筒顶密梁筒内分仓单柱变截面负压筒海上风电基础及施工方法与流程



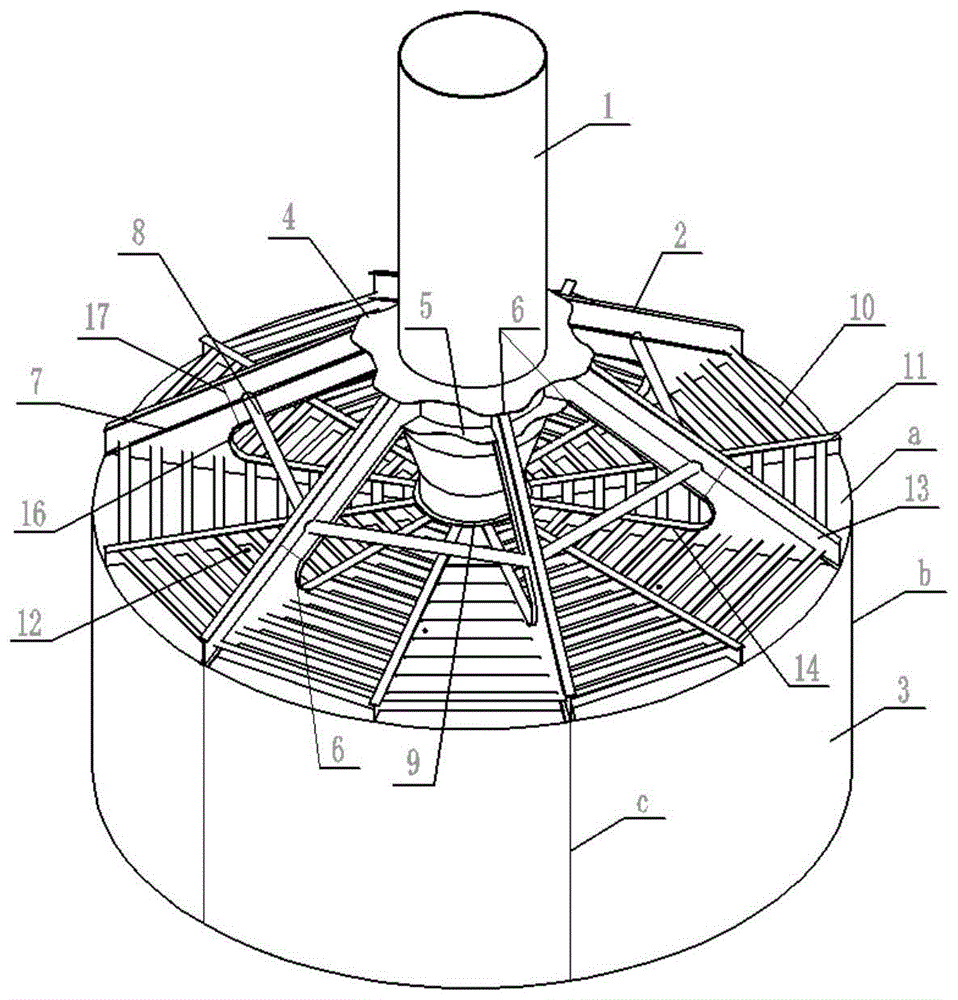
本发明涉及一种海上风电基础结构,具体涉及一种筒顶密梁筒内分仓单柱变截面负压筒海上风电基础及施工方法。
背景技术:
基于我国近海区域较大部分是淤泥、淤泥质土、黏土、砂土等地质条件,为满足地基承载力和基础变形要求,通常采用单桩和导管架等桩式基础,需要大型吊装船和打桩船辅助施工,通过锤击,将桩底打入较好的持力层,这种传统桩式基础造价较高且工期较长,如在福建、广东等海域多为覆盖层较浅的岩石地基,如采用桩式基础需要进行嵌岩施工,难度大、工期长、工程造价高。
随着海上风电机组单机容量的增大,采用传统单桩及导管架基础需要增大基础的尺寸和材料用量,大直径单桩和嵌岩均受大型海上施工设备限制成为不可逾越的问题,且风险大、工期长、工程造价高。
随着技术的不断进步,为解决以上问题,行业内进行了不断的探索。如:
复合筒型基础(专利cn107761755a、cn106759445)已用于海上风电和筒型基础的负压下沉安装方式(专利cn105926661a)可避免海上打桩和嵌岩作业,但所述基础适用水深浅、重量达5000吨,可利用的施工设备资源少,制作、运输和吊装难度大。
一种海上风电复合筒型基础(专利cn207567801u)可避免海上打桩和嵌岩作业,但所述基础中部单柱和钢管斜撑连接处应力集中非常明显,不利于基础的疲劳和冲切,耗钢量大;筒顶板需要设置钢筋混凝土,斜撑内部需要灌注混凝土,施工工序多且复杂,基础重量大,不利于基础制作、运输和吊装;工程造价高。
海上风机单桩-吸力筒组合基础及其施工方法(专利cn110016930a)可避免海上打桩和嵌岩作业,所述基础由上下两个筒组成,施工复杂,变形协调难度大,且中部单桩和筒连接处太薄弱,筒顶板无有效支撑体系,刚度较弱,不能将中部单桩承受的风机荷载有效传递到筒。
一种用于单柱和复合筒组合基础的连接工装(cn110607802a)可避免海上打桩和嵌岩作业,所述基础斜撑和中部单柱连接处仅设置了上环板,此处应力集中会很明显,不利疲劳,耗钢量大;中部单柱直径传伸入筒内形成中间舱室,由于其直径和筒相比较小,在负压下沉过程中容易产生土塞效应,可能导致下沉失败;由于中部单柱直径较小,从而使筒内其他分仓板长度大大增加,在运输和下沉过程中容易产生屈曲破坏;工程造价高。
技术实现要素:
为解决以上问题,本发明提供一种筒顶密梁筒内分仓单柱变截面负压筒海上风电基础及施工方法。
本发明采用的技术方案是:一种筒顶密梁筒内分仓单柱变截面负压筒海上风电基础,包括竖直设置的单柱和设置在单柱底部的负压筒,所述单柱顶部和风机底法兰连接,其特征在于:所述单柱通过斜支撑与负压筒连接;所述斜支撑上端通过上环板和下环板与单柱柱壁固定连接,下端与负压筒顶板固定连接,构成一个整体,将单柱承受的荷载有效传递到负压筒。
作为优选,斜支撑包括沿单柱周向均匀布置的多根斜柱和与斜柱连接的水平梁,多根所述斜柱上部均通过上环板和下环板与单柱连接,多根所述斜柱下部和水平梁之间通过直段相交或圆弧过渡连接;所述水平梁沿着负压筒径向贯通,和负压筒的顶板连接。
进一步的,每根所述斜柱沿长度方向均设有纵向加劲肋,所述纵向加劲肋一端连接于上环板和单柱相交处,另一端延伸至斜柱边缘;所述斜柱和水平梁相交处设有横向加劲肋,所述横向加劲肋垂直于斜柱。
进一步的,相邻两根斜柱之间均设有水平支撑,防止平面外失稳破坏。
进一步的,所述上环板和下环板与斜柱通过直段相交或圆弧过渡连接。
作为优选,所述负压筒的顶板上沿周向均匀布置有多根主梁,每根所述主梁均沿顶板径向设置,所述主梁与斜支撑之间设有多根次梁,多根所述次梁均沿顶板环向布置。
作为优选,所述负压筒包括顶板、外筒壁、外分仓板和内分仓板,所述外分仓板和内分仓板与顶板和外筒壁围合成多个舱室。
进一步的,所述顶板上设有与舱室一一对应连通的排水排气阀。
作为优选,所述单柱由上至下为的等径截面或变径截面的圆形截面,底部通过t型环梁与负压筒的顶板连接。
上述基础的施工方法,包括如下步骤:
a、工厂完成基础预制;
b、基础通过驳船或浮运将基础运到指定安装地点;
c、通过浮吊将基础吊离驳船(浮运通过排出负压筒内的水和气)沉放至海床面;
d、通过基础自重下沉至海床面以下一定深度;
e、通过排出负压筒内的水和气,形成向下负压,基础通过负压下沉将筒顶面沉放至与海床面紧密接触,下沉过程中可通过调整筒内各舱室的负压将基础的安装倾斜率控制在合理范围。
本发明取得的有益效果是:
1、所述基础主体为全钢结构,单柱采用上大下小的变截面,斜支撑以下单柱直径可由7m变为5m,减小耗钢量210吨,同时可减小基础浮力250t。
2、斜支撑底部水平梁贯通筒顶,筒顶部采用密梁结构,设置主梁和次梁,缩短筒顶板计算跨度,筒顶钢板厚度可由40mm降低至20mm,降低耗钢量,提高基础整体刚度,增大基础频率。
3、单柱不伸入筒内,底部通过t型环梁与顶板连接,筒内中部采用空间更大的多边形或圆形舱室,筒内分仓更均匀,在下沉过程中不会形成土塞,考虑单柱为上大下小的变截面造成的基础浮力减小,基础总下沉阻力由100mn减小至70mn,可将筒外壁厚度由40mm降低至25mm;同时可减小筒内其他分仓板的计算长度,增强抵抗屈曲失稳的能力,分仓板厚度由度由35mm降低至20mm,降低耗钢量。
4、斜支撑和单柱连接处增加纵向加劲肋,可大幅减小节点处应力集中现象,上环板应力从350mpa降低至240mpa,钢板厚度从90mm降低至60mm,降低耗钢量。
5、斜支撑和单柱连接处增加下环板,节点刚度增大,可大幅减小节点处应力集中现象,有利疲劳计算,风机及波浪产生的疲劳热点应力由35mpa降低至20mpa,单柱局部钢板厚度从70mm降低至55mm,降低耗钢量。
以广东海域某海上风电项目为计算背景,该专利技术可节省钢材用量30%以上,同时可降低海上浮吊施工船舶的起重量等级,减少施工设备使用费,综合考虑本发明技术可降低基础工程造价25%以上。
综上所述,本发明基础可适用水深5~50米,且构造简单、制作方便,可避免海上打桩和嵌岩作业,可缩短工期;耗钢量少,重量轻,对海上施工设备要求相对较低,可降低基础工程造价25%以上。
附图说明
图1为本发明的结构示意图;
图2为图1的立面图;
图3为图1的俯视图;
图4为斜支撑的结构示意图;
图5为图4的立面图;
图6为负压筒顶板梁系分布示意图;
图7为负压筒内部分仓结构示意图;
图8为上环板或下环板的结构示意图;
附图标记:1、单柱;2、斜支撑;3、负压筒(a、顶板;b、外筒壁;c、外分仓板;d、内分仓板);4、上环板;5、下环板;6、圆弧板过渡;7、纵向加劲肋;8、水平支撑;9、t型环梁;10、次梁;11、主梁;12、排水排气阀;13、斜柱;14、水平梁;15、水平梁相交过渡连接构件;16、圆弧过渡;17、横向加劲肋。
具体实施方式
下面结合附图和具体实施例对本发明作更进一步的说明。
如图1-8所示,本发明的一种筒顶密梁筒内分仓单柱变截面负压筒海上风电基础,包括单柱1和负压筒3,单柱1竖直设置,单柱1顶部和风机底法兰连接,底部与负压筒3的顶板a固定连接。单柱1通过斜支撑2与负压筒3固定连接,斜支撑2上端通过上环板4和下环板5与单柱1柱壁固定连接,下端与负压筒3顶板a固定连接,构成一个整体,将单柱1承受的荷载有效传递到负压筒3上。本发明利用负压系统排出负压筒3内的水和气体,形成负压,将基础下沉安装至表层土中,负压筒3筒顶与海床面接触,如遇表层厚度大的软土层,也可先清除一定深度的软土,然后再安装基础,本发明结合了单桩基础施工简单、传力明确和筒型基础稳定性好、海上安装方便等优点,解决了传统桩式基础需要大型设备海上打桩作业以及嵌岩施工难度大、工期长、造价高等问题。
本实施例中,单柱1为钢管,由上大下小的钢管卷制焊接形成,直径5~20m,壁厚30~200mm,上大下小,中部通过上环板4和下环板5和斜支撑2焊接,底部通过t型环梁9与负压筒3顶板a焊接。
结合图2-5所示,本实施例中,斜支撑2包括多根斜柱13和与斜柱13连接的水平梁14,多根斜柱13沿单柱1周向均匀布置(图4中,单柱1四周均匀布置有6根斜柱13),多根斜柱13上部均通过上环板4和下环板5与单柱1固定连接,多根斜柱13下部和水平梁14之间通过直段相交或圆弧过渡16连接,斜柱13底端既可设置于负压筒3顶板a边缘,也可缩进,设置于负压筒3顶板a直径范围内。水平梁14沿着负压筒3径向贯通,和负压筒3的顶板a固定连接,水平梁14一端斜柱13下部衔接,构成一个类似“u”形结构,另一端均固定在中间的水平梁相交过渡连接构件上,形成一个整体的斜支撑2结构。本实施例中,斜柱13为h型钢,高度1.0~5m;水平梁14为h型钢,高度0.3~2m。
本实施例中,每根斜柱13沿长度方向均设有纵向加劲肋7,纵向加劲肋7一端连接于上环板4和单柱1相交处,另一端延伸至斜柱13边缘。纵向加劲肋7由钢板制成,宽度0.2~1.0m,厚度20~150mm,纵向加劲肋7以上环板4、单柱1和斜柱13相交处为起点,沿着斜柱13焊接于斜柱腹板上,延伸至斜柱13端头。
斜柱13和水平梁14相交处设有横向加劲肋17,横向加劲肋17垂直于斜柱13。横向加劲肋17由钢板制成,宽度0.2~0.8m,厚度20~100mm,横向加劲肋17沿斜柱腹板两侧对称设置,与斜柱13三面槽型焊接。
结合图4和图5,本实施例中,相邻两根斜柱13之间均设有水平支撑8,水平支撑8将所有斜柱13相互连接在一起,防止其平面外失稳破坏。水平支撑8为钢管(本实施例采用直径0.3~1.5m的钢管)、工字型、十字型或箱型等截面。当斜柱13平面外稳定计算满足要求时,水平支撑18可取消。
结合图8,本实施例中,上环板4和下环板5与斜柱13通过直段相交或圆弧过渡连接6,上环板5和下环板5沿着环向与斜柱13顶部焊接,上环板5和下环板5均由厚度20~150mm的波浪形钢板制成。
结合图3和图6,负压筒3的顶板a上沿周向均匀布置有多根主梁11,每根主梁11均沿顶板a径向设置,主梁11与斜支撑2的水平梁14之间设有多根次梁10,多根次梁10均沿顶板a环向布置。主梁11沿径向焊接于顶板a上,一端与单柱1底部的t型环梁9焊接,另一端与外筒壁b焊接,次梁10沿着环向焊接于顶板a上,间距0.5~4.0m。主梁11和次梁10均采用高度为0.3~2m的t型钢。
结合图7,本实施例中,负压筒3包括顶板a、外筒壁b、外分仓板c和内分仓板d,外分仓板c和内分仓板d与顶板a和外筒壁b围合成多个舱室(5~11个舱室)。外筒壁b由钢管卷制焊接而成,筒直径10~50m,筒高5~30m;外分仓板c和内分仓板d由厚度为10~60mm的钢板制成,焊接于外筒壁b内侧,将负压筒3内部分割成7个舱室;顶板a由多块钢板组成,焊接于外分仓板c、内分仓板d和外筒壁b顶部,形成负压筒3,顶板a上设有与各舱室一一对应连通的排水排气阀12。
上述基础的施工方法,包括如下步骤:
a、工厂完成基础预制;
基础预制的步骤如下:
(1)、由上大下小的钢管卷制焊接形成单柱1;
(2)、斜柱13为h型钢,水平梁14为t型钢,水平梁14相交处用实心铸件或厚壁钢管15过渡连接,分散焊接点,斜柱13和水平梁14通过圆弧过渡件16连接,形成斜支撑2体系;
(3)、外筒壁b由钢管卷制焊接而成,外分仓板c和内分仓板d由钢板组成焊接于外筒壁b内侧,将负压筒3内部分割成为7个舱室,顶板a由多块钢板组成,焊接于外分仓板c、内分仓板d和外筒壁b顶部,形成负压筒3;
(4)、上环板4和下环板5沿着环向与斜柱13顶部焊接;
(5)、将斜支撑2体系吊装到负压筒3顶部与顶板a焊接;
(6)、将底部t型环梁9与顶板a焊接;
(7)、单柱1从斜支撑2中间预留孔洞穿过,底部与t型环梁9焊接,中部与斜柱13、上环板4和下环板5焊接;
(8)、纵向加劲肋7以上环板4、单柱1和斜柱13相交处为起点,沿着斜柱13焊接于斜柱腹板上,延伸至斜柱13端头;
(9)、横向加劲肋17沿斜柱腹板两侧对称设置,与斜柱三面槽型焊接;
(10)、顶板a与各舱室对应处开孔设置一处排气排水阀12;
b、基础通过驳船或浮运将基础运到指定安装地点;
c、通过浮吊将基础吊离驳船(浮运通过排出负压筒内的水和气)沉放至海床面;
d、通过基础自重下沉至海床面以下一定深度;
e、通过排出负压筒内的水和气,形成向下负压,基础通过负压下沉将筒顶面沉放至与海床面紧密接触,下沉过程中可通过调整筒内各舱室的负压将基础的安装倾斜率控制在合理范围。
以上显示和描述了本发明的基本原理和主要结构特征。本发明不受上述实例的限制,在不脱离本发明精神和范围的前提下,本发明还会有各种变化和改进,这些变化和改进都落入要求保护的本发明的范围内。本发明要求保护范围由所附的权利要求书及其等效物界定。
起点商标作为专业知识产权交易平台,可以帮助大家解决很多问题,如果大家想要了解更多知产交易信息请点击 【在线咨询】或添加微信 【19522093243】与客服一对一沟通,为大家解决相关问题。
此文章来源于网络,如有侵权,请联系删除


