车站主体围护结构未施工围护桩部位的逆作封堵方法与流程



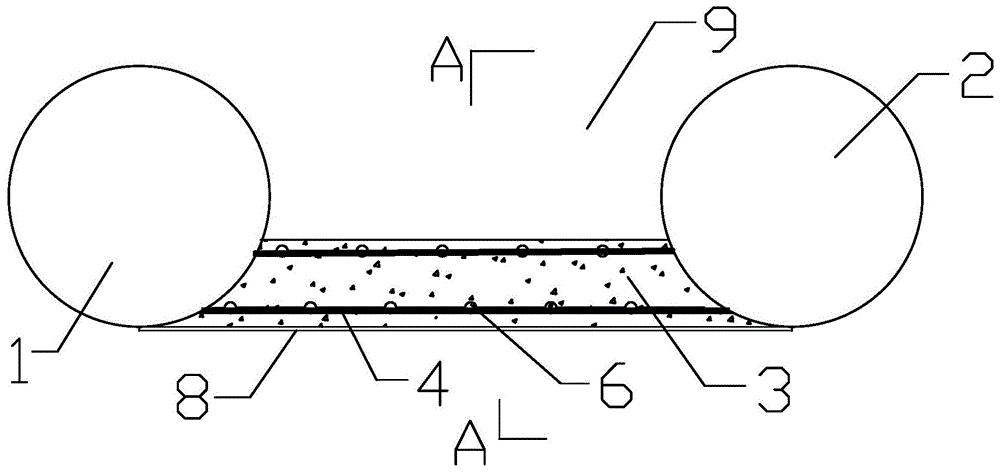
本发明涉及基坑施工领域,特别涉及一种车站主体围护结构未施工围护桩部位的逆作封堵方法。
背景技术:
基坑围护结构,作为地下工程重要组成部分,根据施工工艺的不同主要分为地下连续墙、钻孔灌注桩、工法桩等,施工时通常按照单幅(根)拼接而成。对于车站主体围护结构大多会采取钻孔灌注桩+内支撑系统,主体围护桩采用钻孔灌注桩,桩间设置混凝土挡板以保持桩间土体稳定,桩顶设置冠梁,车站主体基坑竖向采用多道支撑,支撑之间隔段采用连系梁连接。
在基坑施工过程中,经常会遇到通讯线或其它管线横穿基坑的影响围护桩的桩体施工,特别是遇到桩位位于道路交叉口处,车流量较多,管线无法迁改,导致该桩位的桩体无法施工,便会在该部位出现缺口。基坑未施工围护桩会导致该部位发生塌方、渗漏、涌水、涌沙等情况,并产生一系列连锁反应。尽管这些辅助工程的规模小,技术复杂程度不高,但事故一旦发生,事故的处理和恢复生产将非常的复杂和困难,会对总工期和企业的公众信任度产生严重影响。而且基坑所在地层以杂填土、黏质粉土粉砂和粉质黏土为主的情况时,车站负三层处于地下水位以下,围护桩未施工可能导致周边路面沉降、基坑变形、塌方、涌水、涌沙等重大安全隐患,因此,如何科学、高效地对主体围护结构个别围护桩围护桩问题进行处理,实现基坑安全平稳的开挖、支护、结构施工,将是车站施工的关键难题。
技术实现要素:
本发明根据现有技术的不足提供一种车站主体围护结构未施工围护桩部位的逆作封堵方法,该方法能够解决现有围护桩结构部分桩体无法正常施工而导致围护结构无法封闭,从而导致周边基坑路面沉降、基坑变形、塌方、涌水、涌沙等问题。
为了解决上述技术问题,本发明提供了一种车站主体围护结构未施工围护桩部位的逆作封堵方法,其特征在于:所述封堵方法针对车站主体围护结构采取钻孔灌注桩+内支撑系统时,围护结构中未施工围护桩的部位进行封堵,其封堵部位两侧分别设有围护桩体,具体施工步骤如下:
(1)在施工围护结构冠梁时在待封堵部位的冠梁内预埋封堵墙顶部区域的竖向主筋,所述竖向主筋内外双排间距设置,且封堵墙顶部区域的竖向主筋锚入冠梁长度不小于竖向主筋直径的35倍,竖向主筋预留错开距离不小于竖向主筋直径的35倍;
(2)在步骤(1)中的冠梁施工完成后,进行基坑开挖,首次开挖1~2米深度,在基坑开挖过程中,采用挖机掏除待封堵部位的土体,并人工进行平整;同时,针对待封堵部位两侧相邻围护桩体弧顶以内7~9cm位置的混凝土保护层进行竖向凿除,并露出围护桩竖向主筋;
(3)焊接首次开挖区域的封堵墙主筋,首先在步骤(1)中预埋的两排竖向主筋下端焊接封堵墙竖向主筋至基坑开挖底面以下,之后在每排竖向主筋的外侧焊接多根横向主筋形成钢筋网片结构,每排竖向主筋与横向主筋采用点焊连接,其连接点位不少于50%;每根横向主筋的两端与相邻围护桩的竖向主筋焊接,且焊接长度不小于横向主筋直径的5倍;两排钢筋网片之间采用拉钩筋连接;
(4)在临近基坑侧的钢筋网片结构外侧安装模板,模板位于相邻围护桩体弧顶之间,在模板的背面架设多根方木,并在方木背面横向设有多根钢支架,每根钢支架的两端分别与相邻围护桩的竖向主筋焊接;
(5)模板安装完成后,在模板、围护桩与外侧土体围设的封堵墙区域内浇筑混凝土,浇筑完成后采用人工振捣密实,并在混凝土达到初期强度,按规范进行拆模养护,完成第一段封堵墙的施工;
(6)在第一段封堵墙施工完成后,继续开挖基坑,重复步骤(2)~(5)分段施工封堵墙至基坑底面,每次基坑开挖深度为1~2m,每段封堵墙的竖向主筋与上段封堵墙的竖向主筋焊接,每段封堵墙的模板架设过程中,在模板顶部预留下料口,在模板架设完成后,通过下料口浇筑混凝土完成该段封堵墙的施工,并在浇筑完混凝土后将下料口封闭或在该段混凝土封堵墙施工完成后对于下料口部位进行磨平处理;
(7)在基坑挖至底面后,对于封堵墙周围的土体继续开挖0.5~1m,并重复步骤(2)~(5)在基坑以下继续施工0.5~1m的封堵墙,待基坑以下的封堵墙达到设计强度后,将封堵墙周围开挖的土体填埋至与基坑坑底平齐,完成整个封堵墙的施工。
本发明进一步的技术方案:所述封堵方法针对黏土地层或岩层地区的基坑围护结构。
本发明较优的技术方案:所述步骤(3)中封堵墙竖向主筋和横向主筋均采用φ12螺纹钢制作;所述拉钩筋水平方向20cm间距、垂直方向20cm间距布置。
本发明较优的技术方案:所述步骤(5)中在混凝土浇筑前竖向安装直径4~6cmpvc泄水管,其泄水管的出水口朝向基坑内。
本发明较优的技术方案:所述步骤(5)中的混凝土采用型号为c35p8的商品混凝土,混凝土浇筑完成11~13h后拆除模板。
本发明的有益效果:
(1)本发明通过封堵墙钢筋封堵墙钢筋与上方冠梁及两侧围护桩可靠连接,达到围护结构封闭的效果,其止水、加固效果好,解决了现有围护桩结构部分桩体无法正常施工而导致围护结构不能封闭的问题,避免了基坑封闭效果不好而出现的路面沉降、基坑变形、塌方、涌水、涌沙等问题,排除了基坑施工的重大安全隐患,其施工技术工艺简单,过程施工质量易于控制,适合类似地层的工法使用。
(2)本发明在封堵墙在冠梁施工阶段预埋钢筋,保证了钢筋的有效连接,钢筋绑扎与相邻围护桩连接良好,质量可控,保证了围护结构封闭成整体;
(3)本发明的模板稳固性良好,满足混凝土浇筑条件,混凝土浇筑后人工振捣密实,保证封堵墙的强度,混凝土浇筑前竖向安装左右pvc管泄水孔能够保证封堵墙泄水,其封堵墙强度性能满足要求,施工完成后基坑质量安全得到保障。
附图说明
图1是本发明的结构示意图;
图2是本发明的钢筋连接示意图;
图3是本发明图1中aa剖面图;
图4是本发明的模板架设横向剖面图;
图5是本发明的模板架设竖向平面图;
图6是本发明下层钢筋混凝土封堵墙浇筑示意图;
图7是实施例中采取措施各阶段涌水涌沙量曲线图。
图中:1—第一围护桩,2—第二围护桩,3—钢筋混凝土封堵墙,4—横向主筋,5—围护桩竖向主筋,6—竖向主筋,7—冠梁,8—模板,9—土体,10—模板支撑方木,11—下料口,12—模板钢支架,13—拉钩筋,a—基坑侧,b—土体面。
具体实施方式
下面结合附图和实施例对本发明作进一步说明。附图1至图7均为实施例的附图,采用简化的方式绘制,仅用于清晰、简洁地说明本发明实施例的目的。以下对在附图中的展现的技术方案为本发明的实施例的具体方案,并非旨在限制要求保护的本发明的范围。基于本发明中的实施例,本领域普通技术人员在没有作出创造性劳动前提下所获得的所有其他实施例,都属于本发明保护的范围。
在本发明的描述中,需要理解的是,术语“上”、“下”、“内”、“外”、“左”、“右”等指示的方位或位置关系为基于附图所示的方位或位置关系,或者是该发明产品使用时惯常摆放的方位或位置关系,或者是本领域技术人员惯常理解的方位或位置关系,仅是为了便于描述本发明和简化描述,而不是指示或暗示所指的设备或元件必须具有特定的方位、以特定的方位构造和操作,因此不能理解为对本发明的限制。此外,术语“第一”、“第二”等仅用于区分描述,而不能理解为指示或暗示相对重要性。
下面结合实施例对本发明进一步说明,实施例是针对某市地铁6号线a站为三层车站,车站主体围护结构方案采取钻孔桩+内支撑系统,主体围护桩采用
具体见表1。表1主体围护桩类型统计表
混凝土支撑底设置有
车站东北角因通讯线横穿基坑,影响桩位,且桩位位于道路交叉口处,车流量较多,管线无法迁改,导致其中一根桩未施工;东南角因广电通讯、电信、移动、联通、长城宽带等通讯线三道排管影响,导致三根桩无法施工,且无法进行迁改,经现场施工人员剥管摆线,其中两根已施工完成,剩余排管影响一根围护桩未施工。
该车站基坑所在地层主要以杂填土、黏质粉土粉砂和粉质黏土为主,车站负三层处于地下水位以下,围护桩未施工可能导致周边路面沉降、基坑变形、塌方、涌水、涌沙等重大安全隐患,因此,如何科学、高效地对主体围护结构个别围护桩围护桩问题进行处理,实现基坑安全平稳的开挖、支护、结构施工,将是车站施工的关键难题。对此,该项目的技术人员提出了三种解决方案:
方案一:加墙喷射混凝土技术方案
采用在土面挂设钢筋网片,与邻近围护桩预埋钢筋相邻,喷射商品混凝土技术,未施工围护桩部位加厚喷射混凝土厚度,提高混凝土强度等级,达到止水防塌方的目的。
方案二:地面注浆加固+喷射混凝与技术方案
采用地面注浆技术,在未施工围护桩部位侧上方钻孔注浆,在辅以在开挖土体面挂网喷射混凝土,以达到加固土体的目的。
方案三:本申请中的逆作封堵墙技术方案
在未施工围护桩部位自上向下逆作400mm厚的钢筋混凝土墙进行封堵,封堵墙钢筋与上方冠梁及两侧围护桩可靠连接,达到围护结构封闭的效果。从多角度、多方位考虑,对以上三种方案进行对比分析,其分析结果详见见表2。
表2三种方案的技术效果对比表
通过对以上三种方案的对比分析,该项目的负责人认为本申请中的封堵方法在技术可行性、提高基坑开挖安全系数、施工难易程度方面更具优势,所以选择采用了本发明中的逆作封堵墙的封堵方法来对未施工的围护桩部位进行封闭。下面以其中一处未施工围护桩部位的封堵过程进行详细说明,该其待封闭区域的两侧分别设有第一围护桩1和第二围护桩2,如图1所示,其逆作封堵墙置于第一围护桩1和第二围护桩2之间,其具体的施工过程如下:
(1)在施工围护结构冠梁时在待封堵部位的冠梁内预埋封堵墙顶部区域的竖向主筋6,竖向主筋6采用c22螺纹钢,所述竖向主筋6内外双排200mm间距设置,且封堵墙顶部区域的竖向主筋锚入冠梁长度不小于竖向主筋6直径的35倍,竖向主筋6预留错开距离不小于竖向主筋6直径的35倍;
(2)在步骤(1)中的冠梁施工完成后,进行基坑开挖,首次开挖1~2米深度,在基坑开挖过程中,采用挖机掏除第一围护桩1和第二围护桩2土体,并人工进行平整;同时,竖向每20cm凿除第一围护桩1和第二围护桩2弧顶以内7~9cm位置的混凝土保护层进行竖向凿除,并露出围护桩竖向主筋5;
(3)焊接首次开挖区域的封堵墙主筋,如图2所示,首先在步骤(1)中预埋的两排竖向主筋6下端焊接封堵墙竖向主筋至基坑开挖底面以下,之后在每排竖向主筋6的外侧焊接多根横向主筋4形成钢筋网片结构,横向主筋4也采用c22螺纹钢,每排竖向主筋6与横向主筋4采用点焊连接,其连接点位不少于50%;每根横向主筋4的两端与相邻围护桩的竖向主筋焊接,且焊接长度不小于横向主筋4直径的5倍;两排钢筋网片之间采用拉钩筋13连接,采用φ12螺纹钢制作拉钩连接,拉钩水平方向20cm间距、垂直方向20cm间距布置;
(4)在临近基坑侧的钢筋网片结构外侧安装模板8,如图4和图5所示,模板8位于第一围护桩1和第二围护桩2弧顶之间,模板8距离外侧土体之间的间距为40cm左右,模板8安装后保证封堵墙钢筋保护层厚度5cm左右,立模时保证模板8表面平整,错缝处采用双面胶粘贴;在模板8的背面架设多根模板支撑方木10,并在方木背面横向设有多根模板钢支架12,每根模板钢支架12采用工字钢,其两端分别与第一围护桩1和第二围护桩2的竖向主筋焊接;
(5)模板8安装完成后,在混凝土浇筑区域的土体内安装直径5cm左右pvc管泄水孔,泄水管的管口置于基坑内侧,将混凝土浇筑区域的积水引入基坑内;然后在模板8、围护桩与外侧土体围设的宽度为40cm的封堵墙区域内浇筑c35p8商品混凝土,浇筑完成后采用人工振捣密实,混凝土浇筑完毕12小时左右达到初期强度,按规范进行拆模养护,完成第一段封堵墙的施工;
(6)在第一段封堵墙施工完成后,继续开挖基坑,重复步骤(2)~(5)分段施工封堵墙至基坑底面,每次基坑开挖深度为1~2m,每段封堵墙的竖向主筋与上段封堵墙的竖向主筋焊接,每段封堵墙的模板架设过程中,如图6所示,在模板顶部预留下料口,在模板架设完成后,通过下料口浇筑混凝土完成该段封堵墙的施工,并在浇筑完混凝土后将下料口封闭或在该段混凝土封堵墙施工完成后对于下料口部位进行磨平处理;
(7)在基坑挖至底面后,对于封堵墙周围的土体继续开挖0.5~1m,并重复步骤(2)~(5)在基坑以下继续施工0.5~1m的封堵墙,待基坑以下的封堵墙达到设计强度后,将封堵墙周围开挖的土体填埋至与基坑坑底平齐,完成整个封堵墙的施工,封堵墙厚度为40cm,其完成的封堵墙如图1和图3所示。
在逆作封堵墙施工完成后,在基坑开挖、主体施工各施工环节中,发明人进一步对“车站主体围护结构未施工围护桩部位逆作封堵墙技术”效果进行确认,目标完成情况取得表3中的效果:
表3项目验收表
由项目验收表可以得出结论:本发明中的逆作封堵墙施工方法中塌方、涌水涌砂率为0的目标,效果检验曲线图如图7所示,可以很好解决现有围护桩结构部分桩体无法正常施工而导致围护结构无法封闭,从而导致周边基坑路面沉降、基坑变形、塌方、涌水、涌沙等问题,适用于黏土层等稳定性较好的地层的问题。
该项目的技术人员针对实施例取得的经济效益进行计算,其具体如下:
对策表费用max=钢筋预留对策二+基面开挖对策二+钢筋绑扎对策二+模板安装对策二+混凝土浇筑对策一=2000元+10000元+90000元+30000元+30000元=16.2万元;
对策实施费用=钢筋预留对策一+基面开挖对策三+钢筋绑扎对策一+模板安装对策二+混凝土浇筑对策一=1500元+6000元+60000元+40000元+40000元=14.75万元;
节约风险费用100万元,管理费用20万元。
本发明的经济效益主要为:
经济效益=(对策表费用max-对策实施费用)+风险费用+管理费用=(16.2-14.75)+100+20=121.45万元
通过上述效益计算可以看出,本发明在具体应用中取得很好的经济效果,大大节约了施工成本,而且本发明有效的解决了未施工围护桩部位塌方涌水渗水等问题,排除了基坑施工的重大安全隐患,其施工技术工艺简单,过程施工质量易于控制,适合类似地层的工法使用。
以上所述,只是本发明的一个实施例,其描述较为具体和详细,但并不能因此而理解为对本发明范围的限制。应当指出的是,对于本领域的普通技术人员来说,在不脱离本发明构思的前提下,还可以做出若干变形和改进,这些都属于本发明的保护范围。因此,本发明的保护范围应以所附权利要求为准。
起点商标作为专业知识产权交易平台,可以帮助大家解决很多问题,如果大家想要了解更多知产交易信息请点击 【在线咨询】或添加微信 【19522093243】与客服一对一沟通,为大家解决相关问题。
此文章来源于网络,如有侵权,请联系删除


