混凝土内腔多功能施工平台的制作方法



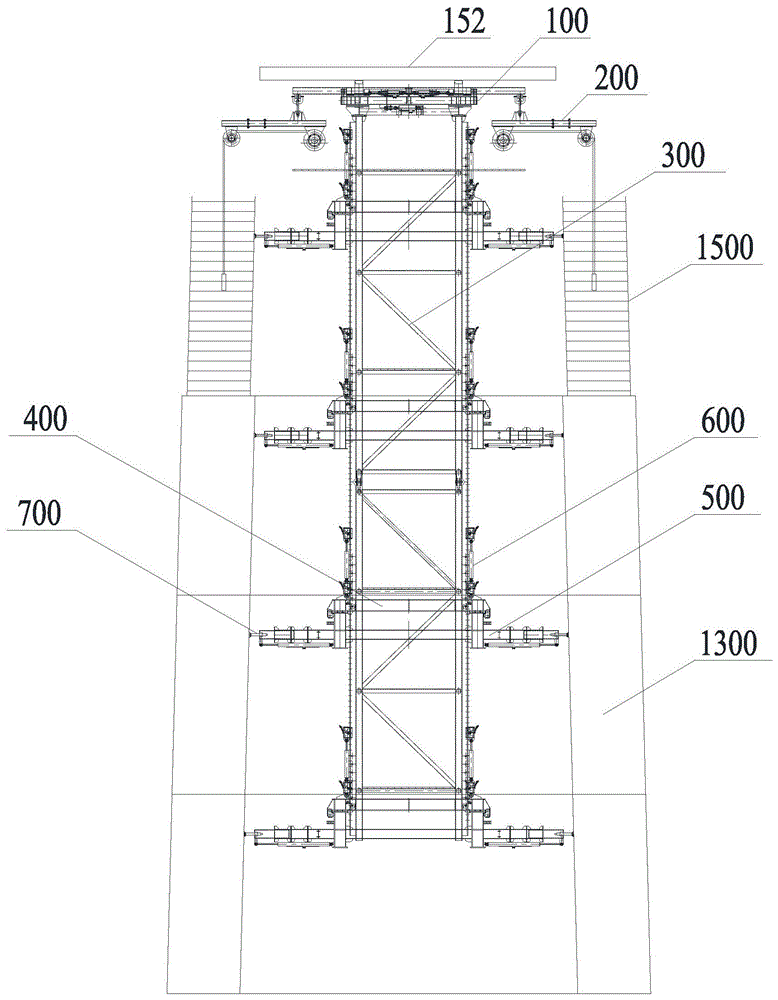
本实用新型涉及桥梁施工技术领域,具体地指一种混凝土内腔多功能施工平台。
背景技术:
在桥梁施工中,主塔外壁施工常采用液压自动爬升系统,而主塔内腔由于空间局限、施工高度高,一般采用翻模或搭设模架施工,在施工过程中不断需要塔吊辅助吊装和定位,效率较低、安全风险大,而且结构使用率低。而若将主塔内腔施工改成液压自动爬升系统,这就要求尽量克服主塔内腔空间不足的影响,设计合理的模板及其支架的爬升系统和爬升装置,以满足安全、可靠和高效的施工,此外在混凝土内腔施工中,钢筋笼以及内模的安装和定位均需用到定位装置,以前主要借助塔吊进行定位,但存在操作空间受限以及定位不精确的问题,而混凝土的浇筑过程中还不断需要振捣作业,人工高空振捣作业十分危险,且不易控制振捣的方位,振捣效果不佳。
技术实现要素:
本实用新型的目的就是要克服上述现有技术存在的不足,提供一种集内模提升、内模支架爬升、混凝土振捣和钢筋笼安装于一体,提高施工效率的混凝土内腔多功能施工平台。
为实现上述目的,本实用新型提供一种混凝土内腔多功能施工平台,其特征在于:包括位于斜塔柱内腔的内模支架,所述内模支架上端固定设有调位装置,所述调位装置下端滑动连接有振捣装置,所述内模支架外侧套设有滑移平台和承载平台;
所述滑移平台与所述内模支架滑动配合,所述内模支架外侧固定设有爬升轨道,所述滑移平台上端铰接有与所述爬升轨道交替顶推滑动的爬升装置,所述滑移平台下端与所述承载平台横向滑动连接,所述承载平台滑动连接有与斜塔柱内腔壁面可拆卸固接的横向伸缩臂。
进一步地,所述爬升装置包括爬升油缸,所述爬升油缸两端分别铰接有上爬箱和下爬箱,所述上爬箱和所述下爬箱内设有爬箱内腔,所述爬箱内腔设有凸轮,所述凸轮通过转轴与所述爬箱内腔内壁铰接,所述凸轮固定连接有拨杆,所述拨杆另一端铰接有复位弹簧,所述复位弹簧另一端与所述上爬箱和所述下爬箱铰接。
进一步地,所述爬升轨道的横截面呈工字型,其外侧面上竖向设有多个间隔设置的凹槽,所述爬箱内腔还设有与所述爬升轨道的翼缘板限位配合的限位凹槽,所述凸轮的两端呈锥形,所述凸轮一端与所述凹槽限位抵接,另一端与所述爬箱内腔内壁限位抵接。
进一步地,所述承载平台包括由横向主梁和纵向主梁拼接而成的框架,所述横向主梁设有上下两层的上腔室和下腔室,所述上腔室和所述下腔室一端开口且开口方向相反。
进一步地,所述上腔室和所述下腔室的开口端均与所述横向伸缩臂滑动套接,所述横向伸缩臂与所述横向主梁之间固定连接有横向伸缩油缸;所述纵向主梁端部滑动套接有纵向伸缩臂,所述纵向伸缩臂与所述纵向主梁之间固定连接有纵向伸缩油缸。
进一步地,还包括固定在所述斜塔柱内腔壁面上的锚固装置,所述横向伸缩臂端部螺纹连接有与所述斜塔柱内腔壁面抵接的横向顶紧螺杆,所述横向伸缩臂竖向螺纹连接有竖向支撑螺杆,所述竖向支撑螺杆支撑在所述锚固装置上;所述纵向伸缩臂的端部螺纹连接有与所述斜塔柱内腔壁面抵接的纵向顶紧螺杆。
进一步地,所述滑移平台为矩形框架结构,所述滑移平台内侧通过定位销轴与所述爬升轨道可拆卸连接,所述滑移平台内侧还固定设有与所述内模支架滚动配合的限位滚轮,所述滑移平台下端面纵向两侧边缘设有限位卡钩,所述限位卡钩与所述横向主梁的纵向两侧边缘卡接固定。
进一步地,所述内模支架包括竖向支架,所述竖向支架支架通过横向支架固定连接,所述竖向支架与所述横向支架之间还固定连接有斜向支架,所述爬升轨道竖直固定在所述竖向支架的纵向两侧。
进一步地,所述调位装置包括底座,所述底座上分层设有纵移层、横移层、旋转层、和竖向顶升层,所述纵移层相对其下一层纵向滑动配合,所述横移层相对其下一层横向滑动配合,所述旋转层相对其下一层转动配合,所述竖向顶升层相对其下一层竖向移动配合。
进一步地,所述底座包括呈矩形的底座框架,所述底座框架上端分别固定设有纵移下滑板和纵移油缸下支座,所述底座框架下端固定设有底座连接座。
进一步地,所述纵移层包括呈矩形的纵移框架,所述纵移框架下端分别固定设有纵移上滑板和纵移油缸上支座,所述纵移上滑板与所述纵移下滑板滑动配合,所述纵移油缸上支座铰接有纵向布置的纵移油缸,所述纵移油缸另一端与所述纵移油缸下支座铰接;所述纵移框架上端分别固定设有横移油缸下支座和横移下滑板。
进一步地,所述横移层包括呈矩形的横移框架,所述横移框架下端分别固定设有横移上滑板和横移油缸上支座,所述横移上滑板与所述横移下滑板滑动配合,所述横移油缸上支座铰接有横向布置的横移油缸,所述横移油缸另一端与所述横移油缸下支座铰接;所述横移框架内侧固定设有旋转油缸下支座,所述横移框架下端固定设有旋转下滑板。
进一步地,所述旋转层包括呈矩形的旋转框架,所述旋转框架内嵌在所述横移框架内并通过旋转销轴与所述横移框架转动连接,所述旋转框架下端分别固定设有旋转上滑板和旋转油缸上支座,所述旋转上滑板与所述旋转下滑板滑动配合,所述旋转油缸上支座铰接有旋转油缸,所述旋转油缸另一端与所述横移油缸下支座铰接,所述旋转油缸与横向和纵向均成一定夹角。
进一步地,所述竖向顶升层包括吊具,所述吊具下端固定设有竖向油缸,所述竖向油缸另一端与所述旋转框架上端固定连接。
进一步地,所述振捣装置包括长度可伸缩的振捣支撑梁,所述振捣支撑梁上端固定设有与所述调位装置下端可纵向滑动的振捣滑移机构,所述振捣支撑梁下端固定设有调节振捣器收放高度的振捣软管收放机构。
进一步地,所述振捣支撑梁端部滑动套接有振捣伸缩梁,所述振捣伸缩梁与所述振捣支撑梁之间固定连接有振捣伸缩油缸。
进一步地,所述振捣滑移机构包括固定在所述振捣支撑梁上端的架体,所述架体铰接有滑移滚轮,所述滑移滚轮与固定在横移层下端的工字型滑移轨道滑动配合。
进一步地,所述振捣软管收放机构包括分别固定在所述振捣支撑梁和振捣伸缩梁下端的主动滑轮和从动滑轮,所述主动滑轮同轴连接有驱动电机和减速器。
进一步地,所述振捣器包括振捣软管以及分别固定在所述振捣软管两端的振捣电机和振捣头,所述振捣软管搭接在所述主动滑轮和所述从动滑轮上。
本实用新型的有益效果如下:
1、集多种功能于一体,提高施工效率。本实用新型通过在混凝土内腔设置内模支架,内模支架上端设置调位装置和吊具来实现对内模以及钢筋笼的爬升以及吊装定位,同时在调位装置下端设置可自动控制振捣位置的振捣装置,内模支架通过与爬升装置的交替顶推爬升保持与待浇筑混凝土节段的高度匹配,滑移平台和承载平台可自动适应斜塔柱内腔斜度的变化,整个多功能平台集内模爬升、钢筋笼安装定位、精确振捣、内模支架自动爬升等多个功能于一体,大大提高了斜塔柱混凝土内腔施工的效率。
2、调位装置定位精确。本实用新型通过在底座上依次设置纵移层、横移层、旋转层和竖向顶升层来实现对待吊装设备的纵向平移、横向平移、竖向移动和旋转等四个自由度的调位,可一次性完成整个调位过程,施工效率高;各个移动层之间均通过油缸实现相应的移动,通过控制油缸的行程可以精确调整待吊装设备的位置。
3、振捣器定位精度高,提高振捣施工效率。通过振捣伸缩梁和振捣滑移机构可控制振捣器的横向位置和纵向位置,通过振捣软管收放机可控制振捣器的竖向高度,这样大大提高了振捣器的定位精度,无需反复调整位置,提高了振捣施工的效率。
附图说明
图1为多功能施工平台结构主视图。
图2为多功能施工平台结构俯视图。
图3为调位装置的主视图。
图4为调位装置的侧视图。
图5为调位装置的俯视图。
图6为底座结构的主视图。
图7为底座结构的俯视图。
图8为纵移层结构的主视图。
图9为纵移层结构的俯视图。
图10为横移层结构的主视图。
图11为横移层结构的俯视图。
图12为旋转层结构的主视图。
图13为旋转层结构的俯视图。
图14为振捣装置结构主视图。
图15为振捣支撑梁结构主视图。
图16为振捣滑移机构主视图。
图17为振捣软管收放机构主视图。
图18为本实用新型装置结构的主视图。
图19为内模支架结构的主视图。
图20为滑移平台与承载平台结构的主视图。
图21为滑移平台结构的俯视图。
图22为滑移平台结构的主视图。
图23为承载平台结构的俯视图。
图24为承载平台结构的主视图。
图25为横向伸缩臂结构的主视图。
图26为上爬箱与爬升轨道配合时的俯视图。
图27为爬升装置结构的主视图。
图28为锚固装置结构的主视图。
图29为步骤1)完成时的多功能施工平台结构示意图。
图30为步骤2)中浇筑时的多功能施工平台结构示意图。
图31为步骤3)中最上层承载平台爬升时的多功能施工平台结构示意图。
图32为步骤3)中最下层承载平台爬升时的多功能施工平台结构示意图。
图33为步骤4)中内模支架爬升完成后的多功能施工平台结构示意图。
图34为步骤5)中钢筋笼安装时的多功能施工平台结构示意图。
图35为步骤6)中内模爬升时的多功能施工平台结构示意图。
图中各部件标号如下:调位装置100、底座110、底座框架111、底座连接座112、纵移下滑板113、纵移油缸下支座114、纵移层120、纵移框架121、纵移上滑板122、纵移油缸123、纵移油缸上支座124、横移油缸下支座125、横移下滑板126、横移层130、横移框架131、横移上滑板132、横移油缸133、横移油缸上支座134、旋转油缸下支座135、旋转下滑板136、旋转层140、旋转框架141、旋转上滑板142、旋转油缸143、旋转油缸上支座144、旋转销轴145、竖向顶升层150、竖向油缸151、吊具152、振捣装置200、振捣支撑梁210、振捣伸缩梁211、振捣伸缩油缸212、振捣滑移机构220、架体221、滑移滚轮222、滑移轨道223、振捣软管收放机构230、主动滑轮231、从动滑轮232、驱动电机233、减速器234、振捣器240、振捣软管241、振捣电机242、振捣头243、内模支架300、竖向支架310、横向支架320、斜向支架330、爬升轨道340、凹槽341、滑移平台400、定位销轴410、限位滚轮420、限位卡钩430、爬箱支座460、承载平台500、横向主梁510、上腔室511、下腔室512、纵向主梁520、横向伸缩臂530、横向顶紧螺杆531、竖向支撑螺杆532、纵向伸缩臂540、纵向顶紧螺杆541、横向伸缩油缸550、纵向伸缩油缸560、爬升装置600、上爬箱610、爬箱内腔611、拨杆612、复位弹簧613、转轴614、凸轮615、限位凹槽616、下爬箱620、爬升油缸630、锚固装置700、牛腿710、预埋螺杆720、紧固螺母730、斜塔柱1000、斜塔柱内腔1100、斜塔柱内腔壁面1200、已浇筑混凝土节段1300、待浇筑混凝土节段1400、钢筋笼1500、内模1600。
具体实施方式
下面结合附图对本实用新型作进一步的详细说明,便于更清楚地了解本实用新型,但它们不对本实用新型构成限定。
如图1~2、图18~20所示,一种混凝土内腔多功能施工平台,用于桥梁斜塔柱内腔混凝土施工,其中,以桥梁长度方向为纵向,以垂直于桥梁长度方向为横向,斜塔柱1000内设有斜塔柱内腔1100,多功能施工平台包括位于斜塔柱内腔1100的内模支架300,内模支架300上端固定设有调位装置100,调位装置100下端滑动连接有振捣装置200,内模支架300外侧套设有滑移平台400和承载平台500;滑移平台400与内模支架300滑动配合,内模支架300外侧固定设有爬升轨道340,滑移平台400上端铰接有与爬升轨道340交替顶推滑动的爬升装置600,滑移平台400下端与承载平台500横向滑动连接,承载平台500滑动连接有与斜塔柱内腔壁面1200可拆卸固接的横向伸缩臂530。
这样,通过在混凝土内腔设置内模支架,内模支架上端设置调位装置和吊具来实现对内模以及钢筋笼的爬升以及吊装定位,同时在调位装置下端设置可自动控制振捣位置的振捣装置,内模支架通过与爬升装置的交替顶推爬升保持与待浇筑混凝土节段的高度匹配,滑移平台和承载平台可自动适应斜塔柱内腔斜度的变化,整个多功能平台集内模爬升、钢筋笼安装定位、精确振捣、内模支架自动爬升等多个功能于一体,大大提高了斜塔柱混凝土内腔施工的效率。
如图3~7所示,调位装置100包括底座110,底座110包括呈矩形的底座框架111,底座框架111与下端的内模支架固定连接,底座框架111上端分别固定设有纵移下滑板113和纵移油缸下支座114,底座框架111下端固定设有底座连接座112;底座110上从下到上依次设有纵移层120、横移层130、旋转层140、和竖向顶升层150,纵移油缸123驱动纵移层120相对底座110纵向滑动配合,横移油缸133驱动横移层130相对纵移层120横向滑动配合,旋转油缸143驱动旋转层140相对横移层130转动配合,竖向油缸151驱动竖向顶升层150相对旋转层140竖向移动配合。这样,通过在底座上依次设置纵移层、横移层、旋转层和竖向顶升层来实现对待吊装设备的纵向平移、横向平移、竖向移动和旋转等四个自由度的调位,可一次性完成整个调位过程,施工效率高;各个移动层之间均通过油缸实现相应的移动,通过控制油缸的行程可以精确调整待吊装设备的位置。
上述技术方案中,如图8~9所示,纵移层120包括呈矩形的纵移框架121,纵移框架121下端分别固定设有纵移上滑板122和纵移油缸上支座124,纵移上滑板122与纵移下滑板113滑动配合,纵移油缸上支座124铰接有两个纵向布置的纵移油缸123,纵移油缸123另一端与纵移油缸下支座114铰接;纵移框架121上端分别固定设有横移油缸下支座125和横移下滑板126。这样,通过控制纵移油缸实现纵移层相对底座纵向平移。
上述技术方案中,如图10~11所示,横移层130包括呈矩形的横移框架131,横移框架131下端分别固定设有横移上滑板132和横移油缸上支座134,横移上滑板132与横移下滑板126滑动配合,横移油缸上支座134铰接有横向布置的横移油缸133,横移油缸133另一端与横移油缸下支座125铰接;横移框架131内侧固定设有旋转油缸下支座135,横移框架131下端固定设有旋转下滑板136。这样,通过控制横移油缸实现横移层相对纵移层横向平移。
上述技术方案中,如图12~13所示,旋转层140包括呈矩形的旋转框架141,旋转框架141内嵌在横移框架131内并通过旋转销轴145与横移框架131转动连接,旋转框架141下端分别固定设有旋转上滑板142和旋转油缸上支座144,旋转上滑板142与旋转下滑板136滑动配合,旋转油缸上支座144铰接有旋转油缸143,旋转油缸143另一端与横移油缸下支座125铰接,旋转油缸143与横向和纵向均成一定夹角。这样,通过控制旋转油缸实现旋转层相对横移层绕旋转销轴旋转。
上述技术方案中,如图3~4、图12~13所示,竖向顶升层150包括吊具152,吊具上端承载待吊装设备,吊具152下端固定设有竖向油缸151,竖向油缸151另一端与旋转框架141上端固定连接。这样,先将待吊装的钢筋笼固定在吊具上端,然后通过控制各个油缸将待吊装钢筋笼移动到两侧已落位钢筋笼的正上方,再将待吊装钢筋笼与吊具解除固定并与已落位钢筋笼进行固定,最后调整吊装调位装置回到内模支架正上方。
如图14所示,振捣装置200包括长度可伸缩的振捣支撑梁210,振捣支撑梁210上端固定设有与调位装置100下端可纵向移动的振捣滑移机构220,振捣支撑梁210下端固定设有调节振捣器240收放高度的振捣软管收放机构230。这样,通过振捣伸缩梁和振捣滑移机构可控制振捣器的横向位置和纵向位置,通过振捣软管收放机可控制振捣器的竖向高度,这样大大提高了振捣器的定位精度,无需反复调整位置,提高了振捣施工的效率。
上述技术方案中,如图15所示,振捣支撑梁210端部滑动套接有振捣伸缩梁211,振捣伸缩梁211与振捣支撑梁210之间固定连接有振捣伸缩油缸212。这样,通过振捣伸缩油缸可以调节振捣伸缩梁伸缩量,从而调节振捣伸缩梁下端的振捣器的横向位置。
上述技术方案中,如图16所示,振捣滑移机构220包括固定在振捣支撑梁210上端的架体221,架体221铰接有滑移滚轮222,滑移滚轮222与固定在横移层130下端的工字型滑移轨道223滑动配合。这样,通过滑移滚轮与滑移轨道之间的滚动可调节振捣器的纵向位置。
上述技术方案中,如图14、图17所示,振捣软管收放机构230包括分别固定在振捣支撑梁210和振捣伸缩梁211下端的主动滑轮231和从动滑轮232,主动滑轮231同轴连接有驱动电机233和减速器234;振捣器240包括振捣软管241以及分别固定在振捣软管241两端的振捣电机242和振捣头243,振捣软管241搭接在主动滑轮231和从动滑轮232上。这样,驱动电机通过驱动主动滑轮对振捣软管进行收束或下放来调节振捣头的高度位置。
上述技术方案中,如图19所示,内模支架300包括竖向支架310,竖向支架310支架通过横向支架320固定连接,竖向支架310与横向支架320之间还固定连接有斜向支架330,爬升轨道340竖直固定在竖向支架310的纵向两侧。
上述技术方案中,如图26~27所示,爬升装置600包括爬升油缸630,爬升油缸630的油缸座一端与下爬箱620铰接,下爬箱620与滑移平台400的上端纵向两侧的爬箱支座460铰接,爬升油缸630的活塞杆一端与上爬箱610铰接,上爬箱610和下爬箱620内设有爬箱内腔611,爬箱内腔611设有凸轮615,凸轮615通过转轴614与爬箱内腔611内壁铰接,凸轮615固定连接有拨杆612,拨杆612另一端铰接有处于压缩状态的复位弹簧613,复位弹簧613另一端与上爬箱610和下爬箱620铰接。
上述技术方案中,爬升轨道340的横截面呈工字型,其外侧面上竖向设有多个间隔设置的凹槽341,爬箱内腔611还设有与爬升轨道340的翼缘板限位配合的限位凹槽616,凸轮615的两端呈锥形,凸轮一端与凹槽341限位抵接,另一端与爬箱内腔611内壁限位抵接。这样,当爬升装置顶推内模支架向上爬升时,承载平台固定支撑在斜塔柱内腔壁面,滑移平台与内模支架解除销连接,上爬箱和下爬箱的凸轮靠爬升轨道一侧的锥形端部斜向上嵌入凹槽中并与凹槽内腔的上壁面抵接,凸轮的另一端的锥形面与爬箱内腔抵接,当爬升油缸的活塞杆顶推上爬箱时,上爬箱的凸轮的两端均被限位无法相对上爬箱转动,凸轮对凹槽内腔的上壁面施加顶推力,从而推动内模支架向上爬升;当爬升装置向上爬升时,向下拨动拨杆带动凸轮转动一定角度,使凸轮靠爬升轨道一侧的锥形端部斜向下嵌入凹槽中并与凹槽内腔的下壁面抵接,当爬升油缸的活塞杆收缩时,上爬箱无法向下运动,下爬箱在活塞杆的收缩拉力作用下向上爬升,直到活塞杆恢复到原始收缩状态。
上述技术方案中,如图23~25所示,承载平台500包括由横向主梁510和纵向主梁520拼接而成的框架,横向主梁510设有上下两层的上腔室511和下腔室512,上腔室511和下腔室512一端开口且开口方向相反,上腔室511和下腔室512的开口端均与横向伸缩臂530滑动套接,横向伸缩臂530与横向主梁510之间固定连接有横向伸缩油缸550;所述纵向主梁520端部滑动套接有纵向伸缩臂540,所述纵向伸缩臂540与所述纵向主梁520之间固定连接有纵向伸缩油缸560。
上述技术方案中,如图23~25、图28所示,还包括多个竖向间隔固定在斜塔柱内腔壁面1200上的锚固装置700,锚固装置700包括牛腿710,牛腿710通过紧固螺母730与预埋在斜塔柱内腔壁面1200中的预埋螺杆720固定连接,横向伸缩臂530端部螺纹连接有与斜塔柱内腔壁面1200抵接的横向顶紧螺杆531,横向伸缩臂530竖向螺纹连接有竖向支撑螺杆532,竖向支撑螺杆532支撑在牛腿710上;纵向伸缩臂540的端部螺纹连接有与斜塔柱内腔壁面1200抵接的纵向顶紧螺杆541。这样,当内模支架固定不动,爬升装置爬升带动承载平台向上爬升时,首先调节横向顶紧螺杆和纵向顶紧螺杆使承载平台解除与斜塔柱内腔壁面的支撑作用,由于斜塔柱内腔壁面在横向上具有一定斜度,因此在爬升完成后,通过横向伸缩油缸和纵向伸缩油缸分别调节横向伸缩臂和纵向伸缩臂的伸缩量使横向顶紧螺杆和纵向顶紧螺杆重新抵接斜塔柱内腔壁面,然后使竖向支撑螺杆支撑在目标高度处的牛腿上。
上述技术方案中,如图21~22所示,滑移平台400为矩形框架结构,滑移平台400内侧通过定位销轴410与爬升轨道340可拆卸连接,滑移平台400内侧还固定设有与内模支架300滚动配合的限位滚轮420,滑移平台400上端部固定设有连接爬升装置600的爬箱支架460,滑移平台400下端面纵向两侧边缘设有限位卡钩430,限位卡钩430与横向主梁510的纵向两侧边缘卡接固定。这样,当进行内模支架和爬升装置的交替爬升时,解除定位销轴与爬升轨道的连接,通过限位滚轮与内模支架滚动配合;同时在整个装置初次安装时以及每次爬升完成时,由于内模支架、滑移平台和承载平台均要保持在横向和纵向上位于斜塔柱内腔中心,初次安装时,先吊装内模支架使其位于斜塔柱内腔中心,然后再调节纵移平台的横向伸缩腿和纵向伸缩腿使承载平台位于斜塔柱内腔中心。
爬升装置包括从上到下依次设置的上层爬升装置、中层爬升装置和下层爬升装置,内模支架与爬升装置交替爬升过程下:
首先将中层爬升装置所在的滑移平台和承载平台分别与内模支架和斜塔柱内腔壁面解除固定连接,并将凸轮的方向调整为朝爬升轨道一侧斜向下方向,爬升油缸先顶推上爬箱到预定位置,然后上爬箱保持不动,爬升油缸的活塞杆收缩拉动下爬箱向上移动到预定位置;其次重复上述过程完成下层爬升装置的爬升;最后,保证所有承载平台与斜塔柱内腔壁面固定连接,解除所有滑移平台与内模支架的固定连接,并将凸轮的方向调整为朝向爬升轨道一侧斜向上方向,启动爬升油缸顶升上爬箱,上爬箱带动内模支架向上爬升到预定位置,完成内模支架的一次爬升过程,待斜塔柱内腔混凝土施工完成某一节段后,再次循环上述爬升过程使内模支架的高度随着混凝土施工节段不断上升。
本实用新型所述的混凝土内腔多功能施工平台的施工过程如下:
1)安装定位多功能施工平台:如图29所示,首先浇筑第一节混凝土节段,并预埋锚固装置700,待混凝土养护完成后,然后吊装并定位内模支架300,使内模支架300位于斜塔柱内腔中心位置,再依次将承载平台500、滑移平台400外套在内模支架300的外侧,并在滑移平台400与爬升轨道340之间安装爬升装置600,在内模支架300的上端固定安装调位装置100,在调位装置100下端安装振捣装置200。
2)完成待浇筑混凝土节段的浇筑:如图30所示,通过调位装置100和吊具152将内模1600吊装并固定在待浇筑混凝土节段1400处的外模上,然后浇筑混凝土并通过振捣装置200进行振捣,完成混凝土的养护。
3)滑移平台和承载平台爬升:如图31~32所示,当已浇筑混凝土节段1300的上端接近内模支架300的上端时,首先完成最上层滑移平台400和承载平台500的爬升,然后由上到下完成全部滑移平台400和承载平台500的爬升,使最上层的承载平台500固定支撑在内模1600上,在爬升之前时,先解除滑移平台400与内模支架300之间的固定连接,并将承载平台500与斜塔柱内腔壁面1200解除固定,将凸轮615靠爬升轨道340一侧的朝向调整为为斜向下,在爬升装置600的顶推下依次向上爬升。
4)内模支架爬升:如图33所示,解除全部滑移平台400与内模支架300之间的固定连接,拨动拨杆612使凸轮615靠爬升轨道340一侧的朝向为斜向上,内模支架300在爬升油缸630顶推力下向上爬升到内模支架300的下端接近最下层承载平台500。
5)钢筋笼安装定位:如图34所示,通过调位装置100和吊具152将钢筋笼1400吊装到待浇筑混凝土节段1400处,使其与下端已浇筑混凝土节段1300固定。
6)内模提升和固定:如图35所示,解除内模1600与外模的固定,并通过吊具152和调位装置100提升到待浇筑混凝土节段1400处,并固定在钢筋笼1500的外侧;最后依次循环步骤2)~步骤6),直到完成所有节段混凝土的浇筑。
起点商标作为专业知识产权交易平台,可以帮助大家解决很多问题,如果大家想要了解更多知产交易信息请点击 【在线咨询】或添加微信 【19522093243】与客服一对一沟通,为大家解决相关问题。
此文章来源于网络,如有侵权,请联系删除


