一种巨型空间弯扭桥拱脚及其制作方法与流程



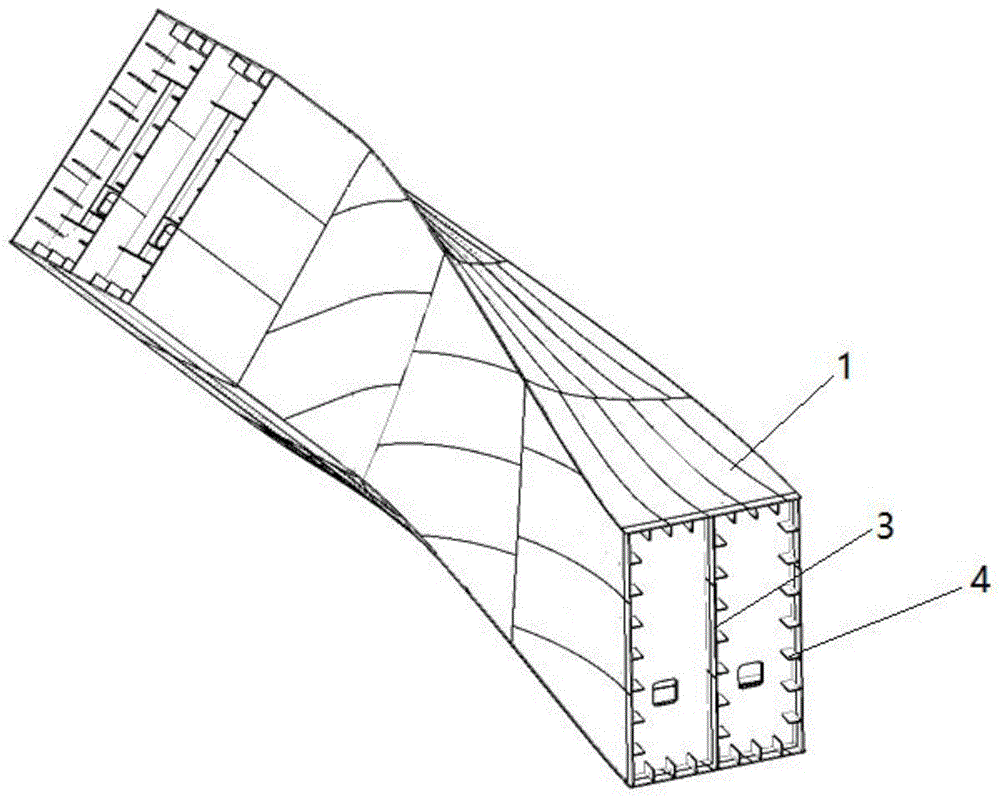
本发明属于钢结构建筑技术领域,特别涉及一种巨型空间弯扭桥拱脚及其制作方法。
背景技术:
随着社会经济的快速发展,各行各业都在不断。建筑行业也是如此,从传统的缓凝土发展至当今盛行的钢结构建筑。钢结构建筑以其施工快、稳定性好以及能够满足建筑的异形需要而受到建筑行业以及开发商的追捧。
现有的钢结构建筑中,常规的拱脚大多都是常规的矩形拱脚,其很难满足建筑桥梁的异形需求,为了更好的满足建筑施工的需要,我们需要不断的钢结构进行改进,且现有的拱脚大多都是在现场进行整体制作,这不仅会给施工带来诸多的问题,同时还会因为尺寸太大给施工带来诸多不便。
技术实现要素:
发明目的:为了克服以上不足,本发明的目的是提供一种巨型空间弯扭桥拱脚,其制作方法简单,通过分段拼装后再进行组装,便于搬运和施工,给施工带来诸多便利;同时通过特殊的制造工艺将拱脚制成弯扭桥拱脚,让其能够更好的满足施工的需要。
技术方案:为了实现上述目的,本发明提供了一种巨型空间弯扭桥拱脚的制作方法,包括:具体的制作方法如下:1):首先对拱脚进行分段,并对各个分段分别进行加工;
2):先对壁板进行定位;
3):对一侧隔板进行定位;
4):对中腹板进行定位;
5):对中腹板另一侧的隔板进行定位;
6):对位于隔板两端的壁板进行定位;
7):最后对最后一块壁板进行定位;
8):最后对各分段紧张整体定位组装。
本发明中所述壁板弯扭加工制作方法如下:1):对根据壁板的需求尺寸对构件进行合理的拆分;
2):先将按实体放样并切割好的壁板进行弯扭加工成形,即通过大型卷板机上斜向滚压成形,滚压成形过程需反复多次,并在加工过程中采用样板进行检测,并通过大型油压机对壁两端进行压制,壁板滚压成形;
3):实体样箱制作:即先在样台上划出弯扭构件四块壁板1:1的展开投影图以及横隔板位置线,由木工按样台上的线型,用木材制作壁板的实际展开样板,并按样台线型组装样,箱组装好后,将横隔板位置线驳到样箱壁板的外侧,并作好记号,同时在壁板外侧弹出壁板两端的企口位置线;
4):壁板加工成形后的检测即:壁板加工成形后,采用实体样箱进行检测;
5):弯扭板单元组装胎架制作,扭板单元组装胎架采用可移动式平台,即胎架底面为一块独立的钢平台,胎架在钢平台上设置,壁板单元组装后连同平台胎架一起吊入焊接工位进行焊接,焊接后胎架再重复转入组装工位进行胎架组装,以便保证流水作业;弯扭板单元组装胎架设置前,应先在平台上根据棱线空间坐标划出壁板作为胎架组装基准面的投影位置线以及横隔板位置线、胎架模板位置线,然后设立胎架模板,模板上口标高尺寸应进行精密控制;
6):壁板定位划线,即将加工成形好的壁板吊入胎架进行定位,当板单元较宽时,定位后先进行壁板拼接纵缝的焊接,壁板定位时必须与胎架密贴,同时定对端面企口位置线和平台上相关定位线形要求,并与胎架定位固定,然后在壁板上划出纵向加劲肋的组装位置线,并检查;
7):壁板纵向加劲肋组装,按壁板上所划出的安装位置线,组装纵向加劲肋,纵向加劲肋组装时严格按划出的安装位置线定位组装,组装采用无码装配,并注意与壁板间的组装间隙以及与壁板间的相对位置,然后定位焊接,并提交检查;
8):壁板与纵向加劲肋焊接,壁板单元组装好后,将板单元连同组装平台一起吊入焊接工位,进行纵向加劲肋的焊接,焊接采用co2气保护焊焊接;
9):壁板单元校正检测,壁板焊接后,需进行焊接变形的校正,将固定壁板的限位全部拆除,在自由状态下进行测量并用火焰进行局部校正,板单元校正后,直接在胎架上进行检测,主要检查壁板与胎架是否密贴以及壁板的局部不平度和壁板扭曲度,壁板单元检测。
本发明中步骤1中对构件进行合理的拆分的具体方法如下:长度方向根据吊装起重能力拆分中若干分段;
板宽方向根据油压机和卷板机进料尺寸限制进行拆分;
拆分出的拼板缝尽量与卷板机进料方向正交。
本发明中步骤4)中壁板加工成形后的检测具体方式如下:
检测壁板加工后的线型是否正确,将加工好的壁板吊入实体样箱上,定对相对位置,检查壁板和样箱之间是否密贴,其间隙不得大于1mm,否则再次用卷板机或油压机进行校正。
本发明中所述的拱脚包括一组壁板、一组隔板和腹板,所述壁板中设有第一壁板、第二壁板、第三壁板和第四壁板,所述第一壁板和第四壁板相对设置,所述第二壁板和第三壁板相对设置,所述腹板设于第二壁板和第三壁板之间,所述隔板设于腹板的两侧。
本发明中所述壁板中设有壁板本体,所述壁板本体以及腹板的内一侧均设有一组加劲板。
本发明中所述隔板的两端呈锯齿状,其与壁板上的加劲板相咬合。
本发明中所述隔板中设有隔板本体,所述隔板本体上设有一组加强板和开口。
进一步的所述胎架中设有一组立柱和横向安装板,所述立柱呈一列设置,所述横向安装板设于立柱上。
更进一步的,所述胎架在正x轴方向每列胎架高度自原点向右依次增加,y轴方向每列胎架中的立柱的高度自y轴向原点方向逐渐增加,负x轴方向上每列胎架高度自原点向左依次减小,y轴方向每列胎架中立柱的高度自y轴向原点方向逐渐减小。
上述技术方案可以看出,本发明具有如下有益效果:
1、本发明中所述的一种巨型空间弯扭桥拱脚的制作方法,其制作方法简单,通过分段拼装后再进行组装,便于搬运和施工,给施工带来诸多便利;同时通过特殊的制造工艺将拱脚制成弯扭桥拱脚,让其能够更好的满足施工的需要。
2、本发明中所述的一种巨型空间弯扭桥拱脚,其结构简单,设计合理,通过弯扭状壁板的设置,让整个拱脚实现弯扭,从而让其更好的满足异形桥梁施工的需要。
附图说明
图1为本发明所述的巨型空间弯扭桥拱脚的结构示意图;
图2为本发明腹板和隔板的安装示意图;
图3为本发明中胎架的结构示意图。
具体实施方式
下面结合附图和具体实施例,进一步阐明本发明。
实施例
下面详细描述本发明的实施例,所述实施例的示例在附图中示出,其中自始至终相同或类似的标号表示相同或类似的元件或具有相同或类似功能的元件。下面通过参考附图描述的实施例是示例性的,旨在用于解释本发明,而不能理解为对本发明的限制。
在本发明的描述中,需要理解的是,术语“中心”、“纵向”、“横向”、“长度”、“宽度”、“厚度”、“上”、“下”、“前”、“后”、“左”、“右”、“竖直”、“水平”、“顶”、“底”“内”、“顺时针”、“逆时针”等指示的方位或位置关系为基于附图所示的方位或位置关系,仅是为了便于描述本发明和简化描述,而不是指示或暗示所指的装置或元件必须具有特定的方位、以特定的方位构造和操作,因此不能理解为对本发明的限制。
此外,术语“第一”、“第二”仅用于描述目的,而不能理解为指示或暗示相对重要性或者隐含指明所指示的技术特征的数量。由此,限定有“第一”、“第二”的特征可以明示或者隐含地包括一个或者更多个该特征。在本发明的描述中,除非另有说明,“多个”的含义是两个或两个以上,除非另有明确的限定。
在本发明中,除非另有明确的规定和限定,术语“安装”、“相连”、“连接”、“固定”等术语应做广义理解,例如,可以是固定连接,也可以是可拆卸连接,或一体地连接;可以是机械连接,也可以是电连接;可以是直接相连,也可以通过中间媒介间接相连,可以是两个元件内部的连通。对于本领域的普通技术人员而言,可以根据具体情况理解上述术语在本发明中的具体含义。
在本发明中,除非另有明确的规定和限定,第一特征在第二特征之“上”或之“下”可以包括第一和第二特征直接接触,也可以包括第一和第二特征不是直接接触而是通过它们之间的另外的特征接触。而且,第一特征在第二特征“之上”、“上方”和“上面”包括第一特征在第二特征正上方和斜上方,或仅仅表示第一特征水平高度高于第二特征。第一特征在第二特征“之下”、“下方”和“下面”包括第一特征在第二特征正下方和斜下方,或仅仅表示第一特征水平高度小于第二特征。
本实施例中所述的一种巨型空间弯扭桥拱脚的制作方法,包括:具体的制作方法如下:1):首先对拱脚进行分段,并对各个分段分别进行加工;
2):先对壁板进行定位;
3):对一侧隔板进行定位;
4):对中腹板进行定位;
5):对中腹板另一侧的隔板进行定位;
6):对位于隔板两端的壁板进行定位;
7):最后对最后一块壁板进行定位;
8):最后对各分段紧张整体定位组装。
本实施例中所述壁板弯扭加工制作方法如下:1):对根据壁板的需求尺寸对构件进行合理的拆分;
2):先将按实体放样并切割好的壁板进行弯扭加工成形,即通过大型卷板机上斜向滚压成形,滚压成形过程需反复多次,并在加工过程中采用样板进行检测,并通过大型油压机对壁两端进行压制,壁板滚压成形;
3):实体样箱制作:即先在样台上划出弯扭构件四块壁板1:1的展开投影图以及横隔板位置线,由木工按样台上的线型,用木材制作壁板的实际展开样板,并按样台线型组装样,箱组装好后,将横隔板位置线驳到样箱壁板的外侧,并作好记号,同时在壁板外侧弹出壁板两端的企口位置线;
4):壁板加工成形后的检测即:壁板加工成形后,采用实体样箱进行检测;
5):弯扭板单元组装胎架制作,扭板单元组装胎架采用可移动式平台,即胎架底面为一块独立的钢平台,胎架在钢平台上设置,壁板单元组装后连同平台胎架一起吊入焊接工位进行焊接,焊接后胎架再重复转入组装工位进行胎架组装,以便保证流水作业;弯扭板单元组装胎架设置前,应先在平台上根据棱线空间坐标划出壁板作为胎架组装基准面的投影位置线以及横隔板位置线、胎架模板位置线,然后设立胎架模板,模板上口标高尺寸应进行精密控制;
6):壁板定位划线,即将加工成形好的壁板吊入胎架进行定位,当板单元较宽时,定位后先进行壁板拼接纵缝的焊接,壁板定位时必须与胎架密贴,同时定对端面企口位置线和平台上相关定位线形要求,并与胎架定位固定,然后在壁板上划出纵向加劲肋的组装位置线,并检查;
7):壁板纵向加劲肋组装,按壁板上所划出的安装位置线,组装纵向加劲肋,纵向加劲肋组装时严格按划出的安装位置线定位组装,组装采用无码装配,并注意与壁板间的组装间隙以及与壁板间的相对位置,然后定位焊接,并提交检查;
8):壁板与纵向加劲肋焊接,壁板单元组装好后,将板单元连同组装平台一起吊入焊接工位,进行纵向加劲肋的焊接,焊接采用co2气保护焊焊接;
9):壁板单元校正检测,壁板焊接后,需进行焊接变形的校正,将固定壁板的限位全部拆除,在自由状态下进行测量并用火焰进行局部校正,板单元校正后,直接在胎架上进行检测,主要检查壁板与胎架是否密贴以及壁板的局部不平度和壁板扭曲度,壁板单元检测。
本实施例中所述壁板弯扭加工制作方法的步骤1中对构件进行合理的拆分的具体方法如下:长度方向根据吊装起重能力拆分中若干分段;
板宽方向根据油压机和卷板机进料尺寸限制进行拆分;
拆分出的拼板缝尽量与卷板机进料方向正交。
本实施例中所述壁板弯扭加工制作方法的步骤4)中壁板加工成形后的检测具体方式如下:
检测壁板加工后的线型是否正确,将加工好的壁板吊入实体样箱上,定对相对位置,检查壁板和样箱之间是否密贴,其间隙不得大于1mm,否则再次用卷板机或油压机进行校正。
本实施例中所述的拱脚包括一组壁板1、一组隔板2和腹板3,所述壁板1中设有第一壁板、第二壁板、第三壁板和第四壁板,所述第一壁板和第四壁板相对设置,所述第二壁板和第三壁板相对设置,所述腹板3设于第二壁板和第三壁板之间,所述隔板2设于腹板3的两侧。
本实施例中所述壁板1中设有壁板本体,所述壁板本体以及腹板3的内一侧均设有一组加劲板4。
本实施例中所述隔板2的两端呈锯齿状,其与壁板1上的加劲板4相咬合。
本实施例中所述隔板2中设有隔板本体,所述隔板本体上设有一组加强板和开口。
本实施例中所述胎架中设有一组立柱和横向安装板,所述立柱呈一列设置,所述横向安装板设于立柱上。
本实施例中所述胎架在正x轴方向每列胎架高度自原点向右依次增加,y轴方向每列胎架中的立柱的高度自y轴向原点方向逐渐增加,负x轴方向上每列胎架高度自原点向左依次减小,y轴方向每列胎架中立柱的高度自y轴向原点方向逐渐减小。
以上所述仅是本发明的优选实施方式,应当指出,对于本技术领域的普通技术人员来说,在不脱离本发明原理的前提下,还可以做出若干改进,这些改进也应视为本发明的保护范围。
起点商标作为专业知识产权交易平台,可以帮助大家解决很多问题,如果大家想要了解更多知产交易信息请点击 【在线咨询】或添加微信 【19522093243】与客服一对一沟通,为大家解决相关问题。
此文章来源于网络,如有侵权,请联系删除


