的使用效果。本发明的一种通过质心位置调节进行自动翻转的十吨级液相材料装填壳体,首先将装填液相材料的薄壁壳体在中部加强筋位置吊起来,通过调节壳体质心位置,使得壳体的空间姿态随着质心的变化进行自适应调整,逐渐完成从躺下姿态到起立姿态,或从起立姿态到躺下姿态的翻转工作。整个翻转过程为壳体在重力作用下自动完成,无需外力作用在壳体外壁上。壳体质心的调节可以精确控制,因此,壳体翻转过程中的速度可以精确控制,壳体翻转过程速度均匀且缓慢,避免了速度突变,避免了过大动载荷,保证了壳体强度不受破坏,进而保证了产品的安全性和可靠性。实施例8:如图1所示,本实施例给出一种通过质心位置调节进行自动翻转的十吨级液相材料装填壳体,包括抛撒管1,上端盖2,下端盖4,液体6,其特征在于还包括壳体3,吊环5,充气管7,临时挡板8,定位螺钉9;抛撒管1为第一圆柱体,抛撒管1的第一圆柱体为回转体,抛撒管1的第一圆柱体的上端面为第一上端圆平面,抛撒管1的第一圆柱体的侧面为第一外圆柱面,抛撒管1的第一圆柱体的下端面为第一下端圆平面;抛撒管1的回转体轴线与水平面垂直,抛撒管1的内部装有炸药,抛撒管1内部的炸药为抛撒液相材料形成云团的能量源;上端盖2为第二圆板,上端盖2的第二圆板为回转体,上端盖2的第二圆板中心带有第二圆孔,上端盖2的第二圆板的上端面为第二上端同心圆平面,上端盖2的第二圆板的外侧面为第二外圆柱面,上端盖2的第二圆板的下端面为第二下端同心圆平面,上端盖2的第二圆孔的内侧面为第二内圆柱面;上端盖2的回转体轴线与抛撒管1的回转体轴线重合,上端盖2位于抛撒管1上端外部,上端盖2的第二内圆柱面与抛撒管1的第一外圆柱面上端接触,上端盖2的第二上端同心圆平面与抛撒管1的第一上端圆平面共面;壳体3为第三圆筒体,壳体3的第三圆筒体为回转体,壳体3的第三圆筒体的外侧面为第三外圆柱面,壳体3的第三圆筒体的内侧面为第三内圆柱面,壳体3的第三圆筒体上端内侧带有第三上端内法兰,壳体3的第三上端内法兰下端面为第三上端向下同心圆环面,壳体3的第三上端内法兰上带有十六个第三螺纹通孔,壳体3的十六个第三螺纹通孔轴线与壳体3的回转体轴线平行,壳体3的十六个第三螺纹通孔绕壳体3的回转体轴线均匀分布,壳体3的第三圆筒体下端内侧带有第三下端内法兰,壳体3的第三下端内法兰上端面为第三下端向上同心圆环面,壳体3的第三下端内法兰下端面为第三下端向下同心圆环面,壳体3的第三下端内法兰的内侧面为第三下端内圆柱面,壳体3的第三下端内法兰上带有一个第三圆形通孔,壳体3的第三圆形通孔轴线与壳体3的回转体轴线垂直,壳体3的第三内圆柱面中部带有第三环形凸台,壳体3的第三外圆柱面中部带有两个第三螺纹盲孔,壳体3的两个第三螺纹盲孔的轴线均垂直于壳体3的回转体轴线;壳体3的回转体轴线与抛撒管1的回转体轴线重合,上端盖2的第二圆板位于壳体3的第三圆筒体内部,上端盖2的第二上端圆平面位于壳体3的第三上端向下同心圆环面下端,壳体3的第三内圆柱面与上端盖2的第二外圆柱面滑动配合接触;下端盖4为第四圆板,下端盖4的第四圆板为回转体,下端盖4的第四圆板的上端面为第四上端圆平面,下端盖4的第四圆板的外侧面为第四外圆柱面,下端盖4的第四圆板的下端面为第四下端圆平面;下端盖4的回转体轴线与抛撒管1的回转体轴线重合,下端盖4的第四上端圆平面与抛撒管1的第一下端圆平面连接,下端盖4的第四圆板位于壳体3的第三圆筒体内部,下端盖4的第四下端圆平面位于壳体3的第三下端向上同心圆环面上端,壳体3的第三内圆柱面与下端盖4的第四外圆柱面滑动配合接触;吊环5由左右两部分组成,吊环5的右部分为第五圆柱体,吊环5的第五圆柱体为回转体,吊环5的第五圆柱体的侧面带有第五外螺纹,吊环5的左部分为第五圆环体,吊环5的第五圆柱体和吊环5的第五圆环体转动配合连接,吊环5共两个;吊环5的第五圆柱体的回转体轴线与抛撒管1的回转体轴线垂直,吊环5的第五外螺纹安装在壳体3的第三螺纹盲孔中;液体6为被炸药抛撒后形成云团的液相材料;液体6位于抛撒管1的第一外圆柱面、上端盖2的第二下端同心圆平面、壳体3的第三内圆柱面和下端盖4的第四上端圆平面组成的封闭空间中;充气管7为第七圆管,充气管7的第七圆管为回转体,充气管7的第七圆管左端带有第七开关;充气管7的回转体轴线与抛撒管1的回转体轴线垂直,充气管7的第七圆管右端与壳体3的第三圆形通孔连接;临时挡板8为第八圆板,临时挡板8的第八圆板为回转体,临时挡板8的第八圆板的上端面为第八上端圆平面;临时挡板8的回转体轴线与抛撒管1的回转体轴线重合,临时挡板8位于壳体3下端,临时挡板8的第八上端圆平面与壳体3的第三下端向下同心圆环面连接;定位螺钉9为第九圆柱体,定位螺钉9的第九圆柱体为回转体,定位螺钉9的第九圆柱体的侧面为第九外圆柱面,定位螺钉9的第九外圆柱面下端带有第九外螺纹,定位螺钉9共十六个;定位螺钉9的回转体轴线与抛撒管1的回转体轴线平行,定位螺钉9的第九外螺纹安装在壳体3的第三螺纹通孔中。关于上端盖2的第二外圆柱面的轴向长度与上端盖2的第二圆板直径之比,主要考虑以下几个因素,既不能太大,以免增加上端盖2不必要的呆重,又不能太小以免上端盖2移动时卡主。通过实验发现,上端盖2在壳体3内部反复移动过程中,当厚度比较小的时候,容易出现卡主现象,一旦卡主,再大的挤压力也无法使其继续运动,而挤压力过大会作用在壳体3上,将壳体3挤破,导致失败。而当上端盖2的第二外圆柱面的轴向长度与上端盖2的第二圆板直径之比不低于1:10时,上端盖2的厚度足够,上端盖2在壳体3内部反复移动过程中,不再出现卡主的问题。上端盖2的重量随着厚度的增加而增大,对于液体材料装填壳体,总重量为10吨级,壳体翻转过程中的难度就在于,总重量太大,翻转惯性大,从而导致壳体承受的压力太大,容易发生破坏,上端盖2的重量过大,只会产生负面效果。因此,上端盖2的厚度越低越好。通过实测实验可知,当上端盖2的第二外圆柱面的轴向长度与上端盖2的第二圆板直径之比不超过1:9时,上端盖2的重量不到总重量的4%,认为不超过4%的上端盖重量在可接受范围以内,因此,上端盖2的第二外圆柱面的轴向长度与上端盖2的第二圆板直径之比不超过1:9。因此,上端盖2的第二外圆柱面的轴向长度与上端盖2的第二圆板直径之比为1:9~10;本实施例中,上端盖2的第二外圆柱面的轴向长度与上端盖2的第二圆板直径之比为1:9。下端盖4的设计同理,下端盖4的第四外圆柱面的轴向长度与下端盖4的第四圆板直径之比为1:9~10;本实施例中,下端盖4的第四外圆柱面的轴向长度与下端盖4的第四圆板直径之比为1:9。上端盖2的第二上端圆平面与壳体3的第三上端向下同心圆环面平行,上端盖2的第二上端圆平面与壳体3的第三上端向下同心圆环面之间的距离为第一距离,壳体3的两个第三螺纹盲孔的轴线所在平面与本发明系统质心距离为第二距离,第一距离和第二距离相同,下端盖4的第四下端圆平面与壳体3的第三下端向上同心圆环面接触。关于壳体3的两个第三螺纹盲孔的轴线所在平面位于本发明系统质心下端距离,主要考虑以下两发方面,既不能太长,导致本发明系统在通过质心调节完成翻转的过程中,由于质心偏移量太大,需要调节的尺寸过多,这部分尺寸未装填液相材料,为无效长度,避免无效长度过多,也不能太短,本发明系统在通过质心调节完成翻转的过程中,由于质心偏移量太小,质心稍微的调节,导致本发明系统在空中旋转角度过大,产生了过大的角速度及角加速度,导致过大的惯性,容易发生危险。通过实验发现,当壳体3的两个第三螺纹盲孔的轴线所在平面位于本发明系统质心下端不低于120mm时,质心偏移量足够,本发明系统在通过质心调节完成翻转的过程中,质心稍微的调节,本发明系统在空中旋转角度不大,产生了的角速度及角加速度不大,在可控制范围以内,满足安全要求。当壳体3的两个第三螺纹盲孔的轴线所在平面位于本发明系统质心下端不超过140mm时,心偏移量不算过大,需要调节的尺寸不算过大,无效长度不超过总长度2%,认为在可接受范围以内。因此,壳体3的两个第三螺纹盲孔的轴线所在平面位于本发明系统质心下端120~140mm;本实施例中,壳体3的两个第三螺纹盲孔的轴线所在平面位于本发明系统质心下端120。关于壳体3的第三环形凸台的上端面距离壳体3的第三螺纹盲孔的轴线距离与壳体3的第三螺纹盲孔公称直径之比,壳体3的第三环形凸台的下端面距离壳体3的第三螺纹盲孔的轴线距离与壳体3的第三螺纹盲孔公称直径之比,主要考虑一下2个方面:既不能太小,导致强度不足,当本发明系统由吊环5吊起时,全部重量,作用在吊环5上,而吊环5将所有重量作用在壳体3的第三环形凸台上,若该尺寸太小,会从壳体3的第三环形凸台处发生断裂,导致系统失效。通过实验发现,当壳体3的第三环形凸台的上端面距离壳体3的第三螺纹盲孔的轴线距离与壳体3的第三螺纹盲孔公称直径之比不低于1.4,壳体3的第三环形凸台的下端面距离壳体3的第三螺纹盲孔的轴线距离与壳体3的第三螺纹盲孔公称直径之比不低于1.1时,壳体3的第三环形凸台强度足够。也不能太大,导致液体材料抛撒后形成的云团由于壳体3的第三环形凸台尺寸过大而发生分层,由于壳体3的第三环形凸台相当于加强筋,当壳体3的第三环形凸台比较小时,对抛撒云团影响不大,云团在后续扩散的时候可以连接到一起。当壳体3的第三环形凸台尺寸比较大时,对抛撒云团影响过大,云团在后续扩散的时候不能连接到一起,形成了断层,影响使用效果。通过实验发现,当壳体3的第三环形凸台的上端面距离壳体3的第三螺纹盲孔的轴线距离与壳体3的第三螺纹盲孔公称直径之比不超过1.6,壳体3的第三环形凸台的下端面距离壳体3的第三螺纹盲孔的轴线距离与壳体3的第三螺纹盲孔公称直径之比不超过1.3时,对抛撒云团影响不大,云团在后续扩散的时候可以连接到一起。因此,壳体3的第三环形凸台的上端面距离壳体3的第三螺纹盲孔的轴线距离为壳体3的第三螺纹盲孔公称直径的1.4~1.6倍,壳体3的第三环形凸台的下端面距离壳体3的第三螺纹盲孔的轴线距离为壳体3的第三螺纹盲孔公称直径的1.1~1.3。本实施例中,壳体3的第三环形凸台的上端面距离壳体3的第三螺纹盲孔的轴线距离为壳体3的第三螺纹盲孔公称直径的1.4倍,壳体3的第三环形凸台的下端面距离壳体3的第三螺纹盲孔的轴线距离为壳体3的第三螺纹盲孔公称直径的1.1。壳体3的两个第三螺纹盲孔的轴线位于同一水平面,关于壳体3的两个第三螺纹盲孔的轴线的夹角,主要考虑一下3个方面:旋转灵敏性,初始起吊安稳性,起吊能力。旋转灵敏性为本发明系统的质心偏移后,本发明系统进行空间旋转的灵敏程度,当旋转灵敏性不好时,本发明系统的质心偏移后,由于本发明系统的质心和两个第三螺纹盲孔连线在竖直方向比较靠近,竖直方向投影几乎重合,导致质心变化后,没有一个偏心的力使得本发明系统进行旋转,这时本发明系统为失稳状态,一旦发生旋转,将是急速大角度旋转,不符合本发明慢速的旋转原则。当旋转灵敏性较好时,本发明系统的质心和两个第三螺纹盲孔连线在竖直方向有一定距离,当本发明系统的质心偏移后,重量乘以本发明系统的质心和两个第三螺纹盲孔连线在竖直方向的距离,为使得本发明系统旋转的力矩,本发明系统随着质心的变化,随即进行空间旋转,避免了失稳的状态。通过实际试验,将旋转灵敏性分为3个标准,以及3个分值。旋转十分灵敏:10分;旋转偶尔灵敏:3分;旋转十分不灵敏:-3分。初始起吊安稳性为本发明系统在通过吊车初始起吊时,安稳程度。主要与吊车初始起吊后,本发明系统的姿态与起吊前相比,旋转的角度。由于吊车将本发明系统起吊的过程中,本发明系统的姿态受重力作用,进行相应的旋转,希望此时旋转的角度越小越好。因为起吊过程不像后续使用过程,旋转的速度可以精确控制,而起吊过程属于简单粗暴过程,希望尽可能小的减小旋转角度,使得壳体只受到向上的力,而进行向上的运动,空间姿态尽可能少的旋转,这样旋转角速度和角加速度都比较小,可以保障壳体安全性。当初始起吊安稳性比较好时,壳体的质心距离2个吊环5连线竖直距离较小,本发明稍微旋转,壳体的质心便可以和2个吊环5连线竖直方向重合,这时,本发明系统已经稳定,稍微旋转的过程中,角速度角加速度均较小,不会发生危险。当初始起吊安稳性不好时,壳体的质心距离2个吊环5连线竖直距离较大,本发明需要旋转很大角度,壳体的质心才能和2个吊环5连线竖直方向重合,这时,本发明系统才能稳定,旋转很大角度的过程中,角速度角加速度均较大,会发生危险。通过实际试验,将初始起吊安稳性分为3个标准,以及3个分值。旋转角度不超过3°:10分;旋转角度3°~10°:5分;旋转角度超过10°:0分。起吊能力为2个吊环5可以起吊的本发明系统的重量多少的能力。由于2个吊环5呈一定角度,起吊时,2个吊环5既承受剪切力,又承受弯转力矩,又承受拉力,应力状态十分复杂,多应力状态下,2个吊环5能承受的本发明系统的重力低于2个吊环实际的抗纯剪切能力。当本发明的结构使得起吊能力较好时,2个吊环5承受的力主要为剪切力,旋转弯矩和拉力均较小,这时,2个吊环5能起吊的本发明的重量接近2个吊环5实际的抗纯剪切能力。当本发明的结构使得起吊能力不好时,2个吊环5承受的力为剪切力、旋转弯矩和拉力均的混合作用,很容易达到2个吊环5母材的极限强度,这时,2个吊环5能起吊的本发明的重量很低,仅为2个吊环5实际的抗纯剪切能力的很小一部分,这时起吊时容易发生危险。通过实际试验,将起吊能力分为3个标准,以及3个分值。起吊重量为实际的抗纯剪切能力的80%以上:10分;起吊重量为实际的抗纯剪切能力的80%~60%:6分;起吊重量为实际的抗纯剪切能力的60%以下:2分。将壳体3的两个第三螺纹盲孔的轴线的夹角分为以下几个区间:179°~180°、178°~179°、177°~178°、176°~177°、175°~176°、174°~175°、173°~174°、172°~173°、171°~172°、170°~171°。分别对以上几个区间的壳体3的两个第三螺纹盲孔的轴线的夹角进行实验,并按照以上三项标准进行评价,获得分值如下:壳体3的两个第三螺纹盲孔的轴线的夹角旋转灵敏性初始起吊安稳性起吊能力总分179°~180°-3101017178°~179°3101023177°~178°10101030176°~177°10101030175°~176°1051025174°~175°105621173°~174°105621172°~173°105621171°~172°100616170°~171°100212通过实验发现,当壳体3的两个第三螺纹盲孔的轴线的夹角为176°~178°时,获得分值最高,获得30分。因此,壳体3的两个第三螺纹盲孔的轴线的夹角为176°~178°。本实施例中,壳体3的两个第三螺纹盲孔的轴线的夹角为176°。壳体3的第三圆筒体的上端左边带有一个活塞,壳体3的第三圆筒体的上端右边带有一个活塞,壳体3的第三圆筒体的下端左边带有一个活塞,壳体3的第三圆筒体的下端右边带有一个活塞,每个活塞均与壳体3螺纹配合连接,每个活塞内侧连接一个万向铰链,通过连杆将壳体3的第三圆筒体的上端左边的活塞的万向铰链和壳体3的第三圆筒体的下端右边的活塞的万向铰链连接,通过连杆将壳体3的第三圆筒体的下端左边的活塞的万向铰链和壳体3的第三圆筒体的上端右边的活塞的万向铰链连接,壳体3的第三圆筒体的上端左边的活塞的万向铰链和壳体3的第三圆筒体的下端右边的活塞的万向铰链组成双万向铰链机构,壳体3的第三圆筒体的下端左边的活塞的万向铰链和壳体3的第三圆筒体的上端右边的活塞的万向铰链组成双万向铰链机构,旋转下端的活塞可以带动上端的活塞进行旋转,使得下端的流体进入上端的空间,或者使得上端的流体进入下端的空间,使得本发明具有质心微调功能;由于通过气体压力进行质心调节,每次调节量比较大,气体的开关很难精确控制流量,而质心的调节很难实现微调。而通过上下活塞的移动,使得内部液相材料可以微控制的进行调节,进而实现质心的微调,有利于精确控制壳体旋转角度,实现旋转工作的精细化。所述一种通过质心位置调节进行自动翻转的十吨级液相材料装填壳体,包括以下步骤:步骤1:将壳体3放在水平台上,使得壳体3的回转体轴线垂直于水平面;步骤2:将下端盖4与壳体3装配;步骤3:将抛撒管1与壳体3装配;步骤4:将上端盖2与壳体3装配;步骤5:将吊环5与壳体3装配;步骤6:将充气管7与壳体3装配;步骤7:将临时挡板8与壳体3装配;步骤8:将定位螺钉9与壳体3装配,定位螺钉9的下端与壳体3的第三上端向下同心圆环面平齐;步骤9:将液体6灌入抛撒管1的第一外圆柱面、上端盖2的第二下端同心圆平面、壳体3的第三内圆柱面和下端盖4的第四上端圆平面组成的封闭空间中;步骤10:将吊绳穿过吊环5的第五圆环体,再将吊绳挂在吊车上,通过吊车将壳体3吊起,使得临时挡板8与地面脱离;步骤11:将本发明的系统由起立姿态转变为躺下姿态:将充气管7的第七圆管的左端与高压空气泵连接,打开充气管7的第七开关,使高压空气进入下端盖4的第四下端圆平面、壳体3的第三下端内圆柱面和临时挡板8的第八上端圆平面组成的封闭空间中,通过高压气体挤压下端盖4,下端盖4再将压力传递给抛撒管1和液体6,液体6再将压力传递给上端盖2,使得抛撒管1、上端盖2、下端盖4和液体6同时向上移动,本发明的系统质心逐渐上移,本发明系统的姿态随着质心的上移逐渐由起立姿态转变为躺下姿态,待抛撒管1的回转体轴线与水平面平行,关闭充气管7的第七开关,断开充气管7的第七圆管的左端与高压空气泵的连接;步骤12:将本发明的系统由躺下姿态转变为起立姿态:打开充气管7的第七开关,放出下端盖4的第四下端圆平面、壳体3的第三下端内圆柱面和临时挡板8的第八上端圆平面组成的封闭空间中的高压气体,将充气管7的第七圆管的左端与真空泵连接,对下端盖4的第四下端圆平面、壳体3的第三下端内圆柱面和临时挡板8的第八上端圆平面组成的封闭空间进行抽真空,使得下端盖4的第四下端圆平面受到负压,下端盖4再将负压传递给抛撒管1和液体6,液体6再将负压传递给上端盖2,使得抛撒管1、上端盖2、下端盖4和液体6同时向靠近临时挡板8的方向移动,本发明的系统质心逐渐靠近临时挡板8,本发明系统的姿态随着质心的靠近临时挡板8逐渐由躺下姿态转变为起立姿态,待抛撒管1的回转体轴线与水平面垂直,关闭充气管7的第七开关,断开充气管7的第七圆管的左端与真空泵的连接;步骤13:将定位螺钉9拧紧,通过定位螺钉9挤压上端盖2的第二上端同心圆平面,固定上端盖2的位置,使得上端盖2与壳体3不能再发生相对运动,卸下临时挡板8,此时,本发明的系统完成实验前准备。使用原方案的翻转车进行壳体的从躺下姿态到起立姿态,及从起立姿态到躺下姿态的翻转实验,实验壳体重量为十吨,实验壳体内部状体液相材料,壳体厚度不超过10mm,为薄壁壳体,反复翻转实验结果如下:分析可知,当壳体壁厚为8mm时,壳体从起立姿态到躺下姿态,壳体完好,但是壳体从躺下姿态到起立姿态便发生破坏,而壳体壁厚不超过7.5mm时,壳体从起立姿态到躺下姿态,便发生破坏。壳体壁厚至少为9mm时,才能确保从起立姿态到躺下姿态以及从躺下姿态到起立姿态均壳体完好。使用本发明的装置及方法,按照步骤1到步骤13,反复进行从躺下姿态到起立姿态,及从起立姿态到躺下姿态的翻转实验,实验壳体重量为十吨,实验壳体内部状体液相材料,壳体厚度为5mm,为薄壁壳体,反复翻转实验结果如下:实验状态实验结果第1次从起立姿态到躺下姿态壳体完好第1次从躺下姿态到起立姿态壳体完好第2次从起立姿态到躺下姿态壳体完好第2次从躺下姿态到起立姿态壳体完好第3次从起立姿态到躺下姿态壳体完好第3次从躺下姿态到起立姿态壳体完好第4次从起立姿态到躺下姿态壳体完好第4次从躺下姿态到起立姿态壳体完好第5次从起立姿态到躺下姿态壳体完好第5次从躺下姿态到起立姿态壳体完好第6次从起立姿态到躺下姿态壳体完好第6次从躺下姿态到起立姿态壳体完好第7次从起立姿态到躺下姿态壳体完好第7次从躺下姿态到起立姿态壳体完好第8次从起立姿态到躺下姿态壳体完好第8次从躺下姿态到起立姿态壳体完好第9次从起立姿态到躺下姿态壳体完好第9次从躺下姿态到起立姿态壳体完好第10次从起立姿态到躺下姿态壳体完好第10次从躺下姿态到起立姿态壳体完好分析可知,总重量为10吨的液相材料装填薄壁壳体,壳体壁厚5mm,连续进行十次由起立姿态到躺下姿态,再由躺下姿态到起立姿态的翻转实验,壳体完好。对于十吨级装填液相材料的薄壁壳体,使用本发明进行翻转,壳体壁厚可以减少至原翻转方案的55%,大幅度降低了壳体壁厚,减少了壳体壁厚对抛撒范围的影响,增加了产品的使用效果。本发明的一种通过质心位置调节进行自动翻转的十吨级液相材料装填壳体,首先将装填液相材料的薄壁壳体在中部加强筋位置吊起来,通过调节壳体质心位置,使得壳体的空间姿态随着质心的变化进行自适应调整,逐渐完成从躺下姿态到起立姿态,或从起立姿态到躺下姿态的翻转工作。整个翻转过程为壳体在重力作用下自动完成,无需外力作用在壳体外壁上。壳体质心的调节可以精确控制,因此,壳体翻转过程中的速度可以精确控制,壳体翻转过程速度均匀且缓慢,避免了速度突变,避免了过大动载荷,保证了壳体强度不受破坏,进而保证了产品的安全性和可靠性。当前第1页1 2 3 
起点商标作为专业知识产权交易平台,可以帮助大家解决很多问题,如果大家想要了解更多知产交易信息请点击 【在线咨询】或添加微信 【19522093243】与客服一对一沟通,为大家解决相关问题。
此文章来源于网络,如有侵权,请联系删除
相关标签:



tips