一种双制式新能源复合轨道系统的制作方法



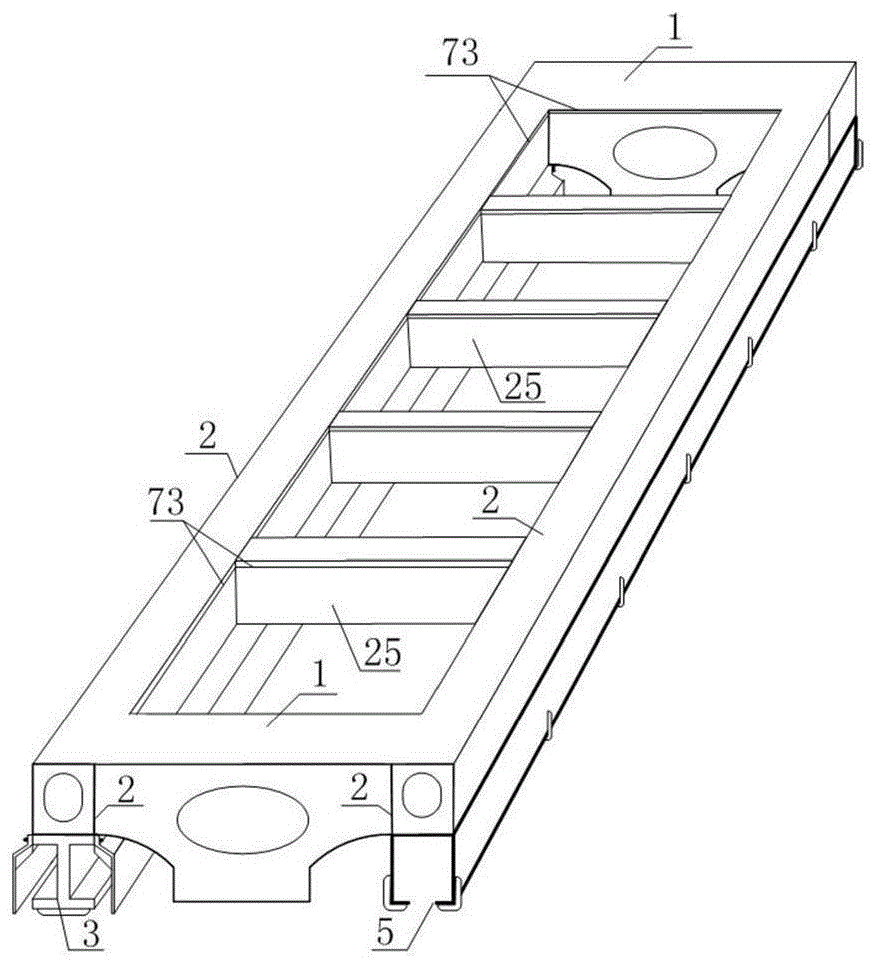
本发明涉及一种双制式新能源复合轨道系统,属于交通技术领域,尤其是一种具有新能源光伏系统和安全救生通道的交通复合轨道运输系统,由复合轨道梁、墩柱、安全救生通道和新能源光伏系统组成。
背景技术:
自世界第一条单轨空中列车建成运行118年来,单轨交通系统不断创新和完善,各种轨道结构持续创新,跨坐式单轨、磁浮单轨、索道单轨等等多种制式的单轨交通技术应运而生。
cn201621135767.6公开一种车箱贯通的悬挂式空中列车,包括轨道梁、走行机构、车箱,走行构架设于轨道梁内,车箱固设于走行构架底部。
cn201620190482.6、cn201620157755.7公开一种空中轨道列车的基桩梁改进结构,包括基桩、以及安装在基桩上的轨道梁,所属的轨道梁是在目前常规轨道梁上开一系列椭圆减重孔,以降低轨道梁的重量。
cn201621135767.6公开一种空中列车墩柱结构,由两根支撑立柱,上部由一根连接横梁相连,上顶端是一根悬挂横梁的框架结构,悬挂横梁的两端悬挂列车轨道。
cn201510741082.x、cn201520873741.0公开一种重载型空中列车,包括支柱以及固定于支柱上的轨道梁,所述支柱顶部具有支柱悬臂,所述支柱悬臂横桥向设有向下方向的两块吊板,吊板下方设置有轨道梁,轨道梁内设有行走机构,行走机构底部与列车本体固定连接,所述的支柱内部和/或外部设有重载结构。
cn201710059568.4、cn201710059520.3公开了一种基于装配式技术的悬挂式单轨交通钢混组合轨道梁,轨道梁顶板1是混凝土平板结构,轨道梁腹板2是波纹钢板,轨道梁底板3是钢板。
cn201710059423.4公开了一种基于装配式技术的悬挂式单轨交通结构体系。预制装配式梁为装配式闭口组合轨道梁或装配式混凝土轨道梁或装配式开口组合轨道梁,采用吊挂方式吊挂在钢墩或混凝土墩下方。
cn201720100635.8公开了一种基于装配式技术的悬挂式单轨交通底部开口轨道梁,该专利公开的底部开口轨道梁是全混凝土结构轨道梁。
cn201020529403.2公开了一种悬挂式单轨交通系统,该实用新型提供了一种悬挂式单轨交通系统,包括:工形轨道梁、支撑轨道梁的立柱、设置在轨道梁上的转向架构架、悬挂于转向架构架下方的车厢、设置在转向架构架上的驱动轮和导向轮。
cn201610087715.4、cn201610088050.9、cn201620123150.6、201620123144.0、cn201620123571.9公开了一种悬挂式单轨交通底板开口组合箱型轨道梁悬挂体系,代替现有的钢结构形式的钢制箱形轨道梁和钢立柱。将拉索依次穿过桥墩盖梁和底座,将底板开口组合箱型轨道梁悬挂在桥墩盖梁的下方,由此形成悬挂式底板开口组合箱型轨道梁悬挂体系。
cn201610090021.6、cn201610087731.3、cn201720104979.6、、cn201620123586.5、cn201620123200.0公开了一种底板外伸、顶板悬挂的组合箱型轨道梁,把混凝土顶板和波纹钢腹板的组合箱型轨道梁悬挂在混凝土桥墩盖梁的下方。解决线形控制难及易腐蚀等问题。
cn201710059549.1、cn201610087771.8公开了一种基于装配式技术的悬挂式单轨交通底部开口轨道梁,该底部开口轨道梁是全混凝图结构。
cn201610088053.2、cn201620123563.4、cn201610089952.4公开了一种底板开口、顶板悬挂的混凝土轨道梁,全混凝图结构底部开口轨道梁的悬挂体系。
cn201610088052.8、cn201620125899.4公开了一种悬挂式单轨交通底板外伸组合箱型轨道梁挡雪板,是一种预制波纹钢板垂直挡雪板。
cn201620125923.4实用新型公开了一种采用预应力筋的悬挂式底板开口组合箱型轨道梁,涉及桥梁领域,具体地说是在悬挂式单轨交通底板开口组合箱型轨道梁中设置预应力,以改善底板开口组合箱型轨道梁的受力状态。
cn201711159220.9公开了一种刚性悬挂式单轨交通体系,应用于轨道交通。本发明所要解决的技术问题是:提供一种刚性悬挂式单轨交通体系,通过采用刚性轨道梁,刚性转向架和刚性桥墩系统,车体和转向架之间刚性连接,实现结构体系的刚性化,使轨道梁变形和车体晃动角度减小。
cn201710059617.4公开了一种装配式单轨交通系统,具体涉及装配式技术在跨座式单轨交通和悬挂式单轨交通中的应用,解决目前单轨交通系统尚未采用标准化设计、预制化生产、装配式施工等问题。装配式单轨交通系统包括装配式轨道梁、装配式桥墩和装配式车站,其特征在于:装配式轨道梁、装配式桥墩和装配式车站。
cn201811600911.2公开了一种侧挂式高架交通系统,包括若干墩柱、若干轨道梁和用于连接所述墩柱和轨道梁的连接装置,所述墩柱的上端面中部设置有空腔,相邻所述墩柱之间连接有所述轨道梁,所述连接装置包括可伸缩连接件和固定连接件。
cn201820752488.7公开了一种用于全预制货运悬挂式单轨的横梁与轨道梁的连接构造,包括在横梁内部预加工有两排螺栓孔,以及分别设于轨道梁两端部的两排螺栓安装孔和橡胶板,所述橡胶板、横梁和轨道梁之间通过螺栓相连接。
cn201820386679.6公开了具有多层轨道梁安装结构的支撑立柱和空中列车轨道系统,支撑立柱包括多层设置的多个立柱单元、支墩和悬臂,可以同时架设多条轨道梁。
cn201830493146.3公开了10种双制式单轨交通结构外观设计。设计1为上钢箱磁浮轨道梁下工字钢悬挂式单轨轨道梁独墩柱式结构,设计2为上钢箱磁浮轨道梁下底部开口钢箱悬挂式单轨轨道梁独墩柱式结构,设计3为上工字钢磁浮轨道梁下工字钢悬挂式单轨轨道梁独墩柱式结构,设计4为上工字钢磁浮轨道梁下底部开口钢箱悬挂式单轨轨道梁独墩柱式结构,设计5为上钢箱跨座式单轨轨道梁下工字钢悬挂式单轨轨道梁独墩柱式结构,设计6为上钢箱跨座式单轨轨道梁下底部开口钢箱悬挂式单轨轨道梁独墩柱式结构,设计7为上混凝土磁浮轨道梁下底部开口混凝土悬挂式单轨轨道梁独墩柱式结构,设计8为上混凝土跨座式单轨轨道梁下底部开口混凝土悬挂式单轨轨道梁独墩柱式结构,设计9为上混凝土磁浮轨道梁下工字钢悬挂式单轨轨道梁框架墩柱式结构,设计10为上混凝土跨座式单轨轨道梁下工字钢悬挂式单轨轨道梁框架墩柱式结构。
cn201811021475.3公开了一种双制式单轨交通系统,包括跨座式单轨交通系统、悬挂式单轨交通系统和磁浮交通系统,其特征在于:在同一个墩柱上设有双制式的单轨交通;或是在同一个框架上设有双制式的单轨交通。
cn201811021621.2公开了一种悬挂式物流单轨交通系统,采用悬挂式物流单轨轨道梁桥系统、悬挂式物流单轨车辆系统、悬挂式物流单轨道岔系统、悬挂式物流单轨装卸系统和悬挂式物流单轨信号系统
cn201811021615.7公开了一种单层立柱式空间运输体系,通过将两种单轨交通结合到同一个单层立柱式空间体系中,或将一种单轨交通和其他交通结合到同一个单层立柱式空间体系中,形成包含多制式交通的基于单轨交通的单层立柱式空间运输体系。
cn201820994578.7公开了一种桥墩和具有其的轨道交通系统,所述桥墩用于支撑上跨下挂式结构的轨道梁且包括:墩柱、侧梁和横梁,所述侧梁为两个且每个所述侧梁的下端均连接至所述墩柱,所述横梁连接在两个所述侧梁的上端之间,所述横梁与两个所述侧梁之间限定出过车空间,所述轨道梁安装在所述横梁上,所述轨道梁的下挂部位于所述过车空间内,所述轨道梁的上跨部位于所述横梁的上方。
cn201720295758.1公开了组合式悬挂单轨交通轨道梁,它包括第一轨道梁主体和第二轨道梁主体,第一轨道梁主体和第二轨道梁主体组合成一个整的轨道梁主体;所述的第一轨道梁主体和第二轨道梁主体均包括轨道梁腹板、轨道梁顶部内翼缘、轨道梁底部内翼缘和轨道梁底部外翼缘;所述的第一轨道梁主体和第二轨道梁主体均采用轧制成型。
cn201810999180.7公开了一种悬挂式单轨车及其轨道梁。所述悬挂式单轨车轨道梁包括装在柱墩顶部且纵向延伸的中间梁模块和装在柱墩顶部且纵向延伸的两组侧边梁模块;两组侧边梁模块对称设置在中间梁模块的两侧,且中间梁模块与相应的侧边梁模块之间可拆卸地固定相连,每个侧边梁模块的外端部设有纵向延伸的走行轨。
cn201810999164.8公开了一种悬挂式单轨车及其配套的轨道梁桥。所述轨道梁桥包括桥墩,装在两个桥墩之间的左右两组箱梁;每个所述箱梁的底端具有支撑梁,所述支撑梁的悬挑部上固定设置有悬挂式单轨车走行轨道;所述悬挂式单轨车走行轨道包括工字梁,固定在工字梁顶端的走行轨;所述工字梁固定在所述支撑梁的悬挑部上;所述走行轨包括轨道梁和设置在轨道梁左右两侧的扣件,以及在扣件与轨道梁的侧壁之间的减震件。
cn201810824283.x公开了一种悬挂式轨道交通双线混凝土墩梁系统,包括混凝土轨道梁、盖梁、牛腿、支座、墩柱、承台和桩基础;所述牛腿设置于所述盖梁两侧,所述牛腿顶面设置所述支座;所述混凝土轨道梁通过所述支座支撑安装于所述盖梁上;所述混凝土轨道梁为工字型截面腹板,所述工字型截面腹板为中空结构;所述混凝土轨道梁的跨度为25m,吊重为76-79t,混凝土用量指标为单线1.19m3/m。
综上所述,现有技术所公开的刚性轨道结构主要是纯混凝土结构,现有技术所公开的半柔性轨道主要是纯钢结构,纯混凝土结构刚性虽然高、但对动态载荷下抗冲击的韧性和弹性不足、且纯混凝土轨道达到设计的结构强度和乘载载荷要求的设计时其厚度较大、综合重量大、地下墩基必须加大而且加深、梁的综合制造成本和运输安装成本都大幅度提高,纯钢结构韧性和弹性好、抗动态载荷冲击能力强、但在大跨度下的刚性不足、挠度大。上述轨道结构承载在强侧向风和动态载荷冲击下物流货运车和客车运行的稳定性存在问题、承载新能源光伏系统重量的能力略显不足。所公开的备用供电方式主要采用车带电池组或全部采用电池组驱动运行,电池组重量太大每天随车往返增加大量能耗。随着我国物流快速发展,大量物流汽车或电动车遍布城市每个角落,占用路权增加了城市道路拥堵和污染问题越来越严重。
技术实现要素:
本发明的目的在于针对现有技术中存在的上述问题,提供一种双制式新能源复合轨道系统,既具有高刚度、又有好的抗动态冲击的韧性和弹性、综合重量轻、安全性高、可承载新能源光伏系统重量和安全疏散通道;复合轨道梁转弯半径小于30米、爬坡能力大于100‰,充分利用道路两侧的绿化带或中分带、不占城市路权、不增加新的拥堵,节约土地、轨道建设拆迁少;噪音低、无污染物排放、节能环保;具备主动快速安全救生通道;新能源光伏系统提供环保不间断动力电源和轨道照明,亮化美化城市;复合轨道梁在城市间,既承担物流主干线轨道功能,连接机场、港口、铁路站和城市物流中心,又兼顾支线和末端轨道,较好地解决物流服务最后一公里问题;复合轨道梁在市区既可通行无人驾驶客运车辆,又能通行现代物流无人驾驶物流车辆,运行速度70~120公里/小时。充分利用城市道路和高速路低空闲置资源,解决了城市交通拥堵难题和物流快速发展造成的运输问题,提供了一种城市智慧交通和智慧物流的解决方案。
发明概述
本发明提供一种双制式新能源复合轨道系统,由复合轨道梁、墩柱、安全救生通道和新能源光伏系统组成。墩柱每间隔10~120米一根安装在城市道路绿化带上或高速路边坡和中分带上,复合轨道梁安装在墩柱上,安全救生通道和新能源光伏系统安装在复合轨道梁上方组成连续延伸的复合轨道系统,无人驾驶新能源物流车或客运车在复合轨道系统内安全高效运行。
发明详述
本发明提供一种复合轨道梁,所述复合轨道梁主体结构为工字复合轨道梁和/或口字复合轨道梁。
所述工字复合轨道梁,由箱梁(2)和工字轨道(3)复合而成。箱梁(2)通过钢筋(21)和剪力板(21a)焊接在工字轨道(3)的工字钢上翼板(36)的上表面、并用混凝土浇注使箱梁(2)与工字轨道(3)复合成固定结构的工字复合轨道梁,所述剪力板(21a)主要是提高混凝土结构与钢结构结合界面的抗热胀冷缩产生剪切力的能力和安全可靠性。其突出优点是充分将钢筋混凝土结构的箱梁(2)的刚性和纯钢结构的工字轨道(3)的强度和柔韧性有机结合在一起,一是使钢筋混凝土结构的箱梁(2)结构优化到最合理刚度、厚度减薄、总重量达到最轻,二是使纯钢结构的工字轨道(3)结构优化到强度、刚度和柔韧性最合理,二者复合后的刚度、强度、柔韧性达到最优,且有足够高承载物流车或客运车动态冲击载荷和风载、热胀冷缩应力、光伏新能源系统载荷等的综合能力。如图1、图2和图3所示。所述钢筋(21)和剪力板(21a)的数量由本领域技术人员根据载荷要求和计算结果进行设计。
所述剪力板(21a)选自普通钢板,钢板上冲有多个孔以增强与混凝土的结合力。
优选的,所述箱梁(2)通过其预埋螺柱(23)和螺帽(24)把工字钢上翼板(36)固定在箱梁(2)的下方,使箱梁(2)与工字轨道(3)复合成可拆卸结构的工字复合轨道梁。或所述箱梁(2)通过其预埋螺柱(23)和螺帽(24)、以及钢筋(21)和剪力板(21a)焊接在工字钢上翼板(36)上表面,三种复合方式共用使箱梁(2)与工字轨道(3)复合成的工字复合轨道梁连接更加牢固,进一步提高热胀冷缩抗剪能力和安全可靠性。所述钢筋(21)和剪力板(21a)的数量由本领域技术人员根据载荷要求和计算结果进行设计。
优选的,所述箱梁(2)为使用混凝土浇注而成的一体结构,包括钢筋(21)和箱梁减重孔(22),所述钢筋(21)内置于箱梁内且捆绑成矩形结构,矩形结构心部设置箱梁减重孔(22)。所述箱梁(2)为空心梁或实心梁,箱梁(2)外形是矩形、台形、圆形、椭圆形、曲线形或其它外观结构形状,由本领域技术人员进行专业设计和制造。如图1和图3所示。刚性的箱梁(2)和刚柔韧相济的工字轨道(3)的复合大幅度提高了轨道梁整体的刚度、强度、韧性、抗动态载荷冲击和抗震抗强风的稳定性、安全性,车辆在工字钢轨道上运行更加平稳,且综合重量轻、造价低。
优选的,所述工字轨道(3)由工字钢轨(31)、加强筋板(32)、耐磨钢板(39)组成。工字钢轨(31)包括水平方向相互平行的工字钢上翼板(36)、工字钢下翼板(37)、以及垂直于工字钢上翼板(36)和工字钢下翼板(37)且分别与工字钢上翼板(36)和工字钢下翼板(37)的中部连接的腹板(38),如图3、图1、图2所示。所述工字钢轨(31)由热轧或焊接生产。在工字钢下翼板(37)的上表面安装有耐磨钢板(39),耐磨钢板(39)提高工字钢轨(31)的使用寿命,耐磨钢板(39)可宽于工字钢下翼板(37),以增加在其上运行的动力车轮的宽度、提高运载能力和驱动摩擦力。优选的,在工字钢下翼板(37)的底部焊接有加强筋板(32),加强筋板(32)每间隔0.3米~5米焊接一个;优选的,工字钢上翼板(36)的两边安装有左右镜像对称的隔音防护罩(33),隔音防护罩(33)可以用螺栓(35)安装,也可以采用焊接或其他方式。在本发明的至少一个优选的实施例中,还包括防护罩支撑板(34),防护罩支撑板(34)焊接在隔音防护罩(33)的上部,以增强隔音防护罩(33)的结构强度,优选的,防护罩支撑板(34)每间隔0.3米~3米焊接一个。所述隔音防护罩(33)采用泡沫铝复合材料、玻纤或碳纤维复合材料、镁合金材料等轻量化材料制造,隔音降噪使环境噪声低于65分贝;防雨雪和轨道结冰,保证交通运输风雨冰雪天气畅通无阻,全天候运行;重量轻、综合建设成本低、且便于维护。由本领域技术人员进行专业设计和制造。如图2和图3所示。隔音防护罩(33)的形状可采用现有技术中的隔音防护罩的任何形状。
所述口字复合轨道梁,由箱梁(2)和口字钢轨道(5)上下复合而成,箱梁(2)通过钢筋(21)和剪力板(21a)焊接在口字钢轨顶板(52)上表面、并用混凝土浇注使箱梁(2)和口字钢轨道(5)复合成一个固定结构的口字复合轨道梁,所述剪力板(21a)主要是提高热胀冷缩抗剪能力和安全可靠性,其突出优点是充分将钢筋混凝土结构的箱梁(2)的刚性和纯钢结构的口字钢轨道(5)的强度、刚度和柔韧性有机结合在一起,一是使钢筋混凝土结构的箱梁(2)结构优化到最合理刚度、厚度减薄、总重量最轻,二是使纯钢结构的口字钢轨道(5)结构优化到强度、刚度和柔韧性最合理,二者复合后的刚度、强度、柔韧性达到最优,且有足够高承载物流车客运车动态冲击载荷和风载、热胀冷缩应力、太阳能新能源系统载荷等的能力。如图1、图2和图4所示。所述钢筋(21)和剪力板(21a)的数量由本领域技术人员根据载荷要求和计算结果进行设计。
优选的,所述箱梁(2)通过其预埋螺柱(23)和螺帽(24)把口字钢轨顶板(52)固定在箱梁(2)的下方,使箱梁(2)和口字钢轨道(5)复合成可拆卸结构的口字复合轨道梁。或所述箱梁(2)通过其预埋螺柱(23)和螺帽(24)、以及钢筋(21)和剪力板(21a)焊接在口字钢轨顶板(52)上表面,三种连接方式使箱梁(2)和口字钢轨道(5)复合连接更加牢固。刚性的箱梁(2)和刚柔相济的口字钢轨道(5)的复合大幅度提高了轨道梁整体的刚度、强度、抗动态载荷冲击和抗震抗强风的稳定性、安全性,车辆在工字钢轨道上运行更加平稳,且综合重量轻、造价低。
优选的,所述口字钢轨道(5)由口字钢轨顶板(52)、口字钢轨侧板(53)、口字钢轨轨道板(54)、l筋板(55)组成。口字钢轨顶板(52)两侧各垂直焊接一口字钢轨侧板(53),左右两侧的口字钢轨侧板(53)相互平行且口字钢轨侧板(53)底部各焊接一水平的口字钢轨轨道板(54),l筋板(55)焊接在左右口字钢轨侧板(53)下部外侧和口字钢轨轨道板(54)的底面,以加强其强度和稳定性。如图1、图2和图4所示。
优选的,左右口字钢轨轨道板(54)与口字钢轨顶板(52)水平方向平行且处于同一横截面上;左右口字钢轨轨道板(54)长度相等,左右口字钢轨轨道板(54)的总长度为口字钢轨顶板(52)长度的1/10~1/4。
优选的,本发明提供一种复合轨道梁,其特征在于,由复合轨道梁主体结构、盖梁(1)、横梁(25)组成;盖梁(1)包括盖梁左翼(11)、盖梁右翼(12);前后镜像对称各一个盖梁(1),前后盖梁左翼(11)的两端部分别与工字复合轨道梁或口字复合轨道梁上箱梁(2)的两端部用钢筋混凝土二次浇注复合在一起,前后盖梁右翼(12)的两端部分别与工字复合轨道梁或口字复合轨道梁上箱梁(2)的两端部用钢筋混凝土二次浇注复合在一起;左右两个复合轨道梁主体结构的两个箱梁(2)之间由0~60个或更多个横梁(25)横向相联接,进一步加强结构的刚度和强度,共同组成一榀复合轨道梁的完整结构。如图1所示。复合轨道梁主体结构的箱梁(2)的上表面、前后两个盖梁(1)的上表面、横梁(25)的上表面共同组成一个复合轨道梁的顶平面。
优选的,所述盖梁(1)前后镜像对称各一个,前后盖梁左翼(11)端部下方悬挂一条工字复合轨道梁或口字复合轨道梁,前后盖梁右翼(12)端部下方悬挂一条工字复合轨道梁或口字复合轨道梁,左右两工字复合轨道梁和/或口字复合轨道梁之间由0~60个或更多个横梁(25)横向相联接,组成复合轨道梁的另一种结构形式。如图9所示。
所述横梁(25)可由钢筋混凝土结构材料、玻璃纤维或碳纤维复合材料、镁铝合金或其他轻质结构材料制造而成,根据需要也可制造成实心横梁或空心横梁。优选的,所述空心横梁(25)是矩形、台形、圆形、椭圆形、曲线形或其它外观结构形状,由本领域技术人员进行设计和制造。优选的,所述横梁(25)的数量为5、10、20、30、40、50、60个以上及上述任意二个数值的组合。
优选的,所述盖梁(1)由盖梁左翼(11)、盖梁右翼(12)、盖梁基座(13)组成,盖梁(1)的上部包括盖梁左翼(11)和盖梁右翼(12)、底部是盖梁基座(13)用钢筋混凝土浇注成一个整体结构。如图1和图2所示。盖梁基座(13)安装在墩柱上。优选的,所述盖梁(1)还包括减重孔(14),减重孔(14)位于盖梁(1)的中部,减重孔(14)为1个或多个,减重孔(14)的设置是为了减轻盖梁(1)的重量,其数量和大小可以由本领域技术人员根据实际结构设计需要而设置。如图1、图2所示。
本发明提供一种双制式新能源复合轨道系统,由复合轨道梁、墩柱、安全救生通道和新能源光伏系统组成。墩柱安装在城市道路绿化带上或高速路两侧的边坡上或中分带上、每间隔10~120米一根沿道路延伸,每一榀复合轨道梁安装在前后两个墩柱上,每一榀复合轨道梁的长度与墩柱的间隔相对应,多榀复合轨道梁依次安装在多个墩柱上;安全救生通道和新能源光伏系统安装于复合轨道梁上表面,组成连续延伸的新能源复合轨道系统,无人驾驶物流车或客运车在复合轨道系统内安全高效运行。如图6和图2所示。
优选的,所述墩柱是安装在城市道路两侧的绿化带内,不占用路权,充分利用城市道路两侧的低空资源,为解决城市拥堵难题提供了一种智慧交通和智慧物流的解决方案。
优选的,所述墩柱包括y型墩柱(6)或通用的“i”型墩柱、或t型墩柱、或倒u型墩柱、或其他结构类型的墩柱,由本领域技术人员根据工程需要进行设计。所述y型墩柱(6)由y型槽(61)、墩柱身(62)、墩柱法兰(63)、墩基(65)组成。墩柱身(62)的顶部是y型槽(61)、墩柱身(62)的底部是墩柱法兰(63)用钢筋混凝土浇注成一个整体,墩柱身(62)通过墩柱法兰(63)安装于墩基(65)上;墩基(65)深埋在地下,墩基(65)上部预埋墩基螺栓(64),墩柱法兰(63)与墩基螺栓(64)连结。优选的,所述每个y型槽(61)内承载着前后两榀复合轨道梁系统主体的两个盖梁基座(14),即前后两榀复合轨道梁系统主体在y型墩柱(6)的y型槽(61)内对接,多榀复合轨道梁系统主体依次连接共同组成一条连续完整交通轨道。优选的,所述墩柱身(62)是矩形、方形、圆型、椭圆型或其他结构造型,下粗上细的台状结构,墩柱身(62)高1~30米、柱身(62)的中心线与地面垂直,外表面与地面成90度~105度角。如墩柱身(62)高10米、15米、20米、25米、30米或上述任意两个数值组成的范围。
优选的,所述y型墩柱(6)由t型墩柱(6a)替代。所述t型墩柱(6a)由盖梁a(1a)、盖梁左翼a(11a)、盖梁右翼a(12a)、墩柱身(61a)、墩柱法兰(63)、墩基(65)组成。墩柱身a(61a)的顶部是由盖梁a(1a)和盖梁左翼a(11a)、盖梁右翼a(12a)组成的盖梁,墩柱身a(61a)的底部是墩柱法兰(63),用钢筋混凝土浇注成一个整体,墩柱身a(61a)通过墩柱法兰(63)安装于墩基(65)上。优选的,所述墩柱身a(61a)是矩形、方形、圆型、椭圆型或其他结构造型,下粗上细的台状结构,墩柱身a(61a)的中心线与地面垂直,墩柱身a(61a)高1~30米、外表面与地面成90度~105度角。具体有本领域技术人员进行设计和制造。如墩柱身a(61a)高10米、15米、20米、25米、30米以上或上述任意两个数值组成的范围。如图9所示。
优选的,所述安全救生通道由救生通道网(7)、钢筋混凝土槽(73)组成。所述钢筋混凝土槽(73)是被预制在盖梁(1)、箱梁(2)和空心横梁(25)的上缘部,围成一个矩形槽,以安装救生通道网(7),如图2、图5和图7所示。救生通道网(7)是沿中部轴(72)可向上折叠的矩形框状结构,救生通道网(7)的矩形边框(71)扣在钢筋混凝土槽(73)内,当发生紧急情况时,用客车上的救生梯子向上顶开救生通道网(7)的一侧,使救生通道网(7)沿着中部轴(71)向上折翻过去,打开了一个救生天窗,救生梯挂在钢筋混凝土槽(73)内,乘客由救生梯快速爬上救生通道网(7)进行撤离,如图6、图7和图8所示。优选的,所述救生通道网(7)是由碳纤维加强的复合材料制成,结构强度高,每平米重量小于5公斤,每平米可承载重量大于300公斤。优选的,所述安全救生通道是主动救生通道,每辆车可配备4-10个救生梯,每批4-10人连续主动救生。
优选的,所述新能源光伏系统由光伏阵列组件(4)、光伏系统控制器(41)、蓄电池组(42)、并网逆变器(43)、切换控制器(44)、轨道亮化系统(45)、外电网系统(46)、薄膜光伏阵列组件(47)组成。光伏阵列组件(4)安装在箱梁(2)的上表面,光伏系统控制器(41)、蓄电池组(42)、并网逆变器(43)和切换控制器(44)分别安装在盖梁(1)上表面或盖梁减重孔(13)的空间内,所述薄膜光伏阵列组件(47)在每一个救生通道网(7)中部轴(72)的两侧各安装一片,不影响救生通道网(7)沿中部轴(72)向上的折叠功能,薄膜光伏阵列组件(47)与光伏阵列组件(4)并联,轨道亮化系统(45)安装在箱梁(2)的侧面和救生通道网(7)的边部,以新颖的交通轨道替代了城市的路灯,城市电线通讯线全部布置在轨道上方,亮化美化城市,还能承接公益广告和商业广告,夜间新能源储电装置能持续为救生通道照明、为城市道路照明。
光伏阵列组件(4)、光伏系统控制器(41)、蓄电池组(42)、并网逆变器(43)、切换控制器(44)、轨道亮化系统(45)、外电网系统(46)、薄膜光伏阵列组件(47)均采用现有技术。刚性复合轨道梁具备了较高的整体刚度、强度和韧性,且具有了足够的承载光伏阵列组件(4)重量的能力和光伏发电的能力。、薄膜光伏阵列组件(47)与光伏阵列组件(4)并联发的电送往光伏系统控制器(41),再由光伏系统控制器(41)送往蓄电池组(42)和并网逆变器(43),并网逆变器(43)输出电源为交流220v或110v送往切换控制器(44),由切换控制器(44)送往轨道亮化系统(45)和轨道供电线路,外电网系统(46)通过切换控制器(44)并网。常规运行白天以新能源供应电力为主、外电网系统(46)为辅助,晚上以外电网系统(46)供电为主、新能源电网蓄电池组(42)储备的电量作备用。光伏新能源电力以轨道照明亮化、公益广告、替代路灯照明为主。当特殊情况下外电网系统(46)突然全部停电,光伏新能源电力通过切换控制器(44)自动为轨道交通车辆供电,保证交通车辆安全到达下一个车站、确保承客安全撤离。光伏供电量可达到轨道交通用电的40%~50%,节能效果显著。如图6所示。
本发明提供一种双制式新能源复合轨道系统及其特点:
1)每一榀复合轨道梁由工字复合轨道梁、口字复合轨道梁、盖梁(1)、横梁(25)组成,前后两个盖梁(1)的盖梁左翼(11)分别与工字复合轨道梁的两端连为一体、前后两个盖梁右翼(12)分别与口字复合轨道梁的两端连为一体,工字复合轨道梁和口字复合轨道梁之间由0~60个或更多个空心横梁(25)横向相联接,组成一榀刚性复合轨道梁主体结构;复合轨道梁采用混凝土轻型优化结构梁与钢结构梁的复合结构,既具备满足要求的高刚度和高强度、又有一定韧性和弹性,达到优化的刚柔结合体,抗动态载荷冲击能力强、客运和物流车运行更稳定、安全性更高,噪声低于65分倍、乘座舒适。复合轨道梁综合重量比纯混凝土结构梁轻15%-20%,综合制造成本低。
2)每一榀刚性复合轨道梁长10米~120米,多榀刚性复合轨道梁安装在y型墩柱(6)上沿城市道路连续安装、延伸组成轨道系统,无人驾驶新能源物流车或客运车在工字复合轨道梁或口字复合轨道梁的轨道内安全高效运行;双制式新能源刚性复合轨道梁转弯半径小于30米、爬坡能力大于100‰,线路选择灵活,建设基本无需大拆迁,充分利用城市道路两侧的绿化带、不占城市路权、不增加新的拥堵。综合建设投资是轻轨投资的1/3-1/6、是地铁投资的1/6-1/12。可迁移更换线路再利用,迁移损失低。
3)安全救生通道安装在工字复合轨道梁和/或口字复合轨道梁、空心横梁(25)以及前后两个盖梁(1)之间围成的方框安全网槽内;安全救生通道是主动救生通道,每辆车可配备4-10个救生梯,每批4-10人同时连续主动救生。
4)新能源光伏系统安装在工字复合轨道梁和/或口字复合轨道梁和盖梁的上表面。常规运行白天以新能源供应电力为主、外电网系统为辅助,晚上以外电网系统供电为主、新能源电网蓄电池组储备的电量作备用。新能源光伏系统电力以轨道照明亮化、公益广告、替代路灯照明,美化了城市。当特殊情况下外电网系统突然全部停电,光伏新能源电力通过切换控制器自动为轨道交通车辆供电,保证交通车辆安全到达下一个车站、确保承客安全撤离。节能,无排放、无污染。光伏供电量可达到轨道交通用电的40%~50%,节能效果显著。
5)复合轨道梁的轨道结构决定了在此轨道上运行的车辆永远不会脱轨,安全性高、不受雨雪冰冻影响、运行计划率可达99.9%以上,大幅度提高了城市交通运输通行效率,较好地缓解决了城市堵车和物流运输问题,缩短了通行时间。充分利用城市低空资源,提供了一种城市智慧交通和智慧物流的解决方案。
附图说明
图1为本发明横截面示意图。
图2为本发明一榀复合轨道梁立体示意图。
图3为本发明工字复合轨道梁横截面示意图。
图4为本发明口字复合轨道梁横截面示意图。
图5为本发明一榀复合轨道梁aa剖面左视图示意图。
图6为本发明安全救生通道和新能源光伏系统示意图。
图7为本发明安全救生通道钢筋混凝土槽俯视示意图。
图8为本发明救生通道网示意图。
图9为本发明工字复合轨道梁和口字复合轨道梁的悬挂结构示意图。
1、盖梁,11、盖梁左翼,12、盖梁右翼,13、盖梁基座,14、减重孔、1a、盖梁a,11a、盖梁左翼a,12a、盖梁右翼a
2、箱梁,21、钢筋,21a、剪力板,22、箱梁减重孔,23、预埋螺柱,24螺帽,25、空心横梁,
3、工字轨道,31、工字钢轨,32、加强筋板,33、异型隔音防护罩,34、防护罩支撑板,35、螺栓,36、工字钢上翼板,37、工字钢下翼板,38、腹板,39、耐磨钢板,
4、光伏阵列组件,41、光伏系统控制器,42、蓄电池组,43、并网逆变器,44、切换控制器,45、轨道亮化系统,46、外电网系统,47、薄膜光伏阵列组件
5、口字钢轨道,52、口字钢轨顶板,53、口字钢轨侧板,54、口字钢轨轨道板,55、l筋板,
6、y型墩柱,61、y型槽,62、墩柱身,63、墩柱法兰,64、墩基螺栓,65、墩基,6a、t型墩柱,61a、墩柱身a
7、救生通道网,71矩形边框,72、中部轴,73、钢筋混凝土槽
具体实施方式
以下实施例是对本发明的进一步说明,但本发明并不局限于此。因本发明比较复杂,因此实施方式仅对本发明的发明点部分进行详述,本发明未详述部分均可采用现有技术。
实施例1:
工字复合轨道梁,由箱梁2和工字轨道3复合而成。箱梁2通过钢筋21和剪力板21a焊接在工字轨道3的工字钢上翼板36的上表面、并用混凝土浇注复合成一个固定整体结构的工字复合轨道梁,所述剪力板21a主要是提高热胀冷缩抗剪能力和安全可靠性。其突出优点是充分将钢筋混凝土结构的箱梁2的刚性和纯钢结构的工字轨道3的刚度+柔韧性有机结合在一起,一是使钢筋混凝土结构的箱梁2结构优化到最合理刚度和总重量最轻,二是使纯钢结构的工字轨道3结构优化到刚度和柔韧性最合理,二者复合后的刚度、强度、柔韧性达到最优,且有足够高承载物流车客运车动态冲击载荷和风载、热胀冷缩应力、太阳能新能源系统载荷等的能力。如图1、图2和图3所示。所述钢筋21和剪力板21a的数量由本领域技术人员根据载荷要求和计算结果进行设计。
剪力板21a选自普通钢板,钢板上冲有多个孔以增强与混凝土的结合力。
所述箱梁2通过其预埋螺柱23和螺帽24把工字钢上翼板36固定在箱梁2的下方,复合成可拆卸结构的工字复合轨道梁。或所述箱梁2通过其预埋螺柱23和螺帽24、以及钢筋21和剪力板21a焊接在工字钢上翼板36上表面,两种复合方式共用使工字钢上翼板36与箱梁2连接更加牢固,进一步提高热胀冷缩抗剪能力和安全可靠性。所述钢筋21和剪力板21a的数量由本领域技术人员根据载荷要求和计算结果进行设计。
所述箱梁2包括钢筋21、箱梁减重孔22。
所述箱梁2为空心梁,由本领域技术人员根据实际需求和计算结果确定。
所述箱梁2是矩形。如图1和图3所示。刚性的箱梁2和刚柔相济的工字轨道3的复合大幅度提高了轨道梁整体的刚度、强度、抗动态载荷冲击和抗震抗强风的稳定性、安全性,车辆在工字钢轨道上运行更加平稳,且综合重量轻、造价低。
所述工字轨道3由工字钢轨31、加强筋板32、隔音防护罩33、耐磨钢板39组成。工字钢轨31包括相互平行的工字钢上翼板36、工字钢下翼板37、以及垂直于工字钢上翼板36和工字钢下翼板37分别与工字钢上翼板36和工字钢下翼板37的中部连接的腹板38,如图1所示。所述工字钢轨31由热轧生产。
实施例2
其他同实施例1,不同之处在于:
所述箱梁2包括钢筋21、箱梁减重孔22,所述箱梁2为实心梁。
所述箱梁2是台形。如图1和图3所示。
所述工字轨道3由工字钢轨31、加强筋板32、隔音防护罩33、耐磨钢板39组成。工字钢轨31包括相互平行的工字钢上翼板36、工字钢下翼板37、以及垂直于工字钢上翼板36和工字钢下翼板37分别与工字钢上翼板36和工字钢下翼板37的中部连接的腹板38,如图1所示。所述工字钢轨31由焊接生产。
在工字钢下翼板37的上表面两侧安装有耐磨钢板39,耐磨板39提高工字钢轨31的使用寿命,耐磨板39可宽于工字钢下翼板37,增加在其上运行的动力车轮的宽度、提高运载能力和驱动摩擦力;在工字钢下翼板37的底部焊接有加强筋板32,加强筋板32每间隔0.3米焊接一个。
实施例3
其他同实施例2,不同之处在于:
所述箱梁2包括钢筋21、箱梁减重孔22,所述左右两个箱梁2之间,由60个或更多个横梁25相连接,以增强梁整体结构的刚性和稳定性。所述箱梁2为空心梁。所述横梁25为由碳纤维复合材料制造而成的空心横梁。
所述箱梁2和空心横梁25是圆形、椭圆形、曲线形或其它外观结构形状,由本领域技术人员进行设计和制造。如图1和图3所示。刚性的箱梁2和刚柔相济的工字轨道3的复合大幅度提高了轨道梁整体的刚度、强度、抗动态载荷冲击和抗震抗强风的稳定性、安全性,车辆在工字钢轨道上运行更加平稳,且综合重量轻、造价低。
所述工字轨道3由工字钢轨31、加强筋板32、隔音防护罩33、耐磨钢板39组成。工字钢轨31包括相互平行的工字钢上翼板36、工字钢下翼板37、以及垂直于工字钢上翼板36和工字钢下翼板37分别与工字钢上翼板36和工字钢下翼板37的中部连接的腹板38,如图1所示。所述工字钢轨31由热轧或焊接生产。在工字钢下翼板37的上表面两侧安装有耐磨钢板39,耐磨板39提高工字钢轨31的使用寿命,耐磨板39可宽于工字钢下翼板37,增加在其上运行的动力车轮的宽度、提高运载能力和驱动摩擦力;在工字钢下翼板37的底部焊接有加强筋板32,加强筋板32每间隔3米焊接一个;工字钢上翼板36的两边用螺栓35安装有左右镜像对称的隔音防护罩33和防护罩支撑板34,防护罩支撑板34焊接在隔音防护罩33的上部,以增强隔音防护罩33的结构强度,优选的防护罩支撑板34每间隔3米焊接一个。所述隔音防护罩33采用泡沫铝复合材料材料制造,如图1和图3所示。
实施例4
其他同实施例3,不同之处在于:
所述箱梁2和空心横梁25是椭圆形或曲线形。
加强筋板32每间隔5米焊接一个;工字钢上翼板36的两边用螺栓35安装有左右镜像对称的隔音防护罩33和防护罩支撑板34,防护罩支撑板34焊接在隔音防护罩33的上部,以增强隔音防护罩33的结构强度,防护罩支撑板34每间隔1米焊接一个。所述隔音防护罩33采用玻纤或碳纤维复合材料。
实施例5
口字复合轨道梁,由箱梁2和口字钢轨道5上下复合而成,箱梁2通过钢筋21和剪力板21a焊接在口字钢轨顶板52上表面、并用混凝土浇注成一个固定整体结构的口字复合轨道梁。所述剪力板21a主要是提高热胀冷缩抗剪能力和安全可靠性,其突出优点是充分将钢筋混凝土结构的箱梁2的刚性和纯钢结构的口字钢轨道5的刚度+柔韧性有机结合在一起,一是使钢筋混凝土结构的箱梁2结构优化到最合理刚度和总重量最轻,二是使纯钢结构的口字钢轨道5结构优化到刚度和柔韧性最合理,二者复合后的刚度、强度、柔韧性达到最优,且有足够高承载物流车客运车动态冲击载荷和风载、热胀冷缩应力、太阳能新能源系统载荷等的能力。如图1、图2和图4所示。所述钢筋21和剪力板21a的数量由本领域技术人员根据载荷要求和计算结果进行设计。
所述箱梁2通过其预埋螺柱23和螺帽24把口字钢轨顶板52固定在箱梁2的下方,组成可拆卸结构的口字复合轨道梁。或所述箱梁2通过其预埋螺柱23和螺帽24、以及钢筋21和剪力板21a焊接在口字钢轨顶板52上表面,两种连接方式使口字钢轨顶板52与箱梁(2)连接更加牢固。刚性的箱梁2和刚柔相济的口字钢轨道5的复合大幅度提高了轨道梁整体的刚度、强度、抗动态载荷冲击和抗震抗强风的稳定性、安全性,车辆在工字钢轨道上运行更加平稳,且综合重量轻、造价低。
所述口字钢轨道5由口字钢轨顶板52、口字钢轨侧板53、口字钢轨轨道板54、l筋板55组成。口字钢轨顶板52两侧各焊接一口字钢轨侧板53,左右口字钢轨侧板53在同一竖直截面向上相互平行且口字钢轨侧板53底部各焊接一水平的口字钢轨轨道板54。如图1和图4所示。
左右口字钢轨轨道板54与口字钢轨顶板52平行且处于同一横截面上;左右口字钢轨轨道板54长度相等,左右口字钢轨轨道板54的总长度为口字钢轨顶板52长度的1/6。
箱梁2两头分别与两个盖梁左翼11或两个盖梁右翼12由钢筋连接、并用混凝土浇注成一个整体结构。
实施例6
其他同实施例5,不同之处在于:
所述口字钢轨道5由口字钢轨顶板52、口字钢轨侧板53、口字钢轨轨道板54、l筋板55组成。口字钢轨顶板52两侧各焊接一口字钢轨侧板53,左右口字钢轨侧板53在同一竖直截面向上相互平行且口字钢轨侧板53底部各焊接一水平的口字钢轨轨道板54,l筋板55焊接在左右口字钢轨侧板53下部外侧和口字钢轨轨道板54的底面,以加强其强度和稳定性。如图1和图4所示。
左右口字钢轨轨道板54与口字钢轨顶板52平行且处于同一横截面上;左右口字钢轨轨道板54长度相等,左右口字钢轨轨道板54的总长度为口字钢轨顶板52长度的1/4。
实施例7
其他同实施例5,不同之处在于:
左右口字钢轨轨道板54与口字钢轨顶板52平行且处于同一横截面上;左右口字钢轨轨道板54长度相等,左右口字钢轨轨道板54的总长度为口字钢轨顶板52长度的1/10。
箱梁2通过悬挂机构悬挂于盖梁左翼11或盖梁右翼12上。
实施例8
复合轨道梁,由第一复合轨道梁、第二复合轨道梁、盖梁1、横梁25组成。所述盖梁1由盖梁左翼11、盖梁右翼12、盖梁基座13组成,盖梁1的上部包括盖梁左翼11和盖梁右翼12、底部是盖梁基座13用钢筋混凝土浇注成一个整体结构。如图1和图2所示。盖梁基座13安装在墩柱上。前后各一个盖梁1,前后盖梁左翼11分别与第一复合轨道梁的两端连为一体,前后盖梁右翼12分别与第二复合轨道梁的两端连为一体;第一复合轨道梁和第二复合轨道梁的两个箱梁2之间由5、10、20、30、40、50、60个或更多个横梁25横向相联接,进一步增强梁整体结构的刚性和稳定性。如图1、图2所示。
第一复合轨道梁和第二复合轨道梁可以相同也可以不同。第一复合轨道梁和第二复合轨道梁分别选自实施例1-7任意一种的工字复合轨道梁和/或口字复合轨道梁。
所述横梁25可由钢筋混凝土结构材料、玻璃纤维或碳纤维复合材料、镁铝合金或其他轻质结构材料制造而成,根据需要也可制造成实心横梁或空心横梁。当制成空心横梁时,所述空心横梁25是矩形、台形、圆形、椭圆形、曲线形或其它外观结构形状。
实施例9
其他同实施例7,不同之处在于:
所述盖梁1还包括减重孔14,减重孔14位于盖梁1的中部,减重孔14为1个或多个,减重孔14的设置是为了减轻盖梁1的重量,其数量和大小可以由本领域技术人员根据实际结构设计需要而设置。如图1、图2所示。
实施例10
其他同实施例7,不同之处在于:
所述上述复合轨道梁的第一复合轨道梁、第二复合轨道梁与盖梁1的连接方式由悬挂替代钢筋混凝土浇注连接方式,所述盖梁1与y型墩柱6由t型墩柱6a替代。所述t型墩柱6a由盖梁1a、盖梁左翼11a、盖梁右翼12a、墩柱身61a、墩柱法兰63、墩基65组成。墩柱身a61a的顶部是由盖梁1a和盖梁左翼11a、盖梁右翼12a组成的盖梁,墩柱身61a的底部是墩柱法兰63,用钢筋混凝土浇注成一个整体,墩柱身61a通过墩柱法兰63安装于墩基65上。所述第一复合轨道梁、第二复合轨道梁分别悬挂在盖梁左翼11a、盖梁右翼12a端部的下面。
实施例11
一种双制式新能源复合轨道系统,由复合轨道梁、墩柱、安全救生通道和新能源光伏系统组成。墩柱安装在城市道路绿化带上或高速路两侧的边坡上、每间隔10~120米一根沿道路延伸,每一榀复合轨道梁安装在前后两个墩柱上,复合轨道梁的长度与墩柱的间隔相对应;多榀复合轨道梁依次安装在多个墩柱上,组成连续延伸的复合轨道系统,无人驾驶新能源物流车或客运车在复合轨道系统内安全高效运行。安全救生通道和新能源光伏系统安装于复合轨道梁上表面。如图1、图2和图6所示。
复合轨道梁可以采用上述实施例8-9任何一种。
所述墩柱为y型墩柱6所述y型墩柱6由y型槽61、墩柱身62、墩柱法兰63、墩基65组成。墩柱身62的顶部是y型槽61、墩柱身62的底部是墩柱法兰63用钢筋混凝土浇注成一个整体,墩柱身62通过墩柱法兰63安装于墩基65上;墩基65深埋在地下,墩基65上部预埋墩基螺栓64,墩柱法兰63与墩基螺栓64连结。所述每个y型槽61内承载着前后两榀复合轨道梁系统主体的两个盖梁基座14,即前后两榀复合轨道梁系统主体在y型墩柱6的y型槽61内对接,多榀复合轨道梁系统主体依次连接共同组成一条连续完整交通轨道。所述墩柱身62的横截面是矩形、方形、圆型、椭圆型或其他结构造型,下粗上细的台状结构,墩柱身62高30米、外表面与地面成90度~105度角。柱身62的中心线与地面垂直。
所述安全救生通道由救生通道网7、钢筋混凝土槽73组成。所述钢筋混凝土槽73是被预制在盖梁1、箱梁2和空心横梁25的上缘部,围成的一个矩形槽,以安装救生通道网7,如图2、图5和图7所示。救生通道网7是沿中部轴72可向上折叠的矩形框状结构,救生通道网7的矩形边框71扣在钢筋混凝土槽73内,当发生紧急情况时,用客车上的救生梯子向上顶开救生通道网7的一侧,使救生通道网7沿着中部轴71向上折翻过去,打开了一个救生天窗,救生梯挂在钢筋混凝土槽73内,乘客由救生梯快速爬上救生通道网7进行撤离,如图6、图7和图8所示。优选的,所述救生通道网7是由碳纤维加强的复合材料制成,结构强度高,每平米重量小于5公斤,每平米可承载重量大于300公斤。优选的,所述安全救生通道是主动救生通道,每辆车可配备4-10个救生梯,每批4-10人连续主动救生。
所述新能源光伏系统由光伏阵列组件4、光伏系统控制器41、蓄电池组42、并网逆变器43、切换控制器44、轨道亮化系统45、外电网系统46、薄膜光伏阵列组件47组成。光伏阵列组件4安装在箱梁2的上表面,光伏系统控制器41、蓄电池组42、并网逆变器43和切换控制器44分别安装在盖梁1上表面或盖梁减重孔13的空间内,薄膜光伏阵列组件47在每一个救生通道网7的中部轴72的两侧各安装一片,薄膜光伏阵列组件47与光伏阵列组件4并联,不影响救生通道网7沿中部轴72向上的折叠功能,轨道亮化系统45安装在箱梁2的侧面和救生通道网7的边部,以新颖的交通轨道替代了城市的路灯,城市电线通讯线全部布置在轨道上方,亮化美化城市,还能承接公益广告和商业广告,夜间新能源储电装置能持续为救生通道照明、为城市道路照明。
光伏阵列组件4、光伏系统控制器41、蓄电池组42、并网逆变器43、切换控制器44、轨道亮化系统45、外电网系统46均采用现有技术。刚性复合轨道梁具备了较高的整体刚度、强度和韧性,且具有了足够的承载光伏阵列组件4重量的能力和光伏发电的能力。薄膜光伏阵列组件47与光伏阵列组件4并联发的电送往光伏系统控制器41,再由光伏系统控制器41送往蓄电池组42和并网逆变器43,并网逆变器43输出电源为交流220v或110v送往切换控制器44,由切换控制器44送往轨道亮化系统45和轨道供电线路,外电网系统46通过切换控制器44并网。常规运行白天以新能源供应电力为主、外电网系统46为辅助,晚上以外电网系统46供电为主、新能源电网蓄电池组42储备的电量作备用。光伏新能源电力以轨道照明亮化、公益广告、替代路灯照明为主。当特殊情况下外电网系统46突然全部停电,光伏新能源电力通过切换控制器44自动为轨道交通车辆供电,保证交通车辆安全到达下一个车站、确保承客安全撤离。光伏供电量可达到轨道交通用电的40%~50%,节能效果显著。如图6所示。
实施例12
其他同实施例11,不同之处在于:
墩柱为通用的“i”型墩柱;墩柱身62高15米、外表面与地面成90度~105度角。柱身62的中心线与地面垂直。
实施例13
其他同实施例11,不同之处在于:
复合轨道梁可以采用上述实施例10中的一种。所述墩柱身61a是矩形、方形、圆型、椭圆型或其他结构造型,下粗上细的台状结构,墩柱身61a高1~30米,如墩柱身61a稿10米、15米、20米、25米、30米或其他高度。墩柱身61a的中心线与地面垂直,外表面与地面成90度~105度角。
起点商标作为专业知识产权交易平台,可以帮助大家解决很多问题,如果大家想要了解更多知产交易信息请点击 【在线咨询】或添加微信 【19522093243】与客服一对一沟通,为大家解决相关问题。
此文章来源于网络,如有侵权,请联系删除


