一种挖掘装载机智能铲掘控制系统、方法及挖掘装载机与流程



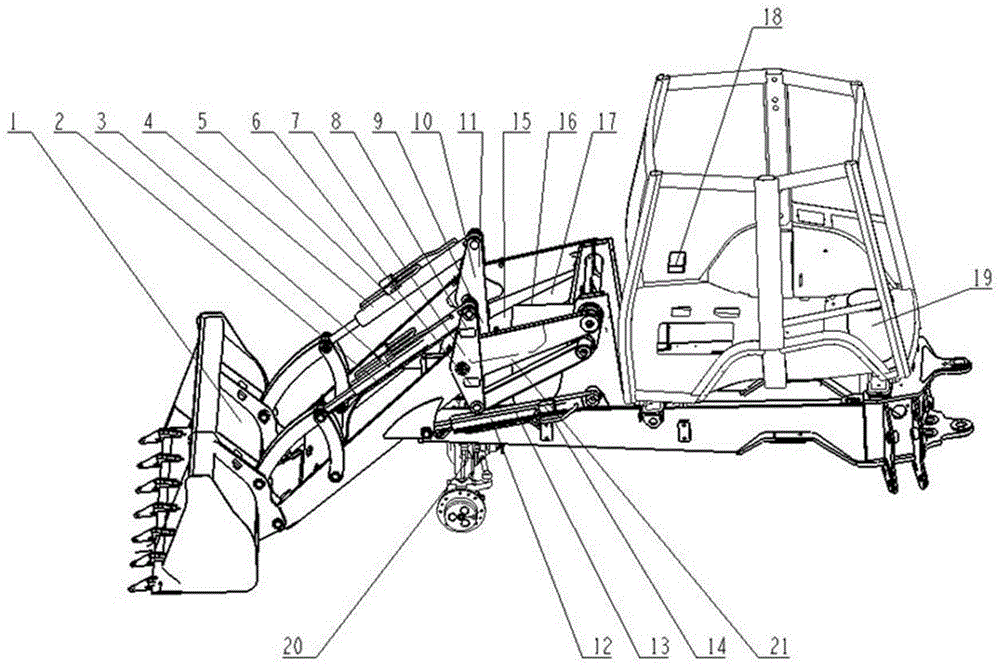
本发明属于挖掘装载机技术领域,具体涉及一种挖掘装载机智能铲掘控制系统、方法及挖掘装载机。
背景技术:
挖掘装载机作为一种多用途的工程机械,在工程建设领域发挥着重大的作用。在整个铲掘作业循环过程中,铲斗的铲掘物料作业过程作业姿态最为复杂,作业阻力最大,且能量消耗占据比重最大。由于挖掘装载机的作业对象是多种多样的岩土介质,特性相差较大,不同作业对象对应着不同的最佳铲掘方式。目前国内挖掘装载机铲掘作业通常的方式是,操作者凭借整机的牵引力将铲斗一次性插入物料,然后操纵动臂手柄和铲斗手柄来实现铲斗的回转和提升来完成铲掘作业,完全依赖于操作者的经验,存在作业效率低和能耗高的问题。
技术实现要素:
为解决现有技术中的不足,本发明提供一种挖掘装载机智能铲掘控制系统、方法及挖掘装载机,可以依据物料特征自动选择最佳铲掘轨迹,铲掘操作不依赖于操作者的经验,具有作业效率高、能耗低等优点。
为达到上述目的,本发明所采用的技术方案是:一种挖掘装载机智能铲掘控制系统,包括:分别与控制器电连接的筛分称重装置、料堆堆积角识别系统、铲斗左右距离识别系统、铲斗插入料堆识别系统、转向系统、铲掘轨迹数据库、前进系统和铲掘系统;控制器接收料堆堆积角识别系统发送的堆积角偏差和铲斗左右距离识别系统发送的距离偏差,并基于堆积角偏差和距离偏差向转向系统发送控制指令,使转向系统调整铲斗与料堆的相对位置;控制器接收料堆堆积角识别系统发送的左、右堆积角和筛分称重装置发送的物料特征参数,并基于左、右堆积角和物料特征参数在铲掘轨迹数据库中匹配最优的铲掘轨迹;控制器基于最优的铲掘轨迹和铲斗插入料堆识别系统发送的铲斗的齿尖与铲斗正前方料堆的距离,向前进系统和铲掘系统发送控制指令以执行铲掘作业。
进一步地,所述料堆堆积角识别系统、铲斗左右距离识别系统和铲斗插入料堆识别系统均同时与距离传感器一、距离传感器二、距离传感器三和距离传感器四电连接;所述距离传感器一和距离传感器二固定在左摇臂上,上下布置,用于获取与铲斗左侧正前方料堆的距离参数;所述距离传感器三和距离传感器四固定在右摇臂上,上下布置,用于获取与铲斗右侧正前方料堆的距离参数。
进一步地,所述料堆堆积角识别系统根据所述距离传感器一和距离传感器二采集到的距离参数计算左堆积角;根据所述距离传感器三和距离传感器四采集到的距离参数计算右堆积角;根据左堆积角和右堆积角计算堆积角偏差;当堆积角偏差超过预设的堆积角偏差阈值时,控制器向转向系统发送控制指令,转向系统调整铲斗与料堆的相对位置;当堆积角偏差满足预设的堆积角偏差阈值时,控制器计算左堆积角和右堆积角的平均值,作为料堆堆积角,以供铲掘轨迹数据库调用。
进一步地,所述铲斗左右距离识别系统根据所述距离传感器一和距离传感器二采集到的左侧距离参数、所述距离传感器三和距离传感器四采集到的右侧距离参数计算相对误差;当相对误差超过预设的距离偏差阈值时,控制器向转向系统发送控制指令,转向系统调整铲斗与料堆的相对位置。
进一步地,所述铲斗插入料堆识别系统根据所述距离传感器一和距离传感器二采集到的左侧距离参数计算铲斗左侧的齿尖与铲斗正前方料堆的距离,根据所述距离传感器三和距离传感器四采集到的右侧距离参数计算铲斗右侧的齿尖与铲斗正前方料堆的距离,并取平均值作为铲斗的齿尖与铲斗正前方料堆的距离l0;当l0减小到零时,则判断铲斗开始插入料堆,同时与通过左动臂油缸压力传感器和右动臂油缸压力传感器采集到的压力突变互相对比验证,共同作为铲斗开始插入料堆的识别判断条件。
进一步地,所述转向系统包括转向控制器和前桥转向油缸,转向控制器接收到控制器发送的转向指令后,控制前桥转向油缸实现转向动作。
进一步地,所述前进系统包括变速箱档位控制器和发动机油门控制器,所述变速箱档位控制器和发动机油门控制器分别与控制器电连接,控制器基于最优的铲掘轨迹向变速箱档位控制器和发动机油门控制器发送控制信号,以调整档位和油门。
进一步地,所述铲掘系统包括液压多路阀,所述液压多路阀根据接收到的控制器发出的动作指令信息,通过调节开闭控制左铲斗油缸、右铲斗油缸、左动臂油缸、右动臂油缸的伸缩执行铲掘动作,同时通过左铲斗油缸位移传感器、右铲斗油缸位移传感器、左动臂油缸位移传感器和右动臂油缸位移传感器实时反馈铲掘动作的执行状态。
进一步地,所述铲掘轨迹数据库内置在控制器中,包含针对不同种类的物料在特定的颗粒粒径分级特征、堆积密度和堆积角条件下,确定的铲斗最佳铲掘作业轨迹,以供控制器调用。
进一步地,所述筛分称重装置包括震动式筛分筒,所述震动式筛分筒固定于驾驶室内,用于测量物料的粒径特征和堆积密度。
一种挖掘装载机,所述挖掘装载机配置有前述的挖掘装载机智能铲掘控制系统。
一种挖掘装载机智能铲掘控制方法,包括:开启自动铲掘作业功能;接收物料特征参数;接收与铲斗左、右两侧正前方料堆的距离参数,并分别计算左堆积角、右堆积角、堆积角偏差和距离偏差;基于堆积角偏差和距离偏差调整铲斗与料堆的相对位置,直至堆积角偏差满足预设的堆积角偏差阈值、距离偏差满足预设的距离偏差阈值;计算料堆堆积角和铲斗的齿尖与铲斗正前方料堆的距离;基于料堆堆积角和物料特征参数在铲掘轨迹数据库中匹配最优的铲掘轨迹;基于最优的铲掘轨迹和铲斗的齿尖与铲斗正前方料堆的距离,向前进系统和铲掘系统发送控制指令以执行铲掘作业。
与现有技术相比,本发明所达到的有益效果:本发明通过筛分称重装置测量分析物料的粒径特征和密度特征,通过实时测量计算铲斗相对于料堆的左右距离及相对偏差和物料堆积角及相对偏差,根据料堆特性和相对位置关系来控制转向系统、前进系统和铲掘系统,调整铲斗插入姿态,自动判断铲斗开始插入物料的条件,并在铲掘作业姿态库中实时对比,匹配调用最优的自动铲掘控制参数,以提高铲掘满斗率,达到铲掘操作不依赖于操作者的经验、作业效率高、能耗低的目的。
附图说明
图1是本发明实施例提供的一种配置有挖掘装载机智能铲掘控制系统挖掘装载机的局部结构示意图;
图2是本发明实施例提供的一种挖掘装载机智能铲掘控制系统的系统结构示意图;
图3是本发明实施例提供的一种挖掘装载机智能铲掘控制方法的控制流程图;
图4是本发明实施例自动识别料堆特性的计算原理图。
具体实施方式
下面结合附图对本发明作进一步描述。以下实施例仅用于更加清楚地说明本发明的技术方案,而不能以此来限制本发明的保护范围。
实施例一:
如图1~4所示,一种挖掘装载机智能铲掘控制系统,包括:分别与控制器电连接的筛分称重装置、料堆堆积角识别系统、铲斗左右距离识别系统、铲斗插入料堆识别系统、转向系统、铲掘轨迹数据库、前进系统和铲掘系统;控制器接收料堆堆积角识别系统发送的堆积角偏差和铲斗左右距离识别系统发送的距离偏差,并基于堆积角偏差和距离偏差向转向系统发送控制指令,使转向系统调整铲斗与料堆的相对位置;控制器接收料堆堆积角识别系统发送的左、右堆积角和筛分称重装置发送的物料特征参数,并基于左、右堆积角和物料特征参数在铲掘轨迹数据库中匹配最优的铲掘轨迹;控制器基于最优的铲掘轨迹和铲斗插入料堆识别系统发送的铲斗的齿尖与铲斗正前方料堆的距离,向前进系统和铲掘系统发送控制指令以执行铲掘作业。
如图1所示,以挖掘装载机的装载端工作装置为例,为一种平行八连杆结构,自动铲掘作业系统装置包括:铲斗1、左铲斗油缸2、左铲斗油缸位移传感器3、右铲斗油缸4、右铲斗油缸位移传感器5、距离传感器一6、左摇臂7、距离传感器二8、距离传感器三9、右摇臂10、距离传感器四11、左动臂油缸12、左动臂油缸位移传感器13、左动臂油缸压力传感器14、右动臂油缸15、右动臂油缸位移传感器16、右动臂油缸压力传感器17、控制器18、筛分称重装置19、转向系统20、前进系统21。
挖掘装载机智能铲掘控制系统的系统结构如图2所示,在挖掘装载机进入施工场地或者更换铲掘作业对象之前,通过筛分称重装置19测试铲掘介质的颗粒级配和堆积密度,作为控制器18的输入信息。在v型作业循环过程中,开启自动铲掘作业按钮26,每次铲斗1向着料堆前进插入的过程中,通过料堆堆积角识别系统23实时测算前方料堆的左、右堆积角并计算相对误差作为堆积角偏差,通过铲斗左右距离识别系统24实时测算铲斗1左、右侧与料堆的距离并计算相对误差作为距离偏差,通过铲斗插入料堆识别系统25实时测算铲斗的齿尖与铲斗正前方料堆的距离,上述三者作为控制器18的输入信息。控制器18根据接收到的输入信息,一方面控制转向系统20调整铲斗与料堆的相对位置关系,一方面在铲掘轨迹数据库28中对比匹配最优的铲掘轨迹策略,当铲斗插入料堆之后,控制器18在操控前进系统21前进的同时,控制铲掘系统22进行自动铲掘作业,以实现不同特性料堆的智能铲掘作业。
料堆堆积角识别系统23、铲斗左右距离识别系统24和铲斗插入料堆识别系统25均同时与距离传感器一6、距离传感器二8、距离传感器三9和距离传感器四11电连接或者通讯协议相连,实时测量并进行数据传递;距离传感器一6和距离传感器二8固定在左摇臂7上,上下布置,用于获取与铲斗左侧正前方料堆的距离参数;距离传感器三9和距离传感器四11固定在右摇臂10上,上下布置,用于获取与铲斗右侧正前方料堆的距离参数。
料堆堆积角识别系统23根据距离传感器一6和距离传感器二8采集到的距离参数计算左堆积角;根据距离传感器三9和距离传感器四11采集到的距离参数计算右堆积角;根据左堆积角和右堆积角计算堆积角偏差。当堆积角偏差超过预设的堆积角偏差阈值时,控制器18向转向系统20发送控制指令,转向系统20调整铲斗1与料堆的相对角度,从而实现铲斗1的正铲,有利于减小偏载程度和提高满斗率;当堆积角偏差满足预设的堆积角偏差阈值时,控制器18计算左堆积角和右堆积角的平均值,作为最终的料堆堆积角,以供铲掘轨迹数据库28调用,计算原理如图4所示。
铲斗左右距离识别系统24根据距离传感器一6和距离传感器二8采集到的左侧距离参数、距离传感器三9和距离传感器四11采集到的右侧距离参数计算相对误差;当相对误差超过预设的距离偏差阈值时,控制器18向转向系统20发送控制指令,转向系统20调整铲斗1与料堆的相对角度,从而实现铲斗1的正铲,有利于减小偏载程度和提高满斗率。
铲斗1根据左、右堆积角和左、右距离完成姿态调整之后,可以近似认为铲斗1处于正铲状态,此时,铲斗插入料堆识别系统25根据距离传感器一6和距离传感器二8采集到的左侧距离参数计算铲斗左侧的齿尖与铲斗正前方料堆的距离,根据距离传感器三9和距离传感器四11采集到的右侧距离参数计算铲斗右侧的齿尖与铲斗正前方料堆的距离,并取平均值作为铲斗的齿尖与铲斗正前方料堆的距离l0,计算原理如图4所示。当l0减小到零时,则判断铲斗开始插入料堆,控制器18接收到信号后,开始调用铲掘系统22进行自动铲掘作业。同时,当铲斗1开始插入料堆的瞬间,左动臂油缸12和右动臂油缸15的油缸压力值会产生大幅度的瞬间增长,利用对应的左动臂油缸压力传感器14和右动臂油缸压力传感器17实时测量油缸压力并反馈给控制器18,将检测到的油缸压力突变与计算距离l0互相对比验证,共同作为铲斗开始插入料堆的识别判断条件。左动臂油缸压力传感器14和右动臂油缸压力传感器17可采用三通连接,与控制器18通过电连接或者通讯协议连接。
转向系统20包括转向控制器和前桥转向油缸等,控制器18根据接收到的铲斗左、右堆积角和距离偏差信息做出是否需要进行转向调整的判断,继而向转向控制器发出转向指令信号,从而控制前桥转向油缸实现转向。调整挖掘装载机的前进方向,以尽可能的实现铲斗1正对着料堆进行铲掘作业。转向系统20的操作命令内置于控制器18中,与装载端的转向控制器通过电连接。
前进系统21包括变速箱档位控制器和发动机油门控制器,与控制器18进行电连接。当铲斗开始插入料堆之后,控制器18根据选择的最佳铲掘轨迹对应的整车前进速度,向变速箱档位控制器和发动机油门控制器发送控制信号,调整相应的档位和油门,从而保持既定速度前进。
铲掘系统22包括液压多路阀29、左铲斗油缸2、左铲斗油缸位移传感器3、右铲斗油缸4、右铲斗油缸位移传感器5、左动臂油缸12、左动臂油缸位移传感器13、右动臂油缸15、右动臂油缸位移传感器16;
液压多路阀29根据接收到的控制器18发出的动作指令信息,通过调节开闭控制左铲斗油缸2、右铲斗油缸4、左动臂油缸12、右动臂油缸15的伸缩执行铲掘动作,同时通过左铲斗油缸位移传感器3、右铲斗油缸位移传感器5、左动臂油缸位移传感器13和右动臂油缸位移传感器16实时反馈各油缸的伸缩长度以判断铲掘动作的执行状态。铲斗1插入料堆后,针对不同料堆特性对应的不同的铲掘轨迹,铲掘系统22可实现动臂抬升和铲斗回转的的组合,从而提高作业效率和满斗率。液压多路阀29为一种电磁式比例液压多路阀,位移传感器可采用液压油缸位移传感器,并与控制器18通过电缆或者通讯协议连接。
铲掘轨迹数据库28,以提效降耗为目标,针对不同种类的物料,如碎石、砂、土、煤等,在特定的颗粒粒径分级特征、堆积密度和堆积角等特性条件下,基于edem-redurdyn-amesim联合仿真确定铲斗的最佳铲掘作业轨迹,并经样机验证、固化,形成数据库。铲掘轨迹数据库28内置在控制器18中,根据筛分称重装置19和料堆堆积角识别系统23的输入信息,进行对比匹配,选择最优铲掘作业,并供控制器19调用,进行下一步的自动铲掘作业。同时,铲掘轨迹数据库28为一种开式系统,可根据最新优化结果或者施工现场测试结果进行调试更新。
筛分称重装置19为一种震动式筛分筒,与实验室用筛分筒结构保持一致,包含一系列不同孔径的筛分盘,并具有分层质量显示功能,可通过螺栓固定于驾驶室内。在进行铲掘作业之前,如果不具备实验室测试分析条件,可通过此装置实现物料的粒径特征和堆积密度测量。测试时,现场取样置于筛分筒内,发动工程车辆并处于怠速状态,依靠驾驶室自身的震动实现筛分,不需要额外的震动电机,可降低成本。
控制器18与附属的可读写显示器、开启按钮26、急停按钮27等,均安装于驾驶室内的操控平台上。可手动输入物料类型、颗粒粒径分级特征、堆积密度等料堆特性信息。打开自动铲掘作业的开启按钮26之后,在向着料堆前进的过程中,控制器18实时接收料堆堆积角识别系统23和铲斗左右距离识别系统24传来的堆积角信息和距离信息,若相对偏差超出预设值,则控制转向系统20调整铲斗姿态,实现正铲。然后控制器18根据接收到的物料特性信息和料堆堆积特性信息,在铲掘轨迹数据库28中对比选择最佳的铲掘轨迹方案。然后控制器18通过铲斗插入料堆识别系统25识别判断铲斗开始插入料堆的条件。最后控制器18通过前进系统21和铲掘系统22,控制铲斗1前进插入料堆、抬升与回转等动作,以实现针对不同物料特性的智能铲掘作业。
如图4所示,为装载工作装置左侧面与料堆的示意图,右侧面与左侧面对称一致。铲掘作业时,铲斗放至水平位置,摇臂同一侧的上、下两个传感器的距离l6为已知、与水平面的夹角θ2为已知,下方距离传感器与铲斗齿尖的水平距离l3和竖直距离l5为已知;
铲斗与料堆的距离为l1和l2,整车前进过程中,通过距离传感器实时测量;
左堆积角θ1=arctan(l6*sinθ2/(l1+l6*cosθ2-l2)),右堆积角计算方法相同;
铲斗齿尖与料堆的距离l0=l2-l3-l4,l4=l5*cosθ2,当l0减小至零时,结合油缸压力突变,可判断铲斗开始插入料堆。
本发明通过筛分称重装置测量分析物料的粒径特征和密度特征,通过测距仪实时测量计算铲斗相对于料堆的左右距离及相对偏差和物料堆积角及相对偏差,控制器根据料堆特性和相对位置关系来控制转向系统、前进系统和铲掘系统,调整铲斗插入姿态,自动判断铲斗开始插入物料的条件,并在铲掘作业姿态库中实时对比,匹配调用最优的自动铲掘控制参数,以提高铲掘满斗率,达到提高作业效率,降低能耗的目的。
实施例二:
基于实施例一所述的挖掘装载机智能铲掘控制系统,本实施例提供一种挖掘装载机,该挖掘装载机配置有实施例一所述的挖掘装载机智能铲掘控制系统,如图1所示。
实施例三:
基于实施例一所述的挖掘装载机智能铲掘控制系统和实施例二所述的挖掘装载机,本实施例提供一种挖掘装载机智能铲掘控制方法,包括:
(1)开启自动铲掘作业功能;
(2)接收物料特征参数;根据物料颗粒级配筛分记录和物料堆积密度称重记录通过手动输入或通过筛分称重装置测量获取;
(3)整车正常前进,驶向料堆;
(4)接收与铲斗左、右两侧正前方料堆的距离参数,并分别计算左堆积角、右堆积角、堆积角偏差和距离偏差;
(5)基于堆积角偏差和距离偏差调整铲斗与料堆的相对位置,调整前进方向,直至堆积角偏差满足预设的堆积角偏差阈值、距离偏差满足预设的距离偏差阈值;
(6)计算料堆堆积角和铲斗的齿尖与铲斗正前方料堆的距离,进行铲斗开始插入料堆条件判断;
(7)基于料堆堆积角和物料特征参数在铲掘轨迹数据库中匹配最优的铲掘轨迹;
(8)基于最优的铲掘轨迹和铲斗的齿尖与铲斗正前方料堆的距离,向前进系统和铲掘系统发送控制指令,调整前进速度,进行自动铲掘作业。
以上所述仅是本发明的优选实施方式,应当指出,对于本技术领域的普通技术人员来说,在不脱离本发明技术原理的前提下,还可以做出若干改进和变形,这些改进和变形也应视为本发明的保护范围。
起点商标作为专业知识产权交易平台,可以帮助大家解决很多问题,如果大家想要了解更多知产交易信息请点击 【在线咨询】或添加微信 【19522093243】与客服一对一沟通,为大家解决相关问题。
此文章来源于网络,如有侵权,请联系删除


