一种直埋扣件的制作方法



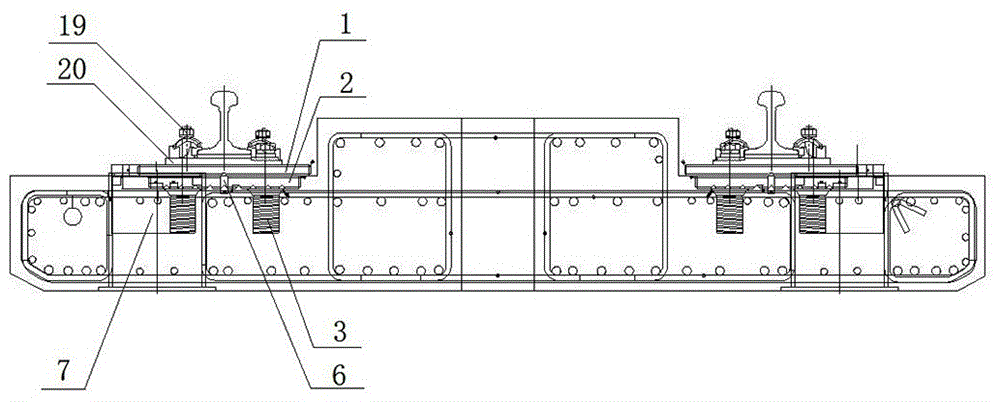
本实用新型涉及轨道施工的技术领域,尤其是一种直埋扣件。
背景技术:
现有的直埋扣件主要存在以下问题:1、由于轨下结构现场浇筑,浇筑过程中尼龙套管容易发生歪斜;2、采用架轨法施工,容易将扣件本体浇筑于轨下结构中,从而影响后续养护维修;3、小半径曲线地段坑横向力能力不足,在较大横向力作用下容易造成尼龙套管的破环,从而导致扣件系统的失效。
技术实现要素:
本实用新型的目的是根据上述现有技术的不足,提供了一种直埋扣件,将尼龙套管与垫板一体制造成型,提高了其整体性,使尼龙套管更容易精准定位,同时也增加了尼龙套管强度与抗拔力。
本实用新型目的实现由以下技术方案完成:
一种直埋扣件,安装于轨道的道床上,其特征在于:包括垫板和支柱,所述垫板包括上板体和下板体,所述下板体的尺寸小于所述上板体的尺寸,所述上板体、所述下板体和所述支柱为一体化连接,所述上板体底部连接有所述下板体,所述下板体底部连接有两对位设置的所述支柱。
所述支柱外部设有外螺纹,所述上板体顶部开设有两内螺纹孔,所述内螺纹孔经所述上板体和所述下板体延伸至所述支柱内部。
所述下板体底部沿其横纵方向上设有若干均匀布置的凸台,所述凸台间形成若干横纵交错的凹槽,所述上板体与所述下板体的连接处边缘中部设有两对称布置的排出口。
两所述支柱分别安装于所述道床的两支柱安装孔内,所述支柱安装孔的深度和直径均满足于所述支柱的安装要求,所述下板体安装于所述道床的下板体安装槽内,所述下板体安装槽的长度、宽度和高度均满足于所述下板体的安装要求。
一种涉及上述的直埋扣件的施工方法,其特征在于:所述的施工方法包括如下步骤:
a、在直埋扣件的安装处开凿下板体安装槽;
b、待下板体安装槽开凿完成后,在下板体安装槽内开凿支柱安装孔;
c、待支柱安装孔开凿完成后,将速干水泥或胶黏剂倒入下板体安装槽内,速干水泥或胶黏剂会顺着下板体安装槽进入支柱安装孔内;
d、将直埋扣件压入下板体安装槽内,使支柱安装于支柱安装孔内,下板体安装于下板体安装槽,直至直埋扣件的上板体底面与道床顶面接触结合。
本实用新型的优点是:
1、由于下板体的尺寸小于上板体的尺寸,可以通过往道床的下板体安装槽内注入速干水泥或胶黏剂,可将两支柱可分别安装于道床的两支柱安装孔内,下板体安装于道床的下板体安装槽内,此时的上板体底面与道床顶面接触,下板体和支柱起到了定位的作用,可以使上板体放置在道床的指定位置,减少了上板体的安装误差,进而减少了上板体上部的钢轨的安装误差,即增加了钢轨的安装精度,减少了钢轨安装及线型调整所需的时间;
2、上板体、下板体和支柱三者为一体化连接设计,省去预埋套管与轨枕的配合,提高了本扣件的整体性,减少了三者间的安装误差,进而提高了上板体的安装精度,同时使支柱和下板体更容易精准定位,也增加了支柱和下板体的强度与抗拔力;
3、凸台及其形成的凹槽,能够有效增加直埋扣件与速干水泥或胶黏剂之间的接触面积,可增强扣件与轨下结构的连接,提高直埋扣件的水平横向剪切力与整体抗拉强度;
4、本扣件的上板体比凿开空间(下板体安装槽)四周大,上板体能平整地放置于道床顶面上,现场安装施工时能够有效避免扣件施工不平整、扣件凸出道床顶面的高度不统一以及扣件安装过程中正反面出错的情况发生;
5、支柱外部设有外螺纹,支柱的外螺纹能够有效增加本扣件与速干水泥或胶黏剂之间的接触面积,可增强扣件与轨下结构的连接,增加了支柱强度与抗拔力;
6、排出口的设计,可避免在轨下结构浇筑施工时将扣件埋覆;
7、本扣件采用玻纤增强聚酰胺66材料,其材料已在预埋套管中应用广泛,具有寿命长,强度高等优点。
附图说明
图1为本实用新型的安装结构示意图;
图2为本实用新型的俯视图;
图3为本实用新型的仰视图;
图4为现有直埋扣件的安装示意图。
具体实施方式
以下结合附图通过实施例对本实用新型特征及其它相关特征作进一步详细说明,以便于同行业技术人员的理解:
如图1-4所示,图中1-21标记分别表示为:上板体1、下板体2、支柱3、内螺纹孔4、凹槽5、排出口6、道床7、t型螺栓8、螺母9、平垫圈10、弹条11、轨下垫板12、铁垫板13、铁垫板下垫板14、轨距块15、螺栓19、垫板20、凸台21。
实施例:如图4所示,现有技术中的直埋扣件由t型螺栓8、螺母9、平垫圈10、弹条11、轨下垫板12、铁垫板13、铁垫板下垫板14、轨距块15、锚固螺栓16、弹簧垫圈17、尼龙套管18构成。其中,t型螺栓8、螺母9、平垫圈10、弹条11、锚固螺栓16、弹簧垫圈17、尼龙套管18所构成的扣件系统主要用于紧扣钢轨使其固定,而轨下垫板12则用于支撑钢轨,铁垫板13、铁垫板下垫板14用于可支撑并相应调整钢轨及扣件系统的高度,而轨距块15则用于调整钢轨的位置,使两根钢轨之间的轨距满足设计需要。
如图1所示,本实施例中的直埋扣件,安装在轨道的道床上。如图1-3所示,本扣件主要包括垫板和支柱3,垫板包括上板体1和下板体2,上板体1底部连接有下板体2,下板体2底部连接有两对位设置的支柱3。如图3所示,下板体2的外轮廓尺寸小于上板体1的外轮廓尺寸,基于此在安装垫板时,通过往道床7的下板体安装槽内注入速干水泥或胶黏剂,可将两支柱3可分别安装于道床7的两支柱安装孔内,下板体2安装于道床7的下板体安装槽内,此时的上板体1的底面便可支撑在道床7的表面上,而下板体2和支柱3便起到了垫板安装时的定位作用,可以使上板体1放置在道床7的指定位置,减少了上板体1的安装误差,进而减少了上板体1上部的钢轨的安装误差,即增加了钢轨的安装精度。此外,由于本扣件的上板体1比凿开空间(下板体安装槽)四周大,上板体1能平整地放置于道床7顶面上,现场安装施工时能够有效避免扣件施工不平整、扣件凸出道床7顶面的高度不统一以及扣件安装过程中正反面出错的情况发生。
如图2和图3所示,上板体1、下板体2和支柱3三者为一体化连接设计,省去预埋套管与轨枕的配合,提高了本扣件的整体性保证了结构强度,减少了三者间的安装误差,进而提高了上板体1的安装精度,同时使支柱3和下板体2更容易精准定位,也增加了支柱3和下板体2的强度与抗拔力。
如图3所示,下板体2底部沿其横纵方向上设有若干均匀布置的凸台21,凸台21间形成若干横纵交错的凹槽5,上板体1与下板体2的连接处边缘中部设有两对称布置的排出口6。凸台21及其形成的凹槽5,能够有效增加直埋扣件与速干水泥或胶黏剂之间的接触面积,可增强扣件与轨下结构的连接,提高直埋扣件的水平横向剪切力与整体抗拉强度。此外,下板体安装槽中多余的速干水泥或胶黏剂可以从排出口6排出,可避免在轨下结构浇筑施工时将扣件埋覆,保证下板体2底部所设置的速干水泥或胶黏剂与其之间的均匀性。
如图1和图2所示,上板体1顶部开设有两内螺纹孔4,内螺纹孔4经上板体1和下板体2延伸至支柱3内部。内螺纹孔4与螺栓19配合,可将上板体1与垫板20连接在一起,用于钢轨扣件的安装;而螺栓19则经由内螺纹孔4延伸至支柱3的内部,进而提高扣件的整体性和强度。
如图1、图2和图3所示,支柱3外部设有外螺纹,支柱3的外螺纹能够有效增加本扣件与速干水泥或胶黏剂之间的接触面积,可增强扣件与轨下结构的连接,增加了支柱3强度与抗拔力。
在一些实施例中,本扣件的支座采用玻纤增强聚酰胺66材料制作,其材料已在预埋套管中应用广泛,具有寿命长,强度高等优点。
此外,结合图1、图2和图3所示,本实施例还包括一种直埋扣件的施工方法,该施工方法如下:
1)在直埋扣件的安装处开凿下板体安装槽,下板体安装槽为长方体空间,其尺寸为450*290*55mm,下板体安装槽的尺寸和形状均与下板体2的尺寸和形状相吻合适配;
2)待下板体安装槽开凿完成后,在下板体安装槽内开凿支柱安装孔,支柱安装孔为直径122mm、深190mm的洞,支柱安装孔的尺寸和形状也均与支柱3的尺寸和形状相吻合适配;
3)待支柱安装孔开凿完成后,将速干水泥或胶黏剂倒入下板体安装槽内,速干水泥或胶黏剂会顺着下板体安装槽进入支柱安装孔内;
4)将直埋扣件压入下板体安装槽内,使支柱3安装于支柱安装孔内,下板体2安装于下板体安装槽,直至直埋扣件的上板体1底面与道床7顶面接触结合;
5)在垫板的上方施作钢轨及相应的扣件系统。
虽然以上实施例已经参照附图对本实用新型目的的构思和实施例做了详细说明,但本领域普通技术人员可以认识到,在没有脱离权利要求限定范围的前提条件下,仍然可以对本实用新型作出各种改进和变换,故在此不一一赘述。
起点商标作为专业知识产权交易平台,可以帮助大家解决很多问题,如果大家想要了解更多知产交易信息请点击 【在线咨询】或添加微信 【19522093243】与客服一对一沟通,为大家解决相关问题。
此文章来源于网络,如有侵权,请联系删除


